Инструменты и приспособления, применяемые при производстве ремонтных работ
МАЗМҰНЫ Кіріспе ……………………………………………………………………… І ЖАЛПЫ БӨЛІМ........................................................................................... 1.1ЦНС-180(ОСС-180) сорғы қондырғысын конструкциясының таңдауының техникалық экономикалық негіздемесі………………………… 1.2 ЦНС-180жұмыс істеу қағидасының сипаттамасы 1.3 ЦНС-180…сорғының техникалық көмек көрсету………………………. 1.4 Құрал жабдықты жөндеуге дайындау............................................. 1.5 ЦНС-180 жөндеу........................................................................... ІІ КОНСТРУКТОРЛЫҚ БӨЛІМ............................................................. 2.1 ЦНС-180 жобаланған қондырғысының негізгі тораптарын есептеу…… ІІІ Еңбек қорғау және техника қауіпсіздігі бөлімі....................... 3.1 ЦНС-180 қондырғысын жөндеу кезінде техника қауіпсізідігі…… V Экономикалық бөлімі............................................................... 4.1 ЦНС-180 қондырғысының техника экономикалы таңдау негіздемесі Қорытынды………………………………………………………………………….. Пайдаланылған әдебиеттер тізімі………………………………………. Қосымша……………………………………………………………………
Кіріспе
Химиялық өнеркәсіппен қатар металлургияны, энергетиканы, машина жасау құрылысын даму деңгейін мемелекеттің экономикалық әлеуеті анықтайды.
|
|
Химия өнеркәсібі халық шаруашылығына ықтимал өнімдеріменқамтамасыз етеді, және қазіргі заманғы қоғамда онсыз өмір сүру мүмкін емес .
Минералдық шикізатты қайта өңдеу нәтижесінде, химиялық кәсіпорындар отын, майлар, минералды полимерлер, органикалық заттар мен басқа да өнімдер өнеркәсіпте және тұрмыстапайдаланады.
Химия өнеркәсібін келешекте даму бағдармаласын жақсарту үшін жаңа технологиялық үдерістерді ,химиялық машина жасау,жаңа катализаторларды дамыту арқылы іске асады.
Химия өнеркәсібін дамыту үшін жетілдіруі бар химиялық машина жасау шешуші роль атқарады.
Теориялық және эксперименттік зерттеулер химиялық және физикалық-химиялық процестеріне химиялық машина жасау дамуы сүйенеді, сондай-ақ қол жеткізу үшін машина жасау, металлургия және техника пісіру.
Химия өндірісі қазіргі уақытта бұл күрделі кешенді машиналар мен жабдықтар үшін арналған физикалық-химиялық процестердің сыйымдылық жабдықтар сақтауға арналған сұйықтықтар мен газдарды, көтергіш-көлік машиналары, бақылау-өлшеу аспаптары және автоматика, электр жабдықтардың жиынтығынан құралған.
|
|
Химиялық жабдықтарды құрастыру кезінде дайындау және басшылыққа ала отырып келесі қағидаларға жүгінеміз:
-барынша тереңдетуге технологиялық процестер ұлғайту есебінен үстіңгі бетінің контактіні фазалардың қарқындату, жылу - және масса алмасу. Ультрадыбыстық және діріл техникасын қолдану.
- өнімділігін арттыру, жабдықтарды мөлшерін ұлғайту есебінен. Аппараттар үлкен мөлшерін кем металлды емес аз қызмет көрсететін персоналдың санын талап етеді.
-жабдықтардың сенімділігін арттыру. Қол жеткізу дұрыс таңдау конструкцияның, материалдардың, машиналар мен аппараттар, сондай-ақ жүргізу есебінен жоспарлы жөндеу және технологиялық қызмет көрсету.
Химия өнеркәсібі - жетекші салаларының бірі, халық шаруашылығы; оған тиесілі анықтайтын ролі жеделдету ғылыми-техникалық үдеріс, арттыру тиімділігі қоғамдық өндірістің материалдық және мәдени деңгейін және халықтың өмір сүру.
|
|
Ғылыми негізі химиялық және онымен сабақтас салалар өнеркәсіп болып табылады химиялық технологиясы, техникалық базасы процесінің осы салалардың - химиялық машина жасау.
Осы жылдар ішінде жаңа прогрессивті өндіріс әзірлеу бойынша синтетикалық шайырлар мен пластмассалар, химиялық талшықтар, синтетикалық каучуктер, концентрацияланған және күрделі минералды тыңайтқыштар, өсімдіктерді химиялық қорғау құралдары және басқа да химия өнімдерін, сондай-ақ микробиологиялық синтез түрлері жасалған. Химия өнеркәсібі Ресейде қазір 50 мыңнан астам өнім түрлеріншығарады.
Дамуының негізгі тенденциялары қазіргі заманғы химия өнеркәсібі, ең алдымен адамзаттың ғаламдық проблемаларының шешімімен анықталады. Оларға мыналар жатады: азық-түлік ресурстары, жер ресурстары, минералдық шикізатты үшін өнеркәсіп, энергетика ресурстары, биосфераның ластануының алдын алу. Барлық осы мәселелер өзара байланысты және кешенді түрде шешілуі тиіс.
|
|
Азық-түлік өнімдерін өндіру және азық-түлік қорларын толықтыру болып табылады ауыл шаруашылығы және мал шаруашылығын химияландыру негізгі ұлғайту арқылы іске асады.
