Определение первоначальной стоимости оборудования
Определяем транспортные расходы ( принимаем 10 % от общей стоимости основного оборудования ) ( руб.)
Sтр = Sобщ • 0.10 ( 1 ) [ 1 ]
где Sобщ - общая стоимость оборудования по спецификации.
Sтр = Sобщ • 0.1 = 0,1• 120000,00= 12000,00
3.2.2 Определяем стоимость оборудования с транспортными расходами (руб.)
Sоб = Sобщ + Sтр ( 2 ) [ 1 ]
Sоб = Sобщ + Sтр = 120000,00+12000,00=132000,00
3.2.3 Определяем стоимость строительно-монтажных работ . Принимаем 20 % от стоимости оборудования с транспортными расходами (руб.).
Sсм = Sоб • 0.2 ( 3 ) [ 1 ]
Sсм = Sоб • 0.2 = 0,2• 132000,00=26400,00
3.2.4 Определяем первоначальную стоимость оборудования
Sперв. = Sоб. + Sсм. ( 4 ) [ 1 ]
Sперв. = Sоб. + Sсм. = 26400,00+132000,00=158400,00
Данные заносим в таблицу.
Таблица 2 - Затраты на монтаж оборудования
наименование затрат | ед. изм. | сумма |
стоимость оборудования | руб. | 120 000,00 |
транспортные расходы | руб. | 12 000,00 |
стоимость оборудования с транспортными расходами | руб. | 132 000,00 |
стоимость строительно-монтажных работ | руб. | 26 400,00 |
первоначальная стоимость | 158 400,00 |
Расчет годового графика ППР
Расчет годового графика планово-предупредительного ремонта
Таблица 3 - Расчет годового графика планово- предупредительного ремонта
оборудование | периодичность | ремонта | продолжительность | ремонта | трудоемкость | ремонта |
Насос ЦНС-180 | КР | ТР | КР | ТР | КР | ТР |
8 640 | 5 040 | 1 080 | 360 | 1 440 | 48 |
3.3.1 Пробег оборудования ( Побор. ) на 01.01.2006 года составляет 6120 часов.
|
|
3.3.2 Определяем количество капитальных ремонтов оборудования
( 5 ) [ 1 ]
где Тк - календарный фонд рабочего времени = 8640 часов в год
Тц - периодичность капитальных ремонтов
3.3.3 Определяем межремонтный цикл - период времени, через который проводится капитальный ремонт оборудования
( 6 ) [ 1 ]
3.3.4 Определяем количество текущих ремонтов
( 7 ) [ 1 ]
где Тт - периодичность текущих ремонтов /час/
Принимаю для расчетов 1 раз в год текущий ремонт
3.3.5 Определяем месяц остановки оборудования на капитальный ремонт.
3.3.5.1. Число суток в месяц - 30.
3.3.5.2 Определяем месяц остановки оборудования на капитальный ремонт
(8 ) [ 1 ]
где Побор. - пробег оборудования после капитального ремонта
720 - количество часов в месяц
Пк.р. - периодичность капитального ремонта (час.)
Принимаю 4-ый месяц
Таблица 4 - Годовой график планово-предупредительных работ.
Наименование оборудования | График ремонтов | Периодичность капитального ремонта | Продолжительность капитального ремонта | Трудоемкость капитального ремонта | |||||||
январь | февраль | март | апрель | май | июнь | июль | август | сентябрь | октябрь | ноябрь | декабрь |
насос ЦНС - 180 | К | Т | 8 640 | 1 080 | 1 440 |
|
|
Узлы насоса ЦНС-180
Секционный корпус
Насос центробежный ЦНС-180 (рис.4.
Корпус такой конструкции представляет собой набор секций крышек всасывания и нагнетания соединенных между собой стяжными шпильками.
Крышки всасывания и нагнетания являются базовыми деталями насоса. В крышках выполнены соответственно приемный и напорный патрубки. Совместно с крышками отлиты опорные лапы, которыми насос фиксируется на фундаментной плите, и корытообразные кронштейны для подшипников. К крышкам на шпильках подсоединяются корпуса концевых уплотнений.
