Мелющие тела, их форма и процесс изнашивания
При эксплуатации барабанных мельниц расходы на покрытие износа шаров, стержней и футеровки составляют одну из главных статей затрат на измельчение. Например, при обогащении весьма абразивных магнетитовых кварцитов стоимость стержней шаров составляет 30–35 % общей стоимости измельчения. Расход стали при измельчении оказывается в некоторых случаях решающим фактором выбора способа измельчения.
Проведено много исследований по выбору оптимальной формы мелющих тел. Испытывали шары, шары со сферическими вогнутостями, кубы, тетраэдры, сдвоенные призмы, сдвоенные усеченные конусы, цилиндры, стержни, эллипсоиды и цильпебсы. Целью этих исследований был переход от точечного контакта (например, между шарами) к более эффективным линейному (например, между стержнями) и контакту между плоскостями (например, между призмами). Однако, всесторонний и значительный износ показал, что лучшими по эффективности являются шары, которые в процессе измельчения уменьшаются в размерах, но не теряют свою сферическую форму. Для тонкого измельчения в последнее время находят применение цильпебсы – стальные цилиндрики, имеющие длину 24–40 мм и диаметр 16–25 мм. Истирающая площадь цильпебса в несколько раз больше, чем шаров того же диаметра, так как шары соприкасаются в одной точке, а цилиндры – по образующей линии. В практике измельчения наибольшее применение нашли шары и стержни.
|
|
Шары изготовляют прокаткой, ковкой или штамповкой из различных износостойких марок стали диаметрами от 15 до 150 мм (в диапазоне 30–110 мм через 10 мм). Шары подвергаются закалке и должны иметь высокую твердость. На поверхности шаров не допускаются трещины, пузыри, закаты, шлаковые включения.
Стержни изготовляют прокаткой из углеродистой стали. Они должны разламываться на короткие куски (а не скручиваться) после изнашивания до некоторого диаметра.
Изнашивание шаров, а также стержней и футеровки происходит в результате трения при скольжении тел в среде абразивного материала, при соударении измельчающих тел между собой и футеровкой при наличии прослоек абразивного измельчаемого материала. При этом происходит абразивное изнашивание, т.е. микрорезание и микроцарапание металла частицами материала и отрыв частиц металла в виде стружки или выколов.
При сухом измельчении изнашивание шаров происходит в основном за счет абразивного действия. При мокром измельчении в агрессивных (химически активных) водных средах абразивное изнашивание сопровождается коррозионным («коррозия» – разъедание) разрушением металла, которое происходит вследствие химического или электрохимического взаимодействия со средой. В различных условиях коррозионный износ составляет от 10 до 60 % от абразивного.
|
|
Изнашивание измельчающих тел – чрезвычайно сложный процесс, зависящий от многих факторов: свойств металла (сплава), из которого изготовлены шары; их размеров; абразивных свойств измельчаемого материала; его крупности и крупности продукта; способа измельчения (сухое или с водой); агрессивности среды (кислая, щелочная); ее температуры; присутствия в ней поверхностно-активных веществ; скоростного режима мельницы; схемы измельчения (открытый или замкнутый цикл) и др.
На практике износ шаров, как видно из вышесказанного, колеблется в широких пределах и может доходить до 1,5–2 кг при расходе футеровок 0,15–0,2 кг на тонну измельченного продукта.
Чтобы поддерживать массу шаровой нагрузки постоянной, в мельницу, компенсируя износ, периодически добавляют необходимое количество новых шаров.
Износ шара проявляется в уменьшении его диаметра. Так как шары в мельницу поступают разновременно, то в ней будут находиться шары разного размера – от самых крупных, только что загруженных, до самых мелких, поступивших значительно раньше.
Эффективная работа мельницы требует, чтобы шаровая нагрузка содержала в достаточном количестве не только крупные шары для измельчения крупных кусков, но и шары среднего размера и даже мелкие для разрушения мелких зерен. Для поддержания в шаровой нагрузке надлежащего соотношения между крупными, средними и мелкими шарами применяют рационную догрузку, т.е. регулярное добавление в мельницу порций шаров различных размеров.
|
|
Размер шаров, загружаемых в мельницу, принимается в зависимости от прочности и величины кусков измельчаемого материала. Они должны быть таковы, чтобы кинетическая энергия шара была достаточной для разрушения измельчаемых частиц. Величина кинетической энергии пропорциональна диаметру мельницы и кубу диаметра мелющего тела. Приблизительный диаметр максимального шара D max в загрузке для грубого измельчения можно определять по формуле Разумова К.А.
мм, (3.10)
для тонкого
мм, (3.11)
где d max – максимальный размер куска измельчаемого материала, мм.
Дата добавления: 2015-12-19; просмотров: 23; Мы поможем в написании вашей работы! |
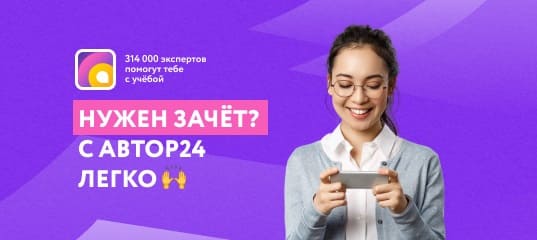
Мы поможем в написании ваших работ!