При циклических нагрузках явление концентрации напряжений выражено значительно сильнее.
На практике повышение усталостной прочности деталей достигают как технологическими, так и конструктивными способами.К технологическим способам относятся термическая и химико-термическая обработка сталей, дробеструйная обработка и накатывание деталей роликами, алмазное выглаживание (уплотнение поверхности скругленным алмазным инструментом), ультразвуковое упрочнение и т. д. Например, накатывание резьб повышает прочность детали в 1,5...2 раза и практически устраняет концентрацию напряжений у основания резьбы.
Концентрация напряжений возникает и в поверхностном слое металла при контактном нагружении, когда сила действует на весьма ограниченном участке поверхности. Этот вид нагружения чаще всего встречается при соприкосновении сферических и цилиндрических тел с плоскими, сферическими или цилиндрическими поверхностями.В зоне соприкосновения образуется плоская площадка, размеры которой зависят от упругости материала и формысжимаемых тел.
Усталостное разрушение (питтинг), обусловленное периодически изменяющимися контактными напряжениями, сопровождается отслаиванием и выкрошиванием крупных частиц металла, в результате чего сочленение, как правило, выходит из строя. Характерным примером такого разрушения служит питтинг рабочих поверхностей зубьев зубчатых колес. Концентрация напряжений возникает на участках зубьев, близких к начальной окружности.
|
|
При конструировании сферических и цилиндрических сочленений, несущих высокие нагрузки, следует учесть, что соприкасающиеся детали должны быть закалены до твердости не ниже HRC60...62 и поверхностью, обработанной не ниже параметра шероховатости Rа0,080.
С целью уменьшения контактных напряжений в тех случаях, когда это допускают условия работы сочленения, детали, воспринимающие нагрузку, следует помещать в гнезда, имеющие диаметр, близкий к диаметру детали (D/d = 1,01...1,02).
12. Контактная прочность деталей.
При контактном нагружении сила действует на малом участке поверхности, вследствие чего в поверхностном слое металла возникают высокие локальные напряжения. Этот вид нагружения встречается при соприкосновении сферических и цилиндрических тел с плоскими, сферическими или цилиндрическими поверхностями.
При теоретическом решении задачи о напряженном состоянии в зоне контакта упругих тел (Герц, Беляев, Фэппль) предполагают, что нагрузка статическая, материалы тел изотропны, площадка контакта мала по сравнению с поверхностями и действующие усиления направлены нормально к этой площадке.
В зоне соприкосновения образуется площадка, размеры которой зависят от упругости материалов в формы сжимаемых тел. При сжатии сфер
|
|
Основные схемы работы сочленений при контактном нагружении представлены в таблице 27 (в скобках приведены конструктивные аналоги).
В схемах 5-12 нагружение имеет циклический характер, даже если действующая сила статическая, так как нагружению подвергаются последовательно различные точки поверхностей. Относительное движение контактных тел нарушает герцово распределение напряжений в зоне контакта. Поверхностный слон в зоне контакта подвергается сжатию и растяжению в тангенциальном направлении. Расположение зон сжатия и растяжения зависит от кинематики движения. При чистом качении (схемы 7 -9) зоны сжатия на обеих сопрягающихся поверхностях (зачерненные участки) расположены по одну сторону от центра контакта (встречно движению), по другую сторону материал подвергается растяжению.
Присутствие смазки действует двояко. При умеренных давлениях в зоне контакта масляная пленка способствует более равномерному распределению давлений, и увеличению фактической поверхности контакта. Перекатывание поверхностей создает определенный гидродинамический эффект: в пленке, вытесняемой из зазора, возникают повышенные давления, способствующие разделению металлических поверхностей, тем более, что при давлениях, существующих в зоне контакта, увеличивается вязкость масла (тиксотропический эффект). В результате нагрузка воспринимается отчасти упругой деформацией выступающих металлических поверхностей, отчасти давлением в масляной пленке (эл астог идродинамическое трение).
|
|
Еще резче выражен гидродинамический эффект при скольжении. Масло, увлекаемое движущейся поверхностью, непрерывно поступает в суживающуюся часть зазора, разделяя металлические поверхности. При благоприятных соотношениях (большие скорости скольжения, малые давления, повышенная вязкость масла) в сочленении наступает жидкостное трение.
При высоких давлениях в зоне контакта масло оказывает отрицательное влияние. Под действием набегающей поверхности, а также вследствие капиллярности, масло внедряется в рыхлоты и микротрещины и расширяет их, вызывая ускоренное выкрашивание металла. Особенно резко это явление выражено в случае, если одна из поверхностей в зоне повышенного давления подвергается растяжению (см. рис. 217, в), способствующему раскрытию микротрещин.
Задача повышения прочности контактных сочленений заключается прежде всего в снижении величины давлений на площадке контакта путем
|
|
13. Конструирование механически обрабатываемых деталей.
При конструировании необходимо предусматривать также удобство обработки деталей на металлорежущих станках, что особенно важно при массовом производстве, когда детали обрабатываются в приспособлениях. На отливках, подвергаемых механической обработке, необходимо иметь базовые поверхности, которые служат опорой при креплении отливки на станке при ее обработке. Эти же поверхности принимают за исходные как при изготовлении моделей, так и при проверке размеров моделей и отливок, неудачное расположение ступенчатых отверстий требует поворота детали при механической обработке на 180°, а улучшенное расположение отверстий по убывающим размерам позволяет обрабатывать отверстия с одной установки. При конструировании валов и подобных им деталей цилиндрические поверхности необходимо располагать по возрастающим или убывающим размерам. Это облегчает обработку и монтаж. При нарезании резьбы до упора создаются производственные затруднения, поэтому при конструировании деталей необходимо применять резьбу в сквозных отверстиях. У деталей с наружной резьбой следует предусматривать канавки для выхода инструмента.
Особенности конструирования поковок (деталей). Штамповкой могут быть получены поверхности поковки без окалины чистотой у6, поэтому механической обработке подвергают только некоторые поверхности. Наружные фасонные поверхности, как правило, не обрабатывают. При конструировании механически обрабатываемых деталей необходимо соблюдать следующие правила:
- сокращать протяженность механически обрабатываемых поверхностей до конструктивно необходимого минимума;
- уменьшать количество металла, снимаемого при обработке;
-предусматривать изготовление деталей наиболее производительными методами обработки без снятия стружки (штамповкой, холодной высадкой, чеканкой и т. д.);
- шире применять профильный и сортовой прокат с сохранением наибольшего числа черных поверхностей;
- предусматривать изготовление деталей из заготовок с формой, возможно близкой к форме окончательною изделия;
- облегчать изготовление трудоемких деталей путем применения составных конструкций;
-избегать излишне точной механической обработки. - - Применять в каждом отдельном случае наиболее низкую точность, обеспечивающую правильную работу узла и удовлетворяющую условию взаимозаменяемости;
- обеспечивать возможность применения наиболее производительных способов механической обработки (обработка мерным многолезвийным инструментом и т. д.);
- предусматривать возможность обработки напроход, являющейся главным условием повышения производительности, получения высокой точности и малой шероховатости обрабатываемых поверхностей;
- при невозможности обработки напроход обеспечивать выход обрабатывающего инструмента на расстояние, достаточное для получения точных поверхностей, обеспечивать удобный подход режущего инструмента к обрабатываемым поверхностям;
- предусматривать возможность обработки максимального числа поверхностей при одной операции на одном станке, с одного установа, одним и тем же инструментом;
- деталям многократного и массового применения придавать формы, допускающие групповую обработку с применением комбинированного инструмента;
- обеспечивать возможность обработки точных соосных и параллельных отверстий с одного установа, облегчающей получение соосности и точных межосевых расстояний;
- предусматривать четкое разделение поверхностей, обрабатываемых на различных операциях, различным инструментом и с различной степенью точности;
- между обрабатываемыми и ближайшими необрабатываемыми поверхностями предусматривать расстояния, обеспечивающие обработку при наибольших возможных по производственным условиям колебаниях размеров заготовки;
- избегать совместной обработки деталей в сборе, нарушающей непрерывность производственного потока, снижающей взаимозаменяемость и затрудняющей смену деталей в эксплуатации;
- сокращать номенклатуру обрабатывающего инструмента путем унификации размеров и формы обрабатываемых элементов;
- в единичном и мелкосерийном производстве сводить к минимуму применение специального режущего инструмента, по возможности обходясь стандартным инструментом;
- придавать обрабатываемым поверхностям форму, обеспечивающую равномерную и безударную работу инструмента;
- разгружать цилиндрический многолезвийный инструмент (сверла, развертки, зенкеры и т. д.) от одностороннего давления при обработке;
- придавать обрабатываемым участкам высокую и равномерную жесткость, обеспечивающую точную обработку и способствующую применению производительных способов обработки;
- предусматривать удобные базы для контроля размеров по возможности с применением универсального измерительного инструмента.
14. Конструирование литых деталей.
Конструкция отливки должна отвечать служебным требованиям детали, технологии ее изготовления, технологии механической обработки и эстетическим требованиям. Внешние контуры литой детали должны представлять собой сочетание простых и прямолинейных контуров, сочленяемых плавными криволинейными переходами. Необходимо стремиться к уменьшению габаритных размеров и особенно высоты детали, устранению выступающих частей, больших тонких ребер, глубоких впадин и поднутрений, затрудняющих изготовление литейной формы.
Внутренние полостилитых деталей следует конструировать открытыми, без поднутрений, что позволит изготовить отливку без применения стержней. Если при изготовлении отливки обойтись без стержней невозможно, то при конструировании литой детали необходимо предусматривать отверстия и окна максимальных размеров в достаточном числе для обеспечения устойчивости стержней в литейной форме, точности их установки, легкого удаления стержней и каркасов из отливки при ее очистке. Стенка литой детали объединяет все ее рабочие элементы (гнезда подшипников, фланцы, поверхности скольжения и качения и др.), придает в значительной степени требуемую конфигурацию, жесткость и прочность. Выбор минимально допустимой толщины стенки отливки определяют размеры и сложность отливки, а также литейные свойства сплава.
Характерной особенностью многих отливок является сочетание массивных направляющих с относительно тонкими стенками, применение ребер жесткости и разветвленных внутренних полостей, разделенных перегородками. Для предупреждения возникновения усадочных раковин и трещин в отливках должны быть правильно выполнены переходы от одного сечения к другому. Ребра жесткости создают местные скопления металла, вызывающие образование усадочных раковин и трещин. Для устранения этого дефекта необходимо Х-образные сечения заменять Т-образными, а соединения ребер со стенками отливки располагать под прямым углом. При пересечении в одной точке нескольких ребер рекомендуется делать кольцевое ребро и присоединять к нему радиальные ребра на достаточном расстоянии друг от друга. Толщина ребер обычно составляет 0,8 толщины стенки отливки.
Для предупреждения усадочных раковин в массивных отливках из сплавов с повышенной усадкой при конструировании должен быть применен принцип направленного или одновременного затвердевания. При направленном затвердевании толщина стенки отливки плавно увеличивается снизу вверх. Кристаллизация металла происходит от тонких сечений отливки, расположенных в нижней части формы, к более массивным сечениям, располагающимся в верхней части формы. При одновременном затвердевании сечения отливок имеют одинаковую толщину как в нижней, так и в верхней части детали. Иногда бывает целесообразным крупные и сложные литые конструкции разделить на более простые элементы или детали с последующим соединением их между собой сваркой, болтовыми соединениями и другими способами. При этом рекомендуется упрощать наиболее сложные и крупные детали и усложнять наиболее простые из стыкуемых деталей. Выступающие части корпусных деталей делают съемными. Для повышения жесткости, уменьшения массы и сокращения объема механической обработки объединяют несколько простых деталей в одну.Конструкция литой детали должна обеспечивать возможность получения ее габаритных размеров, сечений и массы с заданной точностью. Для этого необходимо предусматривать конструктивные уклоны на необрабатываемых поверхностях. Отдельные бобышки и приливы необходимо объединять в один общий прилив и доводить его до плоскости разъема или основания. Для облегчения пригонки сопрягаемых деталей в ее конструкции предусматривают пояски, отбортовку и т. п., что позволяет компенсировать допустимые отклонения в размерах отливки.
15. Конструирование деталей из пластмасс.
Обычно при конструировании деталей из пластмасс учитываются их физико-механические свойства, особенности процесса изготовления, условия эксплуатации и сборки, простота конструкции пластмассовой детали, стоимость оснастки, производительность труда, качество, габаритные размеры детали, масса и др.
Стенки и технологические уклоны. Уклоны в пластмассовых изделиях необходимы для беспрепятственного их извлечения из пресс- формы. Обычно технологические уклоны назначают при получении деталей из пластмасс методом прессования или литьем под давлением.
Соблюдение равностенности для многих изделий из пластмасс является необходимым условием при конструировании. Однако практически это условие неосуществимо. Поэтому правильно сконструированным изделием считается такое, у которого величина равностенности не превышает 30% от наименьшей толщины стенки. При этом в изделии должны отсутствовать резкие переходы. Переходы от большого сечения стенки к меньшему должны выполняться при помощи уклонов, а в цилиндрических элементах при помощи конусности, что способствует упрочнению данных элементов (рис. 101). Утолщение стенок по конструктивным соображениям происходит в следующих случаях: при наличии отверстий и деталей с резьбой (рис. 102).
Ребра жесткости. Ребра жесткости применяются в пластмассовой детали для увеличения жесткости и прочности, усиления особо нагруженных мест или выступающих частей, уменьшения веса детали за счет разгрузки утолщенных мест. Иногда их применяют по чисто декоративным соображениям.
Желательно, чтобы ребра жесткости не доходили до опорной поверхности или края примыкающего к нему элемента детали на величину, равную 0,5 ... 1,0 мм, примыкали к опорной поверхности плавно и имели наибольшее допускаемое значение уклона (рис. 103).
Ребра жесткости, если позволяет их конструкция, лучше располагать так, чтобы они работали на сжатие, а не на растяжение. Там, где увеличивают жесткость крышек, днищ крупногабаритных деталей и боковых стенок, обычно применяют мелкие ребра-нервюры. На рис. 104 изображены некоторые виды нервюр. Их располагают в продольном направлении либо с наружной, либо с внутренней стороны.
Отверстия. В пластмассовых изделиях применяют отверстия различной конструкции, но желательно, чтобы они имели наиболее простую форму. Самые простые по форме — цилиндрические отверстия, наиболее трудоемкие — овальные. Отверстия могут быть сквозными и глухими.
Из всех видов отверстий, наибольшее распространение получили цилиндрические постоянного диаметра, но встречаются и ступенчатые. Они могут быть не только цилиндрическими, но и коническими, а также применяться в сочетании (рис. 105). Если отверстия находятся вблизи края изделия, то желательно, чтобы края соответствовали форме примыкающего к нему отверстия. Это, во-первых, способствует соблюдению равностенности, во-вторых, уменьшает возможную деформацию отверстия в результате неравномерной усадки стенок (рис. 106).
Расстояние между соседними отверстиями или отверстием и краем изделия должно быть не менее половины диаметра отверстия. Диаметры отверстий выбирают по ГОСТ 6636-69, а диаметры сквозных отверстий для болтов, винтов, шпилек и заклепок, устанавливаемых с зазорами в соединяемые детали, регламентированы ГОСТ 11284-75.
Поднутрения. Узкие полости между отдельными частями отливки, различного рода пазы и выемки, затрудняющие формовку и литье, называются поднутрениями. Как правило, они ведут к появлению брака. В деталях из пластмасс наличие поднутрений внутреннего контура недопустимо. В противном случае формующий элемент нельзя из-
влечь. На рис. 107, I дан пример нетехнологичной конструкции изделия из-за поднутрения внутренней полости изделия. На рис. 107, II конструкция видоизменена — она стала более технологичной.
Закругления. Изделия из пластмасс обязательно должны иметь закругления как с наружной, так и внутренней стороны, особенно на кромках и в углах см. ГОСТ 10948-64. Наличие таких закруглений способствует увеличению механической прочности отдельных элементов и изделия в целом.
Величина радиуса закруглений во многом зависит от материала детали, толщины стенки, конструктивных особенностей, а также от типоразмера инструмента, применяемого при окончательной обработке пластмассовой детали. Важно отметить, что величина радиусов на всей длине закругляемого элемента должна быть одинаковой, а закругления внутренних и наружных контуров согласованы между собой, т.е. толщина изделия b должна быть всюду постоянна (рис. 108,I — неправильно и II — правильно).
Резьбы. Резьбы в пластмассовых изделиях получают в основном тремя способами: прессованием (непосредственно в самом изделии), запрессовкой в пластмассовые изделия металлических деталей с резьбой и резанием.Пластмассовые изделия могут иметь как наружную, так и внутреннюю резьбу различного профиля. В практике чаще всего применяют метрическую резьбу с крупным или мелким шагом. Важно отметить, что детали с резьбой любого вида, прессуемые в изделия из пластмасс, обязательно должны иметь фаску на наружном конце резьбы.
В пластмассовых изделиях обычно избегают делать сквозные внутренние резьбы. Но если резьба все же необходима в каком-либо сквозном отверстии, то она выполняется лишь на некоторой его части.
Сварка применяется для соединения деталей из термопластов. Процесс сварки довольно сложный. Типы сварных соединений деталей из пластмасс аналогичны соединениям деталей из металла, т. е. они бывают стыковые, угловые, тавровые.
Сущность процесса сварки пластмасс сварочной горелкой (рис. 109, 3) состоит в том, что кромки свариваемых деталей 1 и присадочный пруток 2 нагревают до размягчения и перехода в вязко-текучее состояние, после чего присадочный пруток при небольшом давлении укладывают в шов. В данном случае, в отличие от сварки металлов, жидкая масса не образуется. Пластмассы, находясь в вязко-текучем состоянии, приобретают липкость, в результате чего в соединяемых деталях под давлением образуется неразъемное соединение.
Сварку пластмасс производят различными способами. Одним из наиболее распространенных является сварка газовыми теплоносителями (нагретыми газами). В качестве теплоносителей применяют подогретые газы (воздух, азот, аргон и др.) либо непосредственно продукты сгорания горячего газа (пропан-бутоновые смеси и др.) в смеси с воздухом. Газ-теплоноситель нагревают до необходимой температуры в специальных устройствах — нагревателях, условно называемых горелками. Горелки бывают двух типов: с электроподогревом (II) и газоподогревом (I) (рис. 110). Они состоят из рукоятки 3, горелки 7 или греющей спирали 8, сопла 6, шлангов подачи сжатого воздуха 2 и газа 1, змеевика 4 и электрического шнура 9. Выход горячего воздуха обозначен цифрой 5. Сварку нагретым газом выполняют одним из двух способов: с применением присадочного материала или без него. При сварке без присадочного материала разогретые газом-теплоносителем кромки пластмасс сдавливают прижимными роликами.
Склеивание. Склеиванием соединяют как пластмассы между собой, так и пластмассы с металлами. Для этой цели применяют клей БФ-2, БФ-4, карбинольный клей, а также клей марок ПУ-2, ПК-5, ВК-32-200 др. Для склеивания слоистых пластиков и пенопластов применяют смоляные клеи ВИАМ-Б-3, КБ-3 и др. К органическому стеклу приклеивают другой материал посредством клея марок ВК-32-70, В-31-Ф9 и др.
Дата добавления: 2019-07-17; просмотров: 277; Мы поможем в написании вашей работы! |
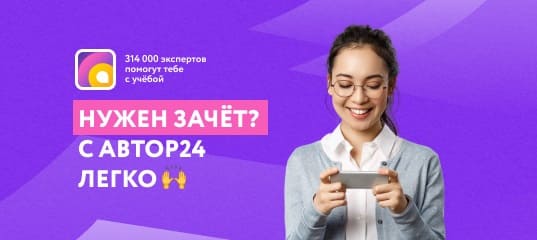
Мы поможем в написании ваших работ!