Изготовление внутрибакового дренажного трубопровода
Такой трубопровод изготавливают намоткой полиимидной или лавсановой пленки на металлическую неразборную оправку. Конструкция трубопровода показана на рис. 6.45, а устройство оправки для намотки прямолинейного длинноразмерного трубопровода с условным диаметром 100 мм и длиной 8000 мм показано на рис. 6.46.
Трубопровод состоит из многослойной пленочной оболочки и двух законцовок, обеспечивающих соединение трубопроводов между собой, а также надежное и герметичное закрепление пленочной оболочки на концах трубопровода. При разработке конструкции были рассмотрены различные варианты законцовок (см. рис. 6.45, а, б, в). Законцовка (см. рис. 6.45, а) включает в себя металлический фланец, пленочную оболочку и окружную подмотку из волокон.
Надежное защемление пленочной облочки на законцовке осуществляют с помощью бурта, канавки и радиальной обмот-
495
6.6. Изготовление трубопроводов
ки, соединения отдельных участков между собой — посредством сварки фланцев. Такую законцовку называют "колокольчик".
Рис. 6.45. Конструкция внутрибакового дренажного трубопровода:
1 - окружные слои; 2— спиральные слои; 3— радиальная подмотка законцовок;
а — металлический "колокольчик"; б — пленочный; в — пластиковый
Рис. 6.46.Типовое конструктивное решение металлической неразборной оправки для намотки прямолинейного длинноразмерного трубопровода
Поскольку у лавсановых и полиимидных пленок коэффициент линейного термического расширения в 2—3 раза больше, чем у коррозионно-стойкой стали, то при захолаживании со-
|
|
6. ПРОЦЕССЫ ИЗГОТОВЛЕНИЯ КОНСТРУКЦИЙ ИЗ КОМПОЗИТОВ
здается дополнительное обжатие хвостовика законцовки, что обеспечивает надежную работу соединения при циклических и криогенных температурных нагрузках. Очевидны и недостатки такого соединения ввиду сравнительно большой массы фланцев и возможностей повреждения пленочной оболочки в процессе сварки, особенно при использовании лавсановых пленок.
Законцовка (см. рис. 6.45, б) выполнена намоткой из той же пленочной ленты, что и сама оболочка трубопровода, подмоткой на концах оболочки утолщений и последующей механической обработкой. Герметичность соединения участков трубопровода обеспечивается в этом случае клиновым уплотни-тельным кольцом. К достинствам такой законцовки относится возможность сборки и разборки соединения при монтажных и ремонтных работах, а также изготовление фланца и оболочки трубопровода как единого целого. Очевидно, что такое соединение менее надежно, чем предыдущее, вследствие низкой прочности материала законцовки на сдвиг.
Наиболее приемлемым и перспективным является законцовка (см. рис. 6.45, в), в которой объединены достоинства двух предыдущих и скомпенсированы их недостатки. Законцовку изготовляют методом литья под давлением из серийно выпускаемых полиалканимидов с применением различных наполнителей и модификаторов. Этот материал относится к классу полиимидов и поэтому по физико-механическим и химическим свойствам совместим с материалом оболочки трубопровода. Он имеет плотность от 1280 до 1610 кг/см3 в зависимости от наполнителя, обладает повышенной (на порядок) сдвиговой прочностью. На практике применяют разъемное соединение участков трубопроводов между собой, элементы которого также изготовляют из высокопрочных наполненных полиалканимидов.
|
|
Технологические процессы изготовления многослойных пленочных трубопроводов с различными конструктивными исполнениями законцовок с прямолинейными и криволинейными участками многовариантны, но имеют общие операции.
Очевидно, что из жестких термореактивных пленок невозможно изготовить герметизирующую оболочку двойной кривизны путем склеивания или сварки предварительно вырезанных из пленки лепестков или заготовок. Поэтому следует счи-
|
|
496
497
6.6. Изготовление трубопроводов
тать более рациональным изготовление полимерных пленочных оболочек методом непрерывной намотки узких лент на оправку, используя для этого технологическое оборудование и оснастку, которые применяют для намотки силовых оболочек сосудов давления и трубопроводов из однонаправленных композитов.
Ширина наматываемой ленты зависит от степени деформируемости материала пленки и кривизны оболочки и в каждом конкретном случае определяется расчетом.
Для соединения наматываемых пленочных лент между собой разработаны две технологии. В первом случае лавсановые и полиимидные пленки, не имеющие каких-либо покрытий, склеивают специальным клеевым составом. При этом для улучшения адгезионных свойств пленок их поверхность предварительно обрабатывают каким-либо физико-механическим способом. Во втором случае полиимидные пленки с односторонним или двусторонним фторопластовым покрытием (типа ПМФ-351 или ПМФ-352) соединяют путем обжатия и спекания при определенной температуре.
Процесс получения многослойных пленочных оболочек включает в себя разрезку рулонной пленки на полосы необходимой ширины, обработку поверхности пленки либо наждачной шкуркой, либо химическим травлением или коронным разрядом, нанесение на нее клеевого состава, намотку на оправку требуемого числа слоев, термообработку и удаление оправки из готового изделия.
|
|
Для склеивания лавсановых лент пленочной оболочки применяют клеевой состав на основе эпоксидного связующего ЭДТ-10, в которое для увеличения эластичности и деформа-тивности добавляется продукт ДЭГ-1 (низкомолекулярная смола). В целях увеличения адгезии к эпоксидному связующему поверхность лавсановой пленки обезжиривают и обрабатывают раствором Na2Cr207 в H2S04 в течение 5... 10 с.
Полиимидная пленка ПМФ-352, используемая для намотки герметизирующих оболочек, имеет двустороннее фторопластовое покрытие (толщиной 5...6 мкм), поэтому намотанные из нее слои необходимо обжать и провести спекание при температуре 565..575 К в течение 45...60 мин.
6. ПРОЦЕССЫ ИЗГОТОВЛЕНИЯ КОНСТРУКЦИЙ ИЗ КОМПОЗИТОВ
Рассмотрим один из вариантов технологического процесса изготовления прямолинейного участка цилиндрической пленочной оболочки из полиимидной пленки ПМФ-352 с металлическими законцовками из коррозионно-стойкой стали 12Х18Н10Т. Процесс включает в себя следующие операции:
1. Сборка и установка на намоточном станке технологичес
кой оправки с закрепленными на ней металлическими закон
цовками.
2. Подготовка поверхности хвостовиков законцовок под склеивание с пленочным слоем и нанесение на поверхность оправки тонкого разделительного слоя графитовой смазки с ее последующей обмоткой фторопластовой лентой без нахлеста.
3. Намотка на оправку полиимидной пленки с расчетными шириной, нахлестом, числом слоев и углами намотки.
4. Окружная подмотка волокном в районе законцовок пленочной оболочки.
5. Намотка разделительного слоя фторопластовой пленки и термоусаживающейся кремнеземной ленты для опрессовки полиимидной оболочки и законцовок в процессе термообработки.
6. Термическая обработка многослойного лейнера при температуре спекания (573 ± 5 К) в течение часа, охлаждение на воздухе.
7. Снятие кремнеземной ленты и фторопластового слоя с наружной поверхности трубы, разборка технологической оправки и съем готового пленочного трубопровода.
8. Установка технологических заглушек на фланцы и подготовка к испытаниям на герметичность и прочность.
Трубопроводы с полиимидными законцовками изготавливают по аналогичной технологии. Для формирования законцовок в данном технологическом процессе необходима дополнительная операция механической обработки, которая выполняется после термообработки.
Трубопроводы с полиалканимидными законцовками также изготовляют согласно приведенной технологии. Однако сами заготовки на заключительном этапе приклеивают на предварительно отвержденную оболочку специальным клеевым составом.
498
499
6.6. Изготовление трубопроводов
Конструктивно-технологические параметры трубопроводов и результаты их испытания представлены в табл. 6.13.
Таблица 6.13
Дата добавления: 2018-05-02; просмотров: 349; Мы поможем в написании вашей работы! |
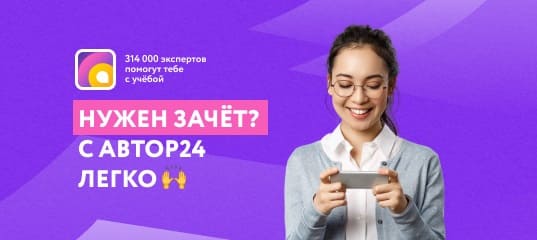
Мы поможем в написании ваших работ!