Технологический процесс производства цельнокатаного колеса ВА005 диаметром 920 мм
Оглавнение
Ведение.. 6
Глава 1. Общая часть.. 7
1.1 Техническая характеристика оборудования цеха. 7
1.2 Технологический процесс производства цельнокатаного колеса ВА005 диаметром 920 мм. 10
1.3 Сортамент цеха. 21
1.4 Технико-экономические показатели работы цеха. 24
1.5 Анализ калибровки рабочего инструмента прошивно-выгибного пресса. 26
ГЛАВА 2. СПЕЦИАЛЬНАЯ ЧАСТЬ.. 28
2.1 Расчет калибровки рабочего инструмента для производства цельнокатаного колеса ВА005 диаметром 920 мм. 28
2.2 Расчет энергосиловых параметров прокатки. 50
2.3 Расчет энергосиловых параметров прессов. 57
2.3.3 Определение усилия прошивочно-выгибного пресса. 61
2.4 Расчет часовой производительности стана по профилю.. 63
Глава 3. Экономическая часть.. 66
3.1 Расчет амортизационных отчислений основных средств. 66
3.2 Расчет показателей использования оборотных средств. 67
3.3 Расчет количественных характеристик персонала. 68
3.4 Расчет фонда оплаты труда работников. 70
3.5 Расчет себестоимости цельнокатаного колеса ВА005 диаметром 920 мм. 74
3.6 Расчет прибыли и рентабельности от реализации продукции. 75
Глава 4. Охрана труда и промышленная безопасность.. 78
4.1 Защита от шума и вибрации. 78
4.2 Микроклимат производственных помещений. 79
Заключение.. 81
Список использованных источников.. 82
Ведение
Нижнетагильский металлургический комбинат, ежегодно увеличивая выпуск железнодорожных колес различного назначения в рамках текущих контрактов, проводит политику самосовершенствования производства, повышает качество продукции в соответствии с требованиями рынков, как внутреннего, так и внешнего. Так же предприятие регулярно осваивает новые колесные профиля для расширения географических поставок.
|
|
Основное назначение колесопрокатного стана – производство цельнокатаных колес и заготовок колес для грузовых составов, тепловозов, электровозов, вагонов метрополитена, железных дорого узкой колеи и другого оборудования.
Целью моего проекта является разработка технологического процесса производства колеса ВА005 диаметром 920 мм по европейским стандартам с целью расширения сортамента в условиях колесобандажного цеха АО «ЕВРАЗ НТМК». Данный профиль эксплуатируется во многих европейских странах на подвижных составах железных дорог. Специально для данного вида профиля в конверторном цехе производят марку стали ER7, которая отличается высокими прочностными и качественными характеристиками.
Основной задачей дипломного проекта является разработка технологического процесса производства колеса ВА005 диаметром 920 мм. Для достижения поставленной задачи в ходе исследования были произведены расчеты калибровки рабочего инструмента деформации – прессов и колесопрокатного стана, а также проверка полученных результатов по энергосиловым параметрам.
|
|
Глава 1. Общая часть
Техническая характеристика оборудования цеха
Техническая характеристика пил
Назначение – порезка цилиндрических круглых заготовок под прямым углом из углеродистой и легированной стали с максимальной прочностью 1300 Н/мм2. Количество пил – 7 шт. Режущий инструмент - пильные круги с твердосплавными пластинками.
Таблица 1
Характеристика пильного круга
Диаметр, мм | Количество зубьев, шт. | Диаметр разрезаемой заготовки, мм |
1430 | 54 | от 200 до 450 |
1700 | 50 | от 200 до 575 |
Ширина реза – до 11 мм.
Длина разрезаемых заготовок - от 2800 до 6600 мм.
