Лекция № 2. Соединения деталей машин
МИНИСТЕРСТВО ОБРАЗОВАНИЯ И НАУКИ РОССИЙСКОЙ ФЕДЕРАЦИ
БЕЛГОРОДСКИЙ ГОСУДАРСТВЕННЫЙ ТЕХНОЛОГИЧЕСКИЙ
УНИВЕРСИТЕТ им. В.Г. ШУХОВА (БГТУ им. В.Г. Шухова)
А.А. Романович
ВВЕДЕНИЕ В СПЕЦИАЛЬНОСТЬ И
ПРОФЕССИОНАЛЬНУЮ ДЕЯТЕЛЬНОСТЬ
Утверждено методическим советом университера в качестве конспекта лекций для студентов очной и заочной форм обучения направления бакалавриата 23.03.02 – Наземные транспортно-технологические комплексы и специальности 23.05.01 – Наземные транспортно-технологические средства
Белгород 2017
УДК 625.7 (07)
ББК 39.311-06-05 Р69
Рецензенты:
Доктор технических наук, профессор Белгородского национального исследовательского университета (НИУ «БелГУ» ) С.В.Сергеев
Доктор технических наук,профессор Белгородского государственного технологического университета им. В.Г. Шухова (БГТУ им. В.Г. Шухова) О. А. Носов
Романович, А.А.
Р69 Введение в специальность и профессиональную деятельность: Конспект лекций - Белгород: Изд-во БГТУ, 2017. - 195 с.
В конспекте лекций представлены основные сведения о деталях машин, узлах и способах их соединения. Рассмотрены впросы связанные с назначением, устройством и принципом работы машин и механизированных установок, применяемых при строительстве, содержании и эксплуатации автомобильных дорог и придорожных сооружений: машины для земляных работ, приготовления и транспортирования материалов, грузоподъемные машины и агрегаты и другие. Приведены методики расчета производительности машин.
|
|
Конспект лекций предназначен для студентов очной и заочной форм обучения направления бакалавриата 23.03.02 – Наземные транспортно-технологические комплексы и специальности 23.05.01 – Наземные транспортно-технологические средства.
Данное издание публикуется в авторском издании.
УДК 625.7 (07)
ББК 39. 311- 06 - 05
© Белгородский государственный
технологический университет
(БГТУ) им. В.Г. Шухова, 2017
Введение
Подъемно-транспортные, строительные и дорожные машины составляют основу комплексной механизации строительного производства. Затраты на поддержание машин в работоспособном состоянии составляют 25-30% от себестоимости машин. Снижение затрат на содержание и эксплуатацию возможно при применении на предприятии новых методов ремонтного обслуживания.
|
|
Обеспечение работоспособного состояния парков машин и оборудования предприятий связано со значительными трудовыми и материальными затратами. С помощью нормативов определяются квартальные и годовые прогнозы потребности в техническом обслуживании и ремонте по парку машин, что необходимо, но недостаточно для управления надежностью в эксплуатации. Требуется также выявлять потребность в ремонтных воздействиях конкретных экземпляров машин и их агрегатов, что дает краткосрочный прогноз, конкретизирующий потребность, определяемую по нормативным данным.
Повышение эффективности от использования это - обеспечение технически грамотного, с максимальным коэффициентом использования подъемно-транспортных, строительных, дорожных машин, их техническое обслуживание и ремонт с минимальным простоем под обслуживанием. Конспект лекций направлен на изучение основных сведений о деталях машин, узлах и способах их соединениях, назначения, устройства и принципа работы машин и механизированных установок, применяемых при строительстве, содержании и эксплуатации автомобильных дорог и придорожных сооружений. Введение в специальность и профессиональную деятельность является дисциплиной, направленной на формирование будущего инженера.
|
|
Лекция № 1. Основные сведения о машинах
Роль машин и оборудования в дорожном строительстве
Работы, выполняемые в строительстве, крайне разнообразны и состоят из процессов различного типа: земельных, погрузочно-разгрузочных, транспортных, грузоподъёмных, по приготовлению, укладке и уплотнению бетонных смесей и др. Для выполнения этих работ используют соответствующие комплекты машин, в которые входят рыхлители, экскаваторы, бульдозеры, грейдеры, погрузчики, уплотняющие машины, механизированные установки для приготовления бетонных смесей, транспортные машины и др.
