Показатели технического уровня и надежности станков: производительность, прочность, точность.
Оглавление
1. Классификация металлорежущих станков. 1
2. Размеры ряда станков. 2
3. Движения в станках. 3
4. Управление станком.. 5
5. Показатели технического уровня и надежности станков: производительность, прочность, точность. 7
6. Показатели технического уровня и надежности станков: жесткость, износостойкость, стойкость к тепловым воздействиям, вибро устойчивость, энергетическая характеристика. 8
7. Передачи, применяемые в станках. 9
8. Муфты.. 10
9. Тормозные устройства. 11
10. Механизмы реверса. 11
11. Коробки скоростей. 11
12. Коробки подач. 12
13. Электрооборудование и элементы систем управления станками. 13
14. Мехатронные узлы.. 13
15. Системы смазывания и охлаждения. 14
16. Токарно-винторезный станок. Назначение, принцип действия. 15
17. Токарные автоматы и полуавтоматы. Назначение, принцип действия. 16
18. Вертикально-сверлильный станок. Назначение, принцип действия. 17
19. Расточной станок. Назначение, принцип действия. 18
20. Координатно-расточные станки. Назначение и принцип действия. 19
21. Шлифовальные станки. Виды шлифовальных станков. 20
22. Зубодолбежные станки. Назначение, принцип действия. 20
23. Зубофрезерные станки. Назначение, принцип действия. 21
24. Резьбофрезерование. Фрезерование дисковой фрезой. 22
25. Резьбофрезерование. Фрезерование групповой фрезой. 22
26. Станки для нарезания резьбы метчиками. Назначение, принцип действия. 23
|
|
27. Станки для вихревого нарезания резьбы. Назначение, принцип действия. 24
28. Резьбошлифовальные станки. Назначение, принцип действия. 27
29. Фрезерные станки. Назначение, принцип действия. Виды. 27
30. Приспособления, расширяющие технологические возможности фрезерных станков. 28
31. Строгальные станки. Назначение, принцип действия. 29
32. Долбежные станки. Назначение, принцип действия. 30
33. Протяжные станки. Назначение, принцип действия. 31
34. Многоцелевые станки. Компоновка. Назначение, принцип действия. 31
35. Автоматическая смена инструмента в многоцелевых станках. 33
36. Мониторинг состояния инструмента и процесса обработки в многоцелевых станках. 35
37. Агрегатные станки. Виды, назначение, принцип действия. 36
38. Силовые головки агрегатных станков. 38
39. Силовые столы в агрегатных станках. Поворотные делительные столы. 39
40. Роботизированные технологические комплексы. Общие требования. 39
41. Конструкции типовых РТК. Виды РТК. 40
42. РТК сборочных операций. 40
43. Средства, обеспечивающие безопасность работы персонала в РТК. 41
44. Техническая документация металлорежущих станков. Транспортирование, установка на фундамент металлорежущих станков. 44
|
|
45. Испытания станков. Виды испытаний. 49
46. Перспективы использования информационных технологий при создании и эксплуатации обрабатывающего оборудования. 51
Классификация металлорежущих станков
Металлорежущий станок-это технологическая машина, предназначенная для материалов резанья с целью получения деталей заданной формы и размеров.
По виду выполнения работ метало резанья, станки разделены на 9 типов, объеденных по техническим и конструктивным признакам.
Токарные станка: автоматы и полуавтоматы (одношпиндельные и многошпиндельные), токарно-револьверные, карусельные, лобовые.
Сверлильные и расточные: настольные и вертикально сверлильные, полуавтоматы (одношпиндельные и многошпиндельные), координатно-расточные, радиально-сверлильные, горизонтально-расточные,горизонтально-сверлильные.
Зуба и резьба обрабатывающие: зубодолбежные, зубонарезные, зуба-фрезерные, резьбонарезные.
