Остановочные и тормозные устройства
Остановочные устройства применяют для того, чтобы удержать груз, поднимаемый лебедками, от падения. Наиболее простое остановочное устройство (рис. 19, а) представляет собой храповое колесо 1 и защелку 2. Колесо может вращаться только в одну сторону, так как вращению в другую сторону препятствует защелка. Вращение колеса в другую сторону возможно только после вывода защелки из зацепления с колесом.
К более сложным механизмам, служащим для удержания груза на весу и регулирования скорости опускания груза и движения машин, относятся тормозные устройства. По конструкции тормозные
устройства подразделяются на колодочные, ленточные, центробежные и дисковые.
Наибольшее применение в связи надежностью в работе и простотой конструкции получили колодочные тормоза. Они пригодны для двухстороннего торможения и применяются в качестве стопорных нормально замкнутых тормозов в грузоподъемных машинах.
Принципиальная схема постоянно-замкнутого колодочного тормоза с пружинным замыкающим механизмом представлена на рисунке 19.
Рис. 19. Тормозные устройства: а - останов храпового типа: 1 - храповое колесо; 2 - защелка; б - колодочный тормоз: 1 - пружина; 2, 3 - тяги;
4 - основание; 5, 6 - рыча ги; 7 - тормозные колодки; 8 - тормозной шкив;
9 -катушка; 10 – якорь
Работа тормоза осуществляется следующим образом. Пружина 1 через тяги 2 и 3 оттягивает находящиеся на основании 4 рычаги 5 и 6, прижимая тем самым тормозные колодки 7 к тормозному шкиву 8. При включении электродвигателя лебедки одновременно включается катушка 9, которая притягивает подвижный якорь 10. Якорь нажимает на тягу 3 и раздвигает рычаги 5 и 6, преодолевая сопротивление сжатой пружины, которая отводит колодки 7 от тормозного шкива При отключении питания пружина возвращает колодки в исходное положение и стопорит шкив.
|
|
Величина тормозного момента, Н∙ м, равна:
Мт = Q/D/2,
где Q - сила прижатия колодок, Н; f - коэффициент трения между поверхностью колодок и шкива; D - диаметр шкива, м.
Лекция № 5. Системы управления машин
Назначение и классификация систем
Системы управления предназначены для периодического включения и выключения различных механизмов машины (муфт, фрикционных тормозов, рулевого управления и др.). По назначению системы управления можно разделить на следующие:
1) управление двигателем;
2) управление муфтами и тормозами;
3) рулевое управление
4) управление установкой рабочего органа (опускание, подъем отвала) бульдозера или автогрейдера.
В зависимости от конструктивного выполнения системы управления подразделяются на механические (редукторные), канатно-блочные, гидравлические, пневматические, электрические, комбинированные.
|
|
Устройство и принцип работы систем управления
Редукторная система управления с приводом от двигателя применяется на таких землеройно-транспортных машинах, как автогрейдеры и грейдеры-элеваторы. Кинематическая схема этой системы управления показана на рис. 20, а. В механических системах применяются червячные, цилиндрические и планетарные редукторы. Наибольшее распространение получили червячные редукторы с самотормозящейся червячной парой. Они обеспечивают фиксацию рабочего органа.
Канатно-блочная система управления применяется в бульдозерах, скреперах, грузоподъёмных машинах и др. Основными частями этой системы управления (рис. 20, б) являются: лебёдка, тормоз, направляющие блоки и канатные полиспасты. Достоинство канатно-блочной системы управления - в простоте конструкции; среди недостатков - громоздкость, низкий КПД, а также невозможность принудительного заглубления рабочих органов.
Гидравлическая система управления применяется для воздействия на муфты, тормоза, рулевые устройства и рабочие органы агрегатов К преимуществам гидравлических систем управления, по сравнению с редукторными и канатно-блочными, относятся: независимость расположения агрегатов, лёгкость включения и выключения, возможность обеспечения большого передаточного числа, наличие устройств, предохраняющих систему от перегрузок. Недостатком гидросистемы управления является сложность (невозможность) работы при низких температурах.
|
|
Рис. 20. Системы управления дорожно-строительных машин: а - редукторная; б - канатно-блочная; в - гидравлическая: 1 - бак; 2 - насос; 3 - обратный клапан; 4 - предохранительный клапан; 5 - аккумулятор; 6 - распределитель; 7 - клапан; 8 - цилиндр; 9 - фильтр; 10 - манометр
Гидравлические системы делят на насосные и безнасосные. Схема насосной системы гидравлического управления показана на рис. 20, в. Рабочая жидкость из бака 1 нагнетается насосом 2 через обратный клапан 3 в аккумулятор 5 и к золотникам распределителя 6. Как только давление в аккумуляторе достигает рабочего, автоматически открывается клапан-пилот 7 и жидкость без давления сливается в бак. Этим разгружается насос и уменьшается его износ. Если клапан-пилот выходит из строя, то его функции выполняет предохранительный клапан 4, включенный параллельно и настроенный на большее давление, чем клапан 7. При остановке насоса обратный клапан 3 закрывается, и система удерживается под давлением. В рабочем цилиндре 8 поршень перемещается рабочей жидкостью при открывании золотника распределителя 6. Фильтр 9 служит для очистки рабочей жидкости от посторонних включений. Давление в системе контролируется при помощи манометра 10.
|
|
Безнасосные системы управления по конструкции подразделяются на гидравлические и пневматические. Они просты по конструкции, отличаются большой надёжностью и долговечностью, применяются в основном для маломощных механизмов. В гидравлических системах (рис. 21) давление в магистрали создаётся усилием нажатия оператора на педаль. При нажатии на педаль 1 рабочая жидкость, находящаяся в цилиндре-датчике 2, через трубопровод 4 вытесняется в рабочий цилиндр 5, поршень которого связан с исполнительным механизмом. Утечка жидкости пополняется из бачка 3. Обратный клапан 6 предотвращает возврат жидкости из цилиндра в бачок.
Пневматическая система управления получает всё большее распространение благодаря ряду преимуществ перед гидравлической.
Основными преимуществами пневматического управления являются большая плавность включения, отсутствие рабочей жидкости и осложнений, вызываемых её утечкой. Давление в системе пневматического управления не превышает 0,7...0,8 МПа, в то время как в гидравлической достигает 10 МПа. Поэтому пневмосистемы применяются лишь при небольших усилиях управления (включении).
В качестве исполнительного устройства применяют пневмо-цилиндры или диафрагменные пневмокамеры.
Рис. 21. Безнасосная система управления: 1 - педаль; 2 - цилиндр-датчик; 3 - бачок; 4 - трубопровод; 5 - рабочий цилиндр;
6 - обратный клапан
Такие камеры, отличающиеся простотой устройства и надежностью, применяют для управления тормозами и фрикционами экскаваторов и дорожных машин.
Дата добавления: 2018-06-01; просмотров: 1308; Мы поможем в написании вашей работы! |
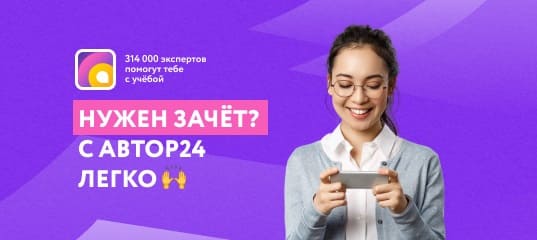
Мы поможем в написании ваших работ!