Развитие нефтеперерабатывающей промышленности в СССР. 21 страница
освобождают от нефтепродуктов, на трубопроводах устанавливают заглушки, аппараты и трубопроводы продувают водяным паром (пропаривают) и инертным газом. Из подготовленных аппаратов берут пробу воздуха, чтобы убедиться в отсутствии газов. При удовлетворительном анализе отглушают дренажные линии и оформляют документацию на проведение в аппаратах огневых или ремонтных работ.
Пуск установки. Ввод установки в эксплуатацию состоит из следующих этапов: опрессовки аппаратов, холодной и горячей циркуляции, вывода установки на режим. Первоначально на установку принимают воздух для контрольно-измерительных приборов, воду, пар и электроэнергию. Затем проводят промывку и гидравлическое испытание на прочность (опрессовку) аппаратов водой. В зимнее время опрессовку осуществляют сырой нефтью или низ-козастывающими нефтепродуктами. После опрессовки на установку принимают жидкое топливо, реагенты и нефть.
Холодная циркуляция необходима для окончательного выявления неисправностей, регулирования работы насосов и отладки приборов контроля и автоматики. При холодной циркуляции нефть сырьевым насосом прокачивается через основную аппаратуру и возвращается во всасывающую линию сырьевого насоса.
Горячая циркуляция предназначена для плавного прогрева аппаратуры и оборудования, удаления из системы воды; ее проводят по схеме холодной циркуляции. Сначала продувают паром топочные камеры печей, затем разжигают печи, постепенно поднимая температуру на выходе из П-1 и в колоннах. После достижения на верху колонн температуры 85—100°С начинается испарение воды из системы. Сигналом об окончании выпарки воды является резкое повышение температуры верха колонн. При повышении температуры верха К-1 и К-2 до 120—130 °С на верх этих колонн подают орошение и включают системы автоматического регулирования температуры верха.
|
|
Регулируя расход орошения, устанавливают заданную температуру верха колонн, после чего налаживают работу систем циркулирующих орошений. Когда температура низа К-1 и К-2 достигнет соответственно 200 и 300°С, на установку подают свежее сырье, открывают задвижки между атмосферной и отпарными колоннами.
По мере появления уровня жидкости в отпарных колоннах включают насосы откачки. Однако керосиновые и дизельные фракции не сразу выводят в товарные резервуары, а первоначально сбрасывают в сырье установки. Так поступают до тех пор, пока не будет получено подтверждение из лаборатории, что эти фракции по качеству соответствуют нормам.
Мощные комбинированные установки первичной переработки нефти пускают в эксплуатацию поблочно: сначала проводят пуск блока атмосферной перегонки, затем блоков стабилизации и вторичной перегонки, вакуумного блока.
|
|
159
§ 31. ТЕХНИКА БЕЗОПАСНОСТИ И ОХРАНА ТРУДА
В результате нарушений технологического режима, несоблюдения правил безопасности при эксплуатации нефтеперерабатывающих производств происходят аварии, несчастные случаи, у работающих развиваются профессиональные заболевания.
Источники опасности при переработке нефти и газа. Аварии и несчастные случаи вызываются следующими причинами.
1. Нефть и все нефтепродукты являются горючими веществами и, кроме того, при определенной температуре способны самовоспламеняться. При первичной переработке и в некоторых других процессах нефтепродукты нагреваются до температур, близких и даже превышающих температуру самовоспламенения. В то же время на установках имеются источники открытого огня — трубчатые печи.
2. В технологических процессах переработки нефти и газа участвует большое количество продуктов, пары которых могут создавать с воздухом взрывоопасные смеси. Такие смеси образуются в закрытых помещениях, каналах, внутри аппаратов. При наличии импульса воспламенения, например искры, смеси взрываются. Источниками импульса воспламенения могут быть искры от неисправного или неприспособленного для работы во взрывоопасных помещениях электрооборудования, открытый огонь, возникающий при соприкосновении пожароопасной среды с нагретыми поверхностями и т. п. Взрывь! и пожары могут вызываться так называемым статическим электричеством, которое возникает при трении друг о друга двух диэлектриков или диэлектриков об металл. На НПЗ статическое электричество можег появиться при перекачке нефти по трубопроводам и резиновым шлангам, переливании нефтепродуктов из сосуда в сосуд, транспортировании сыпучих продуктов по транспортерам и т. д. Источником воспламенения также являются разряды атмосферного электричества — молнии.
|
|
3. Существует возможность разрыва аппаратов и трубопроводов из-за внезапного повышения в них давления.
4. Нефть, нефтепродукты и большинство реагентов, применяемых на НПЗ, относятся к числу вредных веществ, обладающих токсическими свойствами.
5. На технологических установках имеется большое число электродвигателей, осветительных приборов и других электрических устройств. При неправильном обращении с электрическим током возможны электрические удары, когда током поражается весь организм, и электротравмы, результатом которых являются местные поражения тела — ожоги.
|
|
6. На НПЗ имеются аппараты большой высоты, механизмы с быстро движущимися частями (муфты сцепления центробежных насосов, лопасти вентиляторов аппаратов воздушного охлаждения и др.), и поэтому возможны травмы обслуживающего персонала из-за неумелого обращения с оборудованием и приспособлениями или их неисправности.
160
Основные меры борьбы с опасностями.Для предотвращения аварий и несчастных случаев на установках переработки нефти необходимо обеспечить безусловное выполнение всеми работающими норм и правил техники безопасности. Все поступающие на работу обязательно проходят инструктаж по технике безопасности, пожарной и газобезопасности, изучают существующие инструкции. Особое внимание при эксплуатации установок должно быть обращено на герметизацию аппаратов и трубопроводов, контроль за исправным состоянием приборов автоматического регулирования.
При проектировании и эксплуатации заводов предусматривают следующие мероприятия по технике безопасности и охране труда.
1. Для исключения переброски огня в случае пожара с одного объекта на другой между производствами выдерживают противопожарные разрывы. Технологические установки и объекты общезаводского хозяйства оборудуют стационарными и передвижными средствами пожаротушения.
2. В помещениях, где возможно возникновение взрыво- или токсически опасных концентраций продуктов устанавливают специальные приборы, которые сигнализируют о том, что концентрация взрывоопасных или токсических веществ приближается к максимально допустимому значению.
3. Все аппараты, работающие под давлением выше 0,07 МПа, снабжают предохранительными клапанами, которые открываются при опасном превышении давления в аппарате и сбрасывают избыточное количество газа или жидкости.
4: Для обеспечения безопасной работы предусматривают ряд специальных мероприятий: например, насосы, перекачивающие нефтепродукты, устанавливают на открытом воздухе, что позволяет отказаться от сооружения специальных зданий — насосных, которые ранее были основным очагом возникновения взрывов и пожаров.
5. Чтобы предотвратить несчастные случаи во время ремонта, проектами установок предусматриваются стационарные и передвижные механизмы: кран-балки для ремонта насосов, кран-укосины на колонных аппаратах, экстракторы для выемки трубных пучков из теплообменников.
Предупреждение и ликвидация аварий.Аварии на установках являются в первую очередь результатом нарушения технологического режима, правил эксплуатации установок, правил и норм пожарной безопасности при работе с огне- и взрывоопасными веществами. Причиной аварии бывает также прекращение подачи на установку сырья, пара, топлива, воды, электроэнергии.
При прекращении подачи сырья установку следует перевести на горячую циркуляцию. Если прекратилась подача электроэнергии, то следует немедленно провести аварийную остановку. В этом случае последовательно выполняют следующие операции: тушат форсунки печей, перекрывают задвижки на приемных и нагнетательных линиях насосов, тщательно наблюдая за давлением
6 Зак. 380
161
в аппаратах. Необходимо отключить все электродвигатели и прочее электрооборудование, чтобы при восстановлении подачи электроэнергии не произошел самопроизвольный пуск. После возобновления подачи электроэнергии установку выводят на нормальный режим согласно пусковой инструкции.
Прекращение подачи водяного пара — очень серьезная авария, так как при этом установка лишается основного средства пожаротушения. Если пар отсутствует в течение длительного времени, также должна быть проведена аварийная остановка.
Частой причиной аварии на установках является прогар труб в печах.
Порядок ликвидации аварий подробно излагается в производственных инструкциях и, в частности, в плане ликвидации аварий на установке, инструкциях по технике безопасности и пожарной безопасности.
§ 32. ТЕХНИКО-ЭКОНОМИЧЕСКИЕ
ПОКАЗАТЕЛИ УСТАНОВОК
ПЕРВИЧНОЙ ПЕРЕГОНКИ
Об эффективности работы перегонных установок судят по таким показателям, как производительность установки, продолжительность безостановочного пробега, глубина отбора целевых фракций (в процентах от потенциального содержания этих фракций в нефти), качество получаемой продукции, соблюдение норм и экономия в расходовании пара, воды, электроэнергии, реагентов.
Примерные технико-экономические показатели установок пер
вичной переработки нефти приводятся ниже (в расчете на 1 т
нефти): - -
ЭЛОУ-АВТ ЭЛОУ-АВТ мощностью мощностью 3 млн. т/год 6 млн. т/год
Пар, кг......................................... 73,0/32,6. 49,2/1,1
Вода оборотная, м3..................... 8,4 4,8
Электроэнергия, МДж .... 37,4 37,4
Жидкое топливо, т...................... 30,3 33,4
Примечание. В числителе указан общий расход пара в знаменателе — то количество, которое надо подать со стороны остальная потребность в паре удовлетворяется за счет выра ботки в котлах-утилизаторах.
Увеличением продолжительности безостановочной эксплуатации, ростом производительности установки, снижением 'расхода энергоресурсов добиваются снижения себестоимости продукции, повышения производительности труда.
Значительное увеличение мощности достигается в результате реконструкции и модернизации действующих установок. Основные направления реконструкции: увеличение поверхности теплообмен-ной аппаратуры, установка более мощных электродвигателей к насосам, размещение дополнительных труб в печах, замена некоторых устаревших видов оборудования (например, погружных
162
конденсаторов аппаратами воздушного охлаждения, паровых насосов— насосами с электродвигателями и т. д.).
Такой путь наращивания мощностей по первичной перегонке нефти весьма эффективен. Увеличение мощности установки АТ-б на 30—35% за счет ее реконструкции обеспечивает по сравнению со строительством отдельной новой установки; рост производительности труда в 1,3 раза, снижение удельных капитальных затрат на 25%, а удельных эксплуатационных расходов — на 6,5%.
Основные направления совершенствования установок первичной переработки нефти состоят в следующем: обеспечение высокого отбора от потенциала светлых нефтепродуктов и масляных дистиллятов, повышение качества дистиллятов (без налегания соседних фракций по температурам кипения), повышение коэффициента использования энергоресурсов >за счет более полного использования теплоты отходящих потоков, сокращение удельных расходов топлива, электроэнергии, воды, воздуха, реагентов, использование более эффективного оборудования, внедрение прогрессивных средств контроля и автоматики, схем комплексной автоматизации управления процессами.
§ 33. ВТОРИЧНАЯ ПЕРЕГОНКА НЕФТЯНЫХ ФРАКЦИЙ
В некоторых случаях фракции, полученные при первичной перегонке, требуется разделить на более узкие погоны, каждый из которых затем используется по своему назначению. Такое разделение проводится на отдельных установках вторичной перегонки или блоках, которые включаются в состав установок АВТ и AT. Блоки или самостоятельные установки вторичной перегонки бензина построены почти на всех НПЗ.
Вторичная перегонка бензина
Сырье и продукция.Сырьем установки является широкая бензиновая фракция, прошедшая стабилизацию.. Продукцией установки служат следующие бензиновые фракции:
1) н. к. —62 °С — используется как необходимый компонент автомобильного бензина, обеспечивающий его пусковые свойства (см. § 15); состоит из пентанов и изогексана, содержит также некоторое количество бутана и гексана;
2) 62—85 °С — сырье для получения бензола на установках платформинга (см. § 54);
3) 85—105 °G— сырье для получения толуола на установках платформинга;
4) 105—140 °С — сырье для получения ксилолов на установках платформинга;
5) 140—180 °С — используется как компонент авиационного Керосина или как сырье установок каталитического риформ.инга для повышения октанового числа.
6*
163
На некоторых установках набор получаемых фракций несколько иной: получают фракции 62—85 °С, 85—120 °С, 120—140 °С.
Технологическая схема установки. Схема установки вторичной перегонки бензина приводится на рис. 36. Бензиновая фракция н. к. — 180 °С через теплообменник Т-1 поступает в колонну К-1, с верха которой отгоняется фракция н. к. — 85 °С. Эта фракция затем поступает в колонну К-2, где делится на две фракции — н. к. —62°С и 62—85 °С.
Фракция 85—180°С с низа К-1 подается в колонну К-3. С верха К-3 получают фракцию 85—105 °С или 85—120 °С, а с низа — фракцию 140—180 °С. В этой же колонне в виде бокового погона
-VI
Рис 36. Технологическая схема установки вторичной перегонки
бензина:
/ — фракция н.к.— 180°С; II — фракция 105-140°С; III — фракция 85-105 °С;
IV — фракция и. к. —62°С; V — фракция 140- 180 °С; VI — фракция 62-85 °С.
отбирают фракцию 105—140 °С (или 120—140 °С). Боковой погон перетекает' в отпарную колонну К-4, где от него отгоняются легкие фракции, возвращающиеся в К-3.
Тепло, необходимое для осуществления процесса ректификации в колоннах К-1, К-2, К-3, сообщается в нагревательных змеевиках печей П-1 и 17-2, через которые прокачивается циркулирующий продукт с низа колонн. Нагретый рециркулят возвращается в виде парожидкостной смеси или бензиновых паров под нижнюю тарелку соответствующей колонны.
Тепло, необходимое для отгонки легких компонентов из фракции 105—140 °С, сообщается в кипятильнике Т-3. В качестве теплоносителя в Т-3 используется часть рециркулята колонны К-3, возвращающегося из печи П-2.
Верхние продукты ректификационных колонн К-1, К-2, К-3 конденсируются в водяных кожухотрубчатых конденсаторах ХК-1, ХК-2 и ХК-3. Конденсаты собираются в рефлюксных емкостях Е-1, Е-2, Е-3, из которых частично нозвращаются в колонны в качестве острого орошения. Балансовое количество подается на
164
дальнейшую переработку (верхний продукт К-1) или выводится с установки (верхние продукты К-2, К-3).
Технологический режим.Технологический режим зависит от пределов перегонки получаемых фракций. Ниже приводятся показатели режима при получении фракции 85—120 °С с верха К-3:
Температура, °С Давление, МПа
верха К-1............................... 104 К-1 ....................... 0,23—0,28
низа К-1................................. 170 К-2.............................. 0,18—0,22
верха К-2 . . -............... 78 К-3.............................. 0,02-0,06
низа К-2................................. 122
верха К-3............................... 105
низа К-3................................. .................................................................................... 168
вывода бокового погона . . 130
Материальный баланс установки при переработке фракции н. к. —180 С ромашкинской (I) и самотлорской (II) нефтей [в % (масс.)]
I ' п
Поступило:
Бензиновая фракция н. к. — 180°С. 100,0 100,0
Получено:
10,6 | 21,9 |
14,4 | 12,9 |
15,6 | 12,5 |
24,8 | 23,8 |
33,9 | 28,2 |
0,7 | 0,7 |
Фракция н. к. — 62 °С..........................
62—85 °С........................................
85-105 °С.........................................
105-140 °С......................................
140-180 "С......................................
Потери....................................................
Итого . . . 100,0 100,0
Вторичная перегонка масляных фракций
В состав комплексов по производству масел входят вакуумные установки вторичной перегонки. На этих установках широкая фракция, прошедшая несколько ступеней очистки (см. гл. X), делится на два или три компонента более узкого состава. Из этих фракций путем смешения получают затем масла специальных сортов. Существуют также установки вакуумной перегонки гачей, на которых промежуточный продукт производства парафинов — гач (см. гл. XI) также делится на узкие фракции, используемые затем при производстве парафинов.
Вакуумные установки вторичной перегонки масел и гачей имеют вакуумную колонну, печь, теплообменники и насосы.,
Г лава VI
ТЕРМИЧЕСКИЕ ПРОЦЕССЫ ПЕРЕРАБОТКИ НЕФТИ
§ 34. ОБЩИЕ СВЕДЕНИЯ О ТЕРМИЧЕСКИХ ПРОЦЕССАХ ПЕРЕРАБОТКИ НЕФТИ
Первичная перегонка нефти позволяет выделять из нефти в виде отдельных фракций только те вещества, которые в ней изначально присутствуют. Следовательно, и качество, и количество, и ассортимент получаемых товарных продуктов (бензин, керосин, дизельное топливо и т. д.) целиком лимитируются химическим составом исходной нефти.
Еще в прошлом веке стало известно, что под действием высоких температур органические соединения нефти химически видоизменяются, распадаются и вступают в различные вторичные реакции между собой. Это позволило создать новые, так называемые термические процессы переработки нефти, позволяющие получать из нее углеводородные газы, дополнительные количества жидких нефтепродуктов, а также продукт глубокого уплотнения — нефтяной кокс, т. е. такие новые вещества, которых в исходной нефти не было.
Применение термических процессов намного расширило возможности использования нефти как химического сырья.
В зависимости от условий и назначения процессы термической переработки нефтяного сырья получили названия крекинг (от английского глагола to crack — расщеплять), коксование и пиролиз (от греческого pyros — огонь).
Дата добавления: 2018-04-04; просмотров: 438; Мы поможем в написании вашей работы! |
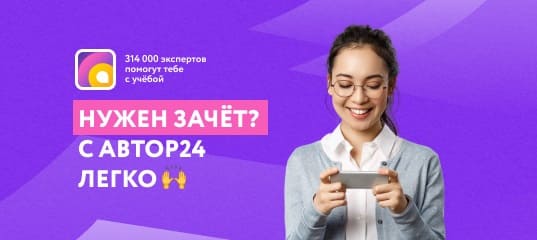
Мы поможем в написании ваших работ!