Производство и обработка стали
Производство стали – это второе звено в производственном металлургическом цикле: руда – чугун – сталь - изделие. Основными способами выплавки стали в настоящее время являются кислородно-конвертерный (более 60 % от всей массы выплавляемой в мире стали), электросталеплавильный (около 25 %) и мартеновский (около 20 %) способы. Для улучшения качества стали или получения металла с особыми свойствами, выплавленная одним из этих методов сталь подвергается вторичной обработке: рафинированию после выпуска из сталеплавильного агрегата (ковшовая металлургия) или переплаву уже затвердевших слитков (переплавные процессы). В связи с потребностями новых отраслей техники роль вторичной обработки стали непрерывно возрастает.
Особое место в черной металлургии занимают внедоменные процессы, используемые для производства сырья для выплавки стали (металлизированных окатышей) и железных порошков для порошковой металлургии. Несмотря на малый удельный вес этих процессов (не более 2 %) роль их в техническом прогрессе весьма велика.
Из трех основных методов производства стали доля мартеновского непрерывно падает, что объясняется его неконкурентоспособностью с кислородно-конвертерным и электросталеплавильным методами, обеспечивающими, наряду с получением высококачественных сортов стали, высокую экономичность производства.
В нашей стране последняя мартеновская печь была пущена в 1970 году; в последующие годы происходила только реконструкция действующих печей путем переделки их на двухванные печи. Тем не менее, доля мартеновской стали, выплавляемой в РФ, достаточно велика и значительно превышает долю стали, получаемой кислородно-конвертерным и электросталеплавильным методами.
|
|
Процесс превращения металлического сырья в сталь заключается в уменьшении содержания в нем углерода, кремния и марганца и полном удалении таких примесей как сера и фосфор(II). Это достигается окислением этих компонентов до соединений, образующих газообразную или жидкую, отделяющуюся от металла, фазу (шлак):
|

Окислителями в процессе выплавки стали могут быть:
- кислород газовой фазы;
- кислород, растворенный в металле;
- кислород в составе оксида железа, растворенного в шлаке;
- оксиды железа в металлической шихте (руда, стальной лом).
Так как в этих случаях металл и шлак являются растворителями, то для выражения концентрации растворенных в них компонентов приняты обозначения в виде квадратных скобок для раствора в металле, например, [С], [О] и круглых скобок для раствора в шлаке, например, (Мп). Так, запись: [Мn] + (FeO) = Мn + Fe, означает, что реакция протекает между растворенным в металле (железе), марганцем и растворенным в шлаке оксидом железа(II).
|
|
При окислении углерода и примесей часть металлического железа окисляется до оксида FeO (угар металла). Для уменьшения потерь металла его регенерируют, то есть восстанавливают до железа. В соответствии с этим в процессе выплавки стали выделяют два последовательно протекающих периода – окислительный и восстановительный, что может быть представлено схемой:
Выплавка стали требует больших затрат тепловой энергии.
Источниками теплоты являются:
- в кислородно-конвертерном методе тепловой эффект окисления компонентов шихты;
- в электросталеплавильном методе энергия электрического тока;
- в мартеновском методе теплота сгорания топлива.
Кислородно-конвертерный метод выплавки стали – это один из вариантов конвертерного метода, предложенного в 1856 году Г. Бессемером. В настоящее время он полностью вытеснил как бессемеровский (в конвертере с кислой футеровкой), так и томасовский (в конвертере с основной футеровкой) конвертерные процессы с воздушным дутьем. К преимуществам кислородно-конвертерного метода по сравнению с мартеновским и электросталеплавильным методами относятся:
|
|
- более высокая производительность сталеплавильного агрегата, достигающая 500 т/ч (производительность других методов не превышает 100 т/ч);
- более низкие капитальные затраты вследствие простоты устройства конвертера;
- меньшие расходы по переделу сырья в сталь, в том числе отсутствие затрат на топливо;
- простота автоматизации и управления процессом плавки.
В то же время применение для продувки чистого (не менее 99.5 %) кислорода вместо воздуха позволяет по сравнению с другими конвертерными методами:
- получать сталь, не содержащую азота;
- за счет избытка тепла, сверх необходимого для разогрева металла до температуры выпуска, использовать шихту, содержащую до 25 % твердого сырья (стальной лом, руда), что существенно снижает себестоимость выплавляемой стали.
Кислородно-конвертерный процесс – один из видов передела чугуна в сталь без использования топлива путем продувки чугуна в конвертере током кислорода. При этом окислительный и восстановительный периоды плавки разделены не только по времени, но и в пространстве: первый протекает в конвертере, второй – после выпуска стали в ковше.
|
|
Окислительный период плавки совпадает по времени с операцией продувки конвертера кислородом. При подаче кислорода под давлением 0.9-1.4 МПа в ванне под воздействием кислородных струй и потоков выделяющихся пузырьков газообразного оксида углерода(II) создается микрогетерогенная система «металл-шлак» с интенсивным массо- и теплообменом. Это ускоряет реакции окисления компонентов металлической шихты, вследствие чего выделяющееся тепло не рассеивается в окружающую среду, а кумулируется в системе, обеспечивая интенсивность процессов нагрева металла и расплавление твердых составляющих шихты.
В процессе продувки окисляются углерод, кремний, большая часть марганца, фосфор и незначительная часть железа. При этом лишь незначительная часть их окисляется непосредственно газообразным кислородом; основная часть компонентов окисляется кислородом, растворенным в металле [О] и «кислородом», растворенным в шлаке (FeO).
Окисление железа. Вследствие высокой (приближающейся к 100 %) концентрации железа в шихте оно окисляется непосредственно газообразным кислородом на поверхности металла в зоне его контакта с кислородной струей:
2 Fe+ О2 = 2 FeO – ΔН (а)
Образующийся оксид железа FeO растворяется частично в металле:
FeO→{Fe + [О]} (б)
и частично в шлаке:
FеО→{Ш + (FeO)} (в)
В незначительной степени железо может окисляться в массе металла за счет высших оксидов железа, содержащихся в руде и стальном ломе:
Fe + Fе2О3→3 FeO
Окисление углерода является основной реакцией при выплавке стали, так как снижает его содержание до предела, за которым чугун превращается в сталь. Углерод окисляется преимущественно до оксида углерода(II): окисление до оксида углерода(IV) незначительно (не более 10-15 %) и возможно лишь при малой концентрации его в чугуне. Окисление начинается с момента подачи кислорода в конвертер и происходит главным образом за счет кислорода, растворенного в металле:
[C]+[O] = CO (г)
и в шлаке: [С] + (FeO) = СО (д)
Суммируя, соответственно, реакции (а), (б), (г) и (а), (в), (г), получаем уравнение итоговой реакции окисления углерода, отражающее начальное и конечное состояние системы в конвертере:
2 С + О2 = 2 CO
Окисление марганца и кремния. Эти реакции, как и окисление углерода, начинаются с момента подачи кислорода и происходят за счет кислорода, растворенного в металле:
[Мn] + [О] = (МnО)
[Si] + 2 [О] = (SiО2)
и в меньшей степени за счет кислорода, растворенного в шлаке, на границе раздела фаз «шлак-металл»:
[Мn] + (FeO) = (МnО) + Fe
[Si] + 2 (FeO) = (SiО2) + 2 Fe
Образовавшиеся при окислении оксиды марганца и кремния переходят в шлак. Таким образом, для окислительного периода плавки в кислородном конвертере характерны как прямое окисление железа в зоне его контакта с кислородной струей («первичная реакционная зона»), так и окисление остальных компонентов за счет вторичных реакций на границе с первичной реакционной зоной и во всем объеме системы.
От последовательности окисления элементов зависит изменение во времени состава ванны в конвертере. Из него следует, что почти весь кремний и большая часть марганца выгорают (окисляются) в первые минуты продувки. Окисление кремния заканчивается через 3-5 мин, причем в результате связывания образовавшегося оксида кремния с известью шлака реакция становится необратимой и металл полностью обескремнивается.
Окисление марганца наиболее интенсивно происходит в начале продувки и за 3-5 мин. окисляется до 70 % марганца, содержащегося в чугуне. В дальнейшем окисление марганца определяется равновесием реакции:
[Мn] + (FeO) ↔ (МnО) + Fe
Высокая скорость окисления марганца и относительно низкая температура в начале плавки ограничивает скорость окисления углерода. В дальнейшем, при снижении содержания марганца и кремния скорость окисления углерода возрастает и падает только при его выгорании.
Реакции дефосфоризации и десульфуризации. Удаление из металла фосфора и серы необходимо потому, что фосфор увеличивает хладоломкость, а сера красноломкость выплавляемой стали. Фосфор растворяется в железе в значительных количествах и переходит в него из чугуна и железного лома. При продувке конвертера фосфор окисляется уже в начале процесса и переходит в шлак:
2 [Р] + 5 (FeO) + 3 (СаО) = (3СаО·Р205) + 5 Fe
Развитию этой реакции способствуют относительно невысокая температура, окислительная среда и высокая основность шлака. Конечное содержание фосфора в выплавляемой стали зависит от содержания его в исходном чугуне и, обычно, составляет 0.002 – 0.004 %.
Сера неограниченно растворяется в жидком и ограниченно в твердом железе и поступает в него из чугуна и неочищенного от смазочных масел стального лома. Десульфуризация металла происходит в течение всей продувки за счет перехода ее из металла в шлак по реакции:
[FeS] + (СаО) = (CaS) + (FeO)
чему способствуют высокая температура, интенсивное перемешивание фаз и низкое содержание в шлаке оксида железа FeO при его высокой основности. Так как в конвертере эти условия полностью не соблюдаются, степень десульфуризации не превышает 40 %. Поэтому, содержание серы в выплавляемой стали определяется главным образом ее содержанием в чугуне, которое не должно быть выше 0.06 % при выплавке углеродистых и 0.035 % при выплавке качественных сталей.
Образование шлака. Шлак в процессе плавки образуется в результате взаимодействия основных, кислотных и амфотерных оксидов различных элементов в составе металлической шихты:
МеО + ЭОn = МеО·ЭОn,
где: Ме – металл; Э – элемент, образующий кислотный или амфотерный оксид.
Основным источником шлакообразования становится поступающий в конвертер оксид кальция СаО и продукты окисления компонентов чугуна (SiО2, MnO, FeO, Р2О5), а также оксиды из растворяющейся футеровки конвертера (СаО, MgO). В твердых шлаках эти оксиды присутствуют в связанном состоянии в виде силикатов и фосфатов, например, ЗСаО·Р2О5 или в виде свободных оксидов. От содержания последних зависит основность (СаО) и окислительная способность (FeO) шлака. В жидком состоянии вследствие диссоциации шлаки представляют расплавы, содержащие катионы Fe2+, Mn2+, Са2+, Mg2+ и анионов O22-, S2-, SiО44-, РO43-, АlO33-, FeO22- и др.
В процессе плавки шлак выполняет несколько функций:
- связывает оксиды, образующиеся при окислении компонентов металлической шихты;
- служит переносчиком кислорода из газовой фазы к жидкому металлу;
- является теплопередающей фазой (при электроплавке);
- защищает металл от насыщения газами из газовой фазы.
Вследствие этого состав, вязкость, количество и скорость образования шлака при плавке оказывают существенное влияние на качество и выход стали и стойкость футеровки конвертера.
К важнейшим свойствам сталеплавильных шлаков относятся:
- основность (кислотность), зависящая от отношения мольных долей (или процентного содержания) оксидов CaO/SiO2; и
- окислительная способность, характеризуемая содержанием в шлаке оксидов железа, главным образом, оксида FeO.
Все реакции окисления компонентов чугуна, протекающие в конвертере экзотермические. При этом количество выделяющегося тепла существенно зависит от состава металлической шихты. В некоторых случаях такие ее компоненты как кремний и фосфор могут быть основным «топливом» при конвертерной плавке. Однако особое значение для температурного режима плавки, процесс а шлакообразования и создания микрогетерогенной системы имеет окисление углерода, при котором образуются газообразные продукты.
Вследствие экзотермичности реакций окисления и их высокой скорости окислительный период плавки в кислородном конверторе протекает в автотермичном режиме и не требует притока тепла извне. При этом обеспечивается нагрев стали, выпускаемой из конвертера, до 1600-1650 оС, что значительно выше температуры заливаемого чугуна (1250-1400 оС).
Восстановительный период плавки при кислородно-конверторной выплавке стали пространственно отделен от окислительного и протекает после выпуска стали из конвертера в ковше. Одновременно с восстановлением оксида железа FeO в восстановительный период происходит процесс перевода растворенного в стали кислорода в нерастворимые в металле соединения и отделение их от стали. Поэтому, восстановительный период плавки называется также операцией раскисления стали. Удаление кислорода из стали устраняет возможность реакции между растворенным в ней углеродом и кислородом при ее медленном охлаждении и образования так называемой «кипящей». стали за счет выделения из нее пузырьков оксида углерода(II).
В качестве реагентов для раскисления, восстанавливающих оксид железа FeO и связывающих растворенный в стали кислород, используют так называемые раскислители, к которым относятся элементы с большим сродством к кислороду, чем железо. Обычно для этой цели применяют марганец и кремний в виде соответствующих ферросплавов, алюминий и сплавы некоторых редкоземельных металлов. При этом протекают реакции:
Mn + [О] = (MnO) Si + 2[O] = (SiO2)
Mn + (FeO) = Fe + (MnO) Si + 2(FeO) = 2 Fe + (SiO2)
Образовавшиеся оксиды раскисляющих элементов переходят в шлак.
Обычно процесс раскисления стали совмещается с введением в нее легирующих добавок в виде ферросплавов, содержащих соответствующие легирующие элементы.
Сталеплавильный агрегат в кислородно-конвертерном методе выплавки стали включает собственно конвертер, систему подачи кислорода и систему отвода и очистки конвертерных газов.
Кислородный конвертер является реактором периодического действия. Это поворачивающийся на цапфах в вертикальной плоскости стальной сосуд грушевидной формы, имеющий концентрически расположенную горловину для заливки чугуна, завалки твердых компонентов шихты и отвода газа. Через горловину вводится в конвертер фурма для подачи кислорода и происходит слив жидкой стали и шлака. Изнутри конвертер футерован огнеупорным материалом. Конфигурацию внутренней полости конвертера (рис. 10.9) выбирают таким образом, чтобы исключить выброс жидкого металла при продувке и обеспечить стабильный режим работы.
Рис. 10.9. Схема кислородного
конвертера
Футеровка конвертера состоит из трех слоев: примыкающего к кожуху арматурного слоя, внутреннего рабочего слоя и соединяющего их промежуточного слоя. Арматурный слой из магнезитового кирпича служит для снижения теплопотерь и защиты кожуха конвертера при прогаре рабочего слоя. Он не требует замены в течение нескольких лет. Рабочий слой изготавливается из безобжиговых огнеупоров на основе каменноугольной смолы или пека, имеет толщину от 0.4 до 0.7 м и выдерживает от 500 до 800 плавок. Так как он подвергается химическому воздействию шлака, размывающему действию потоков металла и шлака и ударам при загрузке шихты, то изнашивается во время работы и требует периодической замены. В последнее время для восстановления рабочего слоя используется метод горячего ремонта (торкретирование футеровки) путем вдувания в конвертер смеси из магнезитового шлака и коксовой пыли. Торкретирование позволяет не останавливать конвертор на длительное время для ремонта.
Система подачи кислорода. По принципу подачи кислорода конвертеры делятся на три типа: с верхней продувкой, с донной продувкой и с комбинированной продувкой. Наиболее распространены конвертеры первого типа. В них кислород подается под давлением 0.9-1.5 МПа через охлаждаемую водой фурму, вводимую на время продувки в конвертер через его горловину.
В конвертерах с донной продувкой, используемых с середины 60-х годов, кислород подается через систему фурм (от 7 до 22 в зависимости от емкости конвертера), установленных в днище конвертера. Для охлаждения фурм в их кольцевое пространство поступает жидкое или газообразное топливо, термическая диссоциация которого, протекающая с поглощением тепла, компенсирует избыточное тепло, выделяющееся при продувке в зоне, прилегающей к фурмам. При донной продувке улучшается перемешивание ванны, повышается скорость выгорания углерода, увеличивается степень дефосфоризации и десульфуризации и уменьшаются потери металла со шлаком. В результате сокращается время плавки и увеличивается выход стали. Однако, донная продувка требует сокращения содержания стального лома в шихте, так как часть тепла при продувке расходуется на диссоциацию углеводородов охлаждающего фурма топлива.
В последнее время получают распространение конвертеры с комбинированной продувкой, в которых через верхнюю фурму подается большая часть кислорода, а через донные фурмы или пористые огнеупорные элементы днища вдувается остальная часть кислорода или смесь его с инертным газом. В таких конвертерах сочетаются преимущества реакторов первого и второго типов.
Система отвода и очистки конвертерных газов. В процессе продувки образуется большое количество конвертерных газов, нагретых до 1450-1650 оС. При интенсивности выхода газов 5-14 м3/т металла, объем их для 350-тонного конвертера достигает 5000 м3. Конвертерные газы состоят главным образом из продуктов окисления углерода и содержат около 85 % оксида углерода(II), 10 % оксида углерода(IV) и 5 % азота, а также значительное количество (до 250 г/м3) мелкодисперсных частиц оксида железа(III) – бурый дым.
Система отвода и очистки конвертерных газов включает котел-утилизатор, в котором используется теплосодержание газов, мокрые скрубберы и электрофильтры для удаления пыли. Очищенный газ собирается в газгольдерах или выбрасывается в атмосферу через дожигающее оксид углерода(II) устройство.
Шихтовые материалы. Шихта для кислородно-конвертерной выплавки стали состоит из металлической части (жидкий чугун, стальной лом или скрап), неметаллической части (известь, плавиковый шпат, охладители) и легирующие добавки. Чугун является основным материалом и доля его в металлической части шихты может составлять от 100 до 70 % , доля металлического лома не более 25-30 %. В кислородном конвертере можно перерабатывать любой передельный чугун с содержанием углерода 3.9-4.3 %. Однако для получения высоких ТЭП и стали надлежащего качества к составу чугуна предъявляют определенные требования по содержанию фосфора (не более 0.20.3 %), серы (не более 0.04-0.06 %) и марганца (не более 0.71.1 %). Металлический лом должен быть малогабаритным, с размерами кусков не более 0.3х0.3х1.0 м3, и содержать минимальное количество вредных примесей и ржавчины. Помимо лома используют также металлизированные окатыши и брикетированное губчатое железо.
Известь, используемая в качестве шлакообразующего материала, должна содержать не менее 90 % оксида кальция и ограниченное количество кремния (не более 3 %) и серы (не более 0.2 %). Для разжижения шлака используется добавка плавикового шпата CaF2.
При пере работке чугунов с повышенным содержанием кремния во избежание подъема температуры плавки сверх оптимальной, в состав шихты вводят охладители в виде железной руды, боксита и агломерата.
Технологический процесс. Процесс выплавки стали в кислородном конвертере состоит из нескольких операций, которым соответствует определенное положение конвертера относительно его оси.
1. Конвертер в наклонном положении:
- завалка металлолома с помощью завалочной машины;
- заливка жидкого чугуна из ковша с помощью заливочного крана;
2. Конвертер в вертикальном положении:
- введение фурмы и продувка кислородом с одновременной загрузкой части шлакообразующих материалов;
- загрузка остальной части шлакообразующих материалов до окончания продувки и выведение фурмы из конвертера, анализ стали.
3. Конвертер в горизонтальном положении:
- выпуск стали через летку в ковш.
4. Конвертер в положении горловиной вниз:
- слив шлака через горловину в шлаковый ковш. Продувку ведут до достижения в металле заданного содержания углерода, определяемого результатами анализа стали, объемом израсходованного кислорода и временем продувки.
Для раскисления стали в ковш вводят в определенной последовательности раскислители. Правильный режим раскисления позволяет снизить угар металла.
Выплавка стали в электрических печах основана на использовании для нагрева, расплавления и поддержания металла в расплавленном состоянии электрической энергии, трансформируемой в теплоту. В отличие от кислородно-конвертерного метода при электроплавке выделение тепла не связано с использованием окислителей. Поэтому, плавку в электрических печах можно вести в любой атмосфере – окислительной, восстановительной, нейтральной (инертный газ) и в широком диапазоне давлений – в вакууме, при атмосферном или повышенном давлениях.
К основным достоинствам электросталеплавильного метода относятся:
- быстрый нагрев металла, что позволяет вводить большое количество легирующих добавок;
- применение безокислительных шлаков и как следствие, малый угар легирующих элементов;
- точное и плавное регулирование температуры и состава металла;
- высокая степень раскисления металла;
- возможность получения сталей с низким содержанием серы и фосфора.
Однако, несмотря на эти достоинства электроплавки, высокое потребление электроэнергии обусловило использование ее преимущественно для производства легированных и высококачественных (с низким содержанием серы, фосфора, кислорода и других вредных примесей) сталей, в том числе, инструментальных, жаростойких, шарикоподшипниковых и т. п. В последнее время, в связи с внедрением в металлургическое производство электропечей большой мощности (до 400 т), электроплавка стала применяться и для получения рядовых углеродистых сталей по упрощенной технологии с их последующим переплавом.
Для выплавки стали применяются электрические печи периодического действия. По принципу генерирования теплоты они делятся на дуговые и индукционные.
В дуговых печах тепло выделяется в результате горения электрической дуги. По расположению дуги относительно металлической шихты дуговые печи подразделяются на печи косвенного нагрева, печи прямого нагрева и печи комбинированного нагрева. Наиболее распространены печи прямого нагрева, в которых электрические дуги горят непосредственно между каждым из электродов и металлом.
В индукционных печах тепло выделяется за счет возникновения в толще шихты индукционных токов. В основе действия индукционных печей лежит трансформаторный принцип передачи энергии от первичной цепи к вторичной. При этом первичной обмоткой – индуктором является соленоид, а вторичной – металлическая шихта.
Дуговые печи. Для электроплавки применяются главным образом трехфазные дуговые печи переменного тока с тремя электродами и непроводящим подом (рис. 10.10). Печь состоит из металлического сварного корпуса, укрепленного в люльке, позволяющей наклонять печь, и поворотного свода, через который в плавильное пространство печи вводятся электроды. Корпус печи изнутри футерован огнеупорным материалом и имеет выпускное отверстие (желоб) для слива металла и рабочее окно, через которое Рис. 10.10. Схема дуговой загружают шлакообразующие материалы, руду и ферросплавы и
печи скачивают шлак. Печь снабжена механизмом наклона в сторону
сливного отверстия и в сторону рабочего окна, механизмом подъема и отворота свода при загрузке печи и механизмом поворота кожуха для ускорения плавления шихты. Печи последних конструкций имеют дополнительное устройство для электромагнитного перемешивания расплавленного металла, что ускоряет процесс плавки.
Электроды печи должны обладать высокой электропроводимостью, выдерживать высокие температуры и иметь достаточную механическую прочность. Этим требованиям удовлетворяют исключительно изделия на основе углерода: угольные и графитированные электроды, получаемые обжигом малозольных углеродных материалов. Для уменьшения расхода материала верхнюю часть электрода изготавливают из стали и охлаждают водой. Электроды укреплены в специальных зажимах и в процессе плавки могут перемещаться в вертикальном направлении в соответствии с заданной программой, что обеспечивает постоянство длины дуги.
Рабочее напряжение, подаваемое на электроды, колеблется в зависимости от емкости печи от 110 до 800 В. Для уменьшения потерь энергии электрический ток подается к печам под напряжением 6-10 кВ через понижающий трансформатор.
Расход энергии на плавку в дуговых печах составляет 500800 кВт·ч на тонну выплавляемой стали. Расход электродной массы 5-9 кг/т стали.
Индукционные печи. Электроплавильные индукционные печи имеют емкость от 0.01 до 12 т и питаются током от различных источников. Для питания малых печей применяют ламповые генераторы с частотой 50-1000 кГц, печей средней и большой мощности – машинные генераторы с частотой 500-10000 кГц, наиболее крупные печи питаются непосредственно от сети током промышленной частоты 50-60 Гц.
Индукционная печь (рис. 10.11) состоит из огнеупорного тигля с сливным носком, помещенного в индуктор в виде соленоида из медной трубки, охлаждаемой водой; Печь заключена в металлический кожух, закрываемый сверху сводом. Для слива металла печь может наклоняться в сторону сливного носика. Процесс плавки в индукционных печах протекает весьма быстро. В качестве металлической шихты в них используется металлический лом известного состава,
Рис. 10.11. Схема индукционной
печи
который точно рассчитан по содержанию углерода, серы, фосфора и легирующих элементов. Так как в индукционных печах отсутствуют электроды, выплавляемая в них сталь не загрязняется углеродом и продуктами их обжига, угар легирующих элементов весьма мал. Поэтому индукционные печи при меняют для выплавки только высококачественных сталей и сплавов сложного химического состава. Расход энергии при плавке в индукционных печах составляет 500-700 кВт·ч на тонну стали.
Технологические процессы выплавки стали в электрических печах весьма разнообразны. Конкретный режим плавки зависит от природы и состава металлической шихты, типа печи и материала ее футеровки. Наиболее распространена плавка в дуговых печах, в частности:
- плавка с полным окислением примесей;
- переплав стальных отходов без окисления;
-плавка на жидкой шихте (дуплекс-процесс) и др.
Ниже рассмотрен один из подобных процессов – типовая плавка в дуговых электропечах на углеродистой шихте с окислением, применяемая для выплавки большинства типов сталей. Процесс включает следующие операции:
- заправка печи,
- загрузка шихты в печь,
- плавление шихты,
- окислительный период плавки,
- восстановительный период плавки,
- выпуск металла из печи.
3anpaвкa печи. Цель этой операции – исправление изношенных и поврежденных в процессе плавки участков внутренней футеровки печи. Для этого в печь забрасывается магнезитовый порошок или смесь порошка со связующим в виде каменноугольного пека.
3агрузка шихты. Основным сырьем для электроплавки является стальной лом, содержание которого в металлической шихте составляет 90-100 %. Для повышения содержания углерода в шихту вводят до 10 % чугуна. В качестве сырья для плавки в электропечах используют также губчатое железо, содержащее 85-93 % металла, и металлизированные окатыши, содержащие не менее 90 % металла. Шихта загружается в печь порциями с помощью бадей и плотно укладывается, что обеспечивает ее проводимость и устойчивое горение дуги.
Плавление шихты. По окончании загрузки шихты электроды опускают до касания с шихтой и включается ток. Под воздействием высокой температуры шихта под электродами плавится и расплавленный металл стекает вниз, образуя в шихте «колодцы», в которые постепенно по программе опускаются электроды, пока не достигнут нижнего положения. Затем, по мере накопления жидкого металла, электроды вновь поднимают. В период плавления происходит частичное окисление компонентов шихты кислородом воздуха и оксидами железа в руде и окалине и формируется шлак. В период плавления полностью окисляется кремний, до 50 % марганца и частично углерод и железо. Время плавления шихты составляет от 1 до 3 часов.
Окислительный период плавки. В этот период в печи протекают процессы окисления углерода до заданного содержания, уменьшение содержания в металле фосфора, азота и водорода и нагрев металла до температуры близкой к температуре выпуска. В качестве окислителей используются оксиды железа, содержащиеся в руде и агломерате в составе шихты, или газообразный кислород, подаваемый под давлением в печь. В конце окислительного периода из печи скачивают образовавшийся шлак.
Восстановительный период плавки. В этот период в печи происходит раскисление металла, удаление серы и состав стали доводится до заданного. Для этого в печь подаются раскислители (ферромарганец, ферросилиций, алюминий) и шлакообразующие компоненты. Одновременно в печь вводят легирующие добавки.
Выпуск металла. По достижении металлом температуры на 120-130 оС выше температуры ликвидуса металл выпускается из печи в ковш.
Значительные простая электрических печей связаны с необходимостью ремонта ее футеровки и составляют от 5 до 10 % всего времени. Продолжительность плавки в электропечах зависит от емкости печи, состава выплавляемой стали, технологии плавки, метода раскисления стали (в печи или в ковше) и мощности трансформатора тока. Для печей емкостью 100 т она равна 4-6 часам. Применение кислорода в окислительный период плавки сокращает время плавки на 10-20 % и, соответственно, увеличивает производительность печи.
Действующие современные мартеновские печи – это крупные сталеплавильные агрегаты сложной конструкции с большим количеством различных дополнительных устройств. Строительство их связано с крупными капитальными затратами. Поэтому одновременный отказ от мартеновского способа производства стали и переход к кислородно-конвертерному и электросталеплавильному способам экономически нецелесообразен. Этим объясняется высокая доля мартеновской стали, выплавляемой до настоящего времени в нашей стране.
Мартеновский процесс выплавки стали ведут на поду пламенной отражательной печи, снабженной регенераторами тепла отходящих газов для подогрева воздуха и топлива, подаваемых в печь. В зависимости от состава металлической печи различают две разновидности процесса:
Скрап-процесс, в котором основным компонентом шихты является стальной лом (скрап) с добавкой 25-40 % чугуна, облегчающего расплавление лома, являющегося источником углерода. Скрап-процесс используется в цехах металлургических и машиностроительных заводов, в которых нет доменного производства.
Скрап-рудный процесс, в котором основным компонентом шихты является жидкий чугун с добавкой 45-25 % скрапа и железной руды для окисления примесей в чугуне. Этот процесс применяется на заводах, имеющих собственное доменное производство.
При выплавке стали в мартеновских печах протекают процессы окисления углерода и примесей в шихте и образования шлаков аналогичные тем, которые идут в кислородном конвертере. Однако мартеновский процесс имеет ряд существенных особенностей. К ним относятся:
- использование в качестве источника тепла реакций сгорания непосредственно в печи газообразного и жидкого топлива (природный газ, мазут, смесь коксового и доменного газов);
- поступление тепла от горящего факела топлива к ванне сверху и отвод тепла снизу, вследствие чего температура шлака превышает температуру металла;
- окислительный характер газовой фазы, состоящей во все периоды плавки из оксида углерода(IV), кислорода, паров воды и азота;
- макрогетерогенность системы «металл-шлак», в которой металл находится под слоем шлака. Вследствие этого все добавки, кислород и тепло поступают в металл через шлак. Поэтому изменение состава, консистенции и температуры шлака существенно влияют на состав и качество выплавляемой стали;
- участие пода печи в протекающих в ней процессах шлакообразования вследствие длительности процесса плавки.
Заключительная операция сталеплавильного производства – выпуск стали в сталеразливочный ковш и ее разливка. От правильного проведения процесса разливки зависят ТЭП производства, оцениваемого по выходу готовых слитков. Существуют два принципиально различных методов разливки стали:
- разливка в изложницы,
- непрерывное литье заготовок.
Первый метод разливки до настоящего времени преобладает, хотя имеет ряд существенных недостатков, главным из которых является высокий дополнительный расход тепла на разогрев слитков перед прокатом.
Метод непрерывного литья заключается в том, что жидкую сталь из сталеразливочного ковша непрерывно подают через промежуточный ковш (демпферная емкость) в охлаждаемый водой кристаллизатор. Образующийся в кристаллизаторе слиток вытягивается из него с помощью валков и поступает в зону вторичного охлаждения, где орошается водой из форсунок до полного затвердевания. Затвердевший слиток без остановки его движения режется на заготовки заданной длины с помощью газорезки или гидравлических ножниц. Скорость разливки (вытягивания слитка) зависит от сечения заготовки и колеблется от 0.4 до 10 м в минуту. Методом непрерывного литья можно получать слитки (заготовки) различного сечения: квадратного (блюмы 500 х 500 мм), прямоугольного (слябы шириной до 2500 мм), профильные заготовки для труб, балок, рельсов, то есть формовать изделие в процессе разливки металла. Непрерывное литье осуществляется в агрегатах, получивших название машин для непрерывной разливки стали (МНРС). По расположению струи металла МНРС делятся на машины вертикального типа, машины с изгибом слитка, машины криволинейного (радиального) типа и машины горизонтального типа. Наиболее распространены МНРС радиального типа, сочетающие преимущества МНРС вертикального типа с относительно небольшой высотой конструкции (10-12 м против 35-40 м).
К достоинствам метода непрерывного литья относятся:
- упрощение и сокращение с 140 до 6 часов технологического цикла;
- снижение на 90 % расхода тепла;
- сокращение в три раза потерь металла и увеличение выхода готовой продукции;
- высокая степень автоматизации и механизации процесса и, как следствие, повышение производительности установки.
Вследствие этого метод непрерывной разливки стали интенсивно внедряется в производство, составляя в настоящее время в индустриально развитых странах свыше 90 % всего объема разлитой стали. В РФ доля непрерывной разливки составляет около 25 % от общего количества.
КОНТРОЛЬНЫЕ ВОПРОСЫ К ТЕМЕ 10.3
10-1.Перечислите основные способы производства стали. В чем заключается сущность процесса переделки чугуна в сталь?
10-2. Укажите преимущества кислородно-конвертерного метода выплавки стали по сравнению с другими конвертерными методами и мартеновским методом.
10-3. Какие реакции и где протекают в окислительном и восстановительном периодах при выплавке стали в конвертере? Чем объясняется последовательность окисления примесей при плавке?
10-4. Какие сорта стали преимущественно выплавляются в электропечах? Перечислите разновидности промышленных электроплавильных печей и укажите их особенности.
10-5. Чем мартеновский метод выплавки стали принципиально отличается от конвертерного? Что такое двухванные мартеновские печи?
ЗАДАЧИ К ТЕМЕ 10.3
10-1. Площадь пода 250-тонной мартеновской печи составляет 75 м2, печь дает 4 плавки в сутки. За каждую плавку бракуется в среднем 2 % слитков. Продолжительность горячих и холодных ремонтов составляет 7 % годового времени. Определите: съем стали в сутки с единицы площади, часовую и годовую производительность печи.
10-2. Какая масса оксида железа(II) вступила в процессе мартеновской плавки в реакцию дефосфоризации 1200 т чугуна, в составе которого 0.5 мас. % фосфора, если в основном продукте было обнаружено 0.001 мас. % фосфора? Выход стали 90 % от чугуна.
10-3. Напишите уравнения реакций, происходящих в мартеновской печи в слоях шлака и металла. Какай объем оксида углерода(II) при нормальных условиях образуется в мартеновской печи, если массовая доля углерода в 600 т металла снизилась с 5 до 1 %?
10-4. Часто во время доводки в расплавленную сталь прибавляют алюминиевые чушки. Напишите уравнения происходящих при этом химических реакций. Сколько алюминия необходимо внести в 50 т стали для снижения массовой доли кислорода с 0.1 до 0.008 %?
10-5. Годовой план мартеновского цеха 1345 тыс. т стали. В составе шихты мартеновских печей 63 % чугуна (по массе). Выход стали из шихты 90 %. Определите годовой расход металлолома и руды, если их массовое отношение в шихте 2:1.
10-6. Определите состав шихты для получения в мартеновской печи стали-40, если известно, что при завалке и расплавлении выгорает 35 % углерода шихты. Массовая доля (%) углерода: в плаве 0.9, в чугуне 4.0, в скрапе 0.3.
10-7. Средняя скорость окисления углерода в 900-тонной мартеновской печи составляет от массы расплава 0.2 % в 1 ч. Сколько оксида углерода(II) (в кг и мЗ при н. у.) образуется за плавку продолжительностью 7 ч? Какай объем кислорода (н.у.) расходуется за это время на окисление углерода?
10-8. Рассчитайте годовую производительность крупнотоннажного конвертора в слитках, если известно, что разовая загрузка в него металлической шихты 250 т, продолжительность плавки 45 мин, бракованные слитки составляют 5 % (от массы шихты). Конвертор работает 320 суток в году.
10-9. Сколько 500-тонных мартеновских печей или 250-тонных конверторов необходимо для обеспечения работы доменной печи, полезный объем которой 3200 м3, КИПО 0/48 и время ремонта 25 суток в 5 лет? Длина плавильного пространства мартеновской печи 19 м, ширина 6 м, съем стали 9 т/м2 пода в сутки, время работы 330 суток в году. Конвертор выдаст 1 плавку за 0.75 ч и работает 320 суток в году. На 1 т мартеновской стали расходуется 0.9 т чугуна, а на 1 т конверторной стали 0.95 т чугуна.
10-10. Определите объем кислорода (н.у.), необходимого для окисления примесей при переделе 1000 т чугуна в сталь, если массовые доли углерода снизились с 4.5 до 0.3 %, кремния с 1.5 до 0.3 % и марганца с 1.7 до 0.4 %.
10-11. Кислородно-конверторный цех имеет два крупнотоннажных конвертора производительностью по 400 т в 1. ч. Определите годовую производительность цеха, расход и себестоимость металлической шихты (на 1 плавку), годовой расход кислорода (н.у.), если известно, что продолжительность плавки 40 мин, среднегодовой брак слитков 8 %, себестоимость 1 т стали 65 руб., себестоимость металлошихты 80 % от стоимости стали, удельный расход кислорода 50 м3/т, цех работает бесперебойно 330 дней в году.
10-12. Сколько стали, в составе которой 99 % железа (по массе), теоретически можно получить методом прямого восстановления в электропечах из 1000 т металлизированных окатышей? Массовая доля железа в сырье 70.29 %.
10-13. Сколько ферросплавов нужно взять для получения в дуговой электропечи 500 т стали марки 45Х2НЗ, если степень использования ферросплавов 90 %, а массовая доля легирующих металлов в каждом 50 %?
10-14. При переделке чугуна в сталь содержание примесей меняется в следующих пределах (масс. долей): углерода – от 0.045 до 0.003; кремния – от 0.015 до 0.003; марганца – от 0.017 до 0.004. Определите объем кислорода на окисление этих примесей при переделке 1000 т чугуна.
10-15. Одним из способов получения высокочистых металлов является синтез карбонилов металлов с их последующим разложением. В порошковой металлургии высокочистый порошок железа получают разложением пентакарбонила железа. Рассчитайте необходимую массу пентакарбонила железа для получения 5 т порошкообразного железа.
10-16. Определите высоту стали в мартеновской печи мощностью 600 т, если под печи имеет размеры 17х7 м2. Плотность стали 7.2 т/м3.
10-17. Определите коэффициент заполнения сталью конвертора шаровидной формы диаметром 8 м, если мощность его составляет 350 т. Плотность стали в жидком состоянии 7.2 т/м3.
10-18. Определите число мартеновских печей с площадью пода 20х5 м2 при съеме стали 9.7 т/сутки∙м2 пода, обеспечивающих работу трех доменных печей полезным объемом 2700 м3 каждая при КИПО 0.59. Выход стали от чугуна 92 %. В резерве 7 % мартеновских печей.
10-19. Определите годовую производительность кислородного конвертора мощностью 250 т, если время плавки равно 45 мин., время работы – 320 суток в году, а брак при плавке составляет 5 %.
10-20. План мартеновского цеха 1.5∙106 т стали в год. В составе шихты мартеновских печей 68 мас. % чугуна. Выход стали из шихты 94 %. Определите годовой расход металлолома и руды, если их массовое отношение в шихте 2:1.
Дата добавления: 2018-02-18; просмотров: 1352; Мы поможем в написании вашей работы! |
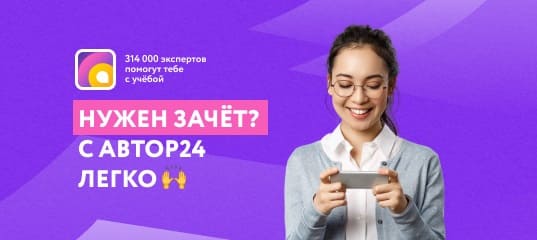
Мы поможем в написании ваших работ!