Отличительные особенности работы комплекса ГД - гребной винт в период старта судна. Факторы, определяющие перегрузку ГД, валопровода. 11 страница
Контролируемые параметры при определении категории технического состояния газотурбокомпрессоров. Признаки загрязнения компрессоров. Критерий неудовлетворительного технического состояния проточной части.
Параметры:
мощность ГД
температуры газов и давление газов перед турбиной
давление наддува
Признаком загрязнения проточной части ГТК может служить повышение температуры воздуха за ним.
Вопрос 60
Оценка ТС в процессе эксплуатации насосов может быть произведена различными способами, например, по отклонению рабочих параметров от эталонных характеристик, возникновению кавитационных режимов, контролю уровня вибрации и ударных импульсов и др. В результате контроля устанавливаются возможные неисправности с последующим отнесением насоса к определенной категории его ТС. В большинстве случаев ограничиваются контролем давления нагнетания - напора (в случае центробежных насосов при закрытых и открытых нагнетательных клапанах), давления всасывания и силы тока электродвигателя.
Снижение подачи и напора насоса может быть связано с различными причинами. Например, с эрозией рабочего колеса, шестерен и винтов, поломкой лопаток и зубьев, отложениями на рабочих узлах, износом внутренних уплотнений и т.п. Величина снижения подачи и напора насоса определяется по уменьшению давления за насосом при следующих условиях: нормально открытые клапаны на всасывающем и нагнетательном трубопроводе, чистые фильтры и отсутствие неплотностей в соединениях.
|
|
Обнаружение разрушения подшипников, попадание посторонних предметов и заклинивание рабочих органов насосов, износ внутренних уплотнений и смещение рабочего колеса возможно при контроле за током электродвигателя с использованием штатных приборов.
При наличии у центробежных насосов вакуум-насоса их ТС контролируется по поддержанию вакуума на входе в насос. При этом рекомендуется предварительно убедиться в плотности системы перед насосом.
При контроле уровня ударных импульсов необходимо иметь в виду, что максимальные значения ударных импульсов могут возникнуть в направлении действия сил на подшипники. Например, у аксиально-плунжерных насосов измерения рекомендуется проводить в плоскости вращения качающего узла. Нормы ТС насосов
По уровню ударных импульсов можно судить о наличии кавитации насосов, срывах потока, износа уплотнений, шестерен, винтов и колес, и подсоса воздуха. При измерении высокого уровня ударных импульсов на подшипниках вихревых и шестеренных насосов необходимо предварительно установить, не является ли их причиной срывные явления в насосе.
|
|
Колебания уровня ударных импульсов в эксплуатации вследствие изменения режима, температурных условий и деформации корпуса судна, а также воспроизводимости приборов может составлять 5-6 ДБ.
При использовании уровня вибрации в процессе контроля ТС насосов должно соблюдаться следующее условие: измерению вибрации должно предшествовать измерение ударных импульсов, с целью установления состояния подшипников и их влияния на общую вибрацию насоса.
Обычно уровень виброскорости (миллиметр в секунду, среднее квадратичное значение) измеряется в таких частотных диапазонах:
- на основной частоте (f о = n/60) , где n- частота вращения, об/мин;
- на лопаточной частоте (f л=Zл/ fо), где Z л - число лопаток или зубьев рабочего колеса, число винтов.
В первом случае выявляются состояния балансировки и центровки, а также проверяется вторая гармоника. Во втором - состояние проточной части и кавитационные явления.
При выборе частотного диапазона рекомендуется руководствоваться типовыми спектрами вибрации насосов.
Типовые спектры вибрации насосов
Рис.10.5 (1 - нарушение центровки; 2 - кавитация). Нормы вибрации, соответствующие трем категориям ТС насосов и электродвигателей, приведены на рис.10.6.
|
|
Нормы вибрации насосов
Рис. 10.6. (l - хорошее ТС; II - удовлетворительное; III - неудовлетворительное).
Колебания уровня вибрации в эксплуатации, связанные с изменением режима и температуры окружающей среды, деформациями корпуса судна, а также воспроизводимости приборов, лежат в пределах 1-2 мм/с.
Степень ТС насосов может быть определена в процессе контроля и по их тепловому состоянию. С этой целью, например, применительно к насосам с подшипниками скольжения оценивается и фиксируется первоначальный уровень разности температур Δ t — tn — ta (tn- температура на поверхности корпуса подшипника; tа - окружающей среды). Повышение Δtn от первоначального уровня на 15-20°С свидетельствует о неисправности подшипника скольжения.
Кроме того, определение ТС насосов может быть осуществлено путем осмотра и при неразрушающем контроле. При этом следует учитывать следующие обстоятельства. Для определения местного уменьшения толщины корпуса насоса из-за кавитационного разрушения используется толщиномер. Контроль толщины корпуса применительно к центробежным насосам рекомендуется производить после 8 лет эксплуатации. Уменьшение толщины корпуса на 20-30% следует считать предельным. Для более крупных насосов предусматривается осмотр рабочего колеса.
|
|
Для этой цели целесообразно использовать эндоскоп. В случае продолжительной работы в кавитационном режиме необходима разборка насоса. Это может быть совмещено с очередным освидетельствованием. При систематических протечках через сальник рекомендуется производить осмотр вала под ним.
61. Способы контроля технического состояния вентиляторов. Факторы, влияющие на изменение балансировки рабочего колеса, центровки, состояния амортизаторов и крепление вентилятора к фундаменту. Нормы вибрации при неудовлетворительном техническом состоянии.
Контроль ТС вентиляторов осуществляется по уровню ударных импульсов и вибрации. В частности, уровень ударных импульсов используется для контроля ТС подшипников качения приводных электродвигателей. С помощью этого параметра определяется наличие повреждений и состояние смазки. По значению уровня вибрации устанавливается изменение балансировки рабочих колес, обусловленное нарушением соединений лопаток с дисками, вмятинами, прогибами, поломками лопаток, ослаблением посадки рабочего колеса на валу, определяется несоответствие центровки, связанной с неправильным выбором радиальных, торцовых зазоров между рабочим колесом и корпусом, а также состояние амортизаторов и крепление вентилятора к фундаменту. Измерение уровня вибрации производится в районе подшипников электродвигателя вгоризонтальной и вертикальной плоскостях Измерения рекомендуется производить после ТО или ремонта по истечении времени приработки, но не ранее чем через час после включения вентилятора в работу. Уровень измерения виброскорости осуществляется на основной частоте. По его значению представляется возможность оценить состояние балансировки и центровки. Нормы вибрации вентиляторов в зависимости от категории их ТС приведены на рис. В качестве примера для контроля ТС конкретных типов вентиляторов (например, В КО 40/63) можно привести следующие данные: при хорошем ТС значение виброскорости должно быть менее 2.2 мм/с, ударных импульсов - менее 20 дБ и соответственно при удовлетворительном - 2.2-5,1 и 20-40, неудовлетворительном - более 5.1 и более 20. При эксплуатации вентиляторов с указанным уровнем ударных импульсов и вибрации контроль ТС в первом случае рекомендуется осуществлять через 12 мес, а во втором – через 6 мес.
V мм/с
N, кВт
. 10. Нормы вибрации вентиляторов в зависимости от категории их технического состояния: I - хорошее; П - удовлетворительное; Ш – неудовлетворительное
62. Показатели, оценивающие качество работы топливных сепараторов. Контролируемые параметры. Внешние признаки, характеризующие наличие неисправностей. Нормы вибрации в зависимости от категории технического состояния.
Контроль ТС центробежных сепараторов осуществляется на основании анализа информации, полученной в процессе измерения ударных импульсов, величины тока нагрузки приводного электродвигателя в момент его пуска и при работе на номинальном режиме, а также времени разгона. Измерение вибрации рекомендуется производить в двух плоскостях (горизонтальной и вертикальной) на корпусе и лапах сепаратора на частотах, соответствующих частоте вращения барабана. Нормы вибрации, соответствующие трем категориям ТС, приведены на рис.8.
V мм\с
N кВт
Рис. 8. Нормы вибрации центробежных сепараторов в зависимости от категории их технического состояния: I - хорошее; П- удовлетворительное;!!! - неудовлетворительное
|По полученным в процессе измерения уровню и соотношению величин dBc и dBм представляется возможность контроля ТС подшипников различных механизмов, вообще, и центробежных сепараторов в частности. Величина dBс является универсальной и может использована для контроля ТС всех подшипников. С ее помощью можно производить контроль общей шероховатости поверхности шариков (роликов) и дорожек подшипников качения, включая и бездефектные. Например, если в процессе подшипника величина dBс возрастает, то это говорит о недостаточной его смазке. Величина dBм позволяет характеризовать наличие дефектов на шариках (роликах) и дорожках качения, а также загрязнение смазки. В случае, если в процессе измерений имеют место высокие значения указанных величин, необходимо прежде всего убедиться в том, что они действительно вызваны дефектом в контролируемом подшипнике, а не другим источником (например, повреждение передачи, трение вала о корпус или крышку корпуса подшипника, задевание крылатки вентилятора за кожух, кавитация насоса и т.п.). Для этого производится измерение на деталях, смежных с корпусом подшипника. Если измеренные величины ниже, чем на корпусе подшипника, значит источник повышенного сигнала - подшипник. Для выявления истинной причины следует произвести смазку подшипника и через несколько часов работы механизма повторить измерение. Если же уровень сигнала на смежной детали окажется выше, то необходимо методом последовательных измерений (удаляясь от корпуса подшипника) найти источник сигнала и установить причину.
В процессе эксплуатации сепараторов вследствие причин, рассмотренных ранее, возникают различного рода повреждения и неисправности. Для их раннего распознавания с целью предотвращения отказа сепаратора могут быть использованы предельные значения параметров контроля ТС, представленные в таблицах, например: ударные импульсы, вибрация, потребляемая мощность, время пуска, частота вращения и т.п.
63. Параметры, характеризующие степень загрязнения поверхностей теплообмена теплообменных аппаратов. Интегральный показатель запаса охлаждающей способности. Сущность косвенной оценки охлаждающей способности. Приборы, используемые при контроле технического состояния.
контроль их ТС следующими КИП: термометры, манометры.. и переносными средствами диагностики: контактные термометры, толщиномеры, эндоскопы. Эндоскопом определяется состояние трубок (трещины, свищи, пропуски в соединениях труб). Толщиномеры используются для определения износа стенок корпусов, труб и других стенок. Загрязнение поверхностей теплообмена ТА определяется по перепадам P и t°. В замкнутых системах ТА в качестве интегрального показателя запаса охлаждающей способности рекомендуется относительное количество охлаждающей среды проходящей например через холодильник. Оно характеризуется отношением разности температуры среды на выходе и на входе в ГД- ∆Тдв и разности температуры на входы и на выходе охладителя- ∆Тохл. Qг= ∆Тдв/∆Тохл. Предельное значение Qг=Qх устанавливается для условий работы двигателя с полной нагрузкой в тропиках. Для низкотемпературных контуров (смазочной системы) Q=10 при условии, что запас температуры среды на входе в двигатель по отношению кмах допустимой температуре составляет не менее 3-5% на полной нагрузке. Для повышения точности контроля используется косвенная оценка охлаждающей способности ТА. Кохл=1-Твых/Тдв. Где Тохл- температура среды на выходе из ТА; Тдв- на входе из двигателя. Предельное значение Кохл=7%. При отсутствии штатных термометров температура поверхностей ТА измеряется дистанционными измерителем THERMOPOINT80. Персональный компьютер: оценка отклонения выбранного диагностического показателя от значения, рассчитанного на математической модели для данных эксплуатационных условий.
64. Контролируемые параметры гидравлических систем и агрегатов. Признаки неудовлетворительного технического состояния. Приборы, используемые для контроля негерметичности гидравлических систем.
Контроль ТС гидравлических агрегатов аналогичен рассмотренным ранее агрегатов СЭУ производятся по: уровню ударных импульсов, вибрации, температурному полю корпуса, термодинамическому КПД, плотности и продуктам износа в рабочей жидкости. По характеру изменения температурного поля корпуса гидроагрегата при его пуске устанавливается ТС его подшипников и деталей качающего узла. Мерой исправного ТС агрегата является практически постоянная скорость изменения прироста температуры с последующим приближением её к нулю. Признаками неудовлетворительного ТС агрегата является резкое увеличение скорости прироста температуры поверхности корпуса в начальный период пуска агрегата. По термодинамическому КПД устанавливается значение объёмных и гидродинамических потерь и определяется КПД агрегата: ζ=(∆Рп/СрР∆Тп)-1. где ∆Рп- перепад давлений на агрегате. ∆Тп- изменение температуры рабочей жидкости вследствие объёмных и гидродинамических потерь. Предельное значение КПД должно составлять не более 10%. Контроль плотности гидравлических систем помогает установить их внутреннюю и внешнюю не герметичность. Для этих целей могут быть использованыгидроманометры. Допустимые утечки за фиксированое время являются мерой плотности узла системы: для насосов- 10% от подачи насоса, для гидроцилиндров- 0,12Д² (Д- внутренний диаметр цилиндра в см), для распределителей- 5%, для предохранительных и регулирующих клапанов 1% от подачи насоса. Для контроля плотности конкретных узлов гидравлической системы в процессе их эксплуатации могут быть использованы течеискатели НКУ-1, LDE-10.контроль осуществляется путём измерения уровня гидродинамического шума на поверхности контролируемого узла гидравлической системы.
66. Способы контроля технического состояния дейдвудных устройств. Основные дефекты и их последствия. Контроль развития задира. Нормы вибрации на дейдвудной втулке при различных категориях технического состояния.
основная цель без разборного контроля таких устройств состоит в установлении зазоров в его подшипниках, а т.ж. в определении ТС гребного вала и дейдвудных подшипников. Используемые при этом методы контроля зависят от типа смазки (водяной или масляной). При использовании водяной смазки зазоры в подшипниках можно контролировать просадкомерами, запрессованными в дейдвудные подшипники, датчиками предельных износов, а т.ж. измерению напряжений на свободном конце гребного вала, измерению расхода воды через дейдвудное устройство в зависимости от зазора в нём (расходомерный метод), уровню вибрации. Для дейдвудных систем с масляной системой смазки, наряду с указанными выше методами используют методы контроля за включениями продуктов износа в масле. Содержание воды в масле не должно превышать 1%. С помощью контроля уровня вибрации дейдвудных устройств определяются дефекты подшипников скольжения (овальность, гранность, локальный износ шейки вала и вкладыша, явление схватывания- заедания). Основными дефектами являются- износ вкладыша и заедание. В первом случае это может привести к нарушению работы масляного клина, увеличению трения и выкрашиванию подшипника. Во втором-может произойти задир вкладыша и заклинивание вала. Контроль развития задира производится по изменению формы плотности амплитуд вибросигнала. Фактический задир может быть определён с помощью датчика слежения, который устанавливается в обойме подшипника.
67. Способы контроля технического состояния рулевых устройств и машин. Соблюдаемые условия при осуществлении контроля. Места измерения вертикальной, траверзнои и продольной вибрации. Нормы вибрации при различных категориях технического состояния.
контроль ТС рулевого устройства (рули, рулевые машины, приводы) проводятся в следующих случаях: пред очередным освидетельствованием судна (на плаву и в доке); перед докованием; перед и после ремонта судна; по мере необходимости при предотказном состоянии. После ремонта определение ТС проводится с целью проверки их качества. В основу определения ТС положен наружный осмотр без демонтажных работ. Наружный осмотр рулей заключается в проверке вертикального зазора между петлями ахтерштевня и руля с целью выявления проседания руля, состояния фланца, соединяющего рудерпис с баллером, на предмет наличия болтов, гаек и стопорных чек, состояния пера руля на предмет отсутствия вмятин, прогибов, изломов обшивки; толщины обшивки пера руля в характерных точках; отсутствие признаков скручивания баллера. При измерении контролируемых параметров РУ и его отдельных эл-тов должны быть соблюдены общие и специфические условия. К общим условиям относятся: скорость судна- эксплуатационная, состояние моря- волнение не более 3 баллов, загрузка судна- любая. Специфические условия зависят от конкретного элемента РУ. Например измерение виброскорости и виброускорения насосов переменной производительности следует проводить при перекладке руля на угол +/-20 с борта на борт на ходу судна по такому циклу: от 0 до 20 лев.борта, затем пауза до полной остановки румпеля, далее от 20 лев.борта через 0 до 20 прв.борта и снова пауза до полной остановки и установка в положение «прямо руль». Измерение вибрации должно осуществляться в 2-ух плоскостях (горизонтальной и вертикальной). Измерение ударных импульсов рекомендуется производить в одном из этих направлений на стоянке или на ходу судна при эксплуатационном режиме работы насосов во время перекладки руля на угол +10 любого борта.измерениевиброускорения на баллере руля рекомендуется производить на ходу при положении «прямо руль», перекладке с борта на борт +/-15, работе одного из насосов и на частоте собственных колебаний пера руля в вертикальном, траверзном и продольном направлениях. Измерение т-ры подшипников насосов производится при установившемся эксплуатационном режиме в течении не менее 1ч на ходу судна.
68. . Причины повышения вязкости моторного масла при длительной работе дизеля. Режимы смазки в зависимости от вязкости смазочного масла. Причины и последствия снижения вязкости масла.
в процессе эксплуатации вязкостно-температурные характеристики масел изменяются. Вязкость увеличивается за счёт процессов окисления, полимеризации и поликонденсации углеводородов масла, накопления механических примесей, испарения легколетучих масляных фракций, попадания в систему смазки тяжелых топлив. Увеличение вязкости и общее загрязнение масляной системы снижают вязкостно-температурную характеристику масла и в итоге могут вызвать износ трущихся поверхностей и возникновение задиров.
Дата добавления: 2019-07-15; просмотров: 328; Мы поможем в написании вашей работы! |
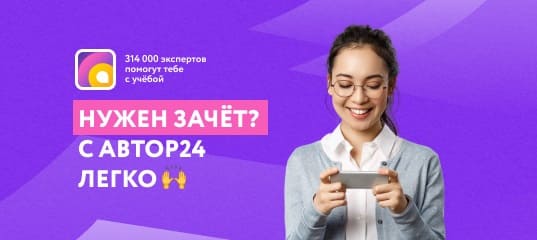
Мы поможем в написании ваших работ!