Размеры штучных заготовок при автоматическом режиме порезки:
длина, мм 260-810
масса, кг 300-915
Таблица 2
Техническая характеристика нагревательной печи
Наименование оборудования | Параметр |
Кольцевая печь LOI | Назначение - нагрев заготовок под прокатку. |
Нагреваемый металл - заготовки из углеродистой и легированной стали. | |
Диаметр заготовок – 430 мм | |
Длина заготовок – 300-1030 мм |
|
|
Продолжение таблицы 2
| Температура выдачи заготовок – 1260 С |
Равномерность нагрева - +/- 15 С | |
Вид топлива – природный газ | |
Максимальное количество заготовок в садке – 462 шт | |
Максимальная производительность – 47 т/ч | |
Число зон автоматического регулирования - 6 |
Техническая характеристика прессопрокатной линии
Таблица 3
Характеристика оборудования прессопрокатной линии
Оборудование | Назначение |
Манипулятор (тип 1075) – робот № 1 | Передача заготовки из начальной точки участка колесопрокатного стана на гидросбив |
Гидросбив окалины | Удаление печной окалины |
Манипулятор (тип 1073) – робот № 3 | Передача заготовки от гидросбива на первый пресс |
Центрователь первого пресса | Центровка заготовки относительно оси пресса |
Первый пресс (усилие - 5000 т) | Осадка заготовки в «плюшку» |
Манипулятор (тип 1074-1) – робот № 5 | Передача заготовки от первого пресса ко второму прессу |
Центрователь второго пресса | Центровка заготовки относительно оси пресса |
Второй пресс Усилие - 9000 т | Формовка заготовки с выполнением отверстия с перемычкой |
Манипулятор (тип 1074-1) – робот № 7 | Передача заготовок от второго пресса к колесопрокатному стану |
Колесопрокатный стан (DRAW 1400) Тип - пятивалковый вертикальный | Прокатка диска и элементов обода заготовки |
Манипулятор (тип 1072-2) – робот № 9 | Передача заготовок от колёсопрокатного стана к третьему прессу |
Третий пресс Усилие - 5000 т | Калибровка заготовки с выгибкой диска и прошивкой отверстия ступицы |
|
|
Продолжение таблицы 3
Манипулятор (тип 1074-2) – робот № 11 | Передача заготовки с третьего пресса на маркировочный пресс и измерительную установку |
Маркировочный пресс | Нанесение клейма на обод с наружной стороны колеса |
Измерительная машина - лазерная установка | Контроль геометрических размеров колес |
Манипулятор (тип 1076) – робот № 14 | Уборка колёс с лазерной установки на ленты транспортера холодильника |
Таблица 4
Характеристика оборудования для термообработки колес
Наименование оборудования | Характеристика |
Закалочная печь | Назначение – нагрев колес под закалку |
Количество – 2 шт. | |
Число зон автоматического регулирования – 8 | |
Топливо – природный газ | |
Закалочные машины | Количество – 12 шт. |
Закалочная среда – вода | |
Отпускные печи | Количество 2 шт. |
Число зон автоматического регулирования теплового режима – 10 | |
Топливо – природный газ | |
Максимальная производительность – 22,4 т/ч |
Таблица 5
Характеристика оборудования механообработки колес
Наименование оборудования | Характеристика |
Станки модели VDM 120-12 | Назначение – механическая полнопрофильная обработка колёс. |
Тип карусельный специальный с числовым программным управлением | |
Количество 8 шт. |
Продолжение таблицы 5
| Наибольший диаметр колес по кругу катания 1600 мм |
Наименьший диаметр колеса по кругу катания 710 мм | |
Установка для считывания маркировки | Количество знаков считываемой группы – 6 |
Максимальная глубина знаков маркировки 7 мм | |
Высота знаков 10-12 мм | |
Станок NBH 290-2 | Назначение – выполнение специальных отверстий и чистовой расточки ступицы. |
Тип – обрабатывающий центр. | |
Количество 1 шт. | |
Балансировочная машина | Назначение – устранение дисбаланса железнодорожных колес |
Тип – BVK-13-FH1 |
Таблица 6
Техническая характеристика линии выходного контроля
Наименование оборудования | Характеристика |
Линия выходного контроля | Производительность 48 шт/ч |
Расчётное время обработки одного колеса 75 с | |
Наружный диаметр колеса, 920-1070 мм | |
Установки магнитолюминесцентного контроля колёс | Количество 2 шт. |
Производительность 24 шт./ч | |
Установка дробемётного упрочнения | Наружный диаметр колёса, 790-1070 мм |
Количество дробемётов 1 шт. | |
Установка покраски колёс | Количество 1 шт. |
Технологический процесс производства цельнокатаного колеса ВА005 диаметром 920 мм
В условиях колесобандажного цеха АО «ЕВРАЗ НТМК» цельнокатаное колесо ВА005 диаметром 920 мм изготавливают из стали марки ER7.
