СИНТЕЗ ПЛОСКИХ РЫЧАЖНЫХ МЕХАНИЗМОВ
Синтез механизма − это проектирование механизма по заданным его характеристикам. Виды синтеза:
1. Структурный синтез – выбор устройства механизма. Производится обычно с помощью справочников по отдельным видам механизмов.
2. Кинематический синтез – проектирование кинематической схемы механизма (выбор размеров звеньев). Выполняется по известным кинематическим характеристикам механизма (ход ведомого звена, его средняя скорость и т.д.).
3. Динамический синтез − выбор масс и моментов инерции звеньев, положений их центров масс, форм звеньев и др. (например, определение момента инерции маховика и выбор его размеров). Выполняется по известным силовым и энергетическим характеристикам машины (мощность, сила полезного сопротивления и др.).
Синтез механизмов аналитическим способом
Начальная стадия синтеза состоит в установлении основных характеристик механизма, которые он должен иметь, чтобы успешно выполнять предназначенную ему работу. Часть этих характеристик может задаваться, исходя из технологических условий: например, известный максимальный размер обрабатываемых деталей на строгальном станке позволяет указать ход выходного звена (резца); оптимальная скорость резания металла, известная из технологии обработки металлов, определяет среднюю скорость выходного звена на этапе рабочего хода и т.д. Заданные характеристики механизма используются для составления уравнений, в которых неизвестными являются длины звеньев. Приведем несколько типичных примеров:
|
|
1. Пусть задан ход ведомого звена (ползуна) кривошипно-ползунного механизма (см. рис.1.1.5) Используя этот размер, можно составить уравнение
-
,
где неизвестными являются длины кривошипа и шатуна и дезаксиал а. В частности, при а = 0,
.
2. Угол давления на ведомое звено – это угол между силой, действующее на ведомое звено со стороны звена, приводящего его в движение, и скоростью точки приложения этой силы. Влияние весов и сил инерции звеньев, а также сил трения не учитывается (рис.2.6.1).
Рис. 2.6.1. Угол давления на выходное звено механизма
компрессора
Если силу , действующую на ведомое звено, разложить на две составляющие, то нетрудно заметить, что с увеличением угла давления полезная составляющая
уменьшается, а давление на направляющую
увеличивается: вместе ней увеличивается и сила трения, что приводит к повышению потерь мощности на трение и увеличение износа. Поэтому угол давления часто ограничивают, задавая максимальный угол давления на участке рабочего хода
, поскольку именно здесь на звенья механизма действуют наибольшие нагрузки.
|
|
Если ведомым звеном является кривошип (как, например, у двигателя внутреннего сгорания), угол давления на него достигает большой величины (рис. 2.6.2). В частности при механизм не сможет выйти из состояния покоя, какая бы большая сила не действовала на кривошип со стороны ползуна. Это состояние механизма называют явлением самоторможения.
Составим уравнение для длин звеньев кривошипно-ползунного механизма, пользуясь заданным максимальным углом давления на ползун на участке рабочего хода. Для этого изобразим механизм в том положении, когда угол давления на ползун достиг своего максимального значения (рис. 2.6.1): .
Из рис. 2.6.1 становится ясно, какую роль для кривошипно-ползунного механизма играет дезаксиал а: он позволяет уменьшить максимальный угол давления на ползун на участке рабочего хода. Очевидно, что без дезаксиала (а = 0) при тех же длинах кривошипа и шатуна этот угол будет больше. Следует сказать, что введение дезаксиала приводит и к отрицательным последствиям: увеличивается максимальный угол давления на ползун на участке холостого хода, но это незначительное ухудшение, т.к. сила давления на ползун на этом участке обычно имеет намного меньшую величину, чем при рабочем ходе.
|
|
Рис. 2.6.2. Самоторможение механизма двигателя внутреннего сгорания
Если задан максимальный угол давления на участке холостого хода , то можно составить еще одно уравнение:
.
3. Средняя скорость движения звена . Обычно для увеличения производительности проектируемой машины стараются повысить среднюю скорость движения выходного звена, но это повышение не может быть беспредельным из-за опережающего роста сил инерции, приблизительно пропорциональных квадратам скоростей звеньев, в результате чего увеличиваются нагрузки на звенья и потери мощности на трение, а так же повышается износ кинематических пар. Поэтому средняя скорость какого- либо звена может быть ограничена. Её заданное значение используют в уравнении
, где Т=
− период движения звена, обычно равный времени одного оборота кривошипа.
4. Коэффициент изменения средней скорости выходного звена К. Часто бывает, что скорость движения выходного звена на участке рабочего хода ограничена технологическими условиями. Например, слишком большая скорость строгания металла на строгальном станке вызывает повышенный износ резца. Поэтому повысить производительность проектируемой машины можно только путем увеличения скорости холостого хода (если такой имеется). С этой целью для кривошипных рычажных механизмов задают коэффициент изменения средней скорости выходного звена К, который равен отношению средних скоростей этого звена на участках холостого и рабочего ходов (см. рис. 2.6.3):
|
|
где - углы поворота кривошипа на участках холостого и рабочего ходов;
− угол между направлениями кривошипа в крайних положениях механизма. Он является дополнительным до
к углу холостого хода:
. Зная К, можно вычислить угол
:
.
Зная угол , например, для кривошипно-ползунного механизма, можно составить уравнение
соs
.
6. Если задана средняя скорость выходного звена на участке рабочего хода Vср..р , можно составить уравнение
Vср. р = .
7. Заданное отношение длин звеньев является готовым уравнением: например, при известном :
.
Если число составленных уравнений будет равно числу неизвестных, содержащихся в них, задача синтеза решается однозначно. Если число уравнений меньше числа неизвестных, проектировщик имеет свободу выбора некоторых из них. Обычно значения этих «лишних» неизвестных выбираются так, чтобы улучшить другие характеристики механизма, не учтенные заказчиком (например, уменьшить габариты или металлоемкость изделия и др.).
СИНТЕЗ ЗУБЧАТЫХ ПЕРЕДАЧ
Достоинства эвольвентного зацепления:
§ сохранение передаточного отношения при небольших изменениях межосевого расстояния;
§ изготовление эвольвентных колес, а также изготовление инструмента для их нарезания более простое по сравнению с зубчатыми колесами, у которых зубья очерчены по другим кривым.
Дата добавления: 2018-04-15; просмотров: 499; Мы поможем в написании вашей работы! |
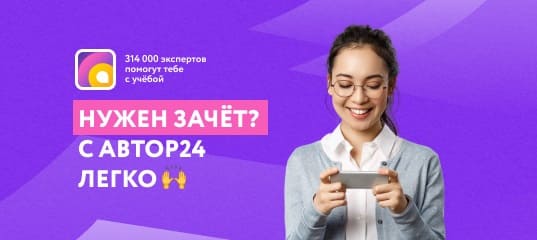
Мы поможем в написании ваших работ!