Режимы автоматической сварки под флюсом стыков труб
Диаметр труб, мм | Толщина стенки, мм | Диаметр электродной проволоки, мм | Слои шва | Сварочный ток, А | Напряжение, В | Скорость сварки, м/ч | Смещение электрода с зенита, мм |
1 | 2 | 3 | 4 | 5 | 6 | 7 | 8 |
325-426 | 6 | 2 | 1 | 350-450 | 34-36 | 15-20 | 35-40 |
Последующие | 350-450 | 36-38 | 15-20 | 30-35 | |||
7-12,5 | 2 | 1 | 400-500 | 34-36 | 30-35 | 35-40 | |
Последующие | 450-500 | 36-38 | 30-35 | 30-40 | |||
Более 12,5 | 3 | 1 | 500-600 | 34-36 | 25-35 | 35-40 | |
Последующие | 650-750 | 36-38 | 30-40 | 30-40 | |||
530-820 | 6-12,5 | 2 | 1 | 400-500 | 42-44 | 35-40 | 60-80 |
Последующие | 500-550 | 42-46 | 35-40 | 40-50 | |||
3 | 1 | 550-650 | 42-44 | 35-50 | 40-60 | ||
Последующие | 700-750 | 44-46 | 35-50 | 30-40 | |||
Более 12,5 | 3 | 1 | 550-650 | 42-44 | 35-50 | 40-60 | |
Последующие | 680-750 | 44-46 | 35-50 | 30-40 | |||
1020-1220 | 7-12,5 | 3 | 1 | 550-650 | 44-46 | 40-50 | 60-80 |
Последующие | 650-750 | 46-48 | 40-50 | 40-60 | |||
4 | 1 | 800-900 | 44-46 | 45-50 | 60-80 | ||
Последующие | 900-950 | 46-48 | 45-55 | 40-60 | |||
1020-1220 | Более 12,5 | 3 | 1 | 750-800 | 44-46 | 45-55 | 60-80 |
Последующие | 800-850 | 46-48 | 40-55 | 40-60 | |||
4 | 1 | 800-900 | 44-46 | 45-55 | 60-80 | ||
4 | Последующие | 1100-1100 | 46-48 | 70-90 | 40-60 | ||
4 | Облицовочный | 800-900 | 46-48 | 40-50 | 40-60 | ||
1420 | 9-16 | 3 | 1 | 750-800 | 44-46 | 40-50 | 80-100 |
Последующие | 800-850 | 46-48 | 40-50 | 40-80 | |||
4 | 1 | 800-900 | 44-46 | 40-55 | 80-100 | ||
Последующие | 800-900 | 46-48 | 40-50 | 40-80 | |||
1420 | Более 16 | 3 | 1 | 750-800 | 44-46 | 40-50 | 60-100 |
Последующие | 800-850 | 44-46 | 50-55 | 60-80 | |||
Облицовочный | 850-900 | 46-48 | 40-50 | 40-80 | |||
1 | 800-900 | 44-46 | 40-55 | 80-1000 | |||
4 | Последующие | 1000-1100 | 44-46 | 70-90 | 60-80 | ||
Облицовочный | 800-900 | 46-48 | 40-50 | 40-80 |
|
|
Примечание:
1. Вылет электрода диаметром Æ 2 мм - 30¸35 мм; Æ 3 мм - 40¸45 мм; Æ 4 мм - 40-50 мм; угол наклона электрода "вперед" - до 30°.
2. Режимы сварки являются ориентировочными. Механические свойства сварных соединений должны удовлятворять требованиям п.п.4.1.6, 4.1.7.
3. При сварке термоупрочненных труб запрещается применять сварочную проволоку Æ 4,0 мм.
5.1.9. Число слоев (без учета подваренного слоя), выполненных автоматической сваркой под флюсом, зависит от толщины стенки трубы и должно соответствовать:
Толщина стенки трубы, мм | Число слоев (не менее) |
до 16,3 | 2 |
до 20,5 | 3 |
до 25,0 | 4 |
до 32,0 | 6 |
5.1.10. Готовый шов должен иметь усиление высотой не менее 1 и не более 3 мм. Ширина сварного шва в зависимости от толщины стенки трубы и вида разделки кромок должна соответствовать данным табл. 1.18. Сопряжения облицовочных швов между собой и основным металлом следует выполнять с плавным переходом.
Таблица 1.18.
Ширина сварного шва в зависимости от толщины стенки трубы и вида разделки кромок
Толщина стенки трубы, мм | Вид разделки кромок (табл. 1.8) | Ширина сварного шва (не более), мм |
7-8 | "U" - образная | 14 +/- 4 |
8-12 | "U" - образная | 20 +/- 4 |
12-16 | "U" - образная | 24 +/- 4 |
15-20,5 | С двойным скосом | 26 +/- 4 |
20,5-28 | С двойным скосом | 32 +/- 4 |
|
|
5.1.11. Подварку стыков труб диаметром 1020-1420 мм следует выполнять в один слой. Шов должен иметь усиление не менее 2 и не более 3 мм. Ширина шва при ручной подварке 9-14, при автоматической - 12-18 мм.
5.1.12. Автоматическую подварку корня шва под флюсом выполняют по всему периметру стыка проволокой диаметром 2 или 3 мм теми же материалами, которые рекомендованы для сварки заполняющих слоев, после сварки корневого слоя шва или после выполнения всех наружных слоев. Для сварки может применяться сварочный трактор типа ТС-17М.
5.1.13. Если подварку осуществляют после сварки корневого слоя шва, то интервал времени между окончанием сварки корня шва и началом сварки подварочного слоя не должен превышать 40 мин. Если подварку выполняют после завершения сварки наружных слоев шва, то интервал времени между окончанием сварки шва и началом выполнения подварочного слоя не должен превышать 1,5 ч.
Полуавтоматическая сварка в среде углекислого газа
5.2.1. Полуавтоматическая сварка в среде углекислого газа /СО2/ может применяться для сварки заполняющих и облицовочного слоев поворотных стыков труб из стали с прочностью до 55 кгс/мм2 при капитальном ремонте газопроводов.
|
|
Сварка должна выполняться полуавтоматами типа ПДГ-309 УЗ или другими аналогичного типа.
Технология сварки должна быть предварительно аттестована.
5.2.2. Сварочные работы с применением полуавтоматической сварки могут выполняться при температуре воздуха не ниже - 18° С.
5.2.3. Сварочная проволока и защитный газ должны соответствовать данным табл. 1.19.
5.2.4. Для предупреждения образования пор в швах необходимо после доставки баллонов к сварочному посту дать углекислоте отстояться в течение 20-25 мин. Затем следует открыть вентиль и выпустить немного углекислоты, содержащей повышенное количество газообразующих примесей, и только после этого можно начинать сварку.
Таблица 1.19.
Сварочная проволока и защитный газ
Область применения | Марка проволоки | Диаметр проволоки, мм | Защитный газ |
Поворотная сварка стыков труб с нормативной прочностью до 539 МПа (55 кгс/мм2) | Св-08Г2С по ГОСТ 3246-84 | 1,0-1,4 | Сварочная углекислота по ГОСТ 8050-85, I-II сорт, пищевая |
5.2.5. Для эффективной осушки углекислого газа его следует пропустить через влагоотделитель, заполненный селикогелем. Смену селикогеля производить одновременно с заменой баллона с углекислотой. Вес селикогеля в осушителе в этом случае должен быть не менее 500 г.
|
|
Для удаления адсорбированной кислоты селикогель перед применением следует просушить горячим воздухом или в печи при температуре 150-200°С в течение 2-х ч.
5.2.6. Сварку следует производить на постоянном токе обратной полярности на режимах, приведенных в табл. 1.20.
Таблица 1.20.
Дата добавления: 2019-11-16; просмотров: 205; Мы поможем в написании вашей работы! |
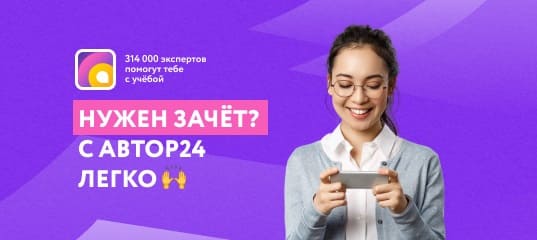
Мы поможем в написании ваших работ!