Стали углеродистые качественные
Углеродистые конструкционные качественные стали обозначают двузначным числом, указывающим среднее содержание углерода в сотых долях процента (например, 05, 10, 15, , 80, 85) для обозначения котельных марок в конце ставится буква К ( например 20К ).
Качественными углеродистыми сталями являются стали марок 08, 10, 15, 20 …, 75, 80, 85. К этому классу относятся также стали с повышенным содержанием марганца (0,7 – 1,0 %) марок 15Г, 20Г, 25Г ..., 65Г, имеющих повышенную прокаливаемость. Низкоуглеродистые стали марок 08, 08кп, 08пс относятся к мягким сталям, применяемым чаще всего в отожженном состоянии для изготовления деталей методом холодной штамповки - глубокой вытяжки. Стали марок 10, 15, 20, 25 обычно используют как цементуемые, а высокоуглеродистые стали 60, 65, 70, 75, 80 и 85 в основном применяют для изготовления пружин, рессор, высокопрочной проволоки и других изделий с высокой упругостью и износостойкостью. Среднеуглеродистые стали 30, 35, 40, 45, 50 и аналогичные стали с повышенным содержанием марганца 30Г, 40Г, 50Г применяют для изготовления самых разнообразных деталей машин. При этом в зависимости от условий работы деталей применяют различные виды термической обработки: нормализацию, улучшение, закалку с низким отпуском, закалку ТВЧ и др. Механические свойства каждой стали можно изменять в широком диапазоне в зависимости от режима термической обработки и для каждой конкретной детали, условий ее эксплуатации должны быть выбраны оптимальный комплекс механических свойств и соответствующая обработка.
|
|
Конструкционные материалы, их классификация. Черные металлы. Сталь легированная, классификация, маркировка, область применения
Основным конструкционным материалом для аппаратуры нефтехимии является сталь, поставляемая в виде листового и сортового проката, труб или отливок.
Применяют также чугун и цветные металлы. Неметаллические материалы; в том числе полимерные, в качестве конструкционных применяют редко; они служат в основном для облицовки или футеровки оборудования и отдельных узлов и деталей.
Сталь и чугун составляют группу черных металлов. Черные металлы – это сплав железа с углеродом и другими химическими элементами, при этом содержание железа должно быть не мене 45%, а углерода до 4,5%.
Сталь
Промышленность выпускает разнообразные по назначению стали, отличающиеся по химическому составу и свойствам. Многообразие сталей необходимо в связи с тем, что машины и аппараты, отдельные их узлы и детали работают в различных условиях: при высоких и низких температурах ( от –250 до +1100оС ) в вакууме и повышенных давлениях, в коррозионной и абразивной среде, в условиях трения скольжения и качения, в условиях ударных, температурных и знакопеременных нагрузок и т. д.
|
|
Сталь - сплав железа с углеродом ( до 2,1 % ) и другими химическими элементами ( примесями и лигирующими добавками ).
Легирующие элементы - химические элементы, специально введенные в сталь для получения требуемых строения, структуры, физико-химических и механических свойств.
Основными легирующими элементами в сталях являются Мn, Si, Сr, Ni, Мо, W, Со, Сu, Тi, V, Zr, Nb, Аl, B. В некоторых сталях легирующими элементами могут быть также Р, N, S, Рb, и др. Перечисленные элементы, а также Н, O, Sn, Sb, Вi могут быть и примесями в стали. Содержание легирующих элементов может колебаться от тысячных долей процента до десятков процентов.
Примесями называют химические элементы, перешедшие в состав стали в процессе ее производства как технологические добавки или как составляющие шихтовых материалов. Их содержание обычно ограничивается следующими пределами: Мn <=0,8 %, Si <=0,4 %, Сr <= 0,3 %, Ni <=0.3 %, Сu <=0,3 %, Мo <=0.1 %, W <=0,2 %, Р <=0,025-0,04 %, S <=0,015-0,05 %. В литейных марках в качестве примесей может содержаться до 0,9 % Мn, до 0,5 % Si, до 0,06 % S и до 0,08 % Р.
Классификация сталей
По химическому составу стали и сплавы черных металлов условно подразделяют на углеродистые (без легирующих элементов), низколегированные, среднелегированные, высоколегированные, сплавы на основе железа.
|
|
Углеродистые стали не содержат специально введенных легирующих элементов. В низколегированных сталях суммарное содержание легирующие элементов должно быть не более 2,5 % (кроме углерода), в среднелегированных - от 2,5 до 10 %, в высоколегированных - более 10 % при содержании в них железа не менее 45 %. Сплавы на основе железа содержат железа менее 45 %, но его количество больше, чем любого другого элемента.
По назначению стали разделяют на конструкционные, инструментальные и стали с особыми физическими и химическими свойствами. Внутри классификации существуют более узкие подразделения сталей как по назначению, так и по свойствам.
По структуре классификация в значительной степени условна.
В равновесном состоянии стали, подразделяют на доэвтектоидные, эвтектоидные и заэвтектоидные.
После охлаждения на воздухе образцов небольшого сечения с температуры приблизительно 900оС стали подразделяют на перлитные, бейнитные, мартенситные, ледебуритные, ферритные и аустенитные.
По качеству стали подразделяют на стали обыкновенного качества, качественные, высококачественные и особо высококачественные. Главными признаками по качеству стали являются более жесткие требования по химическому составу и, прежде всего, по содержанию вредных примесей, таких как фосфор и сера.
|
|
Категория обыкновенного качества относится только к углеродистым сталям, все остальные категории качества могут относиться к любым по степени легирования сталям.
Легированные стали – это сплавы на основе железа, в химический состав которых специально введены легирующие элементы, обеспечивающие при определенных способах производства и обработки требуемую структуру и свойства. В легированных сталях содержание отдельных элементов больше, чем этих же элементов в виде примесей.
Такие легирующие элементы, как V, Nb, Тi, Zr, В, могут оказывать существенное влияние на структуру и свойства стали при их содержании в стали в сотых долях процента. Иногда такие стали называют микролегированными.
Легированные стали маркируются комплексом цифр и букв, причем первые две цифры указывают на содержание углерода в сотых долях процента (отсутствие цифр означает, что среднее содержание углерода составляет около 0,01%), затем последовательно указываются буквы, означающие наличие в стали того или иного легирующего элемента, за каждой из букв одной или двумя цифрами указывается примерное содержание данного элемента в процентах (отсутствие цифр означает, что содержание данного элемента составляет до 1,5%).
Обозначения в марках стали: Г – марганец, С – кремний, Х – хром,
Н – никель, М – молибден, В – вольфрам, Ф – ванадий, Т – титан, Д – медь, Ю – алюминий, Б – ниобий, Р – бор, А – азот (в конце обозначения не ставятся). Буква "А" в конце марки указывает, что сталь относится к категории высококачественной (30ХГСА), если та же буква в середине марки – сталь легирована азотом (16Г2АФ), в начале марки буква "А" указывает на то, что сталь повышенной обрабатываемости (автоматная) – А35Г2. Индекс "АС" в начале марки указывает, что сталь повышенной обрабатываемости (автоматная) со свинцом (АС35Г2), а Ш (через дефис) – особо высококачественную.
Цифры после буквы в обозначении марки стали показывают примерное количество того или иного элемента, округленное до целого числа. При среднем содержании легирующего элемента до 1,5 % цифру за буквенным индексом не приводят. Содержание углерода указывается в начале марки в сотых (конструкционные стали) или десятых (инструментальные стали) долях процента. Например, конструкционная сталь, содержащая 0,42 – 0,5 % С; 0,5 – 0,8 % Мn; 0,8 – 1,0 % Сr; 1,3 – 1,8 % Ni; 0,2 – 0,3 % Мо и 0.1 – 0,18 % V, обозначается маркой 45ХН2МФ.
В зависимости от количества легирующего элемента легированная сталь, как было сказано ранее, подразделяется на:
Биметалл
Для изготовления нефтезаводской аппаратуры широко применяется биметалл – двухслойный лист, состоящий из двух различных металлов. Основной (толстый) лист воспринимает нагрузку. Тонкий слой, называемый защитным или плакирующим, предохраняет основной слой от коррозионного действия среды: обычно в расчетах на прочность толщину тонкого слоя не учитывают. Толщина двухслойных листов по ГОСТ может быть в пределах от 4 до 160 мм.
Основной слой биметалла выполняется обычно из углеродистых сталей ВСт3сп5; 20К; марганцовистых сталей 16ГС, 09Г2С, теплоустойчивой хромомолибденовой стали 12ХМ и др. Защитный слой биметалла толщиной 1 – 6 мм выполняют из сталей 08Х13, 12Х18Н10Т, 10Х17Н13М2Т (для особо агрессивных сред), монеля, никеля и др. марок высоколегированных сталей и сплавов.
Для изготовления труб конденсационно-холодильного оборудования находит применение и биметалл: внутренняя часть труб изготовляется из стабилизированной алюминиевой латуни, а наружная часть – из малоуглеродистой стали.
Применение таких труб дает возможность значительно сократить потребление дефицитных медных сплавов.
Для устранения коррозии холодильников и теплообменников легких дистиллятов под действием H2S, NH3, и СО2 с успехом применяются биметаллические трубы (алюминий – латунь). Алюминиевое покрытие трубы играет роль протектора.
87 ОСНОВНЫЕ ПОЛОЖЕНИЯ ПРАВИЛ ПО РАСЧЕТУ И УСТРОЙСТВУ СВАРНЫХ АППАРАТОВ. РАСЧЕТНЫЕ ПАРАМЕТРЫ (ТЕМПЕРАТУРА, ДАВЛЕНИЕ ДЛЯ РАБОЧИХ УСЛОВИЙ И УСЛОВИЙ ИСПЫТАНИЙ).
Основными расчетными параметрами для выбора конструкционного материала и расчета элементов аппарата на прочность являются температура и давление рабочего процесса.
1 Температура.
Различают рабочую и расчетную температуры.
Рабочая температура t – это температура содержащейся или перерабатываемой среды в аппарате при нормальном протекании в нем технологического процесса.
Расчетная тампература tR – это температура стенки для определения физико-механических характеристик конструкционного материала и допускаемых напряжений. Она определяется на основании выполнении теплового расчета или результатов испытаний. В случае невозможности выполнения теплового расчета, а также, если при эксплуатации температура элемента аппарата может повыситься до температуры соприкасающейся с ним среды, расчетная температура принимается равной рабочей, но не менее 20°С. При обогревании элемента открытым пламенем, горячими газами с температурой свыше 250°С или открытыми электронагревателями расчетная температура принимается равной температуре среды плюс 50°С. При наличии у аппарата тепловой изоляции расчетная температура его стенок принимается равной температуре поверхности изоляции, соприкасающейся со стенкой, плюс 20°С. При отрицательной рабочей температуре элемента за расчетную (для определения допускаемых напряжений) принимается температура, равная 20°С.
Давление
Различают рабочее, расчетное, условное (номинальное) и пробное давления.
Рабочее давление р– максимальное внутреннее избыточное или наружное давление среды в аппарате при нормальном протекании технологического процесса без учета гидростатического давления и допускаемого кратковременного повышения давления во время действия предохранительного устройства (клапана и др.). Если технологический процесс в аппарате протекает при разрежении, то рабочим давлением является вакуум.
Расчетное давление pR– максимальное допускаемое рабочее давление, на которое производится расчет на прочность и устойчивость элементов аппарата при максимальной их температуре. Как правило, расчетное давление принимают равным рабочему давлению или выше.
Расчетное давление может быть выше рабочего в следующих случаях: если во время действия предохранительных устройств давление в аппарате может повыситься более чем на 10% от рабочего, то расчетное давление должно быть равно 90% давления в аппарате при полном открытии предохранительного устройства; если на элемент действует гидростатическое давление от столба жидкости в аппарате, значение которого свыше 5% расчетного, то расчетное давление для этого элемента соответственно повышается на значение гидростатического давления.
Расчетным давлением при испытаниях аппарата является пробное давление.
Условное (номинальное) давлениеру– избыточное рабочее давление при температуре элемента аппарата 20°С (без учета гидростатического давления).
Для более высоких температур элементов аппарата условное давление снижается соответственно уменьшению прочности конструкционного материала.
Условные давления применяют при стандартизации аппаратов и их узлов.
Согласно ГОСТ 356—68, применительно к рассматриваемым аппаратам рекомендуется следующий ряд условных давлений, МПа: 0,1; 0,25; 0,4; 0,6; 1,0; 1,6; 2,5; 4,0; 6,4; 10; 16; 20.
Пробное давлениерпр – избыточное давление, на которое аппарат испытывается на прочность и плотность после его изготовления и периодически при эксплуатации. Значения пробного давления в зависимости от рабочего давления приведены в таблице 2.1.
88)ДОПУСКАЕМЫЕ НАПРЯЖЕНИЯ, МЕТОДЫ ОПРЕДЕЛЕНИЯ ДЛЯ РАБОЧИХ УСЛОВИЙ И УСЛОВИЙ ИСПЫТАНИЙ. КОЭФФИЦИЕНТЫ ЗАПАСА ПРОЧНОСТИ.
Допускаемое напряжение [ ] при расчете по предельным нагрузкам аппаратов, работающих при статистических однократных нагрузках, определяют в соответствии с ГОСТ 14249 – 89 (СТ СЭВ 596 – 86):
– для углеродистых и низкоуглеродистых сталей
; (2.1)
– для аппаратов из аустенитных сталей
(2.2)
Для условий испытания аппаратов из углеродистых и низколегированных сталей допускаемые напряжения определяют по формуле:
. (2.3)
– для аппаратов из аустенитных сталей
. (2.4)
В зависимостях 2.1 – 2.4 напряжения при расчетной температуре имеют следующие значения:
– минимальное значение предела текучести;
– минимальное значение условного предела текучести, при котором остаточное удлинение составляет 0,2%;
– минимальное значение предела текучести при температуре 20 °С;
,
– минимальные значения предела текучести и условного предела текучести при температуре 20°С, при которых остаточные удлинения составляет соответственно 0,2 и 1,0%;
– минимальное значение временного сопротивления (предела прочности);
– среднее значение предела длительной прочности за 105ч;
– среднее значение 1%-го предела ползучести за 105ч.
Коэффициенты запаса прочности должны соответствовать значениям, приведенным в таблице 2.2.
Таблица 2.2 Значения коэффициентов запаса прочности
Условие нагружения | Коэффициент запаса прочности | |||
![]() | ![]() | ![]() | ![]() | |
Рабочие условия Условия испытания: гидравлические испытания пневматические испытания Условия монтажа | 1,5 1,1 1,2 1,1 | 2,4 ― ― ― | 1,5 ― ― ― | 1,0 ― ― ― |
Расчет на прочность цилиндрических обечаек и конических элементов, выпуклых и плоских днищ для условий испытания проводить не требуется, если расчетное давление в условиях испытания будет меньше, чем расчетное давление в рабочих условиях, умноженное на .
Для элементов сосудов и аппаратов, работающих в условиях ползучести при разных за весь период эксплуатации расчетных температурах, в качестве допускаемого напряжения разрешается принимать эквивалентное допускаемое напряжение [у]экв, рассчитываемое по формуле:
, (2.5)
где – допускаемое напряжение для расчетного срока эксплуатации при температурах ti (i = 1,2,…);
Тi – длительность этапов эксплуатации элементов с температурой стенки соответственно ti (i = l, 2,...), ч;
– общий расчетный срок эксплуатации, ч;
m– показатель степени в уравнениях длительной прочности стали (для легированных жаропрочных сталей рекомендуется принимать m = 8).
Этапы эксплуатации: при разной температуре стенки рекомендуется принимать по ступеням температуры 5 и 10°С.
Коэффициент запаса устойчивости при расчете элементов аппаратов на устойчивость по нижним критическим напряжениям в пределах упругости принимается: для рабочих условий nu= 2,4; для условий испытаний и монтажа nu = 1,8.
Исполнительные или принимаемые при конструировании размеры рассчитываемых элементов, как правило, должны быть больше расчетных на значение прибавки:
s ≥sR+ c; (2.6)
При наличии данных о пределе длительной прочности при расчетной температуре допускаемое напряжение для цветных металлов, за исключением алюминиевых литейных сплавов, допускается определить по формуле:
где а10– минимальное значение условного предела текучести при 1%-ном остаточном удлинении при расчетной температуре, МПа;
– коэффициент запаса прочности по условному пределу текучести;
– коэффициент запаса прочности по временному сопротивлению при наличии данных о пределе длительной прочности;
– среднее значение предела длительной прочности за время т часов при расчетной температуре, МПа;
– коэффициент запаса прочности по пределу длительной прочности.
При отсутствии данных об условном пределе текучести при 1% -ном остаточном удлинении используют значение условного предела текучести при 0,2%-ном остаточном удлинении.
Дата добавления: 2019-11-25; просмотров: 229; Мы поможем в написании вашей работы! |
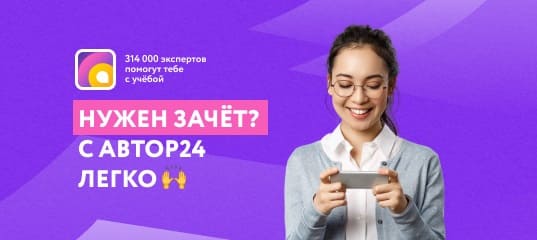
Мы поможем в написании ваших работ!