Изготовление сферического сосуда давления
Рассмотрим технологию изготовления сферического сосуда давления, предназначенного для хранения газообразного азота и газообразного кислорода в системе жизнеобеспечения орбитальной станции. Газ хранится в 12 сферических баллонах вместимостью 27 л каждый под давлением 30 МПа.
На рис. 6.41 представлена конструктивная схема сосуда давления. В качестве герметизирующей оболочки использованы жесткие полимерные полиэтилентефталатные пленки (лавсановые) и ПМФ-352 (полиимидные). Силовую оболочку изготавливают из углепластика методом намотки (УКН-5000 + + ЭДТ-10П).
|
Намотка герметизирующего лейнера и силовой оболочки осуществляется на песчано-поли-мерную оправку, изготовленную в специальной форме согласно технологии, описанной в гл. 2.
Маршрут изготовления сосуда давления состоит из следующих операций.
Рис. 6.41. Типовая конструкция сферического сосуда давления: 1 — герметизирующая оболочка; 2 — штуцер; 3 — гайка; 4 — шайба; |
1. Сборка и установка на намоточном станке СН-6 технологической оправки с металлическими штуцерами.
2. Обезжиривание поверхности штуцеров, контактирующих с наматываемым пленочным лей-
нером. Поверхность штуцеров предварительно пескоструят.
3. Установка кассеты с пленочным материалом на раскладчике намоточного станка, регулировка и настройка механизма технологического натяжения.
|
|
4. Программная многослойная намотка пленочного материала до получения расчетной толщины лейнера.
5. Нанесение верхнего разделительного слоя фторопластовой пленки и обмотка с увеличенным натяжением термоуса-живающейся лентой.
6. Термическая обработка многослойного лейнера при температуре спекания (в данном случае при 573 К) и охлаждение его вместе с печью.
7. Извлечение из нагревательной печи, снятие слоев термо-усаживающейся ленты и разделительного слоя.
8. Снятие кассеты с пленкой и установка кассеты с угле-пластиковым препрегом.
9. Закрепление конца намоточной ленты на наружной поверхности лейнера, установка расчетного технологического натяжения и зональная намотка силовой оболочки.
488
31-2-243
489
6.6. Изготовление трубопроводов
10. Намотка антиадгезионного разделительного слоя фторопластовой пленки.
11. Намотка технологического слоя термоусаживающейся ленты на разделительный слой и закрепление конца ленты на оправке.
12. Установка оправки с намотанной оболочкой в термопечь и термообработка в соответствии с технологическими режимами.
13. Извлечение оправки с изделием из термопечи, размотка слоев термоусаживающейся ленты, снятие разделительного слоя.
|
|
14. Осмотр и контроль поверхности силовой оболочки и штуцеров, удаление отвердевших натеков связующего.
15. Удаление технологической оправки вымыванием водой, нагретой до температуры 70...80 °С.
16. Сушка внутренней поверхности сосуда давления, установка технологических заглушек и опрессовка изделия давлением 0,3...0,5 рабочего давления.
Представленная здесь технология изготовления является типовой для сосудов давления и может незначительно меняться в зависимости от применяемых материалов и типа оправки.
6.6. Изготовление трубопроводов
В настоящее время во всем мире производится более 200 тыс. т труб из ПКМ, в основном из стеклопластика. Трубопроводы из композитов широко применяют в коммунальном хозяйстве, в нефтедобывающей и газовой промышленности, в химических производствах. Особое место занимают трубопроводы в ракетной и аэродинамической технике, где к ним предъявляют высокие требования по удельной прочности, герметичности, хемостойкости и где они должны надежно функционировать в широком диапазоне температур и давлений. Эти требования накладывают отпечаток как на конструкцию, так и на технологию изготовления трубопроводов.
Рассмотрим конструкторско-технологические решения топливопроводов применительно к криогенным топливным системам, работающим на жидком кислороде, водороде или сжиженном природном газе.
|
|
В силу функционального признака в криогенном топливном комплексе выделяют четыре основных типа трубопроводов, расположенных как вне бака, так и внутри его: 1 -заправочно-сливные; 2 — подачи топлива к двигателям; 3 -циркуляции и наддува; 4 - дренажные.
6. ПРОЦЕССЫ ИЗГОТОВЛЕНИЯ КОНСТРУКЦИЙ ИЗ КОМПОЗИТОВ
Конструкции внебаковых трубопроводов более сложные, чем внутрибаковых, так как они помимо герметизирующего лейнера, силовой оболочки и законцовок включают в себя теплоизоляцию и наружную защитную оболочку. Теплоизоляция криогенных трубопроводов предназначена для уменьшения теплопритока к компоненту, сохранение его температуры и кондиционного состояния при нахождении летательного аппарата в заправленном состоянии и для обеспечения минимальных потерь компонента на испарение.
Наружная защитная оболочка защищает теплоизоляцию от криоподсоса воздуха и предохраняет ее от разрушения.
На рис. 6.42 показана конструкция отвода внебакового криогенного топливопровода самолета. Отвод — наиболее сложная в технологическом отношении конструкция.
Рис. 6.42.Отвод внебакового криогенного топливопровода самолета: 1 — законцовка; 2— герметизирующий лейнер (12Х18Н10Т); 3 - силовая углепластиковая оболочка; 4— теплоизолирующая оболочка; 5— наружная защитная оболочка
490
491
6.6. Изготовление трубопроводов
Дата добавления: 2018-05-02; просмотров: 670; Мы поможем в написании вашей работы! |
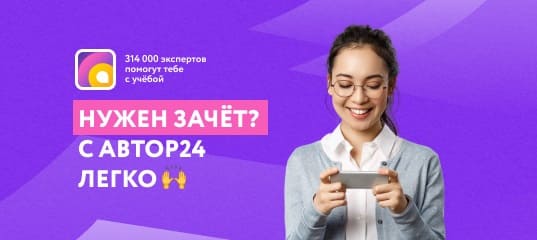
Мы поможем в написании ваших работ!