Определение усилия прошивочно-выгибного пресса
На прессе одновременно осуществляются три технологических операции: выгибка диска, прошивка центрального отверстия и калибровка обода. Поэтому полное усилие, развиваемое прессом:
Pполн= Р1+ Р2+ Р3 (92)
Pполн= 0,12+1,3+20=21,42 МПа
где Р1 – усилие, развиваемое прессом, при выгибке диска колеса, МН;
Р2 – усилие, развиваемое прессом, при прошивке отверстия в ступице колеса, МН;
Р3 – усилие, развиваемое прессом, при калибровке обода колеса, МН.
При производстве колёс с S-образным диском изгибающий момент будет в середине диска. Осевой момент сопротивления изгибу в середине диска рассчитывается по формуле, м3:
(93)
где Dср - диаметр колеса в середине диска, м.
(94)
где d и d1 – внутренний диаметр колеса и диаметр ступицы соответственно (размеры готового колеса в горячем состоянии), м.
Определяем усилие, развиваемое прессом, при выгибке диска колеса:
(95)
где l – длина сечения диска колеса, м.
Усилие, необходимое для прошивки отверстия, рассчитываем по формуле:
|
|
(96)
где K1 - коэффициент, учитывающий повышение усилия резания при затуплении штока, по экспериментальным данным K1= 1,3;
K 2-коэффициент перехода от сопротивления метала резанию к временному сопротивлению при растяжении, по экспериментальным данным K2= 0,6;
F –площадь поперечного сечения прорезаемого отверстия, м².
(97)
где d2 – диаметр отверстия в ступице (размеры готового колеса в горячем состоянии), м;
hвыд – толщина выдавливаемого металла, м (в условиях КБЦ АО «ЕВРАЗ НТМК» hвыд=50 мм).
Калибровка обода колеса заключается в его осаживании между штампов на небольшую величину.
Осадка колеса осуществляется усилием Р3 , которое рассчитывается по формуле:
P3= σs× K ф× F1 (98)
P3= 57·1,920·0,74=20 МПа
где – интенсивность деформации, МПа;
Кф – коэффициент формы заготовки в зависимости от значения коэффициента ϕ (значения в таблице 27).
|
|
Таблица 27
Вспомогательная таблица для расчетов усилия осаживания
Φ | 0 | 1 | 2 | 3 | 4 | 5 | 6 | 7 | 8 | 9 | 10 | 11 | 12 | 13 | 14 | 15 |
Kф | 1,000 | 1,087 | 1,175 | 1,398 | 1,580 | 1,751 | 1,920 | 2,088 | 2,255 | 2,422 | 2,589 | 2,755 | 2,922 | 3,089 | 3,255 | 3,422 |
Формула расчета коэффициента φ:
(99)
где D и В – наружный диаметр колеса и высота обода колеса в горячем состоянии, м;
В2 – высота обода колеса после прокатки, м.
F1 - площадь проекции чернового колеса после прошивочно-выгибного пресса, м2.
(100)
Расчет часовой производительности стана по профилю
На прессо-прокатной линии КБЦ АО «ЕВРАЗ НТМК» осуществляется производство заданного колеса из заготовки диаметром 430 мм. Высота заготовки зависит от профилеразмеров колес. Каждая новая заготовка подается на первый пресс линии через 61 секунду после подачи предыдущей. Время на капитальные и планово-предупредительные ремонты принять равным 17 суток.
Определяем часовую производительность линии, т/час
|
|
, (101)
где - число секунд в одном часе;
m0 - масса исходной заготовки, т;
- ритм прокатки;
Кр- расходный коэффициент при прокатке расчётного профиля на стане.
- коэффициент использования оборудования стана,
.
Определяем расходный коэффициент
(102)
, колес/час (103)
где Ачас.факт. – производительность линии в т/час;
т/час
колес/час
Определяем годовую производительность стана, колес/год
, (104)
где nф – фактическое число часов работы стана в году, в часах.
т/год
(105)
где ;
часа
nном – номинальное число часов работы стана в году, в часах.
(106)
где nкр, nппр – количество дней на капитальные и планово-предупредительные ремонты соответственно.
часа
Глава 3. Экономическая часть
|
|
Дата добавления: 2018-06-01; просмотров: 569; Мы поможем в написании вашей работы! |
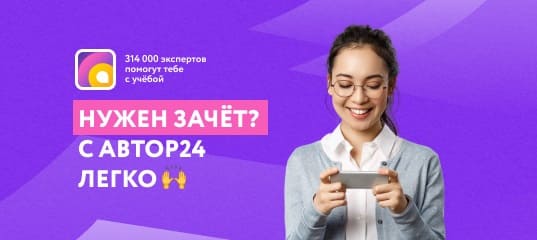
Мы поможем в написании ваших работ!