ГРУППЫ И КАТЕГОРИИ СОСУДОВ И АППАРАТОВ, КОЭФФИЦИЕНТ ПРОЧНОСТИ СВАРНОГО ШВА.
Сварка является основной технологией изготовления стальной сварной химической аппаратуры, когда требуется неразъемно соединить между собой различные ее детали.
Из существующих видов сварки в производстве стальных аппаратов применяется в основном электродуговая сварка разными способами (ручным, автоматическим и полуавтоматическим под флюсом), реже – другие виды сварки (электрошлаковая, газовая, контактная).
В зависимости от толщины соединяемых деталей сварка их производится в один или несколько проходов (слоев).
Сварные швы подлежат контролю качества соединения (внешним осмотром, измерением, механическими испытаниями, металлографическим исследованием, ультразвуковой дефектоскопией, просвечиванием рентгеновскими или γ-лучами, замером твердости, в ряде случаев испытанием на межкристальную коррозию и гидравлическим и пневматическим испытанием).
Коэффициент прочности сварного шва (φ) зависит от вида шва, типа сварки, процентного объема контролируемых швов. Все аппараты делятся на 5 групп приведенных в таблице 3.1.
Группу сосуда с полостями, имеющими различные расчетные параметры и среды, допускается определять для каждой полости отдельно. Сосуды, работающие под вакуумом или без давления (под наливом), независимо от расчетного давления следует отнести к группе 5а или 5б. Объем контролируемых швов для аппаратов: 1-й группы - 100% всех сварных швов; 2-й и 3-й групп 50%; 4-й группы 25%; для остальных 10%. Выбор групп производится по табл.2.1.
|
|
Таблица 2.1 - Группа сосуда
Группа | Расчетное давление, Мпа | Температура стенки, °С | Рабочая среда |
1 | 2 | 3 | 4 |
1 | Более 0,07 (0,7) | Независимо | Взрывоопасная или пожароопасная или 1-го, 2-го опасности |
2 | Более 0,07 (0,7) До 2,5 (25) | Выше 400 | Любая, за исключением указанной для 1-й группы сосудов |
Более 2,5 (25) До 5,0 (50) | Выше 200 | ||
Более 5,0 (50) | Независимо | ||
Более 4,0 (40) До 5,0 (50) | Ниже минус 40 | ||
3 | Более 0,07 (0,7) До 1,6 (16) | Ниже 20 От 200 до 400 | |
Более 1,6 (16) До 2,5 (25) | До 400 | ||
Более 2,5 (25) До 4,0 (40) | До 200 | ||
Более 4,0 (40) До 5,0 (50) | От минус 40 до 200 | ||
4 | Более 0,07 (0,7) До 1,6 (16) | От минус 20 до 200 | |
5а | До 0,07 (0,7) | Независимо | Взрывоопасная или пожароопасная или 1-го, 2-го классов опасности |
5б | До 0,07 (0,7) | Независимо | Взрывобезопасная или пожаробезопасная или 4-го класса опасности |
В зависимости от массы и габаритов аппарата, доступных к перевозке по железной дороге, все аппараты делятся на 5 категорийВ случае, если значения m, D или L будут большими, чем указано в таблице, аппарата должен транспортироваться по железной дороге соответствующими частями с соединением (сваркой или на фланцах) их на монтажной площадке. В этом случае сварка ручная с односторонним проваром, если аппарат может транспортироваться целиком, то сварной шов стыковкой или тавровой с двухсторонним сплошным проваром, выполняемый автоматической и полуавтоматической сваркой сварка. В зависимости от длины контролируемых швов и категории аппарата, т.е. вида шва выбирается коэффициент прочности сварного шва (φ) из таблицы 3.4
|
|
Таблица 2.4 - Коэффициенты прочности сварных швов
Вид сварного шва (по группам) | Значение коэффициентов прочности сварных швов | |
Длина контролируемых швов от общей длины составляет 100% | Длина контролируемых швов от общей длины составляет от 10 до 50% | |
Стыковой или тавровой с двухсторонним сплошным проваром, выполняемый автоматической и полуавтоматической сваркой | 1,0 | 0,9 |
Стыковой с подваркой корня шва или тавровый с двухсторонним сплошным проваром, выполняемый вручную | 1,0 | 0,9 |
Стыковой, доступный к сварке только с одной стороны и имеющий в процессе сварки металлическую подкладку со стороны корня шва, прилегающую по всей длине шва к основному металлу (ручная) | 0,9 | 0,8 |
Стыковой, выполняемыйавтома-тической и полуавтоматической сваркой с одной стороны с флюсовой или керамической подкладкой | 0,9 | 0,8 |
Стыковой, выполняемый вручную с одной стороны | 0,9 | 0,65 |
В тавр, с конструктивным зазором свариваемых деталей | 0,8 | 0,65 |
|
|
НОРМЫ ГИДРАВЛИЧЕСКОГО И ПНЕВМАТИЧЕСКОГО ИСПЫТАНИЙ АППАРАТОВ (ДАВЛЕНИЕ, ВРЕМЯ ВЫДЕРЖКИ, МЕТОДЫ КОНТРОЛЯ И Т.Д.).
Все физико-химические процессы, осуществляемые в химических аппаратах, прежде всего, требуют наличия емкости, ограниченной корпусом. Эти корпуса, по условиям протекающих вних процессов, должны быть достаточно прочными и в подавляющем большинстве случаев герметичными. Гидравлическое испытание проводится для проверки плотности сварных швов и других соединений, а также дает возможность установить качество изготовления и сборки аппарата. Гидравлическому испытанию подлежат все сосуды после их изготовления. Сосуды, имеющие защитное покрытие или изоляцию, после изготовления подвергаются гидравлическому испытанию до наложения покрытия или изоляции. Сосуды, имеющие наружный кожух, подвергаются гидравлическому испытанию до установки кожуха. Допускается эмалированные сосуды подвергать гидравлическому испытанию рабочим давлением после эмалирования. Давление, при котором проводится испытание, называется пробным Рпр.
|
|
Где Р - расчетное давление сосуда, МПа (кгс/см2);
[s]20, [s]t - допускаемые напряжения для материала сосуда или его элементов соответственно при 20 °С и расчетной температуре, МПа (кгс/см2).
Гидравлическое испытание сосудов, устанавливаемых вертикально, допускается проводить в горизонтальном положении при условии обеспечения прочности корпуса сосуда. При этом разработчик сосуда должен выполнить расчет на прочность с учетом принятого способа опирания для проведения гидравлического испытания. Пробное давление следует принимать с учетом гидростатического давления, действующего на сосуд в процессе его эксплуатации. Для гидравлического испытания сосуда должна использоваться вода. Допускается по согласованию с разработчиком сосуда использование другой жидкости. Температура воды должна приниматься не ниже критической температуры хрупкости материала сосуда и указываться разработчиком сосуда в технической документации. При отсутствии указаний температура воды должна быть в пределах от +5 до +40 °С. Разность температур стенки сосуда и окружающего воздуха во время испытания не должна вызывать конденсацию влаги на поверхности стенки сосуда. При заполнении сосуда водой должен быть удален воздух из внутренних полостей. Давление следует поднимать равномерно до достижения пробного. Обычно скорость подъема давления не должна превышать 0,5 МПа в минуту, если нет других указаний разработчика сосуда в технической документации. Использование сжатого воздуха или другого газа для подъема давления не допускается. Давление при испытании должно контролироваться не менее чем двумя манометрами. Манометры выбираются одного типа, предела измерения, одинаковых классов точности, цены деления. Время выдержки сосуда под пробным давлением устанавливается разработчиком проекта. Время выдержки сосуда под пробным давлением зависит от толщины стенки сосуда:
- до 50 мм - 10 минут
- свыше 50 до 100 мм – 20 минут
- свыше 100 мм
После выдержки под пробным давлением оно снижается до расчетного, при котором производят осмотр наружной поверхности сосуда, всех его разъемных и сварных соединений. Обстукивание стенок корпуса, сварных и разъемных соединений, сосуда во время испытаний не допускается.
Сосуд считается выдержавшим гидравлическое испытание, если не обнаружено:
- течи, трещин, слезок, потения в сварных соединениях и на основном металле;
- течи в разъемных соединениях;
- видимых остаточных деформаций, падения давления по манометру.
Сосуд и его элементы, в которых при испытании выявлены дефекты, после их устранения подвергаются повторным гидравлическим испытаниям пробным давлением, установленным «Правилами устройства и безопасной эксплуатации сосудов, работающих под давлением». После проведения гидравлического испытания вода должна быть полностью удалена. Допускается не считать течью пропуски испытательной среды через неплотности арматуры, если они не мешают сохранению пробного давления. Испытание сосудов, работающих без давления (под налив), проводится смачиванием сварных швов керосином или наливом воды до верхней кромки сосуда. Время выдержки сосуда при испытании наливом воды должно быть не менее 4 часов. Контроль сварных швов на герметичность допускается проводить капиллярным методом.
91. ТОНКОСТЕННЫЕ СОСУДЫ И АППАРАТЫ (ТСА). ОБЩИЕ СВЕДЕНИЯ О ПЛАСТИНАХ И ОБОЛОЧКАХ (ОСНОВНЫЕ ПОНЯТИЯ И ОПРЕДЕЛЕНИЯ).
ТОНКОСТЕННЫЕ СОСУДЫ— сосуды, толщина стенок к-рых мала по сравнению с величиной наименьшего радиуса кривизны. Определение тонкостенные сосуды условно и зависит от допустимой точности расчета. Сосуды можно рассматривать как тонкостенные с погрешностью менее 5%, если отношение радиуса (R) к толщине (а) больше 10 (у цилиндрических сосудов) и более 3,5 (у сферич.). Если тонкостенный сосуд не имеет резких переходов, жестких закреплений, не нагружен сосредоточенными силами и моментами, а также во всех сечениях, достаточно удаленных от мест приложения сосредоточенных нагрузок и закреплений, к его расчету может быть применена безмоментная теория оболочек, предполагающая постоянство норм, напряжений по толщине стенки. Для определения напряжений по безмоментной теории достаточно рассмотреть два уравнения равновесия. Первое получается из условия равновесия элемента, вырезанного в оболочке двумя меридиональными и двумя коническими сечениями, после проектирования всех сил на ось z и приводится к уравнению Лапласа
Если тонкостенный сосуд сделан из пластичного материала, для к-рого резкие перенапряжения в небольшой области при статическом на- гружении мало сказываются на несущей способности системы, он может быть рассчитан по безмоментной теории. В случае многократного приложения нагрузки у пластичных материалов запас усталостной прочности, а также запас прочности у хрупких материалов при статической нагрузке необходимо определять с учетом местных напряжений, для чего вычисляются изгибающие моменты и перерезывающие силы. Необходимые для этого формулы получаются из уравнений технич. теории моментных оболочек. Актуальными являются также задачи, связанные с учетом пластических деформаций и деформаций ползучести при расчете тонкостенных сосудов. При всем разнообразии машин и аппаратов, применяемых в газонефтепереработке, их можно представить состоящими из пластин и оболочек, соединенных друг с другом как разъемными, так и неразъемными соединениями.
Оболочкой называется тело, два размера которого значительно больше третьего (толщины стенки S).
Оболочкой вращенияназывается оболочка, образованная вращением какой-либо плоской кривой вокруг оси, лежащей в ее плоскости и на пересекающей ее (рисунок 3.1.1). Оболочку вращения называют осесимметричной, если она нагружена равномерно распределенными относительно оси нагрузками. В простейшем случае примерами осесимметричных оболочек могут служить сферическая, цилиндрическая, коническая и эллиптическая оболочки вращения, нагруженныевнутренним газовым давлением Р.
.
Рисунок 3.1.1 – Оболочка вращения
Кроме того, к таким оболочкам относится колонный аппарат, расположенный вертикально и заполненный жидкой средой (рисунок 3.1.2), т.к. в этом случае нагрузка вдоль оси изменяется постепенно, без резких скачков.
Рисунок 3.1.2 – Эпюра распределения гидростатического давления для колонного аппарата
В горизонтальном аппарате (рисунок 3.1.3), заполненном водой, каждая точка поперечного сечения испытывает разное давление и поэтому эта оболочка уже не относится к осесимметричным.
При изображении оболочек обычно не показывают толщину стенки, а оперируют понятием срединной поверхности.
Срединная поверхность– это поверхность, равноудаленная от наружной и внутренней поверхностей.
Рисунок 3.1.3 – Эпюра распределения гидростатического давления для горизонтального аппарата внутренней поверхностей оболочки
Меридианаминазываются кривые, образованные пересечением срединной поверхности плоскостями, проходящими через ось симметрии оболочки (рисунок 3.1.4).
Рисунок 3.1.4 – Срединная поверхность
Параллелями(параллельными кругами или кольцевыми сечениями) называются окружности, образованные пересечением срединной поверхности плоскостью, перпендикулярной оси оболочки.
Полюсом оболочки называется точка пересечения срединной поверхности с осью (рисунок 3.1.5).
Рисунок 3.1.5 – Основные параметры оболочки
Параметры rm, rt называются радиусами кривизны соответственно меридиана и параллельного круга.
92 НАПРЯЖЕННОЕ СОСТОЯНИЕ МАТЕРИАЛА УПРУГИХ ОСЕСИММЕТРИЧНЫХ ОБОЛОЧЕК (ТОНКОСТЕННЫХ И ТОЛСТОСТЕННЫХ (СОСУДОВ ВЫСОКОГО ДАВЛЕНИЯ - СВД)), НАХОДЯЩИХСЯ ПОД ВОЗДЕЙСТВИЕМ ВНУТРЕННЕГО ДАВЛЕНИЯ. ПРИЧИНЫ И ПРИЗНАКИ ДЕЛЕНИЯ СОСУДОВ НА ТОНКО И ТОЛСТОСТЕННЫЕ.
Дата добавления: 2019-11-25; просмотров: 2335; Мы поможем в написании вашей работы! |
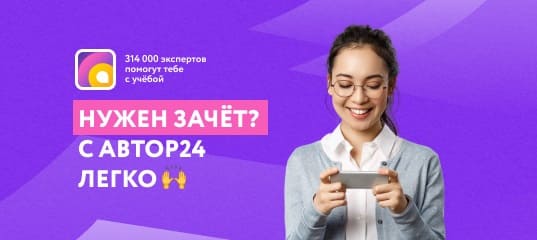
Мы поможем в написании ваших работ!