Методы обеспечения точности, понятие о базировании и размерных цепях
Необходимая точность обработки может быть достигнута следующими основными методами.
а) Метод пробных рабочих ходов- заключается в индивидуальной выверке устанавливаемой на станок заготовки, последовательного снятия стружки с короткого участка путём пробных рабочих ходов, сопровождаемых пробными замерами. Окончательная обработка производится по всей длине заготовки после корректировки положения режущего инструмента по данным пробных замеров.
Достоинства метода:
1. На неточном оборудовании можно получить высокую точность.
2. Исключается влияние износа режущего инструмента на точность, так как при проведении пробных ходов и замеров корректируется положение инструмента.
3. Исключает необходимость пользоваться сложными и дорогостоящими приспособлениями (кондукторами, поворотными и делительными головками и т.д.).
Недостатки:
1. Зависимость достигаемой точности от толщины снимаемой стружки, т.е. нет возможности внести поправку в размер меньше толщины стружки.
2. Высокая квалификация исполнителя.
3. Низкая производительность, высокая себестоимость.
Используется в единичном, мелкосерийном производстве. В серийном - "спасение брака".
б) Метод автоматического получения заданного размера- заключается в том, что партию заготовок обрабатывают на предварительно настроенном станке с установкой заготовок в приспособление без выверки их положения, а режущий инструмент при наладке станка устанавливают на определённый размер, называемый настроечным. Метод более производителен, так как обработка ведётся за один проход, а затраты времени на предварительную наладку раскладываются на всю партию деталей. Применяется в серийном и массовом производстве.
|
|
Преимущества:
1. Повышение точности и снижение брака.
2. Рост производительности.
3. Низкая квалификация рабочих.
Применяются также такие методы как:
1) за один проход с установкой размера по лимбу (нужное деление - пробной обработкой одной детали, или по эталону), - мелко-среднесерийное производство;
2) с использованием подналадчика,с использованием устройств, производящих измерение на ходу - автоматизированное производство.
Понятие о базировани, размерных цепях, размерный анализ технологии изготовления
Базированиемназывают придание заготовке или изделию требуемого положения относительно выбранной системы координат.
База это поверхность или сочетание поверхностей, ось, точка, принадлежащие заготовке или изделию, используемые для базирования. Основные понятия и определения баз.
В зависимости от служебного назначения все поверхности детали подразделяются на основные, вспомогательные, исполнительные и свободные.
|
|
1) Вспомогательными называют поверхности детали определяющие положение всех присоединяемых деталей относительно данных.
2) Исполнительные поверхности – поверхности выполняющие служебное предназначение.
3) Свободной поверхностью называют поверхность не соприкасающуюся с поверхностью других деталей и предназначенную для соединения основных, вспомогательных и исполнительных поверхностей между собой с образованием совместно необходимой для конструкции формы деталей.
4) Базой называют поверхность заменяющую совокупность поверхностей, ось, точку детали или сборочной единицы по отношению к которой ориентируются другие детали изделия или поверхности детали, обрабатываемые или собираемые на данной операции. По характеру своего назначения базы подразделяются на конструкторские, технологические и измерительные.
Группу конструкторских баз составляют основные и вспомогательные базы, учет которых при конструировании (выборе форм поверхностей, их относительного положения, простановки размеров, разработке норм точности и т. п.) имеет существенное значение. Основная база определяет положение самой детали или сборочной единицы в изделии, а вспомогательная база— положение присоединяемой детали или сборочной единицы относительно данной детали.
|
|
Как правило положение детали относительно других деталей определяют комплектом из двух или трех баз.
1) Технологической базой называют поверхность, определяющую положение детали или сборочной единицы в процессе их изготовления.
2) Измерительной базой называют поверхность, определяющую относительное положение детали или сборочной единицы и средств измерения. Базы могут различаться по числу отнимаемых от базируемой детали или сборочной единицы степеней свободы на установочные, направляющие, опорные, двойные направляющие и двойные опорные.
3) Установочной называется база, лишающая деталь или сборочную единицу трех степеней свободы — перемещения вдоль одной координатной оси и поворотов вокруг двух других осей.
4) Направляющей называется база, лишающая деталь или сборочную единицу двух степеней свободы — перемещения вдоль одной координатной оси и поворота вокруг другой оси.
5) Опорнойназывается база, лишающая деталь или сборочную единицу одной степени свободы — перемещения вдоль одной координатной оси или поворота вокруг оси.
|
|
6) Двойной направляющей базой называется база, лишающая деталь или сборочную единицу четырех степеней свободы двух перемещений вдоль двух координатных осей и поворотов вокруг этих же осей.
7) Двойной опорной называется база, лишающая деталь или сборочную единицу двух степеней свободы — перемещения вдоль двух координатных осей.
8) По конструктивному оформлению базы подразделяются на скрытые и конструктивно оформленные.
1) К скрытым базам относятся мысленно проводимая плоскость, ось или точка, используемые в качестве одной из баз.
2) К конструктивно оформленным — реальная поверхность детали или заменяющее ее сочетание поверхностей, используемое в качестве одной из баз.
Размерной цепью называется последовательность всех независимых размеров, расположенных по замкнутому контуру и оказывающих непосредственное влияние на точность замыкающего звена.
Наименьшее число звеньев размерной цепи равно трем.
Все звенья размерной цепи подразделяют на две группы: составляющие звенья и замыкающее звено.
Замыкающим является звено, связывающее поверхности и оси, расстояние между которыми нужно обеспечить или замерить, т. е. звено, для которого ведется расчет размерной цепи.
Замыкающим звено – звено получаемое в процессе изготовления и измерения последним.
Получение того или иного звена в качестве замыкающего зависит от порядка обработки заготовок или сборки деталей.
Звено размерной цепи, изменение которого вызывает изменение исходного звена (для его решения и используется размерная цепь) или замыкающего звена, называется составляющим.
Увеличивающим называют такое звено, которое при своем увеличении увеличивает размер исходного или замыкающего звена.
Уменьшающее звено при своем увеличении уменьшает размер исходного или замыкающего звена.
Общее правило для нахождения увеличивающих и уменьшающих звеньев заключается в составлении уравнения номинальных размеров, связывающего все члены размерной цепи, и решения его относительно номинального размера замыкающего звена. Тогда все члены правой части уравнения со знаком плюс будут увеличивающими звеньями, а со знаком минус — уменьшающими.
При решении размерных цепей возникают две задачи: прямая и обратная.
При прямой задаче по допускам составляющих звеньев находят допуск замыкающего звена.
При обратной задаче по допуску замыкающего звена определяют допуск составляющих звеньев.
Размерные цепи подразделяются на плоские, в которых все звенья лежат в одной плоскости (или в нескольких параллельных плоскостях) и пространственные. Плоские размерные цепи с параллельными звеньями иногда называют линейными.
Дата добавления: 2018-02-28; просмотров: 314; Мы поможем в написании вашей работы! |
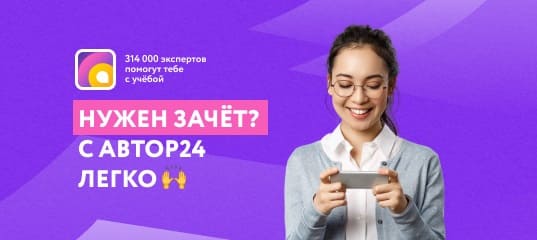
Мы поможем в написании ваших работ!