Секции крышки центрируются на цилиндрических заточках. Уплотнение стыков может осуществляться либо за счет металлического контакта уплотняющих поясков, либо при помощи специальных уплотнительных устройств. Чаще всего применяются уплотнительные кольца из круглого резинового шнура. Для горячеводных насосов (до 200° С) уплотнительные кольца изготовляются из термостойкой резины.
Конструкция стыка секций (рис.5) должна предупреждать возможность раскрытия его при действии внутреннего давления.
Наиболее простым является соединение с внешней заточкой. Соединение с «зубом» более устойчиво к раскрытию стыка, однако выполнение его затруднительно. При высоких давлениях в некоторых случаях применяют соединение с внутренней заточкой.
|
|
Для уменьшения расцентровки секций при сборках и разборках насоса соединение их производится обычно по напряженной посадке.
При уплотнении стыков секций за счет металлического контакта уплотняющие пояски должны быть строго перпендикулярными к оси насоса и иметь чистоту поверхности V 8 – V 9, которая, как правило, достигается притиркой специальными притирами вручную или на станках.
Рис.4. Насос центробежный ЦНС-180
рис.5.
Необходимое уплотняющее усилие создается стяжными шпильками. В горячеводных насосах стяжные шпильки должны также воспринимать усилия от температурных деформаций корпуса. Стяжные шпильки должны равномерно располагаться по окружности на минимально возможном диаметре. Не рекомендуется пропускать их через водопроводящие каналы.
Крышки насоса изготовляются либо литыми, либо сварнолитыми. Материал крышек выбирается в зависимости от внутреннего давления. Для давлений до 100 кг/см2крышки могут быть отлиты из серого чугуна, для более высоких давлений из углеродистой или малолегированной стали. В местах уплотнений секций на крышках может быть предусмотрена наплавка нержавеющими электродами для предупреждения размыва при возникновении неплотности в стыке.
|
|
Секции изготовляются литыми или коваными. Материал секций – чугун или углеродистая сталь. В особо ответственных насосах секции изготовляются из поковок нержавеющей стали.
Обратные подводящие каналы могут быть разделены с отводящими каналами безлопастным кольцевым пространством. Каналы диффузорных отводов могут быть выполнены в одной детали, а обратные подводящие каналы в другой сопрягаемой детали.
В некоторых конструкциях, чаще всего при неразборном роторе, приходится применять разъемные лопастные отводы. Обе половинки при сборке соединяются между собой с помощью стяжных шпилек или болтов. При разъемной конструкции лопастной отвод выполняется двух или четырехканальным. Для снижения потерь в лопастных отводах необходимо обеспечить высокую чистоту и точность диффузорных каналов, в которых скорости потока достигают максимальных величин.
Материал лопастных отводов выбирается из соображений прочности, литейных качеств, коррозионной и эрозионной стойкости. Для холодной нейтральной воды при средних скоростях потока применяется чугунное или стальное литье. Лопастные отводы, работающие на горячей воде или при высоких скоростях потока, отливаются из нержавеющей стали.
Стяжные шпильки
Стяжные шпильки являются одними из наиболее нагруженных деталей насоса.
Изготовляются они обычно из проката углеродистой стали 40 или 45. Сильно нагруженные шпильки могут изготовляться из стали 40Х или других легированных сталей (например, 30 ХМА). Коэффициент линейного расширения материала шпильки должен быть примерно равен коэффициенту линейного расширения материала корпуса. На шпильке рекомендуется предусмотреть направляющий поясок перед резьбой или среднюю часть ее выполнять большего диаметра по сравнению с диаметром резьбы. Это предохраняет резьбу от повреждений при затяжке длинных шпилек. Утолщенная средняя часть уменьшает также возможность скручивания шпильки при затяжке. Изготовлять шпильки из проката без проточки поверху нельзя. Обработка необходима для удаления поверхностного слоя, в котором часто встречаются дефекты.
Ротор в сборе
Рис.6.