Химия өнімін өндіруінің жылдам өсімі, халық шаруашылығының барлық салаларындаоны қолдану үшін елеулі маңызы бар егіншілікті қарқындату, жеделдету ғылыми-техникалық процестің ауыр өнеркәсіп, индустриялық әдістерін, шикізат базасын кеңейту, жеңіл өнеркәсіп және халық тұтынатын тауарлар өндірісі дамыту арқылы болады.
Халық шаруашылығынодан әрі қарқындату дамыту және оның тиімділігін арттыру табиғи ресурстарды кешенді пайдаланудың тиімділігін арттыру және қоршаған ортаны қорғаумаңызды дәрежеде іске асады.Химиялық технологияның қазіргі заманғы деңгейі және әсіресе биотехнология өнеркәсіптік ауқымда емес, тағамдық өсімдік шикізатынан моносахаридтер, этанол, глицерин, өсімдік майлары, белковитаминные концентраттар, амин қышқылдары және басқа да өнімдералуға мүмкіндік береді.
Барлық дамыған елдерде қазір жұмыс іздестіру бойынша үнемді тәсілдерін ірі масштабты өндіріс сутегі және құру сутегі технологиясын өндіружүргізіледі. Сутегі энергетикасын және химия технологиясын, металлургияны, синтетикалық көмірсутек біртұтас технологиялық жүйесіне көшу арқылы барлығын біріктіреді. Сутегі технологиясын қолдану кезінде экономикалық, экологиялық және шикізат проблемалары азаяды.
Химиялық өндірісініңтиімділігінің өсуі оның техникалық деңгейін арттыру агрегаттардың үлкен бірлік қуат үздіксіз енгізу негізінде, аз салмақты және аз энергия сыйымды технологиялық процестердіңесебінен қамтамасыз етіледі.
Шешу салаларының химия кешенінің арттыруыныңжедел дамуына әкелетін табысты шарттарының бірі, технологиялық деңгейі мен пайдалану сенімділігін химиялық кешенін арттыру, технологиялық деңгейі мен пайдалану сенімділігін химиялық жабдықтарды тұрақты жетілдіру болып табылады , химиялық технологияны дамыту, оның теориялық негіздерін және технологиялық сызбаларды әзірлеумен тиімдіаяқталатын және қазіргі заманғы химиялық машина жасау.
І ЖАЛПЫ БӨЛІМ
Құрал-жабдықты жөндеуге тапсыру және дайындау (тазалау, жуу, ЦНС-180 сорғысын бөлшектеу , алдын ала ақау)
Тапсыру алдында жөндеуге сорғы тиіс кірден тазартылып , шлам, промыт және коммуникациялардан ажыратылған болуы тиіс , сондай-ақ ажыратылған жүйелердің көмегімен арнайы бітеуіштерді сәйкес қолданыстағы кәсіпорында нұсқаулықтармен ескере отырып ол тоқтан ажыратылған болуы керек.
Сорғыны (машинистері, аппаратшылары, операторлары) жөндеу, пайдалану және қызмет көрсететін кезекші персонал (кезекші слесарьлар, электриктер, шебер Бөажа) басшылығымен жауапты жөндеуге дайындау үшін адамның (ауысым бастығы, бөлімше) көмегімен дайындайды . Жекелеген жағдайларда өшіру үшін құрал-жабдықтар коммуникациялар бітеуіш орнату тартылуы мүмкін жөндеуші персонал жұмыс істейді тікелей бақылауымен жауапты жөндеуге дайындау.
Құрал-жабдықтар жөндеуге тапсырады ауысым бастығы (қондырғы бастығы немесе оның бөлімшесінен), бұл кезде журналында тиісті жазба жазылады жабдықтарды жөндеуге тапсыру және жөндеуден қабылдау, ол сақталады ауысым бастықтарының.
Қарапайым жөндеуге сәттен бастап есептеледі жабдықты ажырату және шығару мақсатты (аралық) өнімді тапсыру кезіне дейін жөнделген жабдықты пайдаланушы персоналға және шығару құрал-жабдықтарды жұмыс режиміне шығару. Қарапайым жабдықтарды жөндеуге көрсетілген күнтізбелік сағаттар және уақытты қамтиды жүргізуге дайындық, жөндеу және қорытынды жұмыстар. Дайындық жұмыстары үшін қажетті құрал-жабдықты тоқтату, қысымды түсіру, салқындату, жою, өнімнің, үрлеу, шаю, бейтараптандыру, бітеуіш орнату және т. б. Дайындық кезеңі аяқталады сәті тапсыру жабдықтарды жөндеу персоналына (тапсыру үшін жабдықтарды күрделі жөндеу актісі ресімделеді).
