АВТОМАТИЗАЦИЯ ПРОЦЕССА ОТРАЖАТЕЛЬНОЙ ПЛАВКИ МЕДНОЙ ШИХТЫ
7.1. ОПИСАНИЕ ТЕХНОЛОГИЧЕСКОГО ПРОЦЕССА
Печи для отражательной плавки получили наибольшее распространение в медной промышленности. Сущность отражательной плавки на штейн сульфидных концентратов и рудной мелочи заключается в том, что шихта плавится за счет тепла от сжигания углеродистого топлива в газовом пространстве над ванной расплава в печи с горизонтально расположенным рабочим пространством (рис. 7.1).
Шихту при этом загружают на ванну или на откосы вдоль боковых стен печи. Раскаленные топочные газы, проходя над поверхностью ванны и шихты, нагревают их, а также стены и свод, и покидают печь, имея еще сравнительно высокую температуру (выше температуры плавления шлака). Теплопередача в печи осуществляется в основном за счет лучеиспускания от раскаленных стен, свода и раскаленного факела.
Нагреваясь постепенно до высокой температуры, шихта плавится. Металлы, обладающие высоким сродством к кислороду, при этом концентрируются в оксидном расплаве – шлаке. Медь, никель, благородные металлы и часть железа и серы переходят в сульфидную фазу – штейн. Обладая ничтожной взаимной растворимостью и различной плотностью (так, плотность штейна »5 т/м3, а шлака – »3 т/м3), продукты плавки при отстаивании разделяются на два слоя: шлак располагается сверху, а штейн – под ним.
Рис. 7.1. Схема плавления шихты на откосах отражательной печи:
|
|
1 – загрузка шихты; 2 – факел горящего топлива; 3 – шихтовой откос;
4 – направления потоков теплоизлучения от факела.
В процессе плавки железо окисляется кислородом из оксида меди, а медь переходит в сульфид по следующей реакции:
.
Таким образом, при отражательной плавке происходит перевод основной массы пустой породы в шлак и концентрация ценных компонентов в штейне.
Отражательная медеплавильная печь выложена из огнеупорного кирпича. Длина печи достигает 35–40 м, высота – до 3,0–3,5 м. Ширина печи колеблется от 6 до 10 м в зависимости от производительности. Концентрат в печь загружают через воронки, расположенные над отверстиями в своде печи вдоль боковых сторон.
Отражательная печь – это типичная пламенная печь, отапливаемая газом, поступающим в рабочее пространство через горелки, установленные в окнах передней торцевой стены. Воздух для сжигания газа нагнетается в печь вентилятором. Температура в первой, плавильной, зоне печи достигает 1550 оС. В конце печи температура еще высока – до 1200–1250 оС. Примерно треть длины печи в конце ее занимает зона отстаивания, где происходит разделение штейна и шлака. Тепловой коэффициент полезного действия печи невысок, так как температура отходящих газов очень высока. Тепло отходящих газов обычно используется в котле–утилизаторе, расположенном на пути газов за печью, при этом удается снизить температуру газов до 300–400 оС. Часть дымовых газов отводится через обводной дымовой боров мимо котла–утилизатора. Перед котлом и в обводном борове установлены дымовые шиберы (водоохлаждаемые).
|
|
Выпуск шлака производят через летку в задней торцевой стенке печи, а штейна – через несколько отверстий в боковых стенках. Выпуск штейна и шлака осуществляется периодически.
7.2. ВЫБОР СИСТЕМ АВТОМАТИЧЕСКОГО КОНТРОЛЯ
И РЕГУЛИРОВАНИЯ
Центральной системой схемы автоматизации процесса отражательной плавки на штейн должна быть система загрузки материала в печь по импульсу от качества готового продукта. Однако химический состав штейна сейчас непрерывно автоматически не измеряется. Кроме того, объем печи очень велик и изменения в подаче материала отразятся на качестве готового продукта только через значительный период времени. Наконец, выпуск штейна и шлака производится не непрерывно. Перечисленные обстоятельства не позволяют создать надежную систему автоматического регулирования загрузки печи по качеству готовой продукции либо по параметрам режима плавки. Поэтому для подавляющего большинства отражательных медеплавильных печей применяют непрерывную равномерную подачу исходного материла.
|
|
Подачу топлива в печь следовало бы поставить в зависимость от потребления тепла материалом. Однако полностью учесть тепло, потребляемое расплавляемой шихтой, потери тепла с отходящими газами, штейном и шлаком не представляется возможным. Поэтому система регулирования подачи топлива в печь в соответствии с количеством потребляемого тепла сейчас неосуществима. Как правило, управление расходом топлива осуществляется по импульсу от температуры в печи. Весьма значительные размеры печи, наличие в ней большого количества загрузочных окон, охлаждающих факел, не позволяют получить единый представительный отбор импульса по температуре в печи. Так, например, повышение температуры в начале печи может не вызвать соответствующего повышения температуры на выходе из нее ввиду того, что на температуру в конце печи влияет не только начальная температура, но и подсосы воздуха через загрузочные окна, и неравномерное потребление тепла материалом, и другие факторы. Регулятор подачи топлива должен получить несколько импульсов по состоянию температурного поля печи. Две точки наиболее важны для технологического режима плавки. Это максимальная температура в зоне плавления и температура в конце печи. Первая температура характеризует режим плавления, режим основного технологического процесса, а вторая – вязкость шлака, температуру штейна и шлака, от которых зависит их качество.
|
|
Воздух в отражательной печи используется лишь для сжигания топлива. Поэтому наиболее распространенной схемой регулирования подачи воздуха является управление расходом его по соотношению топливо – воздух. Неорганизованные подсосы воздуха в отражательную печь велики из-за большого количества загрузочных отверстий. При этом величина подсосов меняется во времени, что снижает качество регулирования, так как учесть количество воздуха, поступающего в печь помимо вентилятора, не удается. Улучшить систему регулирования можно введением в нее корректирующего импульса по результатам газового анализа потока на выходе из печи. Недостатком схемы с коррекцией является технологическое запаздывание, вызванное значительной длиной печи. В предлагаемой схеме реализуется принцип регулирования подачи вентиляторного воздуха по соотношению газ – воздух. Задание регулятору соотношения меняется вручную в соответствии с режимными картами и показаниями газоанализаторов на кислород и углекислый газ. Автоматический анализ отходящих газов печи на СО2 и О2 помогает дежурному персоналу следить за режимом горения, устанавливать задание регулятору подачи воздуха.
Разрежения по газовому тракту отражательной печи не постоянны из-за наличия подсосов неорганизованного воздуха и периодичности выгрузки материалов. Разрежение у боковых стенок печи в начале ее составляет около 20 Па благодаря инжекции факела. К концу печи разрежение снижается до 5–10 Па, а в газоходе перед котлом–утилизатором вновь несколько увеличивается. От разрежений в печи во многом зависит режим горения (положение факела), унос пыли с газами, работа котла–утилизатора и тяговых устройств, условия труда.
Регулирование тяги в печи целесообразно производить по импульсу от разрежения в начале газоперепускного борова воздействием на дымовой шибер на обводном борове. Использование обводного борова для регулирования тяги позволяет стабилизировать газовый поток через котел–утилизатор, улучшить режим работы его.
Регулирующий дымовой шибер выполнен водоохлаждаемым для защиты от высокой температуры газов. Температура воды на выходе из шибера не должна превышать 80–85 оС во избежание парообразования внутри водяной системы. Контроль и сигнализация температуры охлаждающей воды после шибера позволяют предотвратить аварийный прожог шибера при уменьшении по какой-либо причине подачи воды.
Разрежение и температура отходящих газов после котла–утилизатора характеризуют тепловой режим котла, степень использования тепла в нем. От этих параметров зависит экономичность работы всей установки в целом.
Высокие тепловые напряжения в печи и интенсивный износ кладки потоком запыленных газов могут привести к прожогу печи в отдельных наиболее уязвимых точках. Под печи также работает в тяжелых температурных условиях и может частично прогореть. Такие аварии весьма серьезны, так как требуют длительной остановки печи на ремонт и поэтому необходимо непрерывно контролировать состояние свода и пода печи.
Проведенный выше анализ процесса отражательной плавки медьсодержащего сырья как объекта автоматизации позволяет назвать системы автоматического контроля и регулирования, использование которых обеспечило бы высокие технико-экономические показатели процесса плавки и предотвратило бы возникновение в цехе аварийных ситуаций:
1. Системы автоматического регулирования
– соотношения расходов газ–воздух воздействием на расход воздуха;
– температуры в реакционном пространстве печи воздействием на расход газа;
– разрежения в газоходном тракте перед котлом–утилизатором воздействием на дымовой шибер.
2. Системы автоматического контроля
– температуры, расхода и давления воздуха для сжигания газа;
– расхода и давления газа перед горелкой;
– температуры в различных точках пода печи;
– содержания СО2 и О2 в отходящих газах;
– температуры воды, охлаждающей дымовой шибер;
– температуры и разрежения в газоходном тракте после котла–утилизатора.
Номинальные значения выходных параметров процесса отражательной плавки приведены в табл. 7.1.
Таблица 7.1.
№№ п/п | Наименование параметра | Единица измерения | Номинальная величина |
1. | Температура в реакционном пространстве печи | оС | 1550 |
2. | Разрежение перед котлом–утилизатором | Па | 5–10 |
3. | Температура воздуха для горения | оС | 200–250 |
4. | Давление воздуха | КПа | 2,0–2,5 |
5. | Давление газа | КПа | 130 |
6. | Содержание СО2 в отходящих газах | % | 10–17 |
7. | Содержание О2 в отходящих газах | % | 0,5–2 |
8. | Температура воды после охлаждения дымового шибера | оС | 80–85 |
9. | Температура газа после котла–утилизатора | оС | 300–400 |
10. | Разрежение после котла–утилизатора | Па | 80 |
7.3. ОПИСАНИЕ СИСТЕМ АВТОМАТИЧЕСКОГО КОНТРОЛЯ И РЕГУЛИРОВАНИЯ (рис. 7.2)
7.3.1. Система автоматического регулирования соотношения расходов газ–воздух имеет в своем составе приборы для контроля расходов газа и воздуха. Расход газа и воздуха измеряют расходомерами, включающими сужающие устройства (поз. 4а, 4г), дифманометры (поз. 4б, 4д) и вторичные приборы (поз. 4в, 4е), сигналы с которых поступают на автоматический регулятор (поз. 4ж), а затем – блок ручного управления (поз. 4з), магнитный пускатель (поз. 4и) и исполнительный механизм (поз. 4к), который управляет поворотной дроссельной заслонкой на трубопроводе воздуха.
7.3.2. Система автоматического регулирования температуры
в реакционном пространстве печи
В данном проекте принято автоматическое регулирование подачи топлива по температурам в начале и конце печи. Такая двухимпульсная система принципиально более правильна, чем одноимпульсная – по температуре в ядре горения факела, что связано с весьма значительными размерами печи и наличием в ней большого количества загрузочных окон, ограничивающих возможность получить единый представительный отбор импульса по температуре в печи. Температуру в печи измеряют радиационными пирометрами, включающими телескопы (поз. 5а), которые визированы на дно калильных стаканов, вмонтированных в свод печи, и электронных потенциометров (поз. 5б), с которых сигнал подается на автоматический регулятор (поз. 5в), блок ручного управления (поз. 5г), магнитный пускатель (поз. 5д) и исполнительный механизм (поз. 5е), воздействующий на регулирующий орган, установленный на трубопроводе подачи газа.
7.3.3. Система автоматического регулирования разрежения
на выходе печи
Отбор импульса производится в начале газоперепускного борова (поз. 10а), откуда сигнал направляется на дифманометр (поз. 10б), затем – на вторичный прибор (поз. 10 в), автоматический регулятор (поз. 10г), блок ручного управления (поз. 10д), магнитный пускатель (поз. 10е) и исполнительный механизм (поз. 10ж), управляющий дымовым шибером.
7.3.4. Система автоматического контроля температуры
воздуха
В комплект приборов входит термопреобразователь сопротивления (поз. 1а) и вторичный электронный прибор показывающий и самопишущий (поз. 1б).
7.3.5. Система автоматического контроля давления воздуха
Отбор давления из воздухопровода осуществляется отборным устройством (поз. 2а), а измерение давления – бесшкальным манометром (поз. (2б) и вторичным прибором (поз. 2в).
7.3.6. Система автоматического контроля давления газа
Построена аналогично предыдущей системе и включает отборное устройство (поз. 3а), манометр (поз. 3б) и вторичный прибор (поз. 3в).
7.3.7. Система автоматического контроля температуры
пода печи
Измерение температуры осуществляется с помощью термопар, вмонтированных в кладку пода печи в нескольких точках (поз. 6а). Вторичным прибором служит многоточечный автоматический потенциометр (поз. 6б).
7.3.8. Система автоматического контроля содержания СО2 в отходящих газах включает отборное устройство (поз. 7а), электрический газоанализатор содержания углекислого газа (поз. 7б) со вторичным прибором (поз. 7в).
7.3.9. Система автоматического контроля содержания О2
в отходящих газах
Система состоит из отборного устройства (поз. 8а), магнитного газоанализатора на О2 (поз. 8б) со вторичным прибором (поз. 8в).
7.3.10. Система автоматического контроля температуры воды после охлаждения дымового шибера
Комплект приборов включает термопреобразователь сопротивления (поз. 9а) и вторичный регистрирующий прибор (поз. 9б).
7.3.11. Система автоматического контроля температуры
отходящих газов
Измерение осуществляется с помощью термопары (поз. 11а) и электронного потенциометра (поз. 11б).
7.3.12. Система автоматического контроля разрежения после котла–утилизатора
Включает отборное устройство (поз. 12а), тягонапоромер бесшкальный (поз. 12б) и вторичный прибор (поз. 12в).
Дата добавления: 2018-02-28; просмотров: 1814; Мы поможем в написании вашей работы! |
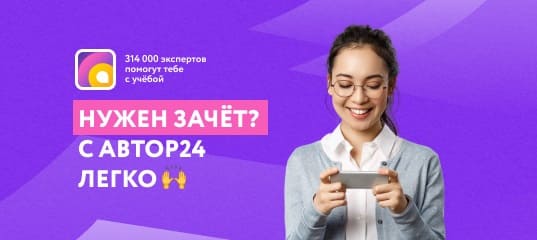
Мы поможем в написании ваших работ!