Большинство работ, выполняемых в строительстве, требует большого количества энергозатрат. Например, на разработку 1м3 грунта затрачивается около 0,3 кВт-ч; на дробление 1 м3 камня - 1...3 кВт-ч; на приготовление 1м3 бетона -0,1...0,15 кВт-ч, а с учётом транспортировки и укладки его в сооружение - более 3 кВт-ч; на погрузку 1т груза - 0,1...0,13 кВт-ч. При работе вручную человек затрачивает за смену в среднем не более 0,5 кВт-ч энергии. Выполнение строительных работ даже на одном объекте характеризуется большим объемом в сжатые сроки, перемещением десятков тысяч кубометров грунта, приготовления и укладки бетонов и растворов и т.д. - всё это возможно только при использовании большого количества высокопроизводительных машин и механизмов.
|
|
Классификация машин
Большое разнообразие машин, с целью более полного использования, требует их классификации по отдельным признакам. Наиболее характерным признаком, по которому возможно произвести группировку всех машин, является - производственным. На основании этого признака все строительные машины можно объединить в следующие группы:
1. Подъёмно-транспортные: краны, подъёмники, лебедки, тали, домкраты, транспортёры, погрузочно-разгрузочные машины и др.
2. Транспортные: тракторы, тягачи, автомобили, прицепы, полуприцепы и др.
3. Машины для подготовительных работ: корчеватели, кусторезы, рыхлители и др.
4. Машины для свайных работ: свайные молоты, вибропогружатели, копры и др.
5. Машины для земельных работ: бульдозеры, скреперы,
грейдеры, грейдеры-элеваторы, экскаваторы, оборудование для гидромеханизации и др.
6. Машины для добычи и переработки каменных и обогощения материалов: оборудование для буровых работ, дробилки, сортировочные, моечные и обогатительные машины.
7. Машины для уплотнения различных типов грунтов и смесей: катки, вибраторы и др.
8. Машины для приготовления и транспортировки бетонной смеси: бетоносмесители, бетононасосы.
9. Машины и агрегаты для механизации отделочных работ.
Современные строительные машины состоят из пяти основных частей:
1. Рабочего оборудования, непосредственно осуществляющего технологическую операцию, например разработку грунта, перемешивание бетонной смеси, перемещение материала.
2. Ходового оборудования, служащего для передвижения машины.
3. Силового оборудования - двигатели, являющиеся источником энергии для осуществления движения элементов машины.
4. Передаточных механизмов, связывающих силовое оборудование с рабочим и ходовым оборудованием.
5. Механизмов управления, служащих для включения и выключения отдельных механизмов машин.
У некоторых машин отдельные части могут отсутствовать, например силового оборудования нет у прицепных машин, ходового оборудования - у стационарных машин.
Силовое оборудование
В строительных машинах применяют следующие виды силового оборудования:
1) электродвигатели;
2) двигатели внутреннего сгорания (ДВС);
3) гидравлический привод;
4) пневматический привод.
Электродвигатели обладают рядом существенных достоинств:
1. Возможностью установки индивидуальных двигателей для каждого механизма (многодвигательный привод), что упрощает трансмиссии.
2. Удобством управления отдельными механизмами, возможность дистанционного управления и автоматизации.
3. Значительной перегрузочной способностью, что особенно важно для машин периодического действия.
4. Высокой экономичностью.
5. Независимостью от температурных и атмосферных условий.
Благодаря этим достоинствам, электрические двигатели широко применяются на стационарных и многих передвижных машинах. Недостаток их заключается в необходимости питающей сети.
Двигатели внутреннего сгорания используются главным образом на передвижных машинах (землеройных, грузоподъёмных, погрузочных и др.). Широкое применение на передвижных машинах объясняется их главным достоинством - независимостью от внешнего источника энергии, что придает машине большую маневренность. Основными недостатками двигателей внутреннего сгорания являются: отсутствие реверсивности и перегрузочной способности, необходимость применения коробки передач для изменения крутящего момента и реверсирования, зависимость от температурных условий и сравнительно малый срок службы.
Гидравлический привод состоит из насоса, системы распределения, рабочих цилиндров с поршнями и трубопровода. Насос приводится в действие обычно от электродвигателя или двигателя внутреннего сгорания.
К основным преимуществам гидравлического привода относятся:
1. Возможность изменения скоростей без применения передач, что позволяет уменьшить вес и габариты привода.