Аяқталған күрделі жөндеу жабдықтар есептеледі аяқтау жөндеу бөлімшесі (ұйымның) барлық жоспарланған жұмыс көлемін актіні ресімдей отырып, қабылдау-жабдықты күрделі жөндеу нысаны бойынша ОС3.Қабылдау туралы құрал-жабдықтарды ағымдағы жөндеу журналында тиісті жазба жазылады жабдықтарды жөндеуге тапсыру және жөндеуден қабылдау. Жабдық иесі жүзеге асырады, техникалық бақылау қабылдаған кезде жөнделген жабдықты жөндеу бөлімшелері (ұйымдастыру) көрсеткіштеріне сәйкес белгіленген ТУ жөндеу.
Сорғышты жөндеу ғана толық электр энергиясын ажырату жолымен алу сақтандырғыш ендірмелердің электр қондырғында және"қосуға болмайды, адамдар жұмыс істеп жатыр" плакат ілінгеннен кейінрұқсат етіледі .
Сорғы агрегатының бөлшектеу жүргізеді, келесі реттілік бойынша:
1)жылғы соратын және арынды құбырлардан сорғыны ажыратады;
2)қаптамасын ажыратады, шектеулі муфтасын;;
3)сорғы мен электр қозғалтқышы іргетас плитасынан ажыратады.
Сорғының бөлшеутеуін келесі реттілік бойынша жүргізіледі:
1)түтіктен айырады 31 (рис. 4);
2) болттарын бұрап 49 және какпақты ажыратады47;
3) бұрандамны бұрап 46және гайканы , кронштейнге қосылған 3 нагнетания какпасына қосады б, бұрандаманы бұрап и отделяют втулку сальниктің какпагын ажыратады 35 артқы кронштейннен;
4) алынады кронштейн артқы 3 бірге подшипником және төлкемен мойынтірек 45, қақпағы мойынтірек 25, ұрушы сақинамен 2, төлкемен сальник 35;
5) ротордың гайкасын бурайды44 және шектеу диск гидравликалық табанынан 4;
6) жылғы қақпақтар айдау 6 сақина гидравликалық табанынан ажыратыды5 корпусы бағыттаушы аппараттарының 11 подкладывают ағаш қырлы бөренелер, сондықтан айдау қақпағы 6 жоқ сүйенді алаң;
7) 19 стяжных шпилькаларды гайкаларынан ажыратады 15 және қашпайды қақпағын айдау 6 төлкемен түсіру 7 және бағыты аппаратының 12;
8)алынады дистанциялық втулку 8;
9) алынады дөңгелегі беру кезінде 9, корпусы бағыттаушы аппаратының 11 бірлесе отырып, жіберуші аппаратымен 12 жалғастыруда бөлшектеуге осындай : реттілігін дейін қақпақтар сору 21;
10) алынады полумуфту сорғының 27 біліктің 41;
11) отворачивают болттар және қашпайды мойынтірек қақпағын 25 және втулку 26;
12) сомындар ажыартады, крепящие алдыңғы кронштейн 24 және отсоединяют кронштейн жылғы қақпақтар сору 21;
13) сомындардан ажыратады, крепящие втулку сальник 35, туғаннан оны қақпақтар сору 21;
14) шығарып алады сорғыш білігі 41 қақпақтар сору 21 қалканмен бәрге 1, төлкемен 32, қақпағы 25, сақиналы 33, төлкемен 34, көйлек, білік 36.6)отсоединяют жылғы қақпақтар айдау 6 сақина гидравликалық табанынан 5 корпусы бағыттаушы аппараттарының 11 салады ағаш қырлы бөренелер, сондықтан айдау қақпағы 6 жоқ сүйенді алаң;
7) бұрандамаларды бурады 19 стяжных шпилькаларды 15 және қашпайды қақпағын айдау 6 төлкемен түсіру 7 және бағыты аппаратының 12;
8)алынады дистанциялық втулку 8;
9) алынады дөңгелегі беру кезінде 9, корпусы бағыттаушы аппаратының 11 бірлесе отырып, жіберуші аппаратымен 12 жалғастыруда бөлшектеуге осындай : реттілігін дейін қақпақтар сору 21;
10) алынады полумуфту сорғының 27 біліктің 41;
11) болттарды ажыратады және қашпайды мойынтірек қақпағын 25 және втулку 26;
12) сомындарды бұрайды, крепящие алдыңғы кронштейн 24 және кронштейн ажыратадыжылғы қақпақтар сору 21;
13) сомындарды ажыратады, крепящие втулку сальник 35, туғаннан оны қақпақтар сору 21;
14) шығарып алады сорғыш білігі 41 қақпақтар сору 21 бірге подшипником 1, төлкемен 32, қақпағы 25, сақиналы 33, төлкемен 34, көйлек, білік 36.
Перед ремонтом насос подвергается наружному осмотру и контролю.