Ротор многоступенчатого насоса (рис.6) представляет собой отдельный комплектный узел, состоящий из вала 2, рабочих колес 3, защитных втулок, разгрузочного диска 4 и других мелких деталей, закрепленных на валу
От правильного выбора конструкции и технологии изготовления ротора и отдельных его деталей в значительной степени зависит надежная работа насоса. Отсутствие вибрации в насосе из-за неуравновешенности ротора при его вращении является одним из основных условий нормальной работы насоса. Выполнение этого требования осуществляется за счет тщательной статической балансировки отдельных деталей ротора и динамической балансировки собранного ротора. Динамическая балансировка ротора производится на специальных станках, обычно при пониженной скорости вращения. При этом может оказаться, что отбалансированный ротор при работе с более высоким числом оборотов из-за возникновения дополнительных динамических прогибов может оказаться разбалансированным. В связи с этим роторы крупных многоступенчатых насосов рекомендуется балансировать при числе оборотов, близком к рабочему, иногда в собственных опорах на месте эксплуатации. Допустимая центробежная сила от неуравновешенного ротора не должна превышать
1–2% веса ротора.
Наиболее благоприятные условия для обеспечения уравновешенности создает так называемая неразборная конструкция ротора, при которой рабочие колеса посажены на вал с натягом. Тип посадки зависит от числа оборотов и температуры перекачиваемой жидкости и выбирается с таким расчетом, чтобы при работе не образовался зазор между валом и ступицей рабочего колеса под действием центробежных сил и температурного расширения. Сборка и разборка такого ротора, как правило, производится с подогревом рабочих колес. Вал ротора имеет ступенчатое уменьшение диаметров посадочных поверхности под колеса.
Неразборный ротор усложняет конструкцию, сборку и разборку многоступенчатого насоса. Поэтому он нашел распространение в насосах с числом оборотов более 3000 в минуту. При меньших оборотах преобладающее распространение получил разборный ротор, в котором рабочие колеса посажены на вал по скользящей или плотной посадке.
Рабочие колеса, разгрузочный диск и втулка насосов, работающих на холодной воде, в осевом направлении фиксируются на валу гайкой; в насосах, перекачивающих горячую воду, между комплектом рабочих колес и втулкой разгрузочного диска предусматривается торцовый зазор 0,5–1 мм для компенсации разности температурного расширения вала и рабочих колес.
При работе насоса через торцы ступиц рабочих колес на вал передается осевое усилие, достигающее десятков тонн. При неперпендикулярности торцов под действием осевого усилия вал может быть дополнительно изогнут, что может привести к разбалансировке ротора. Поэтому торцы рабочих колес обрабатываются с перпендикулярностью 0,01 – 0,02 мм при чистоте поверхности V7–V8. За счет плотного прилегания торцов исключается возможность перетока перекачиваемой жидкости по валу.
В собранном роторе должно быть проверено биение рабочих поверхностей, которые не должны превышать следующих величин в мм:
Уплотнения рабочих колес............................................... 0,05-0,08
Межступенные уплотнения............................................... 0,06–0,09
Втулки концевых уплотнений.......................................... 0,03–0,04
Торцовая поверхность разгрузочного диска ................. 0,02
Шейки вала под подшипники............................................ 0,01–0,02
Биение проверяется при отпущенных и затянутых гайках ротора. Изменение величины биения свидетельствует о неправильно выполненных торцах деталей.
Изготовление роторов высокооборотных насосов требует большой точности и тщательности. Однако применение высоких чисел оборотов приводит к уменьшению диаметра рабочих колес и числа ступеней, что не только способствует повышению надежности работы насоса, но и облегчает обработку ротора.
Вал
Вал является базовой деталью ротора, которая при работе насоса подвержена действию знакопеременной нагрузки. Максимальный диаметр вала выбирается в месте посадки рабочих колес, дальше к обоим концам происходит ступенчатое уменьшение диаметра для установки втулок и других деталей ротора. Посадочные размеры вала высоконапорных насосов выполняются по 2–3-му классу точности. Уступ вала для упора рабочих колес должен быть выполнен строго перпендикулярно оси насоса. Оси шпоночных пазов должны лежать в плоскости, проходящей через ось вала. В многоступенчатых насосах шпоночные пазы рекомендуется располагать поочередно с обеих сторон вала для уменьшения дисбаланса ротора.