Фрезерные станки: вертикально-фрезерные, продольные одноточные, копировальные и гравировальные, фрезерные не прерывного действия, консольно-фрезерные операционные.
Строгательные долбёжные и протяжные: продольные, поперечно-строгательный, долбёжный,протяжные горизонтальные.
|
|
Для испытания инструментов: делительные машины, балансировочные машины
Первая цифра – указывает группу, вторая – номер типа станка, третья и четвертая – характеризует один из главных параметров станка или обрабатываемые на нём детали (высота центров, диаметр прутков, размер стола)
Буква после первой или второй цифры указывает, что станок модернизирован, а буква стоящая после цифр – модификацию базовой модели станка.Например: модель 7А36
7-строгательно-протяжная группа, 3- поперечно-строгательное, 6 максимум длина обрабатываемой детали 600 мм, А-указывает на модификацию станка базовой модели 736
Если буква стоит в конце обозначения модели, то она указывает на класс точности станка.Например:16КП20П-станок повышенного класса точности, нормальный класс не указывается.
ЧПУ-числовое программное управление-последние 2 знака-буква ф с цифрой. Например: зубофрезерный полуавтомат с комбинированной системой ЧПУ-модель 53А20Ф4. В конце обозначение модели и станков м цикловыми системами управления ставят «У», а с оперативным «Т» Наличие в станке инструментального магазина отображается обозначением модели буквой «М». Например:2350ПМФ2 –сверлильный станок с позиционной системой управления, повышенной точности, с магазином инструментов.
|
|
Например: 16К20Ф3 – токарно-винторезный станок (первые 2 цифры) с высотой центров 200 мм нормальной точности, Ф3 – числовое управление, 3 координатных движения по x, y, z.
По степени универсальности станки подразделяются на универсальные, специализированные и специальные. Специализированные станки применяют для обработки деталей одного наименования, но разных размеров. Специальные станки применяются для обработки деталей одного наименования и размера.
Станки подразделяют на 5 классов точности: н-нормальной, п-повышенной, в-высокой, с-мастер станка, а-особо высокой. В зависимости от массы станки подразделяются на лёгкие-до 1 кг, средние-до 10кг, тяжёлые более 10кг. Тяжёлые делятся на крупные-до30 т, тяжёлые до 100 т, уникальные свыше 100т. По степени автоматизации станки подразделяются на станки с ручным управлением, полуавтоматические, автоматические. По расположение шпинделя станки делятся на горизонтальные, вертикальные и наклонные. По концентрации операции станки делятся наоднопозиционные и многопозиционные. Концентрация операций - это сложно одновременной обработки заготовок на станке многими инструментами.
Размеры ряда станков
Для большинства станков стандартами установлены основные (главные) параметры, характеризующие размеры обрабатываемых деталей или размеры самого станка. Совокупность численных значений этих параметров (от наименьшего до наибольшего) образует размерный ряд станков одного типа, т.е. подобных по конструкции, кинематической схеме и внешнему виду.
Конструкция станков размерного ряда состоит в основном из унифицированных узлов, одинаковых или подобных, что облегчает конструирование, изготовление и эксплуатацию станков, а также способствует удешевлению их производства.