2. Большая надёжность в работе.
3. Широкие возможности регулирования.
4. Возможность работы при больших усилиях.
К недостаткам гидравлического привода относится необходимость установки (кроме двигателя) насосов и рабочих цилиндров.
Пневматический привод применяется лишь в некоторых типах вспомогательных устройств, чаще в тормозных устройствах, а иногда в устройствах управления. Этот привод, как и гидравлический, состоит из рабочих цилиндров с поршнями, системы распределения и трубопровода, но вместо жидкости, нагнетаемой насосом, применяется сжатый воздух, подаваемый компрессором. Недостатком пневматического привода является его небольшой КПД, в связи с падением давления сжатого воздуха.
Ходовое оборудование
Ходовое оборудование строительных и дорожных машин предназначено для перемещения машин в процессе работы или для их транспортировки с одного объекта строительства на другой. Ходовое оборудование по устройству классифицируется на гусеничное, пневмоколёсное, рельсовое и шагающее.
Рис. 1. Гусеничное ходовое оборудование: 1- гусеничная цепь;
2 – ведущая звездочка; 3 – направляющее колесо;4 – опорные катки; 5 – поддерживающие катки
Большинство строительных машин снабжены колёсным и гусеничным ходовым оборудованием (движителем). По условиям эксплуатации строительных машин (особенно машин для земляных работ) ходовое оборудование должно обеспечивать максимальную их проходимость по рыхлым, а иногда и сильно увлажненным грунтам. Проходимость машины при прочих равных условиях зависит от величины удельного давления движителя на грунт.
Гусеничное ходовое оборудование обладает большой площадью контакта с грунтом, поэтому удельное давление на грунт здесь ниже, чем в колёсном движителе. Машины на гусеничном ходовом оборудовании обладают большой проходимостью по рыхлым и грунтам с повышенной влажностью. Гусеничное ходовое оборудование (рис. 1) представляет собой гусеничную цепь 1, состоящую из шарнирных звеньев - траков, ведущие звёздочки 2, направляющие колеса 3, опорные 4 и поддерживающие катки 5 и подвеску, соединяющую раму трактора с ходовой частью.
Однако машины на гусеничном ходовом оборудовании по сравнению с колёсными транспортными средствами являются более тихоходными и в самом гусеничном механизме имеют большие потери на трение. Колёсный ход может быть создан как на базе колёс с жёстким недеформируемым ободом, так и на базе колёс, снабжённых пневматическими шинами. Жёсткие колёса применяют лишь в тех случаях, когда машина работает стационарно и колёса нужны для перемещения её с места на место на небольшое расстояние.
Применение пневмоколёсного движителя позволяет развивать дорожно-строительной машине более высокие скорости движения, по сравнению с гусеничным, смягчать толчки и частично поглощать удары, воспринимаемые колёсами от неровностей дороги. В пневмоколесном движителе составными частями (рис. 2) являются: покрышка 1, служащая прочной и эластичной оболочкой, камера 2, накачиваемая воздухом через вентиль 4, и ободная лента 3, предохраняющая камеру со стороны обода 5.
Рис. 2. Пневмоколесное ходовое оборудование: 1 – покрышка;
2 – камера; 3 – ободная лента; 4 – вентиль; 5 – обод
Существуют два основных типа шин: шины высокого давления (5...7 кг/см2) и шины низкого давления (1,75...5,5 кг/см2). Шины низкого давления имеют меньшую толщину стенок, они лучше поглощают удары, обеспечивают плавное движение и большее сцепление с грунтом за счёт увеличенного профиля, что улучшает их тяговые свойства. Маркировка шин наносится на боковой поверхности двумя числами через тире, например 14,00 - 20; 330 - 20 и т.д. Первое число характеризует ширину профиля в дюймах, а второе - внутренний диаметр шины или посадочный диаметр обода в дюймах.
Шагающее ходовое оборудование обеспечивает наименьшее удельное давление на грунт и из-за сложности конструкции применяется в крупных карьерах.
Лекция № 2. Соединения деталей машин
Крепления деталей на раме машины и между собой осуществляются при помощи подвижных и неподвижных соединений. Подвижные соединения обеспечивают требования кинематики машины. Неподвижные соединения необходимы для расчленения машины на узлы и детали при изготовлении, ремонте и транспортировании.
