ГЛАВА 10. МЕТАЛЛУРГИЧЕСКИЕ ПРОЦЕССЫ
В соответствии с промышленной классификацией металлы делятся на черные, к которым относятся железо и его сплавы, марганец и хром, производство которых связано производством чугуна и стали, и цветные, важнейшим из которых является алюминий.
Производство алюминия
По размерам производства (начато с конца XIX в.) алюминий в настоящее время занимает первое место среди всех цветных металлов. Он имеет высокую электро- и теплопроводность (уступая только серебру и меди) и применяется как полупроводниковой материал и материал для деталей теплотехнических устройств. Алюминиевые деформируемые сплавы (дюралюмины и др.) – важнейшие конструкционные материалы в авиа- и других областях техники. Алюминиевые литейные сплавы (силумины и др.) широко применяют в машиностроении. Вследствие высокой коррозионной стойкости алюминиевые сплавы используют в химической и пищевой промышленности, для бытовых изделий. Таким образом, производство алюминия очень востребовано.
Способы восстановления алюминия непосредственно из бокситов и других руд еще не разработаны. Современное производство алюминия состоит из двух основных процессов: получение глинозема Al2O3 из бокситов и получение металлического алюминия путем электролиза расплавленного глинозема.
Глинозем получают щелочными, электротермическими и другими способами. Наиболее распространенным является щелочной способ, разработанный в конце XIX в. К.И. Байером, включающий следующие стадии.
|
|
1. Подготовка боксита – дробление его крупных кусков и затем мокрый размол, т.е. измельчение в шаровых мельницах, куда доливают оборотный раствор с добавками щелочи (NaOH).
2. Выщелачивание (варку) полученной пульпы производят в автоклавах (герметических стальных сосудах цилиндрической формы, диаметром 1.5-2.5 м., высотой 8-14 м.). Процесс идет при температуре 105-250 °С, давлении до 25-30 атм и концентрации щелочи (NaOH) 250-300 г/л. для нагрева и перемешивания пульпы широко используют пар, подаваемый через сопло в днище.
При выщелачивании образуется алюминат натрия:
AlO(OH) + NaOH = NaAlO2 + H₂O Al(OH)3 + NaOH = NaAlO2 + 2H₂O
Образующийся алюминат хорошо растворяется в воде и переходит в раствор. Окиси железа, титана и другие примеси боксита, нерастворяющиеся в щелочах, выпадают в осадок (красный шлам). Кремнезем SiO2 образует нерастворимые соединения – силикоалюминат натрия Na₂O·Al₂O₃·2SiO₂·2H₂O и выпадает в осадок, что приводит к потерям Al₂O₃ и NaOH; поэтому способом Байера невыгодно перерабатывать бокситы с повышенным содержанием кремнезема.
3. Разбавление, сгущение и фильтрацию производят для получения из автоклавной пульпы чистого раствора алюмината натрия. Пульпу разбавляют промывочной водой для последующего более полного удаления твердых частиц красного шлама и направляют в чаны – сгустители. Отстоявшийся осветленный раствор (верхний слив) дополнительно очищают фильтрацией; осадок после многократной промывки идет в отвал.
|
|
4. Выкручивание (декомпозиция) раствора алюмината натрия проводят при понижении температуры и интенсивном перемешивании пульпы:
NaAlO₂ + 2H₂O = Al(OH)3 + NaOH.
Операцию проводят в стальных емкостях (декомпостерах), перемешивания раствор мешалками или сжатым воздухом и постепенно понижая температуру от 60-65 до 40-45 °С. Продолжительность разложения 50-70 ч. Для ускорения процесса в раствор добавляют некоторое количество гидроокиси алюминия, играющий роль центра кристаллизации (затравки). Из раствора гидроокись алюминия выделяют в чанах-сгустителях и разделяют по степени крупности; более крупные частицы направляют на последующую операцию – кальцинацию, более мелкие используют как затравку. Щелочной раствор регенерируют и возвращают в производство.
5. Кальцинацию, т.е. обезвоживание гидроокиси алюминия, производят ее прокаливанием при 1200 °С в трубчатых вращающихся печах или в установках с кипящим слое:
|
|
2Al(OH)₃ + H₂O = Al₂O₃ + 3H₂O.
Выход глинозема составляет около 85 %, на 1т глинозема расходуется 2-2.5 т боксита. Потери связаны с образованием шлакоалюмината натрия при выщелачивании боксита. Поэтому щелочным способом перерабатываются бокситы с небольшим содержанием кремнезема.
Электротермический способ состоит в том, что в электропечи плавят шихту, состоящую из боксита, известняка, кокса и др. Продуктами плавки являются ферросилиций и шлак, содержащий алюминат кальция Al₂O₃·CaO. Измельченный шлак обрабатывают раствором соды, получая алюминат натрия.
Электролиз глинозема для получения металлического алюминия производят в электролизерах – ваннах с различным устройством анодной части (рис.10.1).
Анодное устройство состоит из вертикального установленного самообжигающегося угольного электрода, нижняя часть которого погружена в электролит – расплав, состоящий из глинозема Al2O3 (8-10 %) и криолита – фторида алюминия и натрия Na3AlF6. Электролит нагревается до рабочей температуры 930-950 °С теплом, выделяющимся при прохождении тока между анодом и катодом. Условия электролиза: ток – постоянный, напряжение 4-4.5 В, анодная плотность тока 0.7-1.2 А/см².
|
|
Рис. 10.1. Схема устройства электролизера:
1 – кожух, 2 - огнеупорная футеровка, 3 – футеровка из угольных плит, 4 – глинозем, 5 – слой расплавленного электролита, 6 – гарнисаж, 7 – слой алюминия, 8 – рабочий блок обожженного анода, 9 – токоподводы, 10 – наращиваемый блок, 11 – кожух анодной массы, 12 – анодная масса.
При электролизе в расплавленном электролите происходит диссоциация молекул криолита и глинозема:
Na3AlF6 → 3 Na+ + AlF63-,
Al2O3 →Al3+ + AlO33-.
На катоде разряжаются только катионы алюминия: Al3+ + 3е → Al и таким образом, для получения металлического алюминия практически расходуется только глинозем. По мере объединения электролита глиноземом его периодически догружают в ванну. Признаком обеднения электролита служит так называемый анодный эффект, выражающийся в увеличении напряжения с 4-4.5 до 25-30 В. В результате анодного процесса: 2AlO₃³⁻ - 6e → Al2O3+ ½ O2 выделится газообразный кислород, вызывающий постепенное сгорание угольных анодов. Расплавленный алюминий постепенно скапливается на дне ванны и периодически удаляется при помощи сифонов и вакуумных ковшей.
Для получения 1 т алюминия расходуется около 2 т глинозема, до 0.6 т угольных анодов, около 0.1 т криолита и 16500 – 18500 кВт·ч электроэнергии.
Полученный электролизом первичный алюминий содержит примеси (железо, кремний, частицы глинозема и т. п.), ухудшающие его свойства, и поэтому подвергается рафинированию.
Рафинирование хлора заключается в продувке расплавленного алюминия при 700-750 °С газообразным хлором в течение 10-15 мин. Образующийся при этом хлористый алюминий AlCl3 находится в парообразном состоянии. Выделяясь из метала, он обеспечивает его очистку от растворенных газов и примесей. После рафинирования хлором получают алюминий чистотой 99.85 %.
Электролитическое рафинирование применяют для получения алюминия более высокой чистоты, до 99.999 %.
Новым является способ рафинирования через субсоединения. При пропускании хлористого или фтористого алюминия над расплавленным алюминием при температуре около 1000 °С образуются газообразные неустойчивые субсоединения алюминия AlCl3, AlF. При охлаждении до 700 – 800 °С они разлагаются с выделением алюминия чистотой до 99.999%. Алюминий такой же чистоты можно получать методом зонной плавки.
КОНТРОЛЬНЫЕ ВОПРОСЫ К ТЕМЕ 10.1
10-1.Какие горные породы используют в качестве алюминиевых руд? Как влияет природа сырья на выбор метода производства глинозема?
10-2. Из каких операций состоит процесс получения глинозема методом выщелачивания? Приведите принципиальную схему процесса.
10-3. Почему метод спекания в производстве глинозема может применяться для всех видов алюминиевого сырья?
10-4. Почему электролиз расплава глинозема является единственным промышленным методом производства алюминия? Для чего электролизу подвергают не чистый глинозем, а его расплав в криолите?
10-5. На чем основан метод электролитического рафинирования алюминия?
ЗАДАЧИ К ТЕМЕ 10.1
10-1.Сколько гидроксида натрия вступит в реакцию при мокром щелочном обогащении 1 т диаспора, в составе которого 56 % Аl2О3, 26% Fе2О3 и 3,7% SiO2 (по массе)? Какова массовая доля железа в красном шламе, если в него перешло 4/5 SiO2 в виде алюмосиликата?
10-2.Сколько кальцинированной соды, в составе которой 5 % некарбонатных примесей и 7 % известняка (по массе), необходимо для извлечения сухим щелочным способом глинозема из 120 т гидрагиллитового боксита, в составе которого 40 % Аl2О3 и 12 % SiO2 (по массе), сколько глинозема можно получить при этом, сели выход его составляет 85 %? Примечание: известняк взаимодействует с кремнеземом боксита с образованием двухкальциевого силиката.
10-3.Сколько глинозема, двухкальциевого силиката, соды и поташа можно получить при комплексной переработке 20 т нефелина путем спекания его с известняком, если в составе нефелинового концентрата 12 % Na2O; 7 % К2О; 29 % Аl2О3 и 43 % SiO2 (по массе)? Какая масса известняка потребуется для спекания с нефелином? Массовая доля СаСО3 в известняке 0.9. Производственные потери не учитывать.
10-4.Наиболее распространенные типы электролизеров, эксплуатировавшиеся на заводах СССР, обладали следующими технологическими характеристиками:
Сила тока, кА | 50 | 75 | 130 | 150 |
Суточная производительность по алюминию, кг | 340 | 515 | 900 | 1100 |
Определите расход глинозема, в составе которого 4.5 % (по массе) примесей для каждого типа, если массовая доля алюминия 99.65 %, а выход по току 90 %. Постройте график изменения удельной производительности агрегатов (кг/кА) в зависимости от силы тока.
10-5.На 1 т технического алюминия, в составе которого 0. 4 % примесей (по массе), расходуется 1.93 т глинозема, 22 кг свежего и 13 кг оборотного криолита, 27 кг AIF3 и 535 кг анодной массы, Определите: а) степень извлечения алюминия из ванны (с учетом металла разложившейся части электролита); б) объем газов, образующихся при окислении углерода анода, если в их состав входят 60 % СО2 и 40 % СО (по объему). Примечание: массовые доли углерода в аноде 95 % и примесей в глиноземе 1.5 %.
10-6.Определите коэффициент использования энергии для электролизера с самоспекающимися анодами при производстве алюминия, если рабочее напряжение 4.6 В, напряжение разложения 1.12 В, выход по току 80 %.
10-7.Определите массы (кг) хромистого железняка и боксита с массовой долей основного вещества 60 % необходимых для получения 312 кг хрома? Приведите необходимые уравнения химических реакций, укажите условия их протекания.
10-8.Вычислите массы (кг) халькопирита, необходимого для получения 128 кг электролитически чистой меди (массовая доля CuFeS2 в халькопирите 82 %), и 60 %-ного раствора серной кислоты, если её производственные потери 5 мас. %? Достаточно ли рассчитанного количества серной кислоты для обеспечения производства меди? Приведите все необходимые уравнения химических реакций, дайте расчет.
10-9.Смесь порошков алюминия и оксида никеля(II) подожгли с помощью магниевой ленты. В результате был получен сплав Ni –Al, содержащий 30 % алюминия. Вычислите массовую долю (в %) алюминия в исходной смеси.
10-10.Определите состав образца латуни, если при обработке 16.25 г его хлороводородной кислотой масса уменьшилась на 40 %, а при пропускании через полученный раствор сероводорода выпало 9.7 г белого осадка, растворимого в избытке хлороводородной кислоты. Остаток сплава при нагревании растворили в концентрированной серной кислоте, а при осторожном выпаривании данного раствора выпало 38.08 г голубых кристаллов.
10-11.Для полного разложения некоторого количества гидроксида алюминия потребовалось 76 кДж теплоты. Полученный оксид алюминия растворили в 400 г 8 %-ного раствора гидроксида натрия. Вычислите массовую долю образовавшейся при этом соли. Тепловой эффект реакции разложения гидроксида алюминия составляет 95 кДж/моль.
10-12. Смешали 440 г 20 %-ного раствора гидроксида натрия и 225.5 г 30 %-ного раствора хлорида алюминия. Рассчитайте массовые доли веществ в полученном растворе.
10-13.При обработке 31.5 г смеси алюминия с оксидом алюминия 20 %-ным раствором гидроксида натрия (плотность 1.2 г/мл) выделилось 20.16 л газа (н.у.). Определите состав смеси и объем раствора гидроксида натрия, израсходованный на растворение смеси.
10-14.Какое количество вещества металлического алюминия можно получить, подвергая электролизу расплав оксида алюминия в криолите, который содержит 500 кг Al2O3?
10-15. На разделение смеси металлов, состоящей из меди, железа и алюминия, потребовалось 13.33 г гидроксида натрия, 12.5 л хлора (н.у.), 343.6 мл 10 %-ного раствора соляной кислоты (плотность 1.10 г/мл). Определите массовую долю металлов в смеси.
10-16.При растворении в соляной кислоте смеси алюминия с неизвестным металлом массой 1.82 г, стоящим в ряду стандартных электродных потенциалов после водорода, выделился водород объемом 0.672 л. Чтобы окислить эту смесь, потребовался кислород объемом 0.56 л (н.у.). Определите, какой металл был взят, и массовые доли металлов в исходной смеси.
10-17.Смесь кремния, алюминия и железа массой 4.6 г обработали избытком 40 %-ного раствора гидроксида натрия (плотность 1.4 г/мл), что дало 3.733 л газа (н.у.). При обработке такой же массы смеси избытком раствора соляной кислоты выделилось 2.987 л газа (н.у.). Определите массовые доли компонентов в исходной смеси, а также объем израсходованного раствора гидроксида натрия.
10-18.При обработке сплава алюминия, магния и меди массой 16 г избытком 36.5 %-ного раствора соляной кислоты (плотность 1.10 г/мл) выделился газ объемом 18.84 л (н.у.). Фильтрат, полученный после отделения нерастворившегося вещества, обработали избытком 40 %-ного раствора гидроксида натрия (плотность 1.4 г/мл). Выпавший при этом осадок отделили, промыли дистиллированной водой и прокалили. Масса твёрдого остатка белого цвета составила 0.54 г. Определите массовые доли каждого металла в сплаве и объёмы растворов соляной кислоты и гидроксида натрия, израсходованных в ходе вышеописанных операций.
10-19.Составьте материальный баланс процесса спекания 1 т диаспорового боксита, содержащего 10 мас. % оксида кремния, с карбонатами натрия и кальция до дикальцийсиликата.
10-20.Определите практический расход электроэнергии на производство 1 т алюминия, если практическое напряжение электролиза равно 4.5 В, а выход металла по току составляет 90 %.
Производство чугуна
Производство чугуна – это первая стадия двухступенчатого процесса переработки железных руд в сталь. Чугун выплавляют из железорудного сырья в доменных печах, в которых за счет сгорания топлива создаются высокие температуры, обеспечивающие процессы восстановления оксидов железа руды, образования жидкого чугуна и отделения пустой породы в виде шлака. Подобный процесс получил название доменного процесса или доменной плавки.
В качестве сырья в доменном процессе используют специально подготовленные железные руды (агломерат, окатыши), твердое, жидкое и газообразное топливо, флюсы, марганцевые руды и воздух. Смесь твердых компонентов сырья, загружаемого в доменную печь, называется шихтой.
Топливо обеспечивает создание в печи высоких температур, необходимых для протекания реакций восстановления оксидов железа, образование оксида углерода(II) и водорода, являющихся газообразными восстановителями, диффузию углерода в восстановленное железо и образование чугуна. В качестве топлива используется преимущественно каменноугольный кокс и, для снижения его расхода, добавки газообразного (природный и коксовый газы), жидкого (мазут) и аэрозольного (угольная пыль) топлив. Доменный кокс должен обладать высокой прочностью, сопротивлением к истиранию, не спекаться в условиях доменного процесса и содержать минимальные количества золы, серы и фосфора. Так, например, повышение содержания серы в коксе на 1 % увеличивает расход кокса на 10 % и снижает производительность печи на 20 %. Обычно, в металлургическом коксе содержится: золы 8-12 %, серы 0.5-2.0 % и фосфора до 0.5 %.
Флюсы вводят в шихту для образования с пустой породой руды и золой кокса, содержащих тугоплавкие оксиды кремния, алюминия и кальция, легкоплавкого жидкотекучего и легко отделяемого от чугуна шлака. В качестве флюсов используют не содержащие серы и фосфора карбонат кальция и доломит СаСО3·МgСО3. В современном процессе флюсы вводят не непосредственно в доменную печь, а в шихту при ее подготовке, образуя так называемый офлюсованный железорудный материал.
Марганцевые руды, содержащие оксиды марганца MnО2 и Мn2О3 или карбонат марганца МnСОЗ, используются при выплавке ферромарганца и высокомарганцовистых (с содержанием около1 %) сортов литейного и передельного чугунов.
Воздух, обогащенный кислородом, обеспечивает горение топлива и образование газообразных восстановителей.
Железные руды перед доменной плавкой проходят специальную подготовку. Цель подготовки – повышение содержания железа в железорудных материалах, обеспечение необходимых дисперсности и газопроницаемости их и, как следствие, увеличение производительности доменной печи, снижение расхода кокса и флюсов. Основными операциями подготовки являются обогащенные руды и окускование рудной мелочи. Перед этим сырье подвергают обычным операциям дробления, тонкого измельчения и классификации (грохочения).
Метод обогащения зависит от состава руды, гидрофобности пустой породы и формы нахождения железа в руде. В зависимости от этого для обогащения используют промывку (отмывание пустой, породы), флотацию, гравитационную и магнитную сепарацию. При этом оптимальную степень обогащения выбирают из технико-экономических соображений. По мере повышения содержания железа в концентрате возрастают затраты на обогащение, но сокращаются затраты на доменный процесс.
Наиболее распространенный метод магнитной сепарации, которым получают до 90 % всего железорудного концентрата, основан на различной магнитной проницаемости минералов руды и пригоден для обогащения магнитных железняков. Магнитная сепарация может быть сухой, когда руду загружают на барабаны магнитных сепараторов (рис. 10.2), и мокрой, когда рудную пульпу подают в ванну под вращающийся барабан с электромагнитом, извлекающим из пульпы ферромагнитный минерал. Производительность магнитных сепараторов составляет более 400 т/ч при степени обогащения до 0.75 долей ед.
Рис. 10.2. Схема магнитного ленточного сепаратора:
1 – снимающая лента, 2 –питающая лента, 3 – бункер шихты, 4 – бункер магнитного концентрата, 5 – бункер пустой породы, 6 – магниты.
Для обогащения методом магнитной сепарации немагнитных бурых и красных железняков их предварительно подвергают магнетизирующему (восстановительному) обжигу при 600800 оС в восстановительной атмосфере, образующейся при неполном сгорании топлива:
3 Fе2О3 + СО ↔ 2 FеЗО4 + СО2 3 Fе2О3 + Н2 ↔ 2 FеЗО4 + Н2О
Магнетизирующий обжиг приводит к повышению содержания железа в концентрате и по существу является химическим обогащением.
Полученные в результате обогащения концентраты усредняются по составу, после чего поступают на операцию окускования.
Полученный обогащением рудный концентрат мелкодисперсен и не может непосредственно использоваться для доменной плавки. Поэтому он подвергается операции окускования. Окускованием называется процесс превращения мелкого железорудного материала в кусковой материал необходимых размеров, которые обеспечивают стабильный и высокопроизводительный процесс доменной плавки. В черной металлургии используют два способа окускования: агломерацию и окомкование (окатывание).
Агломерацией называется способ окускования рудного концентрата путем спекания до частиц нужного размера за счет сжигания твердого топлива в слое концентрата или подвода тепла извне, с одновременным удалением из него серы, мышьяка и пустой породы (оксида кремния). В металлургическую практику метод агломерации был введен в 1911 году и стал широко применяться с 30-х годов ХХ столетия.
Агломерацию осуществляют путем просасывания воздуха через слой шихты, состоящей из рудного концентрата (4050 %), известняка (15-20 %), возврата агломерата (20-30 %), коксовой мелочи или коксика (4-6 %) и воды (6-9 %), при температуре около 1400 оС. Процесс агломерации протекает через три последовательных стадии (рис.10.3):
- подготовительная, начинающаяся после зажигания шихты (нагрев шихты, испарение влаги, воспламенение топлива);
- стадия сгорания, сопровождающаяся опусканием зоны горения вниз (сгорание топлива с образованием оксида углерода(II), образование жидкой фазы, частичное восстановление оксидов железа);
- стадия охлаждения образовавшегося агломерата холодным воздухом.
Рис. 10.3. Схема агломерационного процесса:
а – подготовительная стадия, б – стадия сгорания, в – стадия охлаждения
При агломерации в шихте протекают процессы:
- неполного окисления топлива и восстановления оксидов железа:
2 С + О2 = 2 СО
3 Fе2О3 + СО = 2 Fе3О4 + СО2
Fе3О4 + СО = 3 FeO + СО2
- термической диссоциации известняка и образования силикатов (шлак):
СаСО3 = СаО + СО2
2 СаО + SiO2 = 2 СаО·SiO2
2 FeO + SiO2 = 2 FeO·SiO2
- диссоциации дисульфида и обжига сульфида железа:
2 FeS2 = 2 FeS + S2 4 FeS + 7 O2 = 2 Fе2O3 + 4 SO2
В результате агломерации из концентрата удаляется до 95 % серы и до 20 % мышьяка, значительное количество оксида кремния и повышается до 65 % содержание железа. Применение для доменной плавки подобного офлюсованного агломерата исключает процесс диссоциации флюсов, вводимых в доменную печь, сокращая за счет этого на 10-12 % расход топлива; улучшает восстанавливаемость рудного сырья вследствие образования силикатов и освобождения железа из его соединений; уменьшает объем шихты, загружаемой в доменную печь; улучшает условия шлакообразования и отделения шлака от металла. В результате использования при доменной плавке офлюсованного агломерата производительность доменной печи возрастает на 10-12 %.
Процесс спекания шихты происходит на агломерационных машинах. Наиболее распространены машины непрерывного действия ленточного типа с поверхностью спекания до 800 м2. Машина АКМ-800 этого типа имеет длину 102 м, ширину 8 м, что при скорости движения ленты 12 м/мин. дает производительность 30000 т/сут (рис. 10.4).
Рис. 10.4. Технологическая схема агломерации концентрата:
1 – бункер, 2 – транспортер, 3 – барабанный смеситель, 4 – агломерационная машина, 5 - барабанный окомковыватель, 6 – отсасывающий вентилятор, 7 – зажигатлельный горн, 8 – слой шихты, 9 – грохот.
Окомкованием (окатыванием) называется способ окускования тонко измельченного рудного концентрата путем превращения его в комки (окатыши) с последующим упрочняющим обжигом. Производство окатышей в промышленных масштабах было начато в США в 1955 году, а в нашей стране в 1964 году. Окатыши используют как сырье доменной плавки (до 20 % состава железорудной части шихты) и в качестве полупродукта во внедоменном производстве стали.
Окомкование концентрата осуществляется в грануляторах барабанного или тарельчатого типа. При этом в шихту добавляется около 1.5 % мелкодисперсной глины (бентонита) в качестве связующего материала и известняк, если изготавливаются офлюсованные окатыши. Производительность грануляторов составляет 125-150 т/сут. при диаметре окатышей 67 мм. Для обжига окатышей применяются ленточные обжиговые машины с площадью спекания до 500 м2 и производительностью 2500-9000 т/сут. При обжиге сырые окатыши последовательно проходят зоны сушки при 250-400 оС, обжига при 1200-1300 оС, где обогреваются продуктами сгорания газа или мазута, просасываемыми через решетку и охлаждения холодным воздухом (рис. 10.5).
Целью обжига окатышей является упрочнение их до такого состояния, при котором они могут выдерживать без значительных разрушений транспортировку, перегрузки и процесс доменной плавки. При этом, в отличие от агломерации, при обжиге окатышей не происходит спекания материалов шихты. Обычно окомкованию подвергают концентраты магнетита, поэтому при обжиге происходит частичное окисление его до оксида железа(III), который образует в офлюсованных окатышах легкоплавкие ферриты кальция СаО·Fе2О3 и 2СаО·Fе2О3, выполняющие роль шлаковой связки:
4 FеЗО4 + О2 = 6 Fе2О3,
Рис. 10.5. Технологическая схема изготовления окатышей:
1 – бункера компонентов шихты, 2 – сборный транспортер, 3 – смесительный барабан, 4 – бункер бентонита, 5 – тарельчатый гранулятор, 6 – обжиговая машина, 7 – вентиляторы, 8 – грохот,
9 – транспортер шихты.
Содержание железа в окатышах составляет обычно 80-90 %. В большинстве случаев для доменной плавки используют смесь агломерата и окатышей в отношении 2:1.
Процесс доменной плавки происходит в плавильных агрегатах непрерывного действия шахтного типа – доменных печах, представляющих реакторы идеального вытеснения РИВ-Н. В них непрерывно движутся навстречу друг другу два материальных потока: сверху вниз твердая шихта и снизу вверх газообразные восстановители, образующиеся в результате горения топлива и взаимодействия продуктов горения с компонентами шихты. Подобный режим противотока создает постоянство движущей силы и скорости процесса восстановления и обеспечивает стационарность режима работы доменной печи.
Профиль плавильного пространства печи выбран таким образом, чтобы обеспечить равномерное опускание шихты вследствие горения кокса, плавления материалов шихты и периодического выпуска чугуна и шлака, равномерное распределение газового потока по сечению печи и максимально интенсивное протекание процессов восстановления руды, образования и разделения чугуна и шлака. В соответствии с этим в плавильном пространстве печи различают следующие части: колошник, шахту, распар, заплечики и горн (рис. 10.6).
Рис. 10.6. Профиль доменной печи
При установившемся режиме работы печи в ней создается и поддерживается определенный температурный режим и протекают химические и физико-химические процессы, которые могут быть сведены к нескольким группам (они приведены ниже, их номера отмечены на схеме печи в тех зонах ее, в которых они протекают).
1. Подготовительные процессы. К подготовительным процессам, протекающим в интервале температур 100-400 оС, относятся выделение гигроскопической и гидратной воды и летучих веществ из твердого топлива.
2. Образование газообразных восстановителей. Газообразные восстановители образуются в результате полного сгорания углерода кокса и природного газа при температурах 1800-1900 оС и последующего восстановления продуктов окисления при контакте с раскаленным коксом:
С + О2 = СО2 СН4 + 2О2 = 2Н2О;
СО2 + C = 2СО Н2О + C = СО + Н2
Суммируя, соответственно, получаем уравнения образования газообразных восстановителей:
2 С + О2 = 2 СО – ΔН 2 СН4 + О2 = 2 СО + 4 Н2 – ΔН
3. Восстановление оксидов железа. Восстановление оксидов железа начинается при температуре выше 570 оС и в соответствии с теорией А.А. Байкова протекает ступенчато от высших оксидов к низшим: Fе2О3 → Fе3О4 → FeO → Fe.
Заканчивается восстановление при температуре 1200 оС. При доменной плавке прямое восстановление оксидов железа углеродом кокса играет незначительную роль и возможно лишь при высоких температурах. В доменной печи преобладает процесс косвенного восстановления их оксидом углерода(II) и водородом, описываемый уравнениями:
3 Fе2О3 + СО = 2 Fе3О4+ СО2 – ΔН; ΔН = 53.74 кДж (а)
Fе3О4 + СО ↔ 3 FeO + СО2 + ΔН; ΔН = 36.68 кДж (б)
FeO + СО ↔ Fe + СО2 – ΔН; ΔН = 16.06 кДж (в)
3 Fе2О3 + Н2 ↔ 2 Fе3О4 + Н2О – ΔН; ΔН = 12.89 кДж (г)
Fе3О4 + Н2 ↔ 3 FeO + Н2О + ΔН; ΔН = 77.54 кДж (д)
FeO + Н2 ↔ Fe + Н2О + ΔН; ΔН = 24.79 кДж (е)
Из этих реакций – (а), (в) и (г) протекают с выделением тепла, реакции (б), (д) и (е) – с поглощением тепла. Расчет изобарно-изотермических потенциалов реакций (а), (б) и (в) по значениям ΔG оксидов (табл.10.1) дает для них значения, соответственно, -66, -54 и -6 кДж, что подтверждает справедливость теории ступенчатого восстановления оксидов железа.
Таблица 10.1
Изобарно-изотермические потенциалы оксидов
Оксид | FeO | Fе2О3 | Fе3О4 | СО | СО2 | MnO | SiO2 |
ΔGo298, кДж/моль | -252 | -744 | -1020 | -137 | -395 | -364 | -851 |
Каждой из приведенных выше реакций соответствует равновесный состав газовой фазы, характеризуемый отношением CO/CО2 и зависящий от природы оксида железа (его термической стабильности) и температуры. На рис. 10.7 представлены кривые равновесного состава газовой фазы над твердой фазой в функции температуры для реакций (а), (б) и (в). Так как реакция (а) практически необратима, кривая для нее приближается к оси абсцисс; следовательно, даже небольшой концентрации оксида углерода(II) в газовой фазе достаточно для восстановления Fе2О3 до Fе3О4. Реакция (в) является экзотермической, поэтому равновесная концентрация СО для нее возрастает при повышении температуры, в то время как для эндотермической реакции (б) она падает.
Рис. 10.7. Равновесный состав газовой фазы реакций восстановления оксидов железа оксидом углерода(II):
1, 2, 3 – кривые равновесия для реакций а, б, в, соответственно, 4- кривая равновесного состава для реакции СО2 + С = 2 СО, 5 – кривая, отвечающая составу реального газа в печи
Из рис. 10.7 следует, что если оксиды железа находятся в равновесии с газовой фазой, содержащей СО и СО2, то в поле диаграммы ниже кривой 1 устойчив оксид Fе2О3 в поле между кривыми 1 и 2 оксид FеЗО4, в поле между кривыми 2 и 3 оксид FeO и в поле выше кривой 3 металлическое железо. Если в системе находится в избытке углерод, то состав газа будет определяться кривой 4. По условиям термодинамики восстановление оксида FеЗО4 в оксид FeO может начаться при температуре, отвечающей точке А, а оксида FeO в железо – в точке В. Фактический состав газовой фазы в печи таков (кривая 5), что только при высоких температурах достигаются равновесные концентрации СО, отвечающие реакции СО2 + С = 2СО + ΔН. При низких температурах фактическое содержание СО выше равновесного и по отношению к железу в печи всегда поддерживается восстановительная атмосфера (27-30 % СО в газе).
Суммируя реакции а-в, получаем уравнение восстановления оксида железа(III) до металлического железа, из которого следует, что процесс в целом является экзотермическим:
Fе2О3 + 3 СО ↔ 2 Fe + 3 СО2 – ΔН, ΔН = 25.58 кДж,
Из приведенных выше реакций образования газообразных восстановителей следует, что этому способствует увеличение концентрации кислорода в подаваемом в печь воздухе и повышение давления, что и используется на практике.
При температуре выше 900 оС происходит интенсивное восстановление оксида углерода(IV) на поверхности раскаленного кокса и процесс может быть описан уравнениями:
FeO + СО = Fe + СО2 - ΔН С + СО2 = 2 СО + ΔН
Суммируя их, получаем:
FeO + С = Fe + CO + ΔН, ΔН = 153 кДж,
то есть процесс восстановления оксида железа FeO можно рассматривать как протекающий в твердой фазе, как прямое восстановление. Этой реакции на рис. 10.7 отвечает заштрихованная часть поля, следовательно, доля прямого восстановления растет с увеличением температуры доменного процесса.
4. Науглероживание железа и получение чугуна. Науглероживание губчатого металлического железа происходит при его контакте с доменными газами, содержащими оксид углерода(II) и раскаленным коксом. Процесс науглероживания начинается в твердой фазе при температуре около 600 oС на поверхности свежевосстановленного железа, катализирующего реакцию распада оксида углерода(II). При этом образуется высокоактивный сажистый углерод, реагирующий с железом с образованием карбида железа:
2 СО = СО2 + С 3 Fe + С = Fе3С
или 3 Fe + 2 СО = Fе3С + СО2 – ΔН, ΔН = 180.5 кДж.
При переходе металла в жидкое состояние науглероживание становится более интенсивным и протекает уже непосредственно за счет взаимодействия железа с раскаленным коксом с последующим растворением карбида железа в железе. По мере науглероживания температура плавления железа понижается с 1539 оС (чистое железо) до 1135 оС (сплав, содержащий 4.3 % углерода).
5. Восстановление примесей. В состав металлизированных материалов шихты (агломерат, окатыши) входят помимо оксидов железа оксиды различных элементов. По возрастанию сродства к кислороду и термодинамической прочности их оксидов, они располагаются в ряд: Cu, As, Ni, Р, Zn, Мn, V, Сr, Si, Ti, Al, Mg, Са. Степень восстановления этих элементов в доменной печи соответствует их положению в этом ряду. Медь, мышьяк, фосфор подобно железу почти полностью восстанавливаются и переходят в чугун; цинк, хотя и восстанавливается, но возгоняется; ванадий и хром восстанавливаются на 70-90 %. Алюминий, кальций и магний при доменной плавке не восстанавливаются.
Важнейшие элементы в шихте – марганец и кремний, содержащиеся в виде различных силикатов в составе агломерата, золы, кокса и оксидов марганца в составе марганцевых руд. Кремний и марганец (из его низшего оксида) восстанавливаются только по реакциям прямого восстановления при температуре 1150-1300 оС.
SiО2 + 2 С ↔ Si + 2 СО + ΔН, ΔН = 635.1 кДж
МnО + С ↔ Мn + СО + ΔН, ΔН = 288.3 кДж
В отличие от оксида марганца(II) высшие оксиды его легко восстанавливаются в газовой фазе оксидом углерода(II) уже при 200-500 oС в последовательности, аналогичной последовательности восстановления оксидов железа: МnО2 → Mn2O3 → Mn3O4 → MnO.
Расчет изобарно-изотермического потенциала реакций восстановления кремния и марганца по значениям ΔG соответствующих оксидов (табл. 10.1) показывает, что они составляют, соответственно, +61 и -31 кДж, а для реакции восстановления железа из FeO + 109 кДж. Поэтому, прямому восстановлению подвергаются, в первую очередь, кремний и марганец.
6. Образование шлака. При доменной плавке одновременно с образованием чугуна образуется шлак в виде различных силикатов за счет взаимодействия невосстановленных основных (СаО, MgO, МnО и FeO) и кислотных (Аl2О3 и SiO2) оксидов. По мере перемещения в зону высоких температур (выше 1400 oС) шлак обогащается оксидами кальция, магния, алюминия и кремния за счет восстановления оксидов железа и марганца и становится жидкотекучим. Состав доменного шлака: 85-95 % СаО, SiO2, Аl2О3; 2-10 % MgO; 0.2-0.6 % FеО; 0.3-3.0 % МnО; 1.5-2.5 % серы в виде СаS.
7. Реакции с участием серы и фосфора. Сера и фосфор вносятся в доменную печь с материалами шихты: сера в виде органических соединений, сульфидов и дисульфидов железа и других металлов, а также сульфатов с коксом и агломератом, фосфор – в виде тетракальцийфосфата с пустой породой и флюсами. Оба элемента ухудшают качество как чугуна, так и выплавляемой из него стали, поэтому содержание их в металле должно быть ограничено.
Восстановление фосфора в присутствии оксида кремния шихты протекает при температуре выше 1100 оС по реакциям:
4 СаО·Р2О5 + 4 SiO2 = 4СаО· SiO2 + Р2О5
Р2О5 + 5 С = 2 Р + 5 СО
Восстановленный фосфор растворяется в железе и полностью переходит в чугун. Поэтому получить металл с низким содержанием фосфора можно только на основе низкофосфористой шихты.
Сера из шихты в процессе плавки частично, на 10-20 %, переходит в газовую фазу в виде оксида серы(IV), сероводорода и др. соединений, но большая часть ее остается в шихте в виде сульфидов железа FeS, марганца MnS и кальция СаS. Из них сульфиды железа и марганца хорошо растворимы в металле, а сульфид кальция – в шлаке. Поэтому для удаления серы из чугуна необходимо перевести сульфиды железа и марганца в сульфид кальция, который не растворяется в чугуне.
Для этого в печи должны быть созданы условия получения жидкого хорошо нагретого шлака основного характера с высоким содержанием оксида кальция. При взаимодействии такого шлака с сульфидами железа и марганца протекают обменные реакции:
FeS + СаО = FeO + CaS
МnS + СаО = МnО + CaS
Образовавшиеся оксиды металлов восстанавливаются углеродом кокса до свободных металлов, поэтому процесс обессеривания чугуна может быть выражен суммарным уравнением, например, для сульфида железа:
FeS + СаО + С = Fe + СО + CaS (в шлак)
Организация технологического процесса выплавки чугуна из руды должна предусматривать:
- непрерывность процесса плавки при периодичности операций загрузки материалов шихты, выпуска чугуна и шлака;
- осуществление противотока реагентов (шихты и газообразных компонентов сырья);
- использование теплоты продуктов процесса;
- герметизацию оборудования и возможность непрерывного отбора доменного газа.
В соответствии с этим технологическая схема доменного производства (рис. 10.8) включает:
- рудный двор и бункерную эстакаду для хранения, дозировки и загрузки в скипы (тележки) материалов шихты;
- доменную печь;
- систему подогрева и подачи воздушного дутья;
- устройство для уборки и транспортировки жидких продуктов плавки (чугуна и шлака);
- систему очистки доменного газа.
Рис. 10.8. Технологическая схема доменного производства
Агломерат и кокс загружаются на рудном дворе в бункера 1 и 2, из которых они поступают в скипы подъемника 3. Скипы с материалами шихты в определенной последовательности например, АККАК (где А – скип с агломератом, К – скип с коксом), подаются в загрузочное устройство (засыпной аппарат) 5 доменной печи 4. В нижнюю часть печи через фурмы с помощью воздуходувки из каупера (воздухонагревателя) 9 подается воздух, нагретый до 1200-1300 оС. Образующиеся в процессе плавки жидкие чугун и шлак периодически выпускаются из нижней части печи через специальные отверстия – летки. Выпускаемый чугун собирается в ковши емкостью 90-140 т, или в миксеры, футерованные огнеупорным материалом емкостью до 420 т, установленные на железнодорожных платформах. Шлак отводится по желобу в шлаковозы и направляется на грануляцию. Доменный гaз, выходящий из колошника печи, очищается от пыли в пылеуловителе 6, скруббере 7, орошаемом водой, и окончательно в мокром электрофильтре 8. Очищенный и охлажденный до 40 оС газ направляется в каупер 10, где сжигается в токе воздуха и разогревает насадку. Кауперы работают, таким образом, попеременно: один на подогрев воздушного дутья 9, другой – на разогрев насадки 10, что обеспечивает бесперебойность подачи подогретого воздуха в доменную печь. Газы, перед сбрасыванием в атмосферу проходят дымовую трубу 11.
Основными аппаратами доменного производства является доменная печь и каупер.
Доменная печь 4 имеет форму башни из огнеупорного кирпича, заключенную снаружи в металлический сварной кожух. Изнутри печь имеет огнеупорную футеровку. Для уменьшения выгорания кладки она снабжена специальными холодильниками. Масса печи достигает 30 000 тонн, поэтому она устанавливается на мощном фундаменте. Размеры печи зависят от ее полезного объема, который определяется ее полезной высотой (от верхнего уровня шихты до чугунной летки). Размеры остальных элементов печи зависят от ее полезного объема. Так, для наиболее мощных современных печей полезным объемом 5000 м3 полезная высота равна 32.2 м, высота шахты 19.5 м, диаметр и высота горна 14.9 и 4.5 м, соответственно. Материалы шихты подаются в колошник через загрузочное устройство, обеспечивающее равномерное распределение их по сечению печи и герметичность в момент загрузки. В горн печи через равномерно расположенные по его окружности отверстия (от 24 до 40) с помощью фурм подается из общего кольцевого трубопровода подогретый воздух (воздушное дутье) под давлением от 0.1-0.35 МПа. Для выпуска чугуна и шлака в горне печи имеются отверстия – летки (от 10 до 18), забиваемые огнеупорной глиной.
Каупер 9, 10 представляет регенератор периодического действия, в котором используется теплота сгорания доменного или природного газа. Он выполнен в виде металлического цилиндра высотой до 50 м и диаметром 6-9 м общим объемом до 4000 м3, выложенного внутри огнеупорным материалом. Внутренне пространство каупера разделено на две части: камеру сгорания и камеру с насадкой из огнеупорного кирпича, снабженной сквозными каналами. В камере сгорания сжигается доменный газ, к которому для увеличения теплоты сгорания добавляется природный газ, и продукты горения обогревают насадку во второй камере. По достижении 1200-1300 оС дымоход перекрывается и через нагретую насадку пропускается холодный воздух, а обогревающий газ переключается на другой каупер.
Доменная печь представляет весьма мощный и высокопроизводительный агрегат, в котором расходуется огромное количество шихтовых материалов воздушного и газового дутья. Так, печь полезным объемом 5000 м3 потребляет в сутки 23 000 т шихты, 18 000 т воздушного дутья, 1700 т природного газа и выдает 12 000 т чугуна, 4000 т шлака и 27 000 т доменного (колошникового) газа. Поэтому вопросы экономики доменного производства имеют первостепенное значение.
Основные показатели работы доменной печи – это производительность в единицу времени и расход кокса на единицу массы выплавляемого чугуна (УРК). Для оценки производительности печей различного объема применяют относительный показатель - коэффициент использования полезного объема печи (КИПО).
Величина УРК не только влияет на производительность печи, но и показывает эффективность использования химической и тепловой энергии топлива в плавильном пространстве печи. УРК отражает уровень техники и технологии доменной плавки и степень подготовки сырья к ней.
Себестоимость чугуна складывается из затрат на офлюсованную металлическую шихту (агломерат, окатыши), на технологическое топливо и расходов по переделу, включая общезаводские расходы. Первая и вторая группы затрат не зависят от масштабов производства и определяются стоимостью и качеством материалов шихты и уровнем технологии. В среднем они составляют до 90 % себестоимости чугуна. Расходы по переделу составляют около 10 % и являются затратами на переработку шихты в чугун. Их величина зависит от масштабов производства, уровня техники и технологии, стоимости энергии, зарплаты и т.п. Среди этих затрат основное место занимают энергетические, связанные с использованием в доменном процессе пара, воды, электроэнергии, дутья, сжатого воздуха и др. (табл. 10.2).
Таблица 10.2
Структура себестоимости чугуна
Статья | Доля в себестоимости, % |
Металлическое сырье | 30-40 |
Кокс | 40-50 |
Природный газ | 2-4 |
Расходы по переделу | 13-18 |
Заработная плата | 0.3-0.7 |
Доменный процесс организуется для производства целевого продукта чугуна. Однако, помимо чугуна, конечными продуктами доменной плавки являются также шлак и доменный газ.
Из всего выплавляемого чугуна до 90 % его составляет чугун передельный, используемый для производства стали и переплавки в литейный чугун и только 10-15 % составляет серый литейный чугун.
Доменный шлак - побочный продукт плавки. Выход его зависит от состава шихты и составляет 0.3-0.6 т на тонну чугуна. Шлак используют в качестве сырья в производстве цемента, вяжущих веществ, шлаковой пемзы и ваты, ситаллов, материалов для дорожного покрытия. В эти продукты перерабатывается до 75 % годового количества шлака.
Доменный (колошниковый) газ содержит до 60 % азота, 1018 % оксида углерода(IV), 24-32 % оксида углерода(II) и незначительные количества метана и водорода. Теплота сгорания доменного газа составляет около 4000 кДж/м3. Он используется в качестве топлива для обогрева кауперов, в прокатных цехах для нагрева стальных слитков и др.
Под интенсификацией понимают методы и приемы ускорения протекающих в доменной печи процессов с целью повышения ее производительности и улучшения показателей работы. К ним относят:
1. Применение сырья улучшенного качества, в том числе, офлюсованных железорудных материалов с повышенным содержанием железа и малосернистого кокса. Так, повышение содержания железа в агломерате на 1 % увеличивает производительность печи на 2.5 % при одновременном снижении УРК на 2 %; уменьшение массы известняка на 0.1 т/т чугуна при замене обычного агломерата на офлюсованный, снижает УРК на 3 %, а понижение содержания серы в коксе на 1 %, соответственно, на 2.5 %.
2. Повышение температуры воздушного дутья увеличивает поступление в печь физического тепла, что позволяет снизить расход кокса и, соответственно, вносимой с ним золы, и расход флюсов на ее связывание. Так, при повышении температуры дутья от 1000 до 1200 оС УРК снижается на 5 %.
3. Обогащение воздушного дутья кислородом увеличивает скорость горения топлива и последующих процессов образования восстановителей и восстановления оксидов железа, уменьшает количество тепла, выносимого из печи с балластным азотом воздуха. Так, при повышении содержания кислорода в дутье с 21 до 30 % об. УРК снижается на 9 % , а производительность печи увеличивается на 10 %. При более высоком содержании кислорода в печи развиваются излишне высокие температуры, что может вызвать подвисание шихты и замедление плавки.
4. Повышение давление газов в печи увеличивает количество воздуха, подаваемого в печь и форсирует ее работу. При этом, за счет лучшего использования газообразных восстановителей снижается расход топлива и вынос пыли с газом. Так, применение давления на колошнике снижает УРК на 3-7 % и повышает производительность печи на 4-15 %.
5. Использование природного газа. Стоимость кокса составляет до 50 % себестоимости выплавляемого чугуна, к тому же запасы коксующихся углей ограничены. Замена части кокса природным газом обогащает газовую фазу восстановителями, в том числе, водородом, снижает температуру в горне при использовании обогащенного кислородом дутья, повышает удельный вес процессов косвенного восстановления оксидов железа и уменьшает количество образующейся золы и, следовательно, шлака. Применение природного газа повышает производительность печи на 15-20 %.
КОНТРОЛЬНЫЕ ВОПРОСЫ К ТЕМЕ 10.2
10-1.Назовите основные компоненты сырья в доменном процессе и укажите их назначение.
10-2.Какие руды могут подвергаться обогащению методом магнитной сепарации? Что такое агломерация и окомкование рудного сырья?
10-3.Какие процессы и на каком уровне протекают в доменной печи? Чем объясняется последовательность восстановления оксидов железа в доменном процессе? 3а счет каких процессов образуется доменный шлак при выплавке чугуна?
10-4.С какой целью подогревается воздух перед подачей в доменную печь? Для чего в доменную печь вводят природный газ или жидкое топливо?
10-5.Перечислите технико-экономические показатели работы доменной печи и укажите пути их улучшения.
ЗАДАЧИ К ТЕМЕ 10.2
10-1.Составьте графическую схему перераспределения углерода в доменом процессе с учетом потерь железа. В этом процессе углерод кокса перераспределяется между чугуном и доменным газом. Из руды в чугун переходит η < 1.0 мас. долей железа.
10-2. Сколько чугуна, в составе которого 92 % железа (по массе), можно получить из окатышей, которые производит в течение 30 дней установка мощностью 2500 т/сут. Массовая доля Fe3O4 в окатышах 85 %, а в чугун переходит 98 % железа (по массе).
10-3. Используя данные диаграммы состояния железо-углерод, определите структурные изменения в сплаве при 1173 К и снижении массовой доли углерода с 5 до 0.5 %. Что обозначают эти компоненты структуры? Сколько цементита содержится в 1 т сплава, в котором обнаружено 2.6 % углерода (по массе), причем 3/4 его связано химически?
10-4. Вычислите расход руды для выплавки 1 т чугуна, массовая доля железа в котором 93 % с использованием: а) магнетита, в котором 25 % пустой породы; б) гематита, в котором 27 % пустой породы; в) лимонита 2Fе2О3 · ЗН2О, в котором 30 % пустой породы; г) гетита 2Fе2О3 · 2Н2О, в котором 29 % пустой породы; д) сидерита FеСО3, в котором 32 % пустой породы. При расчетах принять во внимание, что во всех случаях из руды в чугун переходит 97 мас. % железа.
10-5. Рассчитайте 30-суточную производительность агломерационной машины в расчете на 1 м2 площади спекания, если в сутки машина производит 3600 т агломерата, а площадь аглоленты 252 м2.
10-6. Сколько чугуна, в составе которого 92 мас. % железа, можно получить из окатышей, которые производит в течение 30 дней установка мощностью 2500 т/сут. Массовая доля Fе3О4 в окатышах 85 %, а в чугун переходит 98 % железа (по массе).
10-7. Домна с полезным объемом 2000 мЗ расходует на 1 т чугуна 395 кг кокса, 140 мЗ природного газа, 161 м3 кислорода, а домна объемом 5000 м3 соответственно 374 кг кокса, 127 мЗ природного газа, 146 м3 кислорода. Определите сокращение удельных затрат сырья и прирост выплавки чугуна в массовых долях, если первая печь производит чугуна 1.6 млн. т/г, а вторая – 4.6 млн. т/г.
10-8. Массовые доли СаО и SiO2 в офлюсованном агломерате соответственно равны 0.1 и 0.12. Сколько известняка необходимо добавить к 1 т такого агломерата, чтобы связать остаточный кремнезем в моносиликат кальция? Массовая доля СаСО3 в известняке 90 %.
10-9. Диаметр колошника домны 8 м, распара 12 м и дна горна 10 м. Высота от верхнего уровня засыпки до распара 20 м, а от распара до дна горна 5 м. В сутки из печи производят 6 выпусков чугуна, по 600 т каждый. Определите: а) полезный объем печи; б) КИПО; в) интенсивность домны (т/м3).
10-10. Массовая доля углерода в коксе 90 %. Какой объем оксида углерода(II) (н.у.) вступит в реакцию полного восстановления 3200 т гематита? Сколько кокса необходимо для образования такого объема газообразного восстановителя?
10-12. На металлургическом заводе первоначальный КИПО трех доменных печей объемом 1300 м3, 1400 м3 и 1719 м3 равнялся 0.7. Сколько чугуна выплавил завод за последующий год, если перед этим удалось увеличить массовую долю агломерата в шихте с 70 до 80 %; снизить массовую долю в коксе серы на 0.2%, а золы на 2 %. Примечание: 1) снижение массовой доли серы в коксе на 0.1 % увеличивает производительность печи на 7 %; снижение доли золы на 1 % – соответственно на 1.5 %, а увеличение доли агломерата на 1 % увеличивает производительность на 1 %; 2) первая и вторая печь останавливались на 30 суточный капитальный ремонт, кроме того, в течение года каждая печь на третьи сутки останавливалась на планово-предупредительный ремонт.
10-13. Доменный газ состава (об. %): оксид углерода(II) - 28; водород - 2.7; азот - 58.5; оксид углерода(IV) -10.5; метан - 0.3 - сгорает в воздухонагревателе при избытке воздуха 20 %. Определите расход воздуха на сжигание 10 000 м3 доменного газа и состав газа, выходящего из воздухонагревателя.
10-14. Определите интенсивность плавки домны с полезным объемом 2500 м3 и производительностью 2.19 млн. т/г, если известно, что расход кокса на 1 т чугуна составил 500 кг, а углеродсодержащих добавок 417 кг. Массовая доля углерода в коксе и в добавках составляет соответственно 0.9 и 0.1.
10-15. В доменном цехе старого металлургического завода у печей с общим объемом 2200 м3 трудилось 980 человек. После реконструкции объем печей возрос до 2600 м3, а число работников уменьшилось на 75 человек. Определите суточный прирост выплавки чугуна на 1 работника, если в результате реконструкции КИПО в среднем снизился с 0.8 до 0.6.
10-16. Первоначальный расход кокса в доменной плавке составлял 600 кг/т чугуна, при замене сырой руды на офлюсованный агломерат расход кокса сократили на 15 %. Еще на 8 % сократился расход кокса при повышении концентрации металла в шихте. Определите первоначальный и конечный среднесуточный расход кокса для домны с объемом 2700 м3, если КИПО1 = 0.58, а КИПО2 = 0.52.
10-17. Какая масса красного железняка, содержащего 78 % оксида железа(III) (остальное – посторонние примеси), потребуется для получения 1.5 т сплава с массовой долей железа 95 %?
10-18. Для восстановления 108 г оксида металла использовали смесь оксида углерода(II) и водорода. При этом образовалось 18 г воды и 11.2 л газа (н.у.). Раствор, полученный при растворении продукта реакции в концентрированной серной кислоте при нагревании, давал синее окрашивание с желтой кровяной солью. Определите состав и объемные доли газов в исходной смеси.
10-19. Определите массу известняка с содержанием 0.9 мас. долей карбоната кальция, добавляемого к 1000 т агломерата, содержащего 0.1 мас. долей оксида кальция и 0.12 мас. долей оксида кремния для связывания последнего до монокальцийсиликата CaО∙SiO2.
10-20. Определите объем доменного газа, выделяемый из доменной печи в сутки, если печь выплавляет за это время 6500 т чугуна с содержанием углерода 0.4 мас. долей. Удельный расход кокса, содержащего 0.92 мас. долей углерода, составляет 0.55 т/т чугуна. В доменном газе содержится (об. долей): оксид углерода(IV) – 0.18; оксид углерода(II) – 0.20.
Дата добавления: 2018-02-18; просмотров: 1723; Мы поможем в написании вашей работы! |
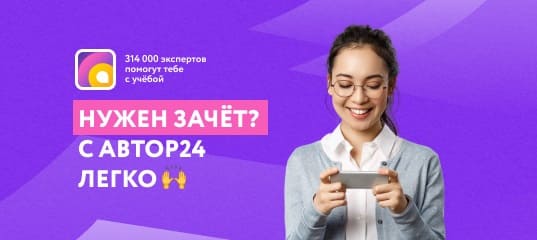
Мы поможем в написании ваших работ!