Таблица 7
Химический состав стали марки ER7
Марка стали | C | Si | Mn | P | S | Cr | Cu | Mo | Ni | V | Cr+Mo+Ni |
Максимальное содержание, % | |||||||||||
ER7 | 0,52 | 0,40 | 0,80 | 0,020 | 0,020 | 0,30 | 0,30 | 0,08 | 0,30 | 0,06 | 0,50 |
Массовая доля водорода в жидкой стали не должна превышать 2 ppm.
После полного цикла производства цельнокатаного колеса ВА005, колеса данного вида приобретают механические свойства согласно таблице 8,
Таблица 8
Механические свойства стали
Марка стали | Обод | Диск | |||
Временное сопротивление Rm, Н/мм2 | Предел текучести ReH, Н/мм2 | Относительное удлинение, % | Временное сопротивление Rm, Н/ММ2 | Относительное удлинение, % | |
ER7 | 820-940 | >520 | >14 | >680 | >16 |
Подготовка исходного полупродукта
Порезка заготовок производится поплавочно. Штучные заготовки с разгрузочного стола передаются на стеллажи и укладываются поплавочно в штабель с помощью специальных захватов. До укладки в штабель каждую штучную заготовку маркируют на боковой поверхности известью номером плавки, номером ручья и номером НЛЗ. Раскрой НЛЗ производиться по ТК-011-82-2016 [16].
Таблица 9
Карта раскроя НЛЗ по чертежу 00186269-195
Количество заготовок | Длина заготовок суммарная, мм | Ширина резов суммарная, мм | Длина НЛЗ, мм, не менее | Масса заготовки, кг |
- | головная обрезь 50 | 10 | 2800 | 460 |
Продолжение таблицы 9
1 | 402 | 20 | 2800 | 460 |
2 | 804 | 30 | ||
3 | 1206 | 40 | ||
4 | 1608 | 50 | ||
5 | 2010 | 60 | ||
6 | 2412 | 70 | ||
7 | 2814 | 80 | 3024 | |
8 | 3216 | 90 | 3436 | |
9 | 3618 | 100 | 3848 | |
10 | 4020 | 110 | 4260 | |
11 | 4422 | 120 | 4672 | |
12 | 4824 | 130 | 5084 | |
13 | 5226 | 140 | 5496 | |
14 | 5628 | 150 | 5908 | |
- | донная обрезь 80 | - | - |
Нагрев заготовки перед деформацией
Передача заготовок для посада в печь осуществляется при наличии паспорта поплавочно. Заготовки к нагревательной печи передаются по одной в горизонтальном положении по специальному рольгангу и подаются в позицию под загрузочную машину таким образом, чтобы клещевой захват загрузочной машины брал заготовку по центру тяжести. Загрузка печи в ряду начинается от внутренней стенки. Заданная температура по зонам печи определяется, исходя из длительности нагрева. Перед и после посада штучных заготовок производится разрыв в печи в 10 рядов.
Таблица 10
Температура в зонах печи
Время нагрева, ч-мин | Температура в зонах, °С | ||||||
1 | 2 | 3 | 4 | 5 | 6.1 | 6.2 | |
4-30 – 6-30 | не более 900 | не более 1080 | 1220+10 | 1300±10 | 1300±10 | 1300±10 | Зона выдачи |
6-31 – 8-00* | 1170±10 | 1270±10 | 1280±10 | 1280±10 |
Выдача заготовок из печи производится разгрузочной машиной. Заготовки извлекаются из печи и устанавливаются на рольганг, по которому доставляются к роботу-манипулятору прессопрокатного участка.
Удаление окалины
Заготовка захватывается портальным роботом № 1 и перемещается в камеру гидросбива для удаления окалины. На первом этапе заготовка удерживается над нижним коллектором, включается высокое давление воды, и производится удаление окалины с нижнего торца заготовки. Затем заготовка перемещается далее и устанавливается на поворотный стол. Во время поворота заготовки включаются боковой и верхний коллекторы, и выполняется удаление окалины с верхней торцевой и боковой поверхностей. Заготовка захватывается роботом № 3 и транспортируется на первый пресс.
Обжатие на первом прессе
После уборки предыдущей заготовки, выполнения охлаждения и смазки, отхода охлаждающей траверсы робот вносит заготовку в межколонное пространство и опускает на нижний штамп. Температура заготовки перед обжатием на прессе должна быть не менее 1000 °С. Клещевины робота выводятся из рабочего пространства пресса, заготовка при необходимости центрируется, и включается перемещение траверсы.
По окончании обжатия траверса останавливается в верхней точке, достаточной для извлечения заготовки. Одновременно с началом подъёма траверсы включается выталкивание пуансоном заготовки из калибровочного кольца. После освобождения заготовки производится снятие заготовки с нижнего штампа роботом № 5 и вывод её из рабочего пространства пресса.
Обжатие на втором прессе
Технология обжатия на втором прессе аналогична технологии обжатия на первом прессе.
Прокатка на стане
После установки заготовки и вывода клещевин манипулятора из рабочего пространства стана включаются приводы стана. В соответствии с программой выполняется прокатка заготовки.
По окончании деформации заготовка останавливается, эджерные валки отводятся. Клещевины робота № 9 захватывают и зажимают заготовку. Валки стана освобождают заготовку, и робот выводит её из рабочего пространства стана.
Обжатие на третьем прессе
После укладки заготовки пресс выполняет незначительно обжатие обода по высоте, выгибку диска, прошивку отверстия. Выталкиватель поднимает заготовку над нижним штампом. Робот № 11 захватывает заготовку, выносит её из рабочего пространства третьего пресса. При нахождении заготовки на прессе производится измерение температуры заготовки. По окончании транспортных операций траверса с коллектором смазки и охлаждения вводится в межштамповое пространство.
Выполнение маркировки
Заготовка роботом № 11 укладывается на опорную плиту. Клещевины робота № 11 отводятся. Маркировочный пресс выполняет рабочий ход траверсы. Временная горячая маркировка заготовок колес наносится на боковой поверхности обода с наружной стороны заготовки колеса. Расстояние oт кромки внутренней поверхности до основания знаков маркировки не регламентируется. Высота знаков маркировки - от 10 до 12 мм, глубина - не более 2 мм.
Маркировка наносится в следующем порядке:
- номер плавки - 6 знаков;
- месяц и две последние цифры года изготовления - 4 знака;
- условная марка стали - R7;
- номер заготовки колеса по системе нумерации предприятия изготовителя - 6 знаков.
Термообработка колес
После завершения технологических операций на прессопрокатной линии колеса передаются на ленточный транспортер и затем на стопосборщик для формирования стоп и последующим складированием на участок отделки. Одной из подготовительной операции перед термообработкой является расчет углеродного эквивалента. В зависимости от его значения выбирается термообработка колес. Данные углеродного эквивалента берутся из паспорта плавки или рассчитывается по формуле:
(1)
где Si, Mn, Cr, Mo, C – массовые доли элементов в стали в процентах.
Значение Сэкв округляется до третьего знака после запятой.
Таблица 11
Значения углеродного эквивалента по группам
Номер группы | 1 | 2 | 3 |
Значение Сэкв | 0,690-0,725 | 0,726-0,740 | 0,741-0,760 |
Нагрев под закалку
В зависимости от группы стали по углеродному эквиваленту выбирают режимы нагрева под закалку. [2]
Таблица 12
Режим нагрева под первичную закалку для группы 1 и 2
Температура, °С по зонам печи | |||||||
Зона 1 | Зона 2 | Зона 3 | Зона 4 | Зона 5 | Зона 6 | Зона 7 | Зона 8 |
не более 700 | не более 740 | 800±10 | 840±10 | 860±10 | 860±10 | 860±10 | не более 860 |
Таблица 13
Режим нагрева под первичную закалку для группы 3
Температура, °С по зонам печи | |||||||
Зона 1 | Зона 2 | Зона 3 | Зона 4 | Зона 5 | Зона 6 | Зона 7 | Зона 8 |
не более 700 | не более 740 | 800±10 | 840±10 | 850±10 | 850±10 | 850±10 | не более 850 |
Заготовки колес с отклонениями от предельных значений температур нагрева отправляются на повторную термообработку.
Таблица 14
Режим нагрева под повторную закалку для групп 1 и 2
Температура, °С по зонам печи | |||||||
Зона 1 | Зона 2 | Зона 3 | Зона 4 | Зона 5 | Зона 6 | Зона 7 | Зона 8 |
не более 700 | не более 740 | 800±10 | 840±10 | 880±10 | 880±10 | 880±10 | не более 880 |
Таблица 15
Режим нагрева под повторную закалку для группы 3
Температура, °С по зонам печи | |||||||
Зона 1 | Зона 2 | Зона 3 | Зона 4 | Зона 5 | Зона 6 | Зона 7 | Зона 8 |
не более 700 | не более 740 | 800±10 | 840±10 | 870±10 | 870±10 | 870±10 | не более 870 |
Длительность нагрева под первичную и повторную закалку – от 3 ч 00 мин до 3 ч 30 мин.
Закалка
После нагрева печные телеги с колесами из нагревательных печей достаются толкателем трансбордера, встают на позицию разгрузки, откуда в дальнейшем колеса забирает робот-манипулятор и транспортирует их на закалочные машины. В закалочных машинах, оборудованных тремя распылительными кольцами, проводится охлаждение обода.
Отпуск
Температура отпуска устанавливается в соответствии с таблицей 16.
Таблица 16
Режим отпуска колес
Температура, °С, по зонам печи | Общее время нахождения колес в печи, ч | |||||||||
1 | 2 | 3 | 4 | 5 | 6 | 7 | 8 | 9 | 10 | |
не более 400 | 450 | 520 | 520 | 520 | 520 | 520 | 520 | 520 | не более 520 | от 2,5 до 4 |
Предельные отклонения температуры в зонах печи ±10 °С. После отпуска заготовки собираются в стопы, стопы выставляются для охлаждения на оборудованные защитными экранами поддоны (термоса).
Механическая обработка
Полнопрофильная механическая обработка заготовок колес производится на участке полнопрофильной обработки колес (УПОК) КБЦ на станках модели VDM 120-12. На всех этапах производства должны использоваться грузозахватные приспособления, обеспечивающие защиту колес от повреждений.
После механической обработки первой заготовки колеса производится измерение всех размеров согласно методике контроля геометрических параметров и качества поверхности, на стендах визуального осмотра. При механической обработки горячая маркировка должна полностью удаляться. Для идентификации колес после механообработки и до транспортирования стопы на промежуточный склад колес, оператором станков модели VDM 120-12 на поверхность катания колеса, предварительно протертую сухой тканью или обтиром, наклеивается стикер с штрих-кодом. [2]
Стикер содержит следующую информацию:
- порядковый номер колеса по системе предприятия-изготовителя - 6 знаков;
- номер чертежа;
- номер плавки - 6 знаков;
- марка стали;
- штрих-код.
После нанесения временной маркировки маркером, колеса должны находиться на промежуточном складе не менее 1 ч.
Маркировка колес
Основная маркировка механически обработанных колес производится в холодном состоянии штамповкой (клеймением) на автоматическом маркировщике модели STMS 10/15 или при помощи переносного ручного маркировщика на стендах визуального осмотра или на линии выходного контроля (ЛВК) № 2. Основная маркировка наносится на торцевой поверхности ступицы с внутренней стороны колеса.
Маркировка выполняется знаками высотой (10±1) мм по часовой стрелке в следующем порядке:
- номер плавки - 6 знаков;
- обозначение предприятия-изготовителя - EV;
- порядковый номер колеса по системе нумерации предприятия- изготовителя - 6 знаков;
- месяц и две последние цифры года изготовления - 4 знака;
- марка стали - ER7;
- тип конструкции
Клеймо о прохождении технического контроля наносится после маркировки типа конструкции. Знаки маркировки должны читаться от центра колеса. Расстояние между группами знаков не нормируется. Глубина знаков маркировки не менее 0,2 мм.
Приемка колес
Колесо при помощи тележки подаётся на пост визуального осмотра №1 (далее – ВО-1) для контроля колеса с наружной стороны. Контролёр УТК ПЖДП на посту ВО-1 на каждом колесе производит визуальный осмотр поверхности и проводит измерения следующих параметров колеса.
По результатам контроля на поверхность катания колес при помощи трафарета белой несмываемой краской для колес наносится фактический диаметр по кругу катания с точностью до 0,1 мм. Фактический диаметр колеса определяется по результатам контроля геометрических параметров колеса. Обозначение диаметра колеса должно быть хорошо читаемо, высота цифр от 60 до 110 мм. Основания знаков маркировки - у гребня колеса. Упрочнение дисков колес дробью не производится. При приемке производится наклейка стикеров.
Нанесение антикоррозионного покрытия
Перед нанесением антикоррозионного покрытия поверхности колес с коррозией и вмятинами подвергаются очистке и ремонту мелкозернистой шлифовкой в пределах допусков на размеры (за исключением поверхности катания и чистового отверстия ступицы). Не подвергаются покраске следующие поверхности колеса:
- поверхность катания;
- боковая поверхность обода с наружной и внутренней стороны колеса;
- поверхность отверстия в ступице.
Нанесение консервационного покрытия
Перед нанесением консервационного покрытия поверхности колес с коррозией и вмятинами подвергаются очистке и ремонту мелкозернистой щлифовкой в пределах допусков на размеры (за исключением поверхности катания и чистового отверстия ступицы).
После нанесения консервационного покрытия на поверхность катания колес, предназначенных для отгрузки в Deutsche Bahn, в двух диаметрально противоположных направлениях наклеиваются этикетки с штрих-кодом, содержащие следующую информацию:
- обозначение конструкции колеса
- номер чертежа предприятия-изготовителя;
- номер плавки - 6 знаков;
- номер колеса по системе нумерации предприятия-изготовителя;
- фактический диаметр колеса по кругу катания с точностью до 0,1 мм.
Низ этикетки должен располагаться у гребня колеса, верх - у наружной стороны колеса.
Упаковка и отгрузка колес
На одной кассете допускается отгрузка колес не более чем одной плавки/партии. При упаковке колес в каждой партии допускается доукомплектовывать не более двух кассет колесами других плавок/партий. Между всеми колесами в кассете, а также под нижнее и на верхнее колеса в кассете укладывается бумага с летучими ингибиторами коррозии. Для защиты от попадания влаги под упаковку сверху на защитный контейнер надевается полимерная пленка и уплотнитель для плотного прилегания защитного контейнера и полимерной пленки. Для защиты холодной маркировки верхнего колеса в кассете между торцом поверхности ступицы с внутренней стороны и стяжными болтами применяется «защитное металлическое кольцо». После удовлетворительного результата визуального осмотра на поверхность металлической кассеты или верхнюю часть деревянной поверхности прижимной планки наносится стикер с индивидуальным штрих кодом, номером кассеты, номером чертежа колес и указанием номеров колес в кассете.
Сортамент цеха
Таблица 17
Сортамент колесобандажного цеха
Наименование продукции | Назначение | Норм. документ на профиль | Ном. Ø по кругу катания, мм | Ø отверстия в ступице, мм | Масса, кг | Марка стали | Норм. документ на тех. требования |
Колесо ц/к с плоскоконическим диском | Для грузовых вагонов | 957 | 175/190 | 398/ 392 | 2, Т | ГОСТ 10791 | |
Чертёж 00186269-162, | |||||||
Чертёж 00186269-163 | |||||||
Колесо ц/к с плоскоконическим диском для ремонтных целей | Для грузовых вагонов | Чертёж 00186269-164, Чертёж 950А | 945 | 175/190 | 374/ 368 | 2 | |
Колесо ц/к | Для спец. подвижного состава | Чертёж 010 | 710 | 145 | 300 | 2 | ГОСТ 10791 |
Колесо ц/к | Для спец. подвижного состава | Чертёж 012 | 1050 | 172 | 468 | 2 | |
Колесо ц/к | Для тепловозов | Чертёж 8ТС.224.042 | 1050 | 248 | 478 | Т |
Продолжение таблицы 17
Заготовка колеса | Для метрополитена | Чертёж 073В-1 | 803 | 151 | 299 | 2 | ГОСТ 10791, ТУ 0943-286-01124323 | |
Заготовка колеса | Для метрополитена | Чертёж 124-1 | 875 | 166 | 322 | 2 | ГОСТ 10791, | |
ТУ 0943-286-01124323 | ||||||||
Заготовка колеса | Для метрополитена | Чертёж 125-1 | 875 | 166 | 322 | 2 | ||
Заготовка колеса ц/к с плоскоконическим диском | Для грузовых вагонов | Чертёж 00186269-147 | 964 | 147 | 465 | 2, Т | ТУ 0943-022-00186269, ГОСТ 10791 | |
Заготовка колеса ц/к с криволинейным диском | Для грузовых вагонов | Чертёж 00186269-149 | 968 | 177 | 515 | Т | ||
Колёсный центр | Для электровозов | Чертёж 2ЭС6.31.110.007 | 1073 |
![]() | 420 | М | ТУ 14-2Р-444 | |
Колёсный центр | Для электровозов | Чертёж НТМК/ЭП2К.31.15.102 | 1070,6 | 232,5 | 484 | М | ||
Колёсный центр | Для тепловозов | Чертёж 00186269-156 | 906 |
![]() | 331 | М | ГОСТ 55498 |
Продолжение таблицы 17
Заготовка зубчатого колеса | Для локомотивов | Чертёж 077А-2 | 1005 | 285 | 400 | 55Ф | ТУ 14-2Р-343 |
Заготовка зубчатого колеса | Для локомотивов | Чертёж 128 | 990 | 202 | 415 | 45ХН, 55Ф,20Х2Н4А | Тех. Соглашение |
Заготовка кранового колеса | Для кранов | Чертёж 00186269-180 | 1010 |
![]() | 1014 | 2 | ГОСТ 10791 |
Заготовка кранового колеса | Для кранов | Чертёж 00186269-186 | 695 |
![]() | 546 | 2 | ГОСТ 10791 |
Колесо ц/к с криволинейным диском | Для грузовых вагонов | Чертёж 00186269-002 | 920 | 180/185 | 326/323 | ER7 | EN13262:2004+A2 |
Колесо ц/к с криволинейным диском | Для грузовых вагонов | Чертёж 00186269-006 | 920 | 199/205 | 337/334 | ER7 | |
Колесо ц/к с криволинейным диском | Для грузовых вагонов | Чертёж 00186269-014 | 920 | 179/185 | 357/354 | ER7 | ТУ 0943-030-00186269, EN13262:2004+A2 |
Колесо ц/к с криволинейным диском | Для электровозов | Чертёж 00186269-192 | 1092,2 | 244,3 | 565 | Класс B | |
Колесо ц/к с криволинейным диском | Для грузовых вагонов | Чертёж 00186269-194 | 920 | 193/200 | 316/313 | ER7 | EN 13262:2004+A2 |
Колесо ц/к с криволинейным диском | Для грузовых вагонов | Чертёж 00186269-195 | 920 | 180 | 327 | ER7 |
Продолжение таблицы 17
Колесо ц/к с криволинейным диском | Для грузовых вагонов | Чертёж 00186269-198 | 920 | 193 | 316 | ER7 | EN 13262:2004+A2 |
Заготовка колеса ц/к с криволинейным диском | Для грузовых вагонов | Чертёж 00186269-166 | 935 | 156 | 494 | ER7 | ТУ 0943-019-00186269, EN 13262:2004+A2 |
Заготовка колеса ц/к с криволинейным диском | Для грузовых вагонов | Чертёж 00186269-167 | 934 | 188 | 430 | ER7 |
Дата добавления: 2018-06-01; просмотров: 1328; Мы поможем в написании вашей работы! |
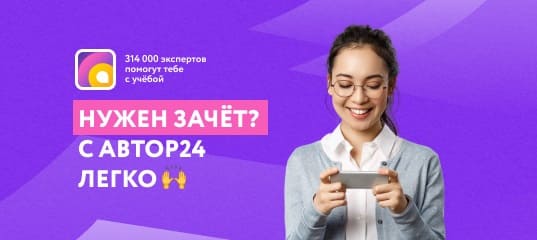
Мы поможем в написании ваших работ!