АВТОМАТИЗАЦИЯ ВРАЩАЮЩЕЙСЯ ВЕЛЬЦ-ПЕЧИ ЦИНКОВОГО ПРОИЗВОДСТВА
4.1. ОПИСАНИЕ ТЕХНОЛОГИЧЕСКОГО ПРОЦЕССА
Отходы производства цветных металлов часто содержат еще немало полезных компонентов. Извлечение их производится в процессах вторичного передела – переработки отходов. Извлечение окислов свинца и цинка из свинцовых шлаков и цинковых кеков осуществляется обычно методом возгонки, т.е. переводом соединений металла из твердой фазы непосредственно в газообразную. Такой процесс называют вельцеванием и проводят во вращающихся трубчатых печах (вельц-печах).
На рис. 4.1 показана схема вращающейся трубчатой вельц-печи.
Исходные материалы для печи – это цинковый кек, остающийся после выщелачивания цинкового огарка, и коксовая мелочь, необходимая как топливо для создания высокой температуры в печи и как восстановитель. Сырье из бункеров I (коксик) и II (кек) ленточными питателями III и IV подается на ленточный транспортер V. С ленточного транспортера смесь исходных продуктов поступает в печь. Вельц-печь представляет собой стальной барабан диаметром 2,5–3,5 м, длиной 40–50 м, установленный с уклоном 2–5о на роликовых опорах VI. Барабан изнутри футерован огнеупорным кирпичом. С торцов барабан входит в горячую (нижнюю) VII и холодную (верхнюю) VIII головки печи. Головки выполнены в виде камер из огнеупорного кирпича. Барабан печи приводится во вращение со скоростью 0,1–0,15 рад/сек (~1,0–1,5 об/мин) мощным электродвигателем с редуктором (на схеме не показаны).
|
|
Из-за наклонной установки барабана и в результате его вращения материал перемещается к нижней головке печи. Время пребывания материала в печи 2–3 ч. По мере медленного продвижения шихты вдоль печи коксовая мелочь загорается и разогревает весь слой материала. В средней, реакционной зоне печи топливо сгорает в атмосфере недостатка кислорода. Образующаяся при этом окись углерода СО восстанавливает окислы металлов. При температуре в реакционной зоне 1200–1300 оС чистые металлы возгоняются (испаряются) и сразу же вновь окисляются в потоке газов, проходящих вдоль печи. Мелкие частицы окислов выносятся газами из печи. Оставшийся в ней раскаленный материал проходит в нижнюю часть барабана и выпускается через нижнюю (горячую) головку печи с температурой до 1150 оС. Этот материал – клинкер – содержит еще некоторое количество Fe, Zn, Pb, Cu, Ag и углерода и поэтому его направляют на дальнейшую переработку.
В печи организован противоток, т.е. потоки газа и материала движутся в противоположных направлениях. Воздух для горения коксика и для образования газового потока внутри барабана подается в горячую головку печи вентилятором IХ. Газы с температурой 650–700 оС отводятся из холодной головки через систему газоходов и холодильников в пылеосадительные устройства Х, а затем дымососом XI выбрасываются в атмосферу. Система очистки газов состоит из пылеосадительных камер, кулеров, электрофильтров (или рукавных фильтров) и т.д. Вся эта сложная установка необходима для наиболее полного выделения из газового потока возгонов – готового продукта процесса вельцевания. Для разогрева печи в период пуска и для надежного зажигания коксика в отдельные периоды нестабильного режима горения в горячую головку печи иногда подается вспомогательное топливо – горючий газ. При нормальном ходе печи газ отключается.
|
|
Основным экономическим и технологическим показателем режима вельцевания является степень извлечения ценных металлов из сырья или количество оставшихся в клинкере металлов. При разработке комплексной системы автоматизации процесса вельцевания следует направить работу отдельных регуляторов на достижение оптимального качества клинкера или на получение максимального количества возгонов. Сейчас еще не существует датчиков для автоматического непрерывного определения указанных параметров. Поэтому принятые на предприятиях схемы автоматизации предусматривают лишь стабилизацию главных технологических параметров вельц-печи.
|
|
В рассматриваемой технологической схеме основным исходным материалом для вельцевания является цинковый кек. Подача его в печь должна быть поставлена в зависимость от качества готовой продукции. Ввиду отсутствия соответствующих датчиков можно предусмотреть поддержание постоянной подачи кека с ручной перестановкой задания регулятору. Уменьшение подачи кека против технологической нормы не отражается на качестве возгонов или клинкера, но ведет к уменьшению производительности печи по сырью, снижает экономичность ее работы. Увеличение расхода кека вызывает перегрузку печи и резкое повышение содержания цинка и свинца в клинкере. Степень извлечения металлов при этом понижается.
Коксик является топливом, восстановителем и «осушителем» для процесса вельцевания. Расход топлива, необходимого для разогрева находящегося в печи материала, зависит от количества последнего. А необходимое для возгонки ценных металлов количество восстановителя также зависит от количества материала в печи и от процентного содержания в нем металлов. Автоматический непрерывный анализ кека сейчас еще не производят. Следовательно, подача коксика должна быть поставлена в зависимость от подачи основного материала – кека. Подачу коксика в такой системе можно регулировать либо по расходу кека, либо по соотношению расходов кека и коксика. Второй вариант встречается чаще, так как он более совершенен.
|
|
Пылеосадительные устройства, улавливающие возгоны из отходящих газов печи, являются весьма важным звеном в процессе вельцевания. Любое нарушение режима работы их снижает коэффициент полезного действия установки, т.е. степень очистки газа от полезных материалов. При этом теряется часть готового продукта. На работе системы пылеулавливания и холодильников отрицательно отражаются резкие колебания температуры газа. Температура отходящих газов в холодной головке печи связана с тяговым режимом. Так как газ нагревается от горящего в реакционной зоне коксика, то изменение скорости движения газа отражается и на температуре его. При повышении температуры следует увеличить скорость газа, т.е. открыть дымовой шибер, и наоборот. При отсутствии запаса по тяге, когда дымовой шибер уже полностью открыт, а температура все еще высока, приходится уменьшать производительность печи. Таким образом, можно предложить такую схему, когда система регулирования температуры работает в две стадии. Первая стадия – управление дымовым шибером до полного открытия его; вторая – снижение подачи материала в печь. Если печь работает не на форсированном режиме и мощность дымососа выбрана правильно, то уменьшение подачи кека регулятором температуры отходящих газов происходит достаточно редко.
На некоторых предприятиях система управления тяговым режимом печи работает по импульсу от разрежения в холодной головке воздействием на дымовой шибер, установленный после пылеосадительных устройств. При этом температура отходящих газов учитывается вводом корректирующего воздействия в регулятор тяги. Иногда корректирующий импульс по температуре в холодной головке печи вводят даже в регулятор подачи воздуха, считая, что расход воздуха значительно влияет на тяговый режим печи. Выбор схемы автоматического регулирования тягового режима зависит от индивидуальных особенностей вельц-печи, от величины неорганизованных подсосов воздуха, от расположения и конструкции пылеосадительных устройств и т.д.
В нижней части печи, после реакционной зоны, происходит остывание клинкера и нагрев воздуха, поступающего в печь. Этот воздух необходим для горения коксика и для окисления паров возгоняемых металлов. Поэтому от температуры в нижней части печи зависит процесс восстановления и возгонки в средней зоне. Значения температуры в нижней части печи и в реакционной зоне технологически связаны. От этих параметров зависит в значительной степени полнота извлечения цинка и свинца из исходных материалов. Все указанные обстоятельства определяют необходимость регулирования температуры в нижней технологической зоне печи. Замеряют температуру клинкера на выходе из печи, а управлять температурой материала на выходе можно воздействием на подачу воздуха в печь. Регулирующий орган устанавливают перед вентилятором, а если поток воздуха разделяется на первичный и вторичный, то регулятор температуры в нижней головке может управлять подачей только вторичного воздуха. Для интенсификации процесса горения коксика и для окисления паров возгоняемых металлов предполагается вводить в печь воздух, обогащенный кислородом. В этом случае стабилизируется соотношение расходов воздух – кислород либо по содержанию кислорода в дутье после смесительной камеры регулируется его подача.
Давление воздуха после вентилятора характеризует дутьевой режим установки, а расход его, как уже было сказано, влияет на основной технологический режим вельцевания. Расход вспомогательного топлива (горючего газа) в печь необходимо контролировать для учета экономичности работы цеха.
Изменение тягового режима по газовому тракту установки свидетельствует о нарушении работы пылеосадительных устройств. Увеличение перепада разрежений на фильтрах может означать забивание их, а уменьшение – наличие неплотностей по тракту.
Режим горения коксика и частично режим восстановления паров металлов в реакционной зоне печи характеризуется содержанием свободного кислорода в отходящих газах печи. Установить строго определенную зависимость между ходом технологического процесса вельцевания и содержанием кислорода в отходящих газах трудно из-за наличия в установке больших подсосов воздуха и непостоянства состава исходных материалов. Тем не менее, непрерывный контроль количества кислорода в газах за печью позволяет вести режим вельцевания по технологическому графику.
4.2. ВЫБОР СИСТЕМ АВТОМАТИЧЕСКОГО КОНТРОЛЯ
И РЕГУЛИРОВАНИЯ
Приведенный выше анализ особенностей вельц-процесса для переработки цинковых кеков – побочных продуктов основного цинкового производства – показывает, что для обеспечения оптимальных условий протекания процесса необходимо в проекте автоматизации соответствующего отделения предусмотреть следующие системы автоматического контроля и регулирования:
1. Системы автоматического контроля и регулирования
– температуры в нижней головке печи;
– расхода коксика;
– расхода кека;
– температуры в верхней головке печи.
2. Системы автоматического контроля
– давления газа и воздуха на входе в печь;
– расхода газа и воздуха на входе в печь;
– температуры в реакционной зоне печи;
– разрежения на выходе из печи и перед эксгаустером;
– содержания кислорода в дымовых газах.
Номинальные значения выходных параметров рассматриваемого объекта автоматизации приводятся в табл. 4.1.
На рис. 4.2 представлена схема автоматизации вельц-процесса, включающая все перечисленные выше системы.
4.3. ОПИСАНИЕ СИСТЕМ АВТОМАТИЧЕСКОГО КОНТРОЛЯ
И РЕГУЛИРОВАНИЯ
4.3.1. Система автоматического регулирования температуры
в нижней головке печи
Температура в нижней зоне печи измеряют радиационным пирометром (поз. 5а), визированным на футеровку, выходящую из-под раскаленного клинкера, на расстоянии 4–6 м от среза печи, и вторичным прибором (поз. 5б). С прибора 5б сигнал поступает на автоматический регулятор (поз. 5в), а затем – на блок ручного управления (поз. 5г) – на магнитный пускатель (поз. 5д) – на исполнительный механизм (поз. 5е), изменяющий расход воздуха в печь с помощью поворотной регулирующей заслонки (поз. 5ж).
Таблица 4.1
№№ п/п | Наименование параметра | Единицы измерения | Номинальная величина |
1. | Температура в нижней головке печи | оС | 1150 |
2. | Температура в верхней головке печи | оС | 650–700 |
3. | Расход коксика | т/ч | 2,0 |
4. | Расход кека | т/ч | 4,2 |
5. | Давление газа на входе в печь | кПа | 10,0 |
6. | Давление воздуха на входе в печь | кПа | 10,0 |
7. | Температура в реакционной зоне печи | оС | 1200–1300 |
8. | Разрежение на выходе из печи и перед эксгаустером | Па | 80,0 |
9. | Содержание кислорода в дымовых газах | % | 2,5 |
4.3.2. Система автоматического регулирования расхода
коксика
На схеме принята система стабилизации расхода коксика в печь. Расход измеряют ленточным весоизмерителем (поз. 8а), связанным со вторичным прибором (поз. 8б). Сигнал, пропорциональный расходу коксика, направляется на вход автоматического регулятора (поз. 8в), где он сравнивается с заданным расходом, а с регулятора регулирующее воздействие через блок ручного управления (поз. 8г) и магнитный пускатель (поз. 8 д) поступает на исполнительный механизм (поз. 8е), перемещающий шиберную задвижку бункера I.
4.3.3. Система автоматического регулирования расхода кека
Имеет точно такую же структуру, как и САР расхода коксика, и включает элементы 9а–9б–9в–9г–9д–9е–шиберная задвижка бункера II.
4.3.4. Система автоматического регулирования температуры
в верхней головке печи
В систему регулирования входят: термопара (поз. 10а), установленная в холодной головке на расстоянии 0,5 м от среза барабана, электронный потенциометр (поз. 10б), автоматический регулятор (поз. 10в), блок ручного управления (поз. 10г), магнитный пускатель (поз. 10д) и исполнительный механизм (поз. 10е). Исполнительный механизм перемещает выдвижной дымовой шибер (поз. 10ж), увеличивая или уменьшая тягу через систему пылеулавливания.
4.3.5. Система автоматического контроля давления газа
и воздуха на входе в печь
Для контроля давления используют отборные устройства (поз. 1а и 4а), бесшкальные монометры с электрическими преобразователями (поз. 1б и 4б) и вторичные приборы показывающие и самопишущие (1в и 4в).
4.3.6. Система автоматического контроля расхода газа
Для контроля расхода газа, поступающего в нижнюю головку печи, используют счетчик расхода (поз. 2а и поз. 2б), указывающий текущий и суммарный расходы газа.
4.3.7. Система автоматического контроля расхода
воздуха в печь
Контроль осуществляется комплектом: сужающее устройство (поз. 3а), дифманометром с электрическим преобразователем (поз. 3б) и вторичным показывающим и самопишущим прибором (поз. 3в).
4.3.8. Система автоматического контроля температуры
в средней зоне печи
Для контроля температуры в средней (реакционной) зоне печи установлены термопары (поз. 6а), соединенные последовательно, чтобы получить усредненный по сечению печи отбор температуры. Суммарная э.д.с. термопар передается на показывающий и самопишущий потенциометр (поз. 6в) через делитель напряжения (поз. 6б) с помощью токосъемного устройства. Необходимость в использовании токосъемного устройства вызвана тем, что термопары вмонтированы в барабан печи, который вращается, а сигнал с них необходимо передать на неподвижно установленный в щитовом помещении показывающий и самопишущий прибор – потенциометр. Само токосъемное устройство состоит из медных колец, закрепленных на корпусе печи, и меднографитовых щеток, скользящих по кольцам.
4.3.9. Система автоматического контроля разрежения
на выходе из печи и перед эксгаустером
В комплект приборов входят отборные устройства (поз. 11а, 12 а), бесшкальные тягомеры с электрическими преобразователями (поз. 11б, 12б) и вторичные приборы (поз. 11 в, 12 в).
4.3.10. Система автоматического контроля содержания
кислорода в дымовых газах
Система включает отборное устройство (поз. 13а), газоанализатор кислорода (поз. 13б) и вторичный показывающий и самопишущий прибор (поз. 13в).
Дата добавления: 2018-02-28; просмотров: 1980; Мы поможем в написании вашей работы! |
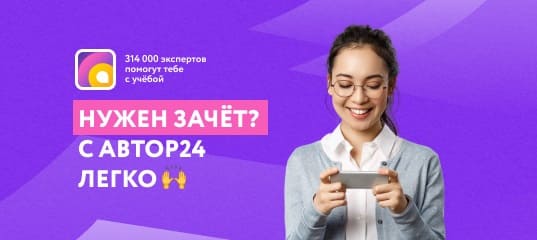
Мы поможем в написании ваших работ!