Раскрой плитных и листовых материалов
Эффективность раскроя зависит от применяемого оборудования и организации процесса раскроя плит и листовых материалов. По технологическим особенностям применяемое при раскрое плит оборудование можно разделить на 3 группы:
- к первой относятся станки, имеющие несколько суппортов продольного пиления и один поперечного. Раскраиваемый материал укладывают на стол-каретку. При движении стола в прямом направлении суппорты продольного пиления раскраивают материал на продольные полосы. На каретке имеются переставные упоры, воздействие которых на конечный выключатель вызывает автоматическую остановку каретки и привод в движение поперечного суппорта пиления;
- ко второйотносятся станки, имеющие также несколько суппортов продольного пиления и один поперечного, но стол-каретка состоит из двух час гей. При продольном пилении обе части стола составляют одно единое целое, а при обратном движении каждая часть движется отдельно до стопорной позиции, определяющей положение поперечного реза. Таким образом, достигается совмещение поперечных резов отдельных полос;
- к третьей относятся станки, имеющие один суппорт продольного движения и несколько - поперечного. После каждого хода суппорта продольноного пиления полоса на подвижной каретке подается для поперечного раскроя. При этом
срабатывают те суппорты, которые настроены на раскрой данной полосы. Суппорт продольного пиления может выполнять несквозной рез (подрезание). Кроме этого, имеются однопильные форматно-раскроечные станки и центры.
|
|
Первая группа оборудования (например, станок ЦТЗФ-1; 1ДТ4Ф) Ориентируется на выполнение простейших индивидуальных карт раскроя. Это снижает коэффициент использования материала.
При реализации более сложных схем после продольного раскроя возникает необходимость в съеме отдельных полос со стола с дальнейшим их накоплением для последующего индивидуального раскроя. При ном резко возрастают трудозатраты, падает производительность.
Вторая группа (например, станок SpK401) позволяет выполнять схемы раскроя с разнотипностью полос, равной двум. При большой разнотипности возникают те же трудности, что и в первом случае.
Третья группа (станки ЦТМФ, МРП) позволяет выполнить раскрой более сложных схем с разнотипностью полос до пяти. Эта группа оборудования имеет высокую производительность и наиболее перспективна.
Раскрой листовых материалов
Для выполнения операций раскроя можно использовать бумагорезательные машины, гильотинные ножницы.
На гильотинных ножницах НГ-18-1. НГ-28, НГ-30, «Куппер» раскраивают шпон в пакетах в продольном, поперечном направлениях без последующего фугования кромок перед ребросклеиванием.
|
|
Основные узлы ножниц: станина, две траверсы - ножевая и прижимная, каретка с упорами, гидро- и электрооборудование. Станина выполнена в виде сборной конструкции и состоит из рабочего стола, направляющих стоек и переднего стола. Ножевая и прижимная траверсы представляют собой сварную балку жесткой конструкции. В нижней части ножевой траверсы имеется плоскость для крепления ножа. Привод ножевой траверсы гидравлический. Упоры каретки выполнены откидными. Настройка упоров на ширину обрезаемого материала производится с помощью механизма
Отсчета.
Прямолинейная и параллельная рубка шпона - существенное достоинство станков типа «Куппер EFS». Высокая точность рубки обеспечивает в дальнейшем качественное склеивание шпона любых сортов. Позиционное устройство управления параллельным упором снабжено цифровым измерителем ширины, цифровой клавиатурой счетчиков циклов рубки и кнопками выбора различных типов операций, высокое качество рубки достигается благодаря поворотному и мощному протягивающему движению ножа под углом 20 градусов. Линия рубки маркируется световым лучом. Широкая прижимная пластина позволяет выравнивать перед рубкой даже волнообразный шпон. Мощный кривошипный привод позволяет рубить шпон поперек волокон. Техническая характеристика оборудования приведена в табл. 19. На бумагорезательных машинах (например, БРП-4М) раскраивают шпон и пленки на основе пропитанных бумаг, пленочные полимерные материалы. Техническая характеристика оборудования приведена в табл. 20.
|
|
На участках для централизованного изготовления пленок на основе пропитанных бумаг применяется оборудование для раскроя пленок на форматные листы - линия ЛРШ-1 и для раскроя рулонов пленки по ширине - станок С5-28-02
19 Раскрой плитных материалов. Организация процесса раскроя (виды раскроя). Эффективность раскроя. Задачи оптимального планирования раскроя. Оборудование. Проектирование участков раскроя. Производительность. Охрана труда и техника безопасности.
В производстве изделий из древесины широко используют плитные материалы, изготавливаемые в соответствии с требованиями стандартов на них. Процесс раскроя плитных материалов проще, чем досок, поскольку при их раскрое нет ограничений по качеству, цвету, дефектам и др. Они стабильны по качеству и формату. Количество типоразмеров заготовок должно соответствовать их комплектности на выпуск изделий, предусмотренных программой. Раскрой плитных материалов организуют в зависимости от назначения получаемых заготовок; его принято делить на три способа: индивидуальный, комбинированный и смешанный (совместный)
|
|
Способы раскроя:
а- индивидуальный; б- комбинированный; в- смешанный (совместный).
При индивидуальном раскрое каждая плита раскраивается на один типоразмер заготовок. Индивидуальный способ раскроя сопровождается большим количеством отходов.
При комбинированном способе раскроя из одного формата можно выкраивать по нескольку различных типоразмеров заготовок или деталей с обязательным соблюдением комплектности по выкраиваемым заготовкам. С точки зрения экономного расхода материалов, комбинированный способ раскроя является, как правило, более эффективным, по сравнению с индивидуальным. Но он более сложен, так как при большом числе типоразмеров трудно обеспечить условие комплектности в каждой карте раскроя.
При смешанном (совместном) раскрое возможно использование вариантов индивидуального и комбинированного раскроя для различных случаев. При совместном способе карта раскроя предусматривает различные типоразмеры без учета комплектности по каждой карте раскроя, но с максимальным выходом деталей и с минимальным повторением одинаковых деталей в разных картах раскроя. Этот способ раскроя является наиболее эффективным по сравнению с остальными.
Производительность на участке раскроя плитных материалов
П=60∙Kд·Kм∙n∙m/tц, П=60∙ Kд·Kм ∙n∙m/ tц,
Kд – коэффициент использования рабочего времени; Kм – коэффициент использования машинного времени. n – коэффициент заготовок, получаемых из одной плиты, шт., определяется по карте раскроя; m– количество одновременно раскраиваемых плит (листов) в пакете, шт. tц – суммарное время, затрачиваемое на подготовку пакета и его продольный раскрой на полосы, мин.
Для раскроя плитных материалов широко применяются круглопильные однопильные станки с ручной подачей: Altendorf. Вертикальные форматно-раскроечные станки заменяют обычные форматно-раскроечные там, где необходима экономия места GVS 13; Автоматические форматно-раскроечные круглопильные станки (центры) с верхней прижимной балкой и пильной кареткой для раскроя облицованных и необлицованных плит из древесных материалов пакетным методом с системой компьютерного управления, оптимизацией раскроя. Его отличают высокое качество распила, точность позиционирования, надежность, мощное и в то же время простое в использовании цифровое управление, широкие технологические возможности.
Первичная механическая обработка заготовок. Задачи, последовательность и содержание операций. Виды технологических баз и правила их выбора. Организация процесса. Охрана труда и техника безопасности.
Брусковые заготовки склеиваются по длине, ширине, толщине с целью получения деталей больших размеров. В связи с этим детали подвергаются первичной механической обработке. Задачей является создание базовых поверхностей для дальнейшей обработки заготовок, а также подготовка к склеиванию и облицовыванию.
Создание базовых поверхностей. Черновые заготовки имеют значительные погрешности формы и размеров. Точная обработка заготовок, обеспечивающая взаимозаменяемость деталей, может быть достигнута при наличии у них чистовых баз, которые используются для базирования заготовок на станке при последующей обработке. Обработку начинают с создания установочной чистовой базы. Вначале выравнивают широкую пласть заготовки. Полученная база используется при обработке следующей поверхности — кромки. Имея выверенные по плоскости и под прямым (как правило) углом поверхности, обрабатывают следующие, придавая детали, требуемые чистовые размеры. При выполнении дальнейших операций необходимо использовать одну и ту же базовую поверхность для максимального числа операций, так как смена баз обусловливает появление случайных погрешностей и увеличивает общую погрешность обработки.
Обрабатываемые детали занимают на станке определенное положение относительно инструмента. Поверхности деталей, прилегающие к устойчивым устройствам станка в процессе обработки, называются технологическими базами. К ним относятся поверхности используемые при контрольных измерениях точности деталей, т.е. поверхности, от которых отсчитывают размеры, их называют измерительными базами. Установочные базы могут быть черновыми, т.е. грубыми, необработанными, и чистовыми – чисто обработанными.
При сборке узлов или изделий каждой детали должно быть придано определенное положение относительно других. Для этого используют сборочные базы, т.е. совокупность поверхностей, которые задают положение детали в изделии относительно других деталей. Эти базы совпадают с измерительными. Использование одних и тех же баз способствует повышению точности сб.единиц.
Точки, линии и плоскости, относительно которых указывают размеры деталей, называют конструкторскими базами. Ими могут быть не только реальные поверхности, но воображаемые. Понятие «база» включает комплекс поверхностей, линий и точек относительно которых деталь ориентируют при проектировании, обработке и сборке.
Технологические схемы мех.обработки брусковых заготовок:
1. Создание базовых поверхностей на фуговальных станках- обработка в размер на рейсмусовых станках- торцев. на ст-х для оперечного раскроя- выборка продолговатых гнезд и отверстий на сверлильно-пазовальных ст-х- шлифование
2. Создание базовых поверхностей на фуговальных станках- обработка в размер на рейсмусовых станках- формирование шипов(проушин)и торц-е на шипорезных ст-х- шлифование
3. Создание базовых поверхностей на фуговальных станках- обработка в размер на рейсмусовых станках по толщине- фрез-е на прод-фрез-х станках-торцевание-формирование шипов(проушин)или сверление отверстий, или выборка продолговатых гнезд и отверстий- шлифование
4. Создание базовых поверхностей на фуговальных станках- обработка в размер на 4-хсторонних продольно-фрез-х ст-х --торцевание-формирование шипов(проушин)или сверление отверстий, или выборка продолговатых гнезд и отверстий- шлифование
5. обработка в размер на рейсмусовых станках- фрез-е профиля на фрезерных ст-х-- торцевание-формирование шипов(проушин)или сверление отверстий, или выборка продолговатых гнезд иотверстий- шлифование
6. обработка в размер на рейсмусовых станках– торцевание—выборка продолговатых гнезд и отверстий—сверление отверстий--- шлифование
7. обработка в размер на рейсмусовых станках--формирова шипов(проушин)и торцевание на шипорезных ст-х—сверление отверстий-- шлифование и др.
8. обработка в размер на на 4-стор-х прод-фрез-х станках--торцевание-
выборка продолговатых гнезд и отверстий-- шлифование
9. обработка в размер на на 4-стор-х прод-фрез-х станках--формирование шипов(проушин)и торцевание на шипорезных ст-х--свеление отверстий-- шлифование
10. Создание базовых поверхностей -- обработка в размер --формирование шипов(проушин)—торцевание-- сверление отверстий-- выборка продолговатых гнезд и отверстий на поточных, автоматич-х и полуавтом-х линиях.
Создание базовых пов-й вызвано необходимостью повышение точности изготовления деталей за счет создания у заготовки технологической установочной базы.
Пов-сти заготовок, получ-х при раскрое п/м, в основном не могут служить технол- ой базой, т.к. имеют низкое кач-во и не являются плоскими в следствие деформаций, вызв-х внутр-ми напряжениями в др-не от усушки. Операцию создания базы вып-ют на одно- или двухсторонних фуговальных станках. На одностороннем обрабатывают только пласть заготовки, на двустороннем- две смежные стороны(пласть и кромка), т.е. создаются 2 базовые пов-сти и угол.
21 Первичная механическая обработка. Обработка заготовок в размер. Применяемое оборудование, режимы обработки, производительность, организация рабочих мест.
Для создания базовой поверхности на одной или двух смежных сторонах используют в основном фуговальные станки. Они бывают с ручной (СФ4-2, СФ6-1 и др.) и механической (СФ4-1А, СФ6-1А, С2Ф4-1, СФК6-1 и др.) подачей.
В зависимости от ширины стола бывают;
-легкие (до 350 мм), - средние (400-600), - тяжелые (600-800)
В зависимости от количества реж. Инструментов:
- односторонние и – двухсторонние.
Часовую производительность фуговального станка можно определить по формуле
|
где и — скорость подачи (при механической — 7—30 м/мин, при ручной примерно 10 м/мин);
Кр - 0,9—0,93;
Км при ручной подаче и длине заготовок до 0,5 м равен 0,7, при длине заготовок свыше 1 м и механической подаче — 0,9;
п — количество одновременно обрабатываемых заготовок;
/мг — длина заготовки;
т — число проходов .
Организация рабочего места
Обработка заготовок в размер по сечению. После создания базовых поверхностей заготовки обрабатывают в размер по сечению. Для этого применяют рейсмусовые и четырехсторонние продольно-фрезерные станки. Рейсмусовые станки бывают односторонние с верхним расположением ножевого вала (СР4-1, СР6-9, СР8-2, СР12-3 и др.) и двухсторонние с верхним и нижним расположением ножевых валов (С2Р8-3, С2Р12-
3, С2Р12-ЗА). На всех рейсмусовых станках подача механическая, которая осуществляется передними и задними вальцами.
Для надежного сцепления с заготовками передний подающий валец выполнен рифленым, а остальные, контактирующие с обработанными поверхностями, гладкими. Кроме того, для одновременного фрезерования заготовок разной толщины (до б мм) передний валец сделан секционным.
Часовая производительность рейсмусового станка определяется по
формуле
Плоскую и профильную обработку прямолинейных заготовок с четырех сторон за один проход можно выполнить на четырехсторонних продольно-фрезерных станках , которые имеют не менее четырех ножевых валов. В зависимости от ширины строгания они подразделяются на легкие (калевочные) — для обработки профильных мебельных и столярных деталей шириной до 160 мм, средние — для обработки деталей шириной до 250 мм и тяжелые
— для обработки погонажных изделий шириной до 650 мм. Подача у четырехсторонних станков вальцовая или вальцово-гусеничная.
Высокого качества в изготовлении четырехсторонних продольно-фрезерных станков добилась немецкая фирма «Вейниг». Станок под названием «Профимат» может изготовить любой произвольный профиль. Четырехсторонний станок обслуживают двое рабочих: один подает заготовки в станок, а другой принимает их и складывает. В отличие от рейсмусовых в четырехсторонних станках и линиях на их основе заготовки подаются по одной, торец в торец.
Часовая производительность четырехсторонних станков
Торцевание заготовок Заготовкам должна быть придана точная длина и ровные торцовые плоскости, расположенные под прямым или другим углом к боковым граням. Торцовку заготовок осуществляют на круглопильных станках с одним, двумя или несколькими пильными дисками.
На однопильном торцовочном станке с кареткой (Ц6-2) можно торцевать заготовки под любым углом. Заготовку базируют по столу и направляющей линейке. При первом резе заготовку устанавливают на каретке «на глаз» так, чтобы опиливался минимальный припуск (рис. 6.21, а). Каретку надвигают на пилу вручную. Для торцевания второго конца заготовку переворачивают и отторцованным концом прижимают к упору, установленному от плоскости пилы на длину заготовки.
Торцовочные станки с кареткой удобны, но малопроизводительны. Часоваяпроизводительность однопильного торцовочного станка
где Кр = 0,9 — 0,93; п — количество торцуемых
заготовок в одной закладке; tц — продолжительность одного цикла; т — кратность торцуемых заготовок.
Двупильного концеравнителя
Пч=60uКрКмn/lупр заг./час,
lупр – растт между упорами транспрт.цепи.
22. Склеивание и облицовывание. Подготовка материалов, способы нанесения клея. Методы интенсификации процесса склеивания древесины. Оценка качества склеивания.
Склеивание является одним из основных видов соединений при производстве изделий из древесины. Оно позволяет получать детали требуемых размеров, увеличивать их формоустойчивость, прочность и улучшать декоративные свойства изделий, повышать полезный выход заготовок, использовать короткомерные и низкосортные заготовки и отходы. Основные его виды: склеивание заготовок и деталей из древесины, древесных, полимерных и других материалов; склеивание деталей из измельченной древесины; склеивание с одновременным гнутьем заготовок из шпона, фанеры, массивной древесины; облицовывание пластей и кромок щитовых деталей; склеивание при сборочных работах. Технологический процесс склеивания включает следующие основные стадии: подготовку склеиваемых материалов; подготовку клеевых растворов; нанесение клея на склеиваемые поверхности; запрессовку склеиваемых заготовок и выдержку их под давлением, выдержку склеенных заготовок после запрессовки.
Качество клеевого соединения предопределяет правильный выбор вида клея. К клею предъявляются технологические и эксплуатационные требования. Первые обусловливают применимость клея в производственных условиях, вторые обеспечивают требуемое качество соединений. Технологические требования регламентируются технологическими режимами, эксплуатационные — техническими условиями {прочность склеивания, водо- и влагостойкость, биостойкость и др.).
Клеевые соединения должны обеспечивать такую прочность склеивания, чтобы она была не ниже прочности склеиваемых материалов. Однако это не всегда достижимо. Например, торцовые клеевые соединения древесины такой прочности не обеспечивают, они составляют примерно 80 % прочности цельной древесины. Клеевые соединения на кромку древесностружечных плит имеют еще меньшую прочность. На прочность клеевого соединения влияют качество подготовки склеиваемых материалов, марка и качество клея, способ склеивания, параметры технологического режима склеивания и технологической выдержки, а также условия последующей эксплуатации клееной конструкции. Подготовка поверхностей к склеиванию зависит от вида материалов, их размера, формы изделия, применяемого оборудования для склеивания и др. Она осуществляется различными способами — пилением, фрезерованием, строганием, шлифованием. При приготовлении клея учитывают его марку. Клей готовят в специально оборудованном помещении с приточно-вытяжной вентиляцией.
Склеивание осуществляют при нормальной температуре в помещении (холодное склеивание) и при повышенной (горячее склеивание).
Клей на детали наносят вручную (как правило, на одну из поверхностей) или клеенаносящими вальцами. В первом случае используют кисти, щетки и специальные приспособления, Для местного нанесения клея используют пластмассовые емкости или тюбики, горлышко их имеет наконечник с отверстием, которым удобно наносить клей в отверстия, на щечки проушин и т. д.
Клеенаносящие вальцы бывают трех видов. Вальцы с нижним питаниемнеудобны в работе, с их помощью нельзя добиться равномерного распределения клея по поверхности заготовки. Вальцы с нижним и верхним питанием позволяют наносить клей на одну или две стороны и регулировать толщину клеевого слоя. Вальцы с дозирующими роликами более совершенны. Клеенаносящие вальцы покрыты резиной с рифлением, дозирующие выполнены стальными, полированными. Клеевой слой можно регулировать с большой точностью.
Холодное склеивание требует минимальных затрат энергии, но оно продолжительно во времени (как правило, 24 ч), поэтому трудно поддается автоматизации. Необходимы также значительный операционный запас заготовок и большая производственная площадь. В связи с этим оно применяется при склеивании крупногабаритных заготовок, а также если клеевой шов значительно удален от внешней поверхности деталей, например при сборочных работах.
Склеивание с нагревом осуществляют при различных способах подвода тепла к клеевому слою — кондуктивном, конвективном, за счет предварительного аккумулирования тепла в одной и двух склеиваемых заготовках, путем нагрева в поле токов высокой частоты (ТВЧ).
Кондуктивный нагрев является одним из наиболее распространенных и применяется при склеивании тонких, толщиной до 10 мм, заготовок, которые контактируют с горячими плитами пресса. Такой способ широко применяется при облицовывании пластей и кромок щитовых заготовок. Нагрев осуществляют обычно паром, горячей водой, маслом или низковольтным током промышленной частоты.
Конвективный нагрев применяют при наклеивании тонких облицовочных материалов на основу сложной формы, например при облицовывании профильных деталей в пневматическом или мембранном прессе. Тепло передается горячим воздухом или инфракрасным облучением.
Нагрев за счет аккумулированного тепла можно осуществлять при достаточной, не менее 10 мм, толщине склеиваемой заготовки. Перед склеиванием одну (более массивную) или обе заготовки нагревают кондуктивным или конвективным способом.
Нагрев в поле ТВЧ производят в специальном прессе. Склеиваемые заготовки помещают между электродами, к которым подводят ток высокой частоты. Высокочастотное поле взаимодействует с молекулами материала,
23 Подготовка шпона к облицовыванию. Применяемое оборудование, режимы обработки, производительность, организация рабочих мест.
Эта операция включает подбор и разметку, раскрой и фугование кромок пачек шпона. При облицовывании применяют строганый и лущеный шпон. Абсолютная влажность строганого и лущеного шпона должна быть 8 ±2%. Различают мелкослойный и крупнослойный шпоны — по проявлению годовых слоев, а также правую и левую стороны листа — по состоянию поверхности.
Правая сторона (более гладкая и плотная) получается на поверхности шпона, прилегающей к прижимной линейке во время его изготовления. Левая сторона (более шероховатая, с мелкими разрывами). При изготовлении шпона она сходит с острия ножа. Предпочтительно, чтобы лицевой стороной шпона была правая сторона. Пачку шпона подбирают по породам древесины, размерам, качеству, цветовому и текстурному рисунку листов. При обработке лущеного шпона, идущего на изготовление внутренних облицовок, пачки шпона не подбирают. Для максимального выхода шпона первый лист отобранной пачки размечают по шаблонам. Это дает возможность формировать облицовку с наиболее красивым рисунком при минимальных отходах шпона. Рабочий, производящий разметку, должен знать размеры и назначение всех облицовок для деталей изделия. Подбор и раскрой шпона показаны на рис. 17. При раскрое на круглопильных станках (рис. 17, 6, I) пачку шпона закрепляют на каретке зажимом. Каретка перемещается по пазам стола станка до пилы. После опиловки продольные кромки не имеют чистоты поверхности и их необходимо фуговать. Операция фугования не требуется, если шпон раскраивают на гильотинных ножницах с прижимной балкой (рис. 17, 6, II). Пачку шпона укладывают на столе, зажимают прижимной балкой и обрезают ножами. Схема организации рабочего места на гильотинных ножницах показана на рис. 18, а. С подстопного места пачки шпона перекладывают на стол и на станке раскраивают. Раскроенные пачки укладывают на этажерки. Необходимо постоянно следить за остротой лезвий режущих ножей.Кромки делянок в пачках фугуют на фрезерных, фуговальных и кромкофуговальных станках. Схемы фугования кромок шпона даны на рис. 19. При фуговании на фрезерном станке пачку шпона зажимают в приспособлении и вместе с ним перемещают по столу станка. При перемещении зажимного приспособления по упорному кольцу кромки обрабатываются фрезой. Кромки выравнивают на кромкофуговальном станке. Пачку шпона укладывают на стол станка, зажимают балкой. При движении каретки с пилой и фрезой по направляющей на кромке вначале опиливают крупные неровности, а затем фрезеруют тонкий слой, что позволяет получить требуемое качество поверхности.
Кромки следует обрабатывать при скорости подачи каретки 6 м/мин и скорости резания фрезы не менее 25 м/с. Толщина слоя, снимаемого фрезой за один проход, должна быть не более 1,5 мм. Схема организации рабочего места при работе на кромкофуговальном станке показана на рис. 18, б. Пачки нефугованного шпона с этажерки перекладывают на стол, на котором выравнивают кромки в пачке. В станке обрабатывают вначале одну, а затем вторую кромку пачки.
Часовая производительность гильотинных ножниц НГ 18
(комп/ч).
где n – количество полос шпона в стопе, шт.; tц – цикл обрезки одной стороны пакета, мин (0,5); l∙b – площадь листа в чистых размерах, м2; ∑Si – площадь комплекта с припусками, м2.
Псм=Тсм∙n∙Кд/ tц∙z,
где tц – цикл обрезки одной стороны пакета; tц =0,5 мин; z– количество резов по периметру; Kд – коэффициент использования рабочего времени, Кд=0,7; n –число полос шпона в пакете
Часовую производительность фуговального станка можно определить по формуле
Часовая производительность фрезерного станка Ф-130-04
где tц – время обработки одной заготовки, мин; Z –число обрабатываемых концов заготовки.
24 Технология облицовывания пластей щитовых заготовок в однопролетных и многопролетных прессах. Производительность, организация рабочих мест.
Облиц-е пластей в многопролетных прессах. Исп-т многопрол. прессы типа П713А, П713Б, которые имеют по 10 пролетов, с размерами плит 2000x1300 мм. Они являются устаревшими, однако еще используются на многих предприятиях.
Щиты очищ. от пыли, затем на них наносят клей на основе КФС, в кот-ю добавл. 1 %-й хлорид аммония. Сформированные пакеты загружают в пресс вручную или механически с помощью загрузочных этажерок. Во всех пролетах заготовки д.б. уложены строго одна над другой.
Облиц-е пластей в однопролетных прессах. Комплекс АКДА 4938-1 имеет ленточную загрузку пресса, щеточный станок для удал. пыли, улучшенную конструкцию питателя и укладчика. Размер плит пресса 3,3 х 1,8 м, усилие пресса 6300 кН. В комплексе АКДА 4940-1 увеличены плиты пресса (5,2 х 1,8 мм) и усилие (до 10 000 кН), гидроцилиндры расположены сверху, что ускоряет время смыкания; улучшена конструкция питателя и укладчика.
Для скоростного облицовывания в однопролетных прессах рекомендуются КФ клеи на основе смол КФ-Ж(М), КФ-БЖ при наибольшей дозировке отвердителя.
Комплекс АКДА 4938-1 работает следующим образом:
Питатель пневмотолкателем подает поштучно щиты в щет-й станок со скоростью 15-20 м/мин. Затем в клеенанос. станке на обе стороны щитов нанос. клей, щиты дисковым конвейером передаются на формирующий конв-р. Пакеты из щитов и шпона формир-ся на лент. формирующем конв-ре. После того как загружен конвейер и закончено время выдержки под давлением предыд. запрессовки, плиты пресса размык. и пакеты лент. конв-ром передаются на приводной конв-р пресса. Облицован щиты одноврем. перемещ на ускоренный лент. разгруз. конв-р-укладчик с подъемной платформой накопителя. После загрузки пресса плиты его смык. и ведется пресс-е. Пресс ДА4938-1 работает в автом. режиме и позвол. вести загр. и выгр. деталей автом-ки. Облиц. щиты направл. на место выд-ки. Облиц-е ведут по следующему режиму.
Часовую производительностьпрессов определяем по формуле
где Кр - коэф. исп-ния раб. врем. (Кр=0,85—0,9); п — число рабочих промежутков пресса; Fnp — площадь плит пресса, м2 ; Кг — коэффициент заполнения плит пресса (К3=0,7); tu — прод-ть цикла одной запрессовки, мин. Формула (7.5) может также иметь следующий вид:
где т — кол-во заготовок в одном промежутке пресса. Продолжительность цикла:
где tn, t3, tnp, tp — соотв. время подготовки пакетов, загрузки пресса, пресс-я и разгр.пресса.
Так как подготовка пакетов выпол-ся во время пресс-я, то в расчет приним. то время, кот-е явл. болыпим. Для однопрол. прессов tn<tnp , для многопролетных - tn>tnp,, поэтому /пр при определении цикла учитывать не следует.
25 Технология облицовывание щитов методом постформинг. Особенности. Материалы, оборудование, режимы, производительность, организация рабочих мест.
Суть этого метода заключается в том, что после облицовывания пластиком оставляется свес, который затем заворачивается и приклеивается к плите (ДСП). Покрытие по типу постформинга является одним из самых прочнейших и имеет отличную износостойкость, царапоустойчивость и стойкость к выцветанию.
Метод постформинга допускает облицовывание любыми материалами, но наибольшее распространение получило облицовывание ламинатами - многослойными пластиками на основе бумаг, пропитанных меламиновыми смолами. В зависимости от требований к прочности и стойкости поверхности к абразивному износу эти пластики делятся по технологии их производства: на пластики CPL - пластики непрерывного способа производства и HPL - пластики высокого давления, изготавливаемые в плоских многоэтажных прессах. Особенность продукции, изготовленной с применением постформируемых пластиков, - закругленные кромки и минимальное количество швов.
Облицовывание на позиционном оборудовании:
Для облицовывания профильных кромок щита со специально оставленным свесом пластика (после приклеивания) исп.сец.станки циклопроходного типа .Облицовочный пласитк пластифицируется нагретой шиной .При передвижении шины по профилю кромки материал принимает форму кромки и приклеивается. Облицовку способом постформинг осуш. На разл.станках, например РФ10/31 фирмы БРАНД.
Производительностьпозиционного:
Проходного: (Для одностороннего)
Двустороннего: ,Где n-кол-во сторон
L-длина кромки l- межторцовый разрыв
Постформинг - процесс формирования термопластичного материала на основу заданной формы под высоким давлением.
Процесс постформинга является незаменимым при изготовлении деталей типа столешниц и подоконников.
Материалы, используемые в процессе постформинг:
Клеи для постформинга должны обладать особенно высокой первоначальной схватываемостью для того, чтобы противостоять напряжению материала и усилию по его разгибанию.
Рекомендуемый тип клея для станков постформинга - универсальный контактный полихлоропреновый PROTOPREN 299 extra на основе растворителя. Нанесение клея осуществляется с помощью кисти или с помощью специальной распылительной головки, работающей при температуре от +55 °С до +60 °С.
Материалы для облицовывания. Процесс постформинга допускает облицовывание любыми материалами: ламинатами, натуральным шпоном, пленками на основе бумаг. Наибольшее распространение получило облицовывание ламинатами. Почему предпочтителен для обклеивания ламинат? Он долговечен, по внешнему виду эстетичен.
Нет проблем цвета и дизайна рисунка. не линяет, не держит пятен, легко чистится.
Оборудование для постформинга обеспечивает оптимальное облицовывание поверхности пласти и кромки заготовки одним и тем же непрерывным материалом. Этот метод идеален , так как заготовка меньше подвергается механическому, тепловому или химическому воздействию, а так же воздействию влаги. Этот тип воздействия может проявить отмеченное отрицательное воздействие на мебель, особенно изделия с необработанными кромками..
Постформинг - метод облицовывания, который увеличивает практичность мебели, а значит и срок ее эксплуатации. Некоторые типичные примеры:
• столешницы и рабочие поверхности кухонь
• мебель для ванной
• офисная мебель
• внутренние полки
• прилавки магазинов
• мебель для банков (стойки)
• барные стойки
• лабораторная мебель
• наружные подоконники
26 Технология облицовывание кромок щитов методом софтформинг. Особенности. Материалы, оборудование, режимы, производительность, организация рабочих мест.
В ее основу были положены способ и режимы хорошо известного к тому времени метода постформинг (Postforming) с использованием клея на основе ПВА-дисперсии.
При облицовывании кромок сложного профиля (способ софтформинг) в станки встраивают блоки, в которых ролики выставляются под углами для прикатки эластичного облицовочного материала к кромке . Для каждого вида профиля можно применить отдельный съемный блок. Клей наносится на кромку, подсушивается и активируется перед прикаткой кромочного материла инфракрасными нагревателями . Если применяют кромочный материал с нанесенным ранее клеевым слоем, перед прикаткой активируют струей горячего воздуха, для чего у станков предусмотрен набор агрегатных устройств. Для одностороннего облицовывания можно сип. Оборудование фирмы «Бранд» типа КВ14-2/200, также Хомаг и др.
Сегодня под способом «софтформинг» понимается процесс облицовывания профильных кромок щитовых деталей путем наклеивания на них полосовых или рулонных облицовочных материалов с использованием клея-расплава.
Станки для облицовывания методом «софтформинг» должны также обеспечивать облицовывание не только профильных, но и плоских кромок. Вместе с тем, при облицовывании плоских кромок для достижения большей прочности производится нанесение клея-расплава на кромку детали. Но нанести клей-расплав на профиль невозможно, и он наносится на оборотную сторону облицовочного материала кромки. Для этого клеенаносящие узлы лучших (и более дорогих) станков для облицовывания профильных кромок выполняются универсальными и имеют два клеенаносящих ролика, установленных в одном бачке
Производительность
:
Где L-длина кромки l- межторцовый разрыв
Софтформинг - облицовывание профильной (любого профиля) кромки материалом рулонным кромочным уже после облицовывания пластей.
Для софтформинга прим. позиционные и проходные станки.
Особенность и сложность этого процесса состоит в точном снятии свесов кромочного материала и облицовки пласти на лицевой стороне детали, в месте их стыка.
Оборудование: для облицовки профильной кромки плиты:
-пневмат настольное устройство торцевой обрезки (для обраб. торц. свесов кромочного мат-ла после его приклеивания);
-фрез. ст. для снятия свесов кромочных мат-в по пласти;
- станок для обраб. прямолин. деталей и деталей с внешними и внутренними радиусами;
- фрез. ст.для снятия свесов кромочных мат-в по полости пневм. для приклеивания кромки.
Произв-ть участков облиц.методом рассчитывается в зав-ти от типа оборуд.: если это проходные линии, то через скорость подачи (П=Т*Кр*Км*U/(L+∆L)); если оборудование позиционное, то через время цикла (например обрезка свесов на позиц станке) (П=Т*Кр/tц).
27 Технология облицовывание криволинейных кромок щитов. Особенности. Материалы, оборудование, режимы, производительность, организация рабочих мест.
Оборудование для облицовывания кромок щитов по сложности и степени автоматизации можно разделить: простейшие станки с ручной и механизированной подачей; односторонние механизированные и полуавтоматические станки и автоматические линии.
Автоматическая линия облицовывания кромок состоит из загрузчика, станка для облицовывания продольных кромок, разворотного ус-ва, станка для облицовывания поперечных кромок разгрузчика-накопителя.
Первая операция, которой подвергается обрабатываемый щит, является форматная обрезка. В начале подрезной пилой 6 снизу производится предварительный пропил, после чего пила 7 отрезает кромку щита. Фрезерный агрегат 8 с правым и левым вращением производит окончательную обработку кромки. Клей на кромку щита наносится приводным роликом 10 смонтированном в клеевом бачке.
На станке можно облицовывать кромки натуральным полосовым или рулонным синтетическим шпоном. Магазин 9 крепится на кронштейне. Здесь же смонтированы пневматические ножницы для разрезания рулонного материала (гильотина). Кромка подается из магазина и прижимается к щиту роликом 11. Недостатком таких механизмов является то, что на кромке щита остаются так наз. свесы.
Щит передней и задней кромки взаимодействует с упорами, и пилы производят поперечный рез, отпиливая свисающую облицовочную кромку. Свесы по толщине щита снимаются фрезерными головками 14, которые могут наклоняться под углом до 45°. На последующих агрегатах производится окончательная обработка облицовочных кромок щита. Две наклонные фрезерные головки 17 образуют фаску на кромках щита. Шлифовальная осциллирующая головка 15 работает по схеме ленточного станка с контактным прижимом. Ус-во 16 для шлифования фасок на кромках состоит из двух щеток из полосок шлиф.шкурки или др. материала. Возможны и др. операции, например скругление кромок 18, прорезание пазов и четверти 19, обработка циклями 20.
В отличие от рассмотренных выше станки для облицовывания щитов овальной формы, с закругленными углами и т.п. выполнены не по протяжной схеме, а по круговой. Все агрегаты располагаются вокруг одной стойки. Деталь крепится на поворотном ус-ве с вакуумными присосками. За время поворота детали она последовательно проходит все операции облицовывания. Обычно эти станки устанавливаются как дополнение к обычным кромкооблицовочным станкам.
Для облицовывания криволинейных поверхностей кромок щитов используют: для нанесения клея – клее намазывающие диски и кисти – щетки.; для склеивания - обогреваемые ваймы, и агрегатные станки. Последние могут облицовывать криволинейные кромки щитовых деталей, на которых на пласти уже напрессован слой пластика. Облицоваывание на проходном и ручном оборудовании. Проходное Sk-774/, МОК-3,. МФК-2 , При исп.клея расплава нагрев до нач. за 30 – 40минут,плавят гранулы протемпр 190-195 град.
Дата добавления: 2018-02-28; просмотров: 5296; Мы поможем в написании вашей работы! |
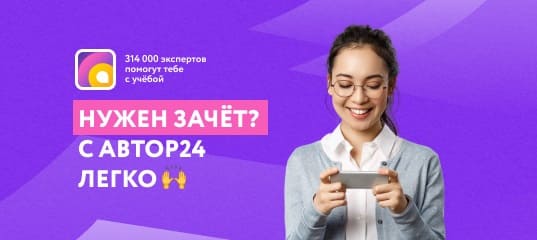
Мы поможем в написании ваших работ!