Шейки вала под подшипники скольжения подвергаются поверхностной закалке. Для их обработки применяются доводочные операции: наружное хонингование или суперфинишная обработка.
В качестве заготовок для валов применяются прокат или поковки. Заготовки валов крупных насосов должны проходить дефектоскопию для выявления скрытых дефектов.
Для изготовления валов насоса, перекачивающих холодную воду, можно рекомендовать сталь 40, 45 или 40Х. Для орячее-водных насосов материал вала должен сохранять свои механические свойства при температуре перекачиваемой жидкости и иметь коэффициент линейного расширения, мало отличающийся от коэффициента линейного расширения материала других деталей ротора. Для валов питательных насосов широко применяется сталь40ХФА.
Валы насосов, перекачивающих агрессивные жидкости, могут изготовляться из обычных материалов, но с защитой вала втулками из коррозионностойкого материала.
Рабочие колеса
Рабочее колесо является основным органом насоса, в котором происходит преобразование механической энергии привода в гидравлическую энергию перекачиваемой жидкости. Проточная часть рабочего колеса определяется гидродинамическим расчетом, а высокие точность изготовления и чистота поверхностей являются важнейшим условием получения требуемых параметров. В высоконапорных насосах применяются рабочие колеса закрытого типа с покрывающим диском.
В большинстве случаев рабочие колеса литые.
В отдельных случаях применяют сварнолитые или сварнофрезерованные рабочие колеса.
Рабочие колеса многоступенчатых насосов (рис.7) изготовляются с удлиненной ступицей, что дает возможность избежать применения дистанционных втулок. Ступица отливается совместно с рабочим колесом, являясь одновременно прибыльной частью, либо приваривается к колесу.
Для уменьшения перетоков перекачиваемой жидкости по валу шпоночный паз в ступице рабочего колеса выполняется не на всю длину.
Неперпендикулярность торцов ступицы рабочего колеса не должна превышать 0,01–0,02 мм. Растачивание посадочного отверстия в ступице колеса выполняется по 2-му классу точности. Чистота водопроводящих каналов рабочего колеса оказывает большое влияние на величину гидравлических потерь.
Рис.7. Рабочее колесо
Экспериментально проверено, что уменьшение шероховатости каналов рабочих колес с Ñ2–Ñ3 до Ñ 4–Ñ5 класса без каких-либо конструктивных изменений приводит к повышению к. п. д. на 3–4%. Повышение чистоты поверхности криволинейных каналов рабочих колес осуществляется либо слесарной обработкой изогнутыми напильниками, пневматическими машинками с гибким валом либо гидроабразивной обработкой.
Ориентировочные значения допустимых отклонений размеров рабочих колес не должны превышать следующих значений:
Размер | Допустимые отклонения в долях наружного диаметра колеса | |
Наружный диаметр | 0 002–0 004 | |
Диаметр входного отверстия » ступицы | 0,005 – 0,010 0,005–0,010
0,001–0,002 | |
Ширина на входе | ||
Шаг лопасти: на входе » выходе | 0,003–0,005 0,005–0,008 | |
Толщина лопасти | 0,002–0,003 |
Выбор материала рабочих колес должен производиться с учетом целого ряда требований. Механические свойства материала должны обеспечивать требуемую прочность рабочего колеса с учетом температурных напряжений. Коэффициенты линейного расширения материалов сопрягаемых деталей должны быть приблизительно одинаковыми.
Не менее важной характеристикой является стойкость материала против коррозии в перекачиваемой жидкости. Часто для определения коррозионных свойств воды используют показатель рН, характеризующий концентрацию ионов водород. С повышением температуры воды показатель рН уменьшается.