Неподвижные соединения подразделяются на разъёмные и неразъёмные. Разъёмные соединения позволяют разбирать сборочную единицу без повреждения деталей. К разъёмным соединениям относятся резьбовые, штифтовые, клиновые, шпоночные, шлицевые и клеммовые. Неразъёмные соединения не позволяют разбирать сборочную единицу без повреждения или разрушения деталей. К неразъёмным соединениям относятся сварочные и заклёпочные.
Резьбовые соединения
Резьбовые соединения деталей осуществляются с помощью резьбы, которая наносится на поверхность соединяемых деталей (винта и гайки) в виде винтовых канавок. Сечение этих канавок, т.е. профиль резьбы, может иметь прямоугольную, треугольную или трапецеидальную форму. По направлению винтовой линии различают правую и левую резьбу. Основными элементами, характеризующими резьбовые соединения, являются: профиль резьбы (рис. 3), наружный диаметр d, средний диаметрd2, внутренний диаметр d1, шаг S, угол профиля, высота профиля резьбы t.
Рис. 3. Элементы резьбового соединения
Если резьба нанесена на поверхности детали, то она называется наружной, а внутри детали - внутренней. Две детали, одна из которых имеет наружную резьбу (болт, винт), а другая - внутреннюю (гайка), образуют винтовую пару. Винтовые пары могут образовываться только при одинаковых параметрах резьбы.
На цилиндрическую поверхность детали одновременно может навиваться одна или несколько винтовых выступов, соответственно образуется одно-, двух-, трёх- и многозаходная резьба. В этих случаях следует различать два понятия: шаг резьбы и шаг винта. Шагом резьбы называется расстояние между двумя одинаковыми точками двух соседних витков резьбы, измеренных по образующей цилиндра. Шагом винта называется расстояние между одинаковыми точками одной и той же винтовой линии. У однозаходной резьбы шаг винта равен шагу резьбы. Во всех остальных случаях шаг винта во столько раз больше шага резьбы, сколько заходов имеет резьба.
Силы трения, а следовательно и торможения, в резьбе зависят от профиля резьбы. С увеличением угла профиля трение в резьбе увеличивается, поэтому прямоугольные, трапецеидальные и упорные резьбы (рис.4, а, б, в) применяют в подвижных винтовых соединениях для передачи движения, где требуются наименьшие потери на трение. Треугольные резьбы (рис. 4, г) применяют в крепёжных деталях, где большое трение в резьбе желательно для предотвращения самоотверчивания. Треугольные крепёжные резьбы стандартизированы. В машиностроении применяется метрическая резьба для диаметров 1...500 мм, имеющая угол профиля 60° и измеряемая в миллиметрах.
Рис. 4. Типы резьб: а – прямоугольные; б – трапецеидальные;
в – упорные; г – треугольные.
В зависимости от назначения применяют резьбы с крупным или мелким шагом, отличающиеся между собой размером шага при одном и том же диаметре.
К числу элементов, при помощи которых осуществляются резьбовые соединения, относятся болты, шпильки, винты, гайки (рис. 5).
Рис. 5. Крепежные детали: а – болтовое соединение; б – соединение шпилькой; в – винт
Сварочные соединения
Сваркой называют технологический процесс получения неразъёмного соединения металлических деталей с применением местного нагрева и использованием сил молекулярного сцепления. Различают два вида сварки:
1) сварка давлением или пластическая, при которой детали, доведённые до пластического состояния, за счёт приложения внешнего усилия соединяются в одно целое;
2) сварка плавлением, при которой расплавленные края деталей образуют общую жидкую ванну, превращающуюся после охлаждения в сварной шов.
В зависимости от способа нагрева сварка подразделяется на химическую (кузнечную, газовую, термитную) и электрическую (дуговую, контактную).
Наиболее распространенным видом сварки является электрическая дуговая, открытая в 1882 г. русским изобретателем Н.Н. Бенардосом и усовершенствованная в 1888 г. Н.Г. Славяновым. Схема сварки по методу Н.Г. Славянова показана на рис. 6.
