АВТОМАТИЗАЦИЯ ПРОЦЕССА АГЛОМЕРАЦИИ СВИНЦОВОГО КОНЦЕНТРАТА
8.1 ОПИСАНИЕ ТЕХНОЛОГИЧЕСКОГО ПРОЦЕССА
Агломерация – это процесс спекания мелкой руды или концентрата в прочный кусковой и пористый материал – агломерат. Агломерация является самым распространенным способом окусковывания. При окусковывании сульфидных материалов происходит полное или частичное удаление серы, в этом случае агломерация является процессом обжига – спекания. На рис. 8.1 приведена схема агломерационной машины свинцового производства с прососом воздуха через слой шихты сверху вниз. Исходные материалы – концентрат, флюсы, возврат – смешиваются в шихтовочном отделении, откуда шихта ленточными транспортерами подается в приемный бункер I агломерационной машины. Важнейшим условием получения высококачественного агломерата является поддержание постоянства качества и количества загружаемой на ленту машины шихты. Из приемного бункера I шихта подается тарельчатым питателем II и маятниковым питателем III в загрузочную коробку машины. Маятниковый питатель служит для равномерного распределения шихты по ширине ленты. Для уменьшения провала мелких частиц сквозь колосники ленты в вакуум–камеры машины VIII, а также для увеличения газопроницаемости слоя шихта увлажняется. При этом средний размер частиц шихты увеличивается. Душирующая установка IV подает воду непосредственно на тарельчатый питатель II. Собственно агломерационная машина представляет собой бесконечную ленту V, составленную из тележек с колосниковым дном (паллеты). Лента укреплена на двух барабанах: ведущем VI и ведомом VII. Ширина ленты составляет 1,5 м, скорость движения колеблется в пределах от 1,3 до 2,0 см/с. Высота слоя шихты на ленте не превышает 200–250 мм. Под колосниками паллет установлено шесть вакуум–камер VIII, из которых газ отбирается эксгаустером IХ. Так организуется просасывание необходимого для горения воздуха через слой шихты сверху вниз. Для зажигания горючих составляющих шихты служит зажигательный горн Х, отапливаемый горючим газом. Машина приводится в движение мощным мотором постоянного тока ХI. Этот мотор питается от генератора постоянного тока, приводимого в движение двигателем переменного тока (система «генератор – двигатель»). Сложность этого устройства оправдана возможностью плавного регулирования скорости ленты.
|
|
При движении шихты по ленте влага из нее постепенно испаряется, затем начинается окисление составляющих шихты, выгорание серы. На рис. 8.1 условно показан слой шихты, из которого удаляется влага, после чего происходит «зажигание» шихты.
Положение этого слоя и определяет ход процесса. В результате горения материала температура слоя повышается и шихта спекается в агломерат. Для спекания свинцовых шихт необходима температура 950–1000 оС. Зона готового агломерата характеризуется законченным термическим процессом. Окончание процесса совпадает с прохождением паллетой последних вакуум–камер, над которыми просасываемый воздух охлаждает спек. На закругленной направляющей разгрузочного участка тележка переворачивается, ударяется о предыдущую и от общего массива агломерата отрывается кусок, равный длине паллеты. Выпавший спек попадает на колосниковый грохот, затем поступает в дробилку и вновь на грохот. Верхний продукт грохота крупностью +20 –100 мм является готовым агломератом и идет в плавку. Нижний продукт грохота измельчают и вводят в шихту как оборотный агломерат.
|
|
8.2. ВЫБОР СИСТЕМ АВТОМАТИЧЕСКОГО
РЕГУЛИРОВАНИЯ
Конечным результатом режима работы агломерационной машины является качество готового агломерата, зависящее в значительной степени от скорости движения ленты. Недопеченный агломерат («недопек») получается при увеличении скорости ленты по сравнению со скоростью процесса спекания; «перепек» образуется при соответствующем уменьшении скорости ленты. Так как фронт (линия) спекания по отношению к ленте движется вертикально вниз, то процесс заканчивается, когда фронт спекания достигает колосников. В этот момент температура в соответствующей вакуум–камере увеличивается до максимального значения, так как путь газового потока от зоны горения вниз минимален. Следовательно, положение точки окончания процесса можно определить по положению максимума температур в верхней части вакуум–камер. Нормальное качество агломерата получается обычно при положении максимума температур слоя над последней или предпоследней вакуум–камерой. Для рассматриваемой машины точка окончания процесса находится над пятой вакуум–камерой, ближе к ведомому барабану. Несоответствие между скоростью движения ленты и скоростью протекания процесса спекания вызывает перемещение максимума температур к началу машины («перепек») либо к концу машины («недопек»). Практическое определение положения точки максимума температур затрудняется тем, что абсолютное значение его может меняться. Наиболее распространенный метод определения положения точки окончания процесса спекания состоит в измерении разности температур в двух соседних вакуум–камерах в конце машины.
|
|
Изменение высоты слоя шихты на ленте осуществляет агломератчик вручную перемещением регулирующего шибера загрузочной коробки с целью поддержания максимально возможной производительности машины. Производительность тарельчатого питателя шихты должна быть поставлена в зависимость от изменения высоты слоя шихты на ленте и скорости движения паллет. Так как связать работу питателя непосредственно с указанными параметрами трудно, обычно предпочитают поддерживать уровень в загрузочной коробке машины постоянным.
|
|
Важным фактором режима спекания является газопроницаемость шихты, поступающей в машину и находящейся на ленте. От газопроницаемости слоя материала зависит количество просасываемого через него воздуха, а следовательно, и интенсивность процесса спекания. В свою очередь газопроницаемость шихты зависит от влажности, так как влага обеспечивает прилипание мелких частиц друг к другу.
Ввиду сложности задачи определения газопроницаемости шихты и поддержания ее постоянной приходится ограничиваться регулированием влажности материала. При этом подачу воды в шихту можно вести по расходу материала либо обеспечивать заданную влажность, измеряя ее в шихте специальным прибором – влагомером.
Зажигательный горн является вспомогательным устройством агломерационной машины. Задачей его следует считать создание достаточной для зажигания шихты температуры над слоем материала в начале ленты. Для свинцовой шихты температура в горне составляет примерно 900 оС. Повышение температуры ведет к перерасходу топлива на зажигание и к оплавлению поверхности шихты, что резко уменьшает газопроницаемость слоя, при этом возможно зажигание материала «гнездами». А понижение температуры в горне приводит к ухудшению условий зажигания. Поддержание постоянства температуры в горне можно обеспечить, изменяя расход топлива – природного газа, при этом для обеспечения высокой степени сгорания газа желательно постоянно поддерживать оптимальное соотношение расходов газ – воздух, изменяя расход воздуха.
Тяговый режим агломерационной машины влияет на расход воздуха, просасываемого через слой, т.е. на протекание основного процесса – спекания шихты. Для обеспечения нормального тягового режима обычно стабилизируют разрежение перед эксгаустером. Нормальное разрежение перед эксгаустером составляет 10–11 кПа. При увеличении разрежения увеличивается расход воздуха, проходящего через слой шихты на ленте, материал охлаждается и процесс замедляется. Кроме того, увеличиваются присосы воздуха в вакуум–камеры, что вызывает перерасход электроэнергии на привод эксгаустера. При уменьшении разрежения снижается расход воздуха, что ухудшает режим горения материала. С другой стороны, разрежение в вакуум–камерах часто колеблется из-за неравномерности физических свойств слоя шихты. Отсюда ясна необходимость регулирования разрежения в сборном газоходе.
Помимо вышеперечисленного очень полезно для управления процессом агломерации иметь информацию о температуре в каждой вакуум–камере.
В целом, функциональная схема автоматизации процесса агломерации свинцового концентрата должна включать следующие системы автоматического контроля и регулирования:
1. Системы автоматического регулирования
– разности температур в двух последних вакуум–камерах путем изменения скорости аглоленты;
– высоты слоя шихты на аглоленте путем изменения производительности питателя шихты;
– влажности шихты путем изменения расхода воды на увлажнение;
– температуры в горне путем изменения расхода природного газа;
– соотношения расходов газ – воздух, путем изменения расхода воздуха;
– разрежения перед эксгаустером путем изменения положения заслонки в газоходе.
2. Система автоматического контроля температуры в вакуум–камерах.
Номинальные значения некоторых выходных технологических параметров процесса агломерации приведены в табл. 8.1.
Таблица 8.1
№№ п/п | Наименование параметра | Единица измерения | Номинальные величины |
1. | Температура в вакуум–камерах | оС | 200–800 |
2. | Температура в горне | оС | 900 |
3. | Высота слоя шихты на ленте | мм | 200–250 |
4. | Разрежение перед эксгаустером | кПа | 10–11 |
8.3. ОПИСАНИЕ СИСТЕМ АВТОМАТИЧЕСКОГО КОНТРОЛЯ И РЕГУЛИРОВАНИЯ (рис. 8.2)
8.3.1. Система автоматического регулирования разности
температур в двух последних вакуум–камерах
В рассматриваемой системе принято автоматическое регулирование скорости ленты по разности температур в пятой и шестой вакуум–камерах. В результате технологических испытаний установлено, что при нормальном ходе процесса эта разность равна нулю. Двойные термопары (поз. 6д и поз. 6е) связаны с автоматическим регулятором (поз. 6к). Регулятор через блок ручного управления (поз. 6л) и силовой блок управления (поз. 6м) воздействует на систему «генератор – двигатель» (поз. 6н), изменяя скорость движения ленты агломерационной машины.
8.3.2. Система автоматического регулирования высоты слоя шихты на аглоленте
В качестве датчика уровня используется трехэлектродный индикатор откоса шихты (поз. 1а). Все три электрода имеют разную длину. Один из них постоянно погружен в шихту, другой находится вне ее, а положение третьего соответствует нормальному уровню шихты в загрузочной коробке. При уменьшении уровня шихты размыкается цепь между средним и первым электродом, а при повышении уровня замыкается цепь между средним и вторым электродом. Электродный датчик связан с релейным регулятором (поз. 1б), который через блок ручного управления (поз. 1в) активизирует пусковую аппаратуру (поз. 1г), включающую маломощный реверсивный двигатель и реостат в цепи обмотки возбуждения двигателя постоянного тока (поз. 1д) тарельчатого питателя шихты.
Схема управления работой питателя шихты обеспечивает наличие постоянного запаса шихты в загрузочной коробке, исключает значительные колебания уровня.
8.3.3. Система автоматического регулирования влажности шихты
В данной системе принято автоматическое регулирование подачи воды в душирующую установку IV по расходу шихты.
Причем расход шихты измеряют по скорости вращения тарельчатого питателя, измеряемой с помощью тахогенератора (поз. 2а). С тахогенератора сигнал поступает на вторичный прибор (поз. 2б), а затем – на автоматический регулятор (поз. 2в), пульт ручного управления (поз. 2г), магнитный пускатель (поз. 3д) и исполнительный механизм (поз. 2е), изменяющий расход воды на орошение с помощью регулирующего органа (поз. 2ж).
8.3.4. Система автоматического регулирования температуры
в горне
Система состоит из термопары (поз. 3а), автоматического потенциометра (поз. 3б), регулятора (поз. 3в), пульта ручного управления (поз. 3г), магнитного пускателя (поз. 3д) и исполнительный механизм (поз. 3е), воздействующего на поворотную заслонку (поз. 3ж), установленную на трубопроводе природного газа.
Известно, что термопары, работающие в тяжелых условиях зажигательного горна, часто выходят из строя. Иногда их заменяют термоимпульсной трубкой петлеобразной формы, через которую непрерывно протекает постоянное количество воды. До и после петли, помещенной в горн, устанавливают термометры сопротивления. Регулирующим импульсом для данной системы служит разность температур воды на входе и на выходе из петли.
8.3.5. Система автоматического регулирования соотношения расходов газ–воздух
Это обычная стандартная система, использовавшаяся и при автоматизации других тепловых объектов. Она состоит из сужающих устройств (поз. 4а – для газа и поз. 4б – для воздуха), дифференциальных манометров (поз. 4в и 4г), вторичных приборов (поз. 4д и 4е), автоматического регулятора (поз. 4ж), пульта (поз. 4з), магнитного пускателя (поз. 4и) и исполнительного механизма (поз. 4к), изменяющего расход воздуха с помощью поворотной заслонки (поз. 4л) на трубопроводе воздуха.
8.3.6. Система автоматического регулирования разрежения перед эксгаустером
Система включает отборное устройство (поз. 5а), дифференциальный манометр (поз. 5б), вторичный прибор (поз. 5в), автоматический регулятор (поз. 5г), пульт (поз. 5д), магнитный пускатель (поз. 5е) и исполнительный механизм (поз. 5ж), связанный с регулирующей поворотной заслонкой (поз. 5з) перед эксгаустером.
8.3.7. Система автоматического контроля температуры в вакуум–камерах
Контроль осуществляется с помощью одинарных и двойных термопар (поз. 6а–6е) и вторичного многоточечного потенциометра (поз. 6и).
ЛИТЕРАТУРА
1. Благовещенская М.М., Злобин Л.А. Информационные технологии систем управления технологическими процессами. М., «Высшая школа», 2005.
2. Текиев В.М., Яржемский А.С. Методические указания по оформлению дипломных (курсовых) проектов и работ. Владикавказ, изд-во «Терек», 2002.
3. Гущин С.Н. Телегин А.С., В.И. Лобанов и др. Теплотехника и теплоэнергетика металлургического производства. /Учебник для вузов. М., Металлургия, 1993.
4. Уткин Н.И. Производство цветных металлов. «Интермет Инжиниринг», 2004.
5. Тарасов А.В. Производство цветных металлов и сплавов. /Справочник в 3-х томах. Т.1. Общие вопросы цветной металлургии. М., Металлургия, 2001.
6. Зеликман А.Н. Металлургия тугоплавких редких металлов. М., Металлургия, 1986.
7. Козлов П.А. Вельц-процесс. М., ФГУП, изд. дом «Руда и металлы», 2002.
СОДЕРЖАНИЕ
Введение............................................................................ ........................................................................................... 1. Виды металлургических печей, особенности их автоматизации...................................................................... 2. Автоматизация процесса обжига цинкового концентрата в кипящем слое....................................................... 3. Автоматизация процесса обжига молибденитового концентрата в кипящем слое............................................ 4. Автоматизация вращающейся вельц-печи цинкового производства..................................................................... 5. Автоматизация вращающейся печи спекания глинозема.................................................................................... 6. Автоматизация вращающейся печи кальцинации глинозема.......................................................................... 7. Автоматизация процесса отражательной плавки медной шихты................................................................... 8. Автоматизация процесса агломерации свинцового концентрата....................................................................... Литература........................................................................ | 3 5 11 23 28 39 50 56 67 78 |
Дата добавления: 2018-02-28; просмотров: 2236; Мы поможем в написании вашей работы! |
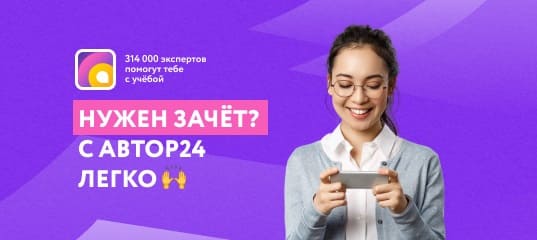
Мы поможем в написании ваших работ!