Особенности облицовывания профильных деталей
Облкцовыванме пластей в мембранных прессах. Некоторые фирмы Германнн выпускают мембранные прессы для облнцовывання деталей крнволннейных профнлей. Сформнрованные пакеты (основа — облн-цовочная пленка) подаются в пресс (рнс. 7.21). Верхняя шгата пресса опускается, н с помоіцью уплотннтеля создается герметнчная камера между верхней н ннжней шгатамн. Включается вакуум-насос, созда-юіцнй разряженне между ннжней плнтой н мембраной — тонкой эластнчной н термостойкой пленкой. Облнцовочная полнмерная пленка высокой эластнчностн облегает профнльную поверхность деталн. Од-нако давлення за счет вакуума недостаточно н между верхней шгатой н мембраной создается нзбыточное вакуумное давленне — 0,5 — 0,6 МПа. Для ускорення прессовання, кроме нагрева мембраны нзлу-чателя, нспользуется предварнтельный нагрев основы с клеем.
После облнцовывання в мембранных прессах пленкамн заготовкн обработке не подвергаются, т. е. основа обрабатывается в размер перед облнцовываннем. В мембранных прессах деталн могут облнцовыва^ься н строганым шпоном, однако в таком случае поверхность должна быть профнлнрована немного, чтобы у шпона не было резкнх нзломов н малых раднусов нзгнбов.
Облнцованные шпоном поверхностн подлежат шлнфованню.
Безмембранное облицовывание.Используется оверлей.
Д.б. эластичная пленка. Она выходит за пределы пресса.
Окутывание.Происходит заворачивание.
|
|
29 Кашированием называется процесс облицовывания полноформатных плит рулонным пленочным материалом на основе бумаг и полимеров методом накатывания. Материалы, применяемые для каширования:
Полимерные пленки на основе бумаг;Полимерные пленки на основе полимеров (пвх, полипропиленовые пленки);Клеевые материалы – карбамидо-формальдегидные смолы (горячее каширование), пва (холодное, теплое каширование), полиуретановые клеи. Каширование применяется как финиш-эффект без дальнейшей отделки лкм
В зависимости от температуры начального склеивания облицовок с основой различают след. Виды каширования: холодное, горячее, теплое, каширование методом квикстеп, короткоконтактное. Первые 3 способа различаются по способу накатывания и прикатываниявалами.
Короткоконтактное каширование – это каширование методом накатывания облицовочного материала и облицовывания в плоском прессе.
В общем случае каширование предусматривает следующие операции:
Очистка кромок и пластей детали от пыли; нанесение клея на пласти детали; удаление влаги из клеевого слоя; размотка пленки из рулона и ее накатывание на пласти деталей; разделение (разрубание) непрерывного полотна пленки в разрывах между деталями; повторное прикатывание пленки; отверждение клеевого слоя.
|
|
При холодном кашировании удаление излишней влаги из клеевого слоя проводится при температуре цеха, а отверждение клея после накатывания пленки - в стопе, в специальном холодном прессе или без пресса, с нагружением сверху для прижатия пленки на верхних деталях стопы. Время отверждения клея - от нескольких часов до суток. Наиболее известными изготовителями такого оборудования являются фирмы burkle, friz (фрг), omma, simi (италия), barberan (испания).
Схема технологического процесса облицовывания методом холодного каширования: 1 – подача плит; 2 – очистка плит от пыли; 3 – нанесение клея; 4 – накатывание ленты на плиту(р=1,2 мпа,); 5 – разделение облицовочного материала по межторцовому зазору; 6 – укладывание плит в стопу.
нагрев клеевого слоя для удал-я из него влаги с целью снижения времени последующего отверждения клея и снижения разбухания верхнего слоя плиты из-за впитывания. Окончательное приклеивание также производится в стопах, но время выдержки при этом снижается до нескольких часов.
схема технологического процесса облицовывания методом теплого каширования: 1 – подача плит; 2 – очистка плит от пыли; 3 – подогрев плиты; 4 – нанесение клея; 5 – накатывание ленты на плиту(t=50-60 ºс, р=1,2 мпа,); 6 – разделение облицовочного мат-ла по межторцовому зазору; 7 – укладывание плит в стопу.
|
|
Горячее каширование включает практически те же операции, что и теплое, но накатывание и прикатывание рулонного облицовочного материала производится горячими валами, нагреваемыми до темп-ры 120-160 °с
Основные изготовители: фирмы burkle и hymen. Схема технологического процесса облицовывания методом горячего каширования: 1 – подача плит; 2 – очистка плит от пыли; 3 – нанесение клея; 4 – подсушивание клеевого слоя; 5 – нанесение отвердителя; 6 – накатывание ленты на плиту( р=1,2 мпа,); 7 – разделение облицовочного материала по межторцовому зазору; 8 – укладывание плит в стопу.
Пч= 60*u*кр*км/l, шт/час где l-длина щита
30 Ламинирование. Применяемые способы. Особенности метода ламинирования. Материалы, оборудование, режимы, производительность, организация рабочих мест.
Ламинирование – процесс облицовывания древесных материалов декоративно-бумажно смоляными пленками, которые пропитаны смолами с неполной степенью отверждения (меламиновые смолы с неполной поликонденсацией). (пресса плоского типа).
|
|
В процессе облицовывания под воздействием давления (до 30 кг/см2) и температуры до 250°С) полностью высушенная, но не полностью полимеризованная смола выдавливается из пленки. Ее слой, прилегающий к подложке (плите), приклеивает к ней пленку, а смола, выдавленная в сторону греющей плиты пресса, создает на поверхности пленки структуру укрепленной на этой плите прокладки - глянцевую, матовую, зерненую, сетчатую и т.д. После окончательной полимеризации содержащейся в пленке пропиточной меламиновой смолы создается термореактивный полимер (смола переходит в твердое состояние. При этом декоративно-защитный слой на плите образуется за счет растекания смолы по поверхности ДСтП с последующим доотверждением и образованием прочного единого покрытия «ДСтП-смола-бумага».
"Ламинирование" производится только в обогреваемых короткотактных прессах ("Burkle", "Wemhoner", "Siempelkamp", "Dieffenbacher" и т. д.), где приклеивание облицовочного материала к подложке осуществляется за счет содержащейся в пленке пропиточной смолы с низкой степенью отверждения. Впрочем, существуют и установки проходного типа на базе ленточных прессов ("Hymmen"). В любом случае, в этом процессе полностью отсутствует нанесение клея.
Тиснение, имитация структуры древесины или других материалов на поверхности бумаги достигается с помощью специальных пресс-прокладок, которые через специальный теплопроводный демпферный материал крепятся к плитам пресса.
Технология: подготовка смол.бумаги (изготовл. меламино-форм. смолы)+бумага-ламинат+ДСтП – пропитка – хранение – подача – загрузка прессование – разгрузка – расформиров. – раскрой – сортировка.
Многоэтажные пресса – с охлаждением, одноэтажные – без охлаждения.
Режим для многоэт.-го пресса – цикл прессования – 10 мин; tпл.пресса – 145-180ºС; нач. tпл.пресса - 60ºС; tохл.плит - 60ºС; р – 1,8-2,2 МПа.
Режим для одноэт.-го пресса – цикл прессования – 1,5-2 мин; tпл.пресса – 145-180ºС; нач. tпл.пресса – 145-180ºС; р – 1,8-2,0 МПа.
При неправильном выборе режима могут появляться микротрещины (внутр. напряжения) из-за чрезмерно быстрого нагрева.
Производительность плоского пресса:
где Кисп, Кзагр – коэффициенты, соответственно использования и загрузки (Кисп=0,7; Кзагр=0,7); Sпл– площадь плит пресса, м2; n – количество рабочих промежутков в прессе; tц – время цикла, мин; Sкомпл – площадь комплекта, м2.
Это процесс облицовывания полимерными материалами на основе бумаг.
Под воздействием температуры смола в пленке плавится и растекается по поверхности бумаги и основы, одновременно выполняя роль и защитно-декоративного слоя, и клеевого, прочно соединяя основу с пленкой.
При ламинировании используются пленки с низкой степенью отверждения, где происходит дальнейшая поликонденсация смолы с переходом ее в нерастворимое и неплавкое состояние. Образуется покрытие с пространственной структурой.
Различают 2 вида ламинирования:
Ламинирование с охлаждением плит в прессе;
Ламинирование без охлаждения плит в прессе.
В зависимости от назначения облицованной плиты, её покрытие может быть одно- или многослойным. Ламинирование с охлаждением. Выполняется в многоэтажных прессах. Весь цикл прессования состоит из следующих этапов:
Снятие пыли с поверхности формирование пакетов: транспортирующий поддон – амортизационная прокладка (25-30 листов спец. Бумаги, асбестовый лист) – латунный хромированный лист или листы из нержавеющей стали, которые смазывают антиадгезионными веществами (анилиновая кислота) – декоративная пленка – плита (основа) – повторение слоев (без поддона); загрузка пакета в пресс, где плиты пресса имеют температуру 60°с (холодные);подача давления (смыкание плит пресса); увеличение температуры до 170°с; выдержка согласно технологического режима; постепенное снижение давления со снижение температу
ры плит пресса; размыкание плит пресса (температура плит 60°с); разгрузка пресса; разбор пакета; транспортировка на участок технологической выдержки.
Поверхность плит при данном способе ламинирования имеет глянцевый или высокоглянцевый показатель. Пч=60*кр*sпл.пр*n/(t*sзаг), n-число этажей
Ламинирование без охлаждения происходит в одноэтажных прессах без снижения температуры плит пресса и без формирования пакета такого, как в предыдущем случае.
Снятие пыли, нанесение облицовочного материала, загрузка пакета в пресс с температурой плит 170°с, выдержка под давлением, выгрузка пакета из пресса с температурой плит 160-170°с, ламинат имеет матовую, полуматовую поверхность.
Пч=60*кр*sпл.пр/(t*sзаг),t-время облицовывания.
Режимы прессования
Параметр | С охлажд | Без охлажд |
Tцикла,мин | 10 | 1,5-2,0 |
Т-ра плит пресса, º с | 160-170 | 160-170 |
Начальн т-ра плит, ºс | 60 | 160-170 |
Давление, мпа | 1,8-2,2 | 1,8-2,2 |
В состав линии облицовывания на базе однопролетного пресса, как правило, входят: автоматический питатель, станок щеточный для очистки от пыли, станок вальцовый клеенаносящий, промежуточный дисковый траспортер, ленточный транспортер для набора прессуемых пакетов, короткотактный проходной пресс, иногда - камера охлаждения и автоматический укладчик.
Число изготовителей прессов и линий облицовывания достаточно велико, например, нелидовский завод гидравлических прессов (россия) - линия акда 4138, днепропетровский завод тяжелых прессов (украина) - линия акда 4940, формы burkle, wemhoner, diffenbacher, siempelkamp, zoos, ott (фрг), italpresse, ormamacchine, simi (италия) и др.
Склеивание и облицовывание. Виды склеивания в производстве мебели. Стадии технологического процесса. Подготовка материалов. Методы интенсификации процесса склеивания древесины. Оценка качества склеивания. Охрана окружающей среды на участке склеивания.
Основные виды склеивания: склеивание заготовок и деталей из древесины, древесных, полимерных и других материалов; склеивание деталей из измельченной древесины; склеивание с одновременным гнутьем заготовок из шпона, фанеры, массивной древесины; облицовывание пластей и кромок щитовых деталей; склеивание при сборочных работах.
Технологический процесс склеивания включает следующие основные стадии: подготовку склеиваемых материалов; подготовку клеевых растворов; нанесение клея на склеиваемые поверхности; запрессовку склеиваемых заготовок и выдержку их под давлением, выдержку склеенных заготовок после запрессовки.
Подготовка поверхностей к склеиванию зависит от вида материалов, их размера, формы изделия, применяемого оборудования для склеивания и др. Она осуществляется различными способами — пилением, фрезерованием, строганием, шлифованием. При приготовлении клея учитывают его марку. Клей готовят в специально оборудованном помещении с приточно-вытяжной вентиляцией.
Холодное склеивание требует минимальных затрат энергии, но оно продолжительно во времени (как правило, 24 ч), поэтому трудно поддается автоматизации. Необходим также значительный операционный запас заготовок и большая производственная площадь.
Склеивание с нагревом осуществляют при различных способах подвода тепла к клеевому слою — кондуктивном, конвективном, за счет предварительного аккумулирования тепла в одной и двух склеиваемых заготовках, путем нагрева в поле токов высокой частоты (ТВЧ).
Кондуктивный нагрев применяется при склеивании тонких, толщиной до 10 мм, заготовок, которые контактируют с горячими плитами пресса. Такой способ широко применяется при облицовывании пластей и кромок щитовых заготовок. Нагрев осуществляют обычно паром, горячей водой, маслом или низковольтным током промышленной частоты.
Конвективный нагрев применяют при наклеивании тонких облицовочных материалов на основу сложной формы в пневматическом или мембранном прессе. Тепло передается горячим воздухом или инфракрасным облучением.
Нагрев за счет аккумулированного тепла можно осуществлять при достаточной, не менее 10 мм, толщине склеиваемой заготовки. Перед склеиванием одну (более массивную) или обе заготовки нагревают кондуктивным или конвективным способом.
Нагрев в поле ТВЧ производят в специальном прессе. Склеиваемые заготовки помещают между электродами, к которым подводят ток высокой частоты. Высокочастотное поле взаимодействует с молекулами материала, вызывая смещение их положительно и отрицательно заряженных частиц. Затрачиваемая при этом энергия выделяется в виде тепла.
Облицовывание предназначено для улучшения декоративных свойств поверхности, повышения прочности деталей, создания защитного покрытия от выделения токсических веществ (при облицовывании древесностружечных плит).
Облицовывание может быть односторонним, когда облицовочный материал наклеивается на одну сторону, и двухсторонним. Его можно проводить в один слой и в два слоя, т. е. с подслоем.
Процесс облицовывания включает следующие стадии: подготовку основы, подготовку облицовки, приклеивание облицовки к основе, технологическую выдержку после облицовывания.
На облицованной поверхности не должно быть непроклеенных мест, пятен просачивающегося клея, отщепов, вмятин, расхождений и нахлесток полос облицовки.
При скл. и облиц. исп. синт. клеи, кот. содержат вещ-ва, оказывающие вредное воздействие на человека. Для поддержания безоп. усл. работы исп. общая приточно-вытяжн.вентиляц. с местными отсосами, располож. внизу мест выделения токсичных в-в. Ведутся работы , чтобы сократить обьёмы вредных выделений при скл..
Местная вентиляция д.б.сблокирована с вкл. устройств, кот. обуславливают выделение этих в-в. Для предохранения окр. среды от технологич.выбросов токсичных в-в прим. спец. улавливающие фильтры или установки, сжигающие токсичные в-ва.
Качество склеивания оценивается по внешнему виду и прочности изделия. Нормативно-техническая документация на изделия из древесины устанавливает нормативную прочность склеивания. Для клееных строительных конструкций из древесины предельные значения напряжений установлены СНиП ПА-10.
Прочность склеивания в настоящее время оценивается по результатам испытаний механическим разрушением стандартных образцов. При качественном склеивании нормативные сопротивления при разрушении образцов должны быть выше или равны нормативным сопротивлениям такому же виду нагрузок склеиваемых материалов. Имеются стандарты, предусматривающие различные методы разрушения образцов для оценки прочности склеивания.
32 Технология облицовывание прямолинейных кромок щитов. Особенности. Материалы, оборудование, режимы, производительность, организация рабочих мест.
Линии МФК-3 и МФК-4 используют для облицовывания шпоном и рулонным полимерным материалом. Эти линии имеют устройство для выборки четверти, линия МФК-4 оборудована микропроцессором.
Перед началом работ на станке клей-расплав, который загружается в клеевой бачок в виде твердых гранул, нагревают до рабочего состояния. Облицовочный материал (шпон натуральный или синтетический) полосовой или рулонный помещают в магазин. В начале движения щита через станок вращающийся ролик захватывает клей из клеевого бачка и наносит его на кромку. Затем полоска облицовочного материала автоматически выдается из магазина и прижимается к кромке шита. Специальный прижим (ролики) выдерживает полоску под давлением в течение всего времени полимеризации клея.
Следует подчеркнуть, что эта операция, как и все остальные, выполняется в процессе перемещения щита через станок. Пильные головки некоторое время перемещаются вместе со щитом, опиливая свесы на кромках. После пильных головок для снятия свесов по длине щит проходит мимо головок фрезерных, которые снимают свесы по толщине детали. Эта операция производится цилиндрическими фрезами, оси которых расположены в горизонтальной плоскости перпендикулярно направлению подачи. Фрезерные головки жестко соединены с копирами, один из которых постоянно прижимается к верхней пласти щита, а другой - к нижней. Затем головки цилиндрических фрез снимают вдоль ребра кромки фаски. Оси головок наклонены.
Угол фаски может меняться от 10 до 40°. Эти головки также соединены с копирами, обеспечивающими формирование одинаковой фаски по всей длине кромки.
Шлифуют каждую кромку при необходимости последовательно двумя шлифовальными головками. Головки оснащаются шлифовальными лентами разных размеров зернистости, что обеспечивает получение заданной шероховатости и поверхностей. Направление вращения лент встречное к направлению подачи щита. Для повышения качества обработки, т. е. шероховатости поверхности и равномерного износа абразивного материала, шлифовальные ленты осциллируют в вертикальной плоскости. Для предотвращения сошлифовывания кромок на углах щита утюжок, с помощью которого лента прижимается к щиту, автоматически подводит ленту к обрабатываемой кромке в тот момент, когда передний торец щита достигает середины утюжка, и отходит тогда, когда с серединой утюжка поравняется задний торец. После шлифования кромок щит передается цепным конвейером станка для облицовывания кромок на конвейер поворотного устройства. Операции повторяются.
Процесс облицовывания прямолинейных плоских кромок осуществляется двумя способами:
1. На автоматических линиях;
2. Облицовывание на станках проходного типа (односторонние).
Примерами автоматических линий служат: МФК-3, МФК-4, Хомаг, Брандт, Швабедиссен.
Технологический процесс:
1. Форматирование щитовых деталей – обрезка по формату (обрезной узел – круглые твердосплавные пилы основные и подрезные, за ними фрезерные головки, которые измельчают крупные отходы, после – фрезерные головки для подчистки кромок)
2. Снятие пыли струей воздуха либо щетками
3. Нанесение клея-расплава. Из стакана, куда засыпаются гранулы (при температуре 60-80 °С), наносится клей.
4. Облицовывание кромки – из кармана выталкиваются полоски шпона, либо если облицовывается рулонным материалом, то устанавливается стол, на который укладывается бобина шпона. В зависимости от марки клея рабочая температура 200-220 °С
5. Снятие свесов фрезами (по 2 головки с каждой стороны), за ними – следующие фрезы для смягчения грани – формируется фаска.
6. После снятия свесов по длине следует разворот на 90° и цикл повторяется
где U = 15-25 м/мин – скорость подачи заготовок;
L – длина детали;
l0 – межторцовые разрывы между заготовками (0,3-0,5 м);
Кр, Км – коэффициент рабочего и машинного времени, если Км = 0,6 – 0,7, то межторцовые разрывы учитывать не следует, т.к. они уже предусмотрены.Автоматический односторонний кромкооблицовочный станок с нанесением клея-расплава на кромку детали. Предназначен для облицовывания с последующей обработкой прямолинейных кромок в одиночном и поточном режимах. Быстросъемный клеенаносящий узел для клея-расплава. Резервуар для клея располагается под клеенаносящим валом, гарантированная эксплуатация без загрязнения станка. Точно дозируемая подача клея посредством регулировки клеенаносящего вала. Не требуется регулировка на толщину заготовки. Выбор направления вращения клеевого вала (по направлению / против направления движения заготовки). Электронный термостат для контроля за температурой клея. Автоматическое снижение температуры клея при перерыве в работе. Активация (нагрев) клея-расплава с помощью инфракрасного излучения. Автоматический магазин для подачи рулонных и полосовых кромочных материалов с держателем для рулонов
33 Склеивание заготовок из древесины по ширине. Технологический процесс. Применяемое оборудование, режимы склеивания, производительность, организация рабочих мест.
Технологический процесс склеивания заготовок в щиты включает подготовку заготовок, склеивание их пластами или кромками, последующую технологическую выдержку и механическую обработку склеенных заготовок.
Подготовка заготовок к склеиванию по ширине — в выравнивании кромок или кромок и одной пласти. В последнем случае обеспечивается более точное базирование заготовок при склеивании. Готовят поверхности к склеиванию фрезерованием. Шероховатость их Rmmax не должна превышать 200 мкм. Допускается склеивать пиленые заготовки до 300 мкм. В этом случае исключается фрезерование, уменьшается припуск на обработку, но требуется больший расход клея.
Клей на детали наносят вручную (как правило, на одну из поверхностей) или клеенаносящими вальцами. В первом случае используют кисти, щетки и специальные приспособления. Для местного нанесения клея используют пластмассовые емкости или тюбики, горлышко их имеет наконечник с отверстием, которым удобно наносить клей в отверстия, на щечки проушин и т. д.
Клеенаносящие вальцы бывают трех видов. Вальцы с нижним питанием неудобны в работе, с их помощью нельзя добиться равномерного распределения клея по поверхности заготовки. Вальцы с нижним и верхним питанием позволяют наносить клей на одну или две стороны и регулировать толщину клеевого слоя. Вальцы с дозирующими роликами более совершенны. Клеенаносящие вальцы покрыты резиной с рифлением, дозирующие выполнены стальными, полированными. Клеевой слой можно регулировать с большой точностью.
Для обеспечения давления применяют винтовые, пневматические и гидравлические приспособления. Склеивание бывает холодное и горячее. При горячем склеивании используют кондуктивный нагрев (паровой, электрический), нагрев за счет аккумулированного тепла, в поле ТВЧ.
Рассмотренные приспособления основаны на холодном склеивании и имеют низкую производительность. С их помощью можно склеивать бруски, но нельзя склеивать щитовые детали. За рубежом, в частности фирма «Брест» (Словения), специализируется на выпуске вайм для склеивания щитовых деталей из брусков на гладкую фугу. Ваймы имеют от 6 до 60 секций и могут склеивать щиты размером 2400 х х 800 мм. Склеивание осуществляется холодным способом при помощи механических зажимных устройств, установленных на бесконечной транспортной ленте. Ваймы быстро переналаживаются на другой размер щитов, требуют мало места для установки, просты в работе. Линия состоит из вальцов для нанесения клея, пневматического высокочастотного пресса с механическим подающим устройством и выходящим транспортером, а также из высокочастотного генератора. В зависимости от типа линии могут склеиваться заготовки в элементы крупных размеров (длиной до 3 м, шириной до 700 мм и толщиной до 100 мм). Влажность склеиваемых заготовок не должна превышать 14 %. Продолжительность рабочего цикла 60—300 с.
Склеивание по ширине обычно происходит либо в вейерных ваймах, либо в струбцинах, либо в прессах проходного или полупроходного типа.
Тех.процесс:
1.Подготовка мат-ла (Поперечный раскрой пиломатериалов (ЦПА-40, ЦКБ-40.01, ЦМЭ-3А(Б), ТС-2, ТС-3). Продольный раскрой пиломатериалов (ЦДК-4-3, ЦДК-5-2, ЦМР-4М). Создание технологической базовой поверхности на пласти и кромке (СФ-4, СФ-6, СФ-6А). Формирование заготовок по сечению в размер (С25-5, С25-1А, С16-42). Торцовка в размер брусковых заготовок с одновременной нарезкой зубчатого клеевого соединения (минишип) (ШО10-4, ШД10-8, ФСШ-4))
2.Подготовка клеевого мат-ла
3.Нанесение клея (вальцовый метод или вручную)
4.Сборка пакета (щита)
5.Запрессовка в прессе
6.Выдержка под давлением (≈5 мин.)
7.Калибрование щита
8.Форматирование
9.Раскрой на заготовки (Торцовка полученного щита (формир-ие чистовой длины) (ЦПА-40, ЦКБ-40.01, ЦМЭ-3А(Б), ТС-2, ТС-3, универсальный круглопильный станок с перемещающейся кареткой Ц6 ). Обрезка щита по длине (универсальный круглоп-ый станок с перемещ-ся кареткой Ц6)).
Параметры | КФ-МХ | ПВА |
Вязкость клея при 20С,с по ВЗ-1 | 50-100 | 11-40 |
Жизнеспособность клея при Т=20С, ч | 2-8 | до 120 |
Расход клея, г/м2 | 130-140 | 260-300 |
Давление прессования, МПа | 0,5-0,8 | 0,5-0,6 |
Тем-ра отверждения, С | 18-22 | 18-22 |
Производительность пресса : П=Тсм·Кр·Sn/(τ·S2), шт
Станки круглопильные для продольного раскроя досок на заготовки: однопильные — цдк5-3 , пятипильный — цдк5-4, десятипильный прирезной станок цмр-4м. схема организации рабочего места у многопильного круглопильного станка для продольного раскроя пиломатериалов. Круглопильные станки для поперечного раскроя пиломатериалов предназначены для распиливания поперек волокон (торцевания) досок и брусков на чистовые и черновые заготовки определенной длины или удаления из них дефектных мест. Используются балансирные, шарнирно-рычажные, суппортные и концеравнительные станки.
Оборудование для поперечного раскроя пиломатериалов: станки торцовочные с нижним расположением пилы тс-2 и тс-3, станок торцовочный шарнирно-маятниковый цмэ-за; ленточнопильные столярные станки лс-40-1, лс80-5.
схема организации рабочего места у станка цпа-40: 1 – роликовый стол; 2 – кронштейны для укладки досок на роликовый стол; 3 – торцовочный станок; 4 – штабеля заготовок; 5 – ящик для обрезков; 6 – площадка подъемного лифта; 7 – штабель досок
Производительность станков для поперечного раскроя определяется числом резов в минуту, зависящим от способа раскроя, толщины досок и породы древесины, организации рабочего места и т д. Сменная производительность псм, шт. Заготовок, определяется по формуле псм= тсм(n-m)кд, Где тсм — продолжительность смены, мин; n — число резов в минуту, m — число дополнительных резов на торцевание и вырезку дефектных мест; кд — коэффициент использования рабочего времени равный 0,93.
Производительность станков для продольной распиловки псм, шт. Заготовок, определяется по формулам:
однопильных псм= тсм u кд км ∕ (l m),
многопильных псм= тсм u кд км (z-1) ∕ l,
Где: u — скорость подачи, м/мин; кд и км - соответственно коэффициенты использования рабочего и машинного времени (кд =0,9 - для однопильных; кд = 0,95 - для многопильных; км = 0,7- для однопильных, с ручной подачей; км = 0,9 - для однопильных с механической подачей; км = 0,95- для многопильных); l- средняя длина заготовки, м; m- число продольных резов в одной заготовке; z - число пил в поставе, шт.
Производительность ленточнопильных станков псм, шт. Заготово , определяется по формуле псм = тсм /(60ттс) ,где тсм — сменный фонд рабочего времени, мин; тст - время работы станка, необходимое для раскроя заготовок, ч. (значения тст устанавливаются опытным путем по нормативам времени).
34 Склеивание заготовок из древесины по толщине. Последовательность и содержание операций. Применяемое оборудование, режимы склеивания, производительность, организация рабочих мест.
Первой технолог-ой операцией является подготовка мат-ла. Затем идет формир-ие пакета. Формир-ие пакета в произв-ве склеен-ых дерев. конструкций для строительных изделий осложняется расположением в одном сечении слоев различного качества. При формир-ии пакета слои из п/м 1-ого сорта желательно помещать в растянутую зону на 0,17 высоты поперечного сечения конструкции. Слои из п/м 2-ого сорта желательно помещать в сжатую зону на расстоянии не < 0,17 высоты поперечного сечения. Среднюю зону по высоте клееных изгибаемых, сжатоизгибаемых и сжатых элементов помещают слои из п/м 3-ого сорта.
При изготовлении комбинированных балок из др-ны хвойных и листв. пород обычно заг-ки из листв. пород укладывают в среднюю зону сечения.
35 Склеивание заготовок из древесины по длине. Организация процесса склеивания. Последовательность и содержание операций. Применяемое оборудование, режимы склеивания, производительность, организация рабочих мест.
Распространено также склеивание брусковых заготовок по длине на зубчатый шип. Для склеивания применяют карбамидо-формальдегидные и поливинилацетатные клеи, а также совмещенные из этих двух типов. Склеивание осуществляют холодным способом или с нагревом в поле ТВЧ. При холодном склеивании в зажимных устройствах дают выдержку 1—2 ч (клей М-70). При склеивании с нагревом в поле ТВЧ продолжительность выдержки необходимо рассчитывать по формуле. Для склеивания шиповых соединений используют различные ваймы или другие зажимные устройства, а в линиях для продольного сращивания заготовок — специальные устройства, обеспечивающие продольное сжатие брусков. При склеивании для всех режимов в помещении температура должна быть не ниже 18 ° С, а относительная влажность воздуха не более 65 %. При холодном склеивании наиболее эффективно использовать клей М-70. Склеивание может вестись обычно и с раздельным нанесением компонентов клея. В последнем случае смолу наносят на поверхность одной детали, а отвердитель (5—10 %й раствор щавелевой или ортофосфорной кислоты) на поверхность другой. Преимущество данного способа — практически неограниченная жизнеспособность клеевого состава. При горячем склеивании наиболее эффективно применять клеи, на основе смол КФ-БЖ, КФ-Б, КФ-Ж. Клеевые соединения брусков должны иметь предел прочности на скалывание в сухом состоянии не менее 2МПа, а стыкованные на кромку древесностружечные плиты — предел прочности на статический изгиб не менее 70 % от прочности цельной плиты. Заготовки необходимо склеивать без смещения одна относительно другой. На них не должно быть потеков, клея, масла, вмятин и других дефектов. 1. Торцовка досок на заданный размер заготовок. 2. Раскрой заготовок по ширине 3. Строгание заготовок на четырёхсторонних продольнофрезерных станках. 4. Торцовка на заданный размер с вырезкой дефектов в простроганных деталях с получением короткомерных деталей разной длинны. 5. Фрезерование зубчатых клинообразных шипов. 6. Нанесение клея на шипы. 7. Запресовка соединений и склеивание в заготовку 8. Раскрой кл. заг. на заданную длину.9. Выдержка в стопе. 10. Окончательное строгание в размер по сечению на четырёхсторонних продольно фрезерных станках. В настоящее время широкое применение получили линии автоматического сращивания по длине.
Процесс склеивания брусковых заготовок по длине
Поперечный раскрой пиломатериалов (ЦПА-40, ЦКБ-40.01, ЦМЭ-3А(Б), ТС-2, ТС-3)
Продольный раскрой пиломатериалов (ЦДК-4-3, ЦДК-5-2, ЦМР-4М)
Создание технологической базовой поверхности на пласти и кромке (СФ-4, СФ-6, СФ-6А)
Формирование заготовок по сечению в размер (С25-5, С25-1А, С16-42)
Торцовка в размер брусковых заготовок с одновременной нарезкой зубчатого клеевого соединения (минишип) (ШО10-4, ШД10-8, ФСШ-4)
Намазывание зубчатого клеевого соединения клеем для холодного склеивания и запрессовка заготовок в гидравлической вайме.
Технологическая выдержка заготовок после склеивания (подстопные места)
Формирование сечения и удаление дефектов склеивания
Параметры | ПВА |
Вязкость клея при 20С,с по ВЗ-1 | 11-40 |
Жизнеспособность клея при Т=20С, ч | до 120 |
Расход клея, г/м2 | 260-300 |
Давление прессования, МПа | 0,5-0,6 |
Тем-ра отверждения, С | 18-22 |
1-стол-каретка; 2-направляющая линейка; 3-стол; 4-гидроцилиндр созд. Давление; 5-упор; 6-прижимной валик; 7-пила для чернового реза; 8-участок сборки; 9-нанесение клея; 10-фреза; 11-пила
Прочность зубчатых соединений завис от их параметров и прочности изготовления. Осн. контролир. параметр – это давление склеивания.
-при длине шипа 50 мм Р=1-1,5МПа
-при длине шипа 32 мм Р=2-2,5МПа
-при длине шипа 20 мм Р=3-3,5МПа
-при длине шипа 10 мм Р=5-6МПа
-при длине шипа 5 мм Р=8-10МПа
36 Гнутье древесины. Назначение процесса. Технология гнутья. Применяемое оборудование и организация процесса. Произв-ть, организация рабочих мест
Многие изд-я из др-ны имеют криволинейные детали различной формы. Их м получать различными способами: выпиливанием криволинейных заготовок 'на ленточнопильных станках, методом гнутья прямолинейных заготовок и методом гнутья заготовок из массивной др-ны или шпона с одновременным склеиванием.
Получение заготовок методом гнутья прямолинейных брусков требует спец обор-я и более сложной технологии и по этой причине его примен-е ограничено.
Для повышения способности др-ны к гнутью производят ее ГТО, т. е. повышают ее пластич-е св-ва. Для предупреждения разрыва волокон на выпуклую сторону накладывают стальную шину толщиной 0,2—2,5 мм. При гнутье шина воспринимает растягивающие напряжения, зона растянутых волокон др-ны уменьшается, а зона сжатых увелич-ся и нейтральная линия смещается в сторону растянутых волокон.
На практике др-ну требуется изгибать до малых радиусов. Хвойн и многие листв-е породы непригодны для гнутья при малых радиусах кривизны. Брак при гнутье обусловлен образованием складок на вогнутой стороне из-за неравномерн сжатия др-ны вдоль волокон и низкого сопрот-я сжатия ее поперек волокон. Для устранения брака использ шаблон с насечкой, а в проц гнутья др-ну подпрессовывают . Брусок с шиной изгибается вокруг шаблона / с крупной насечкой. В месте изгиба прессующий ролик 2 прижимает брусок к шаблону и упрессовывает его. Внутренние слои древесины вдавливаются во впадины насечки и принимают равномерную волнообразную форму,
исключая появление складок. Гнутье бруска не доводят до конца, так как возникающие значительные напряжения сдвига могут привести к сколам у
торцов.
Тех процесс изгот-я гнутых дет вкл раскрой на заготовки, их ГТО, гнутье и сушку после гнутья, а также механическую обработку.
В процессе раскроя нельзя допускать в заготовках дефектов, вызывающих брак при гнутье. Заготовки необходимо вырезать из здоровой древесины, а косослой не должен превышать 5—10 %. При обычном гнутье/сучки не допускаются, а при гнутье с одновременным прессованием допускаются в больших пределах.
При ГТО улучшаются пластические св-ва др-ны. Она м проводиться методами пропаривания и проваривания. Оптимальная влажность древесины при гнутье — 25— 30 %, температура в центре заготовки — 100 °С. При меньшей влажности древесина менее пластичная, при большей — в процессе изгиба и сжатия находящаяся в древесных клетках вода может разрывать ее стенки. Кроме того, увеличится срок сушки деталей.
Пропаривание ведут в пропарочных котлах насыщенным паром ' при давлении 0,02—0,05 МПа (102— 105 °С). Время пропаривания определяют по таблицам или диаграммам (рис. 6.28) в зависимости от толщины заготовки и температуры в ее центре — на пересечении горизонтальной и и вертикальной линий.
Ускоренно нагревать заготовки перед гнутьем можно с помощью токов высокой частоты. Пластичность древесины можно повышать пропитыванием ее растворами аммиака и солей: железных и алюминиевых квасцов, хлорида магния, хлорида кальция и др. Древесину можно пропитывать также 40 %-м раствором мочевины или смесью растворов мочевины, формалина, гидроксида натрияи буры. Процесс пропитки весьма продолжительный: растворами аммиака — до 6 суток, другими растворами — из расчета 3 ч на 1 мм толщины заготовки. Гнутье массивной древесины можно осуществлять в станках с холодными формами, в станках с обогревом и с одновременным
Гнутье без шин ведется лишь при больших радиусах гнутья и малой толщине заготовок, например тонких реек.
Гнутье заготовок производят на замкнутый и незамкнутый контур. При гнутье на замкнутый контур заготовки изгибают вокруг гладкого или зубчатого шаблона При гнутье на незамкнутый контур по окончании процесса концы шин стягивают стяжкой и заготовку вместе с шаблоном и шиной отправляют на сушку. Использ также гнутарно-сушильные станки с горячими шаблонами, в которых заготовки после гнутья остаются в станке для
сушки. Во внутреннюю часть шаблона подается пар (0,05—0,07 МПа) для обогрева. После гнутья заготовки прижимают к шаблону колодками . Выдерживают их в станке для подсушки до влажности 12— 15 %, при которой стабилизируется форма. Окончательное досушивание осуществляют в сушильных камерах после распрессовки и укладки на вагонетку.
Обработка гнутых заготовок не отличается от обработки обычных прямолинейных.
Рабочее место при гнутье заготовок должно быть организовано так, чтобы пропаренные заготовки было удобно сразу подавать к станку. Пропарочные котлы должны, иметь надежную герметизацию и манометры, на которых красной чертой отмечено верхнее значение рабочего давления. Подача пара до открытия пропарочного котла должна быть прекращена. Детали достают только крючьями.. При гнутье нельзя наклоняться над .изгибаемой заготовкой.
контур с шаблоном: а — гладким 7; б — зубчатым 9; 1 — вал; 2 — ролик; 3 — шина; 4—-направляющая каретки; 5— каретка; 6 — заготовка; 8 —редуктор
шлифуемой поверхности детали, норматив расхода шлифовальной шкурки.
Расчет норм расхода шлифовальной шкурки на изделие выполняют в два этапа. Вначале заполняют ведомость расчета площадей шлифуемых поверхностей на изделие, а затем составляют ведомость расчета норм расхода шлифовальной шкурки на изделие.
37 Вторичная механическая обработка заготовок. Состав и последовательность операций. Оборудование, режимы, производительность, организация рабочих мест. Техника безопасности.
Комплекс технологических операций по механической обработке заготовок условно называют вторичной или окончательной механической обработкой. Необходимость такой обработки вызвана тем, что при склеивании и облицовывании встречаются сдвиги склеиваемых слоев, а чистовые заготовки требуют еще обработки для получения взаимозаменяемых деталей, отвечающих требованиям конструкторской документации по форме и качеству. Вторичная механическая обработка состоит из двух частей: окончательной обработки заготовок, обеспечивающей форму, и подготовки поверхности к отделке, формирующей качество.
К стадии вторичной (окончательной) механической обработки относятся технологические операции по формированию шипов, фрезерованию профилей, выборке гнезд и сверлению отверстий. Требования к шероховатости поверхности готовой детали обычно выше технических возможностей оборудования и существующих методов первичной обработки цилиндрическим фрезерованием при оптимальных режимах резания. Поэтому в завершение окончательной обработки вводится обычно технологическая операция для подготовки поверхности готовых деталей и сборочных единиц к отделке.
Порядок выполнения технологических операцийпо вторичной механической обработке заготовок должен быть таким, чтобы поставленная цель достигалась с наименьшими затратами труда и энергии. Предлагаемая последовательность технологических операции по окончательной механической обработке заготовок может изменяться, в зависимости от конкретных условий. При этом необходимо, чтобы последующая операция механической обработки устраняла возможные дефекты предыдущей, а предыдущая исключала необходимость излишнего удаления материала при обработке на последующей операции.
Возможная последовательность и состав технологических операций по окончательной обработке брусковых заготовок следующая: формирование шипов и проушин – фрезерование – выборка пазов и продолговатых гнезд – сверление отверстий – подготовка поверхностей к отделке или: формирование шипов и проушин – выборка пазов и продолговатых гнезд – фрезерование – сверление отверстий – подготовка поверхностей к отделке. В случае технологических операций по окончательной обработке щитовых заготовок возможная последовательность и состав технологических операций может следующая: фрезерование – сверление отверстий – подготовка поверхностей к отделке или: выборка пазов и продолговатых гнезд – фрезерование – сверление отверстий – подготовка поверхностей к отделке.
Дата добавления: 2018-02-28; просмотров: 983; Мы поможем в написании вашей работы! |
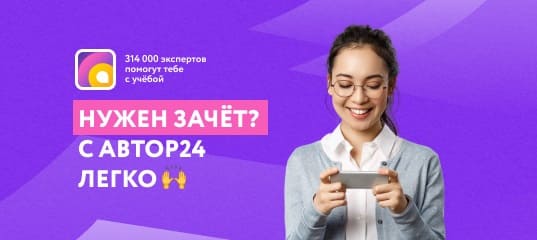
Мы поможем в написании ваших работ!