Изготовление цилиндрической силовой балки с законцовками
Схема армирования материала цилиндрической силовой балки, воспринимающей осевые изгибные и крутильные нагрузки (рис. 6.23), определяется условиями расположения во-
Рис.6.23. Схема формообразования цилиндрической балки: / - оправка; 2 - законцовка; 3 - кольцевая подмотка; 4 -спирально армированный материал балки; 5 — материал, удаляемый после намотки; 6 — разделительный слой
462
463
6.3. Изготовление шпангоутов, балок, отсеков, панелей
локон по траекториям главных напряжений. Минимальное количество направлений армирования материала балки, обеспечивающее статически устойчивую структуру материала, равно трем (± α, 90°, 0°). Для ортотропной цилиндрической балки это могут быть углы армирования ± α и 0°. Значение угла а определяется расчетом.
Такую структуру можно реализовать путем выкладки на цилиндрическую оправку углеродной ленты, ориентированной в осевом направлении (под углом 0°), и спиральной намотки под углом ± α.
Для достаточно длинных балок использование комбинированной выкладочно-намоточной технологии может привести к нарушению ортотропии структуры при выкладке слоя ленты в осевом направлении, что связано с возникновением нежелательной загрузки торцев в готовом изделии. Поэтому для длинных элементов трубчатого типа предпочтительной является намоточная технология, позволяющая получать эквивалентные механические характеристики материала.
|
|
Как правило, трубчатые балки содержат в своей конструкции соединительные законцовки. На наружной поверхности закон-цовки в зоне соединения имеются "шипы", полученные механической обработкой. Перед намоткой на подготовленную поверхность законцовки в зоне соединения с композитной оболочкой наносят слой клея горячего отверждения. После этой операции две законцовки устанавливают на оправку для намотки. Затем балка отверждается в автоклаве с вакуумным мешком или и электропечи методом термомеханического обжатия. В качестве обжимаемого материала может служить сухая стеклоткань, наматываемая на цулагу с заданным натяжением. Съем балки с оправки осуществляют после удаления полюсных участков намотанного материала (см. рис. 6.23, 5). При изготовлении балок большой длины для обеспечения съема изделия с оправки назначают технологические уклоны оправки порядка 1—2°.
В отличие от рассмотренного типового технологического процесса изготовления балки из композитов с полимерной матрицей технология аналогичной металлокомпозитной балки требует уникальных установок для формования изделий.
6. ПРОЦЕССЫ ИЗГОТОВЛЕНИЯ КОНСТРУКЦИЙ ИЗ КОМПОЗИТОВ
|
|
В частности, для изготовления трубчатых балок с законцов-ками из бороалюминия используют установку, представленную на рис. 6.24.
В качестве исходного полуфабриката для формования применяют однослойный бороалюминиевый шпон, полученный методом плазменного напыления чистого алюминия на ленты, образованные плотно уложенными борными волокнами. Полученный таким образом полуфабрикат имеет толщину 0,2 мм и содержание наполнителя 60 %(об.).
Согласно рассматриваемой технологии, бороалюминиевые трубчатые балки формуют непосредственно с металлическими законцовками, выполненными из алюминиевого сплава. При
|
Рис. 6.24.Схема установки для изготовления трубчатых балок из бороалюминия: / — вакуумный насос; 2 — вакуумная печь; 3 — кольцевые обоймы; 4 — законцовка трубчатой балки; 5 - оправка; б - формующая замкнутая оболочка с жидкостью; 7 — бороалюминиевый полуфабрикат; 8 - цулаги |
этом используют паростатичес-кий метод создания формующего давления. На цилиндрическую оправку 5 (см. рис. 6.24) надевают замкнутую герметичную тонкостенную металлическую оболочку типа тора с чечевицеобразным сечением 6, содержащую парообразующую жидкость. Снаружи на оболочку 6 укладывают необходимое количество слоев бороалю-миниевого полуфабриката 7 и одновременно устанавливают детали законцовок 4. Формуемый пакет 7 помещают вместе с цула-гами 8 в виде двух цилиндрических полуоболочек в кольцевые обоймы. Полученную сборку подают в вакуумную печь 2.
|
|
Бороалюминиевые трубчатые балки формуют при температуре 500 °С и давлении 30 МПа, возникающем за счет расширения перегретого пара в полости формующей оболочки.
464
30-243
465
6.3. Изготовление шпангоутов, балок, отсеков, панелей
Данный технологический процесс является достаточно трудоемким, однако позволяет получать изделия с уникальными механическими характеристиками. Одновременное образование законцовочных элементов позволяет решать проблему соединений при сборке изделий с бороалюминиевыми трубчатыми балками.
Дата добавления: 2018-05-02; просмотров: 453; Мы поможем в написании вашей работы! |
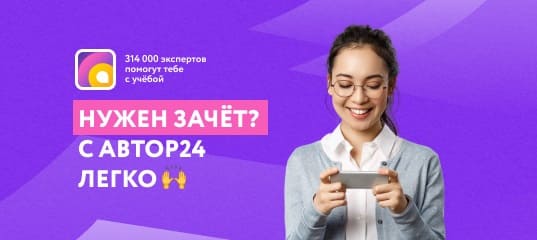
Мы поможем в написании ваших работ!