Проверяется наружное состояние насоса, его комплектность, и проводятся следующие замеры, оформляемые актом: 1) смещение положения ротора в корпусе насоса в радиальном направлении; 2) осевой разбег ротора; 3) несовпадение осей насоса и привода в радиальном направлении. Насосы сдаются в ремонт в собранном виде, полностью укомплектованные деталями вне зависимости от степени их износа. При отсутствии базовых деталей, или при наличии сквозных трещин в стенке корпуса или днища насос списывается. Допускается восстановление таких насосов по разовой. калькуляции. Промывка и очистка деталей. Перед дефекацией детали очищаются от загрязнения,, промываются, обезжириваются и высушиваются. Детали, покрытые тяжелыми; маслянистыми отложениями (детали проточной части насоса) подвергаются промывке в; ванне с 8-10°/о раствором каустической содой. Детали с довольно сильной коррозией подвергаются травлению согласно инструкции по их химической очистке. Промытые и очищенные детали помещаются на 10-15 мин в водный раствор пассиватора для предохранения от коррозии. После пассивирования (раствор содержит 20 г/л воды каустической соды и 50 г/л воды хромпика) детали просушиваются при нормальной температуре. Срок хранения деталей, обработанных пассиватором, составляет 5-10 суток. Технические требования ни дефекацию и ремонт. Дефектация деталей осуществляется на специальном рабочем месте, оснащенном картами дефектации и необходимыми комплектами приборов и измерительных инструментов. Карты дефектации (дефектные ведомости) являются основным техническим документом, на основании которого проводятся осмотр, измерение, а при необходимости испытание деталей. Ремонту подвергаются следующие детали насоса:
Рабочие колеса центробежного насоса. Основные причины выхода из строя рабочих колес: коррозионно-эрозионный износ; увеличение осевого разбега выше допустимого; образование кольцевых рисок, раковин; попадание в проточную часть посторонних предметов. Кольцевые риски могут образовываться в результате трения рабочих колес о направляющий аппарат или уплотнительнюе кольцо при износе разгрузочного узла (гидропяты) или нарушении центровки насоса.
Глубокие риски и раковины устраняют наплавкой уплотни-тельных поясков или другими способами с последующей зачисткой. Шероховатость зачищенных участков поверхности должна быть не менее 6,3 мкм, а ширина их на 20 мм шире периметра площади дефекта. Для наплавки уплотнительных поясков и заварки дефектов мест можно использовать проволоку типа Св-08Х13Н10Г26 или Св-04Х19Н11МЗ диаметром 2-3 мм или электроды типа 3-1 2X13. При использовании этих материалов необходим подогрев до ЗОО-4ОО°С.
Без подогрева для хромистых сталей предусмотрены электроды типа ЭА-395/9 или проволокаСв-10X16Н25АМ6. Наплавленный слой не должен иметь:
непровара по линии соединения основного и наплавленного металла;
шлаковых включений и пор;
трещин;
увеличенной по сравнению с основным металлом твердости, препятствующей механической обработке.
Общие коррозионно-эрозионные поражения можно устранить шпатлевкой с последующим нанесением на колесо полимерного покрытия. Допускаемое уменьшение толщины лопаток и дисков рабочего колеса не более 15% от размера по чертежу, уменьшение наружного его диаметра допускается не более 1,5%.
Неперпендикулярность торцов ступиц рабочих колес должна быть не более 0,01-0,02 мм,так как под действием осевого усилия вал может быть дополнительно изогнут, что может привести к разбалансировке и заклиниванию ротора. Кроме того, плотное прилегание торцов исключает возможность перетока жидкости по валу и размывание его.
При износе торцов их протачивают до получения чистой поверхности. На величину уменьшения осевого размера рабочего колеса подготавливаются прокладочные кольца для получения необходимых размеров при сборке ротора.
Рабочие колеса обрабатывают с помощью конусной оправки с применением патрона с конусностью до 0,05 мм. Допускаемый размер по торцу рабочего колеса не должен превышать 94,5 мм. Увеличение зазора по уплотнительным диаметрам приводит к резкому снижению напора или к нарушению центровки ротора.
Крышки. Восстановление крышек насосов - один из трудоемких процессов при капитальном ремонте. Учитывая большую стоимость и трудоемкость изготовления крышек, их бракуют обычно только при больших дефектах, когда ремонт не может быть выполнен по техническим причинам.
При ремонте крышек выполняют следующие работы: восстанавливают посадочные поверхности; устраняют деформацию, раковины, коррозионные и эрозионные поражения в местах разъема; восстанавливают прочность и герметичность деталей при наличии трещин, свищей, промоин; исправляют резьбовые цилиндрические отверстия под шпильки, болты, штифты.
Посадочные места крышки восстанавливают наплавкой с последующей механической обработкой.
Раковины, коррозионные и эрозионные поражения устраняют наплавкой металла. Затем эти поверхности зачищают или подвергают механической обработке.
Трещины, свищи, промоины обрабатывают с помощью зубила, фрезы, сверла до чистого металла. После этого проводят работы по заварке дефектов, зачистке мест сварки и испытанию давлением, 1,25 раза превышающим пробное. Течь и "потение" металла в месте заварки не допускается.
Отверстия под установочные штифты исправляют несколькими способами:
изготовление ступенчатого штифта;
сверлением с последующей установкой и фиксацией переходной втулки с номинальным внутренним диаметром;
заваркой и сверлением в сборе с сопрягаемой деталью нового отверстия с необходимым диаметром на месте старого.
Поврежденные резьбовые отверстия восстанавливают следующими способами:
нарезка резьбы большего диаметра с применением ступенчатой шпильки, если в сопрягаемой детали соответствующее отверстие можно рассверлить , то используют шпилькубольшего диаметра;
заварка дефектного резьбового отверстия и сверление нового;
- применение пробки с необходимым внутренним диаметром.
