IV. Полярная связь (Ван-дер-Ваальса)
Такая связь образуется в кристаллах водорода и благородных газов в твердом состоянии (при очень низких температурах). На строение материала и его свойства большое влияние оказывают внешние факторы. Главными, из которых, являются условия производства материала, его термическая и механическая обработка, а также условия эксплуатации тех деталей, которые из него сделаны.
Основные понятия теории прочности.
При действии на деталь внешней силы, в материале возникает напряжение. Под напряжением понимают силу, действующую на единицу площади сечения. H=F/S [H/м2]
Любые напряжения можно разложить на нормальные(перпендикулярные поверхности) и касательные (в площади сечения) составляющие.
нормальные
касательные
Рост этих напряжений приводит к разным последствиям. Возрастание нормальных напряжений приводит к хрупкому разрушению материала, а касательных – к пластической деформации материала.
Наибольшее напряжение, при котором возможно восстановление прежних геометрических размеров деталей, при снятии нагрузки называется пределом упругости.
Предельное напряжение, при котором материал выдерживает нагрузку, не разрушаясь, называется пределом прочности.
|
|
Точка В называется точкой охрупчивания (хрупкого разрушения). Участок ОА – зона упругой деформации, участок АВ– зона пластической деформации.
Между упругой деформацией e и напряжением s, задается законом Гука, где Е – модуль упругости и вычисляется как tg α (Е = tg α).
s= Е•e |
Упругая деформация происходит за счет изменения межатомных расстояний в кристаллической решетке. Она устраняется после снятия нагрузки, благодаря силам взаимодействия между атомами.
- Углеродистые стали
Сталь – это сплав железа с углеродом, в котором количество углерода менее
2,14 %. Структура стали в равновесном состоянии определяется количеством в ней углерода. На рис. 1.1 представлена диаграмма состояния Fe – Fe3 C; структурными составляющими сталей являются феррит (твердый раствор углерода в α – Fe, решетка объемно центрированная кубическая), аустенит (твердый раствор углерода в γ – Fe, решетка гранецентрированная кубическая), цементит (химсоединение Fe3 C), перлит (эвтектоидная смесь феррита и цементита).
По структуре стали делятся на доэвтектоидные (C < 0,8 %), в них при комнатной температуре присутствуют феррит и перлит, эвтектоидный (C = 0,8 %), в которых есть только перлит, и заэвтектоидные (C > 0,8 %), где имеются перлит и вторичный цементит.
|
|
Влияние углерода и постоянных
Примесей на свойства стали
В углеродистой стали, кроме железа и углерода, содержатся постоянные примеси: Mn, Si, S, P.
Марганец и кремний – полезные примеси, попадают в сталь в процессе выплавки при раскислении. Эти элементы растворяются в феррите, повышая его прочность, но снижают пластичность.
Фосфор и сера – вредные примеси. Сера образует с железом сульфид FeS входящий в состав легкоплавкой эвтектики Fe+FeS (t пл = 988 °C). Эвтектика располагается преимущественно по границам зерен стали и является причиной хрупкости ее при температурах красного каления (t>800 °C ). Это явление называется красноломкостью.
Фосфор, растворяясь в феррите, упрочняет его, но снижает вязкость. Он повышает температурный интервал перехода стали в хрупкое состояние – порог хладноломкости.
Вредными примесями стали являются также газы (H, O, N,), которые повышают хрупкость.
Если количество постоянных примесей в стали не превышает допустимого (Mn < 0,8 %, Si ≤ 0,5 %,S≤0.05%, P ≤ 0,05 %), то свойства её определяется количеством углерода. С увеличением количества углерода изменяется структура стали. Механические свойства структурных составляющих предложены в табл. 1.1.1
|
|
Феррит – мягкая, вязкая, пластичная и малопрочная структурная составляющая. Различие в твердости и прочности феррита связано с содержанием Mn и Si. Цементит обладает высокой твердостью и хрупкостью. Свойства перлита имеют промежуточные значения сравнительно с ферритом и цементитом.
Таблица 1.1.1
Структурная составляющая | C, % | Механические свойства | ||
бв, МПа | δ, % : | Нв | ||
Феррит | < 0,01 | 250…300 | 40 | 80…100 |
Цементит | 6,67 | - | 0 | 800 |
перлит | 0,8 | 800…900 | 15 | 180…220 |
С ростом содержания углерода от 0,02 до 0,8 % в структуре доэвтектоидной стали увеличивается количество перлита, достигая 100 % в эвтекоидной стали, а когда углерода больше 0,8 %, наряду с перлитом в заэвтектоидной стали появляется структурно свободный цементит. При этом прочность и твердость стали будут возрастать, а пластичность и вязкость – уменьшится (рис. 1.1.1).
Предел прочности достигает максимума при 0,9 % углерода. Дальнейший рост концентрации углерода приводит к снижению прочности, так как в структуре стали цементит образует замкнутую сетку по границам зерен, которая является хрупким каркасом, воспринимающим нагрузку и приводящим к разрушению.
|
|
Высокоуглеродистые стали вследствие высокой твердости и низкой теплопроводности плохо обрабатывается резанием. Вязкие низкоуглеродистые стали также плохо обрабатываются резанием из-за образования трудноудаляемой сливной стружки. Лучше всего поддаются обработке резанием стали, содержащие 0,3…0,4 % C. C увеличением количества углерода снижается технологическая пластичность –
способность деформироваться в горячем и особенно холодном состоянии. Углерод ухудшает и свариваемость стали.
Классификация сталей.
Углеродистые стали по назначению делятся на конструкционные и инструментальные. Конструкционные стали предназначены для изготовления деталей машин, строительных сооружений, приборов. Эти стали должны сочетать прочность с достаточной вязкостью и хорошими технологическими свойствами. Этим требованиям в основном удовлетворяют доэвтектоидные стали.
Инструментальные стали должны иметь высокую твёрдость. Для изготовления режущего инструмента, штампов, мерительного инструмента используют эвтектоидную и заэвтектоидную стали.
Конструкционные стали. Углеродистые конструкционные стали делятся на качественные и обыкновенного качества.
Качественные стали характеризуются пониженным содержанием вредных примесей. Марки качественных сталей: 10, 15, 20 …85. Числа показывают среднее содержание углерода в сотых долях процента.
Низкоуглеродистые стали (С ≤ 0,25 %) обладают невысокой прочностью, но повышенной пластичностью, их применяют для малоответственных деталей (шайбы, прокладки, змеевики), элементов сварных конструкций, штампованных изделий. Эти же стали после поверхностного науглероживания (цементации) используют для деталей, работающих в условиях износа (кулачковые валики, рычаги, толкатели клапанов, пальцы рессор и др.). Среднеуглеродистые стали (0,3 % ≤ C ≤ 0,55 %), сочетающие прочность и пластичность, применяются для изготовления разнообразных деталей во всех отраслях машиностроения (коленчатые и распределительные валы, шатуны, шестерни, штоки).
Стали содержащие 0,6…0,75 % С, обладают наиболее высокой прочность, износостойкостью, упругостью. Из них изготавливают пружины, рессоры.
Углеродистые стали обыкновенного качества в процессе выплавки меньше очищаются от вредных примесей, их отливают в крупные слитки, поэтому они содержат повышенное количество неметаллических включений, но это и наиболее дешевые стали. Из них путем горячей прокатки получают листы, трубы, балки, швеллеры, уголки и др. Марки сталей обыкновенного качества: Ст.1, Ст.2, Ст.3 …Ст.6. Цифры показывают номер марки. От Ст.1 к Ст.6 растут количество углерода и прочность, но снижается пластичность.
В зависимости от назначения и гарантируемых свойств стали обыкновенного качества делятся на три группы.
Группа А. Сталь поставляется с гарантированными механическими свойствами. Их используют в состоянии поставки.
Группа Б. Сталь поставляется с гарантированным химсоставом. В марке сталей этой группы впереди ставится буква Б. Например, БСт.3. Эти стали предназначены для изделий, получаемых горячей обработкой, для выбора режимов которой необходимы сведения по химсоставу.
Группа В. Сталь поставляется с гарантированными химсоставом и механическими свойствами. В марке впереди ставится буква В. Например, ВСт.3. Применяется такая сталь для сварных конструкций, где исходные механические свойства сохраняются в местах, не подвергающихся нагреву при сварке.
Инструментальные стали. Углеродистые инструментальные стали маркируются буквой У и цифрой, показывающей количество углерода в десятых долях процента. Применяются стали марок У7, У8, У9, У10, У11, У12. В марке высококачественной стали с пониженным содержанием серы и фосфора ( < 0,02 % ) в конце ставится буква А. Например: У7А, У10А.
Сталь марок У7, У8 отличается максимальной вязкостью и применяется для инструмента, подверженного ударам (зубила, кузнечные штампы, матрицы, пуансоны). Из стали марок У9, У10 изготавливают режущий инструмент – свёрла, метчики, плашки, развёртки. Сталь марок У11, У12 используется для инструмента, который должен обладать максимальной твёрдостью и износостойкостью, при отсутствии вибрации, ударов (напильники, надфили).
Чугуны.
Сплавы железа с углеродом, в которых углерода более 2,14 %, называются чугунами. Углерод в чугуне может находиться как в свободном состоянии (графит), так и в связанном состоянии (цементит). В белых чугунах, структура которых соответствует диаграмме Fe – Fe3C, есть только цементит (рис. 1.1). Их характерная структурная составляющая – эвтектика (ледебурит). Поэтому белые чугуны очень хрупкие и используются передельный материал для получения стали и ковкого чугуна. В качестве конструкционных материалов применяются чугуны, в которых присутствует графит. В зависимости от формы графитных включений различают серый (пластинчатый графит), высокопрочный (шаровидный графит) и ковкий (хлопьевидный графит) чугуны. Такие чугуны можно рассматривать как сталь (металлическая основа), пронизанную графитными включениями.
Машиностроительные чугуны – литейные сплавы, обладающие хорошей жидкотекучестью и малой усадкой. Получение изделий из чугунных отливок значительно экономичнее, чем изготовление их обработкой резанием из стальных заготовок.
Структура чугунов, содержащих графит, не описывается диаграммой Fe – графит, ибо на процесс графитизации существенное влияние оказывают химический состав сплава и скорость охлаждения отливки.
В машиностроительных чугунах содержится С = 2,4 – 3,8 %, Si = 1,2 – 3,5 %, Mn = 0,6 – 1,25 %, S = 0,1 – 0,12 %, P = 0,2 – 0,4 %.
Кремний особенно сильно влияет на структуру чугуна, усиливая процесс графитизации.
Марганец препятствует графитизации, способствует отбелу (образованию цементита).
Сера также отбеливает чугун и ухудшает литейные свойства (жидкотекучесть).
Фосфор практически не сказывается на графитизации, но улучшает жидкотекучесть, ибо образует лёгкоплавкую эвтектику. Участки фосфидной эвтектики увеличивают твёрдость и износоустойчивость чугуна.
При заданном количестве углерода и кремния процесс графитизации протекает тем полнее, чем медленнее охлаждение. Ускоренное охлаждение частично или полностью прекращает кристаллизацию графита, способствует образованию цементита. Чем тоньше отливка, тем быстрее она охлаждается. Поэтому содержание кремния в таких отливках нужно увеличивать.
Чугун, содержащий графит, имеет как конструкционный материал ряд преимуществ сравнительно со сталью: он лучше обрабатывается резанием, обладает антифрикционными свойствами, нечувствителен к концентраторам напряжений, хорошо работает в условиях колебаний и вибрации.
Серый литейный чугун
Характерной особенностью серых чугунов является пластинчатая, лепестковая форма графита. Свойства чугуна определяются количеством, размером, взаимным расположением графитных включений, а так же структурой металлической основы. Графит обладает очень низкими механическими свойствами, поэтому его можно рассматривать как пустоты в металлической основе. Следовательно, чем больше графитных включений, чем они крупнее, тем ниже механические свойства чугуна. Графит пластинчатой формы играет роль трещин, надрезов, резко снижающих предел прочности при испытании на растяжение и пластичность. Поэтому механические свойства серого чугуна при изгибе выше, чем при растяжении, а относительное удлинение практически равны нулю. На твердость, предел прочности при сжатии графит влияния не оказывает.
По металлической основе различают серые ферритные, феррито-перлитные и перлитные чугуны. Наибольшую прочность обеспечивает перлитная металлическая основа. Маркируются серые чугуны буквами СЧ и числом, показывающим предел прочности при растяжении, уменьшенный в 10 раз, выраженный в МПа.
Марки серых чугунов: СЧ 10, СЧ 15, СЧ 18, СЧ 20, СЧ25. Первая марка соответствует ферритному, последняя – перлитному, остальные чугуны имеют феррито-перлитную металлическую основу. Повышают прочность серых чугунов модифицированием (введением в жидкий чугун перед разливкой модификаторов – ферросилиция, силикокальция в количестве 0,3 – 0,8 %). После модифицирования чугун имеет перлитную металлическую основу с небольшим количеством мелких пластин графита. Марки таких чугунов: СЧ 30, СЧ 35, СЧ 40. Ферритные и феррито-перлитные чугуны применяются для изготовления деталей, испытывающих небольшие нагрузки, а также работающих в условиях сухого трения и трения со смазкой: блоки цилиндров двигателей, головка блока, маховики, колодки, основанием металлорежущих станков. Перлитные чугуны используют для деталей, испытывающих динамические и статические нагрузки: шестерни, станины и стойки стаканов, поршневые кольца.
Высокопрочный чугун
В высокопрочном чугуне графит имеет шаровидную форму. Получают его комплексным модифицированием: введением в жидкий чугун модификаторов – ферросилиция и магния либо церия.
Включения графита шаровидной формы являются меньшим концентратором напряжений, чем пластинчатой. Поэтому прочность и пластичность высокопрочного чугуна выше, чем у серого.
Маркируют высокопрочный чугун буквами ВЧ, число показывает предел прочности при растяжении, уменьшенный в 10 раз, выраженный в МПа. Чугуны ВЧ 50, ВЧ 60 имеют перлитную, ВЧ 45 – перлито-ферритную, ВЧ 40 – ферритную металлическую основу.
Из высокопрочных чугунов изготавливают коленчатые валы автомобилей, прокатные валки, детали станков, корпуса паровых турбин.
Ковкий чугун
Ковким называют чугун с хлопьевидным графитом. Получают его отжигом отливок белого доэвтектического чугуна. В зависимости от режима отжига получают чугуны с различной металлической основой: ферритной, феррито-перлитной и перлитной.
Ковкий чугун, как и высокопрочный, обладает пластичностью. Маркируют чугун буквами КЧ, первое число показывает предел прочности при растяжении, уменьшенный в 10 раз, выраженный в МПа, второе – относительное удлинение (δ, %)
Ковкие чугуны по механическим свойствам близки к высокопрочным чугунам, но они более дорогие из-за большой продолжительности графитизирующего отжига (70…80 ч).
Ковкие чугуны применяются для изготовления деталей, работающих при высоких динамических и статических нагрузках, которые должны обладать повышенной прочностью при высокой пластичности и вязкости: картеры редуктора, ступицы.
Термическая обработка стали
Дата добавления: 2018-04-04; просмотров: 578; Мы поможем в написании вашей работы! |
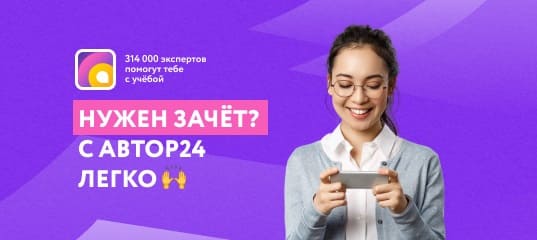
Мы поможем в написании ваших работ!