Одноступенчатый гидрокрекинг газойлей
Прямогонный вакуумный газойль, газойли каталитического крекинга и коксования подвергают гидрокрекингу с целью получения легких топливных фракций: бензина, реактивного и дизельного топлива. Процесс можно осуществлять как в одну, так и в две ступени. Установка одноступенчатого гидрокрекинга Л-16-1 работает на алюмокобальтмолибденовом катализаторе. Технологическая схема реакторного блока практически не отличается от схемы гидрбочистки дизельных топлив (см. рис. 70).
Технологический режим процесса
Температура, °С
на входе в реактор......................................... .... 400—410
в сепараторе С-1............................................ 50
Давление в реакторе, МПа................................... ........... 5
Объемная скорость, ч-1........................................ ........... 1
Кратность циркуляции водорода, м;'/м3 . . . 600
Содержание водорода в циркулирующем
газе на входе в реактор, % (об.)....................... .......... 75
Теплота реакции, кДж на 1 кг сырья . . . 130—250
* Процесс используют для получения сжиженных газов в странах, не располагающих собственными ресурсами природного газа. При этом можно также получать легкие изопарафины — исходное сырье для производства синтетического каучука. Другим направлением процесса может быть производство легкого высокооктанового компонента автомобильных бензинов с высоким содержанием изопарафиновых углеводородов.
275
Регенерация катализатора осуществляется по способу, описан
ному в § 55.
|
|
Материальный баланс. Материальный баланс одноступенчатого
процесса гидрокрекинга вакуумного газойля ромашкинскои нефти
без рециркуляции остатка гидрокрекинга приводится ниже
[в % (масс.)]:
Поступило:
Сырье»- вакуумный газойль . . . 100,0
Водородсодержащий газ 2,09
в том числе 100%-ный водород 0,82
Итого . . . 102,09
Получено:
Углеводородный газ . -2,89
Бензин 4,61
Дизельное топливо 42,83
Остаток гидрокрекинга 47,66
Сероводород 2,07
Отдуваемый водородсодержащий
газ 1,02
Потери 1,01
|
|
Итого . . . 102,09
Аппаратура. Реактор гидрокрекинга (рис. 71) представляет собой цилиндрический аппарат со сферическими днищами. Реактор имеет диаметр 2600 мм, выедту цилиндрической части 11000 мм. Стенка выполнена из* стали 12ХМ и имеет внутреннюю защитную футеровку из торкрет-бетона. Ввод газо-сырьевой смеси осуществляется через штуцер в верхнем днище со специальным распределительным устройством (рис. 72). Вывод продуктов реакции — через штуцер в нижнем днище, снабженный специальной сеткой для задержки катализатора.
Ввиду высокого теплового эффекта реакции необходимо вводить хладагент непосредственно в реактор. По этой причине катализатор не укладывается сплошным слоем, а располагается на 2—4 специальных решетках с промежутками между отдельными слоями. Под решетки через, специальные распределители вводится хладагент.
Установка Л-16-1 используется также для гидроочистки вакуумных газойлей как с целью облагораживания сырья каталитического крекинга, так и для получения малосернистых котельных топлив. При гидроочистке вакуумного газойля арланской нефти (фракция 300—480°С) с содержанием серы 2,83% (масс.) сера удаляется на 90% при парциальном давлении водорода 3,2—3,6 МПа, температуре 380—390 °С, объемной скорости 1 ч-1. При этом фракционный состав вакуумного газойля облегчается (количество фракций, выкипающих до 350 СС, возрастет на 10— 20%), т. е. имеют место реакции гидрокрекинга и меняется углеводородный состав за счет гидрирования полициклических ароматических углеводородов и смол.
|
|
276
Двухступенчатый процесс гидрокрекинга газойлей
При использовании в качестве сырья процесса гидрокрекинга
тяжелых газойлей деструктивной переработки нефти (замедлен
ное коксование, каталитический
riK—^n крекинг), а также прямогонного
^ТьСГл вакуумного газойля сотноситель-
цк^ч \ но ВЫСОким содержанием серы,
азота и полициклических ароматических углеводородов катализатор при работе в одну ступень быстро отравляется и теряет активность. Поэтому необходимо
Рис. 71. Реактор гидрокрекинга:
1 — штуцер для вывода газо-продукто-вой смеси; 2 — штуцер для ввода охлаждающего газа; Л—штуцер для ввода газо-сырьевой смеси; 4—штуцер для термопары; 5 —решетка; в —корпус; 7 —распределительная тарелка; 8—футеровка; 9 — катализатор; 10 — фарфоровые шары.
|
|
Рис. 72. Распределительное устройство для ввода ггзо-сырьевой
смеси: 7 —штуцер для термопары; 2—штуцер для ввода газо-сырьевой смеси; 3 — корпус реактора; 4 — конус; 5— перфорированная полусферическая крышка.
предварительно подготавливать сырье, т. е. проводить процесс в две ступени. На первой ступени используют азото- и сероустойчи-вый алюмокобальтмолибденовый катализатор, а на второй — более активные расщепляющие и изомеризующие катализаторы.
Отличительная черта второй ступени—возможность регулирования избирательности гидрокрекинга (получение преимущественно
277
бензина, реактивного или дизельного топлива) путем изменения температуры и объемной скорости подачи сырья. Как видно из рис. 73, при уменьшении объемной скорости с 4 до 0,5 ч-1 при 400 °С выход бензина повышается с 14 до 54%, а при повышении
4 2/ 0,5 Объемная, скорость, ч~1 Рис. 73. Влияние объемной скорости подачи сырья на выход фракции и. к. — 195 °С [в % (масс.) от гидро- генизата] при 400 и 425 °С. |
температуры (объемная скорость 425 с 1 ч"1) с 400 до 425 °С выход бензина увеличивается с 33 до 62 %. В табл. 14 приводятся свойства исходного сырья и получаемых продуктов при бензиновом варианте двухступенчатого гидрокрекинга вакуумного газойля. Широкая бензиновая фракция отвечает всем требованиям к автомобильному бензину сортов А-72 и А-76 и имеет высокую приемистость к ТЭС. Дизельное топливо соответствует всем требованиям к летнему дизельному топливу. При работе второй ступени с преимущественным получением дизельного топлива бензин имеет октановое число 68—70 по моторному методу. Остаток гидрокрекинга можно успешно использовать в качестве сырья каталитического крекинга или повторно возвращать в процесс.
ТАБЛИЦА 14
Свойства сырья и продуктов установки двухступенчатого гидрокрекинга вакуумного газойля (бензиновый вариант)
Показатели
Исходное
сырье
(фракция
350-500 °С)
Бензин
(фракция
н. к. —195 °С)
Дизельное ТОПЛИВО
(фракция 195-345 °С)
Остаток
(фракция
345-400 °С)
Плотность р^°.......................
Молекулярная масса . . .
Йодное число ................
Содержание серы, %
(масс.)................................
Содержание азота, %
(масс.)................................
Температура застывания,
°С........................................
Октановое число по моторному методу ((Ъз ТЭС)
Цетановое число , . . . .
0,920 330 12
2,1
0,1
30
0,720 120 1
0,01
Отсутствие
73-76
0,830 210 2
0,02
Следы
-10
50-55
0,900
0,04
Следы
35
Технологическая схема.Технологическая схема установки двухступенчатого гидрокрекинга приводится на рис. 74.
Сырье насосом Н-1 подается на смешение с циркулирующим водородсодержащим газом, нагнетаемым компрессором ПК-1 и свежим водородом, поступающим с выкида компрессора ПК-2.
278
Смесь нагревается последовательно в теплообменнике Т-1 и печи П-1 и входит в реактор Р-1 через верхний штуцер. Из нижнего штуцера реактора прореагировавший продукт (гидрогенизат первой ступени) в смеси с газом поступает в теплообменник Т-1, воздушный холодильник Х-1 и водяной холодильник Х-2, где охлаждается до температуры сепарации. В сепараторе С-1 гидрогени-
Рнс. 74. Технологическая схема установки двухступенчатого гидрокрекинга вакуумного газойля:
У —сырье; II — водородсодержащий газ риформинга; III — водородсодержащий газ на отдув; IV— сухой газ; V — сероводород; VI — жирный газ; VII — водородсодержащий газ с установки; VIII — бензин; IX — дизельное топливо; "X — остаток гидрокрекинга.
зат отделяется от циркулирующего газа, избыток которого отдувается из системы, а основное количество поступает на прием компрессора ПК-1 и возвращается на смешение с сырьем.
Гидрогенизат первой ступени с растворенными в нем углево
дородными газами, сероводородом и аммиаком подвергается четы
рехкратной стабилизации при понижении давления в сепараторах
С-2, С-3, С-4 и колонне К-5. Сухие и жирные газы, отделенные от
гидрогенизата, содержат сероводород и поэтому подвергаются
моноэтаноламиновой очистке в колоннах К-1, К-2, К-3. Сухой газ
и сероводород выводятся с установки, а жирные газы поступают
в блок газоразделения (на схеме отсутствует) для получения
фракции Сз—Q. ч
?79
С низа колонны К-5 гидрогенизат первой ступени забирается насосом Н-2, смешивается с циркулирующим водородсодержащим газом второй ступени и свежим водородом и подается в реакторный блок второй ступени. Схемы реакторного блока второй ступени и стабилизации гидрогенизата второй ступени не отличаются от схемы первой ступени. Стабилизированный гидрогенизат второй ступени подвергается разгонке на фракции в атмосферной колонне К-7 и вакуумной колонне К-9.
В отличие от установок гидроочистки и гидрокрекинга в одну ступень циркулирующий водородсодержащий газ не подвергается отмывке от сероводорода. Высокое давление сепарации в первой ступени способствует растворению сероводорода в гидрогенизате, благодаря чему содержание сероводорода в газе находится в допустимых пределах. Во второй ступени крекируется сырье, очищенное от серы, поэтому образование сероводорода незначительно. Промежуточное охлаждение для съема тепла реакции осуществляется подводом холодного циркуляционного газа в реакторы непосредственно между слоями катализатора. _
Технологический режим процесса Реакторный блок
I ступень II ступень III ступень
(бензиновый (дизельный
вариант) вариант)
Общее давление, МПа .... 15 15 15
Температура, "С.......................... ........... 425 425 400-415
Объемная скорость, ч-1 . . . 1 1 1—2
Кратность -циркуляции водо-
родсодержащего газа, м3/м3 1000 1000 1000
Отдельные аппараты
Температура, °С
в сепараторах С-1, С-5................................................................ 50
низа колонны К-5........................................................................ ..... 250
К-6...................................................................... ..... 135
К-7 ................................................................. . 240
К-9...................................................................... ..... 395
Давление, МПа
в сепараторах С-1, С-5........................................................................ 13
С-2, С-6..................................................................... 9
С-3, С-7.................................................................... 2
С-4 С-8.................................................................... ..... 0,2
в колоннах К-5, К-6.................................................................... ..... 0,15
Материальный баланс двухступенчатого гидрокрекинга [а % (масс.)]
I ступень II ступень II ступень
(бензиновый (дизельный
вариант) вариант)
Поступило:
Сырье.......................................... 100,0 100,0 100,0
Водород 100%-ный.................... 1,4 2,5 2,0 .
Итого . . . Ю1.4 102,5 Ю2.0
280
tl ступгнь | til ступень |
(бензиновый | (дизельный |
вариант) | вариант) |
91,4 | 93,2 |
19,0 | 10,0 |
36,0 | 22,0 |
27,4 | 51,0 |
9,0 | 10,2 |
10,0 | 7,7 |
0,2 | 0,2 |
0,5 | 0,4 |
3,0 | 2,7 |
6,3 | 4,4 |
0,1 | 0,1 . |
t ступень
Получено:
Гидрогенизат....................... ■ . . 92,3
фракция н. к. — 85 °С , . —
85-195 °С............................. ......... —
195-345 "С........................... ......... -
Остаток 345 °С — к. к............... ......... —
Углеводородный газ................... ......... 6,0
С,..................................................... 1,8
С2 ................................................ 1,8
С3 ........................................ ......... 1,2
С4 ..................................... ......... 1,2
Сероводород .............. ......... 2,5
Аммиак....................................... ......... 0,1 — —
Потери......................................... ......... 0,5 1,0 1,0 t
Итого . . . 101,4 102,5 102,0
Аппаратура.Реактор установки двухступенчатого гидрокрекинга в принципе такой же конструкции, что и для одноступенчатого процесса. Он имеет два слоя катализатора и диаметр 3,4 м. В каждом реакторном блоке два параллельно работающих реактора. Центробежные сырьевые насосы реакторных блоков создают напор 1700 м столба жидкости.
§ 57. ГИДРООЧИСТКА И ГИДРОКРЕКИНГ ОСТАТКОВ
Увеличение общего объема переработки нефти и вместе с тем рост доли высокосмолистых и высокосернистых нефтей выдвигает проблемы переработки значительного количества тяжелых остатков, в основном мазутов и гудронов. Вопросы гидрокрекинга этих остатков находятся в центре внимания нефтепереработчиков, поскольку загрязнение атмосферы становится все более острой социальной проблемой и она может быть решена только при условии создания процессов получения котельных топлив, содержащих не более 0,3—1,0% (масс.) серы. Хотя такие процессы уже применяются в опытно-промышленных масштабах, основная задача — задача предотвращения быстрой дезактивации катализаторов — не решена. Особое затруднение представляет в этом смысле высокое содержание металлов в нефтяных остатках. Отлагающиеся на катализаторе частицы затрудняют регенерацию, а частая замена отработанного катализатора свежим удорожает процесс. Дезактивация катализатора усиливается еще и наличием большого количества смолисто-асфальтеновых веществ в гудронах и мазутах.
Процесс гидрокрекинга остатков имеет в настоящее время два направления: 1) гидрообессеривание мазутов с целью получения маловязкого и малосернистого котельного топлива или сырья для каталитического крекинга; 2) углубленный гидрокрекинг с целью получения дополнительных ресурсов моторных топлив.
281
Для получения малосернистых котельных топлив из мазутов в настоящее время применяется несколько способов; два способа получили название косвенной гидроочистки.
В первом случае от мазута отгоняется около 60% вакуумного газойля, подвергаемого гидроочистке на стационарном катализаторе. Гидроочищенныи продукт смешивается с неочищенным остатком. Содержание серы этим методом не удается понизить более, чем на 40—45%, поэтому он пригоден лишь для малосернистых мазутов.
Во втором случае, так же как и в первом, от мазута отгоняется вакуумный газойль и гидроочищается. Гудрон подвергается коксованию, а коксовый дистиллят гидроочищается. Этот способ дает высокосернистый кокс, не имеющий применения.
В третьем и четвертом способах предусмотрена прямая гидроочистка или гидрокрекинг на стационарных или движущихся катализаторах.
Процесс гидрообессеривания мазутов протекает в сравнительно мягких условиях на стационарном катализаторе. Предварительно мазут можно подвергать деасфальтизации — удалению смолисто-асфальтеновых веществ. Технологическая схема процесса, его аппаратурное оформление ничем не отличаются от двухступенчатой установки гидрокрекинга вакуумного газойля (см. §56).
В зависимости от качества сырья параметры процесса варьируют в следующих пределах:
Температура, °С.................................................. 315—426
Давление, МПа.................................................... 4,2—20
Объемная скорость, ч-1 ................................ .... 1,0—4,6
Кратность циркуляции водорода, м3/м3 . . 700 —1000
В результате сера удаляется на 80%, металлы — на 60—70%, на 60% снижается коксуемость, падает содержание азота и вязкость. Кроме того, образуется небольшое количество газа и бензина.
Кроме установок со стационарным катализатором разработаны также установки с кипящим слоем катализатора, на которых можно перерабатывать более разнообразное остаточное сырье: мазуты, гудроны, тяжелые газойли коксования и каталитического крекинга, смолистые нефти.
В Советском Союзе разработан процесс гидрокрекинга в трехфазном кипящем слое, где твердая фаза представлена мелкосферическим алюмокобальтмолибденовым катализатором, жидкая фаза — смесью еще непрореагировавшего сырья с уже образовавшимися низколетучими продуктами, а газовая фаза — смесь водорода, сероводорода, аммиака и паров углеводородов. На этой установке можно перерабатывать даже такое тяжелое остаточное сырье, как гудроны ромашкинской и арланской нефти, с получением дизельного и котельного топлива. Спад активности катализатора полностью устраняется его регулярным обновлением без изменения и нарушения технологического режима. Ниже приво-
282
дится характеристика гудронов ромашкинской (I) и арланскрй (II) нефти:
Плотность р|°................................................................ 1,014 1,001
Фракционный состав, % (масс.).................................. ..... 406 293
перегоняется до 350 °С........................................ 0 2
перегоняется до500°С.......................................... 15 28
Молекулярная масса.................................................... 820 670
Коксуемость, % (масс.)............................................... ..... 18,52 16,2
Содержание серы, % (масс.).................................... 3,08 4,00
Содержание ванадия, г/т ....................................... 216 250
При расходе водорода от 1,1 до 1,4% (масс), температуре 400°С, давлении 10 МПа, скорости подачи сырья 0,6 ч-1 и кратности циркуляции водородсодержащего газа 1000 м3/м3 можно получить из этих гудронов продукты соответственно I и II следующего
состава, в % (масс.):
I и
Углеводородные газы............................................................. 3,7 5,6
Бензин н. к.-180°С................................................................ 3,5 5,08
Дизельное топливо.................................................................. ..... 19,2- 24,5
Остаток (фракция выше 350 °С)............................................ ...... 71,2 61,8
Дизельное топливо имеет цетановое число 39—42, температуру застывания порядка —22 °С, содержание серы 0,2—0,3% (масс).
Котельное топливо при гидрокрекинге гудрона ромашкинской нефти соответствует марке М-200, содержит 0,88% (масс.) серы, и 67 г/т ванадия; при гидрокрекинге гудрона арланской нефти — соответствует марке М-100, содержит 1,3% (масс.) серы. В зимний период более целесообразно вместо дизельного и котельного топлива выпускать легкое котельное топливо марки М-40 [выход 90,4—86,3% (масс); содержание серы 0,7—1,0% (масс.)].
Производство водорода. Широкое развитие гидрогенизацион-ных процессов переработки нефти невозможно без достаточных ресурсов водорода. Основное количество водорода на нефтеперерабатывающих заводах получается в процессе каталитического риформинга. Однако при производстве малосернистых продуктов из сернистых и высокосернистых нефтей, а также при гидрокрекинге нефтепродуктов в больших объемах потребность в водороде не.может быть удовлетворена только за счет платформинга. Дополнительно водород может быть получен двояким путем.
Во-первых, водород может быть выделен из метано-водород-ной фракции установок газоразделения, отдувочных газов установок гидроочистки и гидрокрекинга. Содержание водорода в этих газах колеблется от 30 до 60% (об.). Наиболее перспективные методы получения водорода с концентрацией 96—99% (об.) —низкотемпературное фракционирование, адсорбция на молекулярных ситах, абсорбция нефтяными фракциями.
Во-вторых, водород можно получать специальными методами: каталитической конверсией углеводородных газов с водяным паром, термическим разложением углеводородных газов, газификацией тяжелого углеводородного сырья.
Глава VIII ПЕРЕРАБОТКА НЕФТЯНЫХ ГАЗОВ
§ 58. ХАРАКТЕРИСТИКА НЕФТЯНЫХ ГАЗОВ. ОЧИСТКА И ОСУШКА ГАЗОВ
В зависимости от происхождения нефтяные газы делятся на природные, попутные и искусственные.
Природные газы добываются из самостоятельных месторождений, попутные — совместно с нефтью. Характеристика природных и попутных газов приведена в § 4.
ТАБЛИЦА 16
Состав углеводородных газов различных процессов переработки нефти [в % (масс.)]
| Каталити- | UJ | «С | ||||||||||
| Коксование | Каталитиче- | ( | ческий | * | 5 | |||||||
| рмическин кре-нг мазута под влением | ский к | рекмнг | о к s m я m 0.0 35 Ло Ч OJ£> | рифо | )МИНГ | дрокрекннг тя го газойля | I | |||||
Компоненты | медленное | X к в х «и а о | нэиновый 5ычный) жим | зовый есткнй) жим | ычный жим | - * | дроочнстка зельных 4 P | ||||||
| щ а я | я | к | <и a v | я Я " | я о а | to <и | а <и | I О | я я | |||
| няч | m | и и | oSa | [.ia | С»с | О Q. | * a | U Ч | и < | |||
н2+со2................ | 0,2 | 0,4 | 1,5 | 2,5 | 1,0 | 16,0 | 8,5 | 6,5 | |||||
сн4 .... | 16,0 | -32,5 | 26,5 | 11,0 | 9,5 | 34,4 | 5,0 | 12,5 | 27,0 | 34,0 | |||
С2Н4 ■ ■ | 2,5 | 4,5 | 12,5 | 6,0 | 4,0 | 29,3 | — | — | — | — | |||
СгНв • ■ | 17,0 | 21,5 | 20,0 | 8,0 | 5,0 | 6,0 | 9,5 | 24,5 | 21,0 | 24,5 | |||
С3Нв . . | 9,0 | 4,0 | 12,5 | 22,0 | 24,0 | 10,5 | — | — | — | — | |||
С3Н8 . . | 21,5 | 15,0 | 11,0 | 12,5 | 9,5 | 0,2 | 38,0 | 32,0 | 41,0 | 20,5 | |||
иао-С4На | 4,5 | 2.2 | 5,0 | 6,0 | 10,5 | 1.3 | — | — | — | — | |||
H-CiiHg | 9,8 | 4,4 | 5,0 | 14,0 | 15,0 | 1,2 | — | — | — | — | |||
uao-CiHio | 5,0 | 7,0 | 0,7 | . 14,0 | 16,5 | — | 19,0 | 11,0 | } п,о | ) 21,0 | |||
К-С4Н10 . | 14,5 | 8,5 | 4,6 | 4,0 | 4,0 | 0,5 | 20,0 | 14,5 | |||||
С4Н6 ■ . | — | — | 0,7 | — | 1,0 | 1,5 | — | — | — | — | |||
Сумма непредель- | |||||||||||||
| 25,8 | 15,1 | 35,7 | 48,0 | 53,5 | 43,8 | — | — | — . | — | |||
Выход газа, % | |||||||||||||
(масс.) на | с | ыр | ье | 7 | 7 | 12 | 17 | 30 | 77 | 12 | 23 | 1,8 | 0,8 |
Искусственные газы образуются при переработке нефти каталитическими и термическими методами. Составы газов, получаемых при различных процессах (табл. 15), очень заметно отличаются. Газы термических процессов и каталитического крекинга
284
в значительном количестве содержат непредельные углеводороды, а в газах каталитического риформинга, гидроочистки, гидрокрекинга их вообще нет.
ГТТаправление использования газа зависит от его состава. Газ каталитического крекинга, богатый бутиленами и изобутаном, — наилучший вид сырья для установок каталитического алкилиро-вания. Из газов риформинга выделяют водород, точнее — водо-родсодержащий газ с концентрацией водорода 75—90% (об.). Водородсодержащий газ используется для нужд гидрогенизацион-ных процессов: гидроочистки и гидрокрекинга.
На многих современных технологических установках имеются блоки первичной обработки газа. На этих блоках проводится очистка газа от сероводорода, а также выделение из газа углеводородов С3 и С4 в виде жидкой углеводородной фракции — «головки стабилизации».
Однако разделение газа на отдельные индивидуальные углеводороды и узкие углеводородные фракции осуществляется на специально сооружаемых газофракционирующих установках (ГФУ). На нефтеперерабатывающем заводе обычно имеется не менее двух ГФУ, одна из которых предназначена для переработки предельных углеводородов, другая — непредельных.
При переработке предельных углеводородов получаются следующие продукты, которые используются для различных целей:
1) этановая фракция — сырье пиролиза, хладагент на установках депарафинизации масел и др.;
2) пропановая фракция — сырье пиролиза, хладагент для многих технологических установок, бытовой сжиженный газ;
3) изобутановая фракция — сырье для производства синтетического каучука (изопренового и бутилкаучука), используется на установках алкилирования;. .
У?0бутановая фракция — сырье для получения бутадиена в производстве синтетического каучука, сырье пиролиза и компонент сжиженного бытового газа, добавка к автомобильному бензину для придания ему требуемого давления паров;
5) изопентановая фракция — сырье для производства изопренового каучука, компонент в высокооктановых сортах бензинов;
6) пентановая фракция — сырье для процессов изомеризации и пиролиза, в производстве амилового спирта.
На ГФУ непредельных углеводородов из олефинсодержащих потоков выделяются следующие фракции:
1) пропан-пропиленовая — сырье для производства полимер-бензина, фенола и ацетона, синтетических моющих средств, бутиловых спиртов, может быть использована как сырье установок алкилирования;
2) бутан-бутиленовая — сырье установок алкилирования и полимеризации, присадки к маслам, в производстве синтетических каучуков.
Качество сжиженных газов определяется соответствующими техническими условиями.
V
Очистка и осушка газов предшествуют их фракционированию и дальнейшей переработке.
Очистка газов. Нефтезаводские газы, полученные при переработке сернистых нефтей, всегда содержат сероводород и некоторые другие сернистые соединения. Особенно много сероводорода в газах установок, перерабатывающих тяжелое сырье: мазут, вакуумные дистилляты, гудрон. Например, в газе каталитического крекинга вакуумного дистиллята арланской нефти содержится 13—15% сероводорода, а в газах термического крекинга полугудрона этой же нефти до 18% сероводорода.
Сероводород ухудшает работу катализаторов тех каталитических процессов, которые используют в качестве сырья сжиженные газы, его присутствие совершенно недопустимо в бытовом сжиженном газе. Наличие активных сернистых соединений вредно влияет на оборудование газоперерабатывающих установок, вызывает активную коррозию аппаратов и трубопроводов.
Поэтому углеводородные газы, содержащие сероводород и такие активные сернистые соединения, как низшие меркаптаны, перед подачей на ГФУ подвергают очистке. В некоторых случаях газы нефтепереработки очищают также от окиси и двуокиси углерода.
При очистке газа от сероводорода чаще всего используется процесс абсорбции. Абсорбентами для избирательного извлечения сероводорода из газов служат растворы трикалийфосфата, фенолята натрия, этаноламинов.
Наиболее распространена на НПЗ очистка при помощи раствора моноэтаноламина (МЭА).
От сероводорода очищаются не только газы, направляемые на ГФУ, но и товарные сжиженные углеводородные фракции. Очист'-ка товарных фракций проводится с применением щелочи или регенерируемых реагентов — трикалийфосфата, моноэтаноламина и др.
Осушка газа. Осушка необходима в тех случаях, когда газ направляется для каталитической переработки с использованием чувствительного к воде катализатора или когда фракционирование и дальнейшая переработка газа проводятся при низких температурах. Если неосушенный газ охлаждать до температур ниже 0°С, это может привести к забиванию льдом аппаратуры и трубопроводов.
Следует также принимать во внимание способность углеводородов и некоторых других газов образовывать с водой кристаллогидраты, которые представляют собой нестойкие комплексные соединения молекул газа и воды. Известны кристаллогидраты этана С2Н6:7Н20, пропана С3Н8-18Н20 и др. Сероводород с водой также образует гидрат НэЗ-бНгО. Кристаллогидраты появляются в трубопроводах и аппаратах при температурах ниже 15 °С и имеют вид серой, похожей на лед, массы.
Чем меньше молекулярная масса углеводорода, тем выше температура и давление, при которых он способен образовывать кри-
286
сталлогидраты. Метан, например, образует гидрат при 12,5 °С й 10,0 МПа, а этан при этой же температуре образует гидрат уже при 2,5 МПа. Гидраты существуют только в том случае, если парциальное давление паров воды в газовой фазе выше давления паров гидрата. Поэтому при осушке газов снижают содержание влаги в них настолько, чтобы парциальное давление водяного пара стало ниже, чем давление насыщенных паров гидратов. Показателем влагосодержания газов на практике является так называемая точка росы. При охлаждении газа ниже температуры точки росы водяной пар, содержащийся в газах, конденсируется, выпадает в виде «росы».
При осушке газа применяют твердые и жидкие поглотители воды, которые должны отвечать следующим требованиям: высокая влагоемкость, т. е. способность поглощать возможно больше влаги на единицу массы или объема поглотителя; хорошая реге-нерируемость; большой срок службы; невысокая стоимость и простота получения. Наилучшим сочетанием этих качеств из числа твердых поглотителей обладают активированная окись алюминия, силикагель, синтетические цеолиты (молекулярные сита), а из жидких — ди- и триэтиленгликоли.
Жидкостная осушка на НПЗ проводится, как правило, диэти-ленгликолем (ДЭГ). Точка росы при осушке ДЭГ может быть снижена до — 20 °С.
С помощью твердых осушителей глубина осушки заметно повышается. Например, активная окись алюминия осушает газ до точки росы — 70 °С. Цеолиты понижают содержание влаги в газе до 0,001% и точку росы до температуры ниже —75 °С.
При использовании для осушки нефтезаводских газов активных адсорбентов необходимо иметь в виду, что адсорбенты могут способствовать полимеризации содержащихся в газе непредельных углеводородов. Особенно склонны к полимеризаций газы пиролиза.
§ 59, РАЗДЕЛЕНИЕ ГАЗОВ
Способы разделения газовых смесей. Для разделения смеси газов на индивидуальные компоненты или пригодные для дальнейшей переработки технические фракции применяются следующие процессы: конденсация, компрессия, абсорбция, ректификация, адсорбция. На ГФУ эти процессы комбинируются в различ-, ных сочетаниях.
Конденсация — первая стадия разделения газов. С помощью конденсации газ превращается в двухфазную систему жидкость — газ, которую затем механически разделяют на газ и жидкость. В качестве хладагента при конденсации прежде всего используют воду или воздух. В этом случае температура конденсации составляет 35-г40°С. Чтобы увеличить число конденсирующихся компонентов, необходимо понизить температуру конденсации, используя в качестве хладагента испаряющийся аммиак, фреон или углеводородные газы — пропан и этан. При
287
использовании ё качестве хладагента пропана и аммиака температуру конденсации можно понизить до — 40 °С, при использовании этана до — 80 °С.
Компрессия, применяется в схемах разделения газов совместно с конденсацией. При повышении давления газов создаются наиболее благоприятные условия конденсации углеводородов. Из скомпримированного (сжатого) газа в первую очередь конденсируются наиболее тяжелые компоненты.
Абсорбция — это процесс поглощения отдельных компонентов газа жидкостью (абсорбентом), вступающей с ним в контакт. Эффективность абсорбции зависит от температуры, давления, при котором проводится процесс,' физико-химических свойств газа и применяемого абсорбента, скорости движения абсорбируемого ( газа, количества подаваемого абсорбента.
Определенный газовый компонент абсорбируется тогда, когда парциальное давление этого компонента в газовой фазе превышает его парциальное давление в парах, равновесных с жидкостью, являющейся абсорбентом и вступающей в контакт с газом. Следовательно, интенсивность, с которой будет поглощаться абсорбентом извлекаемый из газа компонент пропорциональна разности этих парциальных давлений. Кроме того, количество поглощенного компонента пропорционально времени и поверхности контакта жидкой и газовой фаз.
Влияние давления на процесс абсорбции определяется законом Генри. Согласно этому закону растворимость газа в жидкости пропорциональна его парциальному давлению в парах над жидкостью. Если, не изменяя температуры, повысить давление над раствором, то в жидкость перейдут новые количества газа. Увеличение давления способствует абсорбции.
При повышении температуры растворимость газа в жидкости уменьшается, абсорбция замедляется и может совсем прекратиться. На технологичео«№ установках при извлечении из газа про-» пана и бутана, поддерживается температура не выше 35 °С. с" Выбор абсорбента зависит от свойств абсорбируемого газа. Углеводородные газы наилучшим образом извлекаются близкими им по строению и молекулярной массе жидкими углеводородами легкого бензина.'; Поскольку легкий абсорбент обладает высокой упругостью паров, он в значительной степени увлекается уходящим из абсорбера газом. СОбычно на абсорбционных установках применяют двухступенчатую абсорбцию: основным абсорбентом служит бензиновая фракция, а затем выходящий из абсорбера газ промывается жидкостью тяжелого фракционного состава, например керосино-газойлевой фракцией, для извлечения из газа унесенного бензина. >
Поглощение газа жидкостью сопровождается выделением тепла. Чтобы при этом не ухудшались условия абсорбции, на технологических установках применяют ряд специальных приемов. Одним из эффективных способов повышения степени извлечения целевых компонентов является охлаждение абсорбента и газа перед пода-
288
чей их в абсорбер до температуры ниже рабочей. Съем тепла абсорбции осуществляется в промежуточных выносных холодильниках. Насыщенный абсорбент, взятый с вышележащей тарелки, пропускается самотеком или прокачивается насосом через холодильники, а затем возвращается на нижележащую тарелку. Для охлаждения сырья и циркулирующего абсорбента применяют не только воду, но и искусственные хладагенты: пропан, аммиак.
Поглощенный при абсорбции газ отделяется от абсорбента в отпарной колонне-десорбере. Для десорбции необходимы условия, противоположные тем, при которых следует проводить абсорбцию, т. е. повышенная температура и низкое давление. I Адсорбционный метод разделения газов мало распространен в промышленности. Он основан на способности некоторых твердых веществ с развитой поверхностью (активированного угля, силикагеля и др.) избирательно поглощать различные компоненты газа. Подобно жидким поглотителям (абсорбентам) твердые адсорбенты более интенсивно поглощают тяжелые углеводороды. Подобрав определенный режим адсорбции, можно получить достаточно сухой газ. Адсорбцию применяют для извлечения целевых компонентов из смесей, в которых содержание извлекаемых углеводородов не превышает 50 мг/м3, а также из газов, содержащих воздух.
^ Ректификация является завершающей стадией разделения газовых смесей. Она применяется для получения индивидуальных углеводородов высокой чистоты. Поскольку разделение на компоненты смеси газов проводить затруднительно, при существующих схемах газоразделения на ректификацию подают жидкость, выделенную из газа конденсационно-компрессионным или абсорбционным методом. Особенность ректификации сжиженных газов по сравнению с ректификацией нефтяных фракций — необходимость разделения очень близких по температуре кипения продуктов и получения товарных продуктов высокой счепени чистоты. Ректификация сжиженных газов отличается также повышенным давлением в колоннах, поскольку для создания орошения необходимо сконденсировать верхние продукты ректификационных колонн в обычных воздушных и водяных холодильниках, не прибегая к искусственному холоду.i Чтобы сконденсировать, например, изобутан при 40 СС, надо поддерживать давление в рефлюксной емкости бутано-вой колонны и, следовательно, в самой колонне не ниже 0,52 МПа.
Схема ректификационной установки и последовательность выделения отдельных компонентов зависят от состава исходной смеси, требуемой чистоты продуктов и количества получаемых фракций.
Газофракционирующие установки.Установки разделения газов (ГФУ) подразделяются по типу перерабатываемого сырья—на установки предельных и непредельных газов и по типу применяемой схемы извлечения целевых компонентов из газов—на установки конденсационно-компрессионные и абсорбционные. Как на установках конденсационно-компрессионного типа, так и па установках абсорбционного типа извлеченная из газа жидкая смесь
Ю Зак, 380
289
X
|
|
|
|
|
Рис. 75. Технологическая схема газофракционирующей установки кон
/ — газ установок первичной переработки нефтк; II — головка стабилизации устано
ции каталитического риформинга; IV— пропановая фракция; У-*-изобутановая фра
VIII — пентановая фракция; IX — газовый бензин (С« и в
углеводородов затем разделяется на фракции или индивидуальные углеводороды с применением ректификации.
В качестве примера приводится описание технологической схемы установки конденсационно-компрессионного типа для переработки предельных углеводородов и установки абсорбционного типа для переработки газов каталитического крекинга.
На установку предельных газов (рис. 75) поступает газ с AT и АВТ, головки стабилизации каталитического риформинга и первичной перегонки. Установка состоит из блоков компрессии и ректификации.
Прямогонный газ через сепаратор С-1 подается на сжатие компрессором ЦК-1- При сжатии газ нагревается до 120 °С. Сжатый газ затем конденсируется в водяном конденсаторе-холодильнике ХК-1 и в конденсаторе-холодильнике Х1(-2, охлаждаемом испаряющимся аммиаком. В ХК-1 охлаждение и конденсация заканчивается при 50 °С, а в ХК-2— при 4 °С. После каждой ступени конденсации газожидкостная смесь разделяется на газ и жидкость в сепараторах С-2 и С-3. Газовые конденсаты из сепараторов С-1, С-2 и С-3 совместно с головками стабилизации установок первичной перегонки^ риформинга подаются на блок ректификации./
\|В блоке ректификации из углеводородного сырья сначала удаляются метан и этан. Удаление происходит в ректификационной колонне, которая называется деэтанизатором. Верхний продукт этой колонны — метан и этан, нижний —деэтанизированная фракция. Верхний продукт деэтанизатора охлаждается искусственным хладагентом — аммиаком.
Деэтанизированная фракция из колонны К-1 поступает в депро-панизатор К-2, верхним продуктом которого является пропановая фракция, а нижним — д«пропанизированная фракция. Верхний продукт после конденсации в воздушном конденсаторе-холодильнике ХК-4 и охлаждения в концевом холодильнике выводится с установки, предварительно пройдя щелочную очистку. Нижний продукт из депропанизатора К-2 подается в дебутанизатор К-3.
Ректификатом колонны К-3 является смесь бутана и изобутана, а остатком — дебутанизированный легкий бензин. Ректификат конденсируется в конденсаторе-холодильнике ХК-5, а затем подается на разделение в бутановую колонну К-4. Остаток из колонны К-3 переходит в депентанизатор К-5.
Бутановая колонна служит для разделения смеси бутанов на нормальный бутан и изобутан, а колонна К-5 (депентанизатор) — для отделения от газового бензина пентанов, которые подаются на ректификацию в колонну К~6. Нижний продукт депентанизатора— фракция Се и выше выводится с установки.
5 /„Установка, схема которой приведена на рис. 76, предназначена "для стабилизации бензина каталитического крекинга, очистки газа каталитического крекинга от сероводорода, извлечения из газа углеводородов С3—С4, разделения смеси этих углеводородов на пропан-пропиленовую и бутан-бутиленовую фракции,
10* '■' 291
|
|
|
|
|
|
х |
т
, .Лр)
&
%
Sd
0
-й
Рис. /6. Технологическая схема газофракционирующей устано
I— жирный газ; II — свежий раствор МЭА; III — сероводород; IV — сухой газ; V
VH — стабильный бензин; VIII — пропан-пр
Жирный газ с установки каталитического крекинга поступает на очистку моноэтаноламином в абсорбер K-I- Очищенный газ сжимается компрессором ПК-1 до 1,4 МПа, охлаждается и подается во фракционирующий абсорбер К-2, под 22-го тарелку. На эту же тарелку, но выше ввода газа подается конденсат компрессии.
Во фракционирующий абсорбер вводится также нестабильный бензин, являющийся основным абсорбентом.
Фракционирующий абсорбер, иначе называемый абсорбер-де-сорбером, отличается от обычного абсорбера тем, что представляет собой комбинированную колонну. В верхней части фракционирующего абсорбера происходит абсорбция, т. е. извлечение из газа целевых компонентов, а в нижней — регенерация абсорбента за счет подводимого тепла. Стекая сверху вниз по тарелкам фракционирующего абсорбера, насыщенный тяжелыми компонентами абсорбент встречается со все более горячими парами, десорбирован-ными из жидкости, .которая стекает в нижнюю часть колонны. С верха фракционирующего абсорбера уходит сухой газ, содержащий углеводороды Q—С2, а с низа вместе с тощим абсорбентом выводятся углеводороды С3—С4. В отличие от обычных абсорберов, куда питание подается только в газовой фазе, во фракционирующие абсорберы оно вводится и в виде жидкости, и в виде газа.
Для доабсорбции унесенных с сухим газом бензиновых фракций в верхнюю часть К-2 подается стабильный бензин. Температура в абсорбционной части поддерживается промежуточным охлаждением абсорбента. Насыщенный и деэтанизированный абсорбент из К-2 подается в стабилизатор К-3, верхним продуктом которого является головка стабилизации, а нижним — стабильный бензин. Головка стабилизации поступает на блок очистки, где очищается от сернистых соединений раствором МЭА и щелочью. Затем из очищенной головки в пропановой колонне К-4 выделяется пропан-про-пиленовая фракция. Остаток пропановой колонны п бутановой колонне К-5 разделяется на бутан-бутиленовую фракцию и остаток, который объединяется со стабильным бе.нзином.
§ 60. МЕХАНИЗМ ПРОЦЕССА АЛКИЛИРОВАНИЯ ИЗОБУТАНА ОЛЕФИНАМИ
Реакция присоединения олефинов к парафиновым углеводородам получила название алкилирование парафиновых углеводородов:
CnH2ra + 2 + CmH2m -------- *■ Сп+щНг (п+т)+2 + Q
Подбирая соответствующие .исходные углеводороды, можно получить в одну стадию любой парафиновый углеводород. На практике таким путем производят применяемый в качестве компонента моторного топлива алкилат — смесь высокооктановых изопарафи-новых углеводородов.
Алкилированию можно подвергать углеводороды как низкой, так и высокой молекулярной массы. Но для получения компонентов бензина практическое значение имеет только реакция углеводородов Сг—Сб. Из парафиновых углеводородов метан и этан в
293
реакцию не вступают. Легко алкилируется изобутан, обладающий подвижным водородом при третичном углеродном атоме. Кроме того, разветвленная структура изобутана предопределяет наиболее выгодное с антидетонационной точки зрения строение продуктов синтеза. Поэтому во всех промышленных процессах алкилирования исходным парафиновым сырьем является изобутан. Из олефино-вых углеводородов для алкилирования изобутана следует применять углеводороды Сз—С5.
Алкилирование протекает с выделением тепла и уменьшением объема. Следовательно, исходя из принципа Ле-Шателье, этой реакции благоприятствуют низкие температуры и высокие давления. Наиболее целесообразно проводить алкилирование при температурах близких к 0°С; при этом чем выше молекулярная масса оле-фина, тем ниже должна быть температура. В отсутствие катализаторов реакция алкилирования при низких температурах, однако, практически не идет.
Широкое промышленное распространение поэтому получило каталитическое алкилирование. Лучшими для этой реакции оказались кислотные комплексообразующие катализаторы: хлористый алюминий, промотированный хлористым водородом, серная кислота, жидкий фтористый водород. В настоящее время в СССР при-. меняется серная кислота, в США — серная кислота и жидкий фтористый водород.
Механизм каталитического алкилирования очень сложен. Так, в результате взаимодействия одного изопарафинового и одного олефинового углеводородов образуется не один изопарафиновый углеводород более высокой молекулярной массы, а иногда до двух десятков углеводородов. Так, при анализе алкилата, полученного при сернокислотном алкилиройании изобутана смесью бутиленов нормального строения, обнаружены углеводороды С6—С9 самого разнообразного строения. Исходя из обычного механизма реакции при некаталитическом алкилировании
СН3
i I .£
it г --- *" CH;j- С---- СН-- СН2--- СНз
_____________ ! Т i
| ф у СНз СНз
(СНз)зСН + СНз—СН2—СН=СН2 —
\........................... ,..,t...... t , СНз
1 п -yj> СНз—С—СН2—СН2—СН2—СНз
сн3
следовало бы ожидать преимущественного образования (по правилу Марковникова) 2,2,3-триметилпентана (I). Однако его получилось лишь 1,2%.
Согласно ионному механизму, реакция алкилирования протекает по стадиям с участием ионов карбония. Разберем ее на том же примере сернокислотного алкилирования изобутана а-бутиле-ном,
294
На первой стадии олефин реагирует с катализатором, который отдает свой протон:
СН3—СН2—СН=СН, + H2S04 —у СН3—СН2—СН—СН3 + HSOJ
Казалось бы, что затем следует ожидать развития реакции полимеризации. Но в условиях промышленного процесса (низкая температура, многократный избыток изобутана) полимеризация в значительной мере подавляется. Далее в синтез вовлекается изо-бутан:
СНз СНз
I + I.
СНз—СН + СНз—СН2—СН—СНз —-> СНз—С+ + С4Н10
I I
СНз СНз
С участием третичного иона карбония развивается дальше реакция присоединения непредельного углеводорода.
Вторая стадия — наращивание цепи с образованием нового иона карбония:
СНз СН3
1+ I
СНз—С + СН3—СН2—СН=СН2 —у СНз—С—СН2—СН—СН2—СНз
I I
СНз СНз
Третья стадия особенно осложнена различными превращениями. Во-первых, происходит миграция водорода и местоположение заряда меняется:
СНз СНз
I I +
СНз—С—СНг—СН—СНг—СНз —> СНз—С—СН—СН2—СН2—СНз
i ■ i
СНз • СН3
Легче всего водород переходит от группы —СН2—, труднее —
от группы /СН— и совсем не переходит от метильной группы
-СН3.
Во-вторых, с большой скоростью протекает скелетная изомеризация — перескок метильной группы к углероду, несущему заряд:
СНз
I + СНз—С—СН—СН2—СН—СНз —► СНз—С—СН—СН,—СНо—СНз
I " II""
СН3 СНз СНз
Перемещение метильной группы наиболее вероятно от четвертичного углеродного атома, но возможно и от третичного.
295
Все образующиеся на этой стадии изооктил-ионы в конечном итоге реагируют с изобутаном, отнимая водород от третичного атома углерода, например:
СН3 СН3
СН3—С—СН2—СН—СН2—СН3 -\- НС—СН3 —>
I I
СНз СН3
СН3 СНз
I U
—> СН3—С—СН2—СН,—СН2—СНз+СНз—С
I " I
СНз СНз
На этой стадии образуется конечный продукт реакции, вновь возникает активный третичный ион карбония, и реакция продолжается с новыми молекулами исходного олефина.
С учетом всех перегруппировок, происходивших в третьей стадии, получается смесь диметилгексанов.
При алкилировании изобутана (З-бутиленом и изобутиленом на основании описанного механизма в алкилате накапливаются главным образом триметилпентаны: 2,2,3-; 2,2,4-; 2,3,3-; 2,3,4-. Эти же углеводороды накапливаются и при алкилировании изобутана а-бутиленом. В рассмотренном выше механизме это не находит объяснения. Вероятнее всего под влиянием кислотного катализатора а-бутилен изомеризуется в р-бутилсн, так как миграция двойной связи весьма характерна в присутствии этого типа катализаторов.
Водородный обмен между катализатором и реагирующими углеводородами был доказан с помощью меченых атомов. Применялась серная кислота с тритием вместо водорода и тритий был обнаружен в алкилате.
Сложность состава алкилатов объясняется не только изомеризацией карбоний-ионов. В условиях алкнлирования протекают различные побочные процессы: а) деструктивное алкилирование, б) перераспределение водорода, в) полимеризация и деполимеризация.
Деструктивным алкилированием называются реакции распада и синтеза — распада получившихся изопарафиновых углеводородов на новые углеводороды, которые в свою очередь вступают в реакцию алкилирования с изобутаном, например:
изо-С4Н10 + С4Н8 —► ^ СаН18
CgHls -- > С4Н12 + С3Нб
изо-С4Ню + С3Н6 —> 23 C7Hi6 и т.д.
Перераспределение водорода проявляется в частичном дегидрировании изобутана до изобутилена. Образующийся изобутилен ал-килирует изобутан с образованием изооктана. Так, при алкилиро-
386
вании изобутана пропиленом наряду с изогептанами образуются изооктаны:
МЭ0-С4НЮ —> изо-С^На + Н2 СзН6 + Н2 —v С;|Н8 изо-С.;Н10 + U30-C4H8 —> изо-СаН18
Суммарно можно записать:
2иэо-С4Н10 + С3Н6 —> цзо-СаН18 + С3Н8
Такой тип превращений назван автоалкилированием. Это направление нежелательно, так как ведет к перерасходу изобутана. Полимеризация олефинового компонента в этом процессе — также нежелательная побочная реакция. Продукты полимеризации растворяются в серной кислоте и понижают ее концентрацию. Для предотвращения полимеризации надо обеспечить избыток изобутана в реакционной смеси и хорошее перемешивание углеводородной фазы с серной кислотой.
§ 61. УСТАНОВКА АЛКИЛИРОВАНИЯ ИЗОБУТАНА БУТИЛЕНАМИ
Сырье и товарная продукция.Сырьем установок алкилирова-ния изобутана бутиленами является бутан-бутиленовая фракция (ББФ), вырабатываемая на газофракционирующих установках из газов каталитического крекинга, термического крекинга и коксования. В составе этой фракции содержатся и непредельные углеводороды — бутилены и изо'бутан. Кроме того, в виде примесей в ББФ содержатся углеводороды С3 и С5. В сырье алкилирования количество С3 и С5 не должно превышать З'/о (масс.) каждого. Присутствие в сырье пропилена приводит к увеличению потребности в холоде в связи с более высоким значением теплоты реакции алкилирования пропилена, снижению октанового числа алкилата, увеличению расхода серной кислоты. Наличие углеводородов Cs также нежелательно, поскольку пентаны в реакцию алкилирования не вступают, а из амиленов образуются малоценные побочные продукты.
Следует, однако, отметить, что в перспективе развитие процесса алкилирования связано с расширением сырьевых ресурсов и привлечением в качестве сырья пропан-пропиленовой фракции (ППФ). Новые установки алкилирования в нашей стране и за рубежом проектируются с учетом использования смеси ППФ и ББФ. При использовании ППФ на алкилирование необходимо подавать дополнительный изобутан.
В результате алкилирования изобутана получают алкилат, который на установках алкилирования делится на две фракции — легкую и тяжелую. Качество легкого и тяжелого алкилата при
297
алкилировании изобутана бутиленами характеризуется следующими показателями:
Легкий Тяжелый
алкилат алкилат
Плотность pf.................................................... 0,698-0,715 -
Фракционный состав, °С
н. к............................................................... 45-57 171
10%.............................................................. 75-87 173-188
50%.............................................................. 100-104 177-198
90%.............................................................. 111-121 204-254
к. к............................................................... 150-170 250-301
Октановое число по исследовательскому методу
алкилат без ТЭС......................................... ....... 92-98 80-84
алкилат с добавкой 0,8 мл/л ТЭС . . 104—106 —
Сортность на богатой смеси с добавкой
1,22 мл/л ТЭС................................................ 145—162 —
Давление насыщенных паров при 38° С,
кПа.................................................................. ......... 20,6 —
Бромное число................................................... ..... 0,2—0,3 —
В течение многих лет легкий алкилат в больших количествах потреблялся как основной компонент авиационного бензина. В связи с уменьшением числа самолетов с поршневыми двигателями спрос на авиационные бензины сведен к минимуму, однако потребность в алкилатах не только не уменьшилась, но даже возросла. Они добавляются к бензинам каталитического риформинга и крекинга, чтобы снизить содержание ароматических углеводородов и улучшить пусковые свойства товарных антобензинов.
Тяжелый алкилат (фракция 170—240С'С) используется как компонент дизельного топлива. Побочными продуктами установки являются пропан и бутан-пентановая фракция.
Катализаторы процесса.Алкилирование изобутана олефинами на отечественных установках проводится в присутствии серной кислоты. Для алкилирования бутиленами применяется 96—98%-ная серная кислота, для алкилирования пропиленом необходима кислота более высокой концентрации — в среднем 98—100%. В процессе алкилирования постепенно происходит снижение концентрации серной кислоты, вызываемое взаимодействием кислоты с непредельными углеводородами и влагой. При понижении концентрации реакции алкилирования замедляются, а реакции полимеризации ускоряются. Поэтому отработанную кислоту заменяют свежей, концентрированной.
За рубежом в качестве катализатора применяется также фтористоводородная кислота.
Параметры процесса.Большую роль в создании оптимальных условий реакции играет температура. Она влияет на расход катализатора, выход и качество алкилата. Наилучшие условия процесса достигаются при 5—13 °С. При повышении температуры облегчается перемешивание кислоты и углеводородов, так как понижается вязкость, однако при этом ускоряются побочные реакции
298
полимеризации и сульфирования (окисления) олефинов. При понижении температуры увеличивается избирательность реакции алкилирования, уменьшается расход катализатора, повышается выход алкилата. Однако при температурах ниже 5°С возрастает вязкость углеводородов и снижается подвижность серной кислоты. Ухудшение контакта кислоты с углеводородами приводит к увеличению расхода электроэнергии на перемешивание.
Давление слабо влияет на процесс. Поддерживают давление в таких пределах, чтобы наиболее легкие компоненты, участвующие в реакции, находились бы в жидкой фазе.
Важными параметрами процесса алкилирования являются соотношение между серной кислотой и углеводородами, продолжительность контактирования сырья с катализатором и интенсивность перемешивания. Для получения оптимальных условий алкилирования объемное соотношение к а т а л и з а т о р : у г л е в о д о-роды в реакционной зоне поддерживают от 1 : 1 до 2: 1.
Продолжительность контактирования сырья с катализатором определяется объемной скоростью, которая представляет частное от деления объема подаваемого в единицу времени сырья на объем кислоты в реакторе. На современных установках алкилирования объемная скорость составляет 0,3 ч-1. Увеличение объемной скорости приводит при прочих равных условиях к снижению октанового числа алкилата. На продолжительность контактирования влияют также конструкция реактора и эффективность работы перемешивающего устройства.
В результате перемешивания увеличивается поверхность раздела фаз и улучшаются условия поглощения изобутана серной кислотой. Поскольку изобутан поглощается кислотой гораздо медленнее, чем олефины, в реакторе необходимо создать условия, способствующие ускорению перехода изобутана в кислоту. В противном случае начнется интенсивная реакция полимеризации олефиновв присутствии серной кислоты. Кроме того, если перемешивание недостаточно интенсивно, то может оказаться, что не вся масса кислоты контактирует с углеводородным сырьем.
Предотвращению полимеризации способствует также разбавление сырья циркулирующим изобутаном. Чем выше концентрация изобутана в сырье, поступающем в реактор, тем больше она будет и на поверхности раздела фаз углеводородов с кислотой, где протекает. реакция. Соответственно концентрация олефинов будет ниже. Соотношение изобутан : олефины поддерживают от 4: 1 до 10: 1.
Технологическая схема. Технологическая схема установки сер--
нокислотного алкилирования изобутана бутан-бутиленовой фрак
цией приводится на рис. 77. ,
Установка алкилирования состоит из отделений подготовки сырья, реакторного, обработки углеводородной смеси, фракционирования продуктов. В отделении подготовки сырья (на схеме не показано) щелочной и водной промывкой из бутан-бутиленовой фракции удаляются сероводород и меркаптаны. Здесь же сырье
299
|
■ST-™-1 Ьапк-1 |
Рис. 77. Технологическая схема установки I — сырье; // — свежая серная кислота; /// — отработанная серная кислота; IV—цир VII — бутан; VIII — легкий алкилат; IX — тяжелый алкилат; Х~с
подвергается осушке от воды с помощью водоотделителей, отстойников, гравийных фильтров или электроотделителей. Для осушки применяются также адсорбенты — окись алюминия и цеолиты.
Затем сырье поступает в реакторное отделение. В емкости Е-1 оно смешивается с циркулирующим изобутаном и насосом Н-1 подается через теплообменник и холодильник в реактор контактного типа Р-1. Одновременно с сырьем в реактор вводится серная кислота, которая вступает в контакт с бутан-бутиленовой фракцией.
При взаимодействии изобутана с бутиленами выделяется тепло в количестве 750—1100 кДж/кг алкилата, для съема которого применяется искусственное охлаждение. Хладагентом служит аммиак, который циркулирует в охлаждающей системе. Сжатый компрессором ПК-1 аммиак конденсируется в конденсаторе-холодильнике ХК-1, собирается в емкости Е-4, а затем насосом подается в трубный пучок реактора Р-1, где испаряется за счет снижения давления и повышения температуры. Испаряясь, аммиак снимает избыточное тепло реакции. Газообразный аммиак вновь подается на компрессию.
Из реактора Р-1 продукты реакции поступают в отстойник С-1, где отделяются от серной кислоты. Серная кислота насосом Н-2 возвращается в реактор, а углеводороды через теплообменник Т-1 подаются в отделение обработки углеводородной смеси. Здесь углеводородная смесь освобождается от капелек серной кислоты и эфиров с помощью щелочной и водной промывки. Для осуществления щелочной и водной промывки предназначены смеситель А-1, отстойники Е-2, Е-3 и циркуляционные насосы Н-3, Н-4. Промытая углеводородная смесь поступает на блок ректификации.
В состав новых установок алкилирования включают блоки бокситной очистки от эфиров серной кислоты.
В первой ректификационной колонне К-1, которая называется изобутановой, из продуктов реакции выделяются пропан и избыточный, не вступивший в реакцию изобутан. Затем в проиановои колонне К-2 изобутан отделяется от пропана и возвращается на смешение со свежим сырьем. С низа колонны К-1 смесь бутана и алкилата подается в бутановую колонну К-3, в которой разделяется на бутан (его иногда называют отработанной бутан-бутиленовой фракцией) и суммарный алкилат. Последний затем в колонне вторичной перегонки К-4 разделяется на легкий и тяжелый алкилат.
Технологический режим установки
Температура Температура Давление,
низа, °С перха, °С Мпа
Реактор . ............................... 0—10 0—10 0,6
Ректификационные колонны
изобутановая К-1 .... 95—120 45—55 0,5—0,6
пропановая К-2................... ......... 85-100 40-45 1,6-1,7
бутановая К-3...................... ....... 125-135 45-50 0,3-0,4
вторичной перегонки
К-4.................................... ......... До220 100-115 0,02-0,04
301
Рис. 78. Вертикальный реактор алкилирования контакторного типа:
/—хладагент; // — сырье; /// —серная кислота;
/V —продукты реакции;
/—корпус; 2—цилиндрический кожух; 3—трубчатый
пучок; 4 — пропеллерная мешалка.
302
Аппаратура. Основной
аппарат установки алкилирования—реактор. Существуют различные ре-акторы-алкилаторы, различающиеся по способу подачи сырья и схеме охлаждения. Они могут быть разделены на три типа:
1) емкостные — с применением выносных циркуляционных насосов для перемешивания реакционной смеси;
2) контакторные — с внутренними циркуляционными устройствами и охлаждающими элементами;
3) каскадные—с внутренним охлаждением и внутренними циркуляционными устройствами,без охлаждающих элементов.
Емкостные аппараты сооружались на первых промышленных установках сернокислотного алкилирования На смену им пришли контакторные реакторы, один из которых — вертикальный с охлаждением через поверхность—изображен на рис. 78. В корпусе реактора размещены два пучка труб различного диаметра, причем каждая из труб меньшего диаметра свободно входит внутрь соответствующей трубы большего диаметра. Хладагент подается в верхнюю часть реактора, распределяется по трубкам меньшего диаметра и стекает вниз. Затем он поступает в трубы большего диа-
метра, поднимается вверх и испаряется, отнимая тепло от находящейся в межтрубном пространстве реакционной смеси. Из реактора хладагент выводится на компрессию.
Реакционная смесь перемешивается пропеллерной мешалкой 4. Смесь из кольцевого пространства между стенкой реактора и внутренним цилиндрическим кожухом 2 поступает внутрь кожуха, где размещены охлаждающие трубы. Процесс алкилирования протекает в основном при нисходящем движении реакционной смеси вдоль поверхности охлаждения (пучка труб).
^Ч |
т
Ф
(I
[,Vi
D
V"
VI "
Рис. 79. Каскадный самоохлаждающийся реактор алкилирования:
/ — олефиновое сырье; // —циркулирующая кислота; III — pe-циркулирующнй изобутан и хладагент; IV — пары изобутана и хладагента; V —серная кислота; VI— углеводородный
поток; 1—5 — секции реактора; 6—7 — отстойные зоны; 8—перемешивающие устройства; 9—сепаратор.
Разработаны и внедряются на действующих установках алкилирования взамен описанных выше модернизированные контакторы вертикального и горизонтального типа. В этих аппаратах с целью улучшения теплопередачи и упрощения условий изготовления трубного пучка применены U-образные трубки, увеличена поверхность теплообмена, разработана более совершенная система уплотнения вала пропеллерного насоса. Внедрение новых контакторов позволяет повысить производительность установок.
Еще более эффективны каскадные самоохлаждающиеся реакторы (рис. 79), тепло реакции в которых снимается за счет испарения части реагирующих компонентов. В реакторе имеется несколько реакционных зон, снабженных мешалками, и две отстойные зоны. В каждую из реакционных зон подается смесь олефинов и изобутана. Давление процесса регулируют таким образом, чтобы обеспечить частичное испарение углеводородной фазы. Испаряющиеся углеводороды, главным образом пропан и изобутан, забираются из верхней части реактора компрессором, сжимаются, конденсируются и возвращаются в реактор. Изменением количества
303
с
испаряющегося газа поддерживается постоянство температуры в реакторе. Существуют конструкции каскадного реактора, насчитывающие 5—6 реакционных секций (зон). В первой из отстойных зон отделяется от углеводородов основная масса кислоты, а во второй — небольшая оставшаяся часть.
Каскадные реакторы отличаются от трубчатых простотой конструкции и высокой производительностью. Удельный расход серной кислоты для установок примерно одинаковой производительности в идентичных условиях алкилирования составляет (в кг/т алки-лата): в вертикальном реакторе 200—250, в каскадном 60—100.
Материальный баланс алкилирования.Материальный баланс при переработке бутан-бутиленовой фракции каталитического крекинга (I) и смеси бутан-бутиленовой и пропан-протшленовой фракций, полученных из газов каталитического крекинга, термического крекинга и коксования (II), приводится ниже [в % (масс.)].
I п
Поступило:
Бутап-бутилеповая фракция .... 100,0 54,4
Пропаи-иропилеповая фракция ... — 29,7
Изобутан................................................. — 15,9
Итого ... 100,0
Получено:
Алкилат легкий...................................... ......... 71,5 66,5
Алкилат тяжелый................................... ........... 7,2 5,9
Пропан.................................................... ........... 2,8 14,0
Бутан-пентановая фракция.................... ......... 15,5 10,6
Потери.................................................... 3,0 3,0
Итого . . . 100,0 100,0
Выход суммарного алкилата составляет 170—200% на вступившие в реакцию алкены.
§ 62. ИЗОМЕРИЗАЦИЯ ЛЕГКИХ ПАРАФИНОВЫХ УГЛЕВОДОРОДОВ
Механизм и катализаторы процесса
Для низкомолекулярных парафиновых углеводородов С4—С6 внутримолекулярные химические реакции структурной изомеризации могут протекать в следующих направлениях:
а) превращение углеводородов нормального строения в разветвленные
СНз IСН3-СН2—СН2—СН3 ч=* СН3—СН
I
СНз 304
CH3—CH2—CH2—CH2—CH3 ^=fc СН3—СН—СН2—СН3
I
СН3
изопентан
СНз—СН2—СН,—СН2—СН,—СНз ч=*= СНз—СН—СН,—СН2—СНз
I
СНз
б) перемещение метильного радикала вдоль углеродной цепи
СНз—СН—СН2—СН2—СН3 ч=2: СН3—СН2—СН—СН2—СН3
I I
СНз СНз
СНз
I
СНз—СН—СН—СНз ч=Ь СНз—СН,—С—СНз
II "I
СНз СНз СНз
неогексан
в) изменение числа метильных радикалов в боковых цепях раз
ветвленных углеводородов
СНз
СН3—СН—СН2—СНз =?=fc СНз—С—СНз
I I
СН3 СНз
неопентан
СНз—СН—СН2—СН2—СН3 =<=* СНз—СН—СН—СНз
I I I
СНз СНз СНз
Все эти реакции обратимы, поэтому равновесные концентрации изомеров в смеси зависят прежде всего от температуры процесса.
Практический интерес в настоящее время- представляет получение изобутана в качестве сырья для процесса алкилирования оле-финами; изопентана в качестве сырья для получения изопрена и дальнейшей его полимеризации в изопреновый синтетический каучук и смеси разветвленных пеитанов и гексанов в качестве компонентов высокооктановых автомобильных бензинов.
Термодинамическое исследование реакций изомеризации нормальных алканов показывает, что их превращения в разветвленные структуры наиболее вероятны при сравнительно низких температурах (для бутана не выше 100 °С, для пентана не выше 150 СС), но скорости реакций при этих температурах крайне малы. Это предопределяет необходимость применения активных катализаторов.
Самым активным катализатором изомеризации при низких температурах является хлористый алюминий либо в смеси с хлористой сурьмой, либо в виде комплекса с углеводородами и с добавкой хлористого водорода. Однако этот катализатор недостаточно селективен, вызывает ряд побочных процессов, в том числе крекинг и диспропорционирование водорода, а также весьма коррозионно-активен. По этим причинам в заводской практике для изомеризации пентана и гексана хлористый алюминий не применяется.
30§
В настоящее время наибольшее признание для процессов изомеризации нашли бифункциональные катализаторы, содержащие платину или палладий на окиси алюминия. Их основное достоинство хорошая селективность. Однако для достижения нужной глубины изомеризации температуру процессов иногда приходится повышать до 300—400 °С и выше. В целях предотвращения при этих температурах разложения углеводородов и отложения кокса на катализаторе процессы изомеризации ведут в присутствии водорода и под общим давлением до 3—4 МПа.
На одном из таких катализаторов (ИП-62) на ряде отечественных заводов осуществляется процесс высокотемпературной изомеризации пентановой фракции (380—450 °С; 3,5—4 МПа). Катализатор представляет собой фторированную окись алюминия, на которую нанесена платина. В процессе применяется циркуляция водородсодержащего газа с установок платформинга. Достигается степень превращения сырья за один проход 50—55%. Поэтому в процессе применяется рециркуляция изомеризата. Выход изопен-тана на превращенный пентан составляет 96%•
Помимо целевой реакции структурной изомеризации на данном катализаторе имеет место также частичный крекинг пентана и изопентана, гидроочистка и обессеривание сырья и изомеризата. Однако выход продуктов распада не превышает 2%.
Хорошие результаты достигаются и на цеол«тсодержащих платиновом или палладиевом катализаторах. Так, при изомеризации гексана на платинированном цеолите типа Y при 310—340 °С, 3 МПа, мольном соотношении Н2: СбНн = 3,5 и объемной скорости подачи сырья равной 1 ч-1 — выход изомеров гексана достигал 74%.
В последнее время ведутся работы по подбору бифункциональных катализаторов для низкотемпературного процесса изомеризации пентана и гексана, преимущества которого очевидны.
В частности, на платинированной окиси алюминия, промотиро-ванной хлорорганическим соединением (катализатор НИП-66) при 130—140 СС, 3 МПа, подаче сырья равной 1,5 ч-1 и соотношении Нг: С5Н12 = 2:1 был достигнут выход изопентана из н-пентана равный 70% за один проход.
В дальнейшем на этом же катализаторе при 120 °С из пентан-гексановой фракции за один проход, т. е. без рециркуляции был получен выход изомерных пентанов и гексанов, равный 73%. Необходимо отметить, что при применении.платиновых или палладие-вых бифункциональных катализаторов очень жесткие требования предъявляются к качеству как сырья, так и водородсодержащего газа. Такие примеси как окись углерода, кислород, влага и особенно сернистые соединения являются дезактиваторами катализатора. Поэтому требуется предварительная очистка и осушка водородсодержащего газа и сырья.
Механизм реакций каталитической изомеризации аналогичен механизму превращений углеводородов при каталитическом крекинге и каталитическом алкилировании изобутана олефинами. Во
305
всех этих процессах зарождение цепи химических реакций происходит под действием иона водорода '(протона) кислотного катализатора. Развитие же цепи связано с разнообразными превращениями промежуточных весьма активных ионов карбония или как их еще называют карбкатионов. Механизм изомеризации парафиновых углеводородов на бифункциональных катализаторах имеет то отличие, что первоначально под действием металлического компонента катализатора исходные парафины дегидрируются до моио-олефинов. Полученные олефины подвергаются под влиянием кислотного компонента катализатора структурной изомеризации,которая протекает по карбопий-ионному механизму. На заключительной стадии цепной реакции изоолефины насыщаются водородом и образуется смесь изопарафиновых углеводородов. Эта, сформулированная Миллсом в 1953 г., ныне общепринятая и экспериментально подтвержденная теория изомеризации парафинов над бифункциональными катализаторами хорошо подтверждается тем фактом, что олефины изомеризуются значительно легче, чем парафиновые углеводороды, а сам карбоний-ионный механизм изомеризации оле-финов и парафинов полностью аналогичен. Таким образом, изомеризацию, например, н-гексана над алюмоплатиновым катализатором можно изобразить такой схемой *:
м С—С—С—С—С—С ^=* С—С=С—С—С—С *=±
С—С—С—С—С—С | + |
с—с=с- А с—с=с- А |
м
с—с =<=* с—с—с—с—с
С—С—С—С—С I с с—с—с—с—с . I с |
I
с
С—С ^=± С—С—С—G—С
Установка изомеризации для получения компонента высокооктанового бензина
Сырье. В качестве сырья на установках изомеризации, предназначенных для получения компонента высокооктанового бензина, используется легкая прямогонная фракция, выделяемая на установках вторичной перегонки бензинов. В этой фракции содержится 65—70% пентанов, в том числе 35—45% н-пентана, 20—25% изо-гексанов, а также бутаны и гексан.
Товарная продукция. Товарными продуктами являются изопен-тановая и изогексановая фракции. Октановое число изопентановой фракции равно 89 (по моторному методу, без ТЭС), а изогексановой,
* Реакции, помеченные М (гидро-дегидрогеиизация) протекают на поверхности платины, а помеченные Н на поверхности носителя (А1203).
307
|
|
|
|
|
блок ректификации
Рис. 80. Технологическая схема уставовк / — сырье; Я —свежий водородсодержащий газ; /// — бутаны; IV— иэопентан; V
газ.
содержащей не более 1 % гексана, — 78. Кроме того, на установке выделяют бутановую и гексановуго фракции, а также углеводородный газ.
Технологическая схема(рис. 80). Установка изомеризации состоит из двух блоков — ректификации и изомеризации. Блок ректификации предназначен для выделения из смеси сырья и изомери-зата товарных продуктов — изопентановой и изогексановой фракций, удаления из сырья углеводородов С4 и ниже, подготовки к переработке сырья секции изомеризации — пентановой фракции. В блоке изомеризации осуществляется превращение пентана в изо-пентан.
Схема блока ректификации аналогична описанным выше установкам вторичной перегонки и газофракционирования. Смесь сырья и стабильного изомеризата разделяется в изопентановой колонне К-1 на верхний продукт — смесь изопентана и бутана и нижний продукт—смесь н-пентана и гексанов. В колонне К-2 ректификат колонны К-1 делится на бутаны и изопентан. В колонне К-3 остаток колонны К-1 разделяется на н-пентановуго фракцию, направляемую в блок изомеризации и смесь гексанов, подаваемую в колонну К-4. В К-4 проводится разделение, смеси гексанов на изо-гексан и н-гексан.
Конденсация и охлаждение верхних продуктов ректификационных колонн осуществляется в воздушных конденсаторах-холодиль-• никах; товарных продуктов перед выводом с установки — в водяных холодильниках. Тепло в нижнюю часть колонн подводится через кипятильники, обогреваемые паром.
Пентановая фракция, поступающая на блок изомеризации, забирается насосом Н-11 и подается на смешение с водородсодержа-щим газом. Смесь сырья и водородсодержащего газа нагревается в теплообменнике Т-4 и печи П-1 до температуры реакции и поступает в реактор Р-1, где в присутствии алюмоплатинового катализатора происходит реакция изомеризации.
Газо-продуктовая смесь, выходящая из реактора, охлаждается в теплообменниках и холодильниках, после чего направляется на разделение в продуктовый сепаратор С-1. Из С-1 выходит циркулирующий водородсодержащий газ, который смешивается со свежим водородсодержащим газом, подвергается осушке цеолитами в адсорбере К-5 и подается во всасывающую линию циркуляционного компрессора ПК-1. Сжатый водородсодержащий газ смешивается с сырьем.
Нестабильный изомеризат из С-1 нагревается до 85—90° С в теплообменнике Т-5 и поступает в стабилизационную колонну К-6. С верха К-6 уходит жирный газ, с низа — стабильный изомеризат, который направляется на блок ректификации. Тепло в К-6 подводится через кипятильник, обогреваемый водяным паром.
Катализатор изомеризации периодически — 1 раз в 5—6 мес подвергается окислительной регенерации. Регенерация катализатора проводится так же, как на установках платформинга (см. §51).
309
Технологический режим процесса Блок ректификации Температура, °С верха К-1.................... ". низа К-1 |
верха К-2 низа К-2 . верха К-3 низа К-3 . Давление, МПа в К-1 . . в К-2 . . в К-3 . .
Блок изомеризации
Температура, СС
77 сырья на выходе из
ПО теплообменников . .
55 реакции, в начале
100 цикла ....................
74 в конце цикла . . .
110 верха К-6 .................
низа К-6 .........................
0,6 Давление, МПа
0,7 в реакторе Р-1 ....
0,6 в стабилизаторе К-6
в нагнетательной ли
нии компрессора
ПК-1............................
Объемная скорость подачи
сырья, ч-1...........................
Стгпеиь превращения пен-тана за проход. % (масс.)
340-345
380
450
82
112
3,5
0,85
5,0 1,5 50
Материальныйбаланс. Ниже приводится баланс установки при переработке фракции н. к. — 62 °С ромашкинской нефти, не содержащей углеводородов С4 и гексана (I) и содержащей бутаны и гексан (II), в % (масс):
Фракция н. к. — 62 °С . .
Водородсодержащий газ .
в том числе 100%-иый
Поступило:
..................................... 100,0 100,0
..................................... 1,0 0,8
водород ................. (0,28) (0,22)
Сухой газ..........................
Сжиженный газ ....
Изопентановая фракция
Изогексановая фракция
Гексановая фракция . .
Потери..............................
Итого Получено:
101,0
^,l
68,7 28,4
1,8
100,!
1,6
15,3
53,4
22,1
6,9
1,5
Итого .
101,0 100,8
Перспективы развития процесса.В нашей стране промышленно освоен процесс высокотемпературной изомеризации пеитана на катализаторе ИП-62 (платина на фторированной окиси алюминия) при 380—400 °С. При этих температурах степень превращения пен-тана в изопентан ограничена условиями термодинамического равновесия и составляет 50—55% (масс.) за проход. Значительно более высокой степени превращения можно добиться, если проводить процесс при 100—150 °С. Кроме того, при низких температурах заметно увеличивается степень превращения н-гексана в высокооктановые изомеры — диметилбутаны. Это позволяет расширить ресурсы сырья, подвергнув изомеризации фракцию н. к. —70 °С, в состав которой наряду с пентанами входят гексаны — нормальный и изо. ВНИИНефтехимом создан катализатор НИП-74, на базе которого будут создаваться установки низкотемпературной изомеризации в нашей стране.
U0
Глава IX
Дата добавления: 2018-04-04; просмотров: 2099; Мы поможем в написании вашей работы! |
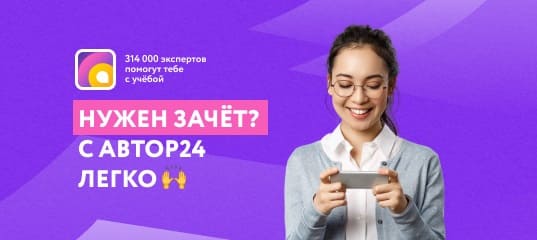
Мы поможем в написании ваших работ!