Конструктивные особенности. Автоматические коробки скоростей, круговые столы, механизмы перемещений. Инструментальные магазины, автооператоры.
Автоматические коробки скоростей. Для осуществления непрерывного процесса резания с постоянной мощностью и скоростью при изменении частоты вращения шпинделя во всех поддиапазонах (что наиболее актуально при торцовом точении) применяют коробки скоростей с автоматическим переключением ступеней (АКС) электромагнитными или гидравлическими муфтами. Коробки АКС выпускаются нескольких типоразмеров и используются в ряде станков с ЧПУ. Унифицированные коробки скоростей АКС предназначены для использования в приводах главного, движения и подач металлорежущих станков токарной, сверлильной, расточной и фрезерной групп, а также для применения в некоторых других машинах. Привод АКС обеспечивает ступенчатое регулирование скорости шпинделя в широком диапазоне с практически постоянной мощностью.
Унифицированные коробки скоростей позволяют сосредоточить с помощью механической передачи все операции управления приводом: пуск, торможение, реверсирование, регулирование скорости. Они обеспечивают высокую скорость переходных процессов, возможность переключения при работе, защиту деталей привода от перегрузок и имеют ряд других преимуществ по сравнению с коробками передач с передвижными блоками зубчатых колес. В АКС применены нормализованные электромагнитные муфты с магнитопроводящими дисками с бесконтактным токоподводом. Гамма АКС включает семь габаритов (0—6) мощностью от 1,5 до 55 кВт.
|
|
Дистанционное управление приводом АКС осуществляется с помощью бесконтактной тиристорной системы управления.
Кинематическая схема привода главного движения станка 16К20ФЗС4 с АКС приведена на рис. 51. Вращение шпинделю передается от асинхронного электродвигателя (мощностью Р=10 кВт и n = 1460 об/мин), помещенного внутри основания, с помощью клиновых ремней 53 и электромагнитных муфт ЭМ на входной вал I автоматической коробки скоростей (АКС), с выходного вала III АКС с помощью зубчатой цепи или клиновых ремней вращения передается на входной вал IV шпиндельной бабки. В шпиндельной бабке предусмотрено переключение вручную двух диапазонов частот вращения c отношением 1:3 АКС по программе имеет девять значений частоты вращения, а в шпиндельной бабке вследствие переключения блока зубчатых колес z43 и z60 вручную увеличивается вдвое, что вместе обеспечивает 18 частот вращения шпинделя в диапазонах от 35 до 1600 об/мин (по девять частот в каждом диапазоне). Управляются АКС от пульта управления системы ЧПУ ЭМ907. Переключатель на пульте управления в автоматическом режиме устанавливается в положение «Автомат».
Для осуществления нарезания резьбы на станках 16К20ФЗС4 и 16К20ФЗС5 в схеме предусмотрен датчик ВЕ-51. Вал VII получает вращение от шпинделя посредством беззазорной зубчатой передачи 60/60 с передаточным отношением, равным единице.
|
|
Некоторые модели современных многооперационных фрезерно-сверлильно-расточных станков с ЧПУ оснащены столами, которые имеют не только линейные программируемые движения, но и поворот, используемый как делительное движение при смене позиции (установа) обработки или в качестве круговой подачи.
Столы таких станков выполняются по конструктивной схеме 15 рис. 3 в виде квадратной плиты с системой высокоточных базирующих и крепежных отверстий 7 (рис. 17).
В геометрическом центре стола 1 выполнено основное базовое отверстие, предназначенное для центрирования приспособлений относительно оси поворота. Эта центрирующая (двойная направляющая) база используется в обязательном порядке, если стол применяется как рабочий орган круговой подачи при обработке кольцевых поверхностей или при высоких требованиях к точности нескольких поверхностей с разных сторон детали относительно центрального (базового) отверстия.
У большинства станков внутри стола имеется гидравлический (реже электромеханический) привод для автоматического зажима заготовок в приспособлении. Выходным элементом привода является шток 3 с внутренней резьбой для соединения с входным элементом зажимного механизма приспособления.
|
|
Приспособления 4 устанавливаются на столе станка по классической схеме базирования «по плоскости и двум пальцам», один из которых срезанный. «Полный» палец обеспечивает базирование либо по центральному отверстию, либо по одному из базовых отверстий с резьбовым участком. Для повышения точности базирования могут использоваться цанговые втулки 5, которые за счет конических втулок 2 при затягивании крепежного винта 6 разжимаются и устраняют зазор в соединении отверстие - палец. Крепление приспособления к столу осуществляется винтами (болтами) по резьбовым отверстиям 7.
Рис. 17. Стол многооперационного фрезерно-сверлильно-расточного станка с линейной и круговой подачами (I – цанговая втулка беззазорного базирования приспособлений)
1. Основным элементом УАСИ является инструментальные магазины – накопители устанавливаемые на многооперационных станках, представляющих собой накопители инструментов большой емкости от 16 и более. В них сосредотачивается необходимый запас режущего инструмента и контрольно измерительной оснастки. Инструментальные магазины – накопители могут устанавливаться на колонне, сверху, сбоку, на шпиндельной бабке или вне станка. Их предпочтительное расположение вне рабочей зоны оборудования так, чтобы выставленные у него инструменты и магазин не мешали подходу заготовки, снятию, а также наладки станка. Работа магазина не должна вызывать не допустимых вибраций при поиске следующего инструмента (при перемещении магазина). Инструментальные магазины используются на фрезерных, расточных, многооперационных станках. Обычно изготавливаются емкостью от 30, 72 инструментов до 360 инструментов. Инструментальные магазины являются вспомогательным устройством не участвующим в процессе резания. Недостаток: магазин находится в рабочей зоне. Преимущества: Наличие большого количества ин-ов, т.е. возможность полной обработки заготовки с одного установа. Исключение столкновений ин-ов, что облегчает программирование, наладку оборудования. Возможность замены вышедшего из строя ин-та в магазине в период работы об-ия, т.е. сокращение вспомогательного времени. Требования к ИМ:1) Достаточная вместимость 2)высокая точность позиционирования ин-та и автооператора.3)высокая надежность.4)минимальное время затрачиваемое на смену ин-та 5-12 сек. Для обеспечения обмена инструментом между шпинделем и ИМ на многооперационных станках используется 2 типа УАСИ: С автооператором и без автооператора. УАСИ без автооператора менее удобны в эксплуатации, т.к. грамоздки и должны размещаться вблизи рабочей зоны оборудования, что является нежелательным по причинам: Возможны загрязнения и попадание стружки При повороте и перемещениях магазина для смены ин-ов возникают вибрации Ограничение рабочей зоны оборудования Невозможность совмещения выбора следующего ин-та с периодом обработки заготовки, что требуе большого вспомогательного времени. Более эффективно использование УАСИ с автооператором, т.к. они обладают рядом преимуществ: Упрощенные условия загрузки ин-та Гнезда магазина защищены от грязи и стружки Нет ограничений рабочей зоны об-ия, т.к. магазин удален от зоны резания и ин-ты не мешают обработки Возможность совмещения поиска следующим по обработки ин-та и предватирельного выхода автооператора в позицию смены с обработкой
Автооператор станка это устройство для автоматической смены инструмента в многооперационном станке. Что делает автооператор станка? Автооператор осуществляет захват инструмента, выполнившего операцию, извлекает его из шпинделя и вставляет на его место другой инструмент. Контроль положения каждого инструмента в шпинделе осуществляется автоматически. Время смены инструмента около 5 секунд.
|
|
10,Агрегатные станки. Назначение, классификация Компоновки, схемы построения. Приспособления и инструмент.
Агрегатный станок – это специальные полуавтоматические или автоматические станки, конструкция которых состоит из унифицированных узлов и механизмов не связанных между собой единой кинематической схемой. Область применения данного оборудования охватывает группу предприятий с крупносерийным и массовым производством. Их основное назначение – это обработка деталей, имеющих объемные (коробчатые) формы. Технические характеристики агрегатных станков позволяют применять их для сверления, нарезания резьбы, фрезерования и много других работ, связанных с токарной обработкой заготовок.
Станки такой модели, еще применяются в тех случаях, когда деталь, которая обрабатывается, закрепляется в неподвижном состоянии, а в движении находится режущий инструмент. Это дает возможность, на одной детали выполнять одновременно несколько операций с разных сторон детали.
Классификация
В зависимости от геометрических размеров заготовок, которые могут обрабатываться, агрегатные станки классифицируются на три группы. Каждая группа отличается габаритными размерами станка, его весом и конструкцией унифицированных узлов.
Группа малогабаритных агрегатных станков. Это группа станков с небольшими размерами пинольных головок. Мощность пинольных головок колеблется от 0,18 до 0,75 кВт.
Группа средних станков. У этой группы станков силовые головки имеют плоскокулачковый привод. Мощность подачи колеблется от 1,1 до 3 кВт.
Группа больших размеров. Такие станки в своей конструкции имеют гидравлические или электромеханические столы. Такие столы предназначены для установки на них шпиндельных узлов.
Агрегатные станки классифицируются также по конструктивным особенностям:
По количеству рабочих позиций классификация осуществляется по следующим признакам:
однопозиционные. Конструкция такого агрегатного станка обеспечивает многостороннюю обработку деталей. Обрабатываемая деталь, на этих станках фиксируется в закрепленном неподвижном положении. Силовая головка агрегатного станка может обрабатывать заготовку с одной, двух или трех сторон;
многопозиционные. На таком оборудовании заготовки могут обрабатываться в последовательном режиме. На каждом режиме обработка может вестись в трехстороннем режиме.
По расположению инструмента. Силовая головка может обеспечить расположения инструмента по отношению к обрабатываемой детали в вертикальном, горизонтальном или наклонном положении.
По способу крепления и передвижению заготовки классификация разделяет станки на следующие виды:
станки, у которых столы неподвижные;
станки с поворотным столом. Такая модель позволяет передвигаться столу вокруг двух осей (вокруг осей в вертикальной и горизонтальной плоскости);
станки с возможностью перемещения в 1, 2, 3-х направлениях.
К отдельной классификационной группе следует отнести агрегатные станки линейного построения. На этих станках можно выполнять сверлильные, фрезерные и другие работы, а также нарезать внутренние резьбы. У таких станков нет закрепленного основания. Конструктивно такие станки состоят из рамы, электродвигателя и держателя рабочего инструмента. Рама оснащена направляющими. Заготовка крепится в специальное приспособление.
Многие промышленники требуют от станочного оборудования высокой степени гибкости при совершенной производительности. Этим требованиям удовлетворяют агрегатные станки с ЧПУ, которые относятся к особой классификационной группе.
Типовые компоновки агрегатных станков
Компоновка агрегатных станков выполняется по схемам в зависимости от конфигурации и геометрических размеров заготовок и заданной точности обработки. При обзоре их можно разделить на следующие виды:
одношпиндельные и многошпиндельные. Это агрегатные станки, компоновка которых строится в зависимости от конструкции силовых головок;
однопозиционные. Это агрегатные станки, основные узлы которых расположены таким образом, что они всегда находятся в центре внимания оператора станка. Заготовки на таких станках закрепляются неподвижно, а отдельные поверхности обрабатываются только одним инструментом;
барабанного типа (многопозиционный). Это станки скомпонованные таким образом, что заготовки обрабатываются с нескольких позиций. При такой компоновке можно одну и ту же поверхность, если применить последовательный цикл, обрабатывать двумя и более инструментами. Для таких целей станок снабжается поворотным столом барабанного типа;
станки односторонние и многосторонние. Эти станки отличаются друг от друга по конструктивному расположению инструмента относительно заготовки. Они могут быть вертикального, наклонного или горизонтального исполнения.
Если рассматривать способы крепления и перемещения обрабатываемых деталей, то станки можно сгруппировать по следующим принципам:
станок с неподвижным столом. Это станок, у которого стол находится в неподвижном положении;
станок с поворотным столом. Это агрегатный станок барабанного типа, у которого стол может вращаться относительно как вертикальной, так и горизонтальной оси;
станок с перемещающимся столом. Стол у такого станка может свободно перемещаться в нескольких направлениях. Обычно в 1, 2 или 3-х направлениях.
Устройство станка состоит из четырех основных групп унифицированных узлов.
Силовые узлы
К таким узлам принадлежат силовые головки и столы.
Силовые головки. С помощью этого узла осуществляется подача шпинделя с инструментом. Головка также придает вращательное движение шпинделю. Широкое распространение получили многошпиндельные агрегатные станки, производитель которых конструирует их таким образом, чтобы главное движение и движение подач осуществлялось одновременно. Нормы точности определяются силовыми головками.
Силовые головки снабжаются своим собственным электрическим приводом. Электрическая схема в виде главного привода предусматривает электрические двигатели. Электросхема также предусматривает блоки управления, защиты от перегрузок, блоки сигнализации.
Шпиндельные узлы
К шпиндельным узлам относятся силовые бабки и шпиндельные коробки.
Агрегатный станок можно наладить таким образом, что он может быть превращен в обычный металлообрабатывающий станок узкого назначения. Это достигается путем установки соответствующих шпиндельных узлов. Например:
если использовать только одну сверлильную бабку, то такой станок превратиться в агрегатно-сверлильный станок. Многошпиндельные агрегатные станки для сверления обычно не применяются на малом и среднем производстве, а вот при массовом производстве, где необходимо выполнять много сверлильных операций на крупных заготовках, они просто незаменимы;
при установке фрезерных бабок, такой станок выглядит как агрегатный фрезерный станок.
Базовые узлы
К базовым узлам относятся: станина, колона, упорные угольники.
Транспортные узлы
К этой группе унифицированных узлов относятся делительные столы.
11, Станки для обработки отверстий. Сверлильные станки, основные параметры, конструкции, кинематические схемы.
Сверлильные станки предназначены для получения сквозных или глухих отверстий, для чистовой обработки отверстий зенкерованием и развёртыванием, для нарезания внутренних резьб метчиками, для зенкования торцовых поверхностей и отверстий.
Существуют следующие типы универсальных сверлильных станков:
1. Настольно-сверлильные; 2. Вертикально-сверлильные (одношпиндельные);
3. Радиально-сверлильные; 4. Многошпиндельные 5. Для глубокого сверления.
Основной параметр, характеризующий размер станка - наибольший условный диаметр сверления в стальных заготовках (2Н135 - две последние цифры в модели станка - 35 мм). К основным размерам относятся также номер конуса шпинделя, наибольший ход шпинделя.
В машиностроении наибольшее распространение получили вертикально - и радиально-сверлильные станки.
Вертикально-сверлильный станок мод. 2А135 (рис. 18, стр.9), например, предназначен для сверления отверстий до диаметра 35 мм. Он имеет приводные кинематические цепи (см. рис.)
Радиально-сверлильные станки предназначены для обработки отверстий в средних и крупных деталях при единичном и серийном производстве. Они позволяют направлять инструмент в любую точку неподвижной детали в зоне хобота станка вокруг колонны и перемещения по его направляющим шпиндельной головки. Высокие детали устанавливаются в яме, сделанной около станка.
Радиально-сверлильный станок мод. 2В56 (рис. 19 стр. 9), например, имеет наибольший диаметр сверления 50 мм, N = 5,5 кВт; n = 55…1140 об/мин, вылет шпинделя до 2100 мм. Кроме кинематической группы привода вращения шпинделя и его подачи, на станке имеется кинематическая группа подъёма хобота.
Для перемещения хобота сверловщик вручную (Pr) включает (+) двигатель подъёма (опускания) хобота Дх, но подача хобота Пх начинается только после освобождения зажима хобота Пзаж на колонне, в конце которого движением разжима включается муфта М и начинается перемещение хобота. Для остановки хобота на нужной высоте сверловщик отпускает кнопку, при этом Дх не останавливается, а реверсируется (Р) (-), после чего в начале зажима хобота он через движение Пзаж выключает муфту М, а в конце движения зажима конечным выключателем КВ выключает сам себя. Перемещение шпинделя бабки по хоботу и поворот хобота выполняются вручную. Для обсверловки тяжёлых деталей применяются переносные радиально-сверлильные станки, перемещаемые краном. Они имеют поворот оси шпинделя на любой угол в двух плоскостях. (рис. 21.)
Многошпиндельные сверлильные станки бывают: 1. с неподвижными осями шпинделя; 2. с переставными шарнирными шпинделями (рис. 20)
Первые – станки общего назначения, предназначены для последовательного выполнения ряда переходов различными инструментами, при перемещении вручную заготовки.
Вторые – настраиваются при серийном производстве для одновременного сверления нескольких отверстий. Возможность изменения взаимного расположения осей шпинделей в них обеспечивается двух шарнирным сочленением шпинделей с центральным приводным валом.
Станки для глубокого сверления (рис. 4 стр. 3) применяются в случае, если длинна отверстия во много раз превышает его диаметр. В них вращение подаётся на сверло или на деталь или на то и другое одновременно. Инструмент является пушечное или ружейное сверло. Стружка непрерывно вымывается СОЖ, подаваемой через центральное отверстие сверла под давлением в 5-20 кг/см2.
12, Расточные станки. Координатно-расточные станки. Кинематика, основные особенности.
Подразделяются на 1. горизонтально-расточные; 2. координатно-расточные; 3. алмазно-расточные; 4. станки для глубокой расточки.
В горизонтально-расточных станках основной размер – диаметр шпинделя. Главное движение резание – вращение шпинделя или вращение планшайбы. К подачам кроме движения стола и бабки относятся ещё осевое движение шпинделя и радиальное движение резцового суппорта на планшайбе. На этих станках могут выполнятся следующие работы: 1. сверление; 2. растачивание отверстий;
3. подрезка торцов; 4. нарезание резьбы; 5. Фрезерование плоскости.
Горизонтально-расточной станок мод. 262 Г (рис 23, стр. 11), например, имеет диаметр шпинделя равный 85 мм. Размеры стола у него 800×1000, n = 20…1000 об/мин у шпинделя и в 2 раза меньше у планшайбы.
Шпиндель за счёт двухскоростного электродвигателя и двух тройных блоков имеет 18 скоростей. Наиболее часто используется осевая подача шпинделя Пос. Подъём бабки Пв.б. кинематически связан с подъёмом опорного люнета Пв.л., чтобы сохранить соосность последнего со шпинделем. Винтовой суммирующий механизм ∑ в приводе Пв.л служит для возможности ручной выверки соосности опорного люнета относительно шпинделя. Все упомянутые движения могут выполнятся также быстро от электродвигателя Дб при выключенной муфте М.
Винторезная кинематическая цепь является
формообразующей,но её кинематическая точность не очень велика, т.к. резьбы нарезается только крепёжные. Настройка её на шаг резьбы ведётся гитарой iвинт. При вращении планшайбы Впл шестерня z = 22 привода радиальной подачи будет обкатываться по центральному колесу z = 116 и за счёт этого вращать реечное колесо z = 16 радиальной подачи, т.е тут имеется скрытый суммирующий механизм ∑комп. На него третью ветвь также от планшайбы подаётся компенсирующее вращение.
В координатно-расточных станках основной размер – ширина стола. Эти станки предназначены для обработки точных отверстий при допуске на расстояние между их осями порядка 5…10 мкм. Бывают одностоечные и двухстоечные – станки (КРС).
Координатно-расточной станок мод. 2А450, например, имеет размеры стола 630×1100, он одностоечный. Электродвигатель Д1 имеет бесступенчатое регулирование.
Подача шпинделя также регулируется бесступенчато с помощью механического вариатора с раздвижными коническими шкивами и стальным кольцом. Бесступенчатое регулирование скоростей и подач позволяет на ходу вывести станок из резонанса, обеспечив тем самым малую шероховатость обрабатываемой поверхности. К станку прилагается накладной, поворотный в двух плоскостях стол.
Алмазно-расточные станки обеспечивают тонкое растачивание отверстий с некруглостью их в пределах 3…5 мкм и шероховатостью поверхности 1,25…0,32 мкм. Частота вращения шпинделя порядка нескольких тысяч оборотов в мин. Подача обычно гидравлическая малая по величине, порядка 10…15 мм/мин. Припуск снимается 0,1…0,4 мм. Расположение шпинделей бывает вертикальным и горизонтальным.
Станки для глубокой расточки мало отличаются от станков для глубокого сверления, только работают расточными головками разной конструкции.
13,Станки для абразивной обработки. Кругло и внутришлифовальные станки.
Шлифовальные станки применяются в основном для снижения шероховатости обрабатываемых деталей и получения точных размеров. В большинстве случаев на шлифование детали поступают после предварительной черновой обработки и термических операций, хотя бывают случаи, когда шлифование является единственным методом обработки. Основной инструмент при шлифовании – шлифовальный круг. На шлифовальных станках можно обрабатывать наружные и внутренние цилиндрические, конические и фасонные поверхности и плоскости, разрезать заготовки, шлифовать резьбу и зубья зубчатых колёс, затачивать режущий инструмент и т.д. Шлифовальные станки в зависимости от назначения подразделяются на круглошлифовальные, внутришлифовальные, безцентровошлифовальные, плоскошлифовальные и специальные.
Главным движением резания во всех шлифовальных станках является вращение шлифовального круга, измеряемое в м/сек. Vшл = 30…40 м/сек.
1. Круглошлифовальные станки.
Обработка длинных валов (рис. а). Станок имеет следующие движения: главное движение – вращение шлифовального круга, круговая подача – вращение
заготовки. Кроме того, имеется продольная подача заготовки Ппр и поперечная подача шлифовального круга (подача врезания) Пвр.
Станки, работающие методом врезания (б) имеют круговую подачу, подачу на врезание (Пвр), а также осциллирующую подачу, т.е. колебательное осевое движение, которое могут совершать шлифовальная бабка или стол.
Круглошлифовальные станки бывают простые и универсальные, т.е. имеющие поворот оси шпиндельной бабки и бабки изделия для шлифования конусов.
Основной размер в них – наибольший диаметр обработки. Он равен 100-1600 мм.
Круглошлифовальный станок мод. 3А151, например, предназначен для обработки деталей с диаметром до 200 и длиной до 700 мм. (рис 38)
Вращение шлифовального круга Vш выполняется от двигателя ДVcN = 7 кВт через сменные шкивы iv. Круговая подача заготовки Vз – от двигателя постоянного тока Д2, через клиноременные передачи сообщает заготовке n = 63…400 об/мин. Продольная подача заготовки Ппр и подача врезания Пвр шлифовального круга выполняется гидравлически от насоса Н1. Продольное перемещение стола Ппр выполняется гидроцилиндром Гц Sпр . Оно управляется реверсивным золотником Зр от управляющего золотника Зу, переключаемого переставным упором Уп или вручную. При этом золотник включения продольной подачи ЗSпр перемещён влево. Переключением его вправо отключается возвратно-поступательная продольная подача стола и создаётся возможность наладочного перегона стола влево или вправо ручным включением крана Кр. При любых гидравлических перемещениях стола в блокировочный гидроцилиндр Гц бл , через канал крана Кр подаётся масло, благодаря чему блокировочная муфта Мбл отключает реечное колесо с z = 10 от маховика ручного перемещения стола, что бы рукоятка этого маховика не травмировала рабочего при вращении. Ручное перемещение стола маховика
возможно только при выключении гидроприводе, когда пружина блокировочного гидроцилиндра включает муфту Мбл.
При правке круга нужна меньшая скорость перемещения стола, поэтому вручную переключают золотник Зправ или Зшл, чтобы слив проходил через дроссель правки Дрпр, а не через досель шлифования Дршл.
Для уменьшения шероховатости поверхности, обрабатываемой врезным шлифованием, шпинделю шлифовальной бабки сообщают осевое колебательное (осциллирующее) движение Посц с частотой n = 40 дв. х/мин и амплитудой 0…3 мм. Для этого со шпинделя червячной парой вращение передаётся эксцентрику, качающему через рычаг шпиндель. Амплитуда регулируется рычагом гидроцилиндра Гц осц. Подача на врезание осуществляется от гидроцилиндра Гцвр.
2. Внутришлифовальные станки. На внутришлифовальных станках шлифуют сквозные и глухие отверстия цилиндрической и конической формы, а также их торцы.
При обычном исполнении станков вращаются как шлифовальный круг Vкр, так и заготовка.
При планетарном исполнении вращение заготовки Vзаг передано оси шлифовального круга Vоси , т.к. заготовки обычно тяжёлые и имеют несимметричную форму. Кроме того подача врезания Пвр выполняется на этих станках не смещением оси шлифовального круга относительно оси шлифуемого отверстия, а изменением величины радиуса вращения оси шлифовального круга относительно оси отверстия.
Для обеспечения достаточной (30-40м/с) скорости резания число об/мин шлифовальных кругов малого диаметра приходиться доводить до 150 000 об/ми.
Опорами шпинделей служат прецизионные радиально-упорные шарикоподшипники со смазкой масляным туманом, а также гидро- и аэростатические подшипники.
Внутришлифовальный полуавтомат мод. 3А252, например, предназначен для шлифования отверстий с диаметром до 200 мм (рис. 39).
Шлифовальный круг имеет две частоты вращения: 3650 и 1000 об/мин, устанавливаемые сменными шкивами. Электродвигатель привода вращение заготовки Взаг – двухскоростной, что в сочетании с бесступенчатым вариатором даёт диапазон частот вращения заготовки nзаг = 110…870 об/мин.
Гидропривод обеспечивает возвратно-поступательное движение шлифовальной бабки Ппр гидроцилиндром Гц Пр с одновременным отключением гидроцилиндром Гцбл ручного привода этого движения маховиком, а также зажима заготовки в патроне гидроцилиндром Гц заж. Включение продольного перемещения шлифовальной бабки Ппр выполняют вручную золотником Зпр, при этом одновременно срабатывает и Гцбл. Реверсирование Ппр выполняется упорами Уп или вручную реверсивным золотником Зр.
Подача врезания Пвр выполняется на каждый двойной ход бабки электромагнитом, срабатывание которого поворачивает краповое колесо с z = 200 на несколько зубьев вместе с корпусом. Этот поворот передаётся через планетарный механизм на ходовой винт с шагом t = 3 мм. Пружина на дальнем конус ходового винта обеспечивает выбор зазора в резьбе.
Левое колесо z = 23 неподвижно и скреплено с корпусом бабки. При вращении корпуса сателлит с z = 23 откатывается по центральному колесу. При этом второй сателлит с z = 22, обкатываясь по колесу с z = 24, скреплённому с ходовым винтом, заставляет его медленно поворачиваться из-за разности передаточных отношений обоих пар. Повороту храпового колеса на 1 зуб соответствует перемещение бабки на 0,00125 мм. Ручное врезание получают вращением маховика . Ходовой винт Xв1 служит для ручного поперечного перемещения бабки, а ходовой винт Xв2 для поворота этой бабки на угол шлифуемого конуса.
14,Бесцентровые станки.
Бесцентровошлифовальные станки
Бесцентровошлифовальные станки применяются в крупносерийном и массовом производстве для наружного и внутреннего шлифования тел вращения. (рис) При шлифовании наружных поверхностей заготовка 3, поддерживаемая ножом 4, располагается между двумя абразивными кругами из которых шлифуемый круг 1, вращаясь с окружной скоростью 30…40 м/с, снимает с заготовки припуск, а другой ведущий круг 2, вращающийся с окружной скоростью 10…50 м/мин, сообщает заготовке вращение (круговую подачу) VSкр и продольную (осевую) подачу Ппр. Установочное поперечное перемещение ведущего круга Пвр определяет диаметр шлифуемой детали. Ось ведущего круга 2 поворачивает на угол α, чтобы он не только вращая заготовку VSкр , но и выполняя её осевую подачу Ппр. При черновом шлифовании α = 1,5…6º, при чистовом α = 0,5…1,5º.
Для прилегания к заготовке ведущего круга, повёрнутого на угол α, по линии, он заправляется как однополостный гиперболоид вращения, движением алмаза параллельно оси заготовки.
Наиболее часто на этих станках применяют сквозное шлифование деталей с постоянным наибольшим диаметром (рис. а), но применяют и шлифование деталей с уступом до упора 5 (рис. б). В этом случае для заготовки 3 и её снятие ведущий круг 2 отводится.
Недлинные заготовки сложной формы шлифуют методом врезания поперечным перемещением ведущего круга 2 (рис. в). При этом в осевом направлении заготовка 3 фиксируется упорами 5, к которому поджимается за счёт небольшого (порядка 30”) поворота оси ведущего круга 2.
Для получения на заготовке конической, фасонной или ступенчатой формы при врезном шлифовании шлифующему, а иногда и ведущему кругу придается с помощью правки соответствующая форма рабочей поверхности по копиру.
Для бесцентрового шлифования отверстий (рис. г) заготовки 1 типа втулок базируются наружной точно обработанной цилиндрической поверхностью на два опорных ролика 2 к которым их поджимает ведущий шлифовальный круг 3. Шлифующий круг 4 кроме вращения имеет возвратного поступательное движение Ппр вдоль оси и подачи врезания Пвр в сторону ведущего круга 3. Радиальные усилия резания замыкаются через толщину стенки заготовки на ведущий круг 3, поэтому не деформируют даже тонкостенную заготовку.
г)
Преимущества бесцентровошлифовальных станков:
1. Большое сокращение вспомогательного времени на установку, выверку
и снятие заготовки, особенно при продольной подаче.
2. Меньший припуск на обработку, т.к. заготовка самоцентрируется.
3. Прогиб заготовки от сил резания исключён.
4. Большая стабильность размеров в партии деталей.
5. Возможность шлифования относительно тонких валов и тонкостенных втулок.
Недостатки: требуется высокая квалификация наладчика.
15, Плоскошлифовальные станки. Кинематика процессов, принципы активного контроля. Компоновки, схемы построения.
По расположению оси шпинделя плоскошлифовальные станки подразделяются на горизонтальные (рис. а и в), работающие периферией круга и на вертикальные (рис. б и г), работающие торцом круга.
По форме стола они подразделяются на имеющие круглый стол (в и г) имеющие прямоугольный стол (а и б).
Главное движение резания у всех разновидностей – вращение шлифовального круга Vкр. При прямоугольном столе имеется его продольное возвратно-поступательное движение Ппр, при круглом – вращение стола Vст. При работе дисковым кругом на станках с горизонтальным шпинделем имеется периодическая поперечная подача Ппоп вдоль оси шпинделя для обработки заготовок по всей их ширине.
У всех вариантов плоскошлифовальных станков имеется ещё периодическая вертикальная подача врезания Пвр, выполняемая в начале каждого хода или оборота стола. Шероховатость поверхностей, обрабатываемых на плоскошлифовальных станках после чернового шлифования достигает от 3,2 до 0,8, после чистового от 0,8 до 0,4 и после тонкого шлифования – 0,4 до 0,2.
16, Шлифовальные станки с ЧПУ. Приспособления и инструмент.
Станки с ЧПУ выпускаются на базе всех типов шлифовальных станков. При этом возникают технические трудности, которые объясняются следующими причинами. Процесс шлифования характеризуется, с одной стороны, необходимостью получения высокой точности и качества поверхности при минимальном рассеянии размеров, с другой стороны – особенностью обрабатывающего инструмента, заключающейся в быстрой потере размерной точности шлифовального круга вследствие его интенсивного изнашивания в процессе работы. Следовательно, в станке необходимы механизмы автоматической компенсации изнашивания шлифовального круга. Система ЧПУ должна быть замкнутой для компенсации деформаций системы СПИД, температурных погрешностей, разных припусков на заготовках, неточностей станка и т.д. Измерительные системы должны иметь высокую разрешающую способность, обеспечивающую жёсткие допуски на точность позиционирования, например, в круглошлифовальных станках такие приборы обеспечивают непрерывное измерение диаметров в процессе обработки с относительной погрешностью не более 0,00002 мм. Контроль продольных перемещений стола должен осуществляться с погрешностью не более 0,1 мм для круглошлифовальных станков и 0,02-0,03 мм для торцекруглошлифовальных.
Из-за большого количества неопределенной технологической информации, содержащейся в программе, программоноситель на перфоленте для шлифовальных станков практически не использовался. Для них используются системы типа CNC и HNC. Для этих систем характерно управление по 3-4 координатам, но в станках, работающих несколькими кругами, возможно управление по 5-6 и даже 8 координатам. Взаимосвязь между оператором и системой ЧПУ шлифовального станка в большинстве случаев осуществляется в диалоговом режиме с помощью дисплея. Имеется также возможность дистанционного ввода программ от центральной ЭВМ при включении станка в автоматизированный участок. Применяются встроенные диагностические системы, повышающие надёжность станков.
17, Зубообрабатывающие станки. Методы нарезания зубчатых колес.
1. Кинематика станков для нарезания цилиндрических зубчатых колёс.
Существуют два основных метода нарезания зубьев зубчатых колёс: метод копирования и метод обкатки.
Метод копирования. При обработке этим методом впадина зубчатого колеса образуется режущим инструментом, профиль режущих кромок которого выполнен по форме впадины нарезаемого колеса. К данному методу относятся фрезерование зубьев модульными дисковыми и пальцевыми фрезами, строгание профильными резцами, обработка протяжками и профильными шлифовальными кругами. Следует отметить, что профиль зуба (кривизна эвольвенты) зубчатого колеса зависит от модуля, угла зацепления и числа зубьев, следовательно, теоретически для обработки каждого зубчатого колеса с определённым числом зубьев и модулем потребуется свой режущий инструмент. Поэтому, например, при обработке дисковыми модульными фрезами зубчатых колёс одного модуля, но с различным числом зубьев применяют наборы фрез из 8, 15 или 27 шт. Метод копирования при изготовлении зубчатых колёс имеет ограниченное применение.
Метод обкатки. При обработке зубчатых колёс методом обкатки в процессе нарезания зубьев воспроизводится работа какой либо зубчатой пары (реечной, цилиндрической, червячной, конической). При этом одна из деталей зубчатой пары является инструментом, а другая – заготовкой. Формирование боковых поверхностей обрабатываемых зубьев происходит при последовательном изменении положений режущих кромок инструмента в процессе огибания (обкатки) инструмента и заготовки. Метод обкатки обеспечивает высокую производительность и точность нарезания зубьев, возможность одним инструментом обрабатывать зубчатые колёса одного и того модуля с любым числом зубьев.
Обработка зубчатых колёс долбяками.
Долбяк 1 имеет форму цилиндрического колеса, зубья которого выполнены с углами резания. При нарезании воспроизводиться работа пары цилиндрических зубчатых колёс (долбяк 1 и заготовки 2). Во время обработки долбяк получает прямолинейное возвратно-поступательное главное движение и медленное вращение вокруг своей оси. В начале нарезания зубьев при согласованном вращении заготовки и долбяка (движение обкатки) происходит радиальное врезание долбяка (или заготовки) до полной глубины резания. Для получения полностью обработанных зубьев на всей окружности заготовка после окончания радиального врезания долбяка должна сделать полный оборот. Резание происходит только при прямом ходе долбяка, а при обратном холостом ходе шпиндель долбяка или стол несколько отводится образуя зазор между инструментом и заготовкой для устранения трения задних поверхностей долбяка в впадине нарезаемого колеса. Долбяками можно производить нарезание цилиндрических колёс наружного зацепления внутреннего зацепления, зубчатых блоков, цилиндрических колёс с косыми зубьями.
Для нарезания цилиндрических колёс с косыми зубьями необходимы специальные долбяки. Угол наклона зубьев долбяка должен равняться углу наклона зубьев нарезаемого колеса. Для нарезания колёс наружного зацепления направление наклона зубьев долбяка должно быть противоположным, а для нарезания колёс внутреннего зацепления – одноименным. Дополнительный к основному вращению поворот долбяка при помощи специальных винтовых направляющих копиров.
Зубодолбёжные станки. Производительность их (кроме работающих многорезцовой головкой) ниже, чем зубофрезерных, однако они незаменимы при нарезании колёс внутреннего зацепления, а так же колёс с буртами и блоков, в которых недостаточно места для выхода фрезы.
Зубодолбёжные станки могут работать: 1. долбяком круглым; долбяком – рейкой; 3. многорезцовой головкой обрабатывающей в шестерне одновременно все впадины (рис. 30-31). В первых двух случаях образующая линии зуба получается методом обкатки, а в третьем случае – методом копирования полной образующей линии.
Зубодолбёжный станок модели 514, рис. 33, предназначен для обработки шестерён с диаметром до 450 мм и модулем до 6 мм. Обработка зубчатых колёс производиться долбяком по методу обкатки.
1. Главное движение (возвратно-поступательное движение долбяка) осуществляется от эл. двигателя Д через клиноременную передачу, два двойных подвижных блока шестерён, кривошипный диск Кр, зубчатую рейку, колесо-колесо, рейку. Расчётные перемещения
Число двойных ходов долбяка в мин. определяют по формуле , где Vср – выбранная средняя скорость резания, м/мин; l = b + c – длина хода долбяка (b – ширина заготовки, c - выбег). Длину хода долбяка регулируют изменением радиуса вращения пальца кривошипа (Кр).
2) Движение круговой подачи – поворот долбяка на его двойной ход. В зубодолбёжных станках под круговой подачей Sкр понимают длину дуги поворота долбяка по делительной окружности за один его двойной ход. Следовательно, цепь подачи соединяют вращение долбяка и перемещение долбяка Т.к. одному двойному ходу долбяка соответствует один оборот кривошипного диска. По УКБ подача начинается от кривошипного диска
где
- модуль долбяка.
Отсюда формула настройки:
.
3) Движение радиальной подачи обеспечивает перемещение заготовки в радиальном направлении до полной глубины нарезания. В цепи подач врезания
Здесь Н – шаг подъёма архимедовой спирали кулачка Квр. Врезание долбяка в заготовку на заданную высоту зуба осуществляется плоским кулачком Квр. На кулачке имеется участок врезания, профиль которого очерчен по спирали Архимеда (занимает угол αвр=90˚) и участки обкатки, очерченные по окружности, занимающие различные углы в зависимости от числа проходов. При нарезании зуба в один проход кулачок, поворачиваясь на угол αвр, действует на долбяк, перемещая его по направлению к заготовке (врезание). Когда ролик достигает точки 1 врезание прекращается. При дальнейшем вращении кулачка на угол α1 происходит обкатка. За это время заготовка совершает 1 оборот. Когда ролик достигает точек 2 он попадает во впадину и заготовка отходит от долбяка.
4) Движение обкатки обеспечивает согласованное вращение долбяка и заготовки. Уравнение кинематического баланса (УКБ) и формула настройки.
Здесь iоб в знаменателе, потому, что порядок сменных шестерён a, b, c, d на схеме обозначен в обратном направлении и
Дата добавления: 2018-02-18; просмотров: 770; Мы поможем в написании вашей работы! |
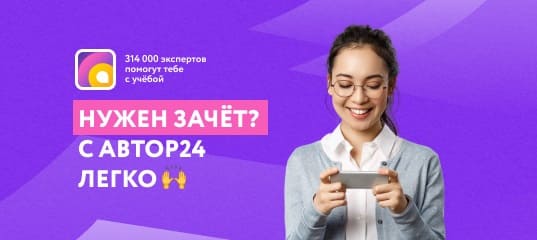
Мы поможем в написании ваших работ!