Перекачиваемая жидкость движется в каналах рабочего колеса с высокими скоростями. Поэтому материал колес должен обладать хорошей стойкостью против эрозии.
Наиболее часто рабочие колеса высоконапорных насосов изготовляются из нержавеющей стали 2Х13Л, углеродистой стали 25Л и чугунов марки СЧ18-36. Из бронзы чаще всего встречаются марки
Бр.ОЦ10-2, Бр.ОФ 10-1 и Бр.АЖН Ю-44.
Разгрузочный диск
Разгрузочный диск (рис.8) служит для восприятия осевого усилия ротора. Различают две разновидности дисков: собственно разгрузочный диск и разгрузочный диск с цилиндрической втулкой.
Рис.8
Разгрузочный диск имеет собственный упор на валу, к которому он прижимается гайкой. Для предотвращения перетока жидкости под диском на внешнем торце его предусматривается специальное уплотнение. С той же целью шпоночный паз в диске выполняют обычно не на всю длину ступицы. В канавках для выхода долбяка должны быть предусмотрены необходимые радиусы закруглений, так как наличие острых углов вызывало появление усталостных трещин и полное разрушение диска.
Рабочая торцовая поверхность диска должна быть строго перпендикулярна оси. Допустимая неперпендикулярность 0,02 – 0,03 мм, а чистота поверхности Ñ7–Ñ8.
Рабочая поверхность подвергается термообработке, твердость должна быть не менее чем на 50 единиц по Бринелю больше твердости рабочей поверхности подушки пяты для уменьшения возможности задирания при металлическом контакте этих деталей в процессе работы.
Перед сборкой ротора разгрузочный диск рекомендуется статически отбалансировать.
При работе на диск действует пульсирующая нагрузка из-за пульсации давления в торцовой щели и вращения диска.
Рассчитать прочность диска с учетом этих условий крайне затруднительно. Поэтому на практике выполняют статический расчет разгрузочного диска, а влияние пульсации и ряда других факторов учитывается введением соответствующих запасов прочности.
Втулки
Основное назначение втулок – предохранять вал от коррозии, эрозии и износа. Существует большое разнообразие втулок по назначению и конструктивным признакам. Наиболее ответственными являются втулки вала в зоне концевых уплотнений насоса. В зависимости от типа уплотнения меняется и назначение втулок.
При мягких сальниковых уплотнениях втулки служат для предупреждения износа вала набивкой. Выполняются такие втулки с гладкой цилиндрической поверхностью, обработанной с высокой степенью чистоты поверхности (Ñ7–Ñ8). Для повышения износостойкости втулок рабочая поверхность их должна иметь высокую твердость.
Втулки вала под концевыми уплотнениями щелевого типа служат для создания дросселирующей щели. Наружная цилиндрическая поверхность втулок может быть либо гладкая, либо иметь кольцевые канавки для увеличения сопротивления щели. Рекомендуемые размеры канавок 1,6x1,6 мм с шагом 3,2 мм.
Втулки на валу фиксируются шпонками. В осевом направлении они зажимаются гайками вала. Для предотвращения протечек жидкости под втулкой предусматриваются специальные уплотнения. Если конструкцией ротора предусматривается передача осевого усилия от разгрузочного диска на втулку, то размеры контактирующего стыка должны выбираться таким образом, чтобы предотвратить смятие торца втулки. Размеры собственно втулки выбираются из условий обеспечения жесткости под действием полного осевого усилия ротора.
Для облегчения изготовления и установки втулки с обоих концов ее выполняются посадочные пояски длиной 15–25 мм.
Внутренняя расточка втулки на оставшейся длине выполняется с диаметром, на 0,5–1 мм превышающим диаметр вала. Втулки на вал, как правило, посажены по скользящей посадке.
Материал втулок выбирается в зависимости от их назначения. Хорошую износостойкость имеют втулки из термообработанной нержавеющей стали. Для повышения износостойкости втулок из обычных материалов применяется поверхностная металлизация (азотирование, борирование и т. д.), упрочнение (накатка роликом и др.) или наплавка твердым сплавом (стеллитом, сормайтом).
