Утилизация колошниковых газов
Примерный состав колошникового газа:
Компоненты | СО2 | СО | СН4 | Н2 | О2+N2 |
Объемная доля в, %: при работе без повышения давления и комбинированного дутья………………………….. | 11.2 | 31.2 | 0.21 | 2.99 | 55.1 |
при работе с повышением давления и комбинированным дутьем…………………………… | 11.3 | 29.0 | 0.20 | 4.30 | 55.2 |
Температура доменного газа на выходе из печи составляет обычно 300-350 ºС.
Доменный (колошниковый) газ, содержащий до 35 % горючих компонентов и 50-60 г/м куб. пыли при работе печи с повышенным давлением на колошнике (и 15-20 г/м куб. - с нормальным давлением), должен быть очищен от пыли перед его отправкой потребителям - на коксовые батареи, на горелки доменных воздухонагревателей и др. - до достижения концентрации пыли не выше 10 мг/м куб. Для очистки газа до столь низких концентраций пыли на металлургических заводах применяют многоступенчатые комбинированные схемы.
Как правило, первоначально очистку доменного газа проводят в сухих пылеуловителях диаметром 5-8 м, в которых осаждаются частички пыли размером 50 мкм и более. В этих аппаратах улавливается 70-90 % пыли, содержащейся в доменном газе, благодаря воздействию сил гравитации и инерционных сил, возникающих при повороте газового потока на 180 градусов. Пыль из пылеуловителя удаляется при помощи винтового конвейера, смачиваемого водой. Остаточное содержание пыли в доменном газе после грубой очистки не превышает 3-10 г/м куб.
|
|
Для второй ступени очистки газа используют системы мокрой очистки. Обычно доменный газ из системы грубой сухой очистки поступает на полутонкую очистку газа, в которой выделяются частички размером 20 мкм и более и газ очищается до остаточного содержания пыли на выходе 0.6-1.6 г/м куб. Полутонкую очистку осуществляют в аппаратах мокрого типа - форсуночных полых скрубберах и трубах Вентури. Газы в доменных скрубберах имеют скорость 1-2 м/с при удельном расходе воды, состовляющем 3-6 кг/м куб. газа. Проходящий через скруббер доменный газ охлаждается с 250-300 до 40-50 градусов цельсия и полностью насыщается влагой. Степень очистки газа от пыли в скруббере не превышает 60-70 %.
После скруббера газ в большинстве случаев поступает в две- четыре низконапорные трубы Вентури, скорость газов в горловине которых равна 50-80 м/с при удельном расходе воды 0.2 кг/м куб. Здесь завершается полутонкая очистка газа.
Тонкую очистку доменного газа, содержащего до 10 мг/м куб. пыли,осуществляют в аппаратах 1 класса. В связи с широким внедрением на заводах черной металлургии газорасширительных станций, использующих потенциальную энергию давления доменного газа для выработки электроэнергии в газовых утилизационных бескомпрессорных турбинах (ГУБТ), для тонкой очистки газа обычно применяют аппараты, работающие с малой потерей давления, например мокрый электрофильтр.
|
|
Таким образом, в зависимости от наличия или отсутствия ГУБТ, на отечественных заводах обычно применяют две схемы очистки доменного газа:
1) доменная печь - сухой пылеуловитель - форсуночный полый скруббер - труба Вентури - каплеуловитель - дроссельная группа - каплеуловитель - чистый газ потребителю;
2) доменная печь - сухой пылеуловитель - форсуночный полый скруббер - труба Вентури - каплеуловитель - мокрый электрофильтр - чистый газ на получение электроэнергии в ГУБТ.
Выбор системы очистки доменного газа зависит от требуемой степени его чистоты и экономических показателей пылеочистки. При применении трубы Вентури расходуется около 600-800кг воды и 10.8-14.4 МДж электроэнергии на 1000 м куб. газа.
За трубой Вентури устанавливают каплеуловитель-сепаратор, которым может быть мокрый циклон, скруббер или канальный сепаратор.
В электрофильтрах для промывки и охлаждения электродов расходуется 0.5-1.5 кг воды и 3.6-4.3 МДж электроэнергии на 1000 м куб. газа.
Затраты на устройства для очистки от пыли и газов всех основных источников загрязнения атмосферы доменного цеха, т.е. газов, отводимых при загрузке кокса в бункеры6 транспортировании и сортировке руды и кокса перед загрузкой в печь, отводе доменного газа и воды из очистных сооружений и отстойников, составляет примерно 15-20 % суммы всех капиталовложений цеха, включая и все соответствующие вспомогательные службы.
|
|
Объем капиталовложений зависит от мощности предприятия и его технической оснащенности. Некоторые устройства используют одновременно для нескольких пылегазоочистных агрегатов (газоходы, отстойники устройства для переработки шлама, вспомогательные агрегаты), благодаря чему объем капиталовложений снижается.
Эксплуатационные затраты на очистные сооружения доменного цеха зависят в основном от стоимости электроэнергии, водоснабжения и обслуживания.
Тема № 7. “Развитие бездоменной металлургии”
7.1. Предпосылки развития бездоменной металлургии
Длительная история сталеплавильного производства всегда была связана со стремлением решить некоторые характерные технические проблемы наиболее удобным способом. Хотя сравнительное значение этих проблем за последние 150 – 180 лет изменилось, все же они остаются важными и до настоящего времени. Имеются в виду следующие проблемы:
|
|
- достижение высоких температур (> 1500 С) с приемлемыми затратами энергии;
- обеспечение высокой стойкости футеровки и других конструктивных элементов;
- обеспечение чистоты металлопродукции от вредных примесей, снижающих ее качество;
- дефицит металлургического кокса;
- снижение общего расхода энергии;
- возможность применения подходящей кусковой руды.
Регулярно делаются все новые попытки решить хотя бы некоторые из этих проблем переходом от схемы доменная печь — конвертер к прямому пути или по крайней мере без применения металлургического кокса. Решение, в основном удовлетворительное в техническом и экономическом отношениях, пока удалось осуществить лишь немногими способами.
7.2. История развития
В России первое внушительное слово в области бездоменной металлургии сказал известный миру русский ученый Д.К. Чернов (1839–1921 гг), являющийся основоположником металловедения и теории термической обработки стали. В январе 1899 г. Он сделал доклад в Императорском Русском техническом обществе на тему: «О прямом получении литого железа и стали в доменной печи». Суть его предложения в докладе выражена так: «Ввиду того, что переход железа в чугун обуславливается преимущественно тесным соприкосновением его с твердым топливом при очень высоких температурах, необходимо удалить это обстоятельство; принимая же во внимание возможность полного восстановления железа лишь с помощью одной углеродной окиси, можно или вовсе не примешивать угля к рудной засыпке или же прибавить такое небольшое количество, чтобы железо могло лишь несколько обуглеродится, но не перейти в чугун. Тогда спускающийся в плавильное производство рудный столб не принесет с собою угля или кокса, как при обыкновенном ходе доменной печи.
Для достижения предполагаемой цели необходимо пропустить через печь два отдельных тока газов: один по шахте вверх, навстречу спускающейся руде, для восстановления железа, а другой, в области горна, для расплавления восстановительного железа и шлаков с отводом продуктов горения из горна в сторону, дабы они не попадали в шахту печи и не мешали восстановительному току». Далее он описывает детали предложения, с помощью которых возможно реализовать главную его идею. (рис. 7.1.)
Рис. 7.1. Печь В.К. Чернова для прямого получения литого железа:
1 – шахта печи; 2 – газогенератор; 3 – плавильный горн; 4 – труба с углем для повышения теплотворной способности газа
Последующий предложения содержат в себе главную идею Д.К.Чернова. В том же 1899 г. Д.К.Чернов высказал и другую идею прямого получения стали путем восстановления железа углеродом из расплавленных оксидов.
Способ "Хёганес" был разработан в 1911 г. и заключается в следующем: весьма чистый магнетитовый концентрат загружают вместе с восстановителем (мелким углем) и доломитом (десульфуратором) в реторты из карбида кремния, причем кольцеобразный цилиндрический столб руды окружен изнутри и снаружи смесью мелкого угля и доломита. Вертикально поставленные реторты обогревают в туннельной печи мазутными или газовыми горелками в течение 48 ч (рис. 7.2). Затем их охлаждают, удаляют остатки золы угля, доломит и коксовую мелочь, после чего извлекают железный порошок с высокой степенью металлизации.
Рис. 7.2. Схема процесса Хёганес (а):
б – расположение реторт на рельсовой тележке; в – поперечное сечение реторты;
I – зона предварительного нагрева; II – зона восстановления; III – зона охлаждения;
1 – карбид кремния; 2 – железорудный концентрат; 3 – смесь мелкого кокса с известняком
Способ Виберга — Сёдерфорса был разработан в 19-20-х годах тоже в Швеции. Кусковые оксиды железа (кусковую руду, агломерат, окатыши) нагревают и восстанавливают в шахтной печи газом (~ 75 % СО и 21 % Н2) при температуре 900-950 °С (рис. 7.3). Полученное губчатое железо охлаждают в нижней водоохлаждаемой секции печи до 100—150 °С. Выходящий из восстановительной печи циркуляционный (колошниковый) газ вместе с водяным паром нагнетают специальной высокотемпературной газодувкой в электрогазогенератор (шахтную печь, заполненную коксом) сверху вниз, Здесь происходит газификация нагреваемого электросопротивлением кокса (по реакции С + С02 = 2 СО), причем содержащаяся в нем сера переходит в свежий восстановительный газ, имеющий температуру ~ 1100 °С, который затем подвергают десульфурации в другой шахтной печи, заполненной доломитом. Производительность с учетом возможностей оборудования не превышает ~ 25 тыс. т в год. При этом на 1 т губчатого железа расходуется 150 кг кокса и 900 кВт • ч электроэнергии.
Рис. 7.3. Схема процесса Виберга-Сёдерфорса:
1 — кокс (или мазут); 2 — подвод электроэнергии; 3 — десульфуратор; 4— избыточныйвосстановительный газ; 5 —окатыши; 6 — отходящий газ; 7 —воздух;
8 — губчатое железо
В конце 50-х годов в странах, имеющих сталеплавильное производство, усилились работы в области прямого восстановления железа, причем параллельно испытывали способы, использующие как твердый восстановитель, так и газ. Эти способы восстановления могут быть подразделены на несколько групп: твердым восстановителем во вращающейся печи; твердым восстановителем в шахте с наружным обогревом; газом в шахтной печи; газом в ретортах; газом в кипящем слое; по схеме решетка — вращающаяся печь.
В это же время разрабатывали и восстановительную плавку металла из руды отчасти для специальных металлургических целей, имея в виду обеспечить последовательное восстановление углем руды предварительно в одной (например, во вращающейся) печи и из продукта, полученного на выходе из этой печи, выплавлять в электровосстановительной печи жидкий металл.
Из всех способов восстановления металла твердым восстановителем во вращающейся печи наибольшее значение приобрели следующие: СЛ — РН; получения губчатого железа фирмы "Крупп" (Крупп — КОД ИР); фирмы "Кавасаки стил"; СДР (способ восстановления в пылевидном состоянии фирмы 'Сумитомо"; СПМ (способ предварительного восстановления фирмы "Сумитомо"); ДРК (корпорации "Директ редакшен); АККАР (способ КОХО) и "Механобрчермет" (СССР).Здесь следует упомянуть также способы: "Хейвелд" ("Элкем" — "Лурги ' - ХСВК); завода "Сибэлектросталь" (СССР); М. Юди ("Стра-теджик Юди"); В.П.Ремина (СССР); НПО "Тулачермет" (кипящий шлаковый слой, СССР).
В качестве основного агрегата во многих способах используют принципиально одинаковый восстановительный реактор — вращающуюся печь. Вместе с оксидами железа в печь загружают уголь (или коксовый возврат) в качестве восстановителя и известняк или доломит в качестве десульфуратора. В первой половине печи оксид железа нагревается, из угля отгоняются содержащиеся в нем летучие, а известняк или доломит обжигаются. Во второй половине происходит восстановление до металлического губчатого железа, причем благодаря дополнительным добавкам угля обеспечивается достаточно высокое содержание углерода в шихте и на выходе из печи. В некоторых способах поэтому применяют устройство для вдувания угля, чтобы ввести в шихту дополнительное количество свежего угля, начиная от выхода из печи. Поток газа направлен навстречу потоку шихты.
Газы, выходящие из шихты, дожигают при помощи ряда воздушных фурм, распределенных по всей длине печи. При этом количество воздуха, вдуваемое на отдельных участках, определяют по количеству тепла, необходимого для поддержания заданного температурного режима по длине печи.
Направление подачи воздуха через фурмы иногда бывает противоположным направлению потока газов. Имеются различия в конкретном исполнении воздушных фурм, в исполнении и расположении измерительных устройств, с помощью которых обеспечивают управление процессом.
Горячий продукт из вращающейся печи охлаждается в расположенном ниже охладителе (который обычно выполняется в виде вращающегося барабана) до температуры < 100 °С. Снаружи охлаждающий барабан орошается водой, иногда в него дополнительно впрыскивают воду, охлаждая металл в комбинированном режиме.
Вращающаяся печь и охладитель защищены от неконтролируемого проникновения воздуха при помощи уплотнений со шлифованными (притертыми) кольцами. Для загрузки исходного материала и выгрузки готового продукта предусмотрены шлюзы. Охлажденный продукт на грохотах и магнитных сепараторах разделяют на губчатое железо, оборотный восстановитель (возврат) и немагнитную фракцию (рис. 7.4).
Рис. 7.4. Схема восстановления твердым восстановителем во вращающейся (барабанной) печи, например процесса СЛ-РН:1-железная руда, уголь, известняк; 2-лервая камера дожигания; 3-вода; 4-воздух; 5-вторая камера дожигания; 6-воздух; 7- котел-утилизатор; 8-электрофильтр; 9 -отходящий газ в атмосферу; 10-пыль; 11 -вращающаяся обжиговая печь; 12-воздух; 13 -подача угля в воздушном потоке; 14 - горячая завалка;15-электропечь; 16-вода; 17 -вращающийся охладитель; 18-грохочение; 19- магнитная сепарация;
20 -губчатое железо; 21 -отходы (хвосты)
Более существенные различия между отдельными процессами имеются в области подготовки исходных материалов. По способам СЛ-РН и КОДИР в восстановительную печь загружают оксид железа только в кусковой форме (окисленные окатыши, кусковую руду или их смеси) с возможно более точным контролем гранулометрического состава и соотношения между оксидом и углеродсодержащим материалом. В способах, предназначенных для переработки металлургической пыли, оксиды в виде сырых окатышей предварительно упрочняются на решетке, расположенной непосредственно перед входом (загрузкой) во вращающуюся печь.
Отходящие из вращающейся печи газы иногда после дожигания (с использованием их тепла) охлаждают, очищают и затем выбрасывают в атмосферу. Пыль, уловленная на фильтрах, и шлам содержат большие количества свинца и цинка, достаточные для их извлечения на последующем этапе переработки.
В принципе, по группе способов восстановления твердым восстановителем можно заключить, что способы восстановления во вращающейся печи допускают широкое варьирование условий работы. Можно перерабатывать различные руды, значительно различающиеся и по химическому, и по гранулометрическому составу, что позволяет решать специальные задачи. То же самое относится и к углеродсодержащему материалу: здесь можно применять и коксовую мелочь, и уголь всех марок вплоть до лигнита.
Эксплуатация таких агрегатов, однако, показывает, что процессом восстановления необходимо управлять достаточно точно, и это предъявляет высокие требования к измерительным приборам и регулирующему оборудованию. Длительное время работы без неполадок возможно только при хорошей подготовке шихты, точном дозировании и надежном измерении температуры, состава газа и расхода воздуха.
Производительность одной линии технологических агрегатов ограничена, отчасти и по механическим причинам. Во вращающихся печах диаметром > 5 м критическим фактором является стойкость огнеупорной футеровки. К тому же условия теплопередачи в такой печи менее благоприятны, чем, например, в шахтной, вследствие чего с повышением диаметра печи температура газа (при заданной температуре шихты) неизбежно должна быть более высокой. Четкие пределы ставятся и температурой размягчения шихты, зависящей от используемого исходного сырья. Если эта температура будет превышена, то произойдет неконтролируемое настылеобразование и агломерация материалов, что вынудит прекратить работу.
Несмотря на высокие требования к исполнению всех деталей и к управлению режимом работы, в техническом отношении восстановительные агрегаты с вращающейся печью несложны и весьма надежны.
Особое положение здесь занимают способ АККАР (рис. 7.5), разработанный в конце 60-х годов фирмой "Аллис Чалмерс", а также способ института "Механобрчермет".
Рис. 7.5. Схема процесса АККАР (реактор с контролируемой атмосферой фирмы "Аллис Чалмерс") : 1 — расходные бункера с шихтой; 2 — грохочение; 3 — бункер для мелочи;
4 — реактор с контролируемой атмосферой; 5 — скруббер; 6 — эксгаустер; 7 — дымовая труба; 8 — подвод мазута; 9 — подвод газа; 10 — охладитель; 11 — магнитная сепарация;
12 — бункер для немагнитной фракции; 13-силосы с готовым продуктом
В качестве восстановительного реактора здесь тоже применяют вращающуюся печь. Особенно характерно первоначально намеченное использование только углеводородов (природного газа или мазута), которые через систему сопел впрыскивают в печь под слой шихты.
Напротив, воздух для сжигания газов вдувают только в свободное печное пространство под шихтой. Поэтому на корпусе печи необходимо иметь систему труб и клапанов, при помощи которой в нужном положении вводят в действие сопловые отверстия, расположенные по всему периметру и по всей длине печи. Опыт эксплуатации показал, что в шихту целесообразно дополнительно вводить твердый углерод в форме угля.
Особое положение занимают также и способы, при которых восстановление руды (по крайней мере частичное) проводят во вращающейся или другой печи, затем горячий продукт перерабатывают в электропечи в металл. В истории развития этих процессов важное значение имели способы В.П.Ремина(СССР) и «Стратеджик Юди»(США), хотя их промышленное применение и не было успешным (рис. 7.6 и 7.7).
Рис. 7.6 Схема электропечи для получения литого железа из руды по методу В.П.Ремина: 1 – камера восстановления; 2 – устройство для подачи восстановления;
3 – кессон для подачи воздуха; 4 – питатели; 5 – контейнеры; 6 – пневматический толкатель; 7 – подовый электронагреватель шихты; 8 – камера подготовки
Они были независимо разработаны в конце 40-х – начале 50-х годов. По этим способам руду, уголь и известняк нагревали и частично восстанавливали отходящим газом из расположенной далее по потоку восстановительной электропечи (степень восстановления руды достигала 30-60%).
Печь В.П.Ремина "глетчерного" или шахтного типа состояла из двух частей: "глетчера" — наклонного пода или шахты, предназначенных для использования тепла отходящих из электропечи газов для нагрева, восстановления до вюстита и плавления шихты; электропечи, предназначенной для восстановления руднофлюсового расплава углеродом полукокса до жидкого железа (низкоуглеродистой стали).
Непрерывно загружаемая в печь смесь из руды (54 % железа в виде гематита крупностью 50 мм) и извести (из расчета основности шихты CaO/Si02 > 2) нагревались до 400-500 °С на наклонном поду (или в шахте с перекрестным теплообменом) пламенем от сжигания отходящего из электропечи газа и методически сталкивалась механическими толкателями в ванну (площадью 25 м2) дуговой электропечи (5 MB-А, 120—267 В), имевшей линейное расположение трех электродов диаметром 300 мм. Здесь шихта расплавлялась и металл восстанавливался из оксидного расплава углеродом полукокса (7 % золы; 0,3—0,4 % серы; крупность < 30 мм), подававшегося питателем через отверстие в своде печи.
Рис. 7.7. Схема процесса "Стратеджик Юди":
/-обычная низкошахтная электропечь; //-печь, применяемая в процессе "Стратеджик Юди"; 1 -бункер подачи шихтовых материалов; 2-вибрационный грохот; 3-дробилка;
4-ленточный конвейер с расходным бункером; 5 -вращающаяся печь; 6-пылеотделитепь (циклон); 7-выход газа; 8 - 10 -расходные бункера руды, добавок, угля соответственно;
11 -ленточный конвейер от дозаторов шихтовых материалов; 12 — подвод добавочного топлива и воздуха; 13 — дозирование шихты в электропечь; 14-электропечь; 15 -печной трансформатор; 16-газ; 17 — жидкий передельный чугун; 18 — шлак.
Вращающаяся печь (М.Юди) не имела подвода воздуха через корпус, следовательно, был предусмотрен только один подвод тепла со стороны выгрузки из печи. Предварительно восстановленный материал вместе с прокаленным углем загружали через футерованную течку (воронку) в дуговую печь, где происходило окончательное восстановление металла и его плавление. Для управления балансом углерода был предусмотрен дополнительный подвод угля через отверстия в корпусе печи (с помощью черпаков). Это делалось для того, чтобы в электропечь поступал только прокаленный углеродсодержащий материал.
Важнейшими проблемами, неразрешенными в процессе испытания способа В.П.Ремина, как и способа М.Юди, явились подвод тепла в зону реакции восстановления железа углеродом из оксидного расплава в начале процесса и подвод оксидов железа в зону реакции при его завершении. Реакция (FeO) + Ств (или [С]) = Fеж + С0газ является сильно эндотермической, что приводит к охлаждению расплава. Кусочки восстановителя, отягченные корольками восстановленного железа (или капли восстановленного науглероженного железа), все глубже погружаются в оксидный расплав, охлаждая и вспенивая его вокруг себя реакционным монооксидом углерода. Этот процесс, бурный при умеренной подаче восстановителя, становится неуправляемым при его избытке, так как, погружаясь до нижних слоев, он превращает в пену весь находящийся в ванне оксидный расплав. Пена фонтанами бьет из электродных отверстий и загрузочных устройств, электрические дуги, поднимаясь вместе с пеной, горят под сводом, вызывая ток, близкий к короткому замыканию, плавка прекращается по воле оператора или в результате автоматического отключения.
Подача восстановителя, исключающая катастрофическое вспенивание, обеспечивала восстановление до 0,22 т/ч железа на 1 м поверхности руднофлюсового расплава. Снижение удельной производительности и было особенно заметно при достижении содержания оксидного железа в шлаке <15 %. В это время возникала вторая проблема — замедление процесса восстановления из-за уменьшения поверхности контакта и концентрации реагентов; интенсивность кипения шлаковой ванны снижалась, а вязкость шлака возрастала.
Таким образом, интенсификация процесса восстановления железа из оксидного расплава возможна при обеспечении подвода в зону реакции энергии в начале процесса и оксида железа при его завершении.
Способ Н.А.Ярко, И.Ю.Кожевникова (1959 г.) состоит в восстановлении железа из рудоугольных брикетов или окатышей в кипящем шлаковом слое (КШС). Рудоугольные окатыши, содержащие стехиометрическое и большее количество углерода, загружали в кипящую ванну мартеновской печи (опыты проводили на 10-т печи), где они нагревались и восстанавливались. Тепло сжигаемого над ванной реакционного монооксида углерода использовали для процесса. Восстановление железа в основном завершалось в твердом состоянии и только часть оксида железа переходила в шлак. Проблемы этого способа близки к проблемам способов В.П.Ремина и М.Юди. Здесь также интенсивность восстановления определялась подводом тепла в шлаковую ванну и достигала 3,7 т железа на 1 м поверхности ванны в сутки, т.е. была близка к производительности упомянутых способов. Содержание железа в конечном шлаке и при этом способе оставалось большим (до 20 %), извлечение железа соответственно составило 80—90 %, что объясняется высоким окислительным потенциалом греющего факела. Расход тепла достигал > 20 ГДж на 1 т жидкого металла.
Способ "Элкем" с вращающейся печью был разработан примерно в середине 50-х годов. При этом способе в печь загружали руду, уголь и в случае необходимости известняк, которые подвергались нагреву, предварительному восстановлению и обжигу. Горячий продукт, выгружаемый из печи, доставляли в транспортных контейнерах к рудовосстановительной электропечи и загружали в нее через специальный бункер, расположенный над печью. Количество углерода, необходимого для полного восстановления железа, подавали во вращающуюся печь. Газ из электропечи, богатый монооксидом углерода, первоначально сжигали на свече, а отопление вращающейся печи было независимым.
В ЮАР на заводе фирмы "Хайвелд стил энд ванадиум корп." с конца 60-х годов успешно эксплуатируют усовершенствованный вариант этого процесса, который постепенно был внедрен на 14 установках. Применяемый на этом заводе ванадийсодержащий титаномагнетит непригоден для передела в доменных печах. Благодаря сравнительно большому доходу от дополнительного производства ванадия такой технологический маршрут на данном заводе остается экономически выгодным вот уже в течение почти двух десятилетий. Вращающиеся печи фирмы "Пурги", работающие в прямотоке, отапливаются мелким углем и дополнительно отходящим газом от электропечи со стороны их загрузки. Воздушные фурмы, расположенные по длине печи, обеспечивают дожигание газа, образующегося в самой вращающейся печи {летучих из коксуемого угля и реакционного газа), чем достигается равномерный температурный режим.
В рудовосстановительной электропечи при плавке предварительно восстановленной руды ванадий переходит в чугун, а титан — в шлак. Затем при обработке в ковше получают ванадиевый шлак, а передельный чугун перерабатывают на сталь.
Другие такие установки были построены на заводе в Скопле (СФРЮ) в первую очередь для производства ферромарганца и ферроникеля.
Рис. 7.8. Крупнолабораторная установка трубчатая печь-электропечь (I – V места установки термопар): 1 – механизм перемещения электродов; 2 – электропечь; 3 – разгрузочная головка; 4 – трубчатая печь; 5 – пылеуловитель; 6 – течка; 7 – питатель; 8 – скруббер; 9 – регулятор давления
В СССР в 1960—1966 гг. был разработан и используется до сих пор способ, похожий на способ "Элкем" и отличающийся от него тем, что восстановление руды во вращающейся печи заканчивают при степени металлизации железа > 90 % и плавят из горячего губчатого железа в электропечи с открытой дугой не чугун, а сталь. Этот способ был реализован в установке вращающаяся печь — электропечь завода "Сибэлектросталь". Эта установка (как и советские установки БМК и ЗМЗ) была использована для проведения испытаний проб окисленных окатышей, предназначенных для разработки технологии ОЭМК. Поэтому ее схема и технология описаны более подробно. Исследования проводили в крупнолабораторной и полупромышленной вращающихся печах.
Крупнолабораторная печь (рис. 7.8) с внутренним диаметром 0,75 и длиной 6 м имела угол наклона к горизонту 4° и могла вращаться с частотой до 3 мин -1. Ее отапливали центральной керосиновой горелкой или путем сжигания реакционных газов и части угля воздухом, подаваемым через центральную фурму в разгрузочной головке печи. В некоторых случаях воздушное дутье обогащали кислородом.
Исходную шихту (рудоугольные или рудные окатыши, известняк и уголь) подавали из бункера в загрузочную головку трубчатой печи. Металлизованная горячая шихта из разгрузочной головки через водо-охлаждаемую течку поступала в электропечь.
Полупромышленная вращающаяся печь также входит в состав агрегата для получения жидкого металла (рис. 7.9); она имеет внутренний диаметр 3 м, длину 21 м, угол наклона к горизонту 2°, частоту вращения 0,2—1,5 мин . Воздух в печь подают через пять фурм, из которых три (периферийные) установлены на ее кожухе и по одной (цент- ральные) в разгрузочной и загрузочной головках печи. В качестве дополнительного топлива используют мазут, холодный или горячий (600 °С) тонкодисперсный буроугольный полукокс, нагретую до 200 °С сухую буроугольную пыль, которые могут быть поданы в печь через горелки, установленные в ее головках. Кроме того, в различное время были опробованы устройства для подачи по длине печи буроугольного полукокса под слой шихты и бурого угля в три точки через спиральные течки и отверстия в футеровке и забрасыванием с помощью воздуха через горячий конец печи на слой шихты.
Рис. 7.9. Схема полупромышленной установки для производства бескоксовой электростали завода "Сибэлектросталь": 1—конвейер; 2 —устройство для удаления золы из металлизованных окатышей; 3-трубчатая печь: 4 - транспортер; 5 - конвейерная обжиговая машина; 6-ролико-укладчик; 7 - гранулятор; 8, 9 - элеваторы; 10 - питатели; 11 - 13 - бункера известняка, концентрата и угля
Печь может работать как при противоточном, так и прямоточном движении материалов и газов. При противотоке шихтовые материалы подают через загрузочную головку, а дополнительное топливо и воздух — через разгрузочную. При прямотоке дополнительное топливо и воздух подают через загрузочную головку. Периферийные фурмы работают в любом случае. Уголь, известняк и иногда окатыши подают в печь в холодном состоянии. Обычно окатыши используют в горячем состоянии (800-1000 °С) непосредственно после окислительного обжига на сочлененной с трубчатой печью конвейерной машине площадью нагрева 6,4 м2 или после нагрева в шахтном подогревателе. Конструкция обжиговой машины аналогична конструкции конвейерной печи для металлизации рудоугольных окатышей.
При противотоке отходящий газ подается на конвейерную машину или шахтный подогреватель и далее поступает на газоочистку. При прямотоке весь газ после предварительного охлаждения водой поступает на газоочистку. Температуру газа по длине вращающейся печи контролируют с помощью термопар. Непрерывно контролируют расходы воздуха и дополнительного топлива, а также давление газа.
Способы восстановления твердым восстановителем (в твердой фазе) в шахте с наружным обогревом не нашли широкого применения, хотя они, бесспорно, важны для получения небольших количеств губчатого железа. Старейшим из двух промышленно применявшихся способов является способ "Эчеверрия", разработанный в конце 50-х годов в Легаспии (Испания).
Кусковую руду или окатыши загружают в непрерывно работающую шахту из жаростойкой стали вместе с антрацитом и известняком. В верхней части шахты эти материалы подогреваются восстановительными газами, а в восстановительный зоне руда восстанавливается при температуре ~ 1050 °С. Тепло, требуемое для восстановления, подводится в столб шихты снаружи через стальной корпус, обогреваемый газовым факелом. В нижней части шахты продукт охлаждается косвенным способом водой. Принцип косвенной теплопередачи в восстановительной зоне ограничивает размеры шахты, что ставит предел и возможной производительности. Срок службы шахты тоже ограничен. Даже при потребности в губчатом железе 20 тыс. т в год требовалось 20 шахтных печей, вследствие чего в цехе было занято большое число работающих.
Фирма "Даниэли" (Буттрио, Италия) разработала в конце 70-х годов способ "Кинглор-Метор" (рис. 7.10), который по сути является усовершенствованием способа "Эчеверрия".
Рис. 7.10. Схема процесса "Кинглор— Метор":
1—руда; 2 — восстановитель; 3 — оборотный уголь; 4— подготовка смеси шихтовых материалов; 5 — загрузочная тележка; 6 — шихтован смесь; 7 — шахтная печь; 8 —отопление шахтной печи по зонам; 9 —охлаждающее устройство; 10 —выгрузка (губчатого железа); 11 — грохочение; 12 — магнитный сепаратор; 13— отсос пыли; 14 —отходящие газы; 15 и 16-магнитная и немагнитная мелкая фракция; 17 — губчатое железо
Решающими факторами, обеспечивающими экономичность процесса, были: изменение формы восстановительной шахты (которую выполнили прямоугольной), разделение обогреваемой области на зоны, применение карбида кремния в качестве материала корпуса шахты и использование модульной конструкции. Здесь тоже нагревали в верхней части шахты кусковую руду, уголь и известняк, восстанавливали руду в восстановительной зоне при температуре ~1050 °С и охлаждали полученный продукт в нижней зоне косвенным способом.
Разделение материала, выгружаемого из печи, осуществляли грохочением и магнитной сепарацией; затем неиспользованную часть углеродоносителя здесь тоже возвращали обратно в шихту.
По удельным капиталовложениям и эксплуатационным расходам этот способ вполне может конкурировать с процессами, обусловливающими производительность ≥300 тыс. т продукции в год, хотя агрегаты этого типа соответствуют по производительности (20 тыс. т) сталеплавильным минизаводам.
7.3. Принцип работы установки П.В.
Восстановление мелкой руды газом в кипящем слое
Уже в конце 50-х годов были начаты попытки получать губчатое железо из мелкой руды в кипящем слое. Из различных предлагавшихся. способов в промышленных масштабах были опробованы только три. В числе важнейших могут быть названы способы "Новальфер", Х.И.Б. и "Фиор".
Работы по способу "Новальфер" (рис. 7.11) велись в Тулузе (Франция) еще до 1950 г. В кипящем слое из мелкой руды (содержащей> 90 % фракции 0,1—0 мм) при помощи газа с большим содержанием водорода получали порошок губчатого железа. На восстановительном этапе (в кипящем слое) мелкая руда, подогретая до ~ 850 °С, подвергалась металлизации до ~ 67 %, а если требовалась более высокая степень металлизации, то после охлаждения, на втором этапе восстановления, при температуре ~ 580 °С этот показатель можно было довести почти до 92 %. Двухступенчатое восстановление с промежуточным охлаждением было принято для того, чтобы не допустить внезапного осаждения кипящего слоя из-за слипания частиц при превышении степени восстановления ~ 75 %. В качестве восстановительного газа использовали водород с близлежащего аммиачного завода, прошедший паровую конверсию с большим избытком пара, отмывку от СО2 и подогрев.
Рис. 7.11. Схема процесса “Новальфер”
1 — руда; 2 — природный газ; 3 — предварительный подогрев руды в кипящем слое;
4 — подогреватель воздуха; 5 — воздух; 6 — бункер; 7 — охладитель; 8 — магнитный сепаратор; 9 — пустая порода; 10 — порошок губчатого железа со степенью металлизации 75 %; 11 — подогреватель (порошка ГЖ с первой ступени восстановления в кипящем слое); 12 — скруббер системы газоочистки; 13— порошок губчатого железа со степенью металлизации 92 %; I и II — ступени восстановления
По способу Х.И.Б. (рис. 7.12), который был разработан как процесс НУ-АЙРОН в середине 50-х годов, фирма "Юнайтед Стейтс стил" построила в конце 60-х годов в Пуэрто Ордас (Венесуэла) промышленную установку.
Рис. 7.12. Схема процесса ХИБ:
1 — сушка; 2 — грохочение; 3 —измельчение; 4 — двухступенчатый предварительный подогрев; 5 —двухступенчатое восстановление (до 75%); 6 — брикетирование; 7 — охлаждение в шахте; 8— природный газ; 9 — пар; 10 - паровая конверсия природного газа; 11 — охлаждение; 12 — предварительный подогрев газа;13 —выходящие газы
Из мелкой фракции, получаемой при грохочении кусковой руды месторождения "Церро Боливар", на этой установке получали брикеты из губчатого железа со степенью металлизации ~70 %. Такая низкая степень металлизации была выбрана потому, что брикеты такого качества считали более подходящим сырьем для доменной плавки, чем материал со степенью металлизации > 90 %. Целью разработок было повышение эффективности доменных печей при плавке таких брикетов. Восстановление доизмельченной руды (фракции 2-0 мм) осуществляли после двухступенчатого нагрева восстановительным газом с большим содержанием водорода в двухступенчатом реакторе с кипящим слоем. Губчатое железо, имевшее температуру ~ 700 °С, брикетировали в горячем состоянии.
Восстановительный газ получали из природного методом паровой конверсии с большим избытком пара, который затем охлаждали для конденсации избыточной влаги и снова нагревали перед передачей в процесс до температуры ~850 °С.
Фирма "Эссо рисёрч + энджиниринг" разработала в начале 60-х годов многоступенчатый процесс с использованием кипящего слоя под названием "Фиор" (рис. 7.13), по которому мелкую руду (фракция 5—0,5 мм) восстанавливали водородом с получением порошка железа, и затем этот порошок подвергали горячему брикетированию.
Рис. 7.13. Схема промышленной установки, работающей по процессу "Фиор":
1 —подготовка (обогащение) руды: 2 — кислородная (воздухоразделительная} установка; 3 — кислород; 4 - природный газ или мазут; 5 — водяной пар; 6 — частичное окисление; 7 —реакторы с кипящим слоем; 8 — воздух; 9 — природный газ или мазут; 70 — котел-утилизатор; 11— скруббер для промывки газа и компрессор; 12 — печь;
73 — брикетирование
При восстановлении мелкой руды в трех последовательных реакторах (перед которыми был поставлен реактор для подсушивания руды) типичная проблема слипания частиц в кипящем слое была решена настолько, что на производственной установке в Матансасе (Венесуэла) был достигнут достаточно высокий коэффициент использования оборудования.
Восстановительный газ получали паровой конверсией с большим избытком пара, причем долю СО конвертировали в удаляемую CO2(обменной конверсией}, так что в цикл циркуляции восстановительного газа поступал почти чистый водород. Оборотный газ после его использования для восстановления промывали водой с целью конденсации влаги, образующейся при восстановлении, и вместе с только что полученным водородом нагревали в газоподогревателе.
Ряд неблагоприятных обстоятельств помешал довести этот процесс восстановления в кипящем слое до промышленного применения. Дальнейшие разработки в области восстановления руды в кипящем слое на основе природного газа весьма мало вероятны.
Восстановление в конвейерной печи
Эта схема не имела промышленного успеха, однако в историческом обзоре эту небольшую группу технологических процессов нужно упомянуть. Восстановитель (уголь) непосредственно включается в состав окатышей, при этом тщательно перемешивается с рудой, в результате создаются хорошие условия для процесса восстановления.
Тем не менее использование тех же реакционных аппаратов, которые применялись для производства сырых окатышей, в процессах прямого восстановления, очевидно, вызвало трудности. Оба способа, "Хит фаст" и "Дуайт-Ллойд-Макуэйн", разработанные в середине 50-х годов, не были доведены до стадии промышленного применения; к концу 60-х годов работы по ним были прекращены.
По способу "Хит фаст" (рис. 7.14), который разрабатывала фирма "Мидланд Росс", из мелкой руды вместе с тонкоизмельченным углем (или коксом) и бентонитом в барабанных окомкователях получали сырые окатыши. Эти окатыши подсушивали на решетке и затем обжигали в конвейерной печи при температуре от 150 до 1000 °С, а далее восстанавливали в двух зонах (температура первой зоны 1000-1150 °С, второй 1150-1250 °С), после чего охлаждали в шахте. Количество угля подбирали так, чтобы в слое на решетке создавались в достаточной мере восстановительные условия. Получение равномерного восстановительного потенциала, очевидно, было затруднительным.
В полупромышленной установке (при переработке до 200 тыс. т сырых окатышей в год) удалось достичь степени металлизации до 90 %. Работы над способом были прекращены, когда был получен заказ на установку меньшей производительности в Орегоне. Проект был изменен. Вместо установки "Хит фаст" фирма "Мидланд Росс" построила первую установку "Мидрекс", которая была пущена в эксплуатацию и успешно проработала около 15 лет.
Рис.7.14. Схема процесса "Хит фаст":
1-сушилка; 2-туннельная печь; 3- мелкая фракция; 4-решетка; 5-воздух; 6 — вход воздуха; 7 — выход воздуха; 8 — приспособление для выгрузки губчатого железа
Способ "Дуайт-Ллойд-Макуэйн" (рис. 7.15) также может быть отнесен к группе способов восстановления с плавлением. По этому способу руду и уголь (некоксующийся) вместе с добавками подвергают мокрому измельчению, затем фильтруют и окомковывают в чашевых окомкователях с получением сырых окатышей. Эти окатыши сушат на агломерационной машине, обжигают и предварительно восстанавливают. Окатыши, восстановленные на ~ 60 % (при температуре 900 °С), окончательно восстанавливают прямо в восстановительной электропечи и переплавляют с получением передельного чугуна.
Рис. 7.15. Схемапроцесса Дуайт-Ллойд-Мак-Уэйн:
1 — мелкий уголь; 2 — мелкая руда; 3 — добавки; 4 — возврат; 5 — измельчающее оборудование; 6 — насос; 7 —фильтры; 8 — чашевый окомкователь; 9 — сушка; 10 — зажигание; 11 —транспортер; 12 — агломашина Дуайт-Ллойд; 13 —весы; 14 — электропечь; 15 — эксгаустер; 16 — дымовая труба; 17 — выпуск передельного чугуна; 18 —скруббер для промывки газа; 19 — мокрый (плавающий) газгольдер; 20 - науглероживание
Что послужило причиной прекращения работ по этому способу — сравнительно высокий расход энергии или специфические технологические проблемы, — точно не известно.
С учетом того, что в долгосрочной перспективе возникнет необходимость применять мелкую руду и мелкий уголь (например, обогащенный уголь из отвалов) как восстановитель в производстве стали, целесообразно не забывать теоретические достижения и опыт, полученные при этом процессе, и учитывать их при обсуждении новых технологических альтернатив.
Роторные способы упоминаются здесь (хотя об их промышленном применении в настоящее время ничего не известно) потому, что в них последовательно реализуют принцип переработки неагломерированного сырья и принимают специальные меры по защите огнеупорной футеровки, а эта задача при восстановительной плавке имеет важное значение.
Разработка процесса "Доред" (рис. 7.16) была начата фирмой "Стора Копперберг" в 1960 г. в Домнарвете (Швеция) на основе процесса "Калдо".
Рис. 7.16. Схема процесса "Доред":
1 - руда (может быть подогрета) и кокс; 2 -кислород; 3- сгорание СО; 4 -отходящие газы; 5-реакционный слой; б - слой шлака; 7-слой передельного чугуна
В горизонтальную вращающуюся (с частотой до 30 мин-1) печь загружают железорудный концентрат, известь и мелкокусковой уголь или коксовую мелочь и вдувают кислород. В ходе процесса формируются три слоя (внизу — передельный чугун, в середине — шлак, вверху — восстановительный реакционный слой). Сгорание газов, выходящих из верхнего слоя, покрывает потребность в тепле на восстановление и плавление.
Процесс "Роторед" (рис. 7.17) разрабатывался Центром металлургических исследований в Риме (Италия) с 1971 г.
Рис. 7.17. Схема реактора "Роторед":
1 - фурмы для ввода добавок; 2 — восстановитель; 3 — оксид железа; 4 — центральная горелка
На стенку вертикальной вращающейся печи загружают руду, добавки и уголь (все эти материалы должны быть в мелкозернистой форме), причем частота вращения печи должна быть достаточно большой, чтобы материалы удерживались на стенке (под действием центробежной силы). При помощи центральной горелки подводится энергия до тех пор, пока не пойдет реакция восстановления; после этого достаточно подавать предварительно подогретый воздух, т.е. некоторое количество дополнительной энергии, чтобы поддерживать ход реакции. Футеровка печи защищена от жидких оксидов железа, так как жидкий чугун, имеющий более высокую плотность, собирается непосредственно у огнеупорной стенки.
Корпорация "Бритиш стил" (Великобритания) в 1968 г. начала разрабатывать процесс СИП (рис. 7.18). В слегка наклоненную вращающуюся печь вдувают мелкую руду, известняк и кусковой некоксующийся уголь и при помощи кислородотопливной горелки в печном пространстве поддерживают температуру — 2000 °С. Чугун, образующийся при быстро протекающем процессе восстановления и плавки, располагается непосредственно на футеровке печи, вращающейся с частотой до 200 мин-1, и стекает в копильник, куда поступают и отходящие газы.
Рис. 7.18. Схема реактора СИП (центробежного получения чугуна) :
1 —горелка; 2 — топливо; 3— кислород; 4 — шихта (У— уголь, Р — руда, И —известняк) ; 5 — подвод охлаждающей воды; 6 —отвод охлаждающей воды; 7 —буртик для недопущения выхода шлака; 8 —ось вращения ротора; 9 —огнеупорная футеровка; Ч—чугун; Ш—шлак; М—мазут
Шлак имеет сравнительно высокое содержание железа (10—25 %), что снижает выход годного. Кроме того, не решены проблемы стойкости футеровки, особенно на стороне выхода чугуна из печи.
Способы, основанные на применении электроэнергии
Способ "Элред" (рис. 7.19) разрабатывался шведскими фирмами "Стора Копперберг" и АСЭА при участии фирмы "Лурги" (ФРГ) с 1971 г. В циркулирующий кипящий слой (/) вводят мелкую руду (≤ 0,1 мм} и мелкий уголь (≤ 0,2 мм). При температуре 900—1000 °С уголь газифицируется воздухом, а мелкая руда восстанавливается на ~ 70 %. Избыток угля в циркулирующем кипящем слое предотвращает спекание металлизованных частиц руды. Работа системы регулируется по времени пребывания и температуры в реакторе.
Рис. 7.19. Схема процесса "Элред":
1 —уголь; 2— воздух; 3 — рудный концентрат; 4 - псевдоожижающий газ (создающий кипящий слой); 5 —предварительно восстановленная железная руда; 6 - отходящие газы; 7— известь; 8—пустотелый электрод; 9 — шлак; 10 — передельный чугун
Предварительно восстановленный материал вводится вместе со шлакообразующими при температуре 600-700 °С через пустотелый электрод в рудовосстановительную электропечь постоянного тока (//). В плазме электрической дуги, возникающей между электродом (катодом) и расплавом (анодом), завершается восстановление и плавление материала с получением чугуна, содержащего 3-4 % углерода. В этом процессе дуга полностью закрыта шлаком.
Удаление серы и фосфора обеспечивается при внепечной обработке. Отходящие газы из кипящего слоя и из электропечи используют для сушки и предварительного подогрева шихтовых материалов и для выработки электроэнергии, которой покрывается вся потребность электропечи. Кроме того, в сеть отдается до 400 кВт•ч на 1 т передельного чугуна.
Способ "Инред" (рис. 7.20) фирма "Болиден" (Швеция) начала разрабатывать в 1972 г. В плавильный циклон вдувают в потоке кислорода рудный концентрат, мелкий уголь и известняк. В закрученном потоке уголь газифицируется, а руда восстанавливается до FeO и расплавляется.
Рис.7.20. Схема процесса "Инред":
1 - мелкая руда; 2-известняк; 3-уголь; 4-кислород; 5-возврат; б- электропечь; 7 — передельный чугун; 8 — шлак; 9 — десульфурация передельного чугуна в ковше; 10 —сброс давления газа; 11 - на газоочистку
Расход энергии на эти реакции покрывается частичным сжиганием СО, полученного при газификации угля, и отходящих газов из восстановительной печи. Расплавленный монооксид железа опускается через вспененный шлак в рудовосстановительную печь, расположенную непосредственно под плавильным циклоном (электрошлаковую печь сопротивления) , и там восстанавливается остатком углерода частично газифицированного угля. Отходящие газы, имеющие температуру ~ 1900 °С, охлаждаются в котле-утилизаторе. Выработанная при этом электроэнергия удовлетворяет потребность восстановительной печи.
Фирма СКФ (Швеция) с 1972 г. разрабатывает способ "Плазмасмелт" (плазменная плавка) (рис. 7.21). Между вольфрамовым катодом и водоохлаждающим медным анодом создается непрерывно горящая дуга, в которой газ (а также, например, и уголь) нагревается, диссоциирует (при температуре > 2000 °С) и ионизируется (> 3500 °С). Поток атомарного или ионизированного газа может иметь высокий энергетический потенциал и отдавать свою энергию с весьма высоким коэффициентом теплоотдачи, что способствует быстрому восстановлению и расплавлению железной руды.
По способу "Плазмасмелт" предварительно восстановленная мелкая руда вместе с угольным порошком и шлаковыми добавками пропускается в потоке (рециркулирующего) технологического газа через плазменную горелку (плазматрон), расположенную на горизонте воздушных фурм небольшой доменной печи, заполненной коксом. Руда здесь окончательно восстанавливается, плавитсн и просачивается вниз в горн, откуда выпускают чугун и шлак, как при нормальной работе доменной печи. В зоне окончательного восстановления устанавливается температура 1700—2000 °С, тогда как в самом плазматроне температура достигает 3000-5000 °С.
Рис. 7.21. Схема процесса "Плазма-смелт":
1 — кокс; 2— регулирование давления; 3 — отходящий газ на осушку концентрата;
4 - подсушенный концентрат; 5 — предварительное восстановление; 6 — известь;
7 - металлизованноежелезо; 8 — плазматрон; 9 —мелкий уголь; 70 — передельный чугун; 11—шлак; 12 — окончательное восстановление и плавка
Газ проходит через коксовый слой снизу вверх, снова полностью превращается в смесь СО + Н2 и покидает колошник с температурой 1000—1200 °С. Слой (столб) кокса в шахтной печи принимает лишь незначительное участие в реакциях и используется преимущественно как реакционное пространство, проницаемое для газа, передельного чугуна и шлака. Этот слой сглаживает небольшие колебания в поступлении углерода через плазматрон, обеспечивает постоянное содержание углерода в чугуне и защищает футеровку печи.
Колошниковый газ (Н2 + СО) охлаждается до ~800 °С и используется в двухступенчатом процессе предварительного восстановления в кипящем слое, обеспечивая восстановление мелкой руды до ~ 60 %. Часть потока охлаждается, компримируется и используется как транспортирующий газ для предварительно восстановленной мелкой руды и в качестве технологического газа в плазматроне.
Естественно попытаться применить плазменную технологию также и для производства губчатого железа. Фирма СКФ предложила технологический процесс "Плазмаред" (плазменное восстановление) (рис. 7.22).
Рис.7.22. Схема процесса "Плазмаред":
1—железорудные окатыши; 2—отходящий газ; 3 — воздух; 4 —восстановительная печь; 5 — губчатое железо; б —десульфурация; 7 — регенерация газа; 8 — топливо; 9— генератор плазмы (плазматрон)
Углеродоносители (уголь, мазут или природный газ) превращаются в плазматроне в восстановительный газ, который охлаждается до ~ 900 °С и подвергается десульфурации в слое кускового доломита, а далее при температуре ~850 °С подводится в восстановительную шахтную печь, в которой восстанавливаются кусковые оксиды железа. Колошниковый газ из восстановительной печи возвращается в плазматрон.
Одна из проблем плазменной технологии при современном уровне знаний заключается в недостаточном сроке службы плазматрона.
Способы, основанные на газификации угля в плавильном газификаторе — конвертере (кипящий слой)
В этой группе способов последовательно проводится принцип применения угля как единственного энергоносителя для восстановления железной руды и для ее расплавления. По основным технологическим этапам процессов КР (восстановление углем), "Крупп—Коин" и "Клёкнер" — КС успешно накоплен опыт эксплуатации в промышленных масштабах.
Разработка процесса КР (рис. 7.23) была начата в 1976 г. фирмой "Корф шталь", а в 1979 г. к ней подключилась фирма ФЁСТ. Этот способ является дальнейшим логическим усовершенствованием процессов восстановления газом с получением продукта — губчатого железа, потому что плавка холодного губчатого железа в дуговой печи связана со все возрастающими издержками на электроэнергию. По способу КР можно перерабатывать кусковую руду, агломерат и (или) окисленные окатыши на передельный чугун с применением угля самых разнообразных марок; таким образом, его можно считать альтернативой для доменной плавки.
Рис. 7.23. Схема процесса КР (восстановления углем)
1 — руда; 2 —циклон; 3— отходящий газ; 4 — избыточный газ; 5 – скруббер угольного газа; 6— передельный чугун и шлак;7 – горячее губчатое железо; 8 – уголь; I — восстановительная шахта; II – плавильный газификатор
Металлургический процесс протекает в двух расположенных один над другим реакторах: восстановительной шахтной печи (вверху) и плавильном газификаторе (внизу). Нижний реактор выполняет двойную функцию: плавит губчатое железо и обеспечивает газификацию угля. Уголь крупностью 50-0 мм без какой-либо предварительной подготовки поступает по труботечкам в плавильный газификатор, вступает в головной части газификатора в контакт с газом, нагретым до температуры ~ 1200 °С, мгновенно высушивается, освобождается от газов, растрескивается и превращается в кокс. В цилиндрической части реактора кокс газифицируется кислородом, вдуваемым радиально. При этом создается стационарный кипящий слой, имеющий температуру ~ 1600 °С. Образующийся так называемый угольный газ содержит примерно 73 % СО, 22 % Н2 и 1 % С02 (остальное - N и СН4).
Губчатое железо, поступающее с температурой 850—900 °С из восстановительной печи, затормаживается в своем падении через кипящий слой, прогревается и в районе расположения кислородных фурм расплавляется. Передельный чугун и шлак выпускают через леточное отверстие.
В восстановительную шахтную печь поступает предварительно очищенный в циклоне восстановительный газ, температура которого устанавливается на уровне ~900 С добавкой холодного угольного газа. Как и в шахтной печи прямого восстановления, шихта восстанавливается в противотоке. Из шахтной печи горячее губчатое железо выгружается шнеками непосредственно в плавильный газификатор. В шахтной печи нет никаких вставных элементов. В отличие от традиционных процессов прямого восстановления в шахту при процессе КР наряду с железной рудой загружают также и добавки.
Горячий угольный газ после плавильного газификатора подвергается грубой очистке в циклонах. Часть его охлаждается добавкой воды и используется для охлаждения восстановительного газа, а другая часть может быть использована (вне процесса) как избыточный газ, Колошниковый газ из восстановительной печи тоже еще обладает достаточно высоким энергосодержанием и может быть использован для различных целей.
Способы, заменяющие доменный процесс (стационарный слой)
Другие пути производства передельного чугуна с возможно более низким расходом первичной энергии имеют целью прямую конкуренцию с доменным процессом. Ставится задачей получение полупродукта типа передельного чугуна, который был бы равноценен передельному чугуну из доменной печи. Приобрели известность два таких способа: плавка губчатого железа фирмы "Сумитомо" и восстановительная плавка фирмы "Кавасаки".
Фирма "Сумитомо метал индастриз" разработала процесс получения передельного чугуна под названием "Сумитомо драй мелтинг" (рис. 7.24). Функция доменной печи — восстановление железной руды и плавка восстановленного железа при одновременном удалении примесей реализуется в двух раздельных печах. В числе преимуществ такой схемы названы возможность применения кокса низкого качества и получение колошникового газа с высокой теплотой сгорания при использовании угольной пыли (пылеугольного топлива), вдуваемой вместе с кислородом.
Рис. 7.24. Схема плавки губчатого железа фирмы "Сумитомо":
1 —кокс;2 — губчатое железо; 3 — шахтная печь предварительного восстановлена; 4 — руда; 5—колошниковый газ; 6 — восстановительный газ; 7 —кислород, мелкий уголь, пар; 8 — жидкий металл, шлак; 9 —печь для окончательного восстановления и плавки
В восстановительной шахтной печи от железной руды (кусковой) отнимается кислород восстановительным газом, подводимым из плавильного газификатора. Затем губчатое железо передается непосредственно в плавильный газификатор и там расплавляется. При этом вырабатывается восстановительный газ. В качестве топлива в плавильный газификатор загружается сверху кокс. Кислород, угольная пыль и пар (необходимый для регулирования температуры) вдуваются через сопла в нижней части печи. Расплавленный передельный чугун выпускается из нижней части печи, как из горна доменной печи.
Восстановительный газ получается в ходе реакции между кислородом, угольной пылью и коксом в плавильном газификаторе. Он содержит до 70% СО и до 25 % Н2 и имеет теплоту сгорания 6300-8000 кДж/м3, т.е. примерно вдвое более высокую, чем у обычного доменного газа. Этот газ может быть использован для выработки электроэнергии, привода кислородных (воздухоразделительных) установок, в нагревательных колодцах и для других потребителей в сталеплавильном и прокатном цехах.
Благодаря применению пыли некоксующихся углей можно сэкономить ~ 75 % коксующегося угля. Это обусловливает значительное снижение капиталовложений в коксохимическое производство.
По осторожным оценкам можно принять, что издержки производства на 1 т передельного чугуна по новому процессу "Сумитомо драй мелтинг" будут на ~15 % меньшими, чем при традиционном доменном процессе.
Процесс восстановительной плавки фирмы "Кавасаки" (рис. 7.25) представляет собой разработку начала 80-х годов; он позволяет получать передельный чугун или ферросплавы из мелких руд. Здесь также расчленяют обычный доменный процесс на две отдельные рабочие операции — предварительное восстановление и восстановительную плавку. Предварительно восстановленная руда плавится на газификаторе, разделяется на металл и шлак, который полностью восстанавливается.
Рис. 7.25. Схема восстановительной плавки фирмы "Кавасаки":
А -печьпредварительного восстановления; Б —печьдля окончательного восстановления и плавки; 1 — кокс низкого качества; 2— отходящий газ; 3 — мелкая руда; 4 - металлизованная мелкая руда; 5 - горячий воздух; 6 — кислород, мелкий уголь; 7 – шлак и жидкий металл
В числе преимуществ процесса названо снижение издержек на производство стали на ~ 15 %. При выплавке ферросплавов (феррохрома или ферромарганца} благодаря отказу от этапа плавки в дуговой печи можно ожидать экономии в расходе энергии почти на 50 %. При этом в печь предварительного восстановления загружают мелкую руду; монооксид углерода (СО), необходимый для восстановления, поступает из печи восстановительной плавки с высокой температурой. Степень предварительного восстановления (металлизации) должна составлять 60-70 %.
При выплавке ферросплавов к восстановительной среде добавляют еще и углеводороды, например метан. Сообщалось, что хромовая руда предварительно восстанавливается на 30-50 %.
В обоих случаях вырабатывается избыточный газ — в основном водород и монооксид углерода, который может быть использован для производства химикатов или в качестве топлива для выработки энергии в самом цехе.
7.3.1 Принцип работы установки «Мидрекс»
На рис.7.26 изображена принципиальная схема процесса «Мидрекс» для прямого восстановления железа из руд.
Рис.7.26. Принципиальная технологическая схема газовых потоков.
1 – промежуточный бункер; 2 – шахта печи; 3 – центральная загрузочная труба; 4 – загрузочные трубы; 5 – восстановительный газ; 6 – колошниковый газ; 7 – скруббер; 8 – технологический газ; 9 – топливный газ; 10 – компрессор; 11 – холодильник; 12 – природный газ;
13 – смешанный газ; 14 – рекуператор; 15 – реформер; 16 – водяной пар; 17 – воздух;
18 – холодильник; 19 – конвертированный газ; 20 – дымовой газ; 21 – дымосос; 22 – труба; 23 – инертный газ; 24 – питатели постоянного действия; 25 – охлаждающий газ; 26 – конвертированный газ в зону охлаждения; 27 – охлаждающий газ в топливный; 28 – технологический газ в охлаждающий; 29 – маятниковое разгрузочное устройство; 30 – газодинамический затвор; 31 – отсечной шибер; 32 – термозонды; 33 – сероочистка; 34 – подача меловой суспензии.
По системе транспорта сырья окисленные окатыши подаются в промежуточный бункер (поз. 1, рис. 7.26) шахтной печи (2), откуда они самотеком через загрузочную трубу (3) и двенадцать распределительных труб (4) поступают в зону восстановления шахтной печи, где и восстанавливаются газом по химическим реакциям:
Fe2O3+3H2=2Fe+3H2O – 880 кДж/т Fe (210000 ккал/т Fe)
Fe2O3+3CO=2Fe+3CO2+250 кДж/т Fe (60000 ккал/т Fe)
Восстановительный газ (5) выходит из зоны восстановления шахты печи, окисленным до СО2, в составе колошникового газа (6) очищается от пыли и охлаждается в скруббере (7). После охлаждения, колошниковый газ разделяется на два потока: технологический (8) и топливный (9) газы.
Технологический газ, содержащий газ-окислитель (СО2) сжимается в двух ступенях компрессоров (10) до (1,2…1,5) бар, т.е. (120…150) кПа, а затем подается в холодильник технологического газа (11), где насыщают его необходимым количеством водяных паров. Технологический газ смешивают с подогретым очищенным газом (13), смесь подогревают в рекуператоре (14) и подают в реакционные трубы реформера (15). При технологической необходимости, используют процесс пароводяной конверсии природного газа, т.е. в технологический газ подают окислитель – водяной пар (16).
Конверсию природного газа окислителями технологического газа проводят на никелевом катализаторе в 288 реакционных трубах при температуре (900..920)0С.
Протекают, ранее указанные, химические реакции с участием двух видов окислителей, содержащихся в конвертируемом газе:
СН4+Н2О=СО+3Н2 – 8650 кДж/м3 СН4 (2070 ккал/ м3 СН4);
СН4+СО2=2СО+2Н2 – 10500 кДж/м3 СН4 (2520 ккал/ м3 СН4).
Тепло для нагрева и конверсии газовой смеси выделяется в межтрубном пространстве реформера за счет сжигания топливной части колошникового газа (9) в 120 главных и 36 вспомогательных горелках. Воздух для сгорания топливного газа подается главной (17) и вспомогательной воздуходувками.
Часть конвертированного (19) газа проходит через холодильник (18), в котором газ охлаждается водой до температуры (30…45)0С. Охлажденный газ используют для регулирования температуры всего потока конвертированного газа (26).
Конвертированный природный газ (после автоматической коррекции по содержанию СН4), с заданной температурой, поступает в зону восстановления шахтной печи через 72 фурменных отверстия. Дымовые газы (20) после реформера используют в рекуператоре для подогрева воздуха, подаваемого на главные горелки, а также для подогрева смешанного и природного газов, а затем выбрасывают дымососом (21) в дымовую трубу (22). Около 10% дымовых газов содержащих СО2 используют для получения инертного газа (23), необходимого для заполнения бункеров (хранилищ) пирофорных (не пассированных) металлизованных окатышей.
Металлизованные окатыши из зоны восстановления через питатели постоянного действия – ППД (24), поступают в зону охлаждения печи, где их температура снижается охлаждающим газом (25).
Для регулирования массовой доли углерода в окатышах и распределения температуры по высоте шахтной печи, в рабочем пространстве печи организованны перетоки холодного конвертированного газа (26) в охлаждающий газ (25), а горячего восстановительного газа из зоны восстановления – в зону охлаждения, со сбросом части охлаждающего газа в топливный газ (27) и, наконец, подача технологического и природного газов охлаждения, а природного газа – в промежуточную зону для участия в процессе металлизации (восстановления).
Выгрузка металлизованных окатышей из печи производится маятниковым разгрузочным устройством – МРУ (29), расположенным в нижней части печи (МРУ может выполнять функцию спеколомателя, устраняя аварийные ситуации на печи).
Для предотвращения утечки горючих газов и пыли из шахтной печи установлены верхний и нижний газодинамические затворы – ВГДЗ и НДЗ (30), оснащенные отсечными шиберами (31).
Металлизованные окатыши распределяют в три бункера хранения продукта перед электросталеплавильным цехом комбината и в три бункера промежуточного хранения перед отгрузкой потребителям (на установке отгрузки окатышей установлено еще два бункера).
«Реметы» – металлизованные окатыши имеющие низкую степень металлизации или содержащие углерод менее требуемых технологической инструкцией (соответственно, менее 90% и 1,2%), транспортируются от шахтной печи на закрытый склад реметов или на открытый склад окисленных окатышей для повторный металлизации (т.е. реметы дозировано направляются в поток шихты, загружаемой в установку металлизации).
Для производства пассированных (непирофорных) металлизованных окатышей, в промежуточном бункере (1) перед загрузкой шихты в печь металлизации предусмотрена обработка окисленных окатышей сырьевым шламом цементного завода или меловой суспензией (34).
Мелочь металлизованныых окатышей подвергают брикетированию (смешивание со связующим веществом – мелассой, сахарной патокой и прессование в таблетки, форма и размер которых напоминают конфеты – «подушечки»). При пресовании металлизованной мелочи сдавлииваются поры и каналы поверхности металлической «губки», что значительно снижает пирофорность металлизованного продукта. Брикеты, как и металлизованные окатыши подают в сталеплавильный цех комбината.
Обобщенная схема процесса «Мидрекс» изображена на рис. 7.27
Рис. 7.27. Схема варианта процесса «Мидрекс» с использованием окисленных окатышей (или кусковой руды): 1- окисленные окатыши; 2 – скруббер; 3 – компрессор; 4 – губчатое железо; 5 – риформер; 6 – рекуператор; 7 – природный газ; 8 – дымовая труба; 9 – отходящий газ
Стилизованная схема процесса «Мидрекс», более удобная для изучения описанной технологии, без разъяснений показана на рис.7.28.
Рис.7.28. Технологическая схема процесса «Мидрекс»
1 – воздуходувка; 2 – теплообменник; 3 – смеситель газов; 4 – конвертер; 5 – компрессор; 6, 7 – скруббер для колошникового газа; 8 – шахтная печь; 9 – вибрационный грохот; 10 – брикетировочный пресс
7.3.2. Принцип работы установки «Хил»
Одним из вариантом восстановления железа в толстом слое является процесс HyL,прошедший три технологические модификации.
Процесс HyL–I (XuЛ-I) (рис. 7.29) – восстановление руды производится в периодически действующих ретортах (рис.29) со стационарным слоем шихты. Ёмкость реторты
(100…150)т.
Рис.7.29. Реторта для металлизации по способу ХиЛ: 1-гидравлический спольз; 2-тележка; 3-привод; 4-кожух; 5-крышка; 6-загрузочная горловина; 7-площадка для обслуживания; 8-резец с рычагом для удаления губки; 9-футеровка; 10-механизм управления откидным днищем; 11-откидное днище; 12-разгрузочный желоб
.
Восстановление в неподвижном слое исключает такие недостатки процесса с движущимся по высоте печи материалом, как канальный ход (неравномерность газового потока по сечению шахты печи), образование мелочи при истирании, вынос пыли, разрушение слоя локальное спекание шихты.
На рис.7.29 показана технологическая схема установки, действующей на одном из металлургических предприятий Мексики.
Губчатое железо производится в четырёх ретортах восстановления исходного продукта (поз. 7). На рис.7.29 слева размещены агрегаты для конверсии природного газа, а справа – установки для получения железа. Мощность установок доведена до 100 т/сутки губчатого железа.
После десульфурации в аппарате (1) природный газ подспользова паровой конверсии в конвертере (2), который представляет собой печь с металлическими трубами, заполненными керамикой с добавкой в качестве катализатора окиси никеля [NiO].
После конверсии в газе – восстановителе содержится 14%CO, 58%H2, 8%H2O, (4…5)%H2O и 15% неразложеного CH4.
Горячий газ осушают в парогенераторе (3) и он проходит через Котёл-утилизатор (4). В сухом газе возрастает количество восстановительных составляющих: H2 – до 73%, а CO- до 16%. Установка имеет четыре реторты (7) диаметром 5,25м. и высотой 15м. В каждой реторте последовательно проводятся все необходимые технологические операции процесса металлизации руды (окатышей): предварительное восстановление, окончательное восстановление, охлаждение и науглерожевание продукта. Общая длительность, технологических циклов – 9 часов. Простои установки при выполнении горящих ремонтов реторт, их загрузки и разгрузки – 1,5 часа на один общий цикл, что обеспечивает производительность всей установки на уровне (9,5…14) т/час металлизованного продукта.
Рис.7.30. Реторта для металлизации по способу ХиЛ:
1-гидравлический спольз; 2-тележка; 3-привод; 4-кожух; 5-крышка; 6-загрузочная горловина; 7-площадка для обслуживания; 8-резец с рычагом для удаления губки;
9-футеровка; 10-механизм управления откидным днищем; 11-откидное днище;
12-разгрузочный желоб.
Реторты переставляются из одной рабочей позиции в другую, что обеспечивает циклический характер эксплуатации установки. Загрузка реторт материалом и подача газа выполняется сверху. Для выгрузки готовой «губки» используется резец и специальные разгрузочные скребки. Губчатое железо поступает в желоб и в бункер (11), а затем по конвейеру – в сталеплавильный цех.
Степень металлизации (75…92)%, на 1т. Готового продукта расходуется 380м3 природного газа и, около, 36 МДж электроэнергии. Содержание углерода в металлизованном продукте регулируется в пределах (1…2,7)%. Кроме периодичности и низкой степени металлизации недостатком ХиЛ-I является необходимость охлаждения конвентированого газа для удоления водяного пара, спользованного при конверсии, а затем – повторного нагрева газа перед подачей в реторты (7). Низко производительный процесс отличается повышенным расходом электрической и других видов энергии и поэтому не получил широкого промышленного распространения.
Устранение недостатков процесса HyL-I, в значительной мере, было достигнуто в процессе HyL-III.
Рис. 7.31. Схема процесса ХиЛ-I:
1 – кусковая руда; 2 – рудная мелочь на агломерацию; 3 – сортированная кусковая руда; 4 – природный газ; 5 – очистка природного газа от серы; 6 – газовый риформер; 7 – паровой барабан; 8 – питательная вода котла; 9 водяной пар; 10 – воздушный охладитель и водоотделитель; 11 – градирня; 12 – реторты (I - IV); 13 – колошниковый газ; 14 – водоотделитель; 15 – подогреватель; 16 – кусковая руда; 17 – губчатое железо в сталеплавильный цех; 18 – брикетирование мелочи губчатого железа; 19 – немагнитная фракция
7.4. Перспективы развития П.В.
Метод прямого восстановления железа в наши дни по принципу остался без изменения – специально подготовленная, то есть обогащенная, руда, - концентрат, где содержится основной окисел железа восстанавливается в шахтной печи с помощью твердого топлива, как это было в древности, или для этой цели используется конвертированный газ - природный метан, но преобразованный в смесь водорода и угарного газа (СО).
Как установлено в настоящее время, можно восстанавливать концентраты руды, которые еще не превращены в окатыши. Более того, оказалось, что концентрат восстанавливается даже с большей скоростью, чем изготовленные из него окатыши. Однако на пути к реализации этого процесса стоят трудности чисто технологического порядка.
Еще одним, и, конечно, наиболее интересным способом восстановления железа, является возможность – использовать чистый водород. Сам процесс восстановления пойдет достаточно быстро, более того, при этом не возникает лишних примесей: продукт восстановления – железо и вода. Однако получение и хранение водорода сопряжено со множеством чисто технических и экономических трудностей. Поэтому чистый водород пока что используют лишь для получения металлических порошков.
Как известно, черная металлургия после электроэнергетики прочно занимает второе место по расходу топливных ресурсов. И подобно ей все увеличивает свои аппетиты. Если прибавить к этому изрядную долю электроэнергии, потребляемой многочисленными комбинатами металлургической промышленности — а она стремительно растет,— становится ясно, сколь необходимо было бы найти хотя бы для специальной металлургии новые источники энергии. Так родилась идея радиационного переплава стали. Радиационные печи интересны, конечно, и тем, что их можно питать энергией самого разнообразного происхождения, лишь бы она была лучистой.
Гораздо приятнее вспомнить день рождения "мирного атома". Он датируется абсолютно точно — это пуск первой в мире атомной электростанции в городе Обнинске 26 июня 1954 года.
С тех пор освобожденная энергия атома хорошо послужила человечеству. По подсчетам некоторых специалистов, к концу века доля энергии, вырабатываемой атомными электростанциями мира, увеличится до 30—40 процентов. В разных странах строится сейчас около двухсот АЭС, причем не-прерывно улучшается технология, рождаются новые, более экономичные конструкции, наконец, с появлением так называемых бридерных реакторов -размножителей резко увеличились потенциальные запасы ядерного горючего.
Прежде чем посмотреть, как можно использовать атомную энергию в металлургии, вспомним, что собой представляет современный ядерный реактор классического типа, использующий реакцию деления ядер тяжелого металла - урана.
Процесс деления происходит в так называемой активной зоне. Там и выделяется энергия. Тепло отводится из активной зоны специальным теплоносителем - вода, тяжелая вода, жидкие металлы. Затем эту энергию утилизируют. Схема устоявшаяся, традиционная: теплообменник - турбина - генератор. И помчался по проводам электрический ток, полученный столь необычным способом. "Атомное электричество", по сути дела, работает и на металлургию, так как входит составной частью в электросистемы и, следовательно, участвует в любых устройствах электрометаллургии.
Однако под атомной металлургией мы понимаем не только использование тепла ядерного реактора. Будущий атомно-металлургический комплекс мыслится как нечто передовое во всех своих звеньях.
Современная технология получения черных металлов требует достаточно высоких температур: выплавка чугуна - 1600 градусов, нагрев – 1400 градусов, термическая обработка проката — 1250 градусов.
Прямо воспользоваться атомными реакторами пока что нельзя, так как подобная «жара» наблюдается лишь внутри активной зоны.
Перевод тепла в зону, где сравнительно спокойно, также требует особых условий. Необходимы металлические теплообменники, сооруженные из жаропрочных коррозионных сплавов. Ведь им надо выдержать одновременно воздействие сильных механических нагрузок, радиации и высокой температуры.
Таким образом, очевидно, что применение атомной энергии потребует принципиального изменения всей технологии черной металлургии.
Конечно, есть второй путь — преобразовать атомную энергию в электрическую, но всё-таки генеральный путь развития черной металлургии на базе атомной энергии иной. Надо коренным образом изменить технологию, что прежде всего означает переход к прямому восстановлению железа.
Сейчас имеются три принципиально отличающихся друг от друга вида технологических процессов такого рода с участием атомной энергии.
Первый — высокотемпературное восстановление. Процесс требует 1600 градусов. Поскольку атомные реакторы такой температуры дать не могут, главным агрегатом служит струйно-плазменный реактор, использующий для генерации плазмы - ядерную энергию.
Восстановительный газ — водород, смешанный или без посторонних примесей, расплавляет железо и его сплавы, восстанавливает, и в виде дождя жидких капель металл попадает в плавильную печь, где идут операции легирования.
Существует схема среднетемпературного восстановления, когда процесс протекает при температуре 900 градусов. Восстановитель — водород или в чистом виде, или с примесью окиси углерода. Железо, естественно, находится в твердом состоянии, образуя при восстановлении своеобразную губку.
Метод позволяет полностью без промежуточных звеньев использовать атомно-энергетическую установку. Большую часть газа-восстановителя нагревают в теплообменнике атомного реактора. Правда, там температура невелика. Но это не беда. К такому "холодному" газу можно подмешать более горячий, нагретый за счет электроэнергии ядерного реактора. Получается смесь, вполне пригодная для технологии.
Наконец, при низкотемпературном восстановлении тепло поставляется атомным реактором. Можно считать, что тут в чистом виде используется ядерная энергия.
Таковы три вида технологических процессов, которые, по мнению многих специалистов, имеют право на существование.
Конечным продуктом везде являются железо, вода и углекислый газ, причем воду можно снова использовать для получения водорода и кислорода. Таким образом, появляются реальные возможности осуществить замкнутый цикл восстановления железа, создать безотходное производство.
Металлургию будущего не без основания часто называют водородной. Использование водорода для нужд черной металлургии — реальность недалекого будущего.
Сейчас водород получают двумя испытанными методами — гидролизом воды и ее электролитическим разложением, проще говоря, электролизом. Существует, правда, химическое разложение, более выгодное, но оно не столь распространено, на что имеется ряд чисто технических причин. Поиск новых способов "продолжается, ибо важность проблемы несомненна.
В целом ряде лабораторий страны изучают взаимодействие молекул воды и так называемых энергоаккумулирующих веществ - сплавов, в состав которых входят алюминий, кальций и кремний. Опять-таки происходит разложение молекул воды, отбирается кислород и, выделяется водород.
Предварительные расчеты и первые эксперименты показали: можно получать водород с такой низкой себестоимостью, что "водородная металлургия" обретет, наконец, надежную экономическую основу. А если учесть еще полную экологическую безопасность водородных методик, то сомнений в том, что именно они и представляют собой будущее нашей старинной профессии, ни у кого не возникает.
При всей внешней таинственности наименования энергоаккумулирующие вещества - ЭАВ - встречаются достаточно часто. Их, скажем, легко получить из золы, запасы которой в нашей стране поистине неисчерпаемы.
Как видите, мы снова выяснили, что необходимо ввести в металлургию прямое водородное восстановление железа, теперь мы пришли к тому же, исходя их энергетических позиций. Кроме того, водородное производство безотходное. Значит, атомная металлургия сулит выигрыш по всем трем направлениям, на которых основано современное экономичное производство - минимум топлива и сырья, максимум забот об окружающей природе.
Разумеется, водородное восстановление - только начало технологического цикла металлургии. Но и остальные звенья - будь то конвертеры, электропечи, заводы-автоматы, аппараты малооперационной технологии - требуют хорошего исходного сырья. Им будет восстановленное водородом железо, то есть побочный продукт ядерных реакторов. Когда речь идет о научно-техническом прогрессе, нельзя ограничиваться технологическими схемами - сами по себе они ничего не решают. Необходимы новые формы содружества науки, техники и производства. Без них новшество, интереснейшие проекты, блестящие разработки ученых застрянут в лабораториях или предстанут в натуре лишь в виде небольших опытных установок, а производство, промышленность по-прежнему будет ориентироваться на "дедовскую" технологию.
Тема № 8: “ Сталеплавильное производство. Подготовка шихты.”
Дата добавления: 2018-04-05; просмотров: 1928; Мы поможем в написании вашей работы! |
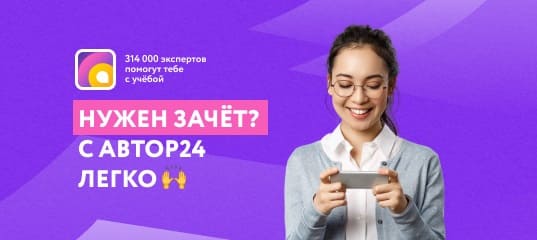
Мы поможем в написании ваших работ!