Секции, направляющие аппараты, подушки, гидропята и диск разгрузочный. Различают следующие группы износа: механический; коррозионный; кавитационный и гидроаббразивный. В зависимости от вида износа подбирают способ устранения дефекта.
Для увеличения срока службы ремонтных деталей и восстановления дефектных мест методом наплавки без сопутствующего подогрева применяют проволоку Св-10X16Н25АМ6 или электрод типа ЭА-395/9. С сопутствующим подогревом применяют электроды Э-12Х13 и проволоку Св-12Х13 или Св-Нн-20Х14, Нп-30Х13. Наплавленные детали в обязательном порядке проходят термообработку для снятия напряжений и цветную дефектоскопию после механической обработки. Механическую обработку производят на токарных станках с применением оправок.
Ремонт валов. Валы несут на себе вращающиеся части насоса. Материалом для их изготовления служит горячий прокат конструкционной углеродистой стали марки 40ХФА. Одно из условий длительной эксплуатации вала, улучшения работы насоса и уменьшения дисбаланса ротора - соответствующая термическая обработка вала. При отсутствии необходимых условий допускается изготавливать валы без термической обработки из стального проката.
Дефекты валов подразделяются на неисправимые и исправимые. К неисправимым дефектам относятся появление на валу трещин и расслоений, а к исправимым- искривление оси; появление овальности и конусности (износ шеек вала); износ резьбы; повреждение шпоночного паза.
Искривление оси вала происходит при выходе из строя опорных подшипников, расцентровке насоса или трении уплотнительных поясков рабочих колес по уплотнительным кольцам. В этом случае в первую очередь устраняют причины изгиба вала: перезаливают подшипники, перецентровывают насос или доводят зазоры до нормальных размеров проточкой уплотняющих деталей ротора на станке. К изгибу вала приводят, кроме того, значительная и продолжительная вибрация насоса независимо от вызвавшей ее причины.
Износ шеек вала происходит вследствие выработки и выхода из строя подшипников скольжения, а также в результате коррозионных оспин, появления рисок и надиров при попадании мелких посторонних предметов во вкладыши подшипников вместе со смазкой.
Перед началом ремонтных и восстановительных работ проводят поверочные работы центровых отверстий вала. Повреждения исправляют зачисткой шабером или устраняют сверле-нием с помощью центрового сверла и зенкерованием.
Поверочные работы и правка валов. Поверку вала на биение производят установкой его в центрах токарного станка. На суппорте станка помещают часовой индикатор, ножка которого опирается на деталь, и проверяют биение в разных местах вала.
Допустимые биения валов (мм) не должны превышать следующих значений:
шейки валов под опорные подшипники 0,02- 0,25;
посадочные места защитных рубашек 0,03-0,04;
посадочное место полумуфты 0,03-0,05.
Если биение превышает допустимые нормы, то вал подлежит правке, для чего применяют следующее приспособление. На станке с шаброванными направляющими фиксируют корпуса подшипников с бронзовыми вкладышами и две бабки с вращающимися центрами. Вал устанавливают в этих центрах и с помощью индикатора определяют его биение.
Далее вал укладывают выпуклой стороной вниз на подшипниках и их закрывают. К месту наибольшего прогиба подводят домкрат и начинают правку. В процессе правки вал несколько раз проверяют индикатором часового типа с ценой деления не более 0,02 мм.
При исправлении методом чеканки вал закрепляют в центрах токарного станка, а к месту максимального его прогиба подводят жесткую опору с прокладкой из твердого дерева или отожженной меди. Так как изогнутый вал имеет растянутые волокна, то его кладут на подкладку и чеканят вогнутую сторону, растягивая волокна и выправляя вал. Чеканку выполняют ударами молотка массой 1-2 кг.
Восстановление поврежденных посадочных мест вала. При износе шеек вала, работающего в подшипниках скольжения, их протачивают на токарном станке с последующей шлифовкой, если эллиптичность или конусность составляет более 0,04 мм.
Восстановление резьбы. Поврежденные резьбы валов можно восстановить либо нанесением покрытий (в основном хро-мовых), либо нарезкой резьбы меньшего размера. Второй способ используется лишь в том случае, когда после шлифовки не получили допускаемого размера резьбы.
Ремонт шпоночных пазов. Наиболее простой способ -перефрезеровка шпоночного паза на следующий стандартный размер. Допускается изготовление переходной шпонки с двумя размерами. В редких случаях возможна перефрезеровка шпоночного паза на валу под углом 120° к старому. При замене шпонки необходимо в шпоночном соединении обеспечить натяг не более 005-0,01 мм.
Шейки валов, как правило, вырабатываются неравномерно: в продольном направлении она принимает форму конуса, а в поперечном - эллипса. Износ резьбы на валах насосов, перекачивающих сточные воды в местах сопряжения с защитными рубашками, можно устранить, применив при сборке сухой графит, разведенный в масле.
Повреждение шпоночного вала происходит в результате разбалтывания шпоночного соединения во время увеличения бокового зазора.
