Фазовые превращения при нагреве и охлаждении
Все изготовленные из стали изделия в процессе их получения и эксплуатации подвергаются воздействию изменяющихся температур. В результате нагрева и охлаждения происходят фазовые превращения, влияющие на структуру и свойства сталей.
Эти превращения можно разбить на три группы:
- Превращения в стали при нагреве.
- Превращения при охлаждении.
- Превращения при нагреве закаленных сталей.
Превращения в стали при нагреве
Температуры, при которых происходят изменения в структуре, принято называть критическими точками. При нагреве стали выделяют следующие точки:
Ас1 – превращение перлита в аустенит (линия РSК диаграммы состояния Fe – Fe3С);
Ас3 – соответствует переходу последних кристаллов феррита в аустенит при нагреве (линия GS);
Асm – конец растворения вторичного цементита в аустените (линия SE).
Во всех сплавах железа с углеродом нагрев выше критической точки Ас1 приводит к превращению перлита в аустенит. В эвтектоидной стали (0,8% С) при дальнейшем повышении температуры никаких фазовых превращений не происходит вплоть до линии солидус. В доэвтектоидных и заэвтектоидных сталях после превращения перлита в аустенит еще остаются избыточные фазы (феррит в доэвтектоидных и цементит в заэвтектоидных). Для получения однофазной аустенитной структуры доэвтектоидные стали необходимо нагреть до температуры выше Ас3, а заэвтектоидные - Асm. Зерна аустенита, образующиеся при нагревании стали выше точки Ас1, получаются мелкими. При дальнейшем повышении температуры нагрева или длительности выдержки при данной температуре происходит рост аустенитного зерна. От размера зерна аустенита, образовавшегося при нагреве, зависит размер зерна продуктов распада аустенита при охлаждении.
|
|
Скорость роста аустенитного зерна различна у разных сталей и даже у одной стали, изготовленной по различным технологиям.
По склонности к росту зерна различают два вида сталей: 1) наследственно мелкозернистые и 2) наследственно крупнозернистые.
К наследственно крупнозернистым относятся стали, раскисленные ферросилицием и ферромарганцем. Стали, дополнительно раскисленные алюминием, - наследственно мелкозернистые. Большинство легирующих элементов (хром, молибден, ванадий, титан и др.) способствуют получению наследственного мелкого зерна. Однако есть и исключения. Марганец, бор и фосфор способствуют росту зерна аустенита. Наследственное зерно – это технологическая характеристика.
Термин „наследственно крупнозернистая” или ”наследственно мелкозернистая” сталь не означает, что данные стали всегда будут иметь крупное или мелкое зерно. „Наследственное зерно” определяет лиш склонность зерна к росту. Поскольку наследственно мелкозернистая сталь при высокой температуре нагрева может иметь более крупное зерно аустенита, чем наследственно крупнозернистая, введено понятие „действительного зерна”, т.е. зерна аустенита, определяемого температурой нагрева и продолжительностью выдержки при последней операции термообработки.
|
|
Механические свойства (ударная вязкость, предел усталости) зависят только от величины действительного зерна.
Если в сталях в результате нагрева образовалось крупное зерно (перегрев), неблагоприятно влияющее на свойства, то его исправляют повторной аустенизацией с меньшим перегревом относительно критических точек.
Превращения в стали при охлаждении.
Аустенит устойчив в углеродистой стали при температуре ³727°С (АсІ). Если его охладить ниже этой температуры, то он оказывается в неустойчивом состоянии и претерпевает превращение. Это превращения может идти двумя путями: изотермически и при непрерывном охлаждении.
Для изучения изотермического превращения аустенита небольшие образцы стали нагревают до температур, соответствующих существованию стабильного аустенита, т.е. выше Ас3 для доэвтектоидной стали. АсІ - для эвтектоидной и Асm – заэвтектоидной. Затем быстро охлаждают (переохлаждают) до температур ниже Ас3 (например, до 700, 600, 500 и т.д.) и выдерживают при этих температурах до полного превращения аустенита. Превращение аустенита начинается не сразу, а через некоторый промежуток времени (инкубационный период). Инкубационный период при разных температурах различен. По зафиксированным точкам начала и конца превращения аустенита строят диаграммы, в координатах температура-время (для времени принят логарифмический масштаб).
|
|
На рис 3.1.2.1 приведена диаграмма изотермического превращения аустенита стали с 0,8% углерода. Область, лежащая левее кривой начала распада аустенита, относится к инкубационному периоду; переохлажденный аустенит практически не претерпевает распада. С увеличением степени переохлаждения длительность инкубационного периода уменьшается, достигая минимума при температуре 550°С, а далее вновь возрастает.
В зависимости от характера превращений, протекающих в переохлажденном аустените, на диаграмме различают три температурные области превращения.
|
|
Рис 3.1.2.1. Диаграмма изотермического распада переохлажденного аустенита в эвтектоидной стали (0,8%С)
1. Перлитная (диффузионная) область – от точки АсІ до изгиба изотермической диаграммы (550° С). При этих температурах происходит диффузионный распад аустенита с образованием структуры, состоящей из феррита и цементита. При небольших степенях переохлаждения аустенит превращается в перлит (грубая ферритоцементитная смесь). Чем ниже температура изотермической выдержки, тем мельче пластинки феррита и цементита. Мелкопластинчатый (дисперсный) перлит, образующийся при 600-650° С, называется сорбитом.
В районе выступа кривых начала и конца распада получается высокодисперсный перлит, который называют трооститом. По мере повышения дисперсности строения прочность и твердость возрастают, а пластичность снижается. Твердость перлита 10-15 HRC, сорбита – 30-35 HRC, троостита – 40-45 HRC.
2. Область промежуточного превращения – от изгиба кривой (550° С) до точки Мн. Аустенит в этой области превращается в структуру, называется бейнитом (игольчатым трооститом). Бейнит состоит из мелкодисперсных частичек (игл) феррита и цементита. Размер этих частиц еще меньше, чем у троостита. Концентрация углерода в феррите выше равновесной (~0,1%), твердость бейнита ~50 HRC
3. Область мартенситного (бездиффузионного) превращения – ниже 240°.
При больших степенях переохлаждения происходит быстрая перестройка Ү - железа в α- железо. Времени на диффузионные процессы не остается, углерод не успевает выделиться из аустенита в виде частиц цементита, как это происходит при образовании перлитных структур. Он остается в ОЦК решетке Fe - a, искажая ее. Пресыщенный твердый раствор углерода в Fe - a называется мартенситом.
Мартенсит – очень твердая и прочная структура. Но пластичность и вязкость его низки. В мартенсите имеются, высокие остаточные напряжения, возникающие из-за увеличения удельного объема, вызванного фазовыми превращениями. Превращение аустенита в мартенсит начинается при определенной температуре, называемой Мн. По мере снижения температуры количество аустенита уменьшается, а количество мартенсита возрастает. Окончание превращения происходит в точке Мк – конца превращения. Положение точек Мн и Мк не зависит от скорости охлаждения и определяется химическим составом аустенита. Чем больше в аустените углерода, тем ниже лежат точки Мн и Мк.
Характерным для мартенситного превращения является то, что даже при температуре ниже Мк в стали наряду с мартенситом присутствует некоторое количество остаточного аустенита.
В процессе термической обработки стали часто превращение переохлажденного аустенита происходит не при изотермической выдержке, а при непрерывном охлаждении. Так как диаграмма изотермического распада аустенита построена в координатах температура-время, то на нее можно наложить линии охлаждения стали. (рис 3.1.2.2).
Наклон линии охлаждения в каждый рассматриваемый момент определяется скоростью охлаждения.
Рис 3.1.2.2. Диаграмма изотермического распада переохлажденного аустенита в эвтектоидной стали с наложенными на нее линиями охлаждения.
Вектор V1 (медленное охлаждение вместе с печью) пересекает линии диаграммы изотермического распада аустенита при высоких температурах и малом переохлаждении, и продуктом превращения является перлит.
С увеличением скорости охлаждения векторы V2 (охлаждение на воздухе) и V3 (охлаждение в масле) пересекают линии диаграммы при более низких температурах и образуются более мелкие феррито-цементные смеси – сорбит и троостит.
При скорости охлаждения V4 полного превращения аустенита в феррито-цементную смесь не происходит, часть его переохлаждается до точки Мн, в результате чего образуется структура, состоящая из троостита и мартенсита (охлаждение в масле, мелкие изделия).
V5 - вектор, который направлен по касательной к выступу изотермической кривой, приводит к переохлаждению всего аустенита до температуры ниже точки Мн и образованию мартенситной структуры. V5(Vкр) называется критической скоростью закалки (минимальная скорость охлаждения, при которой образуется мартенсит без продуктов перлитного распада). Для углеродистой стали это вода. При скорости охлаждения V6 также образуется мартенситная структур (водные растворы солей, щелочей).
Дата добавления: 2018-04-04; просмотров: 4857; Мы поможем в написании вашей работы! |
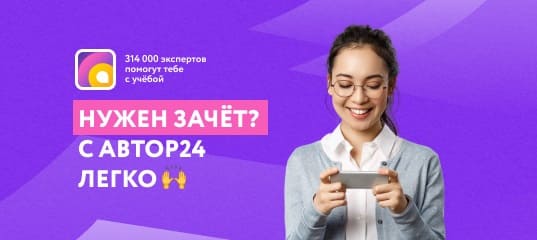
Мы поможем в написании ваших работ!