Параметры режимов автоматической и механизированной дуговой сварки плавящимся электродом. Критерии и документы, в соответствии с которыми следует осуществлять их выбор.
Режимом сварки называют совокупность основных характеристик (парамет- ров) сварочного процесса, обеспечивающих получение сварных швов заданных размеров, формы и качества. Такими параметрами при дуговой сварке являются диаметр электродной проволоки (dэ), значения величин сварочного тока (Iсв) и напряжения на дуге (Uд), скорость перемещения электрода вдоль свариваемых кромок (Vсв), род тока и его полярность. Размерами швов, определяющими качество и работоспособность сварного соединения, являются (рис. 1): – глубина проплавления – h; – ширина шва – e; – высота валика – g. Отношение ширины шва e к глубине проплавления h называют коэффициен- том формы проплавления (φпр): ϕпр = е/h
Для механизированной сварки стыковых швов значения φпр должны нахо- диться в интервале 0,8...4,0.
Отношение ширины шва e к высоте валика g называют коэффициентом формы усиления или коэффициентом формы валика (φв): ϕв =e/g
Значения φв для хорошо сформированных швов не должны выходить за пределы 7...10
Параметры режимов автоматической и механизированной дуговой сварки под флюсом. Критерии и документы, в соответствии с которыми следует осуществлять их выбор.
Основными параметрами режима сварки под флюсом являются диаметр сварочной проволоки, сила сварочного тока, напряжение на дуге, скорость сварки, вылет электрода, род тока и полярность.
Диаметр электродной проволоки оказывает большое влияние на размер и форму сварного шва. Уменьшение диаметра проволоки при том же токе приводит к уменьшению подвижности столба дуги и, как следствие, к увеличению глубины провара и уменьшению ширины шва. Диаметр проволоки зависит от толщины свариваемого металла и способа сварки. Для полуавтоматической сварки диаметр проволоки обычно принимают 1,6; 2,0 мм, для автоматической 2 – 6 мм.
|
|
Сила сварочного тока является параметром, позволяющим наиболее эффективно повышать мощность дуги и производительность процесса сварки. За счет изменения силы тока изменяют глубину провара основного металла. На ширину шва сила тока влияет незначительно. Увеличение глубины проплавления с ростом силы тока обусловлено увеличением тепловой мощности и давления столба дуги.
Род и полярность тока влияют на форму и размеры шва. При сварке на постоянном токе обратной полярности глубина проплавления на 40% больше, чем при сварке на прямой полярности. При сварке на переменном токе глубина провара на 15-20% ниже чем при сварке на постоянном токе обратной полярности. Это объясняется формой столба дуги. Анодное пятно занимает большую площадь по сравнению с катодным. Поэтому ширина ванны на прямой полярности возрастает. Род и полярность тока заметно влияют на скорость плавления, на обратной полярности она ниже на 20 – 30 %, чем на прямой.
|
|
Напряжение дуги зависит в основном от длины дуги и состава газов, заполняющих дуговой промежуток. Чем больше длина дуги, тем больше и напряжение. Увеличение напряжения дуги приводит к увеличению ее подвижности, в результате чего значительно возрастает ширина шва, заметно снижается выпуклость шва, а глубина проплавления остается почти постоянной. При увеличении толщины свариваемого металла увеличение силы тока должно сопровождаться соответствующим повышением напряжения.
Увеличение скорости перемещения дуги до 40 – 50 м/ч приводит к увеличению горизонтальной составляющей давления дуги на расплавленный металл сварочной ванны. Толщина слоя жидкого металла под дугой уменьшается, тепловое действие дуги на основной металл возрастает, глубина проплавления увеличивается, несмотря на уменьшение погонной энергии. При дальнейшем увеличении скорости перемещения дуги, влияние уменьшения погонной энергии становится преобладающим, глубина провара уменьшается. Ширина валика и выпуклость при возрастании скорости перемещения дуги уменьшаются.
|
|
ГОСТ 8713-79СВАРКА ПОД ФЛЮСОМ. СОЕДИНЕНИЯ СВАРНЫЕОСНОВНЫЕ ТИПЫ, КОНСТРУКТИВНЫЕ ЭЛЕМЕНТЫ И РАЗМЕРЫ
Виды оборудования, используемого для производства сварных конструкций. Критерии и документы, в соответствии с которыми следует осуществлять выбор сварочного и вспомогательного оборудования.
Технологическое оборудование для изготовления деталей сварных конструкций можно разделить на группы: для правки, очистки и подготовки поверхности; разметки и маркировки; механической резки; термической резки; гибки; штамповки; механической обработки; средства механизации заготовительных работ.
Оборудование для правки
Правка необходима для выправления проката до его обработки и заготовок после вырезки и производится путем пластического изгиба или растяжения металла.
Оборудование для очистки
Очистку применяют для удаления с поверхности металла средств консервации, загрузнения, смазочно-охлаждающих жидкостей, ржавчины, окалины, заусенцев и шлака, затрудняющих процесс сварки и вызывающих дефекты сварных швов.
Оборудование для резки
При изготовлении деталей сварных конструкций применяют следующие виды резки: ножницами, на отрезных станках, термическую.
|
|
В производстве сварных конструкций применяют ножницы: листовые с наклонным ножом, высечные, дисковые, комбинированные, сортовые, для резки уголка, для резки швеллеров и двутавров пресс-ножницы комбинированные, механизировано-ручные пневматические и электрические.