Ремонт и заливка вкладышей подшипников. При наличии следов касания в верхних половинах владышей их направляют на ремонт с обязательным выявлением причин, вызвавших этот дефект. Ими могут быть: недостаточные или неравномерные зазоры во вкладыше; температурные перекосы корпуса подшипника;отставание баббита от тела вкладыша.
Перед удалением из вкладыша изношенной баббитовой заливки (баббита) необходимо проверить по чертежу ее размеры и конструкцию. При отсутствии чертежа необходимо снять эскиз расположения масляных канавок, карманов, скосов, закруглений и поясков. Удаляют изношенную баббитовую заливку путем нагрева вкладыша в горне (противне) лампой или газовой горелкой с тыльной стороны вкладыша до 240-260 °С, что соответствует началу его размягчения. В результате удара вкладыша о плиту баббит легко отстает.
Запрещается нагревать вкладыш до полного расплавления баббита, так как при этом из него выгорает сурьма и он теряет свои свойства и не может быть повторно использован. Основное условие заливки и схватывания баббита с телом вкладыша - предварительная его подготовка: зачистка, обезжиривание, протравливание и лужение.
Зачистка поверхности вкладыша производится шабером, стальной щеткой и наждачной шкуркой с тщательным удалением остатков старого баббита. Обезжиривание вкладыша производится в кипящем 10%-ном растворе каустической соды или едкого натра (1 кг каустической соды на 10 л воды) в течение 10-15 мин, после чего его промывают горячей водой для удаления грязи и щелочи. Обезжиренная поверхность должна иметь ровный металлический блеск, при необходимости обезжиривание повторяют с зачисткой дефектных мест.
Протравливание вкладыша подразделяется на два этапа: первоначальный и вторичный. Первоначальное протравливание осуществляется погружением вкладыша в раствор соляной или серной кислоты ( 1 л крепкой дымящейся кислоты на 10 л воды), в котором его выдерживают в течение 10 мин. Во избежание травматизма и ожогов кислоту следует лить в воду, а не наоборот. Затем вкладыш промывают горячей проточной водой и высушивают при температуре 200°С.
Вторичное протравливание вклыдыша производится насыщенным раствором хлористого цинка с добавлением к нему хлористого аммония (сухого безводного нашатыря) в количестве 50 г на 1 л раствора.
Лужение используют для покрытия оловом вкладыша. Осуществляют его погружением вкладыша в расплавленное олово при температуре 300-320°С (чистое олово, сплав из 50% олова и свинца, баббит Б-83).
Заливка баббита. Заливка каждого вкладыша баббитом должна производиться при температуре 400-410°С в один прием сильной короткой непрерывной струей.Следует учитывать, что вкладыш предварительно прогреть до 250-260°С. При заливке необходимо следить, чтобы во вкладыш не попали частицы угля и шлака. Подшипники перед заливкой должны быть прогреты до температуры 250-260°С.
Ремонт масляной системы. Маслосистема насосного агрегата - один из самых ответственных узлов. Для подачи смазки в маслосистеме предусмотрен шестеренный насос, ремонт которого производят в следующей последовательности:
снимают и проверяют состояние соединительной муфтыи зацепление в зубьях шестерен ( оно должно быть одинаковым и равномерным по всей длине);2)проверяют зазоры между торцами шестерен и крышка-ми корпуса (они должны быть в пределах 0,001-0,0013 высоты шестерен плюс 0,05 мм);
осматривают канавки в крышках насоса (засоренность их приводит к заклиниванию шестерен и к сработке стенок насоса), а также определяют разбег в зацеплении зубьев (боковой и радиальный зазоры); зазор устанавливают по оттиску свинцовой проволоки при проворачивании собранного насоса, раз бег в зацеплении должен быть в пределах 0,15-0,25 мм, а радиальные зазоры - 1,5-2 мм;
проверяют состояние баббитовой заливки в бронзовых втулках, если зазоры превышают допустимые, следует выпрессовать втулки и заменить их;
обследуют бронзовые втулки, не имеющие баббитовой заливки, если зазоры больше 0,05-0,1 мм (на диаметр), их заменяют.Маслоохладитель. Сначала извлекают трубчатую систему, затем проверяют на плотность задвижки на трубопроводах к маслоохладителю. Ремонтные работы проводятся в следующей последовательности:
1) очищают внутренние поверхности трубок (мягкие отложения чистят шомполами, твердые -химическим способом ра створом соляной кислоты);
2) очищают маслоохладитель с масляной стороны промыв кой из брандспойта горячей водой (60-70°С), с погружением на 10-15 мин трубчатого пучка в ванну с 5-8%-ным раствором едкого натра (каустическая сода) или в кипящий 5%-ный раствор тринатрийфосфата с последующей промывкой и обдувкой воздухом;
2) испытывают маслоохладитель гидравлическим способом.
При осмотре устанавливают неплотности в местах вальцовки и в анкерных болтах; в местах вальцовки их устраняют подвальцовкой трубок, а в анкерных болтах - подмоткой под шайбы болтов льняных волокон, пропитанных белилами или суриком.
