Области применения ПКМ.
Стеклопластики — самые дешевые из всех ПКМ, поэтому их применение оправдано в серийном и массовом производстве. В судостроении — это корпуса лодок, катеров, речных и морских судов; в строительстве и химической промышленности — строительные панели, воздуховоды, реакционные аппараты, различные емкости, химически стойкие и прочные трубы, корпуса насосов, вентиляторов и т.д.; на автомобильном и железнодорожном транспорте — кабины грузовиков, баки для горючего, цистерны для перевозки жидких и сыпучих грузов, приборные панели и многое другое.
Органопластики имеют низкую плотность, высокую прочность, жесткость, влагостойкость, химическую стойкость. Диэлектрические и тепло-физические свойства определили их применение в качестве материалов электро- и коррозийностойкого, фрикционного назначения, а также в производстве спортинвентаря.
Углепластики применяют в автомобильной промышленности, авиационной технике, химической промышленности, производстве спортинвентаря. Биологическая совместимость углеродного волокна с тканями позволяет использовать углепластики для протезирования, в медицинских приборах.
Боропластики применяют из-за их высокой стойкости, прочности и жесткости в основном в авиационной и ракетно-космической технике.
МКМ используют в таких областях, где они должны находиться в агрессивных средах, при статических, циклических, ударных, вибрационных нагрузках. Наиболее эффективно применение МКМ в таких конструкциях, особые условия эксплуатации которых не допускают применения традиционных материалов.
|
|
Следует отметить, что области применения композитов практически неограниченны, и в ближайшие годы надо ждать их широчайшего внедрения.
13.3. Место порошковой металлургии в современном производстве. Технология порошковой металлургии.
Одним из основных направлений технологии машиностроения в настоящее время является разработка таких прогрессивных технологических процессов производства конструкционных материалов которые обеспечивают получение заготовок с минимальными припусками на последующую механическую обработку либо вообще без нее при постоянном снижении расхода дефицитных материалов В решении этой проблемы определенная роль принадлежит порошковой металлургии.
Порошковая металлургия — это отрасль техники, включающая изготовление порошков из металлов и их сплавов и получение из них заготовок изделий без расплавления основного компонента. Методами порошковой металлургии можно создавать материал из различных компонентов с резко отличающимися свойствами комплексом физико-механических свойств. Порошковая металлургия используется как для создания принципиально новых материалов, так и для производства номенклатуры конструкционных деталей общего назначения.
|
|
В настоящее время расширяется сфера применения порошковой металлургии в различных областях промышленности, совершенствуется ее технология. Относительно небольшие производственные расходы на получение изделий из порошковых материалов сочетании с возможностью придания им заданных свойств, окончательной формы и размеров практически без проведения мехам ческой обработки выдвинули порошковую металлургию в ряд более эффективных и перспективных технологий. Эта технологи успешно конкурирует с литьем, обработкой давлением, резанием и другими методами обработки металлов, дополняя или замени их. Ежегодные темпы роста производства порошковых изделий в США, ФРГ, Японии и других странах составляют 15…20 %. Это соответствует тому, что через каждые 5...6 лет объем производств изделий из порошковых материалов удваивается.
Порошковая металлургия, относящаяся к одной из наиболее молодых отраслей современной техники, является в то же время древнейшим способом производства металлов и изделий из них Известно, что уже в глубокой древности (до нашей эры) порошки золота, меди и бронзы использовались для декоративных целей. Способы получения температур, достаточных для расплавление чистого железа отсутствовали, и изготовление заготовок осуществляли методом порошковой металлургии, так называемым кричным методом. С появлением доменного производства изготовление изделий методами порошковой металлургии временно прекратилось.
|
|
В 1826 г. русские ученые П. Г. Соболевский и В. В. Любарский изготовили первые промышленные изделия, применив прессование и спекание платинового порошка. Ими было организовано также производство монет из платины, тиглей и других изделий. Аналогичный способ получения компактной платины англичанин У. X. Волластон предложил только спустя три года. Именно русским ученым принадлежит заслуга возрождения порошковой металлургии и превращения ее в особый технологический метод обработки металлов. Однако развитие печной техники в начале XIX в. привело к освоению производства изделий из платины литьем, и порошковая металлургия вновь незаслуженно была забыта.
Лишь в начале XX в., когда бурное развитие электротехники вызвало необходимость в новых материалах, получить которые известными способами было невозможно, опять обратились к технологии изготовления изделий методами порошковой металлургии. Это привело к ее новому возрождению, дальнейшему развитию и активному внедрению в производство. В 30-х годах было начато производство магнитных и контактных материалов, самосмазывающихся подшипников, твердых сплавов и т. д.
|
|
Освоение технологии производства различных порошков позволило вести исследования в области порошковых конструкционных материалов. Наряду с проведением технологических разработок создавались теоретические основы порошковой металлургии.
В СНГ работает множество научно-исследовательских организаций и специализированных промышленных производств, занимающихся проблемами порошковой металлургии. Среди них ведущими являются Центральный научно-исследовательский институт черной металлургии (ЦНИИчермет), Белорусский Республиканский научно-производственный концерн порошковой металлургии и другие организации.
Технологический процесс производства порошковых изделий и области их применения заключается в получении порошка исходных материалов, состоящих из шихты, прессования порошков и спекания изделий. Каждая из указанных операций вносит свой существенный вклад в формирование исконных свойств порошковых изделий. На практике возможны отклонения от приведенной типовой технологической схемы получения порошковых материалов, которые могут выражаться в совмещении операций прессования и спекания (горячее прессование), спекания свободно насыпанного порошка (отсутствует операция уплотнения), проведении дополнительной обработки (калибрование, механическая и химико-термическая обработка) и др. Методами порошковой металлургии получают: твердые сплавы для изготовления режущего, бурового инструмента, а также деталей, подвергающихся интенсивному изнашиванию; высокопористые материалы для изготовления фильтров, используемых для очистки жидкостей от твердых включений, воздуха и газа, от пыли и т. д.; антифрикционные материалы для производства подшипников скольжения, втулок, вкладышей и других деталей, работающие в тяжелых условиях эксплуатации; фрикционные материалы для получения деталей узлов трен сцепления и тормозных систем машин; жаропрочные и жаростойкие материалы для производства изделий, работающих в условиях высоких температур и в сил агрессивных газовых средах; материалы сложных составов (псевдосплавы) для изготовления электрических контактов, которые получить другими способами не возможно; магнитные материалы для изготовлении постоянных магнитов, магнитоэлектриков, ферритов и т. д.
Получение металлических порошков является важнейшей задачей технологического процесса изготовления деталей из порошковых материалов, от которой зависят их основные свойства.
В настоящее время существуют различные методы изготовления порошков, каждый из которых обеспечивает определенные характеристики. Металлические порошки различаются как по размерам (от долей микрометра до долей миллиметра), так и по форме и состоянию поверхности частиц.
Все известные способы производства порошков условно разделяют на механические и физико-химические.
Механические методы получения порошков — дробление и размол, распыление, грануляция — характеризуются переработкой материалов в порошок практически без изменения их химического состава.
Физико-химические методы - восстановление, термическая диссоциация карбонильных соединений - отличаются тем, что получаемый порошок по химическому составу существенно отличается от исходного материала.
Иногда с целью повышения экономичности процесса или улучшения характеристик материала применяют комбинированные методы получения порошков. Так, при распылении расплавленный металл сначала гранулируют, а затем отжигают в защитной среде водорода. При электролизе получают плотные, но хрупкие продукты, которые затем размалывают.
Наибольшее промышленное распространение получили методы изготовления порошков путем восстановления оксидов и других соединений металлов, распыления и др.
В США, Японии, Англии и Италии, являющихся крупными производителями и потребителями металлических порошков, около 55 % их производят методом восстановления, а остальную часть методом распыления.
Механические методы получения порошков основаны на измельчении частиц материала путем разрушения их под действием внешних нагрузок, преодолевающих внутренние силы сцепления в материале.
Механическое измельчение дроблением, размолом или истиранием целесообразно применять при производстве порошков хрупких металлов и сплавов: бериллия, сурьмы, хрома, марганца, ферросплавов и др. Размол пластичных металлов затруднен, так как под действием внешних нагрузок они в основном деформируются, а не размельчаются.
Дробление металлов производят в щековых, валковых, конусных дробилках и бегунах. Продукты дробления — частицы размером 1...10 мм. Они являются исходным материалом для последующего измельчения в шаровых вращающихся, вибрационных или планетарных центробежных, вихревых и молотковых мельницах.
Недостатками механических методов получения порошков является загрязнение последних продуктами истирания шаров и барабана, их высокая стоимость и относительно низкая производительность процессов.
Получение порошка методом распыления связано с распылением расплавленной струи металла в среде воздуха, инертных газов или при ударах лопаток вращающегося диска. Распылением получают порошки алюминия, свинца, цинка, олова, никеля, латуни, чугуна, железа и др.
Метод грануляций состоит в том, что расплавленный металл льют в жидкость. Частицы порошка, полученного этим способом, имеют размер 0,05...0,35 мм и форму, близкую к сферической.
Одним из физико-химических методов получения порошков является восстановление оксидов и других соединений металлов.
Под восстановлением в порошковой металлургии понимают процесс получения металлов из их химических соединений путем отнятия неметаллической составляющей (кислорода и других элементов) при помощи восстановителя.
Методом восстановления получают порошки кобальта, вольфрама, молибдена, титана, меди, железа и других металлов. В качестве восстановителей применяют газы (водород, конвертерный, доменный, коксовый и др.) или твердые вещества (углерод, магний). Получение металлических порошков восстановлением является наиболее распространенным, высокопроизводительным и экономичным из рассматриваемых методов. В нашей стране разработан метод совместного восстановления смесей оксидов с металлическими порошками гидридом кальция. Этим способом получают порошки высоколегированных сталей и сплавов, обладающие рядом уникальных и ценных для промышленности свойств.
Электролиз водных растворов и расплавленных сред заключается в разложении водных растворов соединений выделяемого металла или расплавленных солей ори пропускании через них постоянного электрического тока. Этим способом получают порошки олова, серебра, меди, железа, а также порошки редких металлов (тантала, тория, ниобия, циркония и др.) с дендритной формой частиц. Порошки отличаются высокой чистотой и хорошей прессуемостью вне зависимости от степени чистоты исходного сырья. Стоимость порошков высока из-за больших затрат электроэнергии и низкой производительности процесса.
Методом диссоциации карбонильных соединений получают высококачественные дисперсные порошки железа, никеля, кобальта и других металлов со сферической формой частиц. Способ основан на способности металла при определенных условиях (высокое давление, повышенная температура) образовывать с оксидом углерода специфические химические соединения, называемые карбонитами. Карбониты неустойчивы при обычных условиях и легко разлагаются при нагревании до 200,..300 ˚С с образованием тонкого порошка металла и оксида углерода.
Метод гидрогенизации основан на свойстве металлов резко повышать свою абсорбционную активность при нагреве до высоких температур. Измельчаемый губчатый металл загружают в реактор, через который пропускают водород. При нагреве до определенной температуры (300...800 °С) происходит активное поглощение металлом водорода, в результате чего он становится хрупким и растрескивается. Порошок получают путем размола губки одним из механических способов и подвергают дегидрогенизации в вакууме при температуре около 800 ˚С. Данным методом получают порошки редких металлов: титана, урана, циркония и др. Недостаток способа - высокая хрупкость и низкая пластичность частиц порошков.
Металлические порошки характеризуются технологическими, физическими и химическими свойствами, основные из которых регламентируются ГОСТами и техническими условиями.
Под формованием заготовок из порошковых материалов следует понимать процесс получения заготовок требуемых форм и размеров, а также достаточной прочности для последующего изготовления из них изделий. Формование предполагает уплотнение порошка. Процесс уплотнения порошкового материала в отличие от деформирования компактного металла сопровождается значительным изменением объема прессуемого тела.
На начальной стадии уплотнение происходит за счет относительного перемещения частиц порошка и их более плотной упаковки, на последующих этапах - в результате упругой и пластической деформации частиц или их хрупкого разрушения (в зависимости от свойств деформируемых порошков). Прочность заготовки с повышением давления прессования увеличивается и обеспечивается за счет механического сцепления частиц и сил межатомных и межмолекулярных связей.
Обычно перед формованием производят подготовку порошков, заключающуюся в их отжиге, классификации и приготовлении.
Отжиг применяют с целью повышения пластичности и прессуемости порошков за счет восстановления остаточных оксидов и снятия остаточных напряжений.
Классификация — разделение порошков на фракции по размерам частиц. Разделение осуществляют с помощью сит либо воздушных сепараторов.
Приготовление шихты производят в мельницах, смесителях и др. Для этого дозированные порции компонентов определенного гранулометрического и химического состава смешивают в указанных устройствах, добавляя в случае необходимости различные технологические присадки: пластификаторы, облегчающие процесс прессования; легкоплавкие присадки, улучшающие спекание; летучие вещества для получения изделий с заданной пористостью. При смешивании порошков материалов, резко различающихся по своим свойствам (например, железа и графита), в целях получения наиболее однородной смеси применяют добавки спирта, бензина, глицерина и др.
Прессование в стальной пресс-форме (рисунок 13.1) является наиболее распространенным способом получения заготовок. Пуансон 1 передает давление на порошок 2, помещенный в пресс-форму 3, и порошок уплотняется.
Рис. 13.1. Схема прессование в стальной пресс-форме:
а - одностороннее, б - двустороннее
Одним из основных недостатков формования в пресс-формах является возникновение сил трения порошка о стенку матрицы (пресс-формы). Это вызывает неравномерное распределение плотности (прочности) по высоте заготовки, особенно если высота значительно превышает ее диаметр.
На практике снижение трения порошка о стенку матрицы, а следовательно, улучшение условий процесса прессования достигается одним из них, например, является замена одностороннего приложения давления (рисунок 13.1, а) на двустороннее (рисунок 13.1, б). В последнем случае два пуансона движутся навстречу друг Другу. Это приводит к более равномерному распределению плотности по высоте заготовки и снижению давления прессования на 30...40 %. Поэтому изделие с более сложной конфигурацией изготавливают двусторонним прессованием. Уплотнение производят на гидравлических или механических прессах, давление прессования составляет 200...1000 МПа в зависимости от свойств порошка и назначения изделия. Детали пресс-форм выполняют из высокоуглеродистых легированных сталей (инструментальных сталей), твердых сплавов. Стойкость стальных пресс-форм составляет 1...50 прессовок, пресс-форм из твердых сплавов - до 500 тыс. прессовок.
Динамическое прессование - это формование заготовок с использованием импульсных нагрузок, отличающееся высокой скоростью их приложения. В качестве источника энергии используют: взрыв заряда взрывчатых веществ, импульсное магнитное поле, сжатый газ и т. д. Высокоскоростное прессование в настоящее время используется при изготовлении высокоплотных крупногабаритных заготовок из труднодеформируемых металлических порошков и порошков керамических материалов.
Только прессованием порошка получить изделие достаточной прочности невозможно. На поверхности частиц порошка образуются оксиды и всегда есть загрязнения, препятствующие возникновению металлических контактов. В силу упругих свойств частиц порошка велико их сопротивление деформированию. Поэтому для повышения прочности и твердости изделий заготовки подвергают спеканию.
Операция спекания состоит в нагреве и выдержке заготовок при температуре, составляющей 0,7...0,8 от абсолютной температуры плавления основного компонента спекаемой композиции. Средняя продолжительность выдержки составляет 1...2 ч.
При спекании заготовок протекают такие сложные физико-химические процессы, как диффузия, восстановление поверхностных оксидов, рекристаллизация. Между частицами порошка возникают металлические контакты, а прочность их сцепления иногда достигает прочности сцепления кристаллов компактных металлов. Спекание сопровождается обычно некоторым уплотнением заготовок - усадкой, которая зависит от дисперсности исходного порошка, температуры и продолжительности спекания. При спекании снимаются остаточные напряжения в заготовках, изменяются их физические свойства и улучшаются механические характеристики. Для предотвращения окисления частиц порошка спекание проводят в вакууме или в защитной атмосфере (водорода, оксида азота, генераторного газа и др.).
Различают спекание в твердой и жидкой фазах. Спекание в твердой фазе производится при температуре, меньшей температуры плавления компонентов смеси, при спекании же в жидкой фазе - при температуре, превышающей температуру плавления одного или нескольких компонентов исходного материала. Спекание в жидкой фазе позволяет получать более плотные изделия за счет активизации капиллярных явлений, приводящих к закрытию пор.
Процесс спекания заготовок в зависимости от температурного режима условно делят на три этапа. На первом этапе (до 150 °С) наблюдается некоторое увеличение прочности и незначительная усадка заготовки, что объясняется испарением адсорбированной воды с поверхности частиц. Происходит увеличение электросопротивления и интенсивная релаксация остаточных напряжений в заготовке. Второй этап характеризуется дальнейшей релаксацией упругих напряжений, что вызывает изменение площади контактов и уменьшение плотности заготовок. На третьем этапе (при температурах, несколько больших температур рекристаллизации для данного металла) происходит сглаживание свободных и контактных поверхностей частиц, контакты между сросшимися зернами расширяются и становятся металлическими вследствие высоких скоростей диффузии и окончательного восстановления оксидов.
Нагрев заготовок при спекании осуществляют в печах различного типа, работающих периодически или непрерывно. Печи периодического действия применяют при небольшом выпуске порошков.
При необходимости порошковые изделия подвергают отделочным операциям: калиброванию, обработке резанием, термической и химико-термической обработке, повторному спеканию, повторному прессованию.
Применение методов порошковой металлургии для изготовления изделий позволяет достигать высокой производительности труда и значительной экономии средств в народном хозяйстве страны. Экономия достигается за счет получения изделий высокой прочности, рационального использования металла, снижения его потерь, повышения качества изделий, создания новых прогрессивных деталей и др.
Если обычное изготовление деталей на металлорежущих станках сопровождается потерями до 20...80 % металла, связано с необходимостью выполнения большого числа технологических операций и значительными трудозатратами, то получение изделий методами порошковой металлургии отличается тем, что при числе операций 3...S отходы металла составляют всего 5...10%. Кроме того, производство порошковых изделий сосредоточено в основном на одном предприятии, не требует большого станочного парка и высокой квалификации рабочих. Изготовление деталей обычного состава методами порошковой металлургии дает возможность уменьшить по сравнению с обработкой резанием удельный расход металла в 3...5 раз, трудозатраты - в 2...8 раз, себестоимость изготовления деталей -в 1.5...3 раза и повысить производительность труда в 1.5...2 раза.
Образующиеся на машиностроительных заводах при обработке деталей из различных металлов резанием отходы в виде стружки и шлама представляют собой хорошее сырье для производства различных деталей машин и приборов. В основном около 50 % стружки, спрессованной в брикеты или. пакеты, используется в сталеплавильном производстве. Часть стружки перерабатывается в порошок, В нашей стране разработана технология измельчения стружки путем размола ее в мельницах в среде жидкого азота. Изделия, изготовленные из отходов методами порошковой металлургии, обладают в ряде случаев более высокой стойкостью, чем детали, полученные по обычной технологии.
Шлам, получающийся в результате отделочной обработки заготовок, является также ценным сырьем для порошковой металлургии. Так, отходы шлифования деталей шарикоподшипникового производства после их сушки и просева составляют основу для изготовления фрикционных дисков, работающих в условиях тяжелых нагрузок. Порошок, полученный из отходов после опиловки и обкатки подшипниковых шариков, может быть использован для изготовления конструкционных деталей общего назначения и т. д.
Многие изделия, изготовленные методами порошковой металлургии, обладают более высокими качествами, чем изделия, полученные традиционными методами. Так, стойкость инструмента из порошка быстрорежущей стали в 3...4 раза больше стойкости инструмента из литой стали.
Эффективность порошковой металлургии повышается в условиях массового производства изделий. Так, в массовом производстве при изготовлении 1 тыс. т деталей методами порошковой металлургии экономится около 1,3 млн. рублей, свыше 2000 т стали, высвобождается более 200 рабочих и 50 металлорежущих станков. С увеличением объема выпуска снижается по сравнению с себестоимостью литых заготовок.
Предполагается дальнейшее развитие теории и практическое применение методов порошковой металлургии.
13.4. Новые методы обработки материалов
Постепенно расширяется применение прогрессивных базовых технологий и будет обеспечивается широкое внедрение в промышленность принципиально новых технологий, в том числе электронно-лучевых, лазерных, плазменных, импульсных, мембранных, которые позволяют многократно повысить производительность труда, поднять эффективность использования ресурсов и снизить энерго- и материалоемкость производства. Рассмотрим некоторые из них.
Лазер представляет собой источник мощного светового монохроматического излучения. Слово «лазер» составлено из начальных букв английской фразы «light amplification by stimulated emission of radiation». В переводе на русский язык она означает «усиление света в результате вынужденного излучения». В советской литературе термин «лазер» употребляется в смысле «оптический квантовый генератор». Лазеры делятся на твердотельные (монокристаллы рубина); газовые, работающие на смеси углекислого газа с азотом; полупроводниковые и жидкостные. В промышленном производстве в основном используются твердотельные и газовые лазеры.
В последнее время они нашли применение в технологических процессах резки различных материалов (фанеры, пластиков, бумаги, картона, стекла, керамики, тканей и др.), сварки металлов, их упрочнения и закалки, выполнения отверстии в твердых сплавах, алмазах и т. д. Благодаря направленности и высокой концентрации энергии лазерного луча удается выполнять технологические операции, вообще не выполнимые каким-либо другим методом.
Лазеры имеют мощность непрерывного излучения до нескольких сотен киловатт и энергию отдельного импульса до нескольких сотен джоулей. Однако при этом они:
- имеют сравнительно большие геометрические размеры;
- потребляют значительную мощность;
- сложны в изготовлении и эксплуатации.
В настоящее время хорошо распространены следующие технологические процессы с использованием мощных лазеров:
- лазерная поверхностная термообработка;
- лазерная сварка;
- лазерная размерная обработка;
- измерительная лазерная технология;
- лазерная интенсификация химических реакций.
Основные методы лазерной обработки, различающиеся режимами проведения технологического процесса обработки, приведены на рисунках 13.2 и 13.3.
Рис. 13.2. Основные технологические процессы лазерной обработки
Рис. 13.3. Режимы лазерной обработки при различных видах воздействия лазерного излучения на поверхность:
q — интенсивность излучения, Вт/см2;
ε - уровень удельной энергии, Дж/см2;
τ — время воздействия, с
Широкое применение лазеры получили в медицине и биологии. На их основе созданы различные установки и инструменты.
Использование лазера дает значительный эффект. Так, например, с помощью лазерного луча можно выполнять отверстия диаметром 0,03...3 мм и глубиной в несколько миллиметров. При этом производительность лазерной установки составляет около 60 отверстий в минуту. С помощью лазера сваривают интегральные схемы, детали приборов точной механики, миниатюрные детали различных изделий и др. Лазерная сварка позволяет повысить производительность труда в 3...5 раз по сравнению с обычным способом сварки. По расчетам специалистов, организация и внедрение в нашей стране централизованного раскроя тканей с использованием лазерных установок позволит получать экономию около 300 млн. рублей в год.
Плазма - это частично или полностью ионизированный газ, обладающий практически одинаковой плотностью положительных или отрицательных зарядов. Плазма может быть низкотемпературной (порядка 105 ˚С) и высокотемпературной (106...108 °С). Низкотемпературная плазма получила более широкое применение в технологических процессах промышленных производств. В СССР созданы плазмотроны мощностью от 100 В до 10000 кВ для устройства для напыления порошковых металлов и их соединений. Использование их дает значительный эффект. Известно, что лопасти гребных винтов различных судов изготовляют из дорогостоящей легированной стали. Была разработана технология плазменного напыления износостойкого порошка на поверхности лопастей, изготовленных из недорогой стали. Винты, полученные таким образом, относительно дешевы, а служат в несколько раз дольше, чем выполненные из легированной стали. На промышленных предприятиях нашей страны применяют плазменно-механическую обработку металлов, суть которой состоит в разупрочнении поверхности заготовок перед резанием. Это дает возможность повысить скорость обработки и увеличить толщину снимаемой стружки. Установлено, что внедрение плазменно-механического метода обработки марганцовистых сталей способствует повышению производительности труда в 4..10 раз, а титановых сплавов в 15 раз.
С помощью плазмотронов можно перерабатывать хлорорганические отходы, которые до сих пор выбрасывались. Из них можно получать новые вещества, необходимые для различных отраслей. Плазменная технология связывается с появлением металлобетонов, где в качестве связующего вещества используют сталь, чугун, алюминий, свинец и т. д. Раньше это было сделать невозможно из-за слабого контактного сцепления между металлом и минеральным наполнителем. Плазменная же технология позволяет производить быстрое поверхностное оплавление частиц горной породы, что обеспечивает хорошую совместную работу металла и минерального наполнителя. Полученный металлобетон прочнее обычного бетона при сжатии в 10 раз, при растяжении - в 100 раз.
При обработке плазмой поверхности кирпичных, бетонных стен или стен, поверхность которых облицована керамической плиткой, образуется стекловидный расплав, который надежно защищает здание от влаги и атмосферных воздействий. Если же на стены здания предварительно нанести растворы солей различных металлов, то их поверхности приобретут соответствующую окраску.
13.5. Химические и электрические способы обработки материалов
При обработке металлов резанием получение деталей необходимых размеров достигается снятием стружки с поверхности обрабатываемой заготовки. Стружка, таким образом, является одним из наиболее распространенных отходов в металлообработке, объем которого составляет примерно 8 млн. т в год. При этом, по меньшей мере 2 млн. т - это отходы переработки высоколегированных и других особо ценных сталей. При обработке на современных металлорежущих станках в стружку зачастую идет до 30...40 % металла от общей массы заготовки.
Поэтому все большее внимание уделяется новым способам обработки металлов, основанным на безотходной или малоотходной технологии. Появление новых способов обработки обусловливается также все более широким распространением в машиностроении и других отраслях народного хозяйства высокопрочных, коррозионно-стойких и жаропрочных металлов и сплавов, обработка которых обычными методами затруднена.
К новым методам обработки металлов относятся химические, электрические, плазменные, лазерные, ультразвуковые, а также гидропластическая обработка металлов.
При химической обработке используется химическая энергия. Снятие определенного слой металла осуществляется в химически активной среде (химическое фрезерование). Оно заключается в регулируемом по времени и месту растворении металла в ваннах. Поверхности, не подлежащие обработке, защищают химически стойкими покрытиями (лаки, краски, светочувствительные эмульсии и др.). Постоянство скорости травления поддерживается за счет неизменной концентрации раствора.
Химическими методами обработки получают местные утонения и щели; «вафельные» поверхности; обрабатывают труднодоступные поверхности.
При электрическом методе электрическая энергия преобразуется в тепловую, химическую и другие виды энергии участвующие непосредственно в процессе удаления заданного слоя. В соответствии с этим электрические методы обработки разделяют на электрохимические, электроэрозионные, электротермические и электромеханические.
Электрохимическая обработка основана на законах анодного растворения металла при электролизе. При прохождении постоянного электрического тока через электролит на поверхности заготовки, включенной в электрическую цепь и являющейся анодом, происходят химические реакции и образуются соединения, которые переходят в раствор или легко удаляются механическим способом, Электрохимическую обработку применяют при полировании, размерной обработке, хонинговании, шлифовании, очистке металлов от оксидов, ржавчины и т. д.
Анодно-механическая обработка сочетает электротермические и электромеханические процессы и занимает промежуточное место между электрохимическим и электроэрозионным методами. Обрабатываемую заготовку подключают к аноду, а инструмент - к катоду. В качестве инструмента используют металлические диски, цилиндры, ленты, проволоку, Обработку ведут в среде электролита. Заготовке и инструменту задают такие же движения, как при обычных методах механической обработки. Электролит подают в зону обработки через сопло.
При пропускании через раствор электролита постоянного электрического тока происходит процесс анодного растворения металла, как при электрохимической обработке. При соприкосновении инструмента катода - с микронеровностями обрабатываемой поверхности заготовки - анода - происходит процесс электроэрозии, присущий электроискровой обработке. Продукты электроэрозии и анодного растворения удаляются из зоны обработки при движении инструмента и заготовки.
Электроэрозионная обработка основана на законах эрозии (разрушения) электродов из токопроводящих материалов при пропускании между ними импульсного электрического тока. Она применяется для прошивания полостей и отверстий любой формы, разрезания, шлифования, гравирования, затачивания и упрочнения инструмента. В зависимости от параметров импульсов и вида, применяемых для их получения генераторов электроэрозионная обработка разделяется на электроискровую, электроимпульсную и электроконтактную.
При определенном значении разности потенциалов на электродах, одним из которых является обрабатываемая заготовка (анод), а другим — инструмент (катод), между электродами образуется канал проводимости, по которому проходит импульсный искровой (электроискровая обработка) или дуговой (электроимпульсная обработка) разряд. В результате температура на поверхности обрабатываемой заготовки возрастает. При этой температуре мгновенно оплавляется и испаряется элементарный объем металла и на обрабатываемой поверхности заготовки образуется лунка. Удаленный металл застывает в виде мелких гранул.
Следующий импульс тока пробивает межэлектродный промежуток там, где расстояние между электродами наименьшее. При непрерывном подведении к электродам импульсного тока процесс их эрозии продолжается до тех пор, пока не будет удален весь металл, находящийся между электродами на расстоянии, при котором возможен электрический пробой (0,01...0,05 мм) при заданном напряжении. Для продолжения процесса необходимо сблизить электроды до указанного расстояния. Электроды сближаются автоматически с помощью следящего устройства того или иного тина.
Электроискровую обработку применяют для изготовлении штампов, пресс-форм, фильер, режущего инструмента, деталей двигателей внутреннего сгорания, сеток и для упрочнения поверхностного слоя деталей.
Электроимпульсная обработка используется как предварительная для штампов, турбинных лопаток, поверхностей фасонных отверстий в деталях из жаропрочных сталей. При электроимпульсной обработке скорость съема металла в 8...10 раз больше, чем при электроискровой.
Электроконтактная обработка основана на локальном нагреве заготовки в месте контакта с электродом - инструментом и удалении размягченного или расплавленного металла из зоны обработки механическим способом (при относительном перемещении заготовки и инструмента). Метод не обеспечивает высокой точности и качества поверхности деталей, но дает высокую скорость съема металла, поэтому используется при зачистке отливок, отрезании литниковых систем, зачистке проката из специальных сплавов, черновом шлифовании корпусных деталей машин из труднообрабатываемых сплавов и т. п.
Электромеханическая обработка связана преимущественно с механическим действием электрического тока. На этом основана, например, электрогидравлическая обработка, использующая действие ударных волн, возникающих в результате импульсного пробоя жидкой среды.
Ультразвуковая обработка металлов - разновидность механической обработки — основана на разрушении обрабатываемого материала абразивными зернами под ударами инструмента, колеблющегося с ультразвуковой частотой. Источником энергии служат электрозвуковые генераторы тока с частотой 16...30 кГц. Рабочий инструмент — пуансон — закрепляют на волноводе генератора тока. Под пуансоном устанавливают заготовку, и в зону обработки поступает суспензия, состоящая из воды и абразивного материала. Процесс обработки заключается в том, что инструмент, колеблющийся с ультразвуковой частотой, ударяет по зернам абразива, лежащим на обрабатываемой поверхности, которые скалывают частицы материала заготовки. Скорость обработки зависит от частоты и амплитуды колебаний, твердости и размеров абразивных частиц. Ультразвуковые колебания инструмента создаются с помощью магнитно-стрикционных вибраторов, преобразующих электрическую энергию в механическую. Ультразвуковая обработка используется для получения твердосплавных вкладышей матриц и пуансонов, вырезания фигурных полостей и отверстий в деталях, гравирования, прошивки отверстий с криволинейными осями, нарезания резьбы, разрезания заготовок на части и других работ.
Точность размеров деталей и шероховатость их поверхностей, обработанных ультразвуковыми методами, зависят от зернистости используемых абразивных материалов и соответствуют получаемым при шлифовании.
13.6. Плазменно-лазерная обработка
Лучевые, или лазерные, методы обработки основаны на использовании сфокусированного луча (электронного, когерентного, ионного) с весьма высокой плотностью энергии. Луч лазера используется как в качестве средства нагрева и размягчения металла впереди резца, так и для выполнения непосредственно процесса резания при прошивке отверстий, фрезеровании и резке листового металла, пластмасс и других материалов.
Процесс резания идет без образования стружки, а испаряющийся за счет высоких температур металл уносится сжатым воздухом. Сейчас лазеры применяют для сварки, наплавки и разрезания в тех случаях, когда к качеству этих операций предъявляются повышенные требования. Например, лазерным лучом путем прожигания или испарения режут сверхтвердые сплавы, сотовые титановые панели в ракетостроении, листовой и панельный алюминий, композиционные материалы, изделия из нейлона и твердую древесину. Высокая плотность энергии в зоне нагрева создает дополнительный эффект очистки металла.
Следует отметить, что пока лазеры имеют сравнительно низкий коэффициент полезного действия из-за преобразования электрической энергии в тепловую, а последней в механическую.
Плазменные методы обработки металлов по праву считаются одними из самых прогрессивных. Огромная температура плазмы, значительная кинетическая энергия ее струи гарантируют высокое качество обработки любых металлов и материалов. Мощность современных плазменных установок достигает 6 МВт.
Использование плазменных и лазерных методов обработки особенно эффективно при изготовлении деталей сложных форм.
13.7. Гидропластическая обработка
Изготовление металлических пустотелых деталей с гладкой поверхностью и малыми допусками (гидравлические силовые цилиндры, плунжеры, корпуса для электродвигателей, вагонные оси, некоторые шестерни) все чаще осуществляется в последнее время не путем снятия стружки, а посредством так называемой гидропластической обработки. Пустотелую цилиндрическую заготовку, нагретую до температуры пластической деформации, укладывают в массивную разъемную матрицу, сделанную по форме изготовляемой детали, и закачивают под давлением воду. Заготовка раздается и принимает форму матрицы. Для изготовления, например, вагонной оси требуется давление 150 МПа. Поэтому рассматриваемый метод не позволяет изготовлять детали значительных размеров, например трубы. Но если сделать так, чтобы вода, попав внутрь заготовок и соприкасаясь с горячим металлом, мгновенно превращалась в пар, ее объем многократно увеличится. За счет этого заготовка будет плотно прижиматься к матрице. Потребуется давление пара лишь 10...20 МПа,
Осуществление этой идеи в нашей стране позволило исключить при изготовлении пустотелых деталей сверление и другие виды механической обработки. Достигается и другой эффект - металл детали становится под давлением более плотным и мелкозернистым. Детали, изготовленные таким способом, имеют более высокую долговечность работы. Новым методом можно изготовлять биметаллические трубы, закладывая в матрицу две заготовки - одна в другую. Возможны и такие оригинальные установки, которые выполняют самые разные операции от пробивки отверстий в фольге до изготовления полусфер из листового металла значительной толщины.
13.8. Основы мембранной технологии
Мембранная технология — новый принцип организации и осуществления процесса разделения веществ через полупроницаемую перегородку, отличающийся отсутствием поглощения разделяемых компонентов и низкими энергетическими затратами на процесс разделения.
По сравнению с традиционными процессами разделения неоднородных систем мембранная технология выгодно отличается высокой энерго- и ресурсо-экономичностью, простотой аппаратурного оформления, экологической чистотой.
Слово «мембрана» имеет латинское происхождение (membrana) и означает — кожица, перепонка. В технологии под мембраной мы будем понимать перегородку, обладающую различной проницаемостью по отношению к отдельным компонентам жидких и газовых неоднородных смесей.
При внешнем сходстве процессов фильтрования и мембранного разделения (рисунок 13.4) между указанными процессами есть принципиальное отличие.
а б
Рис. 13.4. Схемы мембранного разделения и фильтрования:
а — мембранное разделение;
б — фильтрование
В ходе фильтрования хотя бы один из компонентов газовой или жидкой смеси задерживается и фиксируется внутри фильтрующей перегородки. Это приводит к тому, что перегородка постепенно забивается и процесс фильтрования на ней без очистки делается практически невозможным. В отличие от фильтра мембрана не фиксирует в себе ни одного из компонентов разделяемой жидкой или газовой смеси, а только делит первоначальный поток на два, один из которых обогащен по сравнению с исходным каким-то компонентом. Подобный принцип действия мембраны делает ее способной к практически неограниченному сроку службы, без заметного изменения в эффективности разделения смесей.
В зависимости от материала, из которого изготавливают мембраны, их делят на полимерные, металлические, стеклянные, керамические или композиционные.
По механизму действия различают диффузионные, адсорбционные и ионообменные мембраны.
В зависимости от агрегатного состояния разделяемой смеси, движущей силы процесса разделения, размеров частиц компонентов и механизма разделения различают следующие разновидности мембранных процессов: диффузионное разделение газов; разделение жидкостей методом испарения через мембрану; баромембранные процессы разделения жидких смесей; электродиализ.
Диффузионное разделение газов основано на различной проницаемости мембран для отдельных компонентов газовых смесей. Для осуществления диффузионного разделения газовых смесей используются как сплошные, так и пористые мембраны с размерами пор меньшими, чем длина свободного пробега молекул газов при заданном давлении. Движущей силой процессов диффузии компонентов является разность их концентраций на противоположных поверхностях мембраны.
Диффузионное разделение газов сегодня является наиболее крупномасштабным и экономичным методом, широко используется для получения урана-235, являющегося ядерным топливом. Данный процесс используется для создания аппаратов «искусственное легкое», при производстве водорода, выделении гелия из состава природных и нефтяных газов, является перспективным для выделения кислорода из воздуха, удаления диоксида углерода, воды и других компонентов из газовоздушных смесей в системах жизнеобеспечения людей в замкнутых пространствах, для создания контролируемой атмосферы, обогащенной диоксидом углерода, при хранении овощей и фруктов. Созданы и используются специальные пленки, которые помогают длительное время сохранять качество завернутых в них овощей, фруктов, цветов. В основе такой технологии лежит свойство полимерных мембран разделять воздух на молекулярном уровне: в нем становится меньше кислорода, что резко замедляет процессы гниения.
Разделение жидкостей методом испарения через мембрану основано на различной диффузионной проницаемости мембран для паров веществ. Движущей силой процесса является разность концентраций или давлений. Смесь жидкостей, находящихся в контакте с мембраной, нагревают, а пары проникающие через мембрану, отводят с помощью вакуумирования или потоком инертного газа. Наиболее широко данный метод применяется при разделении азеотропных смесей, а также смесей веществ, имеющих невысокую термическую стабильность.
Баромембранные процессы разделения жидких смесей на практике осуществляются под избыточным давлением и поэтому объединены в группу баромембранных.
Установки, работающие по принципу баромембранного разделения, уже сегодня широко используются для обессоливания морской и соленой воды, очистки сточных вод, извлечения ценных компонентов из разбавленных растворов, в пищевой промышленности - для концентрирования сахарных сиропов, фруктовых и овощных соков, растворимого кофе, получения ультрачистой воды для электронной промышленности, медицины и фармацевтики.
Если мембранный процесс применяют для отделения от идеального раствора крупных коллоидных или взвешенных микрочастиц размером 0,1—10 мкм, то его называют микрофильтрацией, или мембранной фильтрацией.
Микрофильтрация нашла широкое применение в микробиологической промышленности при концентрации водных растворов ферментов, белков, нуклеиновых кислот, полисахаридов и других веществ в химической, пищевой и целлюлозно-бумажной промышленности для очистки сточных вод.
Микрофильтрация используется для концентрирования тонких суспензий, осветления растворов, очистки сточных и природных вод при проведении обессоливания морской воды. Мембранное концентрирование различных жидких продуктов с успехом может заменить традиционный процесс - вакуум-выпаривание.
Электродиализ можно определить как перенос ионов через мембрану под действием электрического тока. При наличии мембран, избирательно пропускающих одни ионы и задерживающих другие, можно решать многочисленные задачи выделения ценных компонентов из растворов, обессоливания воды, снижения жесткости, регенерации растворов в гальванических производствах, очистки сточных вод.
Перспективность мембранных методов прежде всего - в их универсальности. Скоро нельзя будет представить ни одной технологической линии в пищевой, медицинской, фармацевтической и ряде других отраслей промышленности, в которой не было бы установок для мембранного синтеза, разделения, концентрирования и очистки продуктов.
13.9. Основы радиационно-химической технологии
За последние два десятилетия сформировалась новая область химической технологии - радиационно-химическая технология (РХТ). Ее предшественницей следует считать ядерную технологию, интенсивное развитие которой (с начала 40-х гг. XX в.) стимулировалось необходимостью срочного решения ряда задач, связанных с практическим использованием атомной энергии.
Целью РХТ является разработка методов и устройств для наиболее экономичного осуществления с помощью ионизирующего излучения физических, химических и биологических процессов, позволяющих получать новые материалы или придавать им улучшенные свойства, а также для решения экологических проблем. Выделение этого направления в отдельную область технологии обусловлено прежде всего особенностью действия ионизирующего излучения на вещество.
Радиационно-химические процессы обусловливаются энергией возбужденных атомов, ионов, молекул. Энергия ионизирующего излучения превышает в сотни тысяч раз энергию химических связей. Механизм радиационно-химических процессов объясняется особенностями взаимодействия излучений с реагирующими веществами.
В качестве источников ионизирующего излучения используются потоки заряженных частиц большой энергии (электроны, α -, β - частицы, нейтроны, γ - излучение).
Выделим достоинства ионизирующего излучения:
высокая энергетическая эффективность излучения, приводящая к тому, что по сравнению с традиционными радиационная технология является в целом энергосберегающей;
высокая проникающая способность излучения. Исходя их этого, излучение наиболее эффективно использовать для обработки блочных материалов и изделий, при стерилизации биомедицинских материалов в упаковке;
излучение представляет собой легкодозируемое средство обработки материалов и не загрязняет продукцию.
Первоначально ионизирующее излучение использовали для производства уникальных продуктов, а также продуктов улучшенного качества. Причем это было продиктовано ценами на указанные продукты. Имелись случаи экономии сырья и энергии. Однако они были единичными.
Сегодня наблюдается явное смещение интересов использования ионизирующих излучений: от получения продуктов с уникальными и улучшенными свойствами к экономии сырья и энергии.
Доказано, что стоимость получения сшитой полиэтиленовой изоляции кабеля при радиационной технологии в 2,2 раза ниже, чем при использовании других методов. Радиационная вулканизация резиновой ленты дает продукцию в 8 раз дешевле, чем при традиционной термической вулканизации. Радиационная стерилизация медицинских инструментов и оборудования в 4,5 раза экономичнее других видов стерилизации, а радиационное консервирование продуктов питания экономичнее других способов почти в 100 раз.
В настоящее время разработаны и находятся в различных стадиях опытно-промышленной реализации более пятидесяти РТП, например:
радиационная полимеризация и сополимеризация, включающая получение древесно-полимерных и бетонно-полимерных материалов, радиационное отверждение покрытий;
радиационное сшивание полимеров и радиационная вулканизация эластомеров;
радиационно-химический синтез (радиационное хлорирование, сульфохлорирование углеводородов);
радиационное модифицирование неорганических материалов (улучшение адсорбционных и каталитических характеристик, радиационное легирование);
радиационная очистка сточных вод.
Основные преимущества РХТ можно сформулировать следующим образом:
1) возможность получения уникальных материалов, производство которых другими способами невозможно;
2) высокая чистота получаемых продуктов;
3) смягчение условий проведения процесса (температуры, давления);
4) возможность регулирования скорости процесса за счет изменения интенсивности излучения, а следовательно, - легкость автоматизации процесса;
5) возможность замены в некоторых случаях многостадийных процессов синтеза одностадийными.
13.10. Эффективность новых способов обработки материалов
Новые способы обработки материалов выводят технологию изготовления деталей на новую, более высокую ступень по сравнению с традиционной технологией. Это наиболее эффективная технология, чаще всего безотходная. Общими преимуществами новых способов обработки являются: отсутствие потребности в специальных инструментальных материалах высокой твердости; практическая независимость производительности от твердости и других свойств обрабатываемого материала; снижение необходимого силового воздействия на заготовку в процессе обработки (за исключением гидропластической обработки); простота устройства станков; легкость автоматизации процесса обработки и др.
Так, производительность труда при ультразвуковой обработке по сравнению, с традиционными способами обработки резанием возрастает в 10...20 раз при выполнении отверстий некруглой формы и в 2...3 раза круглых. При этом экономия материала составляет 20...50 %.
С помощью гидропластической обработки можно пробить любое отверстие в фольге толщиной всего в несколько десятков микрометров, делать в стенке трубы изнутри углубления и отверстия, готовить трехслойные трубы из разных материалов. Оснастка при этом в 10 раз дешевле, чем при механических способах обработки, и обеспечивается полная безопасность труда. При производстве этим способом труб диаметром более 1 м и длиной в несколько метров при годовой программе 20 тыс. т может быть получена экономия в 10 млн. рублей. Производительность труда повышается в 5...10 раз и обеспечивается почти 100 %-е использование металла, а также значительная экономия энергии.
Электроискровые станки с программным управлением могут успешно использоваться при изготовлении деталей для телевизоров, автомобилей, а также авиационных и других двигателей. Точность обработки на них ± 1 мкм.
Внедрение оборудования для плазменного резания и механической обработки деталей способствует повышению производительности труда в 5... 10 раз.
Лазерный луч может сканировать по поверхности деталей, имеющей чрезвычайно сложную форму (лопатки газовых турбин и другие), и выполнять ее обработку. При этом обеспечивается скорость резания до 5 м/мин при обработке изделий из углеродистой и коррозионно-стойкой стали, титана и специальных сплавов.
Аналогичные результаты достигаются при применении и других новых способов обработки.
ЛЕКЦИЯ 14 ТЕХНОЛОГИЧЕСКИЕ ОСНОВЫ СТАНДАРТИЗАЦИИ И ОБЕСПЕЧЕНИЯ КАЧЕСТВА ПРОДУКЦИИ
14.1. Стандартизация технологических решений, процессов, продукции
Большую роль в повышении качества сырья, материалов и готовой продукции играет стандартизация. Стандартизация - это деятельность, направленная на достижение оптимальной степени упорядочения в определенной области посредством установления положений дня всеобщего и многократного использования в отношении реально существующих или потенциальных задач.
Основные результаты деятельности стандартизации - это повышение степени соответствия продукта (услуги), процессов их функциональному назначению, устранение технических барьеров, а международном товарообмене, содействие научно-техническому прогрессу и сотрудничеству в различных областях,
Стандартизация осуществляется в целях обеспечения:
- безопасности продукции, работ и услуг для окружающей среды, жизни, здоровья и имущества;
- технической и информационной совместимости, а также взаимозаменяемости продукции;
- качества продукции, работ и услуг в соответствии с уровнем развития науки, техники и технологии;
- единства измерений;
- экономии всех видов ресурсов;
- безопасности хозяйственных объектов с учетом риска возникновения природных и техногенных катастроф и других чрезвычайных ситуаций;
- обороноспособности и мобилизационной готовности страны;
- выполнения законодательства Республики Беларусь методами и средствами стандартизации.
Основные принципы стандартизации:
- взаимное стремление всех заинтересованных сторон, разрабатывающих, изготавливающих и потребляющих продукцию, к достижению общего согласия с учетом мнения каждой из сторон по управлению многообразием продукции, ее качеству, экономичности, применимости, совместимости и взаимозаменяемости, ее безопасности для жизни, здоровья людей и имущества, охране окружающей среды, и другим вопросам, представляющим взаимный интерес;
- программно-целевое планирование работ по стандартизации;
- техническая, экономическая, социальная обоснованность разработки нормативных документов по стандартизации;
- преемственность при применении нормативных документов по стандартизации;
- комплексность стандартизации взаимосвязанных объектов, включая метрологическое обеспечение, путем согласования требований к этим объектам, к средствам измерений и увязкой сроков введения в действие нормативных документов по стандартизации;
- гармонизация нормативных документов по стандартизации с международными, региональными и национальными стандартами других государств;
- соответствие требований нормативных документов по стандартизации современным достижениям пауки, техники, передового опыта, а также законодательным актам, нормам и правилам органов, выполняющих функции государственного надзора;
- взаимосвязь и согласованность нормативных документов по стандартизации всех уровней;
- открытость информации о действующих нормативных документах по стандартизации;
- утверждение стандартов на основе достижения согласия всеми заинтересованными сторонами;
- пригодность нормативных документов по стандартизации для их применения в целях сертификации.
Объект стандартизации - это продукция, процесс или услуга, для которых разрабатывают те или иные требования, характеристики, параметры, правила и т. п. объекта в целом иди отдельных его составляющих (характеристик). Стандартизация осуществляется посредствам создания нормативных документов. Международная организация по стандартизации (ИСО) рекомендует следующие виды нормативных документов: стандарты, документы технических условий, своды правил, регламенты (технические регламенты), положения.
Стандарт - это нормативный документ, разработанный на основе консенсуса, утвержденный признанным органом, направленный на достижение оптимальной степени упорядочения в определенной области. В нем устанавливаются для всеобщего и многократного использования общие принципы, правила, характеристики, касающиеся различных видов деятельности или их результатов. Документ технических условий устанавливает технические требования к продукции, услуге, процессу. Обычно в документе технических условий должны быть указаны методы и процедуры, которые необходимо использовать для проверки соблюдения требований данного нормативного документа в таких ситуациях, когда это необходимо.
Стандарт как основной вид нормативного документа имеет следующие разновидности: основополагающий стандарт, терминологический стандарт, стандарт на методы испытаний, стандарт на продукцию, стандарт па процесс, стандарт на услугу, стандарт на совместимость.
Выделяют следующие уровни стандартизации: международный; региональный; национальный; административно-территориальный.
Применяемые нормативные документы в системе стандартизации Республики Беларусь: Государственные стандарты Республики Беларусь (СТБ); Международные стандарты (ИСО); Региональные стандарты (EN - стандарты европейской организации по стандартизации); Руководящий документ отрасли (РД); Стандарты предприятий (СП 1); Технические условия (ТУ); Техническое описание (ТО),
Стандарты устанавливаются на продукцию серийного и массового производства, для определения единообразных понятий, технических терминов, обозначений величин и общетехнических требований.
Стандарты на продукцию серийного и массового производства содержат полную техническую характеристику стандартизируемой продукции. Они предусматривают типы, виды, марки, формы, размеры изделий и материалов, которые должны выпускаться по определенным группам продукции с учетом качественных показателей и норм (физико-механические свойства, химический состав, степень чистоты материалов, внешний вид и т. п.). Одновременно предусматриваются правила приемки и методы испытаний, необходимые для проверки с определенной точностью установленных норм, требований и характеристик. Сегодня стандартизированы требования к организационным системам предприятий, направленным на обеспечение качества продукции, созданы системы управлении качеством продукции на предприятии, стандартизированы принципы, методы и подходы в этом направлении.
Применение стандартов обеспечивает взаимозаменяемость отдельных деталей и целых узлов машин и механизмов, позволяет лучше использовать сырье, материалы, топливо и энергию, способствует специализации производства, внедрению новой техники. Снижаются затраты на внедрение в производство стандартных технологических процессов и методов, используемых при проектировании и изготовлении продукции. Особое место занимает унификация. Унификация - это выбор оптимального числа размеров или видов продукции, процессов или услуг (основана на рациональном сокращении излишнего многообразия типов, типоразмеров изделий, их частей, материалов, методов испытаний и т, п.). Применение стандартных деталей и сборочных единиц, позволяет создавать изделия по агрегатному и модульному принципу.
Современный уровень развития технологических процессов позволяет значительно повысить предъявляемые требования к качеству производимой продукции. Но мере развития научно-технического прогресса оно все больше зависит от уровня технологии и определяется такими факторами, как механизация и автоматизация технологических процессов, их непрерывность, качество исходных материалов, энерговооруженность труда, научная организация труда, общая культура производства, требования техники безопасности и охраны труда на производстве.
Качество - это совокупность характеристик объекта, относящихся к его способности удовлетворять установленные и предполагаемые требования. Качество продукции является формой выражения ее потребительной стоимости (полезного свойства) в расчете на единицу физического объема (один технический комплекс, тонна материалов, погонный метр труб и т. д.). При этом качество определяется не только объективными свойствами продукта, но и его эстетическими свойствами, технического уровня изделия (степени совершенства его конструкции, технологии и применяемых материалов) и качества изготовления. Технический уровень продукции - многоплановое понятие, которое нельзя оценить по одному, пусть даже важному, показателю.
Факторы, обусловливающие качество продукции, можно разделить на четыре группы: технические, организационные, экономические и социальные. К техническим факторам относятся: вид изготавливаемой продукции и серийность ее производства; состояние технической документации; качество технологического оборудования, оснастки, инструмента; состояние испытательного оборудования; качество средств измерения и контроля; качество исходных материалов, сырья, комплектующих изделий, Факторы, влияющие на качество продукции, могут быть представлены тремя блоками: качество производимой продукции зависит от внутренних (внутрифирменных) обстоятельств (дисциплина, оборудование, технология, метрологическое обеспечение, испытательная база, технический контроль, организационная структура, система), человеческого фактора (квалификация, опыт, профессионализм, поощрения, активность и инициатива, обмен передовым опытом) и внешних условий (требования рынка, уровень конструкторских разработок, ритмичность поставок от смежников, качество поставляемых сырья, материалов, комплектующих изделий).
Дата добавления: 2016-01-04; просмотров: 46; Мы поможем в написании вашей работы! |
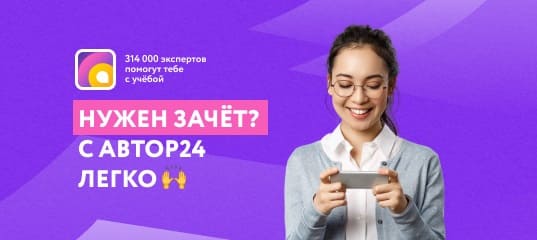
Мы поможем в написании ваших работ!