Размерные ряды металлорежущих станков основных технологических групп
Технологическая группа металлорежущих станков | Главный параметр | Пределы изменения главного Параметра станка, мм |
Токарно-винторезные, токарные и патронные станки | Наибольший диаметр изделия над станиной | 125...5000 |
Токарно-карусельные станки | Наибольший диаметр изделия | 1250... 20 000 |
Токарные многошпиндельные прутковые горизонтальные автоматы | Диаметр прутка | 12... 160 |
Вертикально-сверлильные станки | Наибольший условный диаметр отверстия при сверлении | 3...12 |
Координатно-расточные, сверлильно- фрезерно- станки | Ширина стола | 250... 2000 |
Сверлильно-фрезерные станки | Ширина стола | 200... 2000 |
Круглошлифовальные станки | Наибольший диаметр устанавливаемого изделия | 100... 800 |
Плоскошлифовальные станки | Ширина поверхности стола | 160... 800 |
Электроэрозионные вырезные станки | Длина вырезаемого контура | 160...800 |
Электрохимические копировально-прошивочные станки | Ширина стола | 200... 630 |
Зубофрезерные вертикальные полуавтоматы для обработки цилиндрических колес | Наибольший диаметр обрабатываемого зубчатого колеса | 80... 12500 |
Фрезерные широкоуниверсальные инструментальные станки | Ширина стола | 200... 800 |
Продольно-фрезерныестанки | Ширина стола | 500... 4500 |
Продольно-строгальные станки | Ширина изделия | 2000... 3150 |
При разработке размерных рядов учитывают, что необоснованное расширение номенклатуры выпускаемых станков, сходных по своему назначению, приводит к уменьшению серийности выпуска, возрастанию себестоимости изготовления станков и повышению расходов на их эксплуатацию.
Движения в станках
При изготовлении детали на станках инструмент или заготовка могут выполнять следующие движения: главное, подаче, деление, обкатки, дифференциальное и вспомогательное.
Главное движение резаньяDsnp обеспечивает снятие стружки заготовки с наибольшей скоростью резанья. Главное движение может быть вращательным и прямолинейным посткупальным. Это движение может совершать как заготовке, как и режущий инструмент.
Стандарт токарной группы главным движением является вращение заготовки (а-в). Чистоту вращения заготовки (n) определяют по формуле n=10^3v/пd, где v-скорость резанья,d-диаметр заготовки. В сверлильных, зубо-фрезерных, шлифовальных, фрезерных главное движение сообщается режущему инструменту (г-к). Частоту его вращения (n) рассчитывают по той же формуле только вместо диаметра заготовки подставляют диаметр режущего инструмента (сверла, фрезы и др.) У долбёжных, зубо-долбёжных, продольно строгательных, поперечно-строгательных и протяжных станков главное движение является возвратное поступательное прямолинейное движение. Иногда главное движение получают сложением или вычитанием двух вращательных движений. Например(м): Движение подачи Dns позволяет подвести под режущую кромку инструмента новые участки заготовки. Подачей (s) называется относительное отклонение расстояния пройденного рассматриваемойточкой режущей кромки вдоль траектории этой точки движение подачи. В зависимости от направления перемещения инструмента по отношению к заготовке различают движение подачи: продольное (а, г, ж), поперечное (б, д, з), тангенциальное (в), вертикальное (е. к), круговое (ж-к), осевое (м).
Главным движением и движением подачи в совокупности называют основное движение станка.
Движение деление реализует для осуществления необходимого углового перемещения заготовки относительно инструмента.
Движение обката-это согласованное движение режущего инструмента и заготовки воспроизводящее при формообразовании зацеплений определённой кинематической пары (получение зубчатых колёс).
Вспомогательное движение подготавливают процесс резанья, но сами в них не участвуют (подвод режущего инструмента к заготовке, переключения подачей станка, включение и выключения станка).
Управление станком
Под управлением станков понимают совокупность воздействий на его механизмы, обеспечивающие выполнение технологического цикла обработки. Система управления устройства или совокупность устройств реализующих воздействие управления станком. Цикл работы станка – это совокупность всех движений необходимых для обработки заготовок и выполняемых в определённой последовательности.
Циклы, осуществляемые при работе станочного оборудования делят на 2 группы. Первую группу образуют циклы, которые остаются неизменными и повторяются многократно в процессе эксплуатации оборудования. Например, циклы работы автоматических линий и агрегатных станков.
Ко второй группе относятся циклы, совершаемые однократно в определенные моменты. Эти циклы инициируются специальной командой. Примерами таких циклов являются циклы движений вспомогательных механизмов в станках: поиск и смена инструмента, зажим и освобождение подвижных узлов, загрузка и зажим заготовок, выгрузка обработанных деталей и так далее.