Если в процессе эксплуатации маслоохладителя температура высокая, необходимо проверить зазоры между перегородками и кожухом (кольцевой зазор не должен превышать 1-1,5 мм). Для устранения этого дефекта используют кольцевую наварку металла в местах увеличенного зазора. Зазор должен быть рассчитан таким образом, чтобы была возможность беспрепятственного ввода и вывода трубчатой секции из корпуса.
При сборке маслоохладителя во избежание утечек масла особое внимание следует уделить установке трубной секции и укладке прокладок между водяными камерами и трубчатыми досками.
Замену трубок маслоохладителя производят следующим образом. Удаляют сработанные трубки из конденсатора таким образом, чтобы не были испорчены отверстия в трубных досках. Концы их сгибают в двух-трех местах по окружности, после чего трубки выбивают из отверстий досок медной цилиндрической оправкой с диаметром, несколько меньшим, чем диаметр этих отверстий.
Новые латунные трубки необходимо проверить на отсутствие в них остаточных напряжений. При необходимости они подлежат отжигу паром при температуре 290-300°С в течение 50-60 мин. Затем зачищают отверстия в досках, снимают ржавчину и заусенцы с помощью наждачной шкурки или проволочным ершом, укрепленном на валу электродрели. Внешний диаметр трубок должен быть на 0,15-0,3 мм меньше диаметра отверстий.
Латунные трубки закрепляют в трубных досках развальцовкой с обеих сторон, что обеспечивает большую гидравлическую плотность (герметичность). Нельзя допускать утопления трубки больше чем на 4-6% и удлинения выступающего ее конца больше чем на 0,5-0,6 мм.
После вальцевания для обеспечения плавного входа воды края трубки следует предварительно развальцевать.
Перед сборкой обращают особое внимание:
1)на чистоту посадочных и соприкасающихся торцовых поверхностей деталей. На них не допускаются забоины, заусенцы, грязь и т.п.
2)на годность резиновых уплотнений 39, манжетных уплотнений 23. Собирают насос в следующей последовательности:
1) в крышку всасывания 21 (рис. 4) устанавливают втулку гидрозатвора 37, кольцо; уплотняющее 16 и кольцо соединительное 17;
2)на вал насоса 41 устанавливают кольцо упорное 48 до упора в торец вала;
3)до упора в торец кольца упорного на вал устанавливают рабочее колесо первой ступени 38;
4)вал е установленными на нем деталями вставляют в крышку всасывания 21;
5) корпус направляющего аппарата ll в сборе запрессованным направляющим аппаратом 12 и уплотняющими кольцами 14 и 13 устанавливают в крышку всасывания 21.,
Затем до упора в торец первого рабочего колеса 38 устанавливают на вал второе рабочее, колесо 10, корпус направляющего аппарата с направляющим аппаратом и уплотняющими' кольцами и т.д. до крышки нагнетания;
6)на вал устанавливают дистанционную втулку 8;
7)устанавливают крышку нагнетания б с направляющим аппаратом при выдачи 12, втулкой разгрузки 7;
8)устанавливают стяжные шпильки 15 и стягивают корпус насоса гайками 19j
стяжных шпилек. Гайки стяжных шпилек затягивают постепенно, обходя насос несколько'
раз, не затягивая сразу одну сторону, щуп 0,05 мм не должен проходить в стыки корпусов;
9)на вал устанавливают кольца регулировочные 42;
10) устанавливают диск разгрузки 4 и закрепляют его гайкой ротора 44;
11) сдвигают ротор насоса в сторону всасывания до отказа и замеряют расстояние (Ав) между торцем крышки нагнетания и диском разгрузки;
12) сдвигают ротор насоса в сторону нагнетания до отказа и замеряют расстояние (Ан) между торцем крышки нагнетания и диском разгрузки;
13) определяют общий разбег ротора по формуле Ас = Ан - Ав;
14) определяют толщину регулировочных колец (h), которую необходимо снять по формуле h = Ав + Ас/2 -15, где 15 - толщина кольца гидравлической пяты
15) отворачивают гайку ротора и снимают диск разгрузки;
16) снимают кольца регулировочные суммарной толщиной h;
17) устанавливают кольцо гидравлической пяты 5;
18) устанавливают диск разгрузки и стягивают детали ротора на валу насоса гайкой ротора; 19)проверяют получившийся разбег, т.е. при роторе, сдвинутом до отказа в сторону нагнетания, зазор между диском разгрузки и кольцом гидравлической пяты должен быть равным половине общего разбега Ас/2;
20) устанавливают кронштейн 3, поставив уплотнение с втулкой сальника 35,отбойным кольцом 2, крышкой подшипника 25 с манжетой и прокладкой;
21) устанавливают втулку подшипника 45 с подшипником 1 на вал и закрепляют их , шайбой и гайкой 46;
22) ставят крышку глухую 47 и болты 49;
23) устанавливают кронштейн передний 24 и закрепляют его к крышке всасывания
24) устанавливают на вал втулку распорную 26;
25) закладывают смазку и устанавливают крышку подшипника 25 с манжетой прокладкой, закрепив ее к кронштейну болтами 9;
26) на вал устанавливают муфту 27;
27) в правильно собранном насосе ротор должен свободно вращаться (при незатянутых сальниках) и иметь разбег вдоль оси равный половине общего разбега Ас/2 ±0,8 мм;
28) сливная трубка 20 и штуцеры , на которые крепится трубка 31 ставятся на сурике ГОСТ 8866-76 с подметкой пакли ГОСТ16183-77;
29) нанести риску в собранном насосе при сдвинутом роторе в сторону всасывания; на втулке распорной 2 заподлицо с крышкой подшипника 1 в виде опрокинутой буквы «Т» Измерение параметров и регулирование.
