Сплавы на основе железа?(Черные металлы) Чугун-Сталь
К черным металлам относят железоуглеродистые сплавы на основе железа, которые в зависимости от содержания углерода делят на стали – до 2,14% углерода и чугуны – свыше 2,14% углерода.
=Чугуны-Это сплавы железа с углеродом, содержащие постоянные примеси марганца, кремния, фосфора и серы, а также при необходимости легирующие элементы. –Матерьял с литейными с-вами, очень низкий пластичные с-ва, дешевый матерьял.\\\\\ В зависимости от структуры и состояния, в котором находится углерод (свободный или химически связанный), различают серые, белые и ковкие чугуны.\\
Как конструкционный материал наиболее широко применяются серые чугуны, в которых весь углерод находится в свободном состоянии в виде включений графита пластинчатой формы. Они обладают средней прочностью, хорошими литейными и другими технологическими свойствами. [Серые с помощью литья. Обозначение СЧ12 СЧ18 показывает, что чугун имеет σut = 18 кгс/мм2 = 180 МПа(пред прочности)]\\ В белых чугунах избыточный углерод, не растворившийся в твердом растворе железа, присутствует в виде карбидов железа. Вследствие низких механических свойств – высокой хрупкости и твердости, плохой обрабатываемости резанием –не применяются в качестве конструкционных материалов.\\ Ковкий чугун получают из белого путем последующего отжига до распада графита в виде хлопьев. Детали из него могут подвергаться незначительным деформациям. Они обладают меньшей по сравнению с деталями из серого чугуна хрупкостью, но стоят на 30 … 100% дороже.\\\\ Марки чугуна обозначаются буквами, показывающими назначение чугуна: СЧ – серый чугун, ВЧ – высокопрочный, КЧ – ковкий чугун; для антифрикционных чугунов в начале марки указывается буква А (АСЧ, АВЧ, АКЧ).\\\\Чугуны также классифицируют в зависимости от назначения – на конструкционные и со специальными свойствами; и от химсостава – на легированные и нелегированные.
|
|
==Стали – это деформируемые сплавы на основе железа с углеродом и другими элементами.
По химсоставу стали делят на углеродистые и легированные. Углеродистые стали содержат кроме железа и углерода также марганец (до 1%) и кремний до (0,8%). Чем выше содержание углерода – тем выше прочность и меньше пластические с-ва.\\\ В состав легированных сталей помимо указанных компонентов для улучшения технологических и эксплуатационных характеристик и придания особых свойств вводят легирующие элементы (хром, никель, молибден, вольфрам, ванадий, титан, ниобий и др.)\\\\По назначению стали делят на конструкционные, инструментальные и с спец назначения\\\ По качеству(от содерж серы и фосфора) стали делят на обыкновенные, качественные, высококачественные. Повышен содерж Серы ведет к хрупкости материяла при повышении температуры(красная ломкость). Повыш содерж Фосфора ведет к хрупкости материяла при понижении температуры(хладно ломкость).
|
|
Распространение получили углеродистой стали обыкновенного качества обозначаются буквами Ст (сталь) и цифрами от 0 до 6, например Ст0 – Ст6. Чем больше число, тем больше содержание углерода в стали, выше прочность и ниже пластичность. Стали поставл по тех харак:Сталь Ст3 Ст0- Ст3-крепежи Ст5-оси,валы\\\\ Углеродистые качественные стали маркируются двузначными цифрами (05 08, 10, 15, …, 65(-пружинная сталь)), показывающими среднее содержание углерода в стали в сотых долях процента. Сталь 45 – содерж углерода С≈0,45%
Нержавеющая сталь Х18Н10Т содержит 18% хрома, 10% никеля и до 1,5% титана. Инструментальные стали маркируют буквой У и цифрами: У9 в среднем 0,9% углерода. Шарикоподшипниковая сталь ШХ15 – с содержанием хрома ≈ 1,5%
Достоинства черных металлов:Широкий диапазон с-в и марок, относительная низк стоимость.
Недостатки: плохо сопротивл коррозии, большая Тплав, больш плотнасть =7,8*103кг/м3, не магнитная, малая удельная прочность.
Поставляются в виде листов, стержней, уголков , тавров, швеллеров и других видов профилей разных размеров, оговоренных стандартами.
|
|
Сплавы на основе меди и алюминия(цвет-мет)
==Медь в чистом виде характеризуется высокой электро- и теплопроводностью, хорошей обрабатываемостью давлением, сопротивление корозии, небольшой прочностью и применяется для изготовления токопроводящих деталей. Более широкое применение получили медные сплавы: латунь и бронза.\\\Латунь-сплавы на основе меди где основ добавкой является ЦИНК. Бывают Двухкомпонентные (Cu,Zn) и для улуч с-в многокомпонентные сплавы.\\\ 2-х комп: Л63 (Медь-63% ост Цинк), Л80 (Cu-80% Zn-20%); многокомп ЛС59-1 (медь-59% Свинец-1% Цинк-40%)\\\\
Бронза- сплавы на основе меди с различ элементами и с Цинком если не основной . По основным легирующим элементам: оловянистые, алюминиевые, бериллиевые, кремнистые и т.д
Широко используются оловянистые бронзы, они характеризуются высокой стойкостью против истирания, низким коэффициентом трения скольжения: БрОЦС 6-6-4 Медь-84% Олово-6% Цинк-6% Свинец-4%\\Алюмин желез бронза БрАЖ9-4 Медь-87 Алюм-9 Желез-4 обладают высокими механическими и антифрикционными свойствами, хорошо обрабатываются. \\\ бериллиевая бронза БрБ2 Берилий-2 Медь-98 высокой прочности и упругости, анти-короз.
|
|
Достоинства: низкая Тплав, в завис от состава прочные и пластич, высокме анти-корозионные с-ва. Недостатки: высокая стоймость
== Алюминий чистый применяется редко, так как имеет низкую прочность(8*). Алюминиевые сплавы в зависимости от технологических свойств делят на деформируемые и литейные.\\\ Наибольшее распространение из деформируемых сплавов получили термически упрочняемые с помощью закалки и старения алюминиево-медно-магниевые Дюрали (дуралюминами) Д1, Д16 и алюминиево-магниевые сплавыАМг6.(магний-6%) обладают высокими механическими свойствами.\\\ Из литейных алюминиевых сплавов наибольше распространение получили сплавы алюминия с кремнием – силумины. Они обладают хорошими литейными и средними механическими свойствами. Силумины марок АЛ-2, АЛ-4, АЛ-9 применяют для изготовления литьем.\\\ Достоинства: анти-короз, не большая плотность, высокая удельная прочность, низ Тплав=660С\\ Недостатки: высокая стоймость.
31/ Пластмассы
Пластмассами называют материалы, получаемые на основе природных или синтетических смол (полимеров), которые при определенных температуре и давлении приобретают пластичность, а затем затвердевают, сохраняя форму при эксплуатации. Кроме связующего вещества (полимера) в состав пластмасс входят наполнители, пластификаторы, отвердители, красители. Наполнители вводят в смолы для повышения механической прочности, теплостойкости, уменьшения усадки и снижения стоимости пластмассы. Пластификаторы увеличивают текучесть, эластичность и уменьшают хрупкость пластмасс. Отвердители ускоряют процесс затвердевания пластмасс, красители придают пластмассам нужный цвет\\\\ По поведению при нагреве полимеров пластмассы делят на термопластичные (термопласты) и термореактивные (реактопласты). Термопласты (полиэтилен, фторопласт, полистирол, полиамиды и др.) имеют свойства обратимости: при повторных нагреваниях они переходят в пластическое или вязкотекучее состояние и им можно придать необходимую форму, а затем они вновь затвердевают при охлаждении. Термореактивные пластмассы не переходят в пластическое состояние при повторном нагревании. Они имеют более высокие, чем термопласты, показатели по твердости, модулю упругости, теплостойкости, сопротивлению усталостной прочности.
Достоинства: анти-короз, блеск поверх, нужный цвет, высокие прочносн с-ва, низкая плотность, малая масса, обладает высокими технолог ч-вами, низкий коэфиц отхода, дешевизна.
Недостатки: изменение с-в с течением времени, температура, плохо переносит нагрузки, не теплопроводна.
32/Понятие о Видах термической и химико-термической обработки стали
Термической обработкой называется процесс изменения в заданном направлении структуры и свойств деталей из металлов и сплавов путем теплового воздействия. Тепловое воздействие может сочетаться с деформационным и химическим.\\\\При изготовлении деталей с использованием литья, сварки и горячей обработки давлением из-за разной скорости охлаждения элементов детали возникают значительные остаточные напряжения. Они могут вызвать искажение формы и размеров детали при последующей механической обработке, эксплуатации или хранении на складе.
При термической обработке (рис) проводят нагрев детали до определенной температуры, выдержку при этой температуре и охлаждение с определенной скоростью. Наиболее широко применяются следующие виды термической и химико-термической обработки: отжиг, нормализация, закалка, отпуск, старение и насыщение поверхностного слоя детали различными элементами.
Отжиг заключается в нагреве выше критических температур, выдержке при данной температуре и последующем медленном охлаждении, обычно вместе с печью. Цели отжига – снизить твердость материала для повышения обрабатываемости, измельчить зерно, снять внутренние напряжения\\ Нормализацию (упорядочение) применяют к металлам и сплавам для измельчения зерна, смягчения и улучшения обрабатываемости резанием, выравнивания механических свойств, снятия внутренних напряжений.\\\ Закалку проводят с целью повышения прочности и твердости деталей, ее можно применять для сталей, содержащих не менее 0,3% углерода. Закалка состоит из нагрева до температур фазовых превращений, выдержки и быстрого охлаждения в воде или масле.\\\ Для снятия остаточных внутренних напряжений после закалки, повышения пластичности при сохранении достаточно высоких прочностных характеристик проводят отпуск.\\\ Старение проводят для стабилизации размеров и свойств деталей после сварки, литья или термообработки.\\\\ Чтобы увеличить износостойкость и коррозионную стойкость детали, проводят насыщение ее поверхности при повышенных температурах разными элементами(азотом,бором,хромом,цинк и тд)
Типовые разьемные соединения
Резьбовые соединения
Резьбовыми называют соединения составных частей изделия с применением деталей, имеющих резьбу. Они наиболее распространены в приборо- и машиностроении. Резьбовые соединения бывают двух типов: соединения с помощью специальных резьбовых крепежных деталей (болтов, винтов, шпилек, гаек) и соединения свинчиванием соединяемых деталей, т.е. резьбы, нанесенной непосредственно на соединяемые детали. Достоинствами резьбовых соединений являются простота, удобство сборки и разборки, широкий диапазон типов и размеров, массовый характер производства, взаимозаменяемость, относительно невысокая стоимость и высокая надежность.// Недостатками резьбовых соединений являются наличие концентраций напряжений, уменьшение прочность соединений; чувствительность к вибрационным и ударным воздействиям, которые могут привести к самоотвинчиванию и низкая точность взаимоположения соединяемых деталей.\\\ Основными крепежными деталями резьбовых соединений являются болты, винты, шпильки, гайки, шайбы и стопорные устройства, предохраняющие гайки от самоотвинчивания. Болт – цилиндрический стержень с шестигранной головкой на одном конце и резьбой – на другом. Болты в соединении используют в комплекте с гайкой, при этом резьба в соединяемых деталях не используется (рис. а).Винты – цилиндрические стрежни с головкой на одном конце и резьбой – на другом. Винт ввертывается в резьбовое отверстие одной из скрепляемых деталей (рис. б), головки винтов могут иметь различную форму Шпилька – цилиндрический стержень с резьбой на обоих концах, одним концом она ввертывается в одну из скрепляемых деталей, а на другой ее конец навертывается гайка (рис. в).
Дата добавления: 2020-01-07; просмотров: 214; Мы поможем в написании вашей работы! |
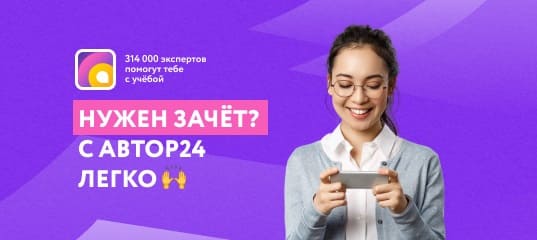
Мы поможем в написании ваших работ!