Изобразите эскиз одного из узлов конвейера, обозначив на чертеже необходимые размеры и посадки.
Люлечные конвейеры (рис. 4.37, 4.38) по конструкции подобны ковшовым конвейерам, но в качестве грузонесущего элемента вместо ковшей используются шарнирно-подвешенные полки (люльки) [2, 3].
Рис. 4.37. Люлечный конвейер:
1 – отклоняющие звездочки; 2 – направляющие; 3 – загрузочное устройство;
4 – НУ; 5 – привод; 6 – разгрузочное устройство; 7 – ходовая часть
Люлечные конвейеры предназначены для перемещения штучных грузов небольшой массы (детали машин, книги, ящики и др.) по сложной трассе (рис. 4.39), расположенной в вертикальной плоскости (междуэтажное транспортирование грузов) в комплексе с технологическим оборудованием.
Загрузка и разгрузка люлечных конвейеров выполняется на вертикальных участках вручную или автоматически с помощью специальных устройств. К основным параметрам относятся: общая длина конвейеров до 150 м; высота вертикальных участков до 30 м; скорость до 0,35 м/с.
Рис. 4.38. Ходовая часть люлечного конвейера:
1 – люльки; 2 – тяговые цепи; 3 – оси
Рис. 4.39. Схемы трасс люлечных конвейеров:
П – привод; НУ – натяжное устройство; З – зона загрузки; Р – зона разгрузки
В люлечных конвейерах используют редукторный привод с тормозом обратного хода цепи для предотвращения обратного движения ходовой части загруженного конвейера в случае перерыва подачи тока.
Несущими элементами люлечных конвейеров являются люльки (подвески) разнообразных конструкций в зависимости от массы, формы и габаритных размеров перемещаемых грузов и способов загрузки и разгрузки. При автоматической загрузке и разгрузке применяют гребенчатые (колосниковые) люльки (рис. 4.38), которые разгружаются на ходу с помощью гребенчатых столов-лотков.
|
|
Тяговым элементом являются две пластинчатые катковые цепи с шагом 100; 125; 200; 250; 315 мм. Загрузочные и разгрузочные устройства выполняют в виде гребенчатых столов-лотков.
Рома ответы
Практическая часть
6. Подвесной толкающий конвейер. Подвесной толкающий конвейер имеет замкнутую тяговую цепь с закреплёнными на ней каретками, движущимися по верхнему ходовому пути. Цепь с каретками приводится в движение приводом, натяжение цепи создаётся натяжным устройством. В тяговую цепь между каретками с определённым шагом встроены толкатели, которые входят в зацепление с головными тележками и перемещают их по грузовому пути. Тележки соединяются между собой в сцепы, на которые закрепляются подвески для транспортировки грузов. Количество тележек в сцепе зависит от габаритов и массы транспортируемого груза. Тяговые и грузовые пути конвейера соединены между собой хомутами. Путь конвейера закрепляется с помощью специальных металлоконструкций и узлов креплений, либо к фермам и колоннам здания либо на независимые опорные стойки и металлоконструкции.
|
|
Поскольку тяговая цепь не соединена жёстко с тележкой сцепа, и они движутся по различным путям, то это позволяет останавливать сцепы в необходимых по технологическому процессу местах. Останов сцепа осуществляется с помощью специальных устройств, называемых остановами. Работа останова выполняется в автоматическом режиме по специальному алгоритму. Грузовые и тяговые пути имеют ответвления, называемые стрелками, которые осуществляют разделение или соединение грузопотоков движущихся по ним сцепов с грузом.
Передача сцепов с одного уровня на другой осуществляется с помощью вертикальных поворотов или подъёмно-опускных секций. Подъёмно-опускная секция представляет собой отрезок грузового пути конвейера, перемещаемого в вертикальной плоскости специальным механизмами. На подъёмно-опускных секциях также можно выполнять операции по установке или съёму изделий на подвеску сцепа или выполнять какую-либо технологическую операцию с изделием.
Подвесные толкающие конвейеры, как правило, объединяются в сложно-разветвлённые системы, занимающие верхнее пространство производственного корпуса. Работа системы конвейеров осуществляется в автоматическом режиме с помощью системы управления, состоящей из силовой и управляющей частей. Функцию управления выполняет программируемый контроллер и система бесконтактный датчиков. Современные системы управления конвейерами позволяют осуществлять адресную доставку грузов, согласно требованиям технологии, а также выдавать информацию о наличии и номенклатуре транспортируемых грузов в АСУП предприятия. Состояние системы конвейеров в реальном масштабе времени отображается на панели визуализации. Такие системы применяют как для транспортных, так и для технологических операций.
|
|
6.1. Изобразите схему, ОКЦ подвесного толкающего конвейера обозначив позициями основные составные части и механизмы. Объясните принцип действия и устройство машины, характер выполняемых технологических операций.
Подвесной толкающий и грузонесущий конвейеры являются комплексными, автоматически действующими транспортно - технологическими системами, предназначенными для механизации и автоматизации межцехового и внутрицехового транспорта в условиях массового, крупносерийного производства. Применение ПТК и ГНК позволяет объединить все грузопотоки в единую автоматизированную транспортную систему, которая одновременно может выполнять функции межоперационных складов. ГНК и ПТК широко применяются в различных отраслях и прежде всего в автомобилестроении.
|
|
6.2. Изобразите полную кинематическую схему приводной станции и ходовой части конвейера, указав позиции основных составных частей. Объясните назначение и устройство ходовой части, принцип ее действия и характерные особенности.
6.3. Изобразите схему сил, действующих на ходовую часть конвейера, приведите последовательность тягового расчета с указанием основных расчетных зависимостей.
6.4. Изобразите эскиз одного из узлов конвейера, обозначив на чертеже необходимые размеры и посадки.
6.5. Изобразите рабочий эскиз одной из деталей рассмотренного узла, обозначив на чертеже необходимые размеры и допуски. Объясните назначение детали. Подберите марку материала детали, а также вид упрочняющей обработки.
В зависимости от условий эксплуатации стойкость валов определяется усталостной прочностью при кручении и изгибе, контактной прочностью или износостойкостью.
– средненагруженные валы (до 80–100 мм) изготовляют из сталей 45, 40Х, 50Х с улучшением (σв = 800–1000 МПа; НВ 217–285);
Отжиг стали 45 — это нагрев материала в специальной печи до очень высокой температуры и последующее его охлаждение, которое выполняется естественным образом, то есть вместе с печью. Существует отжиг первого рода, при котором нагрев идет до критических значений, но не превышает их. Также существует и отжиг второго рода, при котором температура уже превышает критическую отметку и приводит к некоторым изменениям в структуре.
Так или иначе, любой из данных способов позволяет избавиться от неоднородности состава, а также снять внутреннее напряжение материала и достичь зернистой структуры. Кроме того, проведение отжига стали 45 поможет снизить твердость сплава, что значительно облегчит в дальнейшем процесс переработки. Примечательно, что отжиг второго рода подразделяется на несколько следующих категорий, различающихся по их назначению и исполнению:
- диффузионный отжиг
- полный отжиг
- неполный отжиг
- изотермический отжиг
- рекристализационный
Как правило, для углеродистых сталей применяется полный отжиг. Суть данной технологии состоит в том, что заготовки нагреваются до температуры, которая превышает критическую отметку (верхняя точка Ас3) примерно на значение от +30°С до +50°С. После этого сталь 45 охлаждают с медленной скоростью от +150°С до +200°С до тех пор, пока ее температура не сравняется со значением температуры в рабочем интервале от +500°С до +550°С.
Кстати говоря, при отжиге первого и второго рода охлаждение материала происходит в печи, в которой был произведен нагрев. Если же процесс охлаждения производят уже на открытом воздухе, то такая технология будет называться не отжиг стали 45, а нормализация. Поскольку при нормализации стали охлаждение происходит быстрее, перлит получает тонкое строение и наибольшую твердость. Поэтому нормализованная сталь тверже отожженной.
7. Цепенесущий конвейер
Изобретение относится к конвейеростроению, а именно к многорядным цепенесущим конвейерам, и может быть использовано преимущественно для охлаждения заготовок металла в процессе их транспортирования.
Известен многорядный цепенесущий конвейер, состоящий из кинематически связанного с приводом бесконечного гибкого контура, выполненного из параллельно расположенных пластинчатых цепей, замкнутых на приводных и натяжных звездочках и опирающихся в пролете между звездочками на грузонесущей и холостой ветвях на неподвижные направляющие с возможностью поперечного размещения на цепях грузонесущей ветви транспортируемых штучных грузов, например заготовок металла, охлаждаемых в процессе их перемещения, причем в зоне сбегания с приводных звездочек цепи на холостой ветви свободно провисают под действием собственного веса (Спиваковский А.О., Дьячков В.К. "Транспортирующие машины". М.: Машиностроение, 1983 г., с 291-293, рис. 9,6).
Однако недостатком известного конвейера при его использовании для охлаждения заготовок металла является высокая трудоемкость работ при восстановлении оборвавшихся цепей, которые после обрыва сбрасываются с приводной звездочки в подконвейерное пространство. Поскольку используемые для указанных выше целей цепи достаточно тяжелые, а подконвейерное пространство ограничено, то подъем оборвавшихся цепей затруднителен и связан с большой трудоемкостью при выполнении восстановительных операций и значительными затратами рабочего времени и нарушением режима работы производственного участка.
7.1. Изобразите схему ОКЦ цепенесущего конвейера, обозначив позициями основные составные части и механизмы. Объясните принцип действия и устройство машины, характер выполняемых технологических операций.
7.2. Изобразите полную кинематическую схему приводной станции и ходовой части конвейера, указав позиции основных составных частей. Объясните назначение и устройство ходовой части, принцип ее действия и характерные особенности.
7.3. Изобразите схему сил, действующих на ходовую часть конвейера, приведите последовательность тягового расчета с указанием основных расчетных зависимостей.
Помимо продольных динамических сил, вызванных неравномерностью движения, в точке набегания на цепь действуют динамические силы, направленные под углом к оси конвейера и обусловленные тем, что каждый новый зуб входит в зацепление с шарниром цепи с ударом. При большой скорости цепи эти удары могут служить причиной разрушения шарниров, а также возникновения в цепи поперечных колебаний. (При расчетах последние не учитываются, т.к. действуют на небольшой участок цепи с незначительной массой конвейера). Учитываются только продольные колебания.
Рассмотрим схему набегания цепи на звездочку или блок с гранями.
б)
Рисунок - Схема движения цепи по звездочке.
7.4. Изобразите эскиз одного из узлов конвейера, обозначив на чертеже необходимые размеры и посадки.
7.5. Изобразите рабочий эскиз одной из деталей рассмотренного узла, обозначив на чертеже необходимые размеры и допуски. Объясните назначение детали. Подберите марку материала детали, а также вид упрочняющей обработки.
В зависимости от условий эксплуатации стойкость валов определяется усталостной прочностью при кручении и изгибе, контактной прочностью или износостойкостью.
– средненагруженные валы (до 80–100 мм) изготовляют из сталей 45, 40Х, 50Х с улучшением (σв = 800–1000 МПа; НВ 217–285);
Отжиг стали 45 — это нагрев материала в специальной печи до очень высокой температуры и последующее его охлаждение, которое выполняется естественным образом, то есть вместе с печью. Существует отжиг первого рода, при котором нагрев идет до критических значений, но не превышает их. Также существует и отжиг второго рода, при котором температура уже превышает критическую отметку и приводит к некоторым изменениям в структуре.
Так или иначе, любой из данных способов позволяет избавиться от неоднородности состава, а также снять внутреннее напряжение материала и достичь зернистой структуры. Кроме того, проведение отжига стали 45 поможет снизить твердость сплава, что значительно облегчит в дальнейшем процесс переработки. Примечательно, что отжиг второго рода подразделяется на несколько следующих категорий, различающихся по их назначению и исполнению:
- диффузионный отжиг
- полный отжиг
- неполный отжиг
- изотермический отжиг
- рекристализационный
Как правило, для углеродистых сталей применяется полный отжиг. Суть данной технологии состоит в том, что заготовки нагреваются до температуры, которая превышает критическую отметку (верхняя точка Ас3) примерно на значение от +30°С до +50°С. После этого сталь 45 охлаждают с медленной скоростью от +150°С до +200°С до тех пор, пока ее температура не сравняется со значением температуры в рабочем интервале от +500°С до +550°С.
Кстати говоря, при отжиге первого и второго рода охлаждение материала происходит в печи, в которой был произведен нагрев. Если же процесс охлаждения производят уже на открытом воздухе, то такая технология будет называться не отжиг стали 45, а нормализация. Поскольку при нормализации стали охлаждение происходит быстрее, перлит получает тонкое строение и наибольшую твердость. Поэтому нормализованная сталь тверже отожженной.
8. Тележечный конвейер
Тележечный конвейер — конвейер, в котором грузонесущими элементами являются тележки-платформы, передвигающиеся по направляющим и связанные с внешним тяговым элементом. Такие конвейеры используются на металлургических и машиностроительных предприятиях для механизации технологических процессов (например, заливка, охлаждение и выбивка литья; сборка механических агрегатов). Скорость перемещения тележек — до 25 километров в час.
8.1. Изобразите схему ОКЦ тележечного конвейера, обозначив позициями основные составные части и механизмы. Объясните принцип действия и устройство машины, характер выполняемых технологических операций.
Тележки 1 непрерывно перемещаются по рельсам 2 при помощи тяговой горизонтально-замкнутой цепи, приводимой в движение электроприводом станции 11. Собранные формы 6 устанавливаются на тележки конвейера и транспортируются к заливочному участку. Расплав подается посредством литейного крана в ковше 4. Заливка форм производится с платформы 3. После заливки, формы конвейером транспортируются через вентиляционный кожух 10, из которого выделяемые формами газы отсасываются вентилятором.
8.2. Изобразите полную кинематическую схему приводной станции и ходовой части конвейера, указав позиции основных составных частей. Объясните назначение и устройство ходовой части, принцип ее действия и характерные особенности.
Кинематическая схема привода
Согласно [20] привод литейного конвейера состоит из электродвигателя 1, упругих муфт 2 и 8 , редуктора 3 (редуктор служит для передачи вращения и изменяющегося крутящего момента от электродвигателя к исполнительному механизму) и звездочки 5. Звездочка входит в зацепление с шарнирной цепью, кулачки которой, упираясь в направляющий ролик тележки, приводят конвейер в действие.
8.3. Изобразите схему сил, действующих на ходовую часть конвейера, приведите последовательность тягового расчета с указанием основных расчетных зависимостей.
Основными видами сопротивлений являются трение по соприкасающимся поверхностям и сопротивление подъему транспортируемого материала с лентой на наклонных участках.
Последовательность расчета усилий натяжения ленты показана на примере конвейера, схема которого приведена на рис. 3.1.
Расчет всегда начинают с точки 1сбегания ленты с приводного барабана, так как чаще всего именно здесь лента имеет минимальное натяжение. Далее последовательно
Рис. Расчетная схема ленточного конвейера с наклонным и горизонтальным участками
Проходят по контуру весь конвейер, завершая расчет точкой 9 набегания ленты на приводной барабан.
8.4. Изобразите эскиз одного из узлов конвейера, обозначив на чертеже необходимые размеры и посадки.
8.5. Изобразите рабочий эскиз одной из деталей рассмотренного узла, обозначив на чертеже необходимые размеры и допуски. Объясните назначение детали. Подберите марку материала детали, а также вид упрочняющей обработки.
В зависимости от условий эксплуатации стойкость валов определяется усталостной прочностью при кручении и изгибе, контактной прочностью или износостойкостью.
– средненагруженные валы (до 80–100 мм) изготовляют из сталей 45, 40Х, 50Х с улучшением (σв = 800–1000 МПа; НВ 217–285);
Отжиг стали 45 — это нагрев материала в специальной печи до очень высокой температуры и последующее его охлаждение, которое выполняется естественным образом, то есть вместе с печью. Существует отжиг первого рода, при котором нагрев идет до критических значений, но не превышает их. Также существует и отжиг второго рода, при котором температура уже превышает критическую отметку и приводит к некоторым изменениям в структуре.
Так или иначе, любой из данных способов позволяет избавиться от неоднородности состава, а также снять внутреннее напряжение материала и достичь зернистой структуры. Кроме того, проведение отжига стали 45 поможет снизить твердость сплава, что значительно облегчит в дальнейшем процесс переработки. Примечательно, что отжиг второго рода подразделяется на несколько следующих категорий, различающихся по их назначению и исполнению:
- диффузионный отжиг
- полный отжиг
- неполный отжиг
- изотермический отжиг
- рекристализационный
Как правило, для углеродистых сталей применяется полный отжиг. Суть данной технологии состоит в том, что заготовки нагреваются до температуры, которая превышает критическую отметку (верхняя точка Ас3) примерно на значение от +30°С до +50°С. После этого сталь 45 охлаждают с медленной скоростью от +150°С до +200°С до тех пор, пока ее температура не сравняется со значением температуры в рабочем интервале от +500°С до +550°С.
Кстати говоря, при отжиге первого и второго рода охлаждение материала происходит в печи, в которой был произведен нагрев. Если же процесс охлаждения производят уже на открытом воздухе, то такая технология будет называться не отжиг стали 45, а нормализация. Поскольку при нормализации стали охлаждение происходит быстрее, перлит получает тонкое строение и наибольшую твердость. Поэтому нормализованная сталь тверже отожженной.
Б1.В.ОД.5 Специальные краны
1. Магнитный кран
1.1. Изобразите схему ОКЦ магнитного крана, обозначив позициями основные составные части и механизмы. Объясните принцип действия и устройство машины, характер выполняемых технологических операций.
Мостовой магнитный кран используется при монтажных, погрузочных работах на строительных площадках, в складах и на производстве. Электрический ток к катушке электромагнита подводится гибким кабелем, навиваемым на специальный барабан, имеющий кольцевой токоприёмник, кабельный барабан связан с выходным валом редуктора механизма подъёма при помощи зубчатой передачи с паразитной шестерней[1].
Погрузка металлолома краном с электромагнитом
Этим обеспечивается равенство скоростей кабеля и крюка с подвешенным к нему электромагнитом. Диаметр барабана принимается не менее 10 наружных диаметров гибкого кабеля. Крюковая обойма магнитных кранов снабжается приспособлением для предотвращения вращения крюка в горизонтальной плоскости, а сам крюк — замком, предохраняющим выпадение из зёва крюка цепей грузового электромагнита[1].
Номинальная грузоподъёмность электромагнита составляет:
· 40% номинальной грузоподъёмности — при подъёме рельсов и труб[2].
· 15% номинальной грузоподъёмности — при подъёме стальных листов[2].
· 2,5% номинальной грузоподъёмности — при подъёме размельчённой стальной стружки[2].
· 1,5% номинальной грузоподъёмности — при подъёме обычной стальной стружки[2].
Допускается работа электромагнита с грузами, имеющими температуру до 500 °C, так как при более высокой температуре у стали и чугуна уменьшаются магнитные свойства[2]. Новые серии электромагнитов ЭМГ, ЭМГС, ЭМГК, ЭМГП, ЭМГБ, ЭМГР, ЭМГТ могут работать с грузами до 650 °C.
Принцип действия[править | править код]
Рабочий цикл электромагнита[2]:
· Магнит опускают на груз.
· Груз, удерживаемый магнитом, переносят на нужное место.
· Магнит выключают, а груз освобождается.
Достоинства и недостатки[править | править код]
Достоинства электромагнитов[2]:
· Удобство работы и простота управления.
· Быстрая смена на крюке крана.
К недостаткам относят[2]:
· переменную грузоподъёмность.
· невозможность подъёма грузов, нагретых до температуры более 800 °C.
Грузоподъёмные электромагниты в СССР выпускались круглой (серии М) и прямоугольной формы (серии ПМ)[1] согласно ГОСТ 10130-79Е грузоподъёмностью 6 — 20т и 7 — 17т соответственно[2].
На сегодняшний день электромагниты серии М и ПМ сняты с производства и на замену им выпускаются круглые электромагниты серии ЭМГ и специальные электромагниты, в том числе прямоугольные — серий ЭМГС, ЭМГК, ЭМГП, ЭМГБ, ЭМГР, ЭМГТ.
1.2. Изобразите полную кинематическую схему механизма подъема, указав позиции основных составных частей. Объясните назначение и устройство механизма, принцип его действия и характерные особенности.
Кинематическая схема мостового кранапозволяет понять принципы работы всех крановых узлов и механизмов. В целом принцип работы всего подъемно-транспортного оборудования одинаков: основой является одна или две металлических балки, на которых размещена грузовая лебедка, приводимая в движение электрическим двигателем.
Вид кранового оборудования зависит от типа конструкции и специфики поднимаемых грузов. Однако стоит отметить, что основные узлы грузоподъемных механизмов аналогичны.
1.3. Изобразите схему сил, действующих на механизм подъема, приведите последовательность его расчета с указанием основных расчетных зависимостей.
В механизмах подъема кранов широко применяются сдвоенные полиспасты (рис. 3.5.). Они дают возможность уменьшить нагрузку на канат, поскольку груз повешен на нескольких его ветвях, следовательно, уменьшить диаметр и жесткость, улучшить сцепление каната с блоками. При этом обеспечивается стабильное положение вертикальной оси канатов относительно барабана.
Отношение числа канатов, на которых груз подвешен, к числу канатов, навиваемых на барабан, называется кратностью полиспаста. Верхний блок 3 с неподвижной осью называется уравнительным. Он служит для выравнивания длин правой и левой ветвей каната в случае их неравномерного вытягивания.
1.4. Изобразите эскиз одного из узлов механизма подъема, обозначив на чертеже необходимые размеры и посадки.
1.5. Изобразите рабочий эскиз одной из деталей рассмотренного узла, обозначив на чертеже необходимые размеры и допуски. Объясните назначение детали. Подберите марку материала детали, а также вид упрочняющей обработки.
В зависимости от условий эксплуатации стойкость валов определяется усталостной прочностью при кручении и изгибе, контактной прочностью или износостойкостью.
– средненагруженные валы (до 80–100 мм) изготовляют из сталей 45, 40Х, 50Х с улучшением (σв = 800–1000 МПа; НВ 217–285);
Отжиг стали 45 — это нагрев материала в специальной печи до очень высокой температуры и последующее его охлаждение, которое выполняется естественным образом, то есть вместе с печью. Существует отжиг первого рода, при котором нагрев идет до критических значений, но не превышает их. Также существует и отжиг второго рода, при котором температура уже превышает критическую отметку и приводит к некоторым изменениям в структуре.
Так или иначе, любой из данных способов позволяет избавиться от неоднородности состава, а также снять внутреннее напряжение материала и достичь зернистой структуры. Кроме того, проведение отжига стали 45 поможет снизить твердость сплава, что значительно облегчит в дальнейшем процесс переработки. Примечательно, что отжиг второго рода подразделяется на несколько следующих категорий, различающихся по их назначению и исполнению:
- диффузионный отжиг
- полный отжиг
- неполный отжиг
- изотермический отжиг
- рекристализационный
Как правило, для углеродистых сталей применяется полный отжиг. Суть данной технологии состоит в том, что заготовки нагреваются до температуры, которая превышает критическую отметку (верхняя точка Ас3) примерно на значение от +30°С до +50°С. После этого сталь 45 охлаждают с медленной скоростью от +150°С до +200°С до тех пор, пока ее температура не сравняется со значением температуры в рабочем интервале от +500°С до +550°С.
Кстати говоря, при отжиге первого и второго рода охлаждение материала происходит в печи, в которой был произведен нагрев. Если же процесс охлаждения производят уже на открытом воздухе, то такая технология будет называться не отжиг стали 45, а нормализация. Поскольку при нормализации стали охлаждение происходит быстрее, перлит получает тонкое строение и наибольшую твердость. Поэтому нормализованная сталь тверже отожженной.
Руслан ответы
Дата добавления: 2019-07-15; просмотров: 919; Мы поможем в написании вашей работы! |
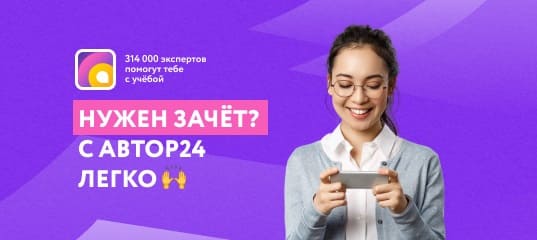
Мы поможем в написании ваших работ!