Определение понятия «заготовка» и виды заготовок, используемых при производстве сварных конструкций
Заготовка (материал) — получивший предварительные формы материал или деталь для последующей обработки, болванка для работы
олучаемые литьем (отливки);
получаемые обработкой давлением (кованые и штампованные заготовки);
заготовки из проката (получаемые отрезкой);
сварные и комбинированные заготовки;
получаемые методами порошковой металлургии.
Заготовка может быть штучной (мерной) или непрерывной, например пруток горячекатаного проката, из которого разрезкой могут быть получены отдельные штучные заготовки.
Заготовки получают также из конструкционной керамики.
Литьем получают заготовки фактически любых размеров простой и очень сложной конфигурации почти из всех металлов и сплавов, а также и из других материалов (пластмассы, керамики и т.д.). Качество отливки зависит от условий кристаллизации металла в форме, определяемых способом литья. В некоторых случаях внутри стенок отливок возможно образование дефектов (усадочные рыхлоты, пористость, трещины, получающиеся в горячем или холодном состоянии), которые часто обнаруживаются только после черновой механической обработки.
Обработкой металлов давлением получают кованые и штампованные заготовки. Ковка применяется в единичном и мелкосерийном производстве, а также при изготовлении крупных, уникальных заготовок и заготовок с особо высокими требованиями к объемным свойствам материала. Штамповка позволяет получить заготовки близкие по конфигурации к готовой детали. Механические свойства заготовок, полученных обработкой давлением, выше, чем литых.
|
|
Сварные и комбинированные заготовки изготовляют из отдельных составных элементов, соединяемых между собой с помощью различных способов сварки. Неправильная конструкция заготовки или неверная технология сварки могут привести к дефектам (коробление, пористость, внутренние напряжения), которые трудно исправить механической обработкой.
Заготовки, получаемые методами порошковой металлургии, по форме и размерам могут соответствовать готовым деталям и требуют незначительной, часто только отделочной обработки.
Заготовки из конструкционной керамики применяют для теплонапряженных и (или) работающих в агрессивных средах деталей.
Поступающие на обработку заготовки подвергают техническому контролю по соответствующей инструкции, устанавливающей метод контроля, периодичность, количество проверяемых заготовок в процентах к выпуску и т.д.
У заготовок сложной конфигурации с отверстиями и внутренними полостями (типа корпусных деталей) в заготовительном цехе проверяют размеры и расположение поверхностей. Для этого заготовку устанавливают на станке, используя ее технологические базы, имитируя схему установки, принятую для первой операции обработки. Отклонения размеров и формы поверхностей должны соответствовать требованиям чертежа заготовки. Заготовки должны быть выполнены из материала, указанного на чертеже, обладать соответствующими ему механическими свойствами, не должны иметь внутренних дефектов (для отливок — рыхлоты, раковины, посторонние включения; для поковок — пористость и расслоения, трещины по шлаковым включениям, «шиферный» излом, крупнозернистость, шлаковые включения; для сварных конструкций — непровар, пористость металла шва, шлаковые включения).
|
|
Дефекты, влияющие на прочность и внешний вид заготовки, подлежат исправлению. В технических условиях должны быть указаны вид дефекта, его количественная характеристика и способы исправления (вырубка, заварка, пропитка различными химическими составами, правка).
Поверхности отливок должны быть чистыми и не должны иметь пригаров, спаев, ужимин, плен, намывов и механических повреждений. Заготовка должна быть очищена или обрублена, места подвода литниковой системы, заливы, заусенцы и другие дефекты должны быть зачищены, удалена окалина. Особенно тщательно должны быть очищены полости отливок. Необрабатываемые наружные поверхности заготовок при проверке по линейке не должны иметь отклонений от прямолинейности более заданных. Заготовки, у которых отклонение от прямолинейности оси (кривизна) влияет на качество и точность работы машины, подлежат обязательному естественному или искусственному старению согласно технологическому процессу, обеспечивающему снятие внутренних напряжений, и правке.
|
|
Отмеченные на чертеже заготовки базы для механической обработки должны служить исходными базами при изготовлении и проверке технологической оснастки (моделей и приспособлений), должны быть чистыми и гладкими, без заусенцев, остатков литников, прибылей, выпоров, литейных и штамповочных уклонов.
Виды заготовительных работ и их краткая характеристика. Подготовительные операции перед раскроем: предварительная очистка и обработка поверхности проката; правка листового, сортового и фасонного проката.
Заготовительные работы — это производство деталей воздуховодов для монтируемых систем вентиляции (СВ), систем кондиционирования воздуха (СКВ) и систем воздушного отопления (СВО). Номенклатура деталей воздуховодов для каждой системы индивидуальна и окончательно определяется в ходе монтажного проектирования. Деталь — часть целого (составная часть системы).
|
|
Различают следующие виды заготовительных предприятий:
— вентиляционный завод (ВЗ) как самостоятельное юридическое лицо;
— центральная заготовительная мастерская (ЦЗМ), как правило, на балансе монтажной фирмы;
— участковая заготовительная мастерская (УЗМ), как правило, на балансе монтажной фирмы. В УЗМ изготавливаются мелкие детали и подмеры по разовым заказам.