Сварочные швы, применяемые в машиностроении и строительных конструкциях, отличаются большим разнообразием. По форме сечения наплавленного металла сварочные швы подразделяются на стыковые и валиковые. Стыковые швы отличаются один от другого сечением, определяемым предварительной подготовкой (разделкой) кромок соединяемых деталей (рис. 7):
- бесскосные швы (рис. 7,а) применяют при малых толщинах
свариваемых деталей;
- швы V-образные (рис. 7, в) применяют в тех случаях, когда
значительная толщина деталей не позволяет обеспечить значительный прогрев;
- шов U-образный (рис.7,г) лучше V-образного с точки зрения
расхода электроэнергии и металла, однако имеет более сложную разделку;
Рис. 6. Схема электродуговой сварки: 1 – источник тока; 2 – соединительный кабель; 3 – электродержатель; 4 – электрод; 5 – электрическая дуга; 6- деталь
Рис. 7. Основные типы разделки сварных швов: а – бесскосный; б – V-образный; в – Х-образный; г – U-образный; д – лобовой шов; е – косой валиковый шов
- шов Х-образный (рис.7, б) целесообразен при больших толщинах деталей, так как имеет малую площадь вырубки металла при
разделке.
Основным типом валикового шва является так называемый нормальный, с сечением в виде равнобедренного треугольника (рис 7, д, е). Размер сечения валикового шва определяется катетом шва К, при выполнении обычно равным толщине свариваемых листов металла. В зависимости от направления действующего усилия различают швы лобовые (рис. 7, д), расположенные перпендикулярно действующему усилию Р, и косые (рис. 7, е), расположенные под углом к действующему усилию.
Расчёт шва сварочных соединений на прочность ведётся в зависимости от типа соединения и вида шва. Для расчета принимают, что действующие усилия распределяются равномерно по длине шва а напряжения - равномерно по сечению.
Стыковые швы рассчитывают на растяжение или сжатие. При этом определяют длину шва, зависящую от действующей растягивающей силы Р, толщины свариваемых деталей и допускаемого напряжения на растяжение [G]p, которые зависят от марки электродов и материала свариваемых деталей. Длина шва в мм определяется по формуле:
Валиковые швы (угловые, лобовые) рассчитывают на срез:
где - допускаемое напряжение на срез наплавленного материала, кгс/мм2 (Па);
- катет шва, мм.
Заклёпочные соединения
Заклёпочные соединения (рис. 8) относятся к типу неразъёмных, так как для разъединения входящих в них деталей необходимо разрушить соединительную деталь - заклёпку.
Заклёпка представляет собой круглый стержень с головкой на одном конце. Головка с другой стороны образуется при осаживании заклёпки обжимкой (рис. 8, а). В процессе осаживания формируется не только головка, но осаживаемый металл стержня плотно заполняет отверстие, в котором находится заклёпка. Осаживание может осуществляться холодным способом, если диаметр заклёпки не превышает 10 мм, и горячим способом при диаметре более 10 мм.
Существуют различные типы заклёпок: с полукруглой головкой, с потайной головкой, с полупотайной головкой, полые.
В соединениях, находящихся под действием продольной нагрузки, заклёпки рассчитывают на срез и проверяют на смятие. Шаг установки заклёпок t (рис.8, б) зависит от их диаметра, назначения заклёпочного соединения и принятого расположения заклёпок. При параллельном их расположении t =3d (где d- диаметр стержня заклёпки). Чтобы заклёпка не прорезала соединяемые детали, расстояние 1 от оси заклёпки до свободной кромки в направлении действующей силы принимается равным (1,5... 2)d.
Необходимое число заклёпок определяется исходя из действующей нагрузки:
где Р - усилие, действующее на заклёпочное соединение, Н; - допустимое напряжение насрез материала заклёпки, кгс/мм2 (Па).
Рис. 8. Заклепочное соединение: а – обжимкой; б – схема установки заклепок
Проверку заклёпочного соединения производят на смятие по формуле:
где - толщина соединяемых деталей, мм; [G]cm - допустимое напряжение на смятие, кгс /мм2 (Па).
Дата добавления: 2018-06-01; просмотров: 846; Мы поможем в написании вашей работы! |
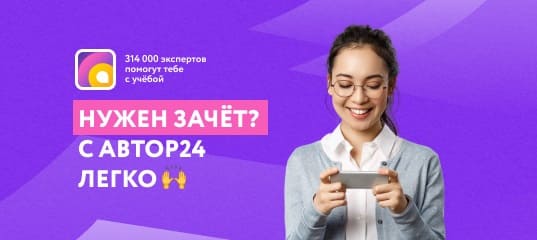
Мы поможем в написании ваших работ!