Оборудование для гибки
Гибку выполняют путем пластического изгиба заготовки.
Оборудование для холодной штамповки
Основные виды холодной штамповки: вырубка, пробивка, гибка, вытяжка и формовка.
Холодную штамповку применяют для изготовления деталей из листового материала толщиной преимущественно до 10 мм. Отверстие пробивают в металле толщиной до 25 мм.
СВОД ПРАВИЛ ПО ПРОИЗВОДСТВУ СВАРОЧНЫХ РАБОТ И КОНТРОЛЮ КАЧЕСТВА СВАРНЫХ СОЕДИНЕНИЙ СП 105-34-96
Схема поста и виды оборудования, необходимого для механизированной сварки в углекислом газе. Критерии и документы, в соответствии с которыми следует осуществлять выбор сварочного и вспомогательного оборудования для данного способа сварки.
Оборудование поста для сварки в среде углекислого газа. Для механизированной сварки в среде углекислого газа применяются полуавтоматы отечественного производства марок ПДГ-516, ПДГ-508, ПДГ-415, ПДГ-252 и др., а также полуавтоматы зарубежных фирм. Сварочные полуавтоматы имеют в своем составе примерно одинаковые функциональные блоки и отличаются друг от друга лишь мощностью и конструктивным исполнением. В качестве примера представлен пост механизированной сварки в углекислом газе полуавтоматом ПДГ-516, блок-схема которого представлена на рис. 10.10.
Сварочная проволока подается в зону сварки подающим механизмом, состоящим из двигателя постоянного тока, редуктора и двух пар роликов-шестерен с гладкими коническими канавками. Рычажным механизмом верхние ролики прижимаются к нижним. Сварочная проволока из кассеты подается роликами-шестернями через шланг в сварочную горелку. Сюда же подаются сварочный ток через кабель от выпрямителя и углекислый газ из баллона с углекислотой. Для сварки в углекислом газе используются выпрямители с жесткой внешней характеристикой марок ВС-300, ВДГ-301 и др. (в процессе сварки напряжение на дуге постоянно и не зависит от величины сварочного тока) или универсальные выпрямители ВДУ-504, ВДУ-506.
Блок-схема полуавтомата для сварки в среде СО2:
1 – сварочная горелка; 2 – механизм подачи электродной проволоки;
3 – кассета с электродной проволокой; 4 – сварочные кабели; 5 – баллон
с углекислотой; 6 – подогреватель газа; 7 – редуктор-расходомер; 8 – кабель
управления; 9 – сварочный выпрямитель; 10 – осушитель газа
В баллоне сварочная углекислота находится в жидком состоянии. После испарения углекислый газ проходит через подогреватель, редуктор-расходомер, электрогазовый клапан и поступает в сварочную горелку. В случае применения несварочной (пищевой) углекислоты, с повышенным содержанием влаги, в газовую магистраль дополнительно включают осушитель. Испарение углекислоты проходит с поглощением тепла. Подогреватель повышает температуру углекислого газа, предотвращая замерзание редуктора. Редуктор-расходомер обеспечивает снижение давления газа до рабочего значения и контроль его расхода в процессе сварки.
Электрогазовый клапан представляет собой исполнительный механизм, открывающий и закрывающий подачу газа в сварочную горелку.
Блок управления сварочным полуавтоматом (БУСП) с электрогазовым клапаном расположен сзади подающего механизма и обеспечивает выполнение следующих операций:
– включение и выключение электрогазового клапана (выключение выполняется с регулируемой задержкой 1…5 с, что обеспечивает защиту жидкого металла вплоть до его затвердевания);
– включение и выключение электродвигателя подачи проволоки (скорость подачи проволоки регулируется резистором на панели блока управления);
– включение и выключение сварочного выпрямителя (выключение выполняется с регулируемой задержкой 0,5…3 с, что обеспечивает заварку кратера).
При нажатии выключателя на сварочной горелке происходит включение газового клапана и подача газа в зону сварки. Через 1 с включаются источник питания сварочной дуги и привод подачи электродной проволоки. При замыкании сварочной проволоки на изделие зажигается дуга.
При размыкании выключателя останавливается двигатель подачи электродной проволоки, происходит растяжка дуги и ее обрыв. Через 0,5…3 с выключается источник питания и через 1…5 с – газовый клапан (снимается напряжение со сварочной горелки и прекращается подача газа). Следующее включение происходит при нажатии кнопки на сварочной горелке.
Основными критериями для выбора рациональных типов оборудования служат:
- техническая характеристика, наиболее отвечающая принятым в разрабатываемом техпроцессе режимам сварки;
- наибольшая эксплуатационная надежность и простота обслуживания;
- наибольший коэффициент полезного действия и наименьшее потребление энергии при работе;
- наименьшие габариты, требующие минимальную площадь для размещения;
- наименьшая масса и минимальная стоимость.
Дата добавления: 2018-08-06; просмотров: 822; Мы поможем в написании вашей работы! |
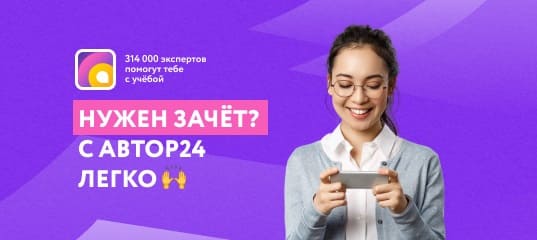
Мы поможем в написании ваших работ!