Технологическое оборудование для производства и упаковки мазей. Номенклатура мазей промышленного производства.
Подготовка основы включает в себя операции растворения или сплавления ее компонентов с последующим удалением механических примесей методом фильтрования.
Плавящиеся компоненты основы (вазелин, ланолин, воск, эмульгатор №1, 2, эмульсионные воски, полиэтиленоксид 1500 и др.) расплавляют в электрокотлах марок ЭК-40, ЭК-60, ЭК-125, ЭК-250 или в котлах с паровыми рубашками марок ПК-125 и ПК-250. По форме они могут быть цилиндрическими или сферическими, а для слива растопленной массы их делают опрокидывающимися или со сливными кранами.
Мазевые котлы изготовляются из меди или чугуна и покрываются полудой или эмалью. Они включены в группу вспомогательного оборудования для производства.
Расплавление основы осуществляется специальной паровой «иглой» (электропанелью) или паровым змеевиком. На рисунке 4.1 представлена электропанель для плавления основ, которая состоит из емкости (1) и конической воронки (2) с решеткой, защитным кожухом и нагревательными элементами (3). Защитный кожух предохраняет проникновение основы к нагревательным элементам, а решетка защищает мазевый котел от попадания примесей. После расплавления основа по шлангу (4) с помощью вакуума перекачивается в котел.
Помимо плавления и транспортировки, устройство позволяет одновременно взвешивать основу на сотенных весах (5).
Рис. 4.1. Электропанель для плавления мазевых основ
|
|
Расплавленную основу по обогреваемому трубопроводу переводят в реактор для приготовления мази. Для перекачивания расплавленной основы используют различные типы насосов. Наиболее целесообразно использовать шестеренчатые насосы, так как они хорошо работают в вязких средах.
В стадию «Подготовка, лекарственных веществ» включается измельчение, просеивание, если лекарственные вещества входят в мазь по типу суспензии; растворение в воде или компоненте мазевой основы, если это мазь-эмульсия или мазь-раствор.
Стадия «Введение лекарственных веществ в основу» может включать добавление твердых веществ к основе (мазь-суспензия) или растворение веществ в основе (мазь-раствор). В случаях комбинированных мазей могут осуществляться и тот, и другой процессы. Для введения лекарственных веществ в основу используются мазевые котлы или реакторы.
Они снабжаются мощными мешалками, приспособленными для работы в вязких средах (якорные, грабельные или планетарные).
Реактор (рис. 4.2) предназначен для смешивания густых компонентов с вязкостью до 200 Н·с/см2. Он имеет корпус (1), крышку (2) с вмонтированной в нее загрузочной воронкой, смотровое окно, клапаны, штуцера и патрубки для введения различных компонентов. Крышка корпуса с помощью траверсы (9) и гидравлических опор (10) может подниматься и опускаться. Внутри корпуса расположена якорная мешалка (3) с лопатками (4), соответствующими профилю корпуса. Мешалки (3) и (4) вращаются в противоположные стороны с помощью гидродвигателей (7) и соосных валов (6). Кроме этого, в корпусе реактора смонтирована и турбинная мешалка (5), вращающаяся с помощью электродвигателя (8). Наличие трех мешалок обеспечивает качественное перемешивание компонентов мази. Загрузка реактора осуществляется через паровой клапан (11), его корпус имеет «рубашку» для подвода горячей или холодной воды.
|
|
Рис. 4.2. Реактор-смеситель
Для смешивания основ и лекарственных веществ используют тестомесильные машины типа ТММ-1М, которые имеют сменный подкатывающийся котел и смешивающий рычаг с лопастями. Котел приводит во вращение электродвигатель.
Фирма «А. Джонсон и Кº» (Англия) выпускает универсальный смеситель «Юнитрон» (рис. 4.3). Он состоит из неподвижного резервуара (1), закрывающегося крышкой (2) с гидравлическим управлением. В крышке имеются впускные каналы и система для мойки резервуара без его вскрытия. В центре котла вмонтирован вал (3), приводящий в движение сменные смесительные насадки (4) и вращающийся скребок (5). В резервуаре имеется нижнее выпускное отверстие (6) и отверстие (7) для подключения гомогенизатора или другого оборудования. Смешивание компонентов в резервуаре можно производить при различных температурах, в среде инертного газа, с постоянным измерением температуры смеси, содержания в ней влаги, определения массы и других параметров.
|
|
Управление всеми операциями выполняется с пульта, на котором установлены записывающие устройства.
Рис. 4.3. Схема смесителя «Юнитрон»
Однако, с помощью одних мешалок нельзя добиться необходимой дисперсности суспензионных мазей. Поэтому мази при их производстве подвергают гомогенизации, для чего используют мазетерки различных типов (дисковая, валковая, жерновая).
Дисковая мазетерка состоит из двух дисков, расположенных горизонтально, один под другим. Вращается нижний диск, верхний неподвижный скреплен с воронкой, в которую подается мазь. В воронке имеется мешалка или скребки, способствующие движению мази. На дисках имеются насечки, более глубокие в центре и сходящие на нет к краям. Мазь поступает в просвет между дисками в центр растирается и одновременно перемещается к краям, с которых снимается скребками в приемник. Степень размола регулируется расстоянием между дисками. Производительность дисковой мазетерки 50-60 кг мази в час.
|
|
Валковая мазетерка состоит из двух или трех параллельно и горизонтально расположенных вращающихся валов с гладкой поверхностью (рис. 4.4). Они могут быть изготовлены из фарфора, базальта или металла. Для создания оптимальной температуры мази, поступающей на валки , их изготавливают полыми, чтобы при необходимости во внутрь можно было подавать воду. При работе валки вращаются с разной скоростью – 38 об/мин, 16 об/мин и 6,5 об/мин (последний, кроме того, совершает колебательные движения). Дифференциацию скоростей вращения валков обеспечивают специальные шестерни.
Рисунок 4.0. 1 - валки: 2 - бункер; 3 - направляющий желоб.
Мазь помещают в бункер, из него она самотеком поступает на валки, зазор между которыми регулируется. С третьего валка мазь поступает по направляющему желобу (3) в приемник фасовочной машины. Различная скорость вращения валков обеспечивает переход мази с одного валка на другой. Измельчающее действие их складывается из трех моментов:
твердые частицы (комки) раздавливаются или дробятся в щелях между валками (1, 2);
размалывающее действие далее усиливается перетирающим действием валков (2, 3), вследствие большей их скорости вращения;
растирающее действие усиливается дополнительными колебательными движениями третьего валка вдоль своей оси и соответствующим зазором между валками.
Валковые мазетерки имеют предохранительное устройство, автоматически останавливающее их работу при попадании посторонних предметов в зазоры между валками. Производительность их – около 50 кг мази в час.Существенно интенсифицировать процессы, протекающие при изготовлении таких дисперсных систем, как эмульсионные, суспензионные и комбинированные мази, можно путем применения РПА
При приготовлении мазей, содержащих аморфные вещества (сера, окись цинка, крахмал и др.), с помощью РПА возможно исключение стадии предварительного измельчения лекарственных веществ. Производство мазей, содержащих лекарственные вещества с прочной кристаллической решеткой (борная кислота, стрептоцид) предусматривает предварительное тонкое измельчение препаратов перед применением РПА.
В любом случае его применение позволяет экономить время, электроэнергию и снижать количество вспомогательных веществ по сравнению с традиционными методами приготовлениямазей.
Технологический процесс приготовления мазей может быть периодическим и непрерывным. Периодический процесс может быть многоступенчатым и зависит от числа аппаратов, в которых последовательно проводят отдельные стадии. В качестве примеров приведем краткое описание периодических процессов производства мазей.
Упаковку мазей производят в емкости из различных материалов. Мази, содержащие водную фазу или летучие компоненты, упаковывают в емкости, предотвращающие их испарение. Для упаковки мазей часто используются банки стеклянные, фарфоровые, из полимерных материалов (полистирол) емкостью 10, 20, 30, 50 и 100 мл, которые закрываются завинчивающимися крышками под обтяжку 00.
Для фасовки мазей ангро используют деревянные бочки (50-100 кг), жестяные или стеклянные банки (5-10-20 кг).
Мази фасуют с помощью шнековых и поршневых дозирующих машин (рис. 4.5). Шнековая самодозирующая машина состоит из бункера (1), заполняемого мазью, и шнека (2), подающего мазь через кран (3) в мундштук (4). Через определенные промежутки времени кран закрывается, и мазь из мундштука выталкивается в баночку или тубу. Фасовка осуществляется по времени закрытия и открытия крана. Банки с расфасованной мазью закрывают крышками.
Рис. 4.5. Шнековая машина для фасовки мазей
Наиболее удобной и современной упаковкой для мазей являются тубы, изготовленные из металла или полимерных материалов. Туба является наиболее гигиеничной и удобной упаковкой – на нее можно наносить деления, допускающие дозирование мази, к ней могут прилагаться насадки (апликаторы) из пластмассы, позволяющие вводить мазь в полости и т.д. Для металлических туб используют алюминий марок А6 и А7. Внутренняя поверхность их покрывается лаком (ФЛ-559), а наружная – эмалевой краской, на которую затем наносится маркировка.
В качестве полимерных материалов для изготовления туб используют полиэтилен низкой и высокой плотности, полипропилен, поливинилхлорид.
С целью герметизации отверстие тубы закрывают сплошной тонкой алюминиевой пленкой, сверху навинчивается конический бушон. Внутри бушона имеется острый шип, которым прокалывают отверстие тубы при использовании.
Для наполнения туб используют тубонаполнительные машины линейного и карусельного типа. Так, машины Colibri, “GA-40”, “GA-85” (Италия) предназначены для наполнения как металлических, так и полиэтиленовых туб (кроме А-85); фирма «Ивка» (Германия) изготавливает машины «ТИ-23», «TF-24», «TF-51»; фирма «Гофлигер-Карг» – тубонаполнительные машины марки «Rossi», которые способны упаковывать мази в металлические, полиэтиленовые и поливинилхлоридные тубы; шведская фирма «Аренко» производит машины типа «Arencomatic-1000» и «Arencomatic-2000»
Последовательность тубонаполнения
На роторном столе (например, у машины TF-51 (рис. 4.6)) смонтированы попарно 20 тубодержателей. Пустые тубы с лотка при помощи подающего устройства устанавливаются на разжатых тубодержателях. Здесь же производится продувка туб и их вакуумирование с целью удаления пыли, остатков упаковочного материала и др. После перемещения роторного стола на определенно заданный угол происходит операция подтяжки колпачков для туб и их рихтовка (вдавливание туб в тубодержатели до отказа). Затем с помощью фотоэлектрического устройства производится ориентация тубы по этикетке. Это же устройство играет и контрольно-блокирующую функцию, отключая подачу мази в случае отсутствия тубы в тубодержателе. В следующей позиции роторного стола происходит наполнение тубы мазью, которая из бункера подается по шлангам через наполнительные сопла. Сопло входит в тубу перед началом наполнения и поднимается по мере ее наполнения. По окончании происходит обратное отсасывание мази, благодаря чему она не вытекает из сопла в промежутках между стадиями наполнения.
Далее происходит герметизация тубы. Края ее сплющиваются и туба фальцуется один раз на 180°. Затем производится окончательная фальцовка, сжатие фальца, нанесение на него рифления, цифр, обозначающих дату выпуска, серию и др. После этого тубы подаются на транспортер или к спусковому желобу.
Рис. 4.6. Схема дозирующего устройства тубонаполнительной машины «TF-51»
а – момент подачи порции мази из бункера (1); б – момент заполнения тубы (4) мазью через шланги (2) и металлические сопла (3)
Тубонаполнительные машины фирмы «Ивка» имеют устройства, позволяющие наполнять тубы мазями в среде инертного газа (антибиотики, легкоокисляющиеся вещества). Машины часто комплектуются в линии с машинами, подающими пустые тубы, упаковочными машинами в бумажные пеналы, складывающими их в картонные коробки, обандероливающими и упаковывающими их в полиэтиленовую пленку. Эти машины одновременно наносят маркировку, сопроводительные надписи и др. Схема технологической линии для наполнения и упаковки туб показана на рис. 4.7.
Рис. 4.7. Схема технологической линии для наполнения и упаковки туб
1 – машина, подающая пустые тубы; 2 – тубонаполнительная машина; 3 – машина для упаковки туб в пеналы; 4 – машина для упаковки пеналов в картонные коробки; 5 – машина для упаковки картонных коробок в полиэтиленовую пленку
Дата добавления: 2019-07-15; просмотров: 2075; Мы поможем в написании вашей работы! |
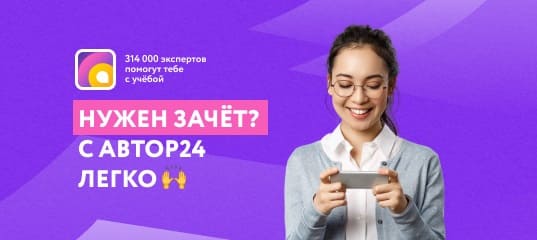
Мы поможем в написании ваших работ!