Химико-термическая обработка (ХТО) стали
ХТО заключается в диффузионном насыщении поверхностного слоя стали при повышенной температуре различными элементами: углеродом (цементация), азотом (азотирование), хромом (хромирование), алюминием (алитирование), бором (борирование).
ХТО используют для повышения износостойкости стали, повышения ее выносливости, а также для придания поверхности особых физических свойств – коррозионной стойкости, жаростойкости и др.
Цементации подвергают детали (шестерни, пальцы, шейки валов и осей), изготовленные из малоуглеродистой стали (менее 0,3% С). После цементации на поверхности содержание углерода составляет 0,8-1,0%. Цементацию проводят при температуре 930-950 оС и выдержке 8-15ч. Глубина цементированного слоя составляет 0,5-1,5мм. В микроструктуре цементированного слоя наблюдаются следующие зоны: (от поверхности в глубину) перлит + цементит вторичный, перлит, перлит + феррит. После цементации для повышения твердости и износостойкости поверхностного слоя стали производят термообработку, которая включает:
а) нормализацию (нагрев 880-920 оС), способствующую измельчению зерна сердцевины и устранению цементитной сетки на поверхности;
б) закалку с критической скоростью (нагрев 750-760 оС);
в) отпуск при 160-180 оС для снятия внутренних напряжений.
Микроструктура поверхностной зоны цементированной стали после термообработки мартенсит + вторичный цементит либо мартенсит, твердость HRС 58-62. Образование мартенсита, имеющего большой удельный объем, способствует возникновению на поверхности остаточных сжимающих напряжений, повышающих выносливость стали.
|
|
Азотированию подвергают шестерни, шпиндели станков, пресс-формы, другие изделия для повышения износостойкости, выносливости, коррозийной и эрозионной стойкости поверхности. Азотируют сталь при температуре 520…600оС, продолжительность процесса 30-90ч. Для обеспечения высокой твердости поверхности HV 1000 и сохранения ее при нагреве до 500…600оС азотируемые детали изготавливают из легированной стали марок 38Х2МЮА, 35ХМА, 38ХЗФЮА. Азотированный слой на этих сталях содержит стойкие нитриды легирующих элементов ALN, Cr2N, MoN и др. Нитриды, обладающие повышенным удельным объемом, способствуют повышению выносливости стали. Перед азотированием стали подвергают улучшению (закалке с высоким отпуском) для повышения прочности сердцевины.
Хромированию подвергают как малоуглеродистые, так и средне- и высокоуглеродистые стали. Хромирование обеспечивает повышение коррозионной и жаростойкости стали, а для стали, с содержанием углерода более 0,3% С также является эффективным способом повышения износостойкости и выносливости стали. Температура процесса хромирования 1050…1150оС, продолжительность 5-10ч. В результате хромирования железа или малоуглеродистой стали, диффузионное покрытие имеет глубину 0,05…0,15мм, твердость 250…300 и представляет собой твердый раствор хрома в железе (до30…60% Cr). Такое покрытие весьма пластично, обладает коррозийной стойкостью в пресной и морской воде, влажном воздухе, растворах азотной кислоты, обладает жаростойкостью (в воздухе при нагреве до 800оС, в сероводороде и сернистых газах – до 500оС). Хромированное покрытие на средне- и высокоуглеродистой стали имеет глубину до 0,01…0,03мм, содержит карбиды (Cr, Fe) 23С6, (Cr, Fe) 7С3, твердость его HV 1350. Образование карбидов обеспечивается диффузией углерода из сердцевины стали. При этом на границе с основой образуется обезуглероженная зона протяженностью ~0,01мм. На участке между нею и карбидной зоной содержание углерода повышено, структура троосто-сорбит (смесь карбидов и феррита). Карбидное покрытие стойко в расплавах цинка, олова, свинца и алюминия.
|
|
Хромированию подвергают калибры, матрицы и пуансоны для холодной штамповки, плунжерные пары, клапаны, сопловые устройства, детали топливной аппаратуры.
Борирование стали применяют для повышения ее абразивной износостойкости и теплостойкости.
|
|
При борировании углеродистой стали, на поверхности ее образуются бориды железа Fe2B (~9% В) и FeB (~16% В). Твердость борированной стали составляет HV 1800…2000 и сохраняется при нагреве до 900…950оС. Глубина борирования 0,1…0,2мм.
Борирование повышает выносливость стали, стойкость ее в расплавах цинка, алюминия.
Борированию подвергают штампы и фильеры, втулки быстроходных дизелей, поршни и трубопроводы машин литья под давлением, вставки и плиты пресс-форм.
Алитированию подвергают мало- и среднеуглеродистые стали для повышения окалиностойкости и стойкости против атмосферной коррозии. Температура алитирования 950…1000оС, продолжительность процесса 5…6ч. Алитированное покрытие, содержащее не более 20…30% Al, представляет собой твердый раствор алюминия в железе, относительно пластично. Твердость его до HV 500. Износостойкость его низка. Алитированное покрытие защищает сталь от окисления длительно до 800…900оС, а кратковременно – до 950…1000оС. Алитируют ящики для термообработки и ХТО, чехлы термопар, тигли для расплавов солей и свинца, ковши для разливки алюминия и его сплавов, газоотводные трубки двигателей, печную арматуру, лопатки газовых турбин.
|
|
Легированные стали и сплавы.
Углеродистые стали дешевые, но обладают рядом недостатков, в первую очередь не имеют специальных свойств. Поэтому для изделий, работающих в сложных условиях, например высоких давлений, температур, коррозионного воздействия сред, применяются легированные стали. Это стали, в которых, кроме железа, углерода и постоянных примесей, вводятся специальные добавки – легирующие элементы (л.э.) с целью изменения эксплуатационных свойств. Легирующими элементами являются Cr, Ni, Al, Si, W и др. При легировании изменяются химсостав, структура и, следовательно, характеристики сплавов.
Дата добавления: 2018-04-04; просмотров: 408; Мы поможем в написании вашей работы! |
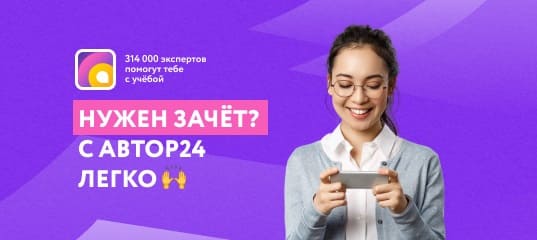
Мы поможем в написании ваших работ!