Показатели технического уровня и надежности станков: жесткость,износостойкость, стойкость к тепловым воздействиям, виброустойчивость, энергетическая характеристика.
Жёсткостью узла называется его способность сопротивляться появлению по осям координат упругих смещений под действием нагрузки.Деформации бывают следующих видов: деформация узлов деталей, деформация станков, контактная деформация, деформация тонких тел.
Износостойкость. В результате постепенного изменения поверхностей трения при взаимодействии двух сопряженных деталей происходит их изнашивание, т.е. уменьшение размеров и изменение формы деталей. По статистике большинство деталей машин выходит из строя из-за износа. При изнашивании в миниатюре происходят пластические и упругие деформации, сдвиг, усталостные разрушения материала деталей.
Диаграмма вставить
Стойкость к тепловым воздействиям. Работа станка сопровождается тепловыделением, вызываемым процессом резания и трением в механизмах. В результате теплового воздействия возникают тепловые деформации, отрицательно влияющие на работоспособность станка. Так, понижается защитная способность масляного слоя в трущихся поверхностях и, следовательно, увеличивается их износ или происходит заедание; изменяются зазоры в подвижных соединениях; нарушается точность обработки, например в результате нагрева передней опоры шпинделя его ось может отклониться, что приведет к снижению точности.
Применяют следующие методы борьбы с тепловыми деформациями технологического оборудования:
1)вынос узлов и механизмов с повышенным тепловыделением (например, гидростанций и гидросистем) за пределы станка;
|
|
2)использование в зоне резания смазочно-охлаждающей жидкости (СОЖ);
3)принудительное охлаждение узлов;
4)создание термоконстантных цехов, в которых поддерживается постоянная температура;
Виброустойчивость. Под виброустойчивостью понимают способность конструкций работать в заданном диапазоне режимов обработки без недопустимых колебаний отдельных узлов и станка в целом. В связи с увеличением скоростей резания и быстрых ходов колебания становятся все более опасными. Если частота собственных колебаний узлов станка совпадет с частотой вынужденных колебаний, наступает резонанс и станок может разрушиться.
Колебания могут возникать по следующим признакам:
1) Дисбаланс вращающих деталей
2) Ошибки в изготовлении зубчатых колёс
3) Внешние источники колебаний и другие.
Энергетическая характеристика. Один из параметров определяющих данную характеристику технологическое оборудование является коэффициент полезного действия. Для станков определяют КПД главного привода и КПД станка в целом. Коэффициент главного привода рассчитывают по формуле: полезная мощность/общая затрачиваемая мощность.
|
|
Передачи, применяемые в станках.
Передачи вращательного движения. Для изменения частоты вращения от ведущего звена к ведущему применяют ременные,зубчатые и червячные передачи.
Отношение частоты вращения ведомого (n1) к частоте вращения ведущего (n2) звена называется передаточным отношением. L=n1/n2.
Ременная передача применяется для передачи вращательного движения между удаленными друг от друга валами.
Зубчатая передача - механизм, который с помощью зубчатого зацепления передает и преобразует движение (без проскальзывания) с изменением угловых скоростей и моментов.
Червячная передача состоит из червяка и червячного колеса.
Преимуществами червячной передачи являются компактность, бесшумность, плавность хода, возможность большого редуцирования, к недостаткам передач относится малый КПД.
Передачи поступательного движения. Эти передачи служат для преобразования вращательного движения в прямолинейное поступательное рабочего органа. В станках применяют реечные передачи, винтовые пары, кулисные, кулачковые механизмы и др.
Реечная передача служит для преобразования вращательного движения реечного-колеса в поступательное перемещение рейки и наоборот. Реечная передача может быть выполнена с прямозубым и косозубым зацеплением колеса с рейкой.
|
|
Реечные передачи используют в металлорежущих станках, например в токарных, для осуществления движения продольной подачи суппорта с резцом относительно обрабатываемой заготовки.
Винтовая передана, применяется в тех случаях, когда нужно получить движение с малыми скоростями. Вращение сообщается винту; гайка и связанные с нею стол или салазки перемещаются прямолинейно-поступательно.
Кривошипно-кулисные механизмы (сокращённо – кулисные механизмы) с возвращающейся кулисой применяются в долбёжных станках, а с касающейся кулисой – в попе-речно-строгальных станках. Кулисные механизмы обеспечивают большую скорость при обратном холостом ходе и плавность движения.
Механизмы периодических движений. Для некоторых станков требуется периодически изменять положение его элементов или отдельных узлов. С этой целью используют храповые и мальтийские механизмы, неполные зубчатые колеса, кулачковые механизмы и механизмы с муфтами обгона, электро-, пневмо- и гидромеханизмы.
Муфты
Для соединения двух соосных валов в станках применяют муфты различных типов.
|
|
Нерасцепляемые муфты служат для жесткого соединения валов.
Рисунок.
Сцепляемые муфты применяются для периодического соединения валов.
Рисунок
Фрикционные муфты, их можно включать при любых скоростях вращения ведущего и ведомого элементов.
Рисунок
Магнитные
Рисунок.
Тормозные устройства
Для остановки или замедления движения подвижных узлов или отдельных элементов станков используют тормозные устройства. Торможение может осуществляться механическими, электрическими, гидравлическими, пневматическими или комбинированными средствами. В станках, не имеющих гидро- или пневмо- привода, применяют механическое или электрическое торможение.
Рисунок
Многодисковый тормоз представляет собой обычную многодисковую муфту, корпус которой жестко закреплен на неподвижной части станка. Привод тормозов на универсальных станках обычно ручной. На автоматизированных станках привод тормозов управляется дистанционно по программе.
Тормоза устанавливают на быстроходных валах коробок скоростей. При необходимости их блокируют с пусковыми муфтами.
Механизмы реверса
Реверсирование направления вращательного или поступательного движения рабочего органа станка осуществляется с помощью механических, электротехнических или гидравлических устройств. В качестве элементарных реверсирующих механических устройств используют в основном цилиндрические, конические и зубчатые передачи. Электрическое реверсирование осуществляется путём изменения направления вращения вала электродвигателя привода; реверсирования гидравлических устройств путём изменения гидроусилителя рабочей жидкости.
Коробки скоростей
Коробка скоростей структурно входит в привод ступенчатого регулирование главного движения станка. Привод станка - это совокупность источников энергии и передающих устройств, его назначение приводить в движение рабочие органы станка несущие заготовку или инструмент, обеспечивая приэто этом необходимые скорости и передавая требуемые усилия.
Коробки скоростей обеспечивают:
· большой диапазон регулирования скоростей на выходе
· отсутствие проскальзывания;
· передачу постоянной мощности;
· достаточно большое число различных скоростей на выходе при относительно небольших размерах самих коробок скоростей;
· передачу больших крутящих моментов;
· высокий КПД
Коробки скоростей станка состоят из двух валовых передач, которые могут передавать ведомому валу II несколько различных скоростей.
По способу переключения скоростей коробки скоростей бывают:
· со сменными зубчатыми колесами.Они имеют малые габаритные размеры, исключают возможность аварийного включения передач.
· с передвижными блоками зубчатых колес и муфтами.получившие широкое распространение преимущественно в универсальных станках с ручным управлением.В станках с ЧПУ применяют зубчатые передачи, переключаемые автоматически с помощью индивидуальных электромеханических (реже гидравлических) приводов.
По компоновке различают коробки скоростей с неразделенным и разделенным приводом. В первом случае коробка скоростей расположена в шпиндельной бабке, а во втором — вынесена за ее пределы.
Коробки подач
Коробки подач в металлорежущих станках предназначены для изменения величины и направления подачи переключением зубчатых колёс.
Конусный набор с накидным зубчатым колесом применяют в приводах токарно-винторезных станов с винтовым управлением.
Преимущество этой передачи малое металлоемкость. Однако из-за наличия накидного зубчатого колеса конусный набор не может быть использован в станках передающих большие мощности, так как механизм имеет низкую жёсткость.
Конусный набор с вытяжной шпонкой - компактный механизм размещающих до 10 различных передаточных отношений.
Гитара – это звено настройки кинематической цепи с помощью слепых зубчатых колёс; применяется в различных кинематических цепях: коробках скоростей, подач, особенно в серийном и массовом производствах.
Дата добавления: 2018-08-06; просмотров: 804; Мы поможем в написании вашей работы! |
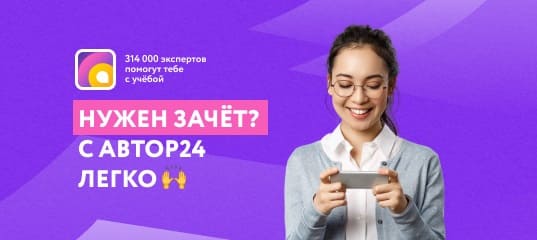
Мы поможем в написании ваших работ!