АВТОМАТИЗЦИЯ ВРАЩАЮЩЕЙСЯ ПЕЧИ
СПЕКАНИЯ ГЛИНОЗЕМА
5.1. ОПИСАНИЕ ТЕХНОЛОГИЧЕСКОГО ПРОЦЕССА
Термические процессы при производстве глинозема (в металлургии алюминия) встречают редко. К ним относятся в первую очередь спекание и кальцинацию, которые проводятся обычно во вращающихся трубчатых печах.
В печи спекания сода взаимодействует с бокситом с образованием твердой фазы алюмината натрия , а известь связывает кремнезем в силикат кальция
, который впоследствии легко выводится из цикла. На рис. 5.1 представлена схема вращающейся трубчатой печи спекания. Дробленая бокситная руда в смеси с известняком и содой подвергается мокрому измельчению. Полученная пульпа поступает в верхнюю холодную головку III печи I.
Конструктивно печь спекания – это барабан диаметром 2,5–3,0 м и длиной 50–70 м. Скорость вращения барабана колеблется в пределах 1,0–2,0 об/мин. Время пребывания материала в печи превышает 2–3ч. Печь отапливают природным газом с помощью горелок, установленных на нижней горячей головке II печи. Для сжигания газа в печь подается воздух. Отходящие газы проходят через пылеулавливающие устройства V (батарейные циклоны и электрофильтр) и выбрасываются в атмосферу дымососом VI. Пыль, собранная в пылеулавителях, содержит некоторое количество алюминия и потому возвращается в бункер возврата, откуда воздухом вдувается в печь по направлению потока газов. Температура спека на выходе из печи составляет 1100–1200 оС. Последующая гидрохимическая обработка чрезмерно горячего материала нарушает технологический процесс выщелачивания и снижает степень извлечения глинозема. Поэтому раскаленный спек после печи проходит через вращающийся трубчатый холодильник VII и, выйдя из него с температурой 110–130 оС, направляется на выщелачивание. Для охлаждения спека используется воздух, просасываемый через холодильник вентилятором IV, и вода, поступающая через брызгальные устройства VIII непосредственно на кожух холодильника. Подача в печь подогретого воздуха повышает температуру факела и экономичность сжигания газа.
|
|
Технологически печь можно разделить на четыре зоны. В первой по ходу материала зоне, в окрестности холодной головки печи, происходит дегидратация шихты, т.е. полное удаление влаги из нее. К концу этой подготовительной зоны материал прогревается до 900 оС. Вторая, средняя, зона служит для декарбонизации, т.е. для выделения углекислого газа из материала (разложение и
). Здесь же при температурах до 1200 оС начинается спекание. В третьей зоне при наиболее высоких температурах газового потока протекает основной процесс спекообразования, прогрев материала до 1200 оС и более. Основные технологические реакции связывания кремнезема в силикат кальция и образования алюмината натрия начинаются в середине зоны декарбонизации и заканчиваются в конце процесса спекания. Четвертая – зона охлаждения, температура шихты в этой зоне около 1100 оС.
|
|
5.2. ВЫБОР СИСТЕМ АВТОМАТИЧЕСКОГО КОНТРОЛЯ
И РЕГУЛИРОВАНИЯ
Производительность печи и степень полноты спекообразования определяются в значительной мере расходом пульпы, поступающей в печь. Система автоматического регулирования расхода пульпы должна обеспечить максимальную производительность печи при заданном качестве готового продукта. Качеством готовой продукции и является в данном случае степень полноты спекообразования, т.е. величина извлечения глинозема и окиси кремния из шихты. Способов непрерывного автоматического определения степени полноты спекообразования пока нет. Поэтому во всех внедренных вариантах систем регулирования расхода материала качество спека не учитывается. Самым простым вариантом является автоматическое поддержание расхода пульпы постоянным. При наличии систем автоматического регулирования плотности и состава пульпы в цехах подготовки ее (перед операциией спекания) стабилизация расхода пульпы в печь улучшает технологический режим спекания, повышает экономические показатели его. Однако, как и все вообще системы стабилизации отдельных технологических параметров, такая схема принципиально несовершенна. Здесь не учитываются неизбежные в производственных условиях колебания физических свойств и химического состава пульпы, изменения температур в печи и т.д.
|
|
Большое количество тепла расходуется в печи на испарение влаги, содержащейся в пульпе, а течение процесса спекообразования также зависит от получаемого материалом тепла. Следовательно, можно считать, что задача системы автоматического регулирования подачи пульпы состоит в соблюдении баланса прихода–расхода тепла при максимально возможной подаче материала. Эту же задачу можно сформулировать и иначе: обеспечить максимально возможную подачу материала в печь при сохранении заданного качества спека и максимально допустимой температуры в горячей головке печи.
При автоматическом поддержании температуры у горячей головки печи постоянной можно косвенно определить количество тепла, потребляемое материалом, по температуре в конце печи (в верхней головке). В такой системе при повышении температуры отходящих газов регулятор должен увеличить расход пульпы.
|
|
При этом для увеличения устойчивости системы регулирования целесообразно импульс по температуре отходящих газов ввести в качестве корректирующего в систему стабилизации подачи пульпы.
Как уже было отмечено, для нормальной работы системы автоматического регулирования подачи пульпы необходима стабилизация температуры у горячей головки печи. Постоянная температура факела улучшает режим спекообразования в третьей технологической зоне, позволяет снизить расход топлива. Система регулирования температуры в третьей зоне печи должна воздействовать на подачу топлива, как и в большинстве пламенных печей металлургии.
Известно, что экономичность режима горения любого вида топлива во многом зависит от правильной подачи воздуха. Наиболее распространенной схемой автоматического регулирования подачи воздуха является поддержание заданного соотношения расходов топливо–воздух. Этот же принцип может быть использован и для печи спекания. Установку задания регулятору соотношения производит дежурный персонал вручную в соответствии с показателями режима горения. Такими показателями могут служить содержание кислорода и двуокиси углерода в отходящих газах печи. Процентное содержание СО2 в отходящих газах еще не определяет полностью режим горения, так как материал богат карбонатами, выделяющими углекислый газ. Поэтому предусматривается автоматический контроль двух компонентов газовой смеси.
Тяговый режим печи влияет на теплопередачу от потока газов к материалу. Изменения разрежения в холодной головке печи могут вызвать колебания температуры в первой зоне, что неблагоприятно отразится на работе системы автоматического регулирования подачи пульпы. С другой стороны, нестабильный тяговый режим ухудшает работу пылеосадительных устройств, увеличивает унос пыли в атмосферу. Уменьшение разрежения в холодной головке печи может вызвать выбивание газов из неплотностей горячей головки. Увеличение разрежения приводит к большим подсосам холодного воздуха и к смещению технологических зон в печи. Регулирование разрежения можно производить как и для большинства пламенных печей воздействием на поворотный шибер перед дымососом.
Контроль давления в горячей головке печи позволяет с большой точностью выбрать задание регулятору тяги, так как система автоматического регулирования тяги должна поддерживать в горячей головке печи небольшое разрежение или атмосферное давление. Кроме того, перепад давлений по печи характеризует движение газового потока вдоль нее, состояние внутренней поверхности барабана и т.п.
Распределение температур газового потока и температур материала вдоль печи является важным фактором процесса спекообразования, автоматический контроль температур дает возможность следить за ходом технологического процесса и вмешиваться в него по мере необходимости. Температуру внутри печи целесообразно контролировать в четырех точках. Стабильный режим спекания характеризуется определенными, известными для каждой печи границами технологических зон. Смещение этих границ в сторону горячей головки печи означает, что печь перегружена материалом, глинозем не полностью извлекается из шихты. Обратное смещение границ может свидетельствовать о недогрузке печи. Практически границы технологических зон можно определить по температурам в печи, поэтому такое значение придают системе контроля температуры.
Процесс охлаждения спека обычно не автоматизирован, так как нет необходимости поддерживать строго постоянную температуру материла на выходе из вращающегося холодильника. К тому же автоматический замер температуры спека не удается пока осуществить с достаточной степенью надежности. Поэтому управление подачей охлаждающей воды производят вручную с помощью вентиля. Количество охлаждающего воздуха, проходящего через холодильник, зависит от работы системы управления подачей воздуха в печь.
От распределения температур по газовому тракту зависит режим работы установок пылеулавливания. Контроль температур за холодной головкой печи и перед дымососом позволяет своевременно обнаружить различные нарушения режима работы газового тракта.
Положение и конфигурация факела в печи во многом зависят от давления воздуха перед горелками. Изменение этого давления вызывает перемещение факела вдоль печи, что отражается на спекообразовании. Контроль всех указанных параметров необходим обслуживающему персоналу для правильного ведения режима горения топлива в печи.
Проведенный выше анализ особенностей процесса спекания боксита с содой и известью в трубчатой вращающейся печи позволяет назвать системы автоматического контроля и регулирования, использование которых обеспечит высокие технико-экономические показатели процесса и предотвратит возникновение аварийных ситуаций на соответствующем производстве:
1. Системы автоматического регулирования
– расхода пульпы в печь с коррекцией по температуре в верхней головке печи;
– разрежения в верхней головке печи путем изменения положения заслонки на трубопроводе с дымовыми газами;
– температуры в нижней (горячей) головке печи путем изменения расхода природного газа;
– соотношения расходов газ–воздух путем изменения расхода воздуха.
2. Системы автоматического контроля
– содержания углекислого газа и кислорода в отходящих газах;
– температуры отходящих газов, газов на выходе из печи, температуры различных зон печи;
– давления воды, поступающей в холодильник, природного газа перед горелкой, горячего воздуха после холодильника;
– давления–разрежения в горячей головке печи.
Номинальные значения выходных параметров процесса спекания приведены в табл. 5.1.
Таблица 5.1
№№ п/п | Наименование параметра | Единица измерения | Номинальная величина |
1. | Температура в верхней головке печи | оС | 800–900 |
2. | Температура в нижней головке печи | оС | 1100–1200 |
3. | Температура в печи по зонам | оС | 800–1200 |
4. | Температура отходящих газов | оС | 800 |
5. | Разрежение в верхней головке печи | Па | 80 |
6. | Давление воды, поступающей в холодильник | кПа | 200 |
7. | Давление природного газа перед горелкой | кПа | 130 |
8. | Давление горячего воздуха после холодильника | кПа | 100 |
9. | Содержание СО2 в отходящих газах | % | 10–15 |
10. | Содержание О2 в отходящих газах | % | 0,5–2,0 |
5.3. ОПИСАНИЕ СИСТЕМ АВТОМАТИЧЕСКОГО КОНТРОЛЯ
И РЕГУЛИРОВАНИЯ (рис. 5.2)
5.3.1. Система автоматического регулирования расхода пульпы в печь с коррекцией по температуре в верхней головке печи
Для измерения расхода пульпы обычно применяют щелевой расходомер истечения (поз. 4а). Щелевой расходомер истечения представляет собой бачок, разделенный на две камеры перегородкой. Пульпа подается в одну из камер, откуда через щель в перегородке перетекает в другую камеру, а из нее – дальше в процесс. Известная зависимость между уровнем во второй камере и расходом истечения позволяет судить о расходе. Уровень во второй камере расходомера измеряют по гидростатическому давлению столба пульпы в ней с помощью дифманометра (поз. 4б) со вторичным прибором (поз. 4в).
Температуру в середине зоны дегидрадации (испарения) измеряют вращающейся термопарой (поз. 5а) и электронным потенциометром (поз. 5б). Использование в качестве корректирующего импульса температуру внутри печи, а не после холодной головки ее позволяет избежать влияния подсосов холодного воздуха на датчик температуры и получить более представительный импульс. Сигналы по расходу пульпы от вторичного прибора (поз. 4в) и по температуре от потенциометра (поз. 5б) суммируются и поступают на вход автоматического регулятора (поз. 4г), который через блок ручного управления (поз. 4д) и магнитный пускатель (поз. 4е) воздействует на исполнительный механизм (поз. 4к), который изменяет положение регулирующего органа (поз. 4и) – специального пульпового клапана.
5.3.2. Система автоматического регулирования разрежения
в верхней головке печи
Отбор импульса производится в верхней головке печи (поз. 6а), откуда сигнал направляется на бесшкальный манометр (поз. 6б), а затем – на вторичный прибор (поз. 6в), автоматический регулятор (поз. 6г), блок ручного управления (поз. 6д), магнитный пускатель (поз. 6е) и исполнительный механизм (поз. 6и), управляющий дымовым шибером (поз. 6к).
5.3.3. Система автоматического регулирования температуры
в нижней головке печи
Контроль температуры осуществляется с помощью «вращающейся» термопары (поз. 9а), установленной в горячей зоне печи, и электронного потенциометра (поз. 9б). С потенциометра электрический сигнал поступает на автоматический регулятор (поз. 9в), блок ручного управления (поз. 9г) и затем – на магнитный пускатель (поз. 9д), который связан с исполнительным механизмом (поз. 9е), изменяющим положение регулирующего органа (поз. 9ж), установленного на трубопроводе природного газа.
5.3.4. Система автоматического регулирования соотношения расходов газ–воздух
Система имеет в своем составе приборы контроля расходов газа и воздуха. Расход газа и воздуха измеряют расходомерами, включающими сужающие устройства (поз. 12а, 13а), дифманометры (поз. 12б, 13б) и вторичные приборы (поз. 12в, 13в), сигналы с которых поступают на автоматический регулятор (поз. 12г), а затем – блок ручного управления (поз. 12д), магнитный пускатель (поз. 12е) и исполнительный механизм (поз. 12и), который управляет поворотной дроссельной заслонкой (поз. 12к) на трубопроводе подогретого воздуха после холодильника.
5.3.5. Система автоматического контроля содержания СО2
и О2 в отходящих газах
Система включает отборное устройство (поз. 1а), установленное в трубопроводе с дымовыми газами после циклона V, и газоанализаторы:
– электрический (поз. 1б) со вторичным прибором (поз. 1г) для определения содержания СО2 в дымовых газах;
– термомагнитный (поз. 1в) со вторичным прибором (поз. 1д) для определения содержания О2.
5.3.6. Системы автоматического контроля температуры
в различных точках технологической схемы
Для измерения температуры газов на выходе из печи и после циклона используют термопары (поз. 3а, 2а), вмонтированные в газоход, и электронные потенциометры (поз. 3б, 2б).
Для измерения температуры в различных зонах печного пространства используют вмонтированные во вращающийся барабан печи термопары (поз. 7а), с которых через токосъемные устройства сигналы поступают на многоточечный электронный потенциометр (поз. 7б).
5.3.7. Системы автоматического контроля давления воды,
природного газа и воздуха
Для контроля давления воды, поступающей в холодильник VII, используют отборное устройство (поз. 8а), бесшкальный манометр (поз. 8б) и вторичный прибор (поз. 8в).
Давление природного газа, используемого для отопления, измеряют комплектом: отборное устройство (поз. 11а), бесшкальный манометр (поз. 11б), вторичный прибор (поз. 11в).
Давление воздуха, поступающего из холодильника, измеряют на входе в нижнюю головку печи, используя отборное устройство (поз. 14а), бесшкальный манометр (поз. 14б) и вторичный прибор (поз. 14 в).
5.3.8. Система автоматического контроля
давления – разрежения в горячей головке печи
Система включает отборное устройство (поз. 10а), бесшкальный тягонапоромер (поз. 10б) и вторичный прибор (поз. 10в).
Дата добавления: 2018-02-28; просмотров: 1772; Мы поможем в написании вашей работы! |
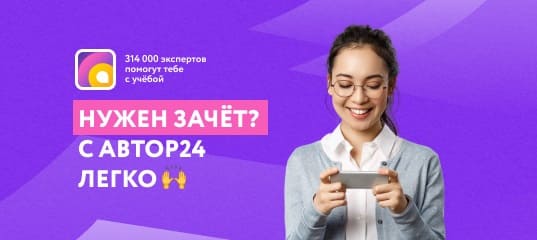
Мы поможем в написании ваших работ!