АВТОМАТИЗАЦИЯ ПРОЦЕССА ОБЖИГА. В. М. Текиев, А. Л. Рутковский, М
Nbsp;
В. М. Текиев, А. Л. Рутковский, М. Э. Багаева
ПРИНЦИПЫ И СХЕМЫ АВТОМАТИЗАЦИИ ПЕЧЕЙ ЦВЕТНОЙ МЕТАЛЛУРГИИ
Методические указания по выполнению курсового
И дипломного проектов
Для студентов специальностей 150103.65 – «Теплофизика, автоматизация и экология промышленных печей, 20301.65 – «Автоматизация промышленных печей и производств»
Владикавказ 2009
ФЕДЕРАЛЬНОЕ АГЕНТСТВО ПО ОБРАЗОВАНИЮ
СЕВЕРО-КАВКАЗСКИЙ ГОРНО-МЕТАЛЛУРГИЧЕСКИЙ ИНСТИТУТ
(ГОСУДАРСТВЕННЫЙ ТЕХНОЛОГИЧЕСКИЙ УНИВЕРСИТЕТ)
В. М. Текиев, А. Л. Рутковский, М. Э. Багаева
ПРИНЦИПЫ И СХЕМЫ АВТОМАТИЗАЦИИ ПЕЧЕЙ ЦВЕТНОЙ МЕТАЛЛУРГИИ
Методические указания по выполнению курсового
и дипломного проектов
Для студентов специальностей 150103.65 – «Теплофизика, автоматизация и экология промышленных печей, 20301.65 – «Автоматизация промышленных печей и производств»
Допущено редакционно-издательским советом Государственного образовательного учреждения высшего профессионального образования «Северо-Кавказский горно-металлургический институт (государственный технологический университет)»
Владикавказ 2009
УДК 669.2/8-52
ББК 34.33
П 75
Текиев В. М., Рутковский А. Л., Багаева М. Э.
П 75 Принципы и схемы автоматизации печей цветной металлургии. – Владикавказ: Издательство СКГМИ (ГТУ) «Терек», 2009. – 78 с.
© Текиев В. М., 2009
|
|
© Рутковский А. Л., 2009
© Багаева М. Э., 2009
© Изд-во СКГМИ (ГТУ) «Терек», 2009
Подписано в печать 27.07.09. Формат 60х84 1/16. Бумага офсетная.
Гарнитура «Таймс». Печать на ризографе.
Тираж 93 экз. Объем 4,5 усл. п.л. Заказ №
Отпечатано в отделе оперативной полиграфии СКГМИ (ГТУ)
362021, Владикавказ, ул. Николаева, 44.
ВВЕДЕНИЕ
Автоматизация производственного процесса представляет собой сложный комплекс мероприятий, цель которых – освободить человека от функций непосредственного управления процессом, передав их специальным устройствам. Для того чтобы технологическое оборудование работало в требуемом режиме, т.е. с высоким коэффициентом полезного действия, с заданной производительностью, давало продукцию высокого качества и работало надежно, необходимо поддерживать величины, характеризующие процесс, постоянными или изменяющимися во времени по определенному закону, который либо известен заранее, либо автоматически определяется во время регулирования.
При проектировании схем автоматизации любых технологических процессов решаются следующие основные вопросы: выбор регулируемых параметров и регулирующих воздействий для систем автоматического управления процессом; выбор параметров автоматического контроля; выбор средств автоматического контроля и регулирования.
|
|
При разработке функциональной схемы автоматизации особенно важен правильный выбор технологических параметров, подлежащих автоматическому регулированию. Обычно для решения этой задачи исходят из известных логических зависимостей между параметрами, влияющими на процесс, и параметрами, характеризующими ход процесса.
В качестве регулируемых величин следует выбирать параметры, непосредственно влияющие на качество готовой продукции, на весь ход технологического процесса. Это прежде всего величины, от которых в наибольшей степени зависят производительность и экономичность работы агрегата, химические и физические свойства продукта на выходе из него. При выборе регулируемых параметров необходимо учитывать главным образом экономический эффект от внедрения автоматики.
Регулирующее воздействие системы должно обеспечить наиболее полное и быстрое изменение регулируемого параметра в требуемом направлении. Вместе с тем регулирующее воздействие одной системы по возможности не должно мешать работе соседних систем.
Непрерывно контролируемые технологические параметры должны наиболее полно отражать ход автоматизируемого процесса и состояние технологического оборудования. Эти величины должны, прежде всего, отражать качество готового продукта, производительность оборудования и экономичность процесса. Кроме того, для наблюдения за режимом работы систем автоматического регулирования необходим непрерывный контроль всех регулируемых параметров. При этом установка каждой системы контроля должна быть строго обоснована, так как завышение без особой необходимости числа контрольно–измерительных приборов уменьшает экономическую эффективность от внедрения автоматики.
|
|
Большое значение имеет выбор соответствующих приборов и регуляторов. Выбор средств автоматизации определяется наличием вспомогательной энергии для измерительных приборов и регуляторов; условиями применения автоматической аппаратуры (агрессивностью, абразивностью, кристаллизуемостью и загрязненностью измеряемой среды); необходимой точностью и быстродействием устройств автоматики; однотипностью аппаратуры и удобством ее обслуживания.
Предлагаемое авторами пособие – «Принципиальные схемы автоматизации печей цветной металлургии» – ставит своей целью оказание помощи студентам специальностей «Автоматизация технологических процессов и производств», «Теплофизика, автоматизация и экология промышленных печей» и «Металлургия цветных металлов» при выполнении ими курсовых проектов и разделов дипломных проектов, связанных с разработкой схем автоматизации процессов цветной металлургии, протекающих в промышленных печах различного принципа действия и различного назначения.
|
|
Пособие может быть полезным и при изучении теоретических учебных курсов, связанных с предметом данных методических указаний.
ВИДЫ МЕТАЛЛУРГИЧЕСКИХ ПЕЧЕЙ,
ОСОБЕННОСТИ ИХ АВТОМАТИЗАЦИИ
Металлургической печью называют устройство для нагрева, обжига или плавления материала с целью дальнейшей обработки его или придания ему требуемых свойств. По назначению печи цветной металлургии можно разделить на плавильные и нагревательные. При плавке материал в результате повышения температуры расплавляется и продукты плавки разделяются по плотности. По химизму процесса плавка может быть восстановительной, окислительной, осадительной и т.д. К основным типам плавильных печей следует отнести шахтные и отражательные печи для плавки руд и концентратов, а также пламенные рафинировочные печи. В нагревательных печах обрабатываемый материал нагревается ниже температуры плавления. Процессы, протекающие в нагревательных печах, весьма разнообразны. К ним относится прежде всего обжиг материала, который может быть в зависимости от химизма процесса восстановительным, окислительным, сульфатизирующим и т.д. Следует также назвать обжиг со спеканием, сушку материала, спекание, возгонку, кальцинацию, термическую обработку полуфабрикатов и другие процессы, протекающие в нагревательных печах.
По режиму работы печи можно разделить на периодические и непрерывного действия. По способу передачи тепла материалу различают печи с радиационным теплообменом, конвективным теплообменом и смешанного типа. Так, например, в отражательных печах тепло передается материалу главным образом излучением (радиацией). В шахтных печах имеет место конвективный теплообмен. Во вращающихся печах передача тепла происходит тем и другим способом.
Решение принципиальных вопросов автоматизации прирометаллургических процессов во многом зависит от отмеченных выше особенностей печей различных типов. Так, для плавильных печей система регулирования температуры должна поддерживать максимально возможную для данной конструкции печи температуру. Величина ее при этом ограничивается только условиями надежности работы кладки и других элементов печи, а не требованиями технологического режима.
В то же время в печах для обжига или спекания материала повышение температуры может привести к расплавлению шихты, что недопустимо с точки зрения технологии. Подача воздуха в отражательные печи, сушильные барабаны, вращающиеся печи кальцинации или спекания регулируется обычно в соответствии с режимом горения в рабочем пространстве печи, так как воздух здесь предназначен только для сжигания топлива. А в печах кипящего слоя, вращающихся вельц-печах воздух участвует в технологическом процессе, поэтому система автоматического регулирования подачи воздуха должна быть построена с учетом показателей технологического режима обжига, вельцевания. Для автоматического регулирования технологического режима печей периодического действия (нагревательные устройства различных типов) широко применяют системы программного регулирования, в то время как для печей непрерывного действия чаще всего используют системы стабилизации отдельных параметров процесса.
При всем многообразии металлургических печей общим для всех конструкций является передача тепла материалу. Подавляющее большинство печей отапливается газообразным, жидким или твердым топливом. Углерод, являясь основной горючей составляющей любого топлива, иногда участвует в качестве восстановителя в технологическом процессе. Широкое применение для отопления металлургических печей находит природный газ. Для сжигания газообразного топлива используют щелевые, беспламенные и инжекционные горелки. Твердое кусковое топливо (кокс, коксовая мелочь) обычно подают в печи в смеси с основным материалом. Измерение расхода топлива осуществляется с помощью весоизмерителей непрерывного действия различных типов, а управление подачей топлива – с помощью автоматических дозаторов, тарельчатых и другого типа питателей. Иногда используют в качестве топлива мазут (жидкое топливо).
Металлургическая печь представляет собой тепловой агрегат. Поэтому работа печи зависит главным образом от теплового режима. Тепловым режимом называют изменение во времени тепловыделения в рабочем пространстве печи. Основные системы автоматического регулирования теплового режима – управление подачей топлива, подачей воздуха и тягой – внедрены почти на всех печах металлургической промышленности. Но автоматизация теплового режима еще не означает полной автоматизации какой-либо печи, так как задачей печи является не сжигание топлива, а получение готового продукта заданного качества и в максимальном количестве (или за минимальное время). Полная, комплексная автоматизация агрегата должна обеспечить выполнение этой задачи. Такие системы оптимального регулирования пока еще почти не применяются для печей цветной металлургии. Причины этого кроются в неприспособленности многих агрегатов для автоматизации, в отсутствии датчиков для определения качества материалов, в сложности многих технологических процессов.
Большое внимание всегда уделяется режиму загрузки материалов в печь. Чаще всего в металлургическую печь загружают смесь нескольких компонентов шихты. Правильная дозировка их и своевременное смешивание (шихтовка) обеспечивают равномерный режим печи, заданное качество материала на выходе, максимальную производительность агрегата. Наиболее распространены в настоящее время системы автоматической стабилизации загрузки вне зависимости от технологического режима и качества исходного и готового продукта.
Конечной целью любого пирометаллургического процесса является получение в чистом виде нужного металла или его соединений. Необходимым условием нормального течения технологического процесса является выделение в печи достаточного количества тепла при сжигании топлива. Таким образом, тепловой режим любой печи – это важнейшая составная часть ее технологического режима. Тесная связь технологического и теплового процессов несомненна, но при изучении схем автоматизации печных установок их все же следует разграничивать, так как принципы автоматизации здесь различны.
Тепловой режим печи является основным, но не единственным фактором, определяющим характер технологического процесса. Иначе говоря, количество и качество готового продукта, получаемого из печи, зависит не только от теплового режима, но и от химического состава материала, загружаемого в печь, от фракционного состава его, от конструкции печи, загрузочных и разгрузочных устройств и т.п. Поэтому автоматизация теплового режима печи является только составной, хотя и наиболее важной, частью автоматизации технологического режима данного агрегата. Методика автоматизации теплового режима металлургических печей в настоящее время достаточно хорошо разработана, и на подавляющем большинстве предприятий давно эксплуатируются системы автоматического регулирования теплового режима печей.
Автоматическое регулирование теплового режима печи обеспечивается, как правило, системой регулирования подачи топлива, системой регулирования подачи воздуха и системой регулирования тяги.
Основным назначением системы регулирования подачи топлива является организация такого режима горения в печи, чтобы количество тепла, выделяющегося в рабочем пространстве, было пропорционально количеству тепла, потребляемого материалом. Строгое поддержание баланса прихода – расхода тепла обеспечило бы оптимальные условия для данного пирометаллургического процесса. Однако такая схема регулирования подачи топлива пока неосуществима из-за невозможности непрерывного измерения количества тепла, потребляемого материалом, находящимся в печи. Поэтому сейчас применяются различные косвенные методы регулирования подачи топлива в печь.
Наиболее распространена схема автоматического регулирования подачи топлива в печь по температуре в рабочем пространстве. Принципиальным недостатком такой схемы является неоднозначность зависимости между температурой в печи и теплопередачей от факела горения топлива к материалу. На передачу тепла материалу, кроме температуры в печи, влияют также и положение факела в рабочем пространстве, и степень черноты факела, и скорость движения газов, и степень заполнения факелом рабочего пространства, и атмосферные условия в цехе, и состояние кладки печи.
Температуру в печи чаще всего измеряют с помощью радиационных пирометров, визированных на свод печи через отверстие в боковой стенке ее или с помощью термопар, установленных в своде печи. Погрешность измерения температуры, имеющаяся при использовании любого из указанных способов, ухудшает качество регулирования. Тем не менее, схема регулирования подачи топлива в печь по температуре в ней относительно проста, достаточно надежна, хорошо освоена и широко применяется на предприятиях, так как указанные выше недостатки ее не всегда имеют решающее значение, а лучшие варианты пока не разработаны.
Для отдельных типов печей применяют схему регулирования подачи топлива по соотношению материал – топливо, считая, что количество топлива, потребное для обработки весовой единицы материала, остается всегда примерно постоянным. Такая схема применима только для печей строго непрерывного действия. Недостатком ее является невозможность учета колебаний качественного состава топлива и материала.
От подачи воздуха в печь во многом зависит экономичность режима горения топлива. Поэтому регулятор подачи воздуха часто называют регулятором экономичности. Действительно, снижение подачи воздуха по сравнению с необходимым количеством вызывает ухудшение условий горения, недожог топлива, а значит, и перерасход его. Повышение подачи воздуха ведет к охлаждению факела в рабочем пространстве печи, т.е. также к перерасходу топлива. Кроме того, увеличивается расход энергии на привод тяго-дутьевых установок. Подача воздуха в печь всегда превышает теоретически необходимое для горения топлива количество его. Это объясняется недостаточно благоприятными условиями перемешивания топлива и воздуха. Отношение рабочего расхода воздуха в печь к теоретически необходимому для горения количеству его называют коэффициентом избытка воздуха a. Коэффициент избытка воздуха во многом определяет режим горения. Для современных печей коэффициент a составляет 1,05–1,1, а иногда и большую величину. Коэффициент избытка воздуха зависит от конструкции печи, горелок, от качества топлива. Неорганизованные присосы воздуха в печь также сильно влияют на режим горения. На некоторых вращающихся печах неорганизованные присосы воздуха настолько велики, что установка регулятора подачи воздуха полностью теряет смысл.
С учетом вышесказанного на практике повсеместно применяют схему регулирования подачи воздуха в печь по соотношению топливо – воздух. Эта схема поддерживает постоянно заданное соотношение между расходом топлива и расходом воздуха. Схема соотношения давно и очень хорошо освоена, проста, надежна, но имеет некоторые принципиальные недостатки. Здесь не учитываются колебания теплоты сгорания топлива, всегда имеющиеся на практике. Кроме того, изменения условий горения топлива не отражаются на работе регулятора подачи воздуха. Между тем при изменении качественного состава топлива или условий его сжигания требуется соответствующим образом изменить коэффициент избытка воздуха. Принципиально более правильной схемой регулирования подачи воздуха является управление расходом его по импульсу от содержания кислорода в отходящих газах печи. Действительно, поддерживая в отходящих газах минимальное содержание кислорода, можно обеспечить наибольшую экономичность режима горения. Из-за значительного запаздывания, недостаточно высокой надежности и сложности существующих газоанализаторов на кислород такая схема применяется редко. Практически надежной и правильной следует считать схему регулирования подачи воздуха по соотношению топливо – воздух с коррекцией по содержанию кислорода в отходящих газах.
Разрежение (давление) в печи также является важным фактором, влияющим на тепловой режим. Повышенное разрежение в рабочем пространстве приводит к увеличению неорганизованных присосов воздуха в печь, т.е. к перегрузке тяговых устройств и к снижению экономичности режима горения. Уменьшение разрежения в печи приводит к выбиванию горячих газов из нее, т.е. ухудшению условий труда, к потерям тепла с газами, к преждевременному разрушению кладки.
Принципиально правильной и применяемой на подавляющем большинстве печей является схема автоматического регулирования тяги по разрежению в рабочем пространстве печи воздействием на регулирующий орган на дымовом тракте ее. Схема эта проста и работает достаточно надежно. При реализации этой схемы следует особенно внимательно отнестись к выбору точки отбора регулирующего импульса, так как нестабильность поля давлений в рабочем пространстве печи, вызванная колебаниями положения факела и неравномерность загрузки материала, затрудняет получение представительного отбора импульса.
Изложенные в данном разделе общие принципы автоматического регулирования теплового режима могут быть отнесены почти ко всем типам пламенных печей цветной металлургии. Принципы и схемы автоматизации рассмотрены в этом пособии на примере печей кипящего слоя для обжига цинкового и молибденитового концентратов, вельц–печи цинкового производства, печей спекания и кальцинации алюминиевого производства, печи отражательной плавки медного концентрата и аппарата для агломерации свинцового концентрата.
АВТОМАТИЗАЦИЯ ПРОЦЕССА ОБЖИГА
Дата добавления: 2018-02-28; просмотров: 1005; Мы поможем в написании вашей работы! |
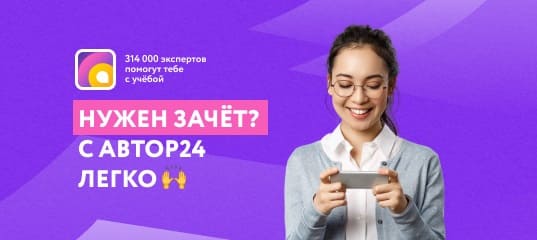
Мы поможем в написании ваших работ!