Технико-экономические показатели работы цеха
Технико-экономические показатели работы цеха за 2016 год представлены в таблице 18.
Таблица 18
Технико-экономические показатели цеха за 2016 год
Наименование | Колесопрокатный стан | |||
2015 год | 2016 год | |||
месяц | с нач. года | месяц | с нач. года | |
Годный прокат |
|
|
|
|
План,тн | 5 100 | 83 709 | 9 899 | 104 473 |
Факт,тн | 6 910 | 87 266 | 11 821 | 90 606 |
% | 135,5 | 104,2 | 119,4 | 86,7 |
откл.,+,- | 1 810 | 3 557 | 1 922 | -13 867 |
Отгрузка тов.продукции |
|
|
|
|
План,тн | 5 282 | 91 152 | 9 930 | 104 255 |
Факт,тн | 7 288 | 90 078 | 10 413 | 86 375 |
Продолжение таблицы 18
% | 138,0 | 98,8 | 104,9 | 82,8 | ||
откл.,+,- | 2 006 | -1 074 | 483 | -17 880 | ||
Отгрузка п/ф |
|
|
|
| ||
План,тн |
| 284 |
| 0 | ||
Факт,тн |
| 208 |
| 0 | ||
откл.,+,- |
|
|
|
| ||
Капитальный ремонт |
|
|
|
| ||
План, сут. | 0 | 0 | 0 | 10 | ||
час | 0,00 | 0,00 | 0,00 | 240,00 | ||
Факт, сут | 0,00 | 0,00 | 0,00 | 9,96 | ||
час | 0,00 | 0,00 | 0,00 | 239,03 | ||
Номинальное время |
|
|
|
| ||
План, сут. | 22,00 | 265,00 | 29,50 | 262,50 | ||
час | 528 | 6 360 | 708 | 6 300 | ||
Факт, сут | 24,59 | 290,08 | 23,73 | 286,31 | ||
час | 590,083 | 6962 | 569,463 | 6872 | ||
Текущие простои |
|
|
|
| ||
План, час | 116 | 1 399 | 156 | 1 386 | ||
% | 22,0 | 22,0 | 22,0 | 22,0 | ||
Факт, час | 317,33 | 3352,17 | 192,47 | 3412,89 | ||
% | 53,8 | 48,1 | 33,8 | 49,7 | ||
Фактическое время |
|
| ||||
План, час | 411,840 | 4 960,800 | 552,240 | 4 914,000 | ||
Факт, час. | 272,750 | 3 609,831 | 376,994
| 3 458,642 | ||
Производительность |
|
|
| |||
в фактический час |
|
| ||||
План, тн/час | 12,38 | 16,87 | 17,93 | 21,26 | ||
Факт, тн/час | 25,34 | 24,17 | 31,36 | 26,20 | ||
в номинальные сутки |
| |||||
План, тн | 232 | 316 | 336 | 398 | ||
Факт, тн | 281 | 301 | 498 | 316 | ||
Брак |
|
| ||||
Всего,тн | 371,038 | 4 120,207 | 58,992 | 2 113,676 |
Продолжение таблицы 18
в том числе: |
|
| ||
по металлу, тн | 176,751 | 2 239,077 | 11,131 | 887,992 |
по прокату, тн | 194,287 | 1 881,130 | 47,861 | 1 225,684 |
Всего,% | 5,08 | 4,49 | 0,49 | 2,22 |
в том числе: |
|
| ||
по металлу,% | 2,42 | 2,44 | 0,09 | 0,93 |
по прокату,% | 2,66 | 2,05 | 0,39 | 1,29 |
НЗП |
|
| ||
на начало месяца | 2 676 |
| 5 063 | |
на конец месяца | 2 228 |
| 6 392 | |
Отклонение |
| |||
Всего,тн | 1 810 | 3 557 | 1 922 | -13 867 |
в том числе: |
|
| ||
Производительность | 3 533 | 25 486 | 5 063 | 14 900 |
текущие простои | -2 491 | -31 940 | -658 | -42 404 |
капитальный ремонт | 0 | 0 | 0 | 19 |
выходные дни | 769 | 9 582 | 0 | 15 137 |
ППР | 0 | 429 | -2 483 | -1 519 |
Расход металла на 1 тн проката |
|
| ||
план, кг/тн | 1 301 | 1 321 | 1 219 | 1 256 |
факт, кг/тн | 1 314 | 1 315 | 1 215 | 1 267 |
экономия (-), перерасход (+) | 94 | -495 | -52 | 1 027 |
Анализ калибровки рабочего инструмента прошивно-выгибного пресса
|
|
Калибровка нажимных роликов, коренного валка и направляющих роликов должна обеспечивать получение требуемых размеров и высокое качество колес, а, следовательно, наибольший выход годного. При этом следует различать калибровку для чистокатаных и чернокатаных колес, подвергающих механической обработке.
Рисунок 1 - Нижний штамп выгибного пресса
Калибровка инструмента для формирования поверхности катания должна гарантировать минимальный съем стружки по диаметру колеса с цель сохранения наиболее износостойкого поверхностного слоя. При этом гребень колеса должен конструироваться с учетом возможности путем удаления дефектов по диаметру. Форма и расположение гребня на готовом колесе играют при этом значительную роль. Что касается чистокатаного колеса, то форма и размеры гребня, а так же профиль катания должны максимально приближаться к профилю обточенного колеса.
Размеры штампов выгибного пресса должны полностью соответствовать заданной конфигурации диска и внутренней поверхности обода. Величина прогиба диска выбирается из условия сохранения в готовом колесе требуемого размера между наружной боковой поверхностью обода и наружным торцевом ступицы-«утопания».
|
|
Верхний штамп должен свободно входить в полость, образованную ободом и ступицей, исправляя лишний эксцентриситет ступицы относительно внутренней поверхности обода.
ГЛАВА 2. СПЕЦИАЛЬНАЯ ЧАСТЬ
Расчет калибровки рабочего инструмента для производства цельнокатаного колеса ВА005 диаметром 920 мм
Принципы калибровки инструмента деформации при производстве колес не отличаются от общих принципов калибровки инструмента при производстве других изделий методами штамповки или прокатки. Калибровка инструмента деформации осуществляется в порядке, обратном ходу технологического процесса. На АО «ЕВРАЗ НТМК» существует следующий порядок операций на прессо-проктаной линии:
1. осадка в кольце;
2. штамповка;
3. прокатка на колесопрокатном стане;
4. выгибка диска и прошивка отверстия.
Соответственно, расчет калибровки необходимо начинать с последней операции.
Определение черновых и горячих размеров колеса
Основные размеры цельнокатаного колеса приведены на рисунке 2
Рисунок 2 - Основные размеры цельнокатаного колеса
Для проектирования калибровки необходимо с учетом допусков определить расчетные размеры колеса. Затем с учетом припусков на механическую обработку и изменения взаимного расположения отдельных элементов в результате термической обработки установить размеры колеса до его механической и термической обработки (так называемого чернового колеса) и рассчитать размеры горячего колеса, полученного с последнего агрегата прессо-прокатной линии.
|
|
Для экономии металла при производстве колес доля допуска, используемая при калибровке и величина припуска на обработку должны быть возможно меньшими. Вместе с тем эти величины должны быть реальными, так как при чрезмерно малых допусках и припусках потери от брака могут оказаться гораздо большими, чем экономия металла за счет снижения допусков и припусков. Рекомендуемые допуски и припуски приведены ниже (для черновых размеров колеса), мм:
наружный диаметр обода……………... внутренний диаметр обода: с наружной стороны…………………... с внутренней стороны………………… ширина обода………………………….. ширина гребня………………………… высота гребня………………………….. толщина диска: у обода………………………………….. у ступицы………………………………. в перегибе……………………………… диаметр ступицы: с наружной стороны…………………... с внутренней стороны………………… длина ступицы………………………… диаметр отверстия в ступице…………. выступ ступицы………………………... | D + (10÷20) d - (10÷15) d4 – (10÷15) В + (8÷12) bгр. + 10 hгр. ± 0 с +(16÷18) а +(16÷18) s+(16÷18) d1 + (11÷13) d3+ (11÷13) L + (12÷18) d2 – (7÷15) l – (3÷5) |
Также необходимо учесть изменения размеров колеса в зависимости от температуры нагрева. Учитывая практические данные, можно определить, что коэффициент линейного расширения β находится в пределах от 12×10-6 до 15×10-6. Размеры колеса в горячем состоянии равны
, (2)
где lг – горячие размеры колеса, мм;
lх – холодные размеры колеса, мм;
t и t0 – температура горячего и остывшего колеса соответственно, ºС.
Если принять, что разница между температурами горячего и остывшего колеса примерно равна 1000ºС, а также учитывая значения коэффициента температурного расширения, то формулу можно представить в следующем упрощенном виде:
(3)
Размеры колес, принятые для последующих расчетов калибровки, представлены в таблице 19.
Таблица 19
Основные размеры цельнокатаного колеса
Наименование размеров | Размеры колеса по стандарту, мм | Расчетные размеры готового колеса, мм | Размеры чернового колеса, мм | Размеры горячего колеса, мм |
Наружный диаметр обода, D | 920+4 | 920 | 930 | 942 |
Внутренний диаметр обода: с наружной стороны, d с внутренней стороны, d4 | 810-4 810-4 | 810 810 | 800 800 | 810 810 |
Продолжение таблицы 19
Ширина: обода, В гребня, bгр. |
135±1 32,5 | 135 32,5 | 145 42,5 | 147 43 | |
Высота гребня, hгр. | 28 | 28 | 28 | 28,4 | |
Толщина диска: у обода, с у ступицы, а в перегибе, s | 20+2 20+2 20+2 | 20 20 20 | 37 37 37 | 37,5 37,5 37,5 | |
Диаметр ступицы: с наружной стороны, d1 с внутренней стороны, d3 | 230+4 230+4 | 230 230 | 242 242 | 245,1 245,1 | |
Длина ступицы, L | 190+2 | 190 | 205 | 207,7 | |
Диаметр отверстия в ступице, d2 | 180-2 | 180 | 170 | 172,2 | |
Выступ ступицы, l | 55+2 | 55 | 50 | 50,7 | |
Для дальнейших расчетов необходимо использовать только размеры горячего колеса. Калибровку инструмента горячей деформации рассчитываем в порядке, обратном ходу технологического процесса, поэтому прежде всего рассмотрим калибровку инструмента деформации выгибного пресса.
Калибровка выгибных штампов
Основные размеры верхнего и нижнего выгибных штампов представлены на рисунке 3
Рисунок 3 - Основные размеры выгибных штампов
Все размеры, относящиеся к верхнему штампу имеют индекс «в», а к нижнему – «н».
Диаметр верхнего штампа, определяющий внутренний диаметр обода с наружной стороны, принимаем равным соответствующему горячему размеру колеса.
(4)
Диаметр нижнего штампа устанавливается аналогично.
(5)
Однако, в соответствии со стандартом, на внешнем участке штампа может выполняться фаска или закругление определенных размеров.
Высоту штампов Н определяем с учетом припуска на торцовку обода.
(6)
(7)
Для определения высоты периферийной части штампов К необходимо учитывать, что при выгибке диска штампы соприкасаются с колесом не по всей поверхности. Верхний штамп находится в контакте с колесом на участке перехода диска в ступицу, а нижний – на участке перехода диска в обод. Между верхним штампом и колесом на участке перехода диска в обод, а также между нижним штампом и колесом на участке перехода диска в ступицу имеется зазор.
Тогда высота периферийной части штампов К будет равна
(8)
, (9)
где δ – зазор, принимаемый равным 6 мм.
Уклон периферийной части штампов α0, а также уклон полости штампов αс определяем по чертежу колеса.
Так как одна из частей ступицы выступает относительно диска больше другой, то в этом случае глубину горловины нижних штампов hн принимаем конструктивно в соответствии с чертежом колеса. Тогда глубину горловины верхнего штампа определяем по формуле:
(10)
Где
Наружный диаметр полотна штампов С определим из простого геометрического соотношения:
(11)
Наружный диаметр нижнего штампа определяется с учетом припуска на торцовку обода, выполненного на штампе в виде фаски или закругления:
(12)
Радиусы перехода от диска к ступице R1 и от обода к диску R2 принимаем в соответствии с чертежом колеса. Радиусы сопряжения этих мест с диском R3 определены также с учетом зазоров, учитывающих колебания в толщине диска.
Для колес с криволинейным диском определяются радиусы изгибов штампов, формирующих диск, а также диаметры штампов, являющиеся центрами окружностей для построения изгибов.
Рисунок 4 - Выгибной штамп для формирования криволинейного диска колеса
Рисунок 5 - Диск с глубоким центральным изгибом
Радиусы изгибов диска в трех сопряженных окружностях одинаковы (Rд) и определяются по чертежу колеса с учетом коэффициента температурного расширения равного 1,013.
(13)
(14)
(15)
(16)
где s – толщина диска колеса в горячем состоянии, мм.
Диаметры штампов DR1, DR2, DR3, являющиеся центрами окружностей для построения изгибов, определяются по чертежу колеса с учетом коэффициента температурного расширения. Дальнейшие расчеты ведутся независимо от вида диска колеса.
Диаметр полости верхнего штампа под ступицу определяем с учетом раздачи полости штампов в процессе работы:
(17)
При совмещении операций выгибки и прошивки на одном прессе необходимо учитывать существенную раздачу нижних штампов в результате прошивки:
(18)
Большой диаметр полости верхнего и нижнего штампов определяем по следующим формулам:
(19)
(20)
Остальные размеры выгибных штампов принимаются с учетом конструкции и размеров пресса. Результаты сводим в таблицу 20.
Таблица 20
Результаты расчета калибровки выгибных штампов
Диаметр штампов, мм | верхнего Dв | 810 |
нижнего Dн | 810 | |
Диаметр полотна штампов, мм | верхнего Св | 784,4 |
нижнего Сн | 783,9 | |
Диаметр полости штампов под ступицу, мм | верхнего, Ав | 243,1 |
нижнего, Ан | 240,1 | |
Большой диаметр полости штампов, мм | верхнего, Вв | 271,9 |
нижнего, Вн | 302,5 |
Продолжение таблицы 20
Высота периферийной части штампов, мм | верхнего, Кв | 47,75 |
нижнего, Кн | 55,75 | |
Глубина горловины штампов, мм | верхнего, hв | 53,7 |
нижнего, hн | 116,5 | |
Радиусы закругления штампов, мм | от диска к ступице, R1 | 43 |
от обода к диску, R2 | 26 | |
Уклон периферийной части штампов | верхнего, α0в | 15 |
нижнего, α0н | 15 | |
Уклон полости штампов | верхнего, αсв | 15 |
нижнего, αсн | 15 | |
Радиусы изгибов диска | верхнего, Rдв1 и Rдв3 | 47,3 |
верхнего, Rдв2 | 84,8 | |
нижнего, Rдн1 и Rдн3 | 84,8 | |
нижнего, Rдн2 | 47,3 | |
Диаметры штампов выгибного пресса | первый, DR1 | 344,4 |
второй, DR2 | 547 | |
третий, DR3 | 749,6 |
Калибровка валков колесопрокатного стана
При калибровке деформирующего инструмента для прокатки колеса следует не только учитывать индивидуальное назначение валка или группы валков, но и их работу по формоизменению заготовки во взаимосвязи друг с другом.
Калибровка наклонных (эджерных) валков вертикального колесопрокатного стана
На колесопрокатных станах с вертикальным расположением заготовки во время прокатки калибровка наклонных валков немного отличается от калибровки наклонных валков горизонтальных станов.
Рабочую часть эджерных валков вертикальных станов можно разделить на две части: средний и концевой конусы (Рисунок 6). Их функция аналогична функции соответствующих конусов наклонных валков горизонтального колесопрокатного стана. Обжатие обода по высоте, то есть главную задачу начального конуса, выполняют боковые валки (ролики).
Рисунок 6 - Основные размеры наклонного валка вертикального колесопрокатного стана
Диаметром Dн.в. наклонного валка будем считать минимальный диаметр среднего конуса. Данный размер также принимается, исходя из конструктивных соображений. Однако, по сравнению с диаметром Dн.в. наклонных валков горизонтальных станов, минимальное значение данного размера не может быть менее 250 мм. В соответствии с требованиями стандарта переход цилиндрической части валка в средний конус сопрягается дугой окружности радиусом r =10 мм.
В соответствии с эскизом валка конструктивно принимаем углы наклона в следующих пределах:
- угол наклона образующей среднего конуса к оси валка αс.к. рекомендуется принимать, опираясь на опытные данные, в пределах (45÷49)º;
- угол наклона образующей концевого конуса к оси валка αк.к. рекомендуется принимать, опираясь на опытные данные, в пределах (28÷32)º.
Образующая среднего конуса составляет с образующей начального конуса угол φ1, град.:
(21)
Длина образующей среднего конуса определяется, исходя из размеров обода горячего колеса до поступления его на выгибной пресс. На выгибном прессе, как правило, осуществляется незначительное обжатие обода по высоте. Тогда, высота обода вне диска после прокатки на колесопрокатном стане будет составлять, мм:
, (22)
где В и с – соответствующие размеры горячего колеса (таблица), мм;
Δhвыг. – обжатие обода по высоте на выгибном прессе, мм.
Рекомендуется принимать Δhвыг. = (3÷5) мм.
Определим длину образующей среднего конуса lс, мм:
(23)
Тогда горизонтальная проекция длины среднего конуса lс.г. будет составлять, мм:
(24)
Определим расчетный диаметр окружности А, являющейся линией пересечения среднего и концевого конусов, мм:
(25)
Радиус сопряжения среднего и концевого конусов R устанавливаем в соответствии с радиусом перехода диска в обод в соответствии с чертежом.
Определим расстояние от образующей начального конуса до точки приложения радиуса сопряжения среднего и концевого конусов К, мм:
(26)
Длину образующей концевого конуса принимаем конструктивно. При этом следует иметь в виду, что наклонный валок должен размещаться между ободом и ступицей, не повреждая ступицу при загрузке колеса в стан и во время прокатки. Опираясь на практические данные, принимаем суммарную длину горизонтальной проекции образующих среднего и концевого конусов lоб.г.=145 мм. [10] Тогда горизонтальную проекцию образующих концевого конуса lк.г. определим из формулы, мм:
(27)
Концевой конус состоит из нескольких участков: тороидального, конического полирующего, конического дискообразующего концевого конического. Тороидальный участок ограничен радиусом R.
Конический полирующий участок имеет угол наклона α1, соответствующий углу наклона концевого конуса (α1=αк.к.=30). Длина конического полирующего участка lк1 определяется как, мм:
(28)
Конический дискообразующий участок имеет угол наклона α2, град.:
(29)
Длина конического дискообразующего участка lк2 определяется как, мм:
(30)
Концевой конический участок имеет угол наклона α3, град.:
(31)
Использование наклонных валков с такой калибровкой концевого конуса позволяет улучшить качество поверхности раскатываемой части диска. Определим минимальный диаметр концевого конуса В из следующих геометрических соображений, мм:
, (32)
где р определяется из следующей формулы, мм:
(33)
Результаты расчета сводим в таблицу 21.
Таблица 21
Результаты расчетов наклонных валков
диаметр наклонного валка | Dн.в. | 300 |
минимальный диаметр концевого конуса | В | 292,3 |
расчетный диаметр окружности, являющейся линией пересечения среднего и концевого конусов | А | 417 |
угол наклона образующей начального конуса к оси валка | αн.к. | 0 |
Продолжение таблицы 21
угол наклона образующей среднего конуса к оси валка | αс.к. | 48 |
угол наклона образующей концевого конуса к оси валка | αк.к. | 30 |
радиус сопряжения среднего и концевого конусов | R | 26 |
расстояние от образующей начального конуса до точки приложения радиуса сопряжения среднего и концевого конусов | К | 32,75 |
горизонтальная проекция полотна начального конуса | lн.г. | - |
горизонтальная проекция длины среднего конуса | lс.г. | 32,86 |
горизонтальная проекция образующих концевого конуса | lк.г. | 92,14 |
Калибровка коренного валка колесопрокатного стана
Калибровку коренного валка выполняют таким образом, чтобы обеспечить необходимый профиль поверхности катания и гребня у чернового колеса (Рисунок 7).
Рисунок 7 - Основные размеры коренного валка
Диаметр коренного валка принимаем в соответствии с цеховыми данными 1300÷1400 мм. Диаметр коренного валка по гребневому ручью А определяем с учетом высоты гребня hгр:
(34)
Высота калибра коренного валка принимается на 15÷20 мм больше ширины обода В. Высота части валка, располагающаяся ниже гребневого ручья принимается конструктивно (как правило, эта величина находится в пределах 30÷50 мм). [10]
Таблица 22
Результаты расчетов коренного валка
диаметр коренного валка | Dк.в. | 1400 |
высота коренного валка | Н | 167 |
диаметр коренного валка по гребневому ручью | А | 1343,2 |
Калибровка формовочных штампов
Основные размеры верхнего и нижнего формовочных штампов представлены на рисунке 8.
Рисунок 8 - Основные размеры формовочных штампов
Наружный диаметр штампов определяем, исходя из требуемой величины раскатки, по следующей формуле:
(35)
(36)
где d и d4 – внутренние диаметры колеса, мм;
Δd – величина раскатки колеса по диаметру на колесопрокатном стане (среднее значение Δd≈120÷150), мм.
Высоту периферийной части формовочных штампов определяем, как сумму толщины части обода прокатываемого колеса, выступающей над диском, и величины обжатия на стане по высоте:
, (37)
где hоб – высота обода вне диска после прокатки колеса, мм
Δh – высота обжатия обода колеса по высоте наклонными валками (среднее значение Δh≈20÷30), мм.
Уклон периферийной зоны штампов для улучшения условий деформирования принимаются в пределах γ=(19÷20)º, а уклон боковой поверхности ступицы α=10º. Диаметры полотна верхнего и нижнего штампов определяем из соотношений:
(38)
(39)
Размеры центральной полости формовочных штампов определяем в соответствии с аналогичными размерами выгибных штампов.
Высота центральной полости верхнего и нижнего формовочных штампов:
(40)
(41)
Верхний диаметр центральной полости штампа Ав определяем с учетом раздачи полости штампа в начале эксплуатации (≈5-6 мм), а также с учетом фаски размерами (10÷12)×45º:
(42)
Нижний диаметр центральной полости штампа Ан определяем по формуле:
, (43)
где d1, d3, l – горячие размеры колеса, мм.
Определяем диаметры центральной полости верхнего и нижнего формовочных штампов по следующим формулам:
(44)
(45)
Радиусы перехода от диска к ступице R1 и от обода к диску R2 соответствуют аналогичным радиусам выгибных штампов. Высоту штампов H, а также другие размеры штампов определяем конструктивно.
Таблица 23
Результаты расчета формовочных штампов
наружный диаметр штампов | верхнего Dв | 660 |
нижнего Dн | 660 | |
высота периферийной части формовочных штампов | верхнего Кв | 71,25 |
нижнего Кн | 71,25 | |
диаметры полотна штампов | верхнего Dпв | 625 |
нижнего Dпн | 619 | |
высота центральной полости штампов | верхнего, hфв | 53,7 |
нижнего, hфн | 116,5 |
Продолжение таблицы 23
диаметр центральной полости штампов | верхнего, Ав | 243 |
нижнего, Ан | 217 | |
диаметры центральной полости формовочных штампов | верхнего, Вв | 262 |
нижнего, Вн | 236 | |
высота штампов | верхнего, Нв | 144 |
нижнего, Нн | 144 | |
радиусы переходов | от диска к ступице, R1 | 43 |
от обода к диску, R2 | 26 | |
уклон периферийной зоны штампов | Γ | 20 |
уклон боковой поверхности ступицы | Α | 10º |
Калибровка формовочного кольца
Формовочное кольцо ограничивает течение металла и формирует боковую поверхность обода (Рисунок 9).
Рисунок 9 - Монтажный узел формовочного пресса
Размеры формовочного кольца определяются объемом металла в колесной заготовке, при этом не обязательно отчетливое заполнение металлом наружной кольцевой полости образуемой штампами и формовочным кольцом.
Во избежание образования дефектов в процессе деформирования необходимо достаточно хорошее заполнение верхней части кольцевой полости. Внутренняя поверхность формовочного кольца должна иметь уклон, обеспечивающий выпадение колесной заготовки из кольца.
Рисунок 10 - Основные размеры формовочного кольца
Обычно этот уклон обода заготовки заключен в кольцо трапецеидального сечения. Высота трапеции Н равна ширине обода после формовки. Данная величина определяется с учетом небольшого обжатия на выгибном прессе Δhвыг и обжатия обода наклонными валками на колесопрокатном стане Δh :
, (46)
где В – ширина обода готового колеса, мм.
Внутренний диаметр кольца равен наружному диаметру формовочных штампов,
dк = Dв(н) (47)
dк =660мм
Наружный диаметр кольца равен полусумме оснований трапеции а1.
Полусумма оснований трапеции может быть определена как сумма внутреннего диаметра кольца и толщина обода после формовки:
а1 = dк + 2t, (48)
а1 = 660+ 2*76=812мм
где t – толщина обода после формовки, мм.
(49)
где D и d – наружный и внутренний диаметры готового колеса соответственно, мм.
Δt – обжатие обода по толщине на колесопрокатном стане, мм (среднее значение Δt≈10÷20 мм) .
Наружный диаметр формовочного кольца принимается конструктивно.
Таблица 24
Результаты расчетов формовочного кольца
Высота трапеции | Н | 176 |
внутренний диаметр кольца | dк | 660 |
полусумма оснований трапеции (наружный диаметр) | а1 | 812 |
Размеры и формы остальных видов инструмента деформации, используемого на операциях, предшествующих штамповке, определяются, в основном из конструктивных соображений, и специальных пояснений не требуют.
Определение размеров исходной и осаженной заготовки
В качестве исходной заготовки для производства колес применяют непрерывнолитые заготовки круглого сечения диаметром 430мм.
Определяем среднюю массу заготовки mз
(50)
Определяем высоту исходной заготовки Н0:
(51)
где V0 – объём исходной заготовки, м3;
D0 – диаметр исходной заготовки, м (в соответствии с технологией АО «ЕВРАЗ НТМК» принимают равным 430 мм в холодном состоянии).
Находим объем исходной заготовки
(52)
где ρ – плотность стали, принимаем равной 7,8 т/м3.
Диаметр осаженной заготовки Dос принимают примерно равным наружному диаметру формовочного кольца, то есть Dос= 812 мм.
Определяем высоту осаженной заготовки:
(53)
Расчет формоизменения колесной заготовки
Внутренний диаметр колеса после формовки узнаем из формулы в мм:
(54)
Где d2 - внутренний диаметр колеса после прокатки. Принимаем размер d готового колеса в горячем состоянии, мм.
Δd - величина раскатки колеса по диаметру на колесопрокатном стане
Размер толщины обода после прокатки рассчитаем по формуле:
(52)
Где D - наружный диаметр обода в горячем состоянии, мм.
d - внутренний диаметр обода с наружной стороны в горячем состоянии;
Размер толщины обода после формовки можно узнать из формулы:
(53)
Где Δh - высота обжатия обода колеса по высоте наклонными валками
Высоту обода после прокатки вычислим по формуле:
(54)
где B - высота обода в горячем состоянии
После формовки происходит обжатие обода боковым валком на 5-7 мм, следовательно высоту обода после формовки рассчитаем так:
(55)
В1=151+6=157 мм
Толщина диска при выгибке не меняется:
(56)
h2 = 37,2 мм
где с толщина диска в горячем состоянии в перегибе.
На колесопрокатном стане диск обжимается по высоте на 0,4-1 мм:
(57)
h1 = 37,5+1=38,5 мм
Дата добавления: 2018-06-01; просмотров: 767; Мы поможем в написании вашей работы! |
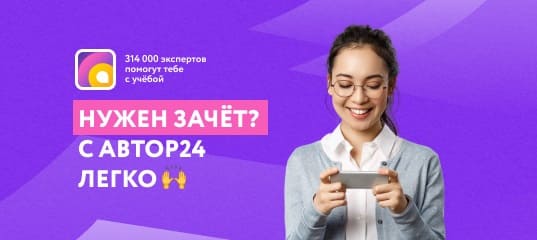
Мы поможем в написании ваших работ!