Превращение при нагреве закаленных сталей
Термическая обработка .заключается в нагреве закаленной стали ниже точки Ас1,называетсяотпуском стали.
Образующийся в результате закалки мартенсит является неравновесной фазой и при нагреве распадается с образованием ферритно-цементитной смеси. Этот распад имеет диффузионный характер и скорость его определяется температурой нагрева .
При температурах ниже 150°С из мартенсита избыточный углерод выделяется в виде очень тонких (в несколько атомных слоев ) пластин карбида Fe2C .величина внутренних напряжений уменьшается (первое превращение при отпуске )
При нагреве до 250-350 °С происходит распад мартенсита и превращение остаточного аустенита в мартенсит, в результате которого образуются дисперсные карбиды, решетка которых неразрывно связана с кристаллами низкоуглеродистого мартенсита (второе превращение при отпуске ).
Третье превращение при отпуске (350-400 °С) характеризуется завершением выделения из мартенсита избыточного углерода в виде цементита Fe3С и превращением его в феррит. Цементит, образующийся при отпуске, имеет округлую зернистую форму. При дальнейшем нагреве вплоть до точки Ас1 происходит коагуляция (укрупнение) карбидов (четвертое превращение).
С увеличением температуры отпуска прочность и твердость уменьшаются, пластичность и вязкость увеличиваются.
Технология термической обработки стали.
Отжиг.
Отжиг - это технологическая операция, состоящая из нагрева стали до определенной температуры (она может быть как выше, так и ниже критических точек), выдержки при этой температуре и последующего медленного охлаждения с печью. В большинстве случаев отжиг применяют как подготовительную термическую обработку.
|
|
В результате отжига твердость и прочность стали снижаются.
Различают два вида отжига: первого и второго рода.
Отжиг первого рода не зависит от фазовых превращений в стали. Отжиг второго рода основывается на фазовых превращениях.
К отжигу первого рода относятся:
-Гомогенизация (диффузионный отжиг). Применяют для слитков и отливок легированной стали с целью уменьшения дендритной или внутрикристаллитной химической неоднородности (ликвации). Ликвация понижает пластичность и вязкость стали .Нагрев при диффузионном отжиге должен быть высоким (1100-1200°С), так как только в этом случае более полно протекают диффузионные процессы, необходимые для выравнивания состава стали. Продолжительность отжига достигает 8-100 часов и более.
-Рекристаллизационный отжиг.
Используют обычно между операциями холодного деформирования для устранения наклепа в стали. Температура рекристаллизационного отжига выше температуры рекристаллизации (Тр≈0.5-08 Т. плавл.).Она зависит от состава стали и обычно находится в пределах 650–760 °С. Продолжительность отжига 8–12 часов.
|
|
- Отжиг для снятия остаточных технологических напряжений.
Применяют для отливок, сварных изделий, деталей после обработки резаньем и другое в том случае, когда несколько технологических операций следуют друг за другом. Температура отжига в зависимости от вида изделия изменяется в довольно широких пределах(160-700°С), продолжительность отжига составляет 2–3 часа.
К отжигу второго рода относятся:
- Полный отжиг. Заключается в нагреве доэвтектоидной стали на 30–50 °С выше температуры Ас3, выдержке при этой температуре до полного прогрева и завершения фазовых превращений в объеме металла и последующего медленного охлаждения. Применяют этот вид отжига обычно для получения в стали мелкого зерна .
- Изотермический отжиг. В этом случае сталь нагревают до точки Ас3+(50-70°С), затем быстро переносят в другую печь с температурой на 100–150 °С ниже Ас1. При этой температуре назначают изотермическую выдержку, необходимую для полного распада аустенита, после чего следует охлаждение на воздухе. Применяют вместо полного отжига. Преимущество изотермического отжига состоит в уменьшении длительности процесса и получении более однородной структуры.
|
|
- Неполный отжиг (сфероидизирующий отжиг).
Сталь нагревают до t>Ас1. Применяют для эвтектоидной и заэвтектоидной сталей с целью получения в них зернистого перлита вместо пластинчатого. Стали с зернистым перлитом имеют более низкие значения твердости и лучше обрабатываются резанием.
-Отжиг нормализационный (нормализация)
Заключается в нагреве доэвтектоидной стали до температуры выше Ас3, заэвтиктоидной выше Аст на 50˚С с последующим охлаждением на воздухе. Структура углеродистой стали после нормализации – сорбит. Нормализация устраняет крупнозернистую структуру. Для низкоуглеродистых сталей нормализацию используют для улучшения обрабатываемости резанием. Для среднеуглеродистых сталей нормализацию иногда применяют вместо улучшения (закалки и высокого отпуска) как окончательную термообработку. В заэвтектоидных сталях с помощью нормализации устраняют цементитную сетку, которая может возникнуть при медленном охлаждении.
Закалка.
Закалка заключается в нагреве стали до температур, повышающих критические точки на 30-50 0С, выдержке для завершения фазовых превращений и последующего охлаждения со скоростью больше критической.
|
|
Доэвтектоидные стали нагревают до температур выше Ас3 (полная закалка), заэвтектоидные – до температур выше Ас1 (неполная закалка) (рис. 3.2.2.1)
При неполной закалке доэвтектоидных сталей в их структуре наряду с мартенситом сохраняются участки феррита. Из-за низкой твердости феррита (НВ 80) твердость стали после закалки существенно понижена.
Для заэвтектоидных сталей полная закалка является оптимальной, поскольку после неё образуются мартенсит и вторичный цементит, обладающий высокой твердостью, что обеспечивает высокую износостойкость стали.
Охлаждающие (закалочные) среды должны обеспечить большую скорость охлаждения при температурах наименьшей устойчивости аустенита (650-550 0С), чтобы предупредить его распад на феррито – цементитную смесь. Углеродистые стали обычно при закалке охлаждают в воде, легированные – в масле.
Глубина закаленного слоя (прокаливаемость) зависит от химического состава стали. Она растет с увеличением количества легирующих элементов. Твердость стали после закалки (закаливаемость) определяется содержанием в ней углерода. Чем больше углерода, тем выше закаливаемость. Поэтому низкоуглеродистые стали (С ≤ 0,2%) не закаливаются.
Самый простой способ закалки – это закалка в одном охладителе (непрерывная закалка) – вектор 1 на рис. 3.2.2.2. Однако в этом случае в стали возникают высокие внутренние напряжения. Они слагаются из температурных напряжений, связанных с неравномерным охлаждением по сечению изделия, и структурных, с вязанных с изменением удельного объема стали при фазовых превращениях, которые идут не одновременно по толщине изделия. Внутренние напряжения вызывают деформацию изделий и образование в них трещин.
Для уменьшения величины напряжений, применяют более сложные способы закалки.
Прерывистая закалка (в двух средах). Изделия сначала быстро охлаждают в воде до температуры несколько выше точки Мн, а затем в менее интенсивном охладителе – масле (рис. 3.2.2.2, вектор 2).
Ступенчатая закалка. Сталь охлаждают в солённой ванне с температурой несколько выше точки Мн (обычно 180 – 250 оС) и выдерживают в ней сравнительно короткий промежуток времени, определяемый по диаграмме изотермического превращения аустенита (Выдержка не должна вызывать бейнитного превращения аустенита) (рис 3.2.2.2, вектор 3).Затем изделие охлаждают до комнатной температуры на воздухе. В результате выдержки в соляной ванне происходит выравнивание температуры по сечению изделия. Этот метод закалки характеризуется минимальными напряжениями.
Изотермическая закалка. Её осуществляют аналогично ступенчатой, но изделия выдерживают в ванной дольше, до конца изотермического превращения аустенита в промежуточной области (рис. 3.2.2.2, вектор 4). В результате образуется бейнит. На Бейнит обычно термообрабатывают ресурно – пружинные стали.
Поверхностная закалка. При поверхностной закалке закаливается только поверхностный слой, сердцевина изделия остается вязкой и воспринимает ударные нагрузки. Основное назначение поверхностной закалки: повышение твердости, износостойкости и предела выносливости обрабатываемого изделия. Наиболее часто применяют поверхностную закалку с индукционным нагревом током высоты частоты (ТВЧ). Для нагрева изделие помещают в индуктор, представляющий собой один или несколько витков пустотелой водоохлаждаемой медной трубки. Переменный ток, протекая через индуктор, создает переменное магнитное поле. В результате на поверхности изделия индуцируются вихревые токи, вызывающие ее разогрев. Глубина разогрева , 𝐟, Гц – частота тока. После нагрева деталь перемещают в душирующее устройство (спрейер). Изменяя частоту тока, можно регулировать толщину закаленного слоя. Завершающая операция – низкий отпуск.
Для поверхностной индукционной закалки чаще применяют углеродистые стали, содержащие 0,4 – 0,5% С. Перед закалкой ТВЧ для получения вязкой сердцевины сталь подвергают нормализации либо улучшению.
Процесс поверхностной закалки ТВЧ высокопроизводителен, его легко автоматизировать, он практически не сопровождается деформацией изделий и образованием окалины на их поверхности. Получение на поверхности мартенсита с большим удельным объемом повышает выносливость стали.
Для получения равномерного по глубине закаленного слоя необходимо, чтоб индуктор повторял контур изделия, что для сложных изделий очень трудно. Поэтому в таком случае часто применяют закалку с глубинным нагревом сталей пониженной прокаливаемости, что достигается снижением в них количества кремня и марганца. В этом случае применяют стали с уменьшенным Si и Mn. Например, 55ПП – 0,55 % С, ПП – пониженная прокаливаемость.
Отпуск.
Отпуск является заключительной операцией термической обработки, формирующей структуру и свойства изделия. Подвергают отпуску сталь, закаленную на мартенсит. При отпуске температура нагрева ниже линии фазовых превращений Ас1, охлаждение углеродистых сталей осуществляют на воздухе. Различают три вида отпуска: низкий, средний и высокий.
Низкий отпуск проводят с нагревом до 150 – 200 оС. При низком отпуске снижаются внутренние напряжения. Твердость остается высокой. Структура стали после низкого отпуска – отпущенный мартенсит. Используют такой вид отпуска для режущего, мерительного инструмента.
Средний отпуск проводят при 350 – 500 оС. В результаты образуется троостит отпуска (НRC 40 – 50). Происходит дальнейшее снижение внутренних напряжений. Применяется средний отпуск для рессор и пружин, а также инструмента горячей обработки давлением.
Высокий отпуск (550 – 650 оС) обеспечивает образование сорбита отпуска, сочетающего прочность, пластичность и ударную вязкость. Закалка с высоким отпуском называется улучшением. Улучшению подвергают детали машин, работающие при ударных, циклических нагрузках (валы, оси, шестерни и др.), НRС ~ 30 – 35.
Структуры, представляющие собой феррито - цементитные смеси (троостит, сорбит), полученные при отпуске, имеют зернистое строение, что обеспечивает им более высокую ударную вязкость по сравнению с аналогичными структурами закалки.
Дата добавления: 2018-04-04; просмотров: 952; Мы поможем в написании вашей работы! |
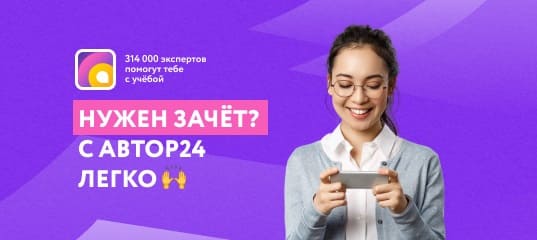
Мы поможем в написании ваших работ!