Одним из простых способов является хромирование гальваническим способом с нанесением слоя толщиной 0,2 мм
Соединительные муфты
В насосостроении наибольшее распространение получили два типа соединительных муфт: упруго-пальцевые и зубчатые (рис.9).
Указанные типы соединительных муфт обладают важным для эксплуатации качеством – в известных пределах допускают расцентровку спариваемых валов. Кроме того, они допускают осевое перемещение одного валов.
Упруго-пальцевые муфты состоят из двух полумуфт, насаживаемых на спариваемые валы.
Рис.9. Соединительные муфты
В одной из полумуфт крепятся пальцы с эластичными буферами. Буфера изготовляются из набора резиновых колец или в виде цельной резиновой втулки. Резиновые буфера устанавливаются в отверстия другой полумуфты.
Между торцами полумуфты имеется зазора, который выбирается в зависимости от величины возможных осевых перемещений валов.
Размеры упруго-пальцевых муфт выбираются по ГОСТу.
Полумуфты фиксируются на валу шпонками. В осевом направлении полумуфты могут быть зафиксированы гайками.
Буфера имеют возможность скользить в отверстиях полумуфты, благодаря чему гасятся небольшие продольные колебания полумуфты. Погрешность центрования в определенных пределах компенсируется эластичностью буферов.
Упруго-пальцевые муфты в насосах, как правило, применяются для мощности до 500 кВт. Для соединения валов крупных насосов применяются зубчатые муфты. Зубчатые муфты применяются также для малых мощностей, когда применение упруго-пальцевой муфты нежелательно (например, для нефтяных насосов).
Зубчатая муфта состоит из двух зубчатых втулок, насаженных на валы, и двух зубчатых обойм. Обойма и втулка соединяются между собой внутренним цилиндрическим зубчатым зацеплением с нормальным модулем. Геометрические размеры муфт выбираются по ГОСТу 5006 – 55. Обе обоймы соединяются призонными болтами. С торцов обоймы закрываются крышками с уплотнением.
Вращение от одного вала к другому передается через зубчатые зацепления, которые допускают небольшие радиальные и осевые перемещения обойм. Для предотвращения защемления зубчатой пары внутренняя полость муфты заполняется консистентной смазкой.
В крупных насосных агрегатах в некоторых случаях для возможности снятия полумуфт без демонтажа насоса между торцами валов выдерживается определенное расстояние. В этом случае применяются муфты с удлиненными обоймами. Иногда между обоймами устанавливается промежуточная втулка.
Зубчатые муфты обычно балансируются динамически. В связи с этим должны быть обозначены взаимное положение деталей муфты и нумерация болтов по отверстиям.
Соединительные муфты в насосном агрегате закрываются защитным кожухом. Если зубчатая муфта смазывается жидкой смазкой, в этом случае предусматривается специальный защитный кожух, который крепится к подшипнику насоса. Слив масла из кожуха осуществляется но сливной трубе.
Подшипники
В большинстве насосов применяются выносные подшипниковые опоры. К корытообразным кронштейнам корпуса насоса крепятся корпуса подшипников, в которых устанавливаются подшипники. При сборке насоса корпуса подшипников регулировочными винтами могут перемещаться в плоскости, перпендикулярной к оси насоса. После того как ротор займет нужное положение, корпуса подшипников фиксируются штифтами. В некоторых конструкциях насосов корпуса подшипников фиксируются в корпусе по цилиндрической расточке.
Для малых и средних насосов в качестве радиальных опор применяются шарико– роликоподшипники (рис.10). Основным их преимуществом являются минимальные потери на трение, небольшие размеры, легкая смена и способность многих подшипников качения воспринимать не только радиальные, но и осевые усилия.
Рис.10. Подшипник насоса с принудительной смазкой
Смазка подшипников качения применяется как консистентная, так и жидкая с помощью смазочных колец.
При больших окружных скоростях работоспособность шарикоподшипников резко снижается. Кроме того, при разрушении подшипника, как правило, происходит разрушение ротора насоса.
