ОПЕРАЦИИ, ПРЕДШЕСТВУЮЩИЕ СБОРКЕ ИМС
Сюда относятся контрольные операции, скрайбирование и ломка пластин и подложек.
Зондовый контроль полупроводниковой пластины
Он осуществляется на автоматических установках. Групповая пластина устанавливается на предметном столике с вакуумным присосом. Предметный столик перемещается под головкой, имеющей контрольные щупы (зонды). Перемещение пластины идет с шагом, соответствующим размеру отдельной ячейки.
Перед началом контроля пластину ориентируют с помощью меток. Зонды контактируют с периферийными контактными площадками ячейки. Зондовые установки действуют совместно с контрольной аппаратурой, выдающей контрольные сигналы. При наличии годной ячейки выдается сигнал на следующий шаг. Если ячейка неисправна, то выдается сигнал на маркирующее устройство, наносящее цветную метку на ячейку.
Пример установки Зонд АЧМ. Количество зондовых головок – 60. Шаг перемещения от 0,01мм до 9,99мм.
Контроль и подгонка пленочных элементов ГИМС
При контроле пленочных элементов ГИС на первом этапе бракуют схемы с явно выраженными дефектами пленок.
С помощью микроскопа, например, МБС-1 контролируется правильность чередования слоев, качество слоев подложки, качество рисунка элементов.
На втором этапе контролируются электрические параметры элементов с помощью приборов (измерение емкости, – прибор Е12). Подключение к приборам осуществляется с помощью зондовых контактных приспособлений. ГИМС изготавливается на групповой подложке 60х48.
|
|
Скрайбирование и ломка пластин и подложек
Пластины на отдельные кристаллы (и платы) разделяют путем скрайбирования и последующей ломки. Сущность скрайбирования заключается в нанесении на поверхность пластины со стороны структур рисок алмазным резцом или лазером. Риски наносят в двух взаимных перпендикулярных направлениях по границам ИМС. Ширина рисок 20-40 мкм, глубина10-15 мкм.
Резец представляет собой 3-х или 4-хгранную пирамиду. При толщине пластины до 400мкм, нагрузка составляет . Наличие на пластине
увеличивает износ резца.
Для скрайбирования диэлектрических подложек используется стеклорезы. По форме стеклорез тоже представляет 4-хгранную пирамиду, но ему нужно большее усилие.
Механическое скрайбирование имеет малую ширину риски и высокую производительность. Скорость продвижения резца . Недостатком механического скрайбирования является малая точность и зависимость качества ломки от размеров кристалла (в том числе и от толщина).
При лазерном скрайбировании используются оптические квантовые генераторы. Ширина риски не более 120мкм. Недостаток - малая производительность .
|
|
Ломка проскрайбированных пластин весьма ответственная операция. Созданы различные установки для ломки пластин. В процессе ломки пластина лежит рисками вниз на гибкой опоре, а стальные или резиновые валики прокатывают пластину последовательно в двух взаимно перпендикулярных направлениях. Таким образом, сначала пластина ломается на полосы, а затем эти полосы ломаются на кристаллы.
СБОРОЧНО-МОНТАЖНЫЕ ОПЕРАЦИИ
Сборка это индивидуальная обработка микросхем.
В общем виде сборка включает этапы:
1. Изготовление деталей и узлов корпуса микросхемы.
2. Крепление подложек и кристаллов к основанию корпуса.
3. Присоединение выводов.
4. Герметизация.
Характер сборочно-монтажных операции во многом определяется конструкцией корпуса. Требования к корпусам включают с одной стороны - механическую прочность, герметичность, высокую теплопроводность. Эти требования необходимы для защиты микросхемы от окружающей среды. С другой стороны - возможность надежного соединения выводов корпуса с контактными площадками ИМС, низкую стоимость, простоту в изготовлении.
Конструкторско - технологические характеристики корпусов
|
|
В порядке снижения надежности:
- металлокерамические
- керамические
- металлостеклянные
- стеклянные
- металлополимерные
- полимерные
БИС обычно монтируют в металлокерамических и керамических корпусах.
Металлокерамический корпус. Это корпус с керамическим основанием и механической крышкой.
1-Керамическое основание
2-Выводы корпуса
3-Стекляный изолятор
4-Металлическая рамка
5-Верхняя крышка;
6-подложка;
7-перемычка-провод, соединяющий периферийные контактные площадки с выводами корпуса.
Металлостеклянный корпус имеет металлическое основание и металлическую крышку.
1. Основание
2. Вывод
3. Корпус
4. Подложка
5. Изоляция
6. Сварка
Детали корпуса изготавливаются методом холодной штамповки Герметизация корпуса осуществляется путем сварки по контуру. Сборка основания с выводами и образование металлостеклянного спая осуществляется в групповых кассетах методом термической обработки в конвейерных печах.
Основание, а иногда и крышка делаются стеклянными. Если крышка у такого корпуса металлическая, то герметизация осуществляется сваркой.
Материалы для корпусов подбираются с учетом согласования по ТКЛР. Например, сплав ковар (Fe-Ni-Co); 29НК; керамика 22ХС, поликор ПТ-1, стекло СТ2-4, С48-2. Герметичные вакуумные слои получают в течение 1 часа.
|
|
Пластмассовый корпус. Имеет штыревые выводы; основание и крышка выполняются из пластмассы.
Эти корпуса не имеют хорошей герметизации из-за рассогласованности ТКЛР полимеров и металлов.
Полимерный корпус
Процессы, используемые при изготовлении корпусов:
1. Штамповка
2. Керамическая технология
3. Пайка и сварка при герметизации
4. Прессование
5. Заливка
Дата добавления: 2018-05-12; просмотров: 505; Мы поможем в написании вашей работы! |
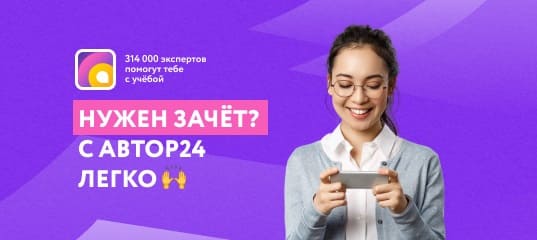
Мы поможем в написании ваших работ!