Измерение напора насоса производится манометром, подключенным на напорном, трубопроводе перед регулирующей задвижкой.
Соответствие напора насоса его значениям в рабочей части характеристики достигается регулирующей задвижкой в случае несоответствия сопротивления трубопроводов.
Манометры выбираются так, чтобы их шкала использовалась не менее чем на 2/3
В процессе сборки секционных насосов главное внимание должнобыть уделено центровке ротора в осевом направлении с тем, чтобыобеспечить соосность колес с направляющими аппаратами и нормальный средний зазор между разгрузочными диском и кольцом. Нормальный осевой люфт ротора у насосов с разгрузочным диском составляет±0,2 мм, т. е. суммарно 0,4--0,5 мм. Учитывая внешнее сходствоодноименных деталей во всех секциях и вместе с тем наличие неоди-наковых по величине и знаку отклонений от номинала осевых размеров корпусов секций, колес, втулок, вала и уплотнительных колец, необходимо при разборке пронумеровать все детали и записатьосевые размеры каждой детали с тем, чтобы эти индивидуальные раз-меры были выдержаны при изготовлении заменяемых деталей и чтобывсе детали собирались по рискам в правильной последовательности. Центровка колес ротора вдоль оси вала облегчается применением установочных шаблонов. При этом рекомендуется следующий порядок сборки секционных насосов.
Рисунок 3 Риска. Установка первого колеса секционного насоса по шаблону: 1-крышка всасывания; 2-колесо; 3-вал; полумуфта; 5-шаблон; 7-подшипник;
Вал с надетой на него полумуфтой 4 вставляется в крышку всасыванияt затем на вал надевается первое колесо 2 с упором в заточку. образовавшийся узел «вал--колесо» устанавливается по щаблону и на валу против торца крышки всасывания делается риска Р. Далее последовательно ставятся первая секция корпуса с направляющим аппаратом первого колеса, следующие рабочие колеса и соответствующие им секции корпуса с направляющими аппаратами, распорная втулка и, наконец, крышка нагнетания, после чего все секции и обе крышки стягиваются болтами. В процессе сборки надо следить затем, чтобы ступицы колес, равно как и плоскости направляющих аппаратов, плотно прилегали друг к другу.
Затем на задний конец вала навертывается разгрузочный диск до упора в распорную втулку и весь ротор сдвигают в сторону всасывания, выбирая люфт между разгрузочным диском и опорным кольцом.
При правильной сборке секций и колес риска Р должна оказаться точно против торца крышки всасывания.
Если -риска уходит внутрь грундбуксы сальника, то распорную втулку надо заменить длинной либо нарастить шайбами; наоборот,--при риске выступающей из крышки, распорная втулка требует подрезки.
Обилие прокладочных соединений между секциям наличие двух сальников заставляет особенно внимательно относиться" я к уплотнению насоса, так как подсос воздуха на входе жидкости не только снизит производительность насоса, но и приведет срыву подачи жидкости или к усиленной кавитации.
Затягивание скрепляющих болтов должно производиться.по правилам многоболтовой .сборки, т. е. накрест и в 3--4 обхода всех гаек.Сальниковая набивка должна применяться необходимого сеченияи хорошего качества и укладываться в сальник отдельными разрез-ными уплотнительными кольцами в количестве 3--4 шт. При этомстык одного кольца должен быть смещен по отношению к другому,на 90°.
Инструменты и приспособления, применяемые при производстве ремонтных работ
1. Мерительный инструмент (линейки,штангенинструмент)
2. Сварочное оборудование(токарные станки,проточка,обработка торцов),щупы,зазоры.
3. Угольники(угольники торцевые,ступици колес)
4. Зубило, фрезы, сверло для обработки трещин, свищей, крышки, корпус, центровых отверстий вала.
5. Метчики,плошки-для восстановления резьбовых отверстий и крепежных деталей
6. Печи для термообрабртки деталей.
7. Шабер для заливки шеек вала.
8. Индикатор часового типа для проверки биения вала.
9. Молоток для иправления искревления вала (чеканка)
10. Домкрат для правки вала.
11. Горн и паяльная лампа для удаления старого баббита из подшипников скольжения.
Дата добавления: 2018-06-27; просмотров: 470; Мы поможем в написании вашей работы! |
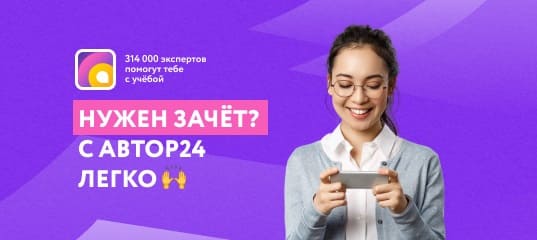
Мы поможем в написании ваших работ!