Поэтому для ответственных насосов в качестве радиальных опор часто применяются подшипники скольжения, которые при правильной установке и эксплуатации имеют практически неограниченное время эксплуатации.
В разъемном корпусе 1 подшипника устанавливается вкладыш 2 из двух половин. От проворачивания вкладыш фиксируется в корпусе цилиндрическим штифтом 3. Масло от маслосистемы подводится к штуцеру 8 и поступает к вкладышу. Для регулирования количества масла предусмотрены специальные дроссельные шайбы 7. Контроль за работой подшипников осуществляется через смотровое окно 5 на сливном трубопроводе. Замер температуры вкладыша производится термометром сопротивления 4. Для замера температуры масла в отверстие на сливном трубопроводе, закрытое пробкой 6, может быть установлен ртутный термометр.
Вкладыши подшипников, залитые баббитом Б-83 или Б-16, могут устанавливаться в разъемном корпусе как по цилиндрической, так и по сферической расточке с натягом. Для лучшего сцепления баббита с вкладышем в последнем выполняют продольные или поперечные пазы «ласточкин хвост». Изготовляются вкладыши, как правило, из углеродистой стали. Чугунные вкладыши обладают способностью поглощать вибрацию, однако заливка их значительно сложнее, чем стальных.
Длина подшипников скольжения
L = (1 ÷ 1,5) d.
Величина диаметрального зазора в подшипнике выбирается в зависимости от диаметра вала и приведена в таблице 3
Таблица 3
Диаметр вала в мм | Зазор на сторону в мм верхний боковой | |
50–80 80–120 120–180 | 0,10–0,18 0,16–0,24 0,24–0,36 | 0,5–0,09 0,08–0,12 0,12–0,18 |
Смазка подшипников скольжения осуществляется жидким маслом принудительно от маслонасоса или с помощью смазочных колец. В последнем случае для охлаждения масла в корпусе подшипника предусматриваются специальные камеры либо трубчатые холодильники. Кольцевая смазка применяется для окружных скоростей шейки вала до 8 м/сек. Принудительная смазка может осуществляться маслонасосом, установленным на валу насоса, либо с самостоятельным приводом.
В обычных конструкциях насосов без отжимного устройства для ограничения перемещения ротора в сторону нагнетания под действием случайных усилий применяют упор ротора с указателем осевого сдвига
К торцу корпуса подшипника (рис.11) подсоединяется корпус 1 упора ротора с радиально-упорным шарикоподшипником 2, во внутреннюю обойму которого запрессована упорная втулка 3, ограничивающая перемещение ротора. При работе насоса между торцами вала и втулки образуется зазор порядка 2 мм.
С упором ротора совмещен указатель осевого сдвига. В корпусе 1 выфрезеровано окно, закрываемое хомутом 4. По краям окна нанесены две риски. На валу при сборке насоса наносятся три кольцевые риски.
Средняя риска 6 указывает положение ротора при упоре разгрузочного диска в подушку пяты. При отсутствии износа пяты эта риска должна совпадать с рисками на корпусе.
Рискаа соответствует положению ротора при упоре вала в упорную втулку.
Риска в определяет положение ротора при допустимом износе гидропяты, равном 1,5–2 мм.
Торец корпуса закрывается съемной крышкой, которая снимается при измерении числа оборотов насоса тахометром. Для смазки упорного подшипника достаточно капель масла, которые при работе попадают на него от основного подшипника.
Дата добавления: 2018-06-27; просмотров: 884; Мы поможем в написании вашей работы! |
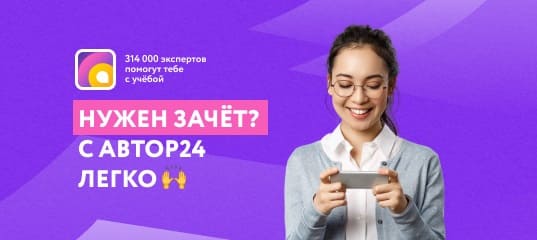
Мы поможем в написании ваших работ!