Управление станком может быть ручным или автоматическим.Автоматическое управление подразделяется на: кулачковое; с помощью регулируемых упоров; программное и адаптивное.
По виду различают цикловое и числовое программное управление.
Цикловым программным управлением (ЦПУ) называют управление обработки заготовки на станке под управляющей программе, в которой данные представлены в цифровой форме.
При составлении программ для обработки изделий на станках с ЧПУ необходимо правильно выбрать положительное направление осей координат станка и заготовки. На станках с ЧПУ принято правая система отсчёта координат. Начало выбирают произвольное.
Положительное направление движение рабочего органа соответствует направлению отвода инструмента заготовки. Положительным направлением рабочих органов несущих инструменты обозначают без штрихов, причём положительным направлением считает направление вращения против часовой стрелки.
Направлений движений рабочих органов несущих заготовку обозначаются буквами с штрихами.
В станах ось Z определяется по отношению к шпинделю обеспечивающие главное вращательно движение. При отсутствии шпинделя ось Zперпендикулярна к рабочей поверхности стола.
Ось X располагается горизонтально, параллельно поверхности закрепления заготовки.
После выбора осей Xи Z ось Y проставляется таким образом, чтобы образовалась правая система координат. Для этого глядя на конец оси Z необходимо повернуть ось X против часовой стрелки. Кодирование управляющих программ стандартизованно.
Показатели технического уровня и надежности станков: производительность, прочность, точность.
Каждый станок имеет определенные выходные параметры. К ним относятся: производительность, точность, прочность, жесткость, виброустойчивость, стойкость к тепловым воздействиям, износостойкость, надежность, показатели качества, экономические и энергетические показатели. Все они, вместе взятые, характеризуют технический уровень станка.
Производительность. Это основной критерий количественной оценки станочного оборудования. Производительность станка характеризуется числом деталей, изготовленных на нём в единицу времени, если например: на обработку одной детали затрачивается время (t), то производительность (Q) станка будет Q=1/t, измеряется в штук/мин, а если Nдеталей для металлорежущих станков различают:
Для металлорежущих станков различают:
1)идеальную (технологическую) производительность Qид= 1/tр, где tр — время резания;
2)цикловую производительность Qn = 1/(tp + tх), где tхх — время на холостые ходы;
3) фактическую (реальную) производительность Qф = 1/(tр + tхx + + tпр), где tпр — время, затрачиваемое на смену инструмента, его регулирование, ремонт механизмов станка и т.д., этот параметр называют прочими потерями времени, приходящимися на одну обработанную деталь.
Прочность. Расчеты на прочность деталей, выполняемые при проектировании станков, осуществляют по величинам допускаемых напряжений, коэффициентам запаса прочности или вероятности безотказной работы. Расчеты по допускаемым напряжениям наиболее просты и удобны, их используют для станков массового производства.
Точность. Для деталей машин понятие точности включает точность формы и размеров отдельных участков детали, а также точность взаимного положения этих участков.Точность обработки на станке будет в первую очередь зависеть от точности и шероховатости поверхностей деталей узлов станка. Однако при проектировании и изготовлении машин нужно учитывать и другие факторы, влияющие на ее точность.
Дата добавления: 2018-08-06; просмотров: 2009; Мы поможем в написании вашей работы! |
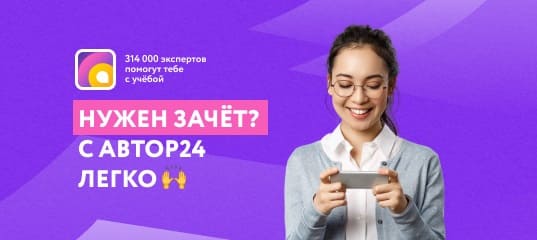
Мы поможем в написании ваших работ!