Поступающий на судостроительные заводы прокат, как правило, имеет местные бухтины и общую волнистость, величины которых часто превышают допустимые (до 3 мм/м и до 10 мм на всю длину проката). Это обусловлено неравномерным обжатием листов валками при их прокатке на металлургических заводах и последующим неравномерным охлаждением. Остаточные деформации прокат может получить и в процессе его транспортировки. Эти искривления вносят погрешности в изготовление деталей. Поэтому в КОЦ обработку проката начинают с предварительной правки, которая заключается в создании в укороченных волокнах проката деформаций растяжения. Исходя из способа получения этих деформаций растяжения существуют способы правки изгибом и растяжением.
Правку изгибом выполняют в основном на валковых листоправильных машинах (рис. 4.2, а). Лист затягивается между двумя рядами валков силами трения и многократно изгибается. В результате изгиба укороченные волокна растягиваются. Число проходов зависит от исходного состояния проката и квалификации рабочего и не превышает пяти. Степень изгиба проката при правке определяется величиной зазора между нижними и верхними рабочими валками, который устанавливают перемещением верхней траверсы.
Передний направляющий валок обеспечивает ввод листа в вальцы, а задний — горизонтальность выходящего листа (рис. 4.2, а). Для правки листов толщиной свыше 6 мм обычно применяют 5- или 7-валковые машины, для меньших толщин — 9-11-валковые. В отдельных случаях предварительную правку листов можно выполнять в листогибочных вальцах и на прессах.
Правку растяжением выполняют на правильно-растяжных машинах.Она возможна для материалов сотношениемσв/σт. Большинство судостроительных сталей удовлетворяет этому условию. Прокат 6 закрепляют по торцевым кромкам в зажимных губках машины 7 (рис.4.2, б). Под действием гидравлического давления они растягивают прокат (на 1-2 %), устраняя практически все искривления за одно приложение нагрузки. Производительность труда по сравнению с правкой в валковых машинах возрастает в 6-8 раз. Основной недостаток способа — это повреждение поверхности проката насечкой от зажимных губок, что требует отрезки проката длиной до 300 мм.
Профильный прокат правят в основном на горизонтально-гибочных прессах, а также на роликовых правильных и растяжных машинах, гидравлических гибочных прессах. Для профильного проката допускается местная волнистость до 2 мм/м, но не более 8 мм на всю длину.
Прокат, поступающий на судостроительный завод, обычно покрыт слоем окалины и ржавчины, а также имеет другие загрязнения. Для последующей обработки его необходимо очистить и покрыть антикоррозионным составом, защищающим металл на весь межоперационный период. Основной способ очистки проката толщиной свыше 4 мм — механический. Для проката меньшей толщины применяют химическую очистку.
Механическую очистку дробеметным способом выполняют обычно в составе поточной линии, включающей также сушку и нанесение антикоррозионного покрытия. Существуют линии с вертикальным и горизонтальным положением листа в процессе очистки. Схема типовой линии дана на рис. 4.3. Подача проката на линию осуществляется перегружателями или кранами.
В камере предварительной сушки прокат нагревают газовыми горелками до 70—80 °С. Жировые загрязнения при этом сгорают. Нагрев ослабляет и связь окалины с основным металлом, так как они имеют разные коэффициенты линейного расширения, ускоряется и последующая сушка антикоррозионного покрытия.
В дробеметной камере на поверхность листа выбрасывается из дробеметных аппаратов со скоростью до 80 м/с чугунная или стальная дробь диаметром 0,5—2,5 мм. Сбиваемые окалина, ржавчина и дробь далее попадают в сепаратор, откуда дробь поступает для повторного использования, а мелкие частицы отсасывают воздухом и удаляют.
В окрасочной камере на прокат наносят антикоррозионное покрытие. В основном применяют двухслойное покрытие фосфатирующими грунтами типа ВЛ-02 и ВЛ-023, защищающими металл в течение 8 месяцев. При однослойном грунте ВЛ-023 металл защищен на срок до 3 месяцев.
Поточные линии с горизонтальным расположением листа можно использовать для обработки и профильного проката. Скорость движения проката на отечественных линиях 1—3 м/мин,а годовая производительность 200—300 тыс. м. Для профильного проката имеются и специальные линии.
Химическую очистку листов выполняют травлением в 15—20%-м растворе соляной или серной кислоты в течение 1—3 ч в зависимости от марки проката и состояния его поверхности. После травления осуществляют промывку в холодной воде, нейтрализацию в 3—5%-м растворе кальцинированной соды в течение 3—5 мин, и окончательную промывку в воде. На очищенный прокат наносят фосфатирующий раствор «Мажеф» и после его сушки — раствор олифы в уайт-спирите. Такое покрытие защищает металл на срок до 3 месяцев. По сравнению с механической химическая очистка имеет ряд недостатков: тяжелые условия труда, невозможность организации поточной линии, трудности с утилизацией отходов, поэтому широкого распространения она не получила.
Дата добавления: 2018-08-06; просмотров: 876; Мы поможем в написании вашей работы! |
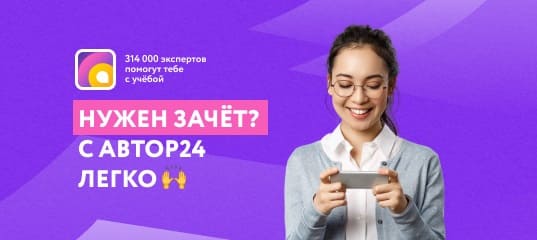
Мы поможем в написании ваших работ!