Классификация зубчатых передач по расположению осей колес
1. Оси параллельны (плоские механизмы). Начальные поверхности − цилиндры. Передачи с цилиндрическими колесами: прямозубые, косозубые, шевронные.
|
|

Достоинство косозубых колес состоит в бόльшем коэффициенте перекрытия, по сравнению с прямозубыми, что позволяет повысить плавность хода и передаваемое усилие.
Недостаток − осевая сила, для компенсации которой необходимо применять радиально-упорные подшипники. Устранен у шевронных передач.
2. Оси пересекаются (пространственные механизмы). Начальные поверхности −конусы. Коническая передача: колеса с прямыми, тангенциальными и криволинейными зубьями
Модуль передаточного отношения . (3.1.2)
|
3. Скрещивающиеся оси (пространственные механизмы). Начальные поверхности − гиперболоиды вращения. Применяются упрощенные варианты:
Начальные поверхности − цилиндры: винтовая передача и ее модификация − червячная.
Начальные поверхности − конусы: гипоидная передача и ее модификация − спироидная.
Основные размеры прямозубого эвольвентного колеса
Основная теорема зацепления. Общая нормаль к вращающимся соприкасающимся профилям (зубьям) делит межосевое расстояние обратно пропорционально угловым скоростям профилей.
|
|
Для равномерного вращения обоих колес точка ее пересечения с линией центров должна быть неподвижной. Это условие выполняется, в частности, для профилей, очерченных по эвольвенте окружности.
Модуль зацепления m − число миллиметров диаметра какой-либо окружности колеса приходящееся на один зуб.
Делительная окружность − окружность зубчатого колеса, на которой модуль и шаг принимают стандартное значение.
Шаг p − расстояние по дуге окружности между одноименными точками профилей соседних зубьев (рис. 3.1.6).
|
|

|
Толщина зуба sy − расстояние по дуге окружности ry между разноименными точками профилей зуба. Ширина впадины ey − расстояние по дуге окружности ry между разноименными точками профилей соседних зубьев.
Угол профиля αy − острый угол между касательной к профилю в данной точке и радиусом-вектором, проведенным в данную точку из центра колеса.
Инволюта inv αy − угол развернутости эвольвенты, табличная функция αy
|
|
Для сокращения номенклатуры режущего инструмента стандарт устанавливает нормативный ряд модулей и определенные соотношения между размерами элементов зуба. Эти соотношения определяются:
§ для зубчатых колес определяются параметрами исходной рейки через параметры ее нормального сечения − исходный контур;
§ для зубчатого инструмента определяются параметрами исходной производящей рейки через параметры ее нормального сечения − исходный производящий контур (рис. 3.1.7);
По ГОСТ 13755-81 значения параметров исходного контура должны быть следующими:
· угол главного профиля α = 20 0 ;
· коэффициент высоты зуба h*a = 1 ;
· коэффициент высоты ножки h*f = 1,25;
· коэффициент граничной высоты h*l = 2 ;
· коэффициент радиуса кривизны переходной кривой r *f = c* / ( 1 - sinα ) = 0,38 ;
· коэффициент радиального зазора в паре исходных контуров c* = 0,25 .
|

Производящий контур − проекция режущих кромок инструмента на плоскость перпендикулярную оси заготовки. Исходный производящий контур отличается от исходного высотой зуба h0 = 2,5m.
Изготовление зубчатых колес
Нарезание эвольвентных профилей методом обката или огибания является наиболее распространенным способом производства зубчатых колес. Режущим инструментом в этом случае может быть зубчатая рейка (гребенка), червячная фреза или долбяк в форме шестерни. Нарезание колес производится соответственно на зубострогальном, зубофрезерном или зубодолбежном станках. Применяется также горячий прокат.
|
|
При обкатке режущий инструмент и заготовка получают относительное движение, такое же, как при зацеплении зубчатой рейки (или шестерни) с колесом.
Наиболее распространенными станками для нарезания эвольвентных .цилиндрических колес методом обкатки являются зубодолбежные станки с инструментом в виде режущей шестерни. Для нарезания эвольвентных колес с крупным модулем более приспособлен зубострогальный станок с инструментом − рейкой. Процесс нарезания колеса рейкой осуществляется при сложном движении заготовки А (рис. 3.1.8), складывающемся из поступательного и вращательного движений в горизонтальной плоскости, и при возвратно-поступательном движении инструмента Б по вертикали.
Обкаточное движение подачи заготовки происходит в промежутке между двумя рабочими ходами инструмента, когда он находится в верхнем положении.
Преимуществом зуборезных станков, работающих по методу обката, является то, что одним и тем же инструментом можно нарезать эвольвентные профили зубьев для колес с разными числами зубьев.
|
|
|
Делительная прямая рейки − прямая, касающаяся делительной окружности колеса.
Делительная окружность колеса − окружность, на которой шаг зацепления равен шагу инструментальной рейки .
Если делительная окружность колеса касается модульной прямой рейки, то профиль зуба будет нормальным («нулевым» или «некорригированным»). У такого колеса высота головки зуба hг равна модулю, а толщина зуба S по делительной окружности равна ширине впадины
Корригированными или «исправленными» называются зубчатые колеса, нарезанные смещенной инструментальной рейкой (рис. 3.1.9). В этом случае делительная окружность колеса с модульной прямой рейки не соприкасаются. Корригирование зубчатых колес производится с целью уменьшения габаритов и улучшения качества (исправления) зацепления: устранения подрезания ножки зуба, увеличения коэффициента перекрытия, уменьшения износа, повышения прочности зуба.
При нарезании корригированных колес расстояние между модульной прямой рейки и делительной окружностью нарезаемого колеса называется сдвигом рейки, где х называют смещением рейки.
Смещение рейки х сравнительно с ее положением для нормальных (нулевых) колес при сдвиге в направлении от центра колеса считается положительным, а в направлении к центру — отрицательным.
Минимальное смещение рейки, необходимое для устранения подрезания ножки зуба, определяется формулой
,
где f – коэффициент высоты головок зубьев,
z – число зубьев колеса,
– угол профиля рейки.
При f = 1 и =20° расчетная формула имеет вид
.
К методу обката можно отнести также нарезание зубьев червячной фрезой и прокат зубчатых колес.
|

Применяется также метод копирования,когда линия режущей кромки инструмента соответствует форме нарезаемого зуба: нарезание модульной фрезой. Недостаток: т.к. форма зуба даже для колес одинакового модуля зависит от числа зубьев, приходится на каждый модуль иметь 8 фрез.
К этому методу относятся также точное литье, штамповка.
Методы изготовления конических и гипоидных передач: зубострогание, нарезание резцовыми головками, протягивание.
Дата добавления: 2018-04-15; просмотров: 1170; Мы поможем в написании вашей работы! |
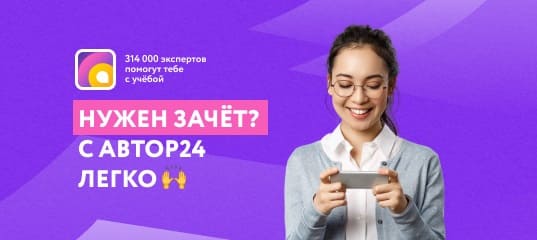
Мы поможем в написании ваших работ!