Изготовление сложнопрофильных деталей
И тормозных дисков из углерод-углеродных
Композиционных материалов
В технологии изготовления сложнопрофильных тонкостенных деталей из углепластиков, УУКМ и карбидоуглеродных материалов при создании сложных многослойных конструкций с трехмерной структурой используют различные методы армирования (см. гл. 3):
многослойными тканями (плетение тканей по системе двух или трех нитей);
пакетами сшитых однонаправленных монолент (прошивка сухих и пропитанных лент);
|
нитевидными кристаллами (хаотическое армирование полимерной матрицы и армирование вискеризованными во локнами);
коротковолокнистой арматурой (хаотическое и регулярное армирование).
Наибольший практический
Рис. 6.34. Деталь входного уст интерес для создания технологии ройства сверхзвукового ЛА из сложнопрофильных деталей сшитых многопрофильных элементов представляют два метода:
476 |
6. ПРОЦЕССЫ ИЗГОТОВЛЕНИЯ КОНСТРУКЦИЙ ИЗ КОМПОЗИТОВ
прошивка сухих пакетов и прошивка пропитанных лент. В частности, метод прошивки положен в основу технологии изготовления детали входного устройства сверхзвукового летательного аппарата (рис. 6.34), представляющей собой сложный элемент конструкции из сшитых многопрофильных элементов. В процессе изготовления отдельных элементов конструкции прошивке подвергаются пакеты из углеродных лент (табл. 6.11), состоящие из восьми слоев общей толщиной 1,8 мм. Для прошивки используют углеродные нити, характеристики которых приведены в табл. 6.12. Пакеты набираются из углеродных монолент, ориентированных один относительно другого под углом 45°, что обеспечивает снижение анизотропии физико-механических характеристик конечного пакета.
|
|
Таблица 6.11 Характеристики углеродной ленты
Параметры | Значение |
Толщина углеродной ленты, мм | 0,11...0,15 |
Ширина ленты, мм | 255 ±20 |
Линейная плотность, г/м | 35 ±5 |
Число нитей в основе ленты шириной 10 см | 485 ±30 |
Плотность нити в основе ленты, г/см | 1,69-0,05 |
Таблица 6.12 Характеристики углеродных нитей
Параметры | Значение |
Линейная плотность, текс Отклонение от заданной линейной плотности, текс Предельное удлинение не менее, % | 215 ±15 0>4 |
В связи с тем9 что при сухой сшивке трудно сохранить заданную ориентацию монослоев вследствие их смещения механизмом подачи швейной машины, и при этом часть волокон прорубается при прохождении иглы через прошиваемый пакет, в технологии изготовления используют метод прошивки пропитанных связующим углеродных монолент.
477
6.4. Изготовление сложнопрофильных деталей
В качестве таких связующих служат три типа полимерных композиций: жидкое стекло, поливиниловый спирт (ПВС), карбометилцеллюлоза. Все эти матрицы водорастворимы и легко удаляются при температуре до 60 °С. Наилучший результат получают при использовании в качестве связующего 3%-ного раствора ПВС, которым пропитывают пакет слоев монолент и смачивают углеродную нить.
|
|
Для защиты крайних слоев пакета в процессе прошивки от механических повреждений в прошивочном тракте швейной машины имеются водонепроницаемые защитные пленки (полиэтиленовые, триацетатные и лавсановые). Наиболее эффективно использование лавсановой пленки, обладающей повышенной формоустойчивостью при смачивании ее раствором ПВС. В качестве прошивочного агрегата применяют универсальную швейную машину с усовершенствованным трактом подачи нити, максимально исключающим резкие перегибы углеродной прошивной нити по всему тракту. При этом натяжение прошивной нити по тракту составляет не более 0,1 кг, что исключает ее повреждение в процессе прошивки пакета. При прошивке используют несколько типов швейных игл диаметром от 1,5 до 3 мм. После прошивки детали подвергают сушке при температуре 100 + 20 °С.
Лавсановую пленку после изготовления детали удаляют с поверхности механическим путем.
|
|
Изготовление сложнопрофильных образцов типа тавра или
|
коробчатых конструкций проводится путем совместной прошивки отдельных элементов с последующей их фиксацией (с силой Р) в специальных приспособлениях-оправках (рис. 6.35) и сушкой в термопечи.
Рис. 6.35.Фиксация тавровой конструкции из УУКМ в приспособлении: / - композит; 2 — уголок; 3 - плита |
Тормозные диски из хаотично армированных УУКМ широко используют в авиации и транспорте. В технологическом процессе для формирования армирующего каркаса применяют смесь рубленых углеродных и арамидных волокон, а в качест-
6. ПРОЦЕССЫ ИЗГОТОВЛЕНИЯ КОНСТРУКЦИЙ ИЗ КОМПОЗИТОВ
ве связующего — порошок резольной фенолформальдегидной смолы с добавками веществ — модификаторов коэффициента трения и износа (карбонат кальция, сульфид бария).
В основу получения хаотично армированного препрега положен метод гидросуспензионного формования при помощи вакуумного фильтра (нутч-фильтр).
Оборудование, используемое в промышленной технологии формования заготовок тормозных колодок, состоит из следующих технологических единиц: миксера для приготовления водных суспензий; миксера с регулируемой скоростью перемешивания для приготовления дискретно-волоконной массы; двух емкостей для оборотной воды; нутч-фильтра и вакуумного насоса; систем перепуска; термошкафа; карбонизатора.
|
|
Проектная мощность линии составляет 300...400 тормозных колодок в смену. Технологический процесс изготовления тормозных дисков, основанный на методе нутч-формования пре-прегов дискретно хаотической структуры, включает в себя следующие операции.
1. Приготовление фрагментов углеродных нитей длиной
1...10 мм при помощи воздушно-механической мельницы. При
этом используют различные типы наполнителей УКН-5000 и др.
2. Приготовление водяной суспензии связующего.
3. Механическое разноскоростное размешивание фрагментов нити в водяной суспензии до получения однородной волокнистой массы.
4. Нутч-фильтрация полученной массы.
5. Сушка в термошкафу при температуре 95 °С в течение 12 ч — получение препрега.
6. Закладка препрега в подогретую до 150 °С пресс-форму; прессование с удельным давлением 35 МПа; выдержка в течение 40 мин; распрессовка (прессование производится на металлическую основу).
7. Карбонизация при температуре 1000 °С при заданном усилии прессования.
8. Четыре цикла пропитки пеком с последующей карбонизацией.
9. После третьего и четвертого циклов графитизация при температуре 2400 °С в течение 1,5 ч.
478
479
6.4. Изготовление сложнопрофильных деталей
6. ПРОЦЕССЫ ИЗГОТОВЛЕНИЯ КОНСТРУКЦИЙ ИЗ КОМПОЗИТОВ
Модификация свойств УУКМ позволила значительно расширить область их применения. Например, высокие фрикционные свойства, малая скорость износа, сочетание высоких прочностных и теплофизических характеристик с малой плотностью обусловили применение УУКМ в тормозных системах. Самолет "Конкорд" — первый гражданский самолет, на котором были установлены тормоза из УУКМ, что позволило снизить массу самолета на 634 кг (по сравнению с тормозной системой из бериллия). Разработанный и успешно применявшийся в отечественной практике УУКМ марки "Термар" имеет недостаточно высокий ресурс работы (не более 300...400 взлетов и посадок), в то время как в соответствии с современными требованиями к тормозным дискам количество взлетов и посадок должно быть не менее 1000.
В настоящее время разработаны два типа УУКМ для тормозных дисков, полностью удовлетворяющие требованиям авиационной промышленности: коэффициент трения — 0,24...0,35; интенсивность износа — не более 2,0 мкм/торможе-ние; коэффициент стабильности — не менее 0,75.
В процессе разработки материала был осуществлен полный комплекс исследований, включавший в себя этапы проектирования, технологической отработки, структурных исследований, определение физико-механических характеристик материала. Заключительной стадией работ стали испытания тормозных дисков. Эти испытания проводились с использованием установок серии "Трибовак", работающих в соответствии с различными кинематическими схемами, при следующих условиях: среда в камере трения — воздух при атмосферном давлении; нагрузка на вращающийся образец — 5 МПа; скорость скольжения — 0,345 м/с; начальная температура образцов — 20 °С.
Испытания моделей пар трения показали, что лучшими трибологическими характеристиками обладает материал структуры 4D на основе высокомодульной нити УКН-5000, уплотненный пироуглеродом из газовой фазы и донасыщенный каменноугольным пеком с последующей карбонизацией и гра-фитизацией.
В производстве тормозных дисков используют следующие режимы насыщения каркасов согласно пековой технологии:
1) пропитка пеком:
предварительное вакуумирование, МПа......................................... 0,01
температура, °С..................................................................................... 270
давление, МПа................................................................................... 2,88
время пропитки под давлением, мин............................................... 60,0
охлаждение........................................ произвольное в инертной среде;
2) карбонизация под давлением:
предварительное вакуумирование, МПа.............................................. 0,01
температурный режим:
подъем температуры до 300 °С со скоростью 5 °С/мин подъем температуры до 450 °С со скоростью 1 °С/мин
выдержка при 450 °С, ч ....................................................................... 4
подъем температуры до 1000 °С со скоростью 1 °С/мин
выдержка при 1000 °С, ч.................................................................. 3 — 4
рабочее давление в ходе процесса, МПа.................................................. 55
охлаждение............................................. произвольное в инертной среде;
3) графитизация при температуре 2400 °С в течение 1,5 ч.
Лучшие характеристики по коэффициенту трения и его стабильности имеет материал структуры 4D.
С целью снижения интенсивности линейного износа разработанных УУКМ проводились исследования по модификации углеродной матрицы методами борирования, силицирования и алюмосилицирования.
Силицирование проводят посредством окунания заготовок в расплав кремния с 10%-ным содержанием алюминия. Лучшие результаты получают для УУКМ после силицирования с 10%-ным содержанием алюминия, однако это значение превышает максимально допустимое.
УУКМ для изготовления дисковых тормозов должны обладать высокой стойкостью к окислению.
Лучшими противоокислительными покрытиями являются материалы на основе карбидов и нитридов кремния.
Наиболее часто используют шликерный метод силицирования УУКМ с применением порошкообразного нитрида кремния и газофазный — с применением гафния.
При изготовлении дисков наилучшей является структура армирования материала 4D. При этом три направления армирования лежат в плоскости ХУ и повернуты одно относительно другого на угол 60°. Четвертое направление перпендикулярно плоскости ХУ. Плоскость диска при этом совпадает с плоскос-
480
31-1-243
481
6.5. Изготовление топливных баков и сосудов давления
6. ПРОЦЕССЫ ИЗГОТОВЛЕНИЯ КОНСТРУКЦИЙ ИЗ КОМПОЗИТОВ
|
товления бака: одновременная намотка двух полукорпусов; раздельная намотка полукорпусов. |
тью ХУ, а ось Z перпендикулярна поверхности диска. Для армирования используют жгуты из нитей в два и шесть сложений.
6.5. Изготовление топливных баков и сосудов давления
Топливные баки ракет, самолетов, вертолетов имеют, как правило, цилиндрическую форму с днищами.
Сосуды давления широко используют в двигательных установках в качестве вытеснительной системы подачи топлива. Кроме того, их применяют в системе барботирования компонентов топлива, в пневмогидравлических системах управления, для поддержания избыточного давления в дисках, в системах жизнеобеспечения космических кораблей, в качестве емкостей для хранения жидких и газовых веществ.
Сосуды давления для аэрокосмической и ракетной техники конструктивно могут быть выполнены в виде цилиндра с днищами в форме сферы или тора, а также в виде комбинаций этих форм.
В общем случае конструкция топливных баков и сосудов давления состоит из силовой оболочки, внутренней герметизирующей оболочки (лейнера) и присоединительной арматуры (штутцеров, фланцев, законцовок). В некоторых случаях они могут иметь внешнюю или внутреннюю теплоизоляцию. Основным технологическим способом изготовления баков и сосудов давления является метод намотки волокнистых КМ (см. гл. 2).
Рассмотрим технологию изготовления топливных баков на примере разработки конструкции и технологии подвесного бака вертолета для сжиженного газа.
Дата добавления: 2018-05-02; просмотров: 1300; Мы поможем в написании вашей работы! |
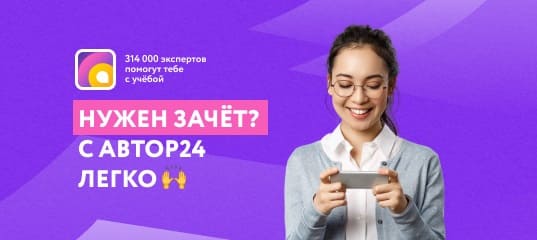
Мы поможем в написании ваших работ!