Разработка технологического процесса ковки
Чертеж поковкисоставляется на основании чертежа готовой деталис учетом допусков на поковку, припусков на механическую обработку и напусков (рисунок 9.4, а). Для деталей сложной формы (с фланцами,уступами, выемками), когда длина или диаметр уступа малы по сравнению с размерами смежных участков, форма поковки упрощается. Увеличенный в таком случае припуск называется напуском.
При составлении чертежа поковки необходимо обеспечить ее технологичность. Форма поковки должна быть простой (цилиндрической или плоской), следует избегать конических и клиновых поверхностей, ребер бобышек, выступов. При ковке надо обеспечить правильное направление волокон; они не должны пересекаться.
Размеры исходной заготовки для поковки рассчитывают с учетом отходов на угар, прибыли, обрубки и необходимой степени уковки.
Выбор и последовательностьопераций ковкизависит от формы поковки и технических требований на нее. Для сплошных деталей круглогои прямоугольного сечения (осей, валов, колонн, брусков, пластин и т. п.)общими операциями ковки являются: протяжка, комбинация протяжкис осадкой, прошивкой, рубкой, надрубкой уступов.
Рисунок 9.4 – Чертёж поковки шестерни и схема процесса ковки рычага с вилкой.
Для одноколейных и многоколенных валов, крюков, кроме этих операций, необходимы закручивание и гибка. Для полых деталей малой высоты (бандажи, диски, кольца) применяют осадку, комбинацию осадки с протяжкой, прошивкой, рубкой, раскаткой на оправке; для протяженных полых деталей (цилиндры, барабаны, валы) – протяжку, комбинацию протяжки с осадкой, прошивкой, раскаткой на оправке.
|
|
На рисунке 9.4 показана схема технологического процесса ковки рычага с вилкой (рисунок 9.4, б), включающая операции протяжки (рисунки 9.4, г, д, е, з), надрубки (рисунок 9.4, в, г, ж) и гибки (рисунок 9.4, ж).
Температурный интервал и режим нагрева
Для повышения пластичности и уменьшения сопротивления деформированию металлы и сплавы перед обработкой давлением нагревают до определенной температуры. Для каждого металла существует такой температурный интервал (диапазон температур начала и окончания обработки), в котором обеспечиваются оптимальные условия горячей обработки давлением. Нагрев металла сопровождается рядом явлений, которые необходимо учитывать при выборе температуры и режима нагрева.
Окисление металлов. При нагревании стали выше 700 °С происходит интенсивное окисление поверхностного слоя с образованием окалины, состоящей из оксидов железа Fe2O3, Fe3O4, FeO. С повышением температуры до 1330—1350 °С окалина плавится и железо горит с образованием снопа ярко–голубых искр. Потери металла на окалину (угар) при однократном нагреве в пламенной печи составляют 1,5—2,5 %, при электронагреве 0,4—0,7%. Кроме безвозвратных потерь металла, образование окалины в 1,5—2 раза повышает интенсивность изнашивания деформирующего инструмента, так как твердость ее выше твердости деформируемого металла.
|
|
При высоких температурах наряду с окислением железа происходит также обезуглероживание поверхностного слоя стали вследствие выгорания углерода. Толщина обезуглероженного слоя составляет обычно 0,2—0,5 мм, достигая иногда 1,5—2,0 мм.
Для уменьшения окисления металла применяют электронагрев, а также нагрев заготовок в защитной атмосфере.
Перегрев и пережог. При высоких температурах нагрева интенсивно растет зерно. Это явление называется перегревом.Перегретая сталь характеризуется более низкими механическими свойствами – уменьшение относительного удлинения и ударной вязкости составляет около 25%. Структуру перегретой стали в большинстве случаев можно исправить отжигом.
При нагреве стали до температуры, близкой к температуре плавления, происходит интенсивная диффузия в нее кислорода, образованиеоксидов по границам зерен и расплавление легкоплавких межзёренных прослоек, что приводит к появлению трещин и потере пластичности. Это явление называетсяпережогом.Оно не устраняется термической обработкой, и пережженный металл приходится отправлять на переплавку.
|
|
Температурный интервал горячей обработки давлением. Для максимального повышения пластичности металла температура начала обработки должна быть возможно более высокой, но не вызывающей перегреваи пережога. Температура окончания обработки должна быть выше температуры рекристаллизации и фазовых превращений.
Температурный интервал горячей обработки давлением углеродистых сталей с 0,2–0,7 % углерода 1280–800 °С; с 0,8–1,3 % углерода – 1100–760 °С. Медные сплавы обрабатывают в интервале температур 900–700 °С; дуралюмин – 470–400 °С; титановые сплавы – 1100–900 °С.
Режим нагрева. Нагрев заготовок обычно происходит неравномерно. Вначале нагреваются наружные слои, а затем за счет теплопроводности – сердцевина. При большой разности температур поверхности исердцевины возникают температурные напряжения (снаружи – сжимающие, внутри – растягивающие), которые могут привести к образованию трещин. Опасность их появления больше у легированных и литых сталей,у которых теплопроводность меньше, и она возрастает с увеличениемсечения заготовки. Поэтому заготовки из легированных сталей и заготовки диаметром больше 150 мм нагревают постепенно (методически) в дваэтапа: медленный нагрев и выдержка при 700–800 °С, а затем нагрев донеобходимой температуры с максимально возможной скоростью.
|
|
9.8 Содержание отчета:
В отчёте должны быть: цель работы, сущность и схемы процессов обработки металлов давлением, заполненная технологическая карта, виды операций ковки, инструмент, оборудование.
9.6. Контрольные вопросы:
9.6.1. Объясните сущность протяжки.
9.6.2. Объясните сущность осадки.
9.6.3. Объясните сущность прошивки.
9.6.4. Объясните сущность гибки.
9.6.5. Объясните сущность закручивания.
Дата добавления: 2018-05-12; просмотров: 437; Мы поможем в написании вашей работы! |
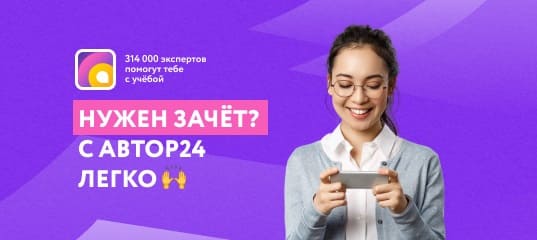
Мы поможем в написании ваших работ!