Технологическая схема кормоцеха для свиноводческой фермы с законченным производственным циклом на 3000 голов типовой проект № 802-117) 7 страница
Технологическое оборудование кормоцехов должно обеспечивать измельчение концентрированных кормов до размеров частиц 0,2 – 1,0 мм. При любой степени дробления качество концентрированных кормов считается выше, чем меньше в нем пылевидного продукта. Последний всегда вызывает большие потери вследствие распыла, налипания на рабочие органы кормораздатчиков, кормушек, плохого смачивания водой и образования комочков. При измельчении сена в муку для свиней размеры частиц должны быть в пределах 0,2 – 2,0 мм. Не рекомендуется хранить сенную муку в открытых бункерах более трех суток.
Сочные корма и силос необходимо измельчать до состояния пасты или мелкой резки. В измельченной массе 70 – 75% частиц должны быть размером до 10 мм, а частиц крупнее 10 мм не должно быть более 30%. Наличие частиц размером более 20 мм не допускается. Измельчать корнеплоды нужно только перед скармливанием или в процессе приготовления кормовой смеси, так как в измельченном виде они быстро окисляются, теряют сок, чернеют и покрываются плесенью. Картофель надо мыть, запаривать и мять до состояния пюре. Допускается измельчение запаренного картофеля до частиц размером 10 мм в количестве 7% по массе. Максимальный размер частиц не должен превышать 20 мм. При дозированной подаче компонентов в смеситель отклонение от заданной нормы для комбикормов должно быть не более ±5%, для сочных кормов – ±15%, для добавок – ±1%. Показатель степени однородности кормовой смеси должен быть не менее 90%. Влажность готовых кормовых смесей должна составлять 70 – 75%.
|
|
6.2. Выбор и обоснование технологической схемы обработки кормов
В условиях Нечерноземной зоны России, Беларуси и Прибалтийских государств в рацион для кормления свиней включают концентраты, корнеклубнеплоды, травяную муку, зеленую массу бобовых культур, белковые и минеральные добавки. При откорме свиней широко используются и пищевые отходы от частного и общественного секторов питания.
Выбор основного оборудования для кормоцеха следует начинать с разработки технологических схем переработки всех видов кормов, входящих в рационы различных половозрастных групп свиней, и определения суточной, разовой и часовой производительности отдельных линий и кормоцеха в целом.
Технологические схемы обработки, приготовления и раздачи кормов проектируют с учетом экономической эффективности, определяемой конкретными условиями хозяйств, типом кормления и составом рационов, взаимным расположением основных и вспомогательных помещений на ферме, их количеством, местом и порядком кормления животных, системой их содержания, конструкцией технологического оборудования, принятого для обработки кормов, внутренней планировкой помещений и другими факторами.
|
|
После определения марочного и количественного состава основного оборудования разрабатываются диаграммы технологического процесса приготовления кормов и выбор вспомогательного оборудования для всех технологических линий кормоцеха.
Можно использовать следующие технологические схемы приготовления корнеклубнеплодов:
1) мойка – отделение камней – измельчение – дозирование –смешивание;
2) мойка – отделение камней – запаривание (варка) – разминание – дозирование – смешивание;
3) мойка – отделение камней – измельчение – дозирование – дрожжевание–дозирование жидких дрожжей – смешивание.
Приготовление концентрированных кормов следует проектировать по следующим схемам:
1) очистка – измельчение – дозирование – смешивание;
2) очистка – измельчение – дозирование – дрожжевание – дозирование – смешивание;
3) очистка – дозирование – смешивание;
4) очистка – измельчение – дозирование – смешивание–гранулирование.
Первую и вторую схемы рекомендуется использовать при переработке фуражного зерна в комбикорм, а четвертую – при производстве в хозяйстве гранулированных комбикормов.
|
|
Пищевые отходы скармливают по следующей схеме: измельчение (на специальных дробилках) – отделение непищевых отходов – запаривание – охлаждение – дозирование – смешивание.
При отсутствии в хозяйстве витаминной травяной муки в кормоцехе готовят сенную муку по схеме: измельчение – дозирование – смешивание.
6.3. Определение производительности технологических линий приготовления кормов и потребности в основных машинах
и оборудовании
Для расчета производительности технологических линий кормоцеха необходимо знать структуру поголовья, рационы, тип кормления и способ содержания свиней на ферме, физико-механические свойства кормов и технические характеристики машин и оборудования, выпускаемых промышленностью.
Расчет технологических линий выполняется по каждому виду корма в отдельности. Для расчета выбирают такой период года, когда суточный объем кормов, подлежащих обработке, максимальный.
Максимальный суточный расход отдельных видов кормов и годовую потребность комплекса в них определяют по формулам (14) и (15).
Нормы суточной потребности в кормах на голову животных приведены в табл. 3 [14].
Суточный расход кормов на все поголовье свиней определяют по формуле
|
|
(20)
При проектировании кормоцеха свиноводческой фермы необходимо определить производительность технологической линии смешивания кормов, а также установив по принятому распорядку дня работы кормоцеха время приготовления и раздачи кормов, число смесителей, их тип и режим работы технологической линии и кормоцеха в целом.
Поскольку влажность кормовой смеси при раздаче кормов оказывает существенное влияние на работу мобильных и стационарных кормораздатчиков и в значительной мере определяет необходимую часовую производительность линии смешивания, то необходимо сначала определить количество воды, которое следует добавить в смесь рациона для достижения заданной зоотехническими требованиями влажности корма.
Исходную влажность кормовой смеси компонентов рациона (без добавления воды) вычисляют по формуле
(21)
где W1, W2, W3, – влажность отдельных компонентов рациона, %. При расчетах следует принять влажность концентрированных кормов 14, корнеклубнеплодов – 75 – 82, силосованного картофеля – 75, зеленой массы – 80, травяной сенной муки – 12 – 16, обрата – 91%.
Влажность кормовой смеси следует принимать 60 – 70% при раздаче мобильными кормораздатчиками и 70 – 80% – при использовании трубопроводного транспорта.
Количество воды, которое необходимо добавить в смесь для получения заданной влажности корма, определяют по формуле
, (22)
где Wз – заданная влажность, %.
Суточная производительность линии смешивания с учетом добавляемой воды в кормосмесь составит:
Qсм.сут = Qсут + Qв. (23)
Количество кормосмеси, которое необходимо приготовить для разовой выдачи животным, определяют с учетом принятой кратности кормления:
(24)
где Кк – кратность кормления животных в течение суток, равная 2; 3.
В зависимости от распорядка дня фермы (комплекса) устанавливают время на подготовку корма для разовой выдачи (для одного кормления):
(25)
где Tсм – продолжительность смены, ч;
h – число рабочих смен (h = 1; 2).
Требуемая производительность технологических линий обработки и подачи компонентов кормосмеси
(26)
приготовления и выдачи готовой смеси
(27)
где Киф – коэффициент использования фонда рабочего времени машины.
Значение Киф находят по следующей формуле
(28)
где – внецикловые простои машины за смену по i-м причинам.
К внецикловым потерям времени работы машин (агрегатов) относятся потери времени на устранение отказов по техническим и технологическим причинам вследствие планового ремонта общефермских устройств, проведения ежедневного и периодического технического обслуживания, по организационным и прочим причинам.
При вероятности подготовки требуемого количества корма F = 0,94 – 0,95 к установленному времени кормления Траз = 90 – 120 мин коэффициент использования фонда рабочего времени Киф = 0,87 – 0,78, при Траз = 120 – 360 мин и не увеличении простоев по техническим и технологическим причинам при работе кормоцеха по схеме с нагруженным резервированием (отказ некоторого числа технологических линий обработки и подачи компонентов готовой продукции не может рассматриваться как отказ системы в пределах зоотехнических требований) Киф = 0,78 – 0,5 и менее.
Во всех случаях оборудование кормоцеха должно обеспечивать фактическую производительность не меньше требуемой:
qфi ³ qтрi , qф ³ qтр.
Число машин для операции с непрерывным рабочим процессом в i‑й технологической линии определяют по формуле
nм = qтрi : qтi, (29)
где qтi – теоретическая производительность выбираемой машины по ее технической характеристике, т/ч.
Число машин nL для операции с периодическим рабочим процессом
, (30)
где Qi – количество корма i-го вида, проходящего обработку в машине (агрегате) за сутки, т;
gi – объемная масса i-го корма (табл. 17), т/м3;
n – количество видов кормов, обрабатываемых в машине;
V – рабочий объем машины (агрегата) по ее технической характеристике (для смесителей см. приложение 4), м3;
j – коэффициент заполнения объема, равный 0,80 – 0,85;
Кц– число циклов обработки корма одной машиной (агрегатом) за сутки.
Значение Кц находят по формуле
(31)
где Тц – время одного цикла, ч.
Значение Тц находят по формуле
Тц = tз + tраб + tв, (32)
где tз и tв – время загрузки и выгрузки машины, ч;
tраб – время выполнения основной технологической операции, ч.
Требуемую часовую производительность вспомогательных технологических линий кормоцеха можно вычислить по формуле
qтрi = p·qтр.см /100, (33)
где p – содержание компонента в кормосмесях, %.
Краткая характеристика машин для свиноводческих ферм приведена в приложении 4. После расчета и выбора основного оборудования кормоцеха составляют структурные схемы обработки кормов, определяющие последовательность выполнения технологических операций в кормоцехе. В соответствии с этими схемами выбирают вспомогательное оборудование кормоцеха: транспортеры, шнеки, бункера, дозаторы, парообразователи, средства автоматизации и т. д.
Таблица 17. Объемная масса, углы естественного откоса и коэффициенты трения для различных видов кормов
Корм | Влажность, % | Объемная масса, т/м3 | Угол естественного откоса в движении, град | Коэффициент трения, по металлу |
Комбикорм | 10 – 15 | 0,45 – 0,58 | 31,0 | 0,46 – 0,52 |
Сахарная свекла | 75 – 85 | 0,58 – 0,80 | 30,0 | 0,62 – 0,92 |
Кукурузный силос | 75 – 80 | 0,28 – 0,50 | 45 – 55 | 0,52 – 0,64 |
Сенаж | 42 – 55 | 0,15 – 0,27 | 45 – 50 | 0,45 –0,52 |
Зеленая масса (тимофеевка, люцерна) | 64 – 80 | 0,20 – 0,40 | 49,0 | 0,60 – 0,72 |
Картофель | 75 – 80 | 0,65 – 0,75 | 25,0 | 0,78 – 1,0 |
Сенная мука | 16 | 0,15 – 0,18 | 48,0 | 0,65 |
Морковь | 87,3 – 88,4 | 0,55 – 0,60 | 37,0 | 0,69 – 1,15 |
Кукуруза | 17 – 18 | 0,73 – 0,75 | 28,0 | 0,37 1 |
Пшеница | 17 – 18 | 0,67 – 0,83 | 25,0 | 0,37 |
Рожь | 17 – 18 | 0,65 – 0,79 | 26,0 | 0,47 |
Ячмень | 17 – 18 | 0,55 – 0,75 | 27,5 | 0,37 |
Овес | 17 | 0,40 – 0,51 | 27,5 | 0,37 |
Один из вариантов структурных схем основных технологических линий обработки кормов показан на рис. 2, а технологические схемы работы кормоцехов изображены на рис. 3 и в приложениях 21 – 31. Количество приемных бункеров, бункеров-накопителей, питателей-дозаторов должно соответствовать виду и количеству корма, который хранится и перерабатывается в кормоцехе. Минимальная вместимость приемных бункеров различных кормов должна быть не меньше грузоподъемности одной транспортной единицы, используемой в хозяйстве для доставки кормов из хранилищ, или кратна ей. Она определятся по формуле
Vб = Gтр/gb, (34)
где Gтр – грузоподъемность транспортной единицы, доставляющей корма, т;
g – объемная масса корма, т/м3;
b – коэффициент заполнения бункера, равный 0,8 – 0,9.
Вместимость бункеров для концентратов должна быть рассчитана не менее чем на трехсуточную норму их расходования, что исключает работу складов и транспорта в выходные и праздничные дни. Она вычисляется по формуле
Vк = Qк · tд/gb, (35)
где Qк – суточный расход концентратов, т;
tд – число дней хранения компонентов в бункере.
Производительность транспортирующих устройств для подачи концентрированных кормов, травяной муки, обрата и воды в смеситель должна быть взаимоувязана с производительностью основных машин других технологических линий. Можно принять для расчета транспортирующих устройств названных линий такую их производительность, чтобы на подачу каждого компонента затрачивалось не больше времени, чем на подачу картофеля или зеленой массы.
Время подачи запаренного картофеля в смеситель вычисляется по формуле
Тк = Qзап.карт/Qвыг.шн, (36)
где Qзап.карт – масса запаренного картофеля, загружаемого в смеситель для приготовления смеси за один цикл работы смесителя, т/ч;
Qвыг.шн – производительность выгрузного шнека, т/ч.
Для запарников корнеклубнеплодов ЗПК-4 и АЗК-3 производительность выгрузного шнека соответственно равна 6 и 10 т/ч.
Массу компонентов рациона, загружаемых в смеситель за один цикл его работы, определяют по формуле
Qi = p · V · gсм /100, (37)
где V – рабочий объем выбранного смесителя, м3;
gсм – объемная масса смеси при ее заданной влажности, т/м3;
p – содержание компонента в кормосмеси, %.
Объемную массу кормовой смеси находят по следующей формуле:
gсм = (Q1g1 + Q2g2 +…+ Qngn)/(Q1 + Q2 +…+ Qn), (38)
где g1 , g2,…,gn – объемная масса компонентов смеси, кг/м3;
Q1, Q2,…,Qn – масса соответствующего компонента, кг.
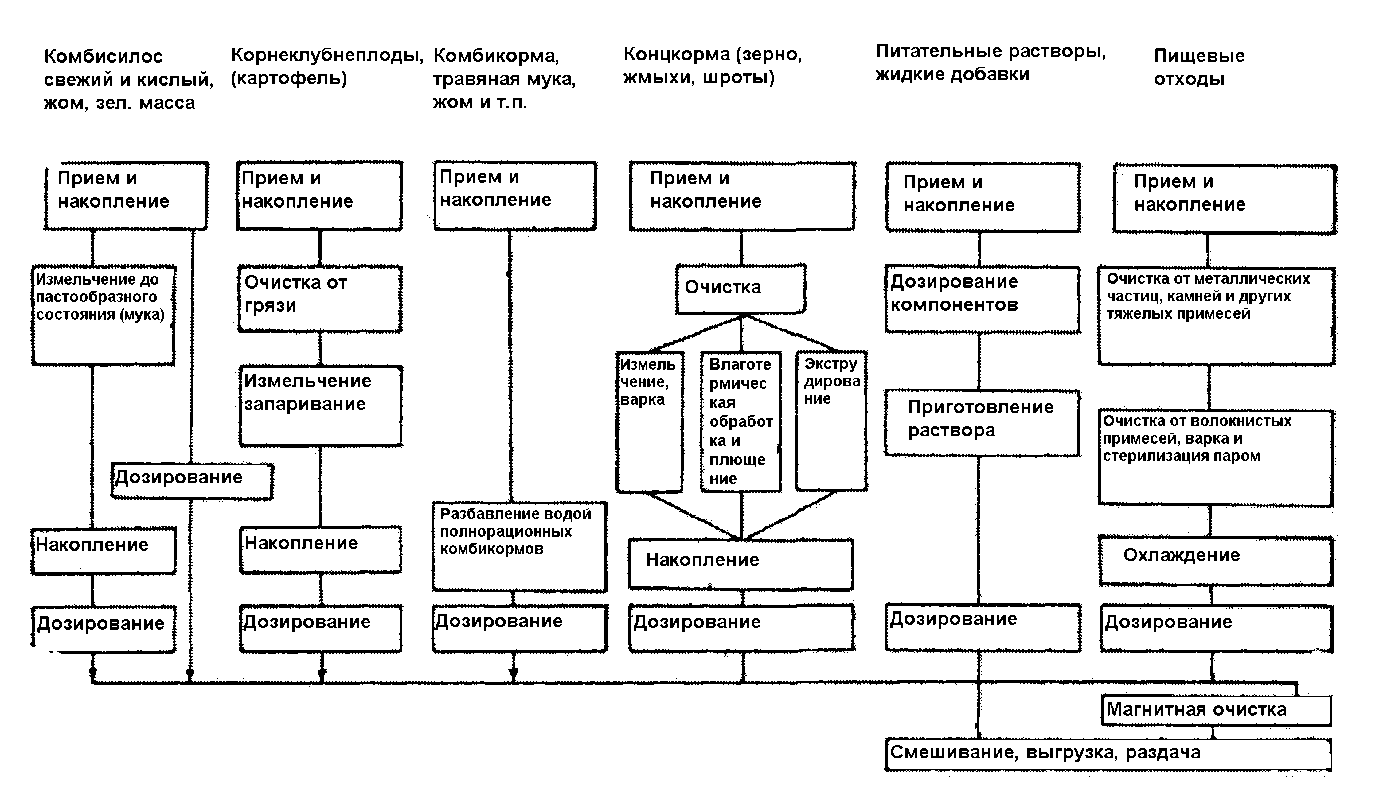
Рис. 2. Структурная схема основных технологических линий, применяемых в кормоцехах по приготовлению влажных кормовых смесей для свиней.
Рис. 3. Технологическая схема кормоцеха КЦС-12 (т. п. № 802-6-2) (картофельно-концентратный тип кормления): 1 – автомобилеразгрузчик ГАП-2Ц; 2 – бункер концкормов; 3, 4 – транспортеры; 5 – бункер-накопитель; 6 – шнековый транспортер; 7 – нория; 8, 9 – перекидные клапаны; 10 – весовой дозатор; 11, 12 – шнеки; 13 – запарник картофеля ЗПК-4; 14 – транспортер корнеклубнеплодов ТК-5Б; 15 – смеситель С-12;
16 – перекидной клапан; 17 – транспортер ТСН-2,0 для удаления камней и грязи;
Дата добавления: 2018-08-06; просмотров: 330; Мы поможем в написании вашей работы! |
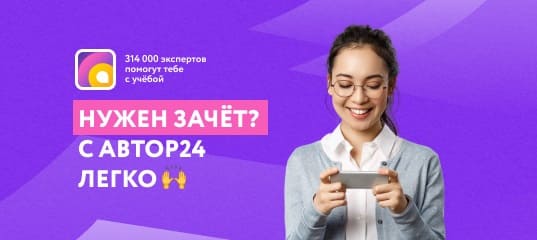
Мы поможем в написании ваших работ!