Основы проектирования технологических проектов
Технологический процесс изготовления машин и механизмов - это часть производственного процесса, связанного с изменением физико-механических свойств, формы и размеров заготовок, а также со сборкой изделий (т.е. с созданием определенной взаимосвязи между деталями и сборочными единицами в изделии).
В современных условиях, при значительном повышении сложности технологических процессов, предприятия не могут качественно выполнять работы, руководствуясь только чертежами . Поэтомунеобходимо создавать специальные документы, отражающие содержание технологического процесса в которых по всем операциям должны быть указаны:
способы и последовательность выполнения работ;
применяемые приспособления и инструмент;
специальность исполнителей;
трудоемкость, время и место выполнения работ;
Основные требования по приемке.
Задачи проектирования технологических процессов
Проектирование технологических процессов предусматривает:
· определение способов и порядка изготовления, учитывающих тип производства и соответствующие ему организационно-технические условия;
· выбор оборудования, приспособлений, режущего, измерительного и др. инструмента, необходимых для выполнения установленного объема работы;
· определение режима работы оборудования, учитывающего
наиболее полное его использование;
· расчет норм времени на каждую операцию;
|
|
· установление разряда работы по каждой операции.
Виды технологических процессов
· По степени унификации различают следующие виды технологических процессов: единичный; типовой; групповой.
· Вид технологического процесса определяется количеством изделий, охватываемых процессом (одно изделие, группы однотипных изделий).
Единичный технологический процесс — технологический процесс, относящийся к изделиям одного наименования, типоразмера и исполнения, независимо от типа производства (применяется для изготовления изделий одного наименования, типоразмера и исполнения независимо от типа производства).
Типовой технологический процесс — технологический процесс, характеризуемый единством содержания и последовательности большинства технологических операций и переходов для группы изделий с общими конструктивными признаками.
Исходную информацию для разработки техпроцессов подразделяют на базовую, руководящую и справочную.
Базовая информация включает данные, содержащиеся в чертежах и технических условиях на изготовление и приёмку изделия, размер и срок выполнения программного задания (по этапам).
Руководящая информация содержит требования отраслевых стандартов к технологическим процессам и методам управления ими, а также стандартов на оборудование и оснастку, документацию на действующие единичные, типовые и групповые технологические процессы, производственные инструкции, документацию по технике безопасности и промышленной санитарии, материалы по выбору технологических нормативов (режимов обработки, припусков, норм расхода материалов) и др.
|
|
Справочная информация состоит из описаний прогрессивных методов изготовления, каталогов, паспортов, справочников, альбомов компоновок прогрессивных средств технологического оснащения, планировок производственных участков и пр.
К исходным данным относятся также следующие виды технико-экономической информации: технологический классификатор объектов производства, классификатор технологических операций, система обозначения технологических документов, стандарты ЕСТД и типовые технологические процессы и операции (см. гл. I).
Проектирование
Прежде чем приступить к составлению технологического процесса, необходимо тщательно ознакомиться с системой простановки на чертеже размеров, определяющих взаимное расположение обрабатываемых поверхностей. Она в значительной степени предопределяет выбор установочных баз и последовательность обработки, так как в первую очередь обрабатывают те поверхности, от которых определяется большое число других поверхностей.
|
|
После выбора установочных баз и технологического маршрута производят расчет припусков, в результате которого с учетом заданной точности и шероховатости поверхности определяют необходимые переходы, находят промежуточные размеры заготовки по всем переходам от готовой детали до черновой заготовки, устанавливают допуски на межоперационные размеры в пределах заданного квалитета точности. При этих расчетах выявляют целесообразность раздельного выполнения черновой и чистовой, а в ряде случаев получистовой обработки.
При разделении процесса на черновые и чистовые операции поверхности детали получают окончательную форму и размер не сразу: их обрабатывают несколько раз на разных операциях; каждая предшествующая операция подготавливает поверхность к обработке на последующей операции. При переходе от одной операции к другой точность поверхности постепенно повышается; возрастает и точность ее расположения относительно других поверхностей детали.
Выбор технологической схемы обработки
|
|
В общем виде выбор последовательности операций производится cледующим образом. Обработка должна начинаться с поверхности, которая будет технологической базой для установки детали в процессе ее изготовления, причем обработку поверхности нужно выполнять с такой точностью (по линейным размерам и геометрической форме), которая обеспечила бы необходимую точность установки детали при дальнейших операциях.
Выбор режимов резания
При выборе режимов резания следует придерживаться определенного порядка. Сначала устанавливают глубину резания t, мм. Если припуск может быть снят в один рабочий ход, глубина резания равна припуску на обработку. Глубину резания могут ограничивать недостаточная мощность привода станка, нежесткость обрабатываемой заготовки, ненадежное закрепление ее на станке и другие факторы. При этих условиях приходится снимать припуск за несколько рабочих ходов с малой глубиной резания. Глубина резания связана и с видом обработки. Например, при шлифовании припуск всегда снимают за несколько рабочих ходов.
Дата добавления: 2018-02-28; просмотров: 296; Мы поможем в написании вашей работы! |
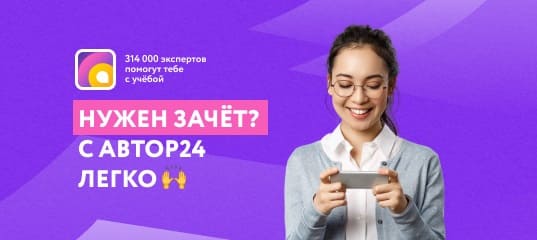
Мы поможем в написании ваших работ!