ДЕПАРАФИНИЗАЦИЯ И ОЧИСТКА СВЕТЛЫХ НЕФТЕПРОДУКТОВ
§ 63. ДЕПАРАФИНИЗАЦИЯ ДИЗЕЛЬНЫХ ТОПЛИВ
Депарафинизацией называется процесс выделения из нефтяных фракций твердых углеводородов, выпадающих в виде кристаллов при охлаждении нефтяной фракции. По своему групповому составу это могут быть высокомолекулярные парафины, а также нафтеновые, ароматические и нафтено-ароматические углеводороды с длинными боковыми алифатическими радикалами нормального и слаборазветвленного строения.
Дизельные фракции парафинистых нефгей содержат значительное количество алканов нормального строения, благодаря чему имеют сравнительно высокую температуру застывания —10 -=-
—11°С. Чтобы получить из таких фракций дизельное зимнее топливо с температурой застывания —45 "С и дизельное арктическое топливо с температурой застывания —60 °С, эти фракции подвергают депарафинизации.
Выделенные из дизельного топлива легкоплавкие парафины представляют собой ценный продукт нефтепереработки, в дальнейшем используемый для производства белково-витаминных концентратов микробиологическим способом.
Одним из методов отделения дизельного топлива от парафинов является карбамидная депарафинизация.
Карбамид (ЫН2)гСО представляет собой белое кристаллическое вещество, гигроскопичное, легко растворимое в воде и низших спиртах, с температурой плавления 132,5°С. При нагревании с водой в щелочной среде карбамид разлагается на двуокись углерода и аммиак. Карбамид обладает способностью к образованию кристаллических комплексов с алканами нормального строения, у которых число атомов углерода в молекуле не менее шести (см. § 11). Углеводороды гибридного строения, имеющие в составе молекулы длинные неразветвленные алифатические радикалы, также образуют карбамидные комплексы. Способность углеводородов к комплексообразованию и прочность полученного комплекса повышаются с увеличением длины неразветвленной цепи алифатического углеводорода. Образование комплекса сопровождается выделением теплоты, количество которой возрастает с увеличением молекулярной массы углеводородов.
|
|
311
Образование комплекса протекает по схеме:
парафин + карбамид ^=± комплекс
Для каждого углеводорода имеется верхний температурный предел, выше которого его комплекс с карбамидом разлагается. Поэтому для более полного извлечения парафиновых углеводородов процесс комплексообразования следует вести при пониженных температурах.
Влияние температуры комплексообразования на выход и температуру застывания депарафинированного дизельного топлива показано на рис. 81. При температуре процесса выше 20 °С температура застывания дизельного топлива и его выход возрастают, что указывает на неполное комплексообразование. Соотношение карбамид: сырье также влияет на ход
|
|
-20 г
85*-
0 40 80 /20 160 Расх.од карбамида. % (масс.) Рис. 82. Зависимость темпе» ратуры застывания депара-фината от расхода карбамида (расход активатора — 3% (масс.) на карбамид). |
10 20 30 40 50 Температура комплексе/образования,0 С
Рис. 81. Зависимость температуры застывания (/) и выхода (2) депара-фината от температуры комплексообразования.
процесса. На рис. 82 приведена зависимость между расходом карбамида и температурой застывания депарафинированного дизельного топлива. Для дизельных топлив оптимальным является соотношение карбамид : сырье =1:1.
Полнота комплексообразования зависит от хорошего контакта дизельного топлива и карбамида. Для снижения вязкости и улучшения контакта используют растворители, которые хорошо растворяют и нормальные парафиновые углеводороды, и карбамид. Наиболее часто применяют изопропиловый и изобутиловый спирты. Отрицательная роль растворителя — частичное разрушение комплекса, что в итоге увеличивает расход карбамида.
Сильное влияние на интенсивность комплексообразования оказывают вещества, получившие название активаторов: метиловый спирт, ацетон и др. В составе активаторов обязательно должно быть некоторое количество воды. Следует учитывать, что избыток акти-
|
|
312
ватора ухудшает комплексообразование, сдвигая равновесие влево. Активатор и его количество подбирают экспериментальным путем.
Глубина извлечения парафинов зависит также от продолжительности контакта сырья и карбамидного раствора. С повышением температуры кипения и вязкости нефтяной фракции время контакта увеличивается. Для дизельного топлива в условиях интенсивного перемешивания процесс комплексообразования заканчивается примерно за 30—40 мин. Необходимым условием успешного ведения процесса является чистота применяемого карбамида. Незначительные примеси, встречающиеся в техническом карбамиде, делают его непригодным.
В настоящее время для депарафинизации дизельного топлива карбамидом применяется несколько технологических схем, например депарафинизация с кристаллическим карбамидом и депара-финизация в спирто-водном растворе карбамида. Основные этапы процесса — образование карбамидного комплекса, отделение его, промывка и деструкция.
|
|
Образование комплекса, требующее тесного контакта карбамида и дизельного топлива, происходит или в мешалке, или в трубчатом реакторе с принудительным перемешиванием при помощи насосов. При этом реагирующая смесь охлаждается водой. Использование низкокипящих растворителей, например хлористого метилена (температура кипения 41°С) или изобутилового спирта в смеси с бутаном, дает возможность отводить тепло из реактора чза счет частичного испарения растворителя.
Отделение комплекса от депарафинированного продукта осуществляется отстаиванием, фильтрованием, центрифугированием.
Комплекс-сырец, представляющий собой белый сметанообраз-
ный продукт, увлекает с собой некоторое количество дизельного
топлива. При разрушении комплекса это топливо попадает в па
рафин и делает его непригодным для дальнейшего использования.
Поэтому вводится стадия промывки комплекса-сырца лигроином
(пределы выкипания 180—220 °С). Промывка обычно проводится
в две или три ступени, расход лигроина составляет от 40 до 140%
на сырье. <
Деструкция промытого комплекса происходит при нагревании его до 70—75 °С. Свободный карбамид растворяется в водной среде, а парафины отстаиваются.
Технологическая схема.Схема процесса депарафинизации дизельного топлива спирто-водным раствором карбамида приводится на рис. 83.
Депарафинируемое дизельное топливо подается сырьевым насосом Н-1 через холодильник Х-1 в реактор Р-1. Предварительно сырье смешивается со спиртовым раствором карбамида, который подается насосом Н-7 из емкости Е-3. Для интенсивного перемешивания дизельного топлива с раствором карбамида и охлаждения смеси реакцию проводят последовательно в три ступени в реакторах Р-1, Р-2 и Р-3, причем часть продукта циркулирует через холодильники Х-1, Х-2 и Х-3.
313
Из реактора Р-3 карбамидный комплекс и депарафинированное дизельное топливо поступают в отстойник Е-1, где разделяются на два слоя: верхний — депарафинированное дизельное топливо и нижний — смесь спиртового раствора карбамида и кристаллического комплекса. Дизельное топливо насосом Н-10 отводится с установки. Смесь раствора карбамида и кристаллического комплекса подвергается трехкратной промывке лигроином для удаления остатков дизельного топлива (на схеме показана промывка в одну ступень). Карбамидный раствор с низа отстойника Е-1 подается в смеситель И-1, где контактирует с лигроином, поступающим с выкида насоса Н-9. В отстойнике Е-2 смесь разделяется
|
|
*-т |
А—*Л^ |
ХК-1 |
ES^H-7 |
Рис. 83. Технологическая схема установки денарафинизации дизельного топлива спирто-водным раствором карбамида:
/—сырье; Л —зимнее дизельног топливо; ///— компонент летнего дизельного топлива;
IV — жидкие парафины.
на бензиновый слой с извлеченным дизельным топливом и промытый карбамидный раствор с кристаллическим комплексом. Карбамидный раствор насосом Н-5 направляется в пароподогреватель Т-2. При этом комплекс разрушается. Жидкие парафины и карбамид выделяются в свободном виде. Таким образом, спиртовой раствор карбамида регенерируется.
Отстой жидких парафинов от карбамидного раствора происходит в обогреваемой емкости Е-3. Жидкие парафины из верхней части емкости Е-3 поступают в емкость Е-4, а спиртовой раствор карбамида возвращается на смешение с сырьем. Лигроин из емкости Е-2 подается насосом Н-6 через теплообменник Т-1 в колонну К-1, где отгоняется от дизельного топлива. Отогнанный лигроин вновь используется для отмывки комплекса, а дизельное топливо отводится с установки и может быть использовано как добавка к летнему дизельному топливу. Основные параметры технологического процесса приводится ниже:
Температура комплексообразования, "С . |
20—30 75
314
Время контакта в Р-1, Р-2, Р-3, мин .... 30—50
Массовое соотношение раствор : сырье . ... 4,2:1
Содержание карбамида в растворе, % ■ • • • 38—43
Концентрация изопропилового спирта, % • • 62—68
Успешное проведение процесса зависит как от тщательного регулирования температуры, так и в особенности от соотношения карбамида, сырья, активаторов и растворителей. Поэтому большое внимание уделяется периодическому лабораторному контролю за качеством сырья, карбамида и промежуточных растворов.
К основным неполадкам ведения процесса следует отнести забивку трубок холодильников, а также комплексопроводов кристаллическим комплексом, поскольку комплекс обладает высокой адгезией (способностью прилипать) к металлам. Трубы холодильников промывают горячей водой, комплексопроводы облицовывакЗт фторопластом.
Материальный баланс.Материальный баланс процесса карб-амидной депарафинизации дизельного топлива с целью получения дизельного зимнего топлива с температурой застывания —45°С (I) и дизельного арктического топлива с температурой застывания —60°С (II) приводится ниже [в % (масс.)]:
Поступило:
Сырье
фракция 200-350 °С............................................. 100 —
« 200-320 °С............................................ - 100
Итого ... 100 100
Получено:
Депарафинированное дизельное топливо
Парафин ............................ .................
Потери............................................................
85,0 | 82,6 |
14,1 | 16,5 |
0,9 | 0,9 |
Итого . . . 100,0 100,0
Техника безопасности.На установке используют токсичные и взрывоопасные вещества: изопропиловый спирт, бензин, метиловый спирт. Поэтому все сбросы из аппаратов направляются в специальные скрубберы, орошаемые водой для улавливания изопропилового спирта, который возвращается в процесс. Дренаж с установки осуществляется в специальную емкость.
Примерные технико-экономические показатели на производство 1 т зимнего дизельного топлива
Пар, кг
Р-1,2 МПа ..................................................... ... 107
Р-0,3 МПа ..................................................... ... 125
Вода оборотная, м3...................................................... ... 34,1
Электроэнергия, кВт/ч................................................. 41,2
Топливо (газ), кг.......................................................... ... 49,3
315
§ 64. ИЗВЛЕЧЕНИЕ ЖИДКИХ ПАРАФИНОВ МЕТОДОМ АДСОРБЦИИ НА МОЛЕКУЛЯРНЫХ СИТАХ
Жидкие парафины приобрели большое значение как сырье нефтехимического и микробиологического синтеза. На их основе получают поверхностно-активные вещества, моющие средства, кормовые белки. Наибольшим спросом пользуются жидкие парафины Сю—С|8, получаемые из прямогонной дизельной фракции 200—320 °С.
Жидкие парафины являются побочным продуктом производства низкозастывающих дизельных топлив методами карбамидной депарафинизации (см. § 63) и адсорбции на цеолитах — молекулярных ситах (характеристику адсорбентов-цеолитов см. на стр. 219—220).
Установки адсорбционного извлечения парафинов на молекулярных ситах строятся в нашей стране и за рубежом. Наряду с высоким качеством парафинов адсорбционное извлечение позволяет обеспечить высокую степень выделения алканов из сырья, превышающую 95%. Это в 1,3—1,5 раза выше, чем при карбамидной депарафинизации.
Установки для получения жидких парафинов адсорбционным извлечением. Процесс производства нормальных парафинов из нефтяных фракций с помощью цеолитов включает следующие протекающие последовательно стадии: адсорбцию — поглощение алканов нормального строения из сырья и десорбцию — выделение их из полостей цеолита. Между этими стадиями в процесс включается дополнительная операция — продувка, при которой из адсорбента удаляются компоненты сырья, а с внешней поверхности цеолита — неселективно адсорбированные углеводороды.
Существует несколько различных способов десорбции углеводородов: отдувка газом, термический, снижением давления, вытес-нительный, при котором молекулы адсорбированного вещества вытесняются из полостей цеолита и заменяются молекулами вытеснителя.
На рис. 84 приводится схема блока адсорбции установки извлечения нормальных парафинов. Гидроочищенная дизельная фракция предварительно подвергается осушке в колоннах К-1 и К-2, а затем смешивается с водородсодержащим газом и проходит через теплообменник Т-1 и печь П-1, где испаряется и нагревается до 350—400 °С. Назначение водородсодержащего газа — улучшить условия теплообмена, подавить реакции крекинга и полимеризации сырья и адсорбированного продукта на молекулярных ситах.
Парообразная смесь поступает в реакторный блок, который состоит из трех адсорберов — К-3, К-4, К-5, работающих по сменно-циклическому графику. Схема работы адсорберов следующая: в течение первого периода протекает стадия адсорбции, затем адсорбер переключается на стадию продувки и, наконец, в нем проводится стадия десорбции. Десорбция осуществляется с помощью вытесняющего средства — аммиака. Все стадии поочередно
316
протекают в каждом из трех адсорберов. Переключение адсорберов происходит автоматически с помощью запрограммированных быстродействующих запорных клапанов. Время десорбции больше, чем адсорбции.
Приведенная на рис. 84 схема характеризует тот момент работы установки, когда в адсорбере К-3 проводится адсорбция, в К-4— продувка, в К-5— десорбция.
Парообразная смесь выходит из К-3 и поступает в блок очистки и конечной обработки, где охлаждается, конденсируется и разделяется на водородсодержащий газ, депарафинат-дизельную
|
- v
•VI
Рис. 84. Технологическая схема установки абсорбционного извлечения парафинов:
/ — сырье; //—аммиак; /// — водородсодержащий газ; IV— фракция 190—240 °С нормальных парафинов; V — фракция 240 — 320 °С нормальных парафинов; VI — депарафинированный продукт; А—блок очистки и конечной обработки.
фракцию, не содержащую нормальных алканов, и аммиак. Аммиак содержится в парах, уходящих из адсорбера потому, что в процессе адсорбции он вытесняется из пор цеолита. Водородсодержащий газ и аммиак возвращаются в процесс, а депарафинат используется как компонент низкозастывающего дизельного топлива.
В адсорбер К-4 подается аммиак, подогретый до необходимой температуры в печи П-2. Смесь аммиака и удаленных при продувке продуктов объединяется с парами из адсорбера К-3 и поступает в блок очистки и конечной обработки.
В адсорбер К-5 подается предварительно осушенный в К-2 и нагретый в печи П-3 аммиак. Из К-5 выходит смесь аммиака и Нормальных парафинов,л которая поступает в блок очистки и конечной обработки.
§ 66. ОЧИСТКА СВЕТЛЫХ ДИСТИЛЛЯТОВ
Светлые нефтепродукты — карбюраторные, реактивные и ди^ зельные топлива, бензины-растворители, осветительный керосин, полученные непосредственно из ректификационных колонн установок АВТ, гидроочистки, каталитического крекинга и других, еще
317
не являются товарными продуктами, так как содержат компоненты, ухудшающие их эксплуатационные качества.
Из бензинов, реактивных и дизельных топлив необходимо удалить сероводород, меркаптаны, нефтяные кислоты; из крекинг-бензинов помимо сероводорода и меркаптанов удаляют диеновые углеводороды, из бензинов-растворителей и осветительных керосинов — ароматические углеводороды.
Для получения низкозастывающих дизельных топлив, из последних выделяют твердые парафиновые углеводороды.
Для удаления нежелательных компонентов применяют химические и физико-химические методы очистки: обработку щелочью и серной кислотой, карбамидную депарафинизацию, адсорбцию.
Щелочная очистна
Щелочная очистка (защелачиванне) используется для удаления из нефтепродуктов сероводорода, низших меркаптанов и нефтяных кислот; щелочная доочистка — для удаления из нефтепродуктов следов серной кислоты и кислых продуктов реакции после сернокислотной очистки.
Для удаления сероводорода применяют обычно раствор едкого натра или кальцинированной соды Na2C03. Сероводород реагирует со щелочью по уравнениям:
2NaOH + H2S —>■ Na2S + 2Н20 NaOH + H2S —► NaHS + H20
Меркаптаны реагируют со щелочью с образованием меркап-тидов:
RSH + NaOH 4=fc RSNa + НО
Меркаптиды хорошо растворяются в щелочи и поэтому могут быть удалены из дистиллятов. Удалению меркаптанов в виде мер-каптидов препятствует гидролиз последних.
Нефтяные кислоты образуют со щелочью или содой соли нефтяных кислот — мыла:
RCOOH + NaOH —* RCOONa + Н20 2RCOOH + Na2C03 —»- 2RCOONa + С02 + H20
Соли нефтяных кислот переходят в водный раствор щелочи и, таким образом, легко отделяются от нефтепродукта.
Для щелочной очистки светлых нефтепродуктов обычно применяют 10% раствор NaOH. Температура защелачивания бензинов 40—50 °С, керосинов 60—70 СС, дизельных топлив 80—90 °С. Повышение температуры уменьшает опасность образования водных эмульсий и облегчает отстой нефтепродукта от щелочного раствора. Следы щелочи удаляются из нефтепродукта водной промывкой.
В настоящее время наиболее широко распространена полунепрерывная схема защелачивания топливных дистиллятов. Нефтепродукт поступает непрерывно, а щелочной раствор циркулирует в системе и периодически обновляется. Отработанный раствор со-
818
держит 2% NaOH. Таким образом, степень использования щелочи составляет 80%.
Качество очистки контролируют специальной пробой на коррозию медной пластинки. Как только очищаемый продукт перестанет выдерживать эту пробу, отработанный щелочной раствор полностью заменяют свежим.
Расход щелочи зависит как от конечной концентрации щелочи в отработанном растворе, так и от содержания сернистых или кислородных соединений в очищаемом продукте. Для ирямогон-ного бензина расход составляет 0,32 кг/т.
Осушка светлых нефтепродуктов. Одним из узких мест щелочной очистки было до недавнего времени окончательное удаление влаги из очищенного дистиллята. В отстойнике полнота удаления влаги не достигается. Введение в схему электроосадителя, аналогичного по конструкции горизонтальному электродегидратору установки ЭЛОУ, значительно улучшило осушку.
Применяется также осушка нефтепродукта (в частности, керосина) воздухом, пропускаемым вверх навстречу топливу, стекающему вниз по насадке цилиндрического аппарата.
Следует отметить, что аппаратура для щелочной очистки, водной промывки и осушки размещается непосредственно на установке получения дистиллятов: установках АВТ, гидроочистки и т. д.
Крупными недостатками щелочной очистки являются безвозвратная потеря дорогого реагента и образование большого количества трудноутилизируемых сернисто-щелочных стоков.
Кислотная очистка
Очистка серной кислотой применяется для удаления из нефтепродуктов непредельных и ароматических углеводородов, а также смолистых, азотистых и отчасти сернистых соединений.
При смешении нефтепродукта с серной кислотой и последующем отстое образуются два слоя: верхний — очищенный продукт, нижний — кислый гудрон, представляющий собой отработанную кислоту с растворенными в ней продуктами реакции.
Механизм сернокислотной очистки. На парафиновые и нафтеновые углеводороды серная кислота при нормальной температуре не действует.
С непредельными углеводородами серная кислота образует кислые и средние эфиры:
RCH=CH2 + H2S04 —*■ RCH—OS02OH
U
СН;, . I
RCH=CH. + H2S04 RCH=CH2 |
RCH-Оч
^S02
RCH—CK
I CH3
319
Кислые эфиры растворяются в серной кислоте, а средние —i в очищаемом продукте, поэтому образование средних эфиров нежелательно.
Кроме этих реакций протекает реакция полимеризации моно-олефинов. Полученные полимеры остаются в очищаемом продукте и, имея более высокую температуру кипения, ухудшают фракционный состав бензинов. Чтобы удалить полимеры из бензина, применяют вторичную перегонку. Диолефины и циклоолефины при полимеризации дают высокомолекулярные смолообразные вещества, переходящие в кислый гудрон.
Ароматические углеводороды сульфируются только концентрированной серной кислотой, взятой в избытке. При этом образуются сульфокислоты и сульфоиы, растворимые в серной кислоте;
C6HB + H2S04 —v C6H5S02OH + Н20
сульфокнслота
CGH0 + CsH5SO,OH —> (C0H5)2SO2 + Н20
сульфон
Нефтяные кислоты частично растворяются в серной кислоте, частично сульфируются. Смолистые вещества, как правило, полностью переходят в кислый гудрон.
Сероводород и меркаптаны, если они не были предварительно удалены защелачиванием, реагируют с серной кислотой:
H2S + H2SO., —> S + SOz + 2Н20
2RSH + H2S04 —> RS—SR + S02 + 2H20
Сера и дисульфиды остаются в очищаемом продукте. Остальные сернистые соединения частично растворяются в серной кислоте.
Для сернокислотной очистки осветительного керосина применяется 92—94%-ная серная кислота, для удаления ароматических углеводородов из бензинов-растворителей — 98%-ная кислота или олеум. Температура сернокислотной очистки дистиллятов должна быть как можно ниже: повышение температуры от 0 до 30 °С увеличивает потери с кислым гудроном.
Сернокислотная очистка имеет целый ряд недостатков, которые подробно разобраны в § 73.
Адсорбционная и каталитическая очистка светлых нефтепродуктов. Внекоторых случаях для очистки светлых нефтепродуктов от смолистых, асфальтеновых и других нежелательных соединений применяют естественные глины, искусственные алюмосиликаты, активированный уголь и другие твердые вещества. В основе их использования лежит явление адсорбции, описанное выше (см. §11, §59).
По адсорбируемости полярными адсорбентами первое место Среди компонентов нефтяных фракций занимают смолисто-асфаль-теновые вещества. Затем идут непредельные и ароматические углеводороды, причем непредельные углеводороды, особенно диолефины при адсорбции полимеризуются.
320
Адсорбционную активность адсорбента характеризуют количеством поглощенного вещества. Она тем выше, чем больше пористость адсорбента и его удельная поверхность, чем меньше частицы адсорбента. Для повышения активности адсорбенты подвергаются предварительной обработке (активации), которая проводится кислотным выщелачиванием, высушиванием, прокалкой. Температура прокалки не должна превышать 400—500 °С, так как при более высокой температуре возможно спекание и уплотнение пор адсорбента и, следовательно, ухудшение его свойств.
Адсорбенты используются в виде порошка или крупки. Порошки применяют при жидкофазной очистке, смешивая адсорбент с очищаемым продуктом. Адсорбенты в виде гранул (крупки) засыпают в адсорбционные колонны, а нефтепродукт пропускают через слой адсорбента в жидком или парообразном состоянии.
Ниже рассмотрены примеры адсорбционной и каталитической очистки светлых нефтепродуктов.
Адсорбционная очистка ароматических углеводородов служит для удаления непредельных углеводородов и придающих ароматическим углеводородам окраску смолисто-асфальтовых веществ. В настоящее время при получении ароматических углеводородов' из катализата риформинга для этой цели применяется метод гидрирования катализата в специальном дегидрирующем реакторе. Установлено, что очистка глинами в 2—3 раза дешевле, чем применяемый способ.
В результате очистки бромное число катализата снижается с 1,5—2,0 до 0,05 г Вгг на 100 г. Очистке можно подвергать либо катализат, либо экстракт ароматических углеводородов, выделенный из катализата. Установлено, что при очистке экстракта адсорбционная активность адсорбента значительно выше и срок службы больше. Для очистки, как показали исследования, могут быть применены естественные глины, активированные термическим, а в некоторых случаях, кроме того, еще и химическим способом. Режим процесса очистки: давление — 2,5—3,5 МПа, температура— 225—230 °С, срок службы глины — около 150 сут.
Каталитическая очистка бензинов применяется для удаления непредельных углеводородов из бензиновых фракций вторичного происхождения. Она осуществляется на обычных установках каталитического крекинга без изменения их схемы и замены катализатора — синтетического алюмосиликата. На некоторых НПЗ сооружены блоки из трех установок каталитического крекинга, две из которых предназначены для получения бензина из более тяжелых фракций, а третья — для его очистки (тритинга). Температура в реакторе каталитической очистки около 450°С, выход продуктов равен: авиационного очищенного бензина 70%, тяжелого бензина— компонента автомобильного топлива 6%. газойля 5%, сухих и сжиженных газов 10—12%.
П Зак. 3S0
Глава X
ПРОИЗВОДСТВО МАСЕЛ
§ 66. ОСНОВЫ ТЕХНОЛОГИИ ПРОИЗВОДСТВА НЕФТЯНЫХ МАСЕЛ
Нефтяные минеральные масла самого разного назначения получают из остатков атмосферной перегонки — мазутов. Процесс производства любых масел состоит из 3 этапов:
1) подготовка сырья — получение исходных масляных фракций;
2) получение компонентов из исходных масляных фракций;
3) смешение компонентов (компаундирование) и «сдабривание» их присадками для получения товарных марок масел.
Подготовка сырья заключается в разгонке мазутов под вакуумом (см. § 24, 25). Фракции, используемые для производства масел, по способу получения делят на две группы: дистиллятные — выделяемые в виде погонов при вакуумной разгонке мазута (300— 400 °С, 350—420° С, 420—450 °С), и остаточные — остаток вакуумной перегонки мазута (выше 500 °С) т. е. гудрон. Соответственно масла, полученные при переработке дистиллятных масляных фракций, называют дистиллятными, масла, полученные из гудрона— остаточными.
Производство компонентов из исходных масляных фракций — сложный многоступенчатый процесс. Основное назначение каждой ступени — полное или частичное удаление определенных групп соединений, отрицательно влияющих на эксплуатационные свойства масел. Из нефтяных фракций необходимо удалять все кислые соединения, непредельные углеводороды, частично сернистые и смолистые соединения, полициклические ароматические углеводороды с короткими боковыми цепями, твердые парафины.
В нашей стране масла длительное время вырабатывались только из бакинских и грозненских нефтей. В 1950-х гг. возникла острая необходимость в дополнительных сырьевых ресурсах для производства масел. Это привело к созданию новой базы по производству масел на заводах Татарской и Башкирской АССР. В 1950—1960 гг. были созданы крупнейшие заводы по производству масел из ромашкинской и других нефтей восточных районов. В настоящее время сырьевая база производства масел еще более расширилась за счет мангышлакской, усть-балыкской, самотлор-ской нефтей.
Нефти восточных районов и нефти Западной Сибири отличаются от бакинских и грозненских высоким содержанием серы,
322
*
смолисто-асфальтеновых веществ, твердых углеводородов. Поэтому схемы получения товарных масел из подобных нефтей значительно сложнее.
При получении масел из бакинских нефтей используют в основном очистку серной кислотой в сочетании с очисткой отбеливающими глинами. Для производства масел из смолистых и пара-финистых нефтей повсеместное распространение получили процессы с избирательными растворителями в сочетании с адсорбционной очисткой и гидроочисткой, причем число ступеней очистки возросло до трех-четырех.
В основе производства компонентов масел из исходных масляных фракций лежат методы избирательного удаления указанных выше нежелательных компонентов. Эти методы могут быть физическими — экстракция растворителями, осаждение из раствора при понижении температуры; физико-химическими — адсорбция; химическими — взаимодействие с серной кислотой, гидроочистка.
Производство остаточных масел сложнее, чем дистиллятных из-за высокого содержания смолисто-асфальтеновых веществ в гудронах. Полученный при вакуумной разгонке гудрон подвергают прежде всего деасфальтизации — удаляют смолисто-асфальтено-вые вещества. Деасфальтизат направляют на очистку избирательными растворителями (селективную очистку) фенолом или фурфуролом. Цель селективной очистки — извлечение остаточных смолисто-асфальтеновых веществ и полициклических ароматических углеводородов с короткими боковыми цепями. (Вместо деасфальтизации и селективной очистки можно применить очистку парными растворителями.)
Из рафината селективной очистки осаждают твердые парафины при помощи таких избирательных растворителей, как ацетон, дихлорэтан и др. Продукт депарафинизации окончательно доводят до кондиции путем адсорбционной или гидроочистки.
Дистиллятные масляные фракции^ как правило, в деасфальтизации не нуждаются. В остальном общие схемы производства дистиллятных и остаточных масел совпадают.
Принципиальная схема производства компонентов масла из дистиллятных и остаточных фракций приведена на стр. 414. Там же показана схема производства парафина и церезина из побочных продуктов депарафинизации.
Внедрение в нефтеперерабатывающую промышленность процессов гидрокрекинга и гидроизомеризации несколько изменит схему получения дистиллятных масел. Продукт гидрокрекинга вакуумного газойля фракция 350СС—к. к. представляет собой ценное сырье для производства масел и нуждается только в депарафинизации.
Высококачественные масла можно получать также при гидроизомеризации парафинов и гачей — побочных продуктов депарафинизации масел.
В результате очистки масляных фракций от смолистых веществ цвет масел изменяется — они становятся светлее. Удаление
11* 323
смолистых веществ и полициклических ароматических углеводородов1 с короткими боковыми цепями способствует снижению коксуемости и повышению индекса вязкости масел. Удаление смолистых веществ и непредельных углеводородов значительно увеличивает термоокислительную стабильность. Очистка от кислых соединений снижает коррозионную активность, а выделение из состава масел твердых углеводородов приводит к понижению температуры застывания. Эффективность технологических процессов производства масел и характеризуется достижением необходимых качественных показателей масел, а также выходом целевого продукта.
ТАБЛИЦА 16
Свойства масел из восточных нефтей
Показатели | Моторные масла | Индустриальные масла | Компрессорное | |||
МС-20С | ДС-П | АС-10 | ИС-12 | ИС-45 | масло KC-I9 | |
Вязкость мм2/с, не менее при 100 °С . . . ... при 50 "С . . . . Индекс ' вязкости, Температура застывания °С, не выше Зольность (без присадки), % (масс), Содержание серы (без присадки), % (масс), не более . . | 20 85 — 18 0,003 1,0 | 10,5-11,5 83 -15 0,005 1,1 | 9,5-10,5 85 -15 0,005 1,0 | 10-14 -30 0,005 1,0 | 38-52 85 -10 0,005 1,1 | 17-21 85 -18 0,005 1,0 |
Масла товарных марок приготовляют смешением отдельных компонентов (компаундированием) с добавлением присадок. Например, четыре марки товарных масел можно получить из трех компонентов, характеристика которых приводится ниже:
1-й компо- 2-й комло- 3-й компо-
нент нент нент
(350-420 °С) (420-500 °С) (выше 500 °С)
Вязкость, мм2/с'
при 50 °С............................. ............. 14,4 42,1 -
при 100 °С........................... ................. 4 7,5-8,1 22-24
Индекс вязкости......................... ................ 87 83 84
Температура застывания, °С —30 —30 —23
Товарные масла, полученные из этих компонентов, имеют следующий состав [в % (масс.)]. '
1-й компо- 2-й компо- 3-й компо-
нент нент нент
Автотракторное масло
АС-6..................................... ........ 42 58 -
АС-10.................................. ........ — 70 30
Авиамасло МС-20...................... ........ - 12 88
Веретенное 2............................... 100 — —-
824
Приготовление товарных масел осуществляется на установке компаундирования. Если имеются легкие, средние и тяжелые ди-стиллятные, а также остаточные компоненты, то можно приготовить масла почти любых сортов. Соотношение компонентов устанавливают по номограмме для определения вязкости смесей нефтепродуктов (см. номограмму в конце книги) в зависимости от вязкости компонентов и конечной вязкости товарного масла. В каждом отдельном случае соотношение компонентов уточняется в соответствии с лабораторными анализами готового масла.
Основные свойства некоторых марок товарных масел, полученных из восточных сернистых нефтей, приводятся в табл. 16.
§ 67. ПРИМЕНЕНИЕ ИЗБИРАТЕЛЬНЫХ РАСТВОРИТЕЛЕЙ В ПРОЦЕССАХ ОЧИСТКИ МАСЕЛ
Масляные фракции состоят из смеси углеводородов различных классов и гетероциклических соединений разнообразного строения. Физические свойства углеводородов зависят как от их принадлежности к определенному классу, так и от молекулярной массы. Физические свойства гетероциклических соединений отличаются от свойств углеводородов. В частности, все эти соединения по-разному и при различных температурах (избирательно) растворяются в ряде органических растворителей.
Избирательными, или селективными, растворителями называют такие жидкие вещества, которые обладают способностью извлекать при определенной температуре из смеси (например, из нефтепродукта) только какие-то определенные компоненты, не растворяя остальных компонентов и не растворяясь в них. Наибольший интерес для целей очистки представляют такие растворители, которые способны растворять различные вещества, входящие в состав масел, при резко отличающихся практических температурах растворения.
Иногда растворители хорошо растворяют углеводороды, а нежелательные компоненты осаждаются из раствора и легко отделяются. На этом принципе основаны процессы удаления смоли-сто-асфальтеновых веществ (деасфальтизация) и твердых углеводородов (депарафинизация).
В других процессах, наоборот, растворители хорошо растворяют нежелательные компоненты, но почти не растворяют ценных компонентов масляной фракции. Этот способ применяется при селективной очистке фенолом и фурфуролом. Очищенный продукт и концентрат нежелательных компонентов в каждом процессе имеют свои названия. Так, при деасфальтизации очищенная масляная фракция называется дезсфальтизатом, а концентрат смолисто-ас-фальтеновых веществ — асфальтом. При деперафинизации получаем депарафинированное масло (депмасло, депарафинат) и концентрат твердых углеводородов, называемый или гач, или петро-латум. При фенольной и фурфуроль'ной очистке получаем
325
очищенное масло-рафинат и концентрат смолистых, асфальтеновых и полициклическнх ароматических углеводородов — экстракт.
Селективность растворителей не идеальна, т. е. растворитель полностью растворяет одну из фаз и частично — вторую. Например, фенол хорошо растворяет полициклические ароматические углеводороды, но при этом частично растворяет и углеводороды масла. Следовательно, фенол обладает низкой селективностью или хорошей общей растворяющей способностью. Низкая селективность приводит к тому, что вместе с экстрактом или с гачем увлекаются ценные компоненты масла, а в деасфальтизат попадают смолы и асфальтены. В первом случае уменьшается выход масла, во втором — ухудшается качество деасфальтизата.
Добавление воды, а также бензола и толуола изменяет селективность и общую растворяющую способность таких растворителей, как фенол, фурфурол, дихлорэтан, спирты, кетоны. Добавление воды повышает селективность растворителя и снижает его общую растворяющую способность. Введение бензола и толуола, наоборот, понижает селективность растворителя, при этом повышается его общая растворяющая способность.
Ниже приводятся общие требования к растворителям.
1. Растворитель должен обладать ярко выраженной избирательной растворимостью, сохраняющейся в широком интервале температур.
2. Растворитель не должен хорошо растворяться в очищаемом продукте.
3. Желательна большая разница плотностей растворителя и сырья, что облегчает процесс разделения на фазы.
4. Растворитель должен быть химически стабильным и химически инертным по отношению к сырью, нетоксичным, невзрывоопасным и не должен вызывать коррозии аппаратуры.
5. Растворитель должен легко и полно регенерироваться. Для этого его температура кипения должна быть значительно ниже температуры кипения масла. Однако слишком низкая температура кипения также нежелательна, ибо приводит к необходимости вести процесс под давлением.
6. Растворитель должен иметь низкую теплоту испарения, что способствует снижению энергетических затрат и расхода охлаждающей воды.
7. Растворитель должен быть дешевым и недефицитным.
Физические свойства некоторых растворителей, применяемых
для производства масел, приводятся в табл. 17.
Для процессов очистки масел избирательными растворителями кроме того имеют значение следующие факторы: температура процесса, критическая температура растворения масляной фракции в растворителе, соотношение растворителя и сырья, способ взаимодействия растворителя с сырьем. Эти факторы будут подробно разобраны в разделах, посвященных соответствующим процессам. Давление сказывается лишь при использовании в качестве растворителей сжиженных газов (пропан, сернистый газ).
326
Шизические свойства растворителей, применяемых в
Показатели
Фенол
Фурфурол
Пропан
.м-Крезол
гс-Кре
со ю
Химическая формула ...................................
Молскулнрная масса........................................
Плотность РТ......................................................
Температура плавления при
0,1 МПа, °С......................................................
Температура кипения при 0,1 МПа,
°С.........................................................................
Растворимость в воде при 38 °С,
% (масс.)...........................................................
Растворимость воды при 38 °С,
% (масс.)...........................................................
Температура кипения азеотрэпнсй
смеси с водой, °С...........................................
Содержание растворителя в азео-
тропной смеси, % (масс.).......................
Критическая температура, °С . . .
Критическое давление, МПа . . .'.
Удельная теплоемкость при 20 °С,
кДж/(кг-°С)......................................................
Теплота испарения при температуре кипения кДж/(кг-°С) . . . .
* При 0 "С.
С6Н5ОН
94,11
1,071 (25 °С)
42,0
181,4
9,5
33,0
99,6 9,2
2,35 446
С4Н3ОСНО 96,09 1,1614
-38,7
161,7
9,0
6,5
97,8 35
1,58 450
С3Н8 44,09 0.5020
-187,7 -42,2
96,8 4,2
2,43*
419
СН3С6Н4ОН 108,06 1,0465
11,8 201,1
2,5
14,5
98,9 6
2,09 421
СН3С6Н
108,06 1,03
34,6
202,3
2,2
14,5
98,7 6
2,0
421
Регенерация растворителя из растворов масла и растворов нежелательных компонентов осуществляется в несколько стадий: сначала растворитель отгоняют при повышенном или атмосферном давлении, затем с применением водяного пара и иногда с использованием вакуума. Остаточное содержание растворителя в продуктах очистки не должно превышать 0,005—0,02% (масс).
Ценные углеводороды масла, как уже было упомянуто, могут попадать в экстракт или в гач. В основном это происходит из-за недостаточной селективности растворителя по отношению к углеводородам, по своему строению занимающим промежуточное положение между ценными и нежелательными компонентами масла. Потеря этих компонентов, получивших название внутреннего ра-фината при фенольной и фурфурольной очистке или просто масла в случае депарафинизации, снижает выход целевого продукта. Внутренний рафинат можно выделить с помощью следующих технологических приемов:
1) понижение температуры экстрактного раствора;
2) добавление воды в экстрактный раствор;
3) добавление экстракта в экстрактный раствор;
4) промывка порцией свежего растворителя при повышенной температуре.
При этом первые три метода повышают селективность растворителя, что приводит к выделению из экстрактного раствора внутреннего рафиката, а четвертый способствует выделению масла из гача или петролатума.
§ 68. ДЕАСШАЛЬТИЗАЦИЯ МАСЕЛ
Остаточные масла производят из гудронов и полугудронов. Эти фракции, особенно полученные из смолистых нефтей, могут содержать более" 50% (масс.) смол и асфальтенов, подлежащих удалению. Сложный состав смолисто-асфальтеновых соединений затрудняет подбор для них избирательных растворителей. Поэтому более целесообразно подбирать растворитель для ценных углеводородов масла. Смолисто-асфальтеновые вещества почти не будут растворяться в этом растворителе и выпадут в осадок. В качестве растворителя обычно применяют жидкий пропан.
Температура процесса. Область температур, в которой смолы легко отделяются от раствора углеводородов масла в пропане, лежит в пределах 50—85 СС.
Верхний предел температур ограничен критической температурой сжижения пропана (96,8 °С). Чем ближе температура процесса к критической, тем меньше растворяющая способность жидкого пропана и тем хуже растворяются в нем углеводороды масла, частично осаждаясь вместе со смолами. Выход масла вследствие этого снижается. Наоборот, при понижении температуры растворяющая способность жидкого пропана растет и уже при 40 °С смолы частично растворяются в пропане, отчего качество очищенного масла ухудшается.
328
Взаимодействие растворителя и сырья происходит в колонном
аппарате, причем пропан подается в низ колонны и поднимается
вверх противотоком к более тяжелому сырью, подаваемому сверху
и спускающемуся вниз. В верхней части колонны поддерживается
температура 75—85 °С, в нижней — 50—60 °С. Создание разности
температур между верхом и низом колонны позволяет более тща
тельно отделять смолы и асфальтены от масел. Эта разность тем
ператур, получившая название
градиента деасфальтизации,
обычно равна 15—20 °С.
50 |
<о -40 5 О4 *■ |
И0| 20 3 а; 10 « |
Для поддержания пропана в сжиженном состоянии процесс деасфальтизации осуществляется под давлением 4,0—4,5 МПа.
2 4 Ё 8 10 12 Соотношение пропан:сырье Рис. 85. Зависимость выхода (/), коксуемости (2) и вязкости (3) деасфальтизата от объемного соотношения пропана и сырья. |
Соотношение растворитель: сырье. Необходимое соотношение растворителя и сырья определяется опытным путем и зависит от содержания в сырье углеводородов. Чем выше их содержание, тем больше должно быть соотношение между объемом пропана и объемом сырья. Применяют объемное соотношение пропан : сырье от 4 : 1 до 8: 1. Увеличение количества пропана до определенного предела улучшает осаждение смолисто-асфальтеновых веществ, а это, в свою очередь, благотворно отражается на качестве деасфальтизата. С какого-то значения соотношения, разного для каждого вида сырья, избыток пропана частично растворяет нежелательные компоненты, при этом выход деасфальтизата растет, но качество его ухудшается (рис. 85).
Процесс деасфальтизации можно вести в одну ступень, но лучших результатов достигают при двухступенчатой схеме. Раствор асфальта, полученный в первой ступени, подвергают деасфальтизации во второй ступени, чтобы извлечь из него остаток ценных углеводородов масла. При помощи двухступенчатой схемы выход масла из гудрона повышается на 10%. Деасфальтизаты I и II ступеней сильно отличаются по качеству. Деасфальтизат II ступени используется для выпуска очень вязких масел. Качество гудрона ромашкинской нефти и полученных из него продуктов деасфальтизации приводится ниже:
Гудрон
Плотность pf................. ..... 1,010
Коксуемость, % (масс.) 18—20
Вязкость при 100 °С,
мм2/с.............................. ....... —
Температура размягче
ния, °С.......................... ....... 35
Деасфальтизат I | Деасфаль тнзат II |
0,915 | — |
1,1-1,3 | 1,5-2,2 |
20-23 | 30-55 |
Асфальт
66-75
329
Технологическая схема.Технологическая схема установки двухступенчатой деасфальтизации гудрона показана на рис. 86. Сырье — гудрон — сырьевым насосом //-/ подается в пароподогреватель Т-1 и далее в середину экстракционной колонны I ступени К-1. В нижнюю часть колонны К-1 с нагнетания насоса Н-2 поступает жидкий пропан. Раствор деасфальтизата I в пропане уходит с верха колонны К-1, а раствор асфальта I с низа колонны К-1
*>т |
Х-4 |
■ я
Рис. 86. Технологическая схема установки двухступенчатой деасфальтизации остаточных масел пропаном: / — сырье; // — пропан; /// — деасфальтизат первой ступени; IV — деасфальтнзат второй ступени; V — асфальт; VI — водяной пар; V// — вода.
направляется в середину экстракционной колонны II ступени К-2. В нижнюю часть колонны К-2 также поступает жидкий пропан. С верха колонны К-2 уходит раствор деасфальтизата II в пропане. Растворитель из растворов деасфальтизата I и II ступени регенерируется раздельно. Раствор деасфальтизата I ступени с верха колонны К-1 входит в испаритель Т-2, где часть пропана отпаривается. Далее раствор деасфальтизата первой ступени подо-
33Q
гревается в теплообменнике Т-5 и направляется в колонну К-5, где снова отпаривается часть пропана за счет снижения давления. С низа колонны К-5 раствор деасфальтизата I ступени поступает в колонну К-6, где окончательно отпаривается пропан водяным паром. С низа колонны К-6 деасфальтизат I ступени насосом Н-5 откачивается с установки через холодильник Х-4.
Раствор деасфальтизата II ступени с верха колонны К-2 отпаривается последовательно в двух испарителях с паровым пространством Т-3 и Т-4; окончательно пропан отпаривается водяным паром в колонне К-7, после чего охлаждается и откачивается с установки. Раствор асфальта II с низа колонны К-2 подается в печь П-1 и колонну К-4, где от него отделяется основная масса пропана. С низа колонны К-4 раствор асфальта II направляется на окончательную отпарку водяным паром в колонну К-3. С низа колонны К-3 асфальт II откачивается с установки насосом Н-4 через теплообменник Т-5 и холодильник Х-3.
Пары пропана под давлением 2,7 МПа из испарителей Т-2, Т-3 и колонны К-4 конденсируются в холодильнике Х-1 и собираются в емкости Е-1. Пары пропана под давлением 1,9 МПа из испарителя Т-4 и колонны К-5 конденсируются в холодильнике Х-2 и собираются в емкости Е-2, откуда насосом Н-3 пропан перекачивается в емкость Е-1. Газообразный пропан и водяные пары из колонн К-3, К-6 и К-7 подвергаются охлаждению в конденсаторе смешения К-8, орошаемом водой. Пропан с верха колонны К-8 поступает в компрессор ПК-1, сжимается до 1,9 МПа и поступает в систему жидкого пропана.
Дата добавления: 2018-04-04; просмотров: 3136; Мы поможем в написании вашей работы! |
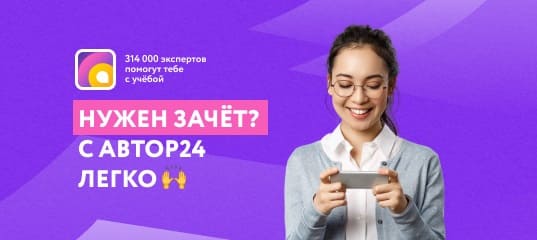
